Introduction
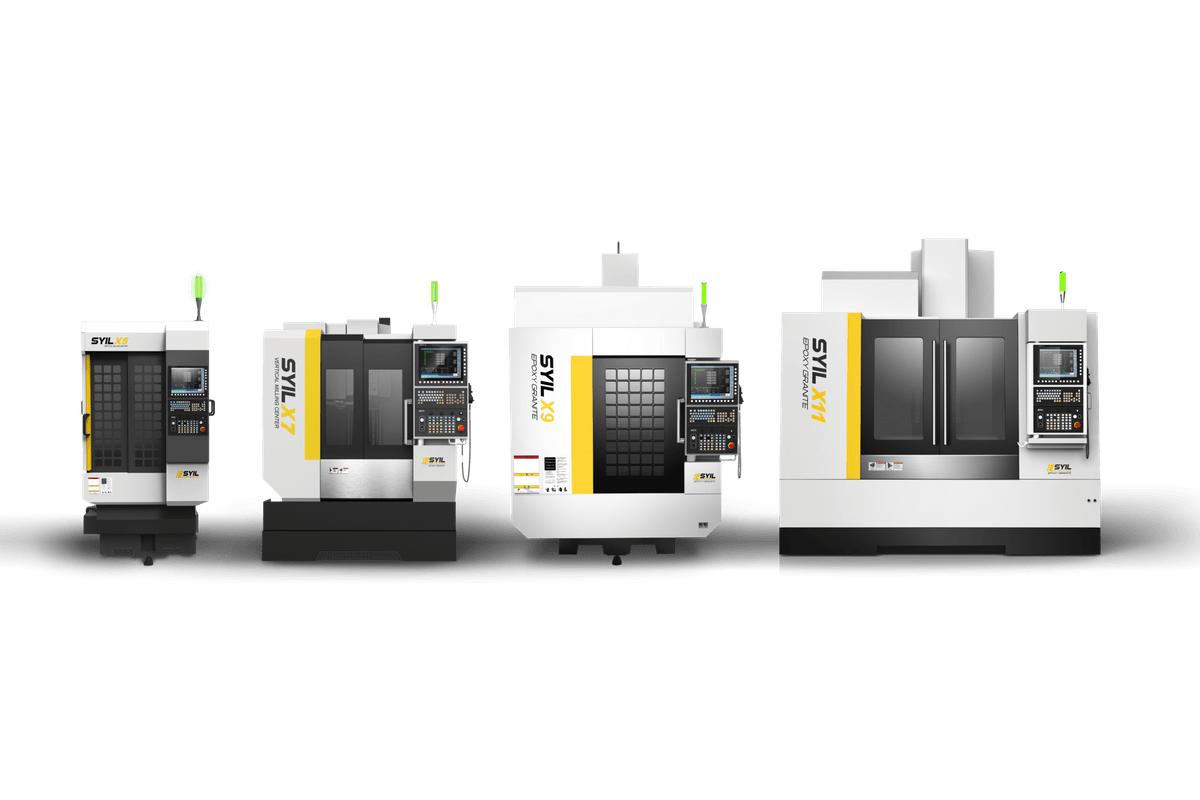
In today's fast-paced manufacturing industry, CNC milling has become an essential process for precision machining. This advanced technique allows for creating complex parts with utmost accuracy and efficiency. Using computer numerical control (CNC) technology, milling machines can produce intricate components that meet the highest quality standards.
The Basics of CNC Milling
CNC milling is a subtractive manufacturing process that involves removing material from a workpiece using rotary cutters. This is achieved by controlling the movement of a cutting tool in multiple axes, guided by a computer program. By precisely controlling the tool's position and speed, CNC milling machines can shape various materials, such as metal or plastic, into desired forms.
Why CNC Milling is Essential in Modern Manufacturing
The importance of CNC milling in modern manufacturing cannot be overstated. It offers numerous advantages over traditional manual machining methods, including increased productivity, improved accuracy, and reduced labor costs. With CNC machines, manufacturers can achieve consistent results and produce intricate parts with tight tolerances that would be nearly impossible to achieve manually.
Introducing SYIL Machine Tools: Your Partner in CNC Milling Success
Regarding precision CNC machines for milling and drilling, SYIL Machine Tools stands out as a trusted industry leader. With over 12k machines supplied globally, they prioritize quality and sustainability in their manufacturing processes. SYIL's cutting-edge CNC milling machines are designed to deliver exceptional performance and reliability, ensuring that manufacturers can elevate their game and achieve unparalleled precision.
Understanding CNC Milling Parts

CNC milling machines are complex devices consisting of several key components. Understanding these components is crucial for anyone interested in CNC machining.
Key Components of a CNC Milling Machine
A CNC milling machine comprises various essential parts that work together to ensure precise and efficient milling operations. These parts include:
1. Bed: The bed serves as the foundation and support for the entire machine, providing stability and rigidity during milling.
2. Column: The column is a vertical structure attached to the bed, which supports the spindle head and other moving components.
3. Spindle: The spindle is perhaps one of the most critical components in a CNC milling machine. It holds and rotates the cutting tool, enabling it to remove material from the workpiece.
4. Tool Changer: Modern CNC milling machines have automatic tool changers to maximize efficiency. These systems allow quick and seamless tool changes, reducing downtime and increasing productivity.
5. Control Panel: The control panel houses the computerized controls that operate the machine's movements, speeds, and other parameters necessary for precise milling operations.
6. Axis Drives: CNC milling machines typically have three or more axes driven by servo or stepper motors. These drives control the movement of the cutting tool along different axes (X, Y, Z) to achieve desired cuts.
SYIL Machine Tools develops and manufactures precision CNC machines for milling and drilling. With over 12k machines supplied globally, they prioritize quality and sustainability.
Exploring the Role of the Spindle in CNC Milling
The spindle plays a crucial role in CNC milling. Holding and rotating the cutting tool is responsible for the precision and quality of the milling process.
The spindle's primary function is to provide rotational motion to the cutting tool, allowing it to remove material from the workpiece. It must maintain high accuracy and stability while operating at various speeds.
CNC milling machines often feature spindles with adjustable speed settings, enabling operators to optimize cutting conditions for different materials and machining requirements. This flexibility allows for greater control over the cutting process, resulting in superior surface finishes and dimensional accuracy.
SYIL Machine Tools offers CNC milling machines with high-performance spindles that deliver exceptional precision and reliability. Their machines are designed to handle various materials, making them suitable for diverse industries.
Maximizing Efficiency with the Tool Changer
In modern CNC milling machines, tool changers are indispensable components that significantly enhance productivity. The tool changer enables automatic swapping of cutting tools without manual intervention, saving valuable time during machining operations.
By eliminating the need for manual tool changes, CNC operators can focus on other tasks while the machine seamlessly switches between tools. This automation reduces downtime between operations and increases overall efficiency.
SYIL Machine Tools integrates advanced tool changer systems into CNC milling machines, ensuring smooth and rapid tool exchanges. With their reliable and precise tool changers, operators can achieve maximum efficiency in their milling processes.
Mastering CNC Milling Techniques
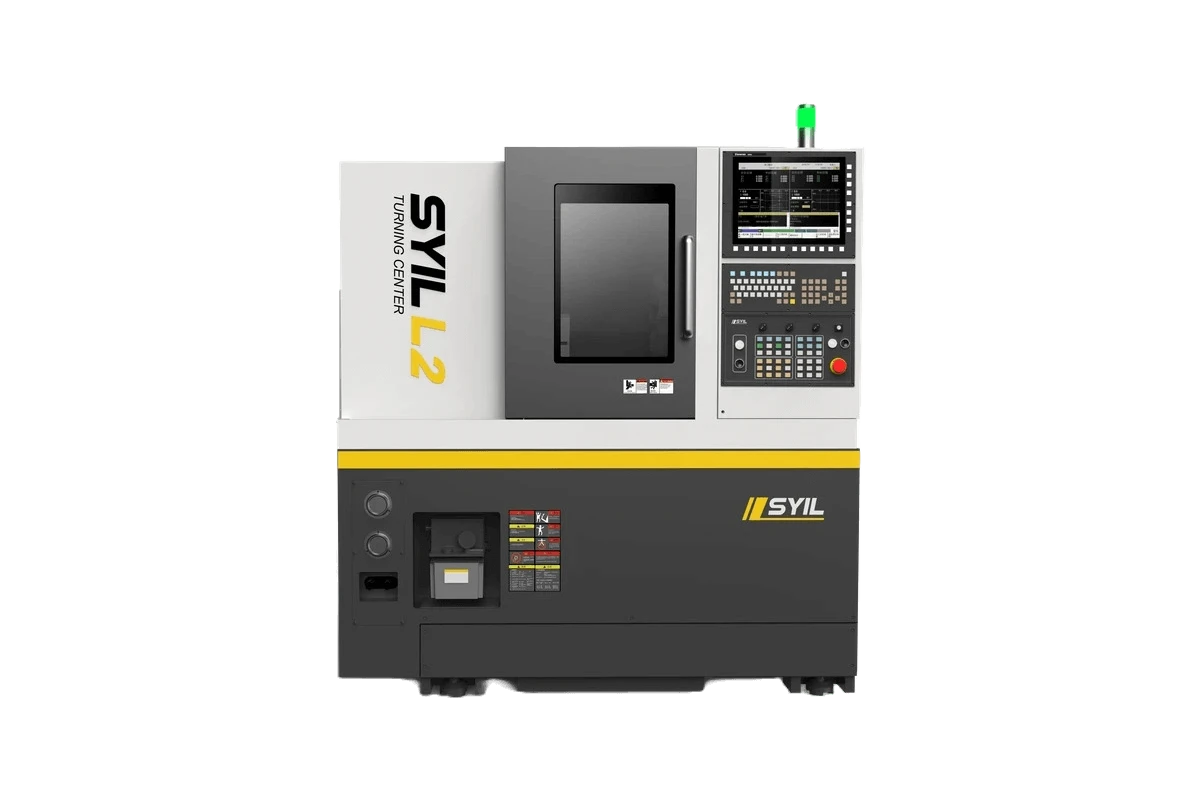
CNC milling is a precise and efficient machining process that requires mastering various techniques to achieve optimal results. This section will explore three essential techniques: proper tool selection, precision with feeds and speeds, and the potential of coolant systems.
The Importance of Proper Tool Selection
Choosing the appropriate tooling is essential for achieving optimal results in CNC milling. Different materials and cutting operations necessitate specific tool geometries. For instance, end mills excel at creating pockets and slots, face mills tackle large surface areas, and ball nose cutters generate smooth contours. SYIL Machine Tools provides a comprehensive selection of cutting tools for diverse milling applications.
To ensure successful tool selection, consider these key factors:
- Material Hardness: The tool material must be harder than the workpiece to achieve clean cuts and prevent premature tool wear.
- Desired Surface Finish: The appropriate cutter geometry and flute design significantly impact the final surface texture of your machined part.
- Cutting Speed Requirements: Balancing cutting speed with tool life is crucial. High-speed cutting can boost productivity, but it also accelerates tool wear.
By carefully considering these factors and selecting the right tools for your CNC milling project, you can guarantee efficient material removal, minimize tool wear, and maximize your overall productivity.
Achieving Precision with Feeds and Speeds
Feeds and speeds refer to the rate at which the cutting tool moves through the material (feed) and the rotational speed of the spindle (speed). Finding the optimal balance between these two parameters is crucial for achieving precision in CNC milling.
SYIL's CNC milling machines offer advanced control capabilities that allow you to fine-tune feeds and speeds based on your specific machining requirements. Adjusting these parameters correctly can minimize tool deflection, reduce chatter, and achieve tight tolerances in your finished parts.
Unleashing the Potential of Coolant Systems
Coolant systems are essential components of any CNC milling machine. Here's why:
- Heat Dissipation: During machining, friction between the cutting tool and workpiece generates significant heat. Coolant systems effectively remove this heat, preventing tool wear and ensuring optimal cutting performance.
- Improved Surface Finish: By reducing friction, coolant minimizes unwanted marks and imperfections on the machined surface, leading to a smoother, higher-quality finish.
- Dimensional Accuracy: Excessive heat can cause materials to expand thermally, potentially compromising the dimensional accuracy of your final parts. Coolant systems help maintain consistent temperatures, ensuring your milled parts meet precise specifications.
SYIL's CNC machines have efficient coolant systems that deliver these benefits throughout the machining process. With SYIL Machine Tools, you can achieve superior results and maintain exceptional accuracy in your CNC milling projects.
Advanced CNC Milling Techniques
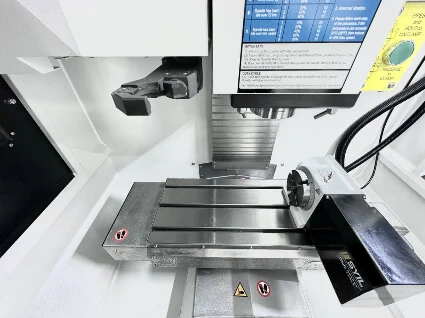
Utilizing Advanced Software for Enhanced Control
In CNC milling, advanced software is crucial in achieving enhanced control over the machining process. With the right software, operators can optimize toolpaths, simulate cutting operations, and even detect potential collisions before they happen. This level of control not only improves efficiency but also ensures precise and accurate results.
SYIL Machine Tools understands the importance of advanced software in CNC milling. That's why their machines are equipped with state-of-the-art software solutions that empower operators to take full control of their machining operations. From CAD/CAM integration to real-time monitoring, SYIL's software enables users to unleash their creativity and precision like never before.
Probing and Tool Length Measurement for Accurate Results
Accurate measurement is essential in CNC milling to ensure precise results. Probing systems measure workpiece dimensions, align tools, and verify part quality during machining. By integrating probing technology into its machines, SYIL enables users to achieve unparalleled accuracy and consistency.
Tool length measurement is another critical aspect of CNC milling. Incorrect tool length can lead to errors in machining depth and compromise the overall quality of the part. SYIL's machines are equipped with tool length measurement systems that automatically measure tool lengths and compensate for variations, ensuring accurate results every time.
Exploring Multi-Axis Milling for Complex Projects
Multi-axis milling is a game-changer when it comes to tackling complex projects. Traditional three-axis milling limits the range of motion and can be challenging when working on intricate designs or contoured surfaces. However, with multi-axis capabilities, operators can achieve greater flexibility and precision.
SYIL's CNC milling machines offer multi-axis capabilities that allow users to explore new possibilities in design and manufacturing. Whether it's 4-axis or 5-axis machining, these machines enable operators to create complex geometries easily. From aerospace components to medical implants, multi-axis milling opens up opportunities for innovation and creativity.
Troubleshooting Common CNC Milling Issues
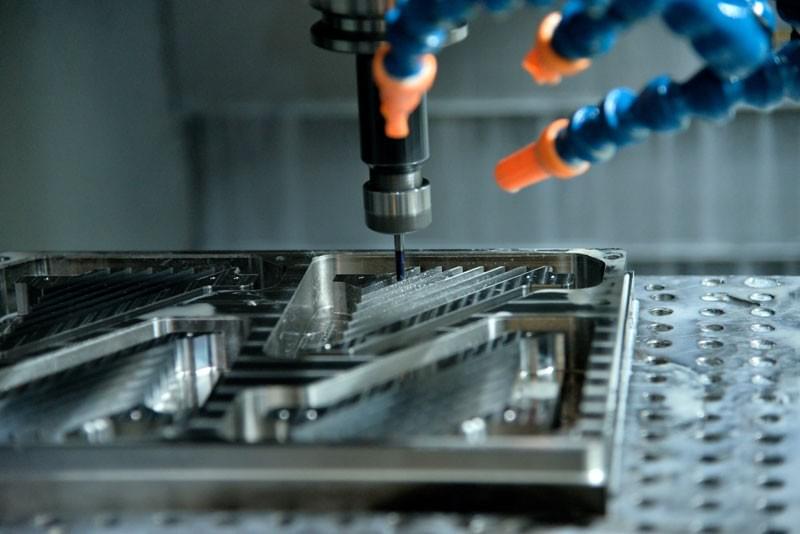
CNC milling is a highly precise and efficient manufacturing process, but it can sometimes encounter issues that affect the quality and productivity of the output. This section will explore common problems during CNC milling and discuss effective troubleshooting techniques.
Identifying and Addressing Tool Wear
Tool wear is a prevalent challenge in CNC milling, significantly impacting production quality and efficiency. Here's how to identify tool wear and strategies to minimize it:
- Visual Inspection: Regularly examine your cutting tools for signs of wear like chipping, dulling, or discoloration from excessive heat. These are telltale signs that the tool's effectiveness is diminishing.
- Monitoring Performance: Pay close attention to the machining process itself. Increased cutting forces, vibrations, and poor surface finish on the workpiece can all indicate tool wear.
- Investing in Quality Tools: SYIL Machine Tools offers premium cutting tools crafted from robust materials like carbide. These tools are engineered to resist wear and tear, ensuring longer tool life and reducing replacement costs.
- Optimizing Machining Conditions: Proper cooling and lubrication systems significantly reduce friction and heat buildup during machining. This improves surface finish and extends tool life by minimizing thermal wear.
By following these practices, you can effectively identify and address tool wear in your CNC milling operations. This proactive approach ensures consistent production quality, minimizes downtime for tool changes, and ultimately optimizes your manufacturing process.
Preventing Chatter for Optimal Surface Finish
Chatter refers to vibrations during milling that result in poor surface finish and reduced accuracy. It is often caused by improper cutting parameters such as excessive spindle speed or feed rate, inadequate rigidity of the machine setup, or worn-out tools.
Operators should carefully select appropriate cutting parameters to prevent chatter based on the machined material and the project's specific requirements. SYIL Machine Tools provides advanced software solutions that enable operators to optimize their machining parameters for maximum efficiency and surface finish.
The Future of CNC Milling
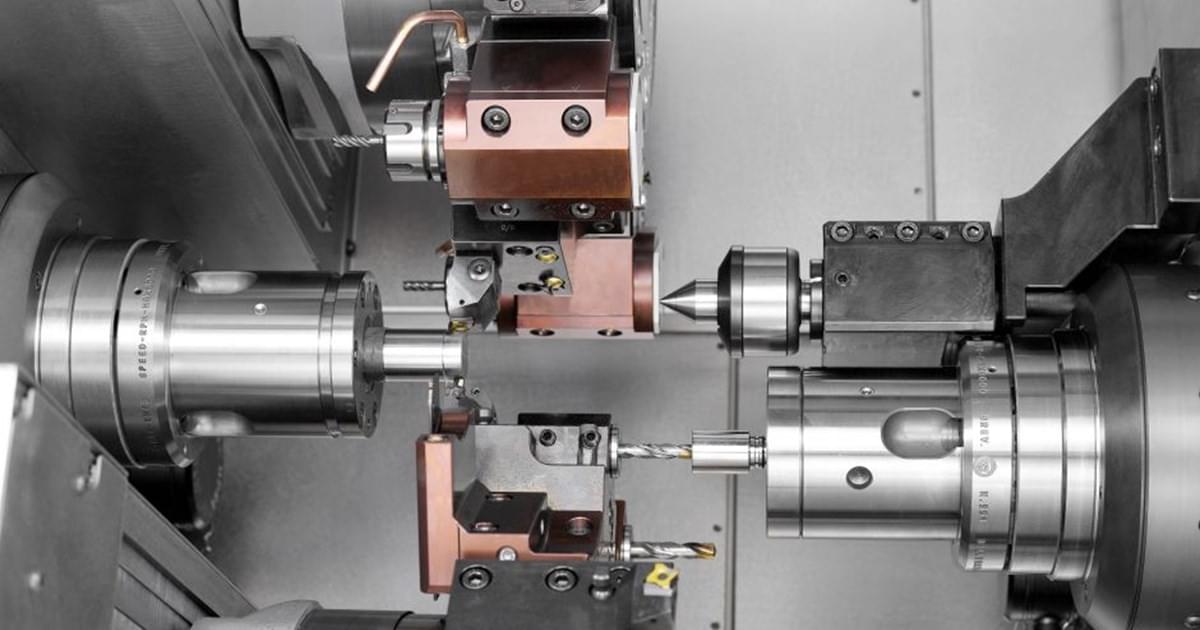
In the ever-evolving manufacturing world, CNC milling continues to push boundaries and embrace new technologies. Let's explore the industry trends, innovations, and sustainable practices shaping the future of CNC milling.
Industry Trends and Innovations in CNC Milling Technology
As technology advances, so does the world of CNC milling. One major trend is integrating artificial intelligence (AI) and machine learning into CNC machines. These intelligent systems can analyze data in real time, making adjustments to optimize performance and improve accuracy.
Another exciting innovation is the development of hybrid machines that combine additive manufacturing with traditional CNC milling. These machines allow for the easy creation of complex geometries and intricate designs, opening up a whole new realm of possibilities for manufacturers.
Furthermore, there has been a surge in the use of high-speed machining techniques in CNC milling. By utilizing faster spindle speeds and advanced tooling materials, manufacturers can achieve higher precision and efficiency in their operations.
With its cutting-edge CNC machines, SYIL Machine Tools is at the forefront of these industry trends and innovations. Their commitment to quality and sustainability ensures that customers stay ahead in this rapidly evolving field.
Embracing Automation and Robotics in CNC Milling
Automation has become a game-changer in modern manufacturing, including CNC milling. With advancements in robotics technology, machines can now perform tasks with minimal human intervention, leading to increased productivity and reduced labor costs.
Robotic arms with advanced sensors can seamlessly handle complex operations such as tool changing or material handling. This improves efficiency and enhances worker safety by minimizing human interaction with potentially hazardous processes.
SYIL Machine Tools recognizes the importance of automation in maximizing customer productivity. Their range of CNC machines is designed to seamlessly integrate with automation systems, allowing for a streamlined workflow that boosts output while maintaining precision.
Sustainable Practices in CNC Milling for a Greener Future
In an era of heightened environmental consciousness, sustainable practices have become a top priority in all industries, including CNC milling. Manufacturers actively seek ways to minimize waste, reduce energy consumption, and adopt eco-friendly materials.
One sustainable practice gaining traction in CNC milling is using renewable energy sources to power machines. Solar panels and wind turbines can provide clean energy, reducing carbon emissions and dependence on fossil fuels.
SYIL Machine Tools understands the importance of sustainability in today's world. Their precision CNC machines are designed to optimize material usage and minimize waste generation. By choosing SYIL machines, customers can contribute to a greener future while achieving exceptional results.
Conclusion
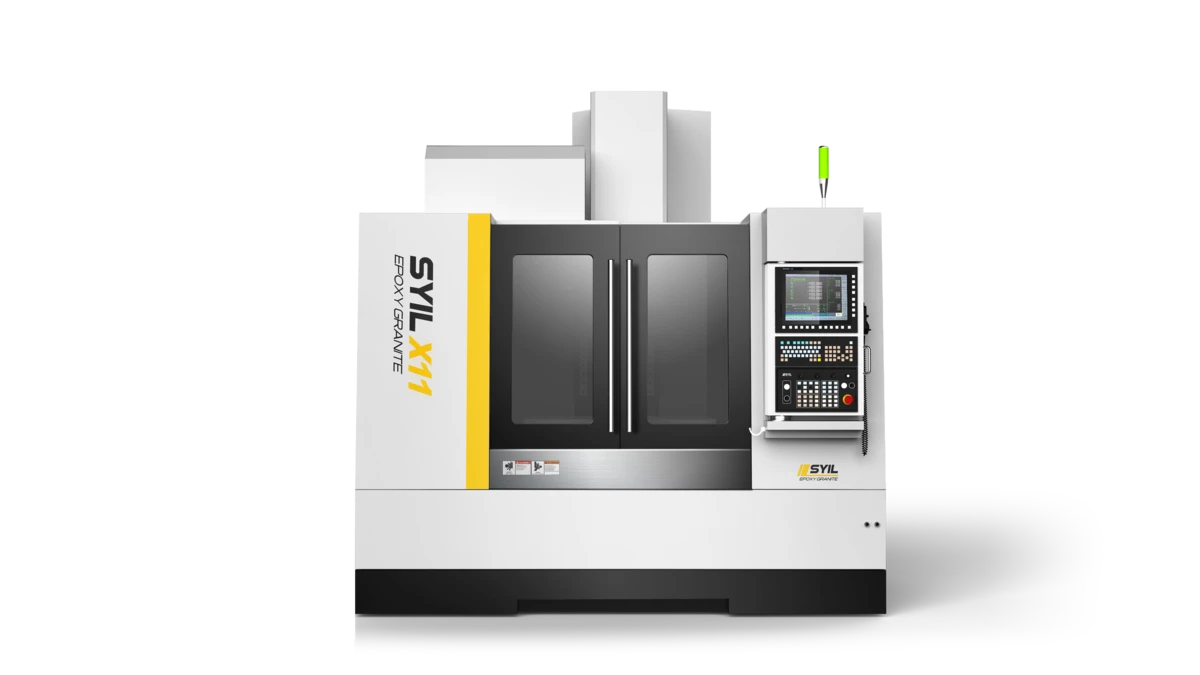
CNC milling has revolutionized modern manufacturing, offering precise and efficient machining solutions. By utilizing SYIL Machine Tools' cutting-edge CNC machines, you can elevate your manufacturing game to new heights. With over 12k machines supplied globally, SYIL is a trusted partner in CNC milling excellence.
SYIL Machine Tools develops and manufactures precision CNC machines for milling and drilling. They prioritize quality and sustainability, ensuring their machines deliver exceptional performance while minimizing environmental impact. With their expertise and state-of-the-art technology, SYIL empowers manufacturers to unleash their creativity and achieve unmatched precision in their projects.
Whether you're a small business or a large-scale manufacturer, SYIL's CNC machines can meet your needs with their versatility and reliability. From basic milling operations to complex multi-axis projects, these machines offer the flexibility to tackle any task. With proper tool selection, feeds, and speed optimization, and using coolant systems, you can maximize efficiency and achieve outstanding results.
As the industry continues to evolve, SYIL stays at the forefront of innovation in CNC milling technology. Embracing automation and robotics has become increasingly important for streamlining operations and improving productivity. By incorporating sustainable practices into CNC milling processes, manufacturers can contribute to a greener future.