Introduction
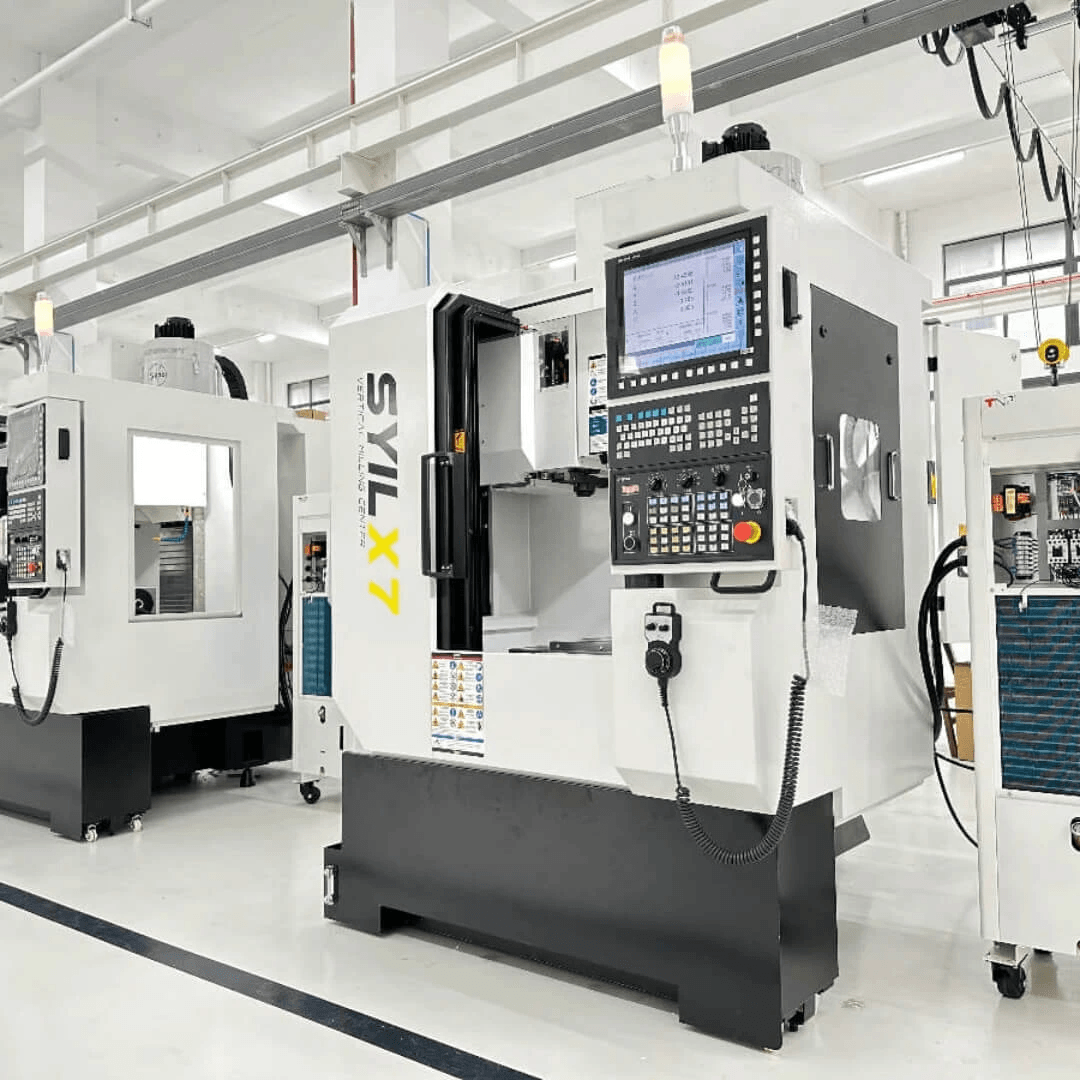
In today's fast-paced manufacturing world, Computer Numerical Control (CNC) has emerged as a game-changer. By automating processes that were once manual and labor-intensive, CNC technology enhances precision and efficiency across various industries. Understanding what a CNC machine is used for is crucial for grasping its significance in modern production environments.
What is Computer Numerical Control?
Computer Numerical Control refers to the automated control of machining tools and 3D printers by means of a computer. Essentially, it transforms traditional manual operations into precise, programmable tasks that can be executed with incredible accuracy. This technology allows engineers and machinists to create complex parts with minimal human intervention, revolutionizing how products are manufactured.
Importance of CNC in Modern Manufacturing
The importance of CNC in modern manufacturing cannot be overstated; it increases productivity while reducing errors and waste. With the ability to produce highly intricate designs quickly, manufacturers can meet market demands more effectively than ever before. Moreover, the adoption of computer numerical control systems leads to significant cost savings over time due to less material waste and faster production cycles.
Overview of CNC Applications
CNC machines find applications across an impressive range of industries—from aerospace to automotive, medical devices to consumer goods. They are utilized not only for mass production but also for precision engineering and prototyping tasks that require high levels of detail and accuracy. As we delve deeper into this topic, we'll explore questions like Is it hard to learn CNC? or What are the 5 common types of CNC machines?—each critical for understanding this fascinating field.
Understanding Computer Numerical Control
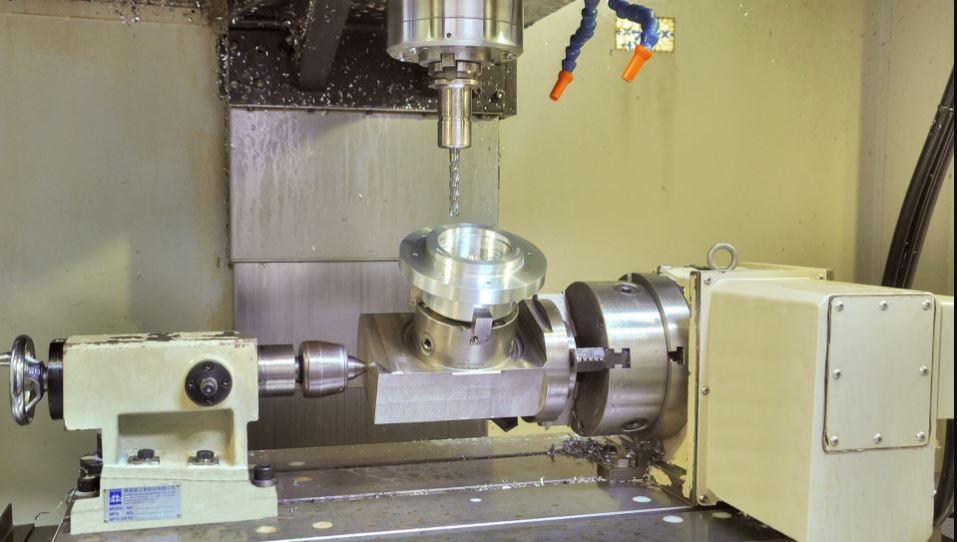
Computer Numerical Control (CNC) revolutionizes the manufacturing landscape by automating machine tools through computer programming. This technology enables precise control over machining processes, making it a cornerstone of modern manufacturing. To truly appreciate its significance, we must delve into its definition, operational mechanisms across industries, and the essential components that make up a CNC system.
Definition of Computer Numerical Control
Computer Numerical Control refers to the automated control of machining tools such as drills, lathes, and mills via computer systems. Unlike traditional manual machining methods, CNC allows for higher precision and repeatability in production processes. Essentially, CNC transforms raw materials into finished products with minimal human intervention, leading to greater efficiency and accuracy.
How CNC Works in Different Industries
CNC technology finds applications across various industries including aerospace, automotive, and electronics. In aerospace manufacturing, for instance, computer numerical control is used to create intricate components that require high precision and reliability. Similarly, in the automotive sector, CNC machines are employed for everything from prototyping parts to mass production runs—making them indispensable tools in modern manufacturing practices.
Key Components of a CNC System
A typical CNC system comprises several key components that work together seamlessly to achieve desired outcomes. The main elements include the computer interface where design files are uploaded; the controller that interprets these files; and the machine itself which carries out the physical operations like cutting or milling. Additionally, feedback systems such as sensors play a vital role in ensuring accuracy throughout the machining process—highlighting just how essential these components are for effective computer numerical control.
What is a CNC Machine Used For?
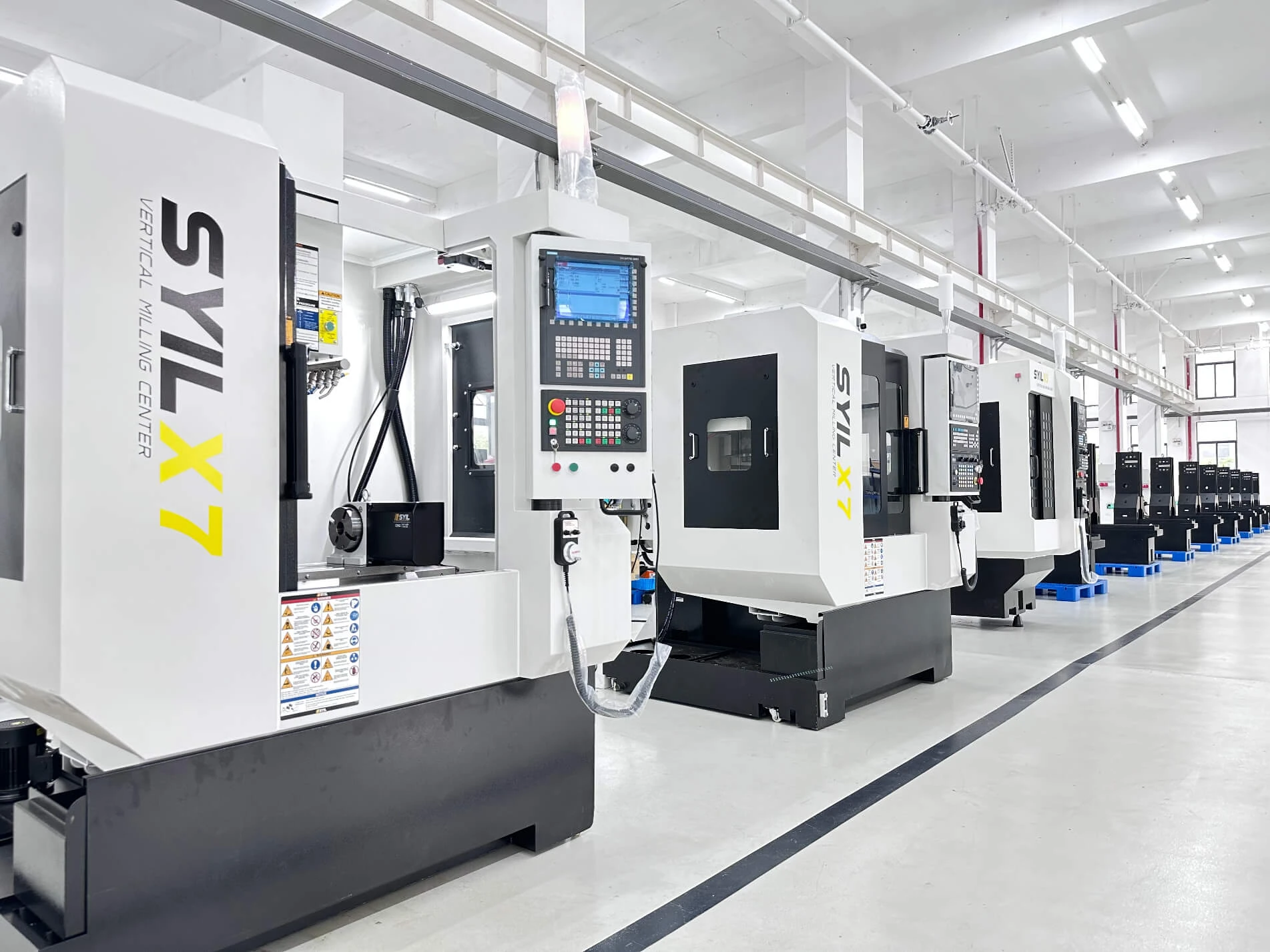
CNC machines have revolutionized the manufacturing landscape, serving a multitude of purposes across various sectors. From aerospace to automotive, the applications of computer numerical control are vast and varied. Essentially, these machines automate processes that were once labor-intensive, improving efficiency and precision.
Applications Across Various Industries
Computer numerical control is utilized in numerous industries, each benefiting from its unique capabilities. In the automotive industry, CNC machines are essential for creating complex engine components with high precision. Similarly, in the aerospace sector, they produce parts that must meet stringent safety standards while maintaining lightweight properties—showcasing just how versatile a CNC machine can be.
Moreover, CNC technology finds its place in woodworking and metalworking shops where custom designs are crafted with ease. Jewelry makers also leverage computer numerical control to create intricate designs that would be nearly impossible to achieve manually. Overall, understanding what a CNC machine is used for reveals its critical role in modern manufacturing across diverse fields.
Precision Engineering and Prototyping
One of the standout features of computer numerical control is its ability to deliver unmatched precision in engineering tasks. This accuracy makes it an invaluable tool for prototyping new products; designers can quickly iterate their ideas into tangible models without extensive manual labor or time delays. With a CNC machine at their disposal, engineers can ensure that every prototype meets exact specifications before moving into mass production.
Additionally, this level of precision allows for tighter tolerances in finished products—a necessity in industries like medical device manufacturing where even minor errors can have significant consequences. Consequently, projects that require meticulous detail benefit immensely from adopting computer numerical control methods during both prototyping and production stages.
Benefits for Mass Production
When it comes to mass production, computer numerical control truly shines by enhancing speed and efficiency while maintaining quality standards. A well-programmed CNC machine can operate continuously with minimal human intervention—allowing manufacturers to scale up their output without sacrificing accuracy or consistency. This capability translates into reduced labor costs and faster turnaround times on large orders.
Moreover, the repeatability offered by CNC machines means that once a design is programmed into the system, it can produce thousands of identical parts with little variation between them—ideal for industries relying on high-volume production runs such as electronics or consumer goods manufacturing. As companies increasingly seek ways to optimize their operations and reduce waste, understanding what a CNC machine is used for becomes vital in staying competitive within today's market landscape.
Is it Hard to Learn CNC?
Learning Computer Numerical Control (CNC) can seem daunting at first, but with the right approach, it becomes an exciting journey into the world of precision manufacturing. Many beginners find themselves overwhelmed by the technical jargon and complex machinery involved, but breaking it down into manageable parts can ease this learning curve. Whether you’re a hobbyist or looking to dive into a professional career, understanding what is a CNC machine used for? and how it operates will significantly enhance your confidence.
Learning Curve for Beginners
For those asking, Is it hard to learn CNC?, the answer often lies in individual experience and background. While some may find the programming aspect challenging initially, hands-on practice with a CNC machine can rapidly build proficiency. With time and dedication, most learners discover that mastering computer numerical control is not only achievable but also incredibly rewarding as they see their designs come to life.
Resources for CNC Training
A variety of resources are available for anyone keen on diving into computer numerical control training. Online courses, community colleges, and vocational schools offer structured learning environments where students can gain practical skills and theoretical knowledge about what are the 5 common types of CNC machines? Additionally, many manufacturers provide workshops that allow aspiring operators to work directly with equipment under expert guidance. Utilizing these resources makes it easier for beginners to overcome initial hurdles in learning how to operate a CNC machine effectively.
Career Opportunities for CNC Operators
The demand for skilled CNC operators continues to rise across various industries due to the increasing reliance on computer numerical control technology in manufacturing processes. Career opportunities range from entry-level positions in machine shops to advanced roles involving programming and operation of sophisticated computer numerical control systems. As industries evolve and adopt new technologies like 3D printing integrated with traditional machining methods, understanding what is the difference between NC and CNC will give job seekers an edge in this competitive field.
What is the Difference Between NC and CNC?
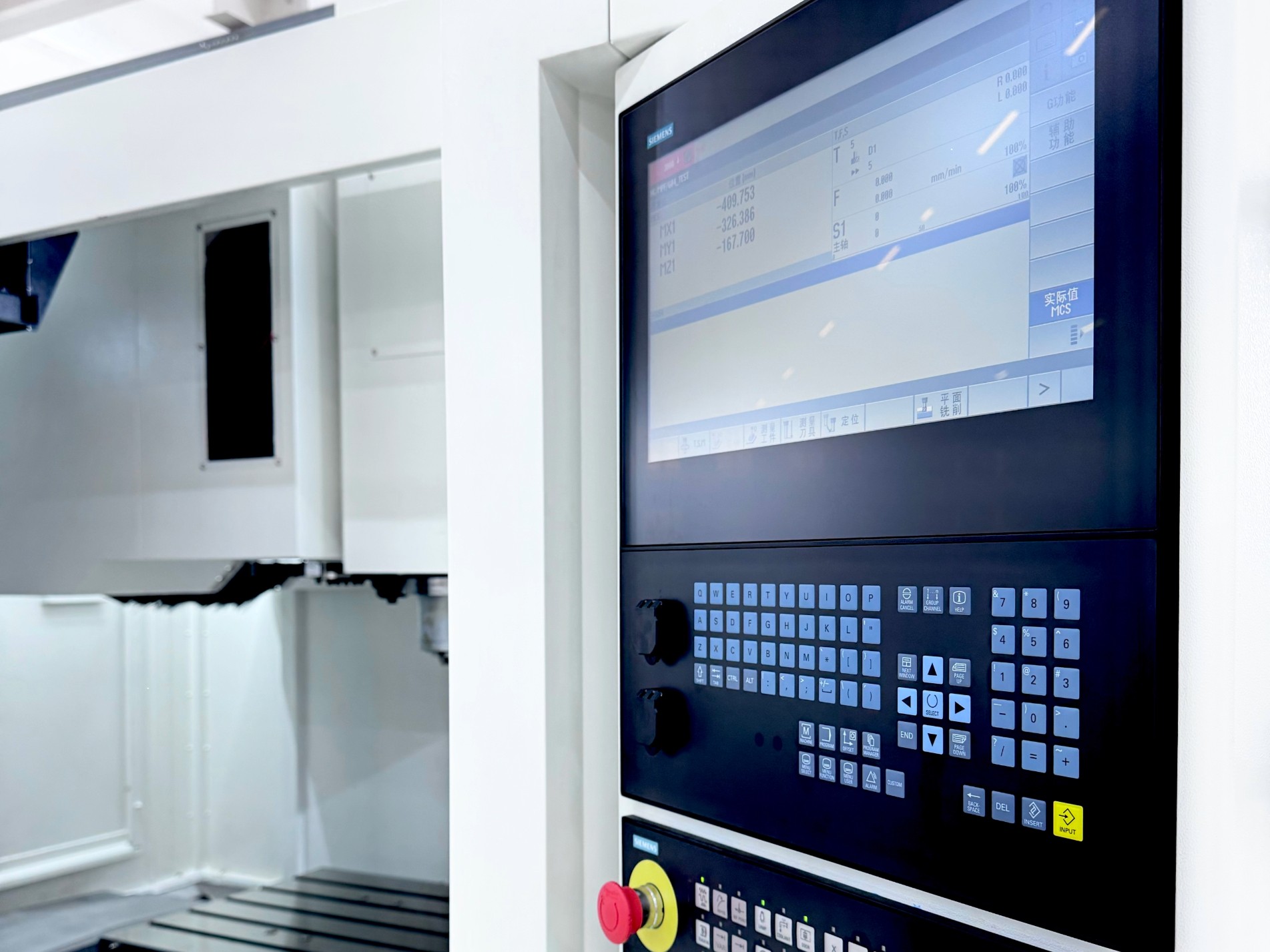
In the realm of modern manufacturing, understanding the distinction between Numerical Control (NC) and Computer Numerical Control (CNC) is crucial. While both methods involve controlling machine tools through programmed commands, CNC represents a significant evolution of NC technology. This section delves into what NC entails, how CNC has advanced the field, and its profound impact on manufacturing processes.
Explanation of Numerical Control (NC)
Numerical Control (NC) refers to a method in which machines are operated using predetermined sequences of commands encoded on physical media like punched tape or cards. Initially developed in the 1940s and 1950s, NC machines required manual input for programming, which limited their flexibility and efficiency. The essence of NC lies in its ability to automate machining processes but with constraints that modern manufacturers find increasingly inadequate.
Advancements in Computer Numerical Control
Computer Numerical Control (CNC) emerged as a game-changer by integrating computers into the control process, allowing for more sophisticated programming methods and real-time adjustments. Unlike traditional NC systems that relied on static command inputs, CNC systems enable dynamic interaction through software interfaces that can be easily modified or updated. These advancements have led to greater precision and versatility in what a CNC machine can do, making it invaluable across various industries—from aerospace to automotive manufacturing.
Impact on Manufacturing Processes
The transition from NC to CNC has revolutionized manufacturing processes by enhancing productivity and reducing lead times significantly. With computer numerical control systems, manufacturers can achieve higher levels of automation while ensuring consistent quality across production runs—an essential factor for mass production scenarios. Moreover, as industries continue to adopt innovative technologies like CAD/CAM integration alongside CNC machinery, they are experiencing unprecedented efficiencies that were once thought impossible with traditional NC methods.
What Are the 5 Common Types of CNC Machines?
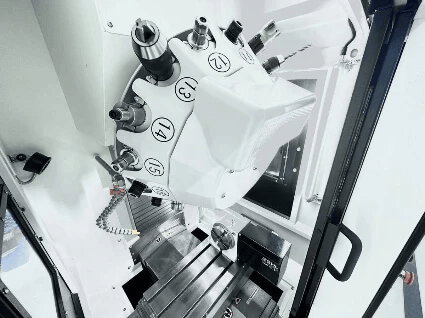
CNC machines are the backbone of modern manufacturing, providing precision and efficiency across various industries. Understanding the different types of CNC machines is essential to grasping what is a CNC machine used for in practical applications. From milling to laser cutting, each machine has its unique capabilities that cater to specific manufacturing needs.
Overview of CNC Mills and Lathes
CNC mills and lathes are two of the most common types of computer numerical control machines found in workshops today. A CNC mill operates by removing material from a workpiece through rotating cutting tools, allowing for intricate designs and shapes to be produced with high precision. On the other hand, a CNC lathe spins the workpiece against a stationary tool, making it ideal for creating cylindrical shapes and components.
Both CNC mills and lathes exemplify what is a CNC machine used for: producing detailed parts with tight tolerances that would be nearly impossible to achieve manually. The versatility of these machines means they can handle everything from one-off prototypes to large-scale production runs, showcasing their importance in various sectors such as aerospace, automotive, and medical device manufacturing. In essence, these machines represent the core functionality of computer numerical control technology.
Introduction to CNC Routers and Lasers
Moving beyond mills and lathes, we encounter CNC routers and lasers—machines that excel in different areas of fabrication. A CNC router utilizes high-speed spinning bits to cut materials like wood, plastic, or soft metals with impressive accuracy; this makes it perfect for signage or furniture design projects where intricate patterns are required. Conversely, laser cutters employ focused beams of light to slice through materials like metal or acrylic with exceptional precision.
These types of computer numerical control machines highlight another aspect of what is a CNC machine used for: achieving diverse results across multiple materials while maintaining high levels of detail. The versatility offered by routers and lasers allows manufacturers to expand their capabilities without needing an entirely new set-up—an attractive prospect for businesses looking to innovate while controlling costs effectively. The advancements in technology have made these machines indispensable tools across industries such as woodworking, metalworking, and even textile production.
The Role of SYIL CNC Machines in Industry
When discussing what are the 5 common types of CNC machines, it's hard not to mention SYIL's contribution within this landscape. SYIL manufactures high-quality desktop-sized CNC milling machines that cater specifically to small businesses or hobbyists who want access to professional-grade equipment without breaking the bank. These compact yet powerful devices allow users from various backgrounds—be it engineering students or entrepreneurs—to engage with computer numerical control technology firsthand.
The role SYIL plays extends beyond just providing machinery; they also help demystify whether it is hard to learn CNC by offering user-friendly interfaces combined with extensive training resources tailored for beginners eager to dive into this field. Their commitment not only empowers individuals but also fosters innovation within local communities as more people gain access to cutting-edge manufacturing technologies—demonstrating how accessible computer numerical control can be when supported by industry leaders like SYIL.
In conclusion, understanding the different types of common CNC machines equips you with insight into their applications across various sectors while showcasing their significance in modern manufacturing practices today.
Conclusion
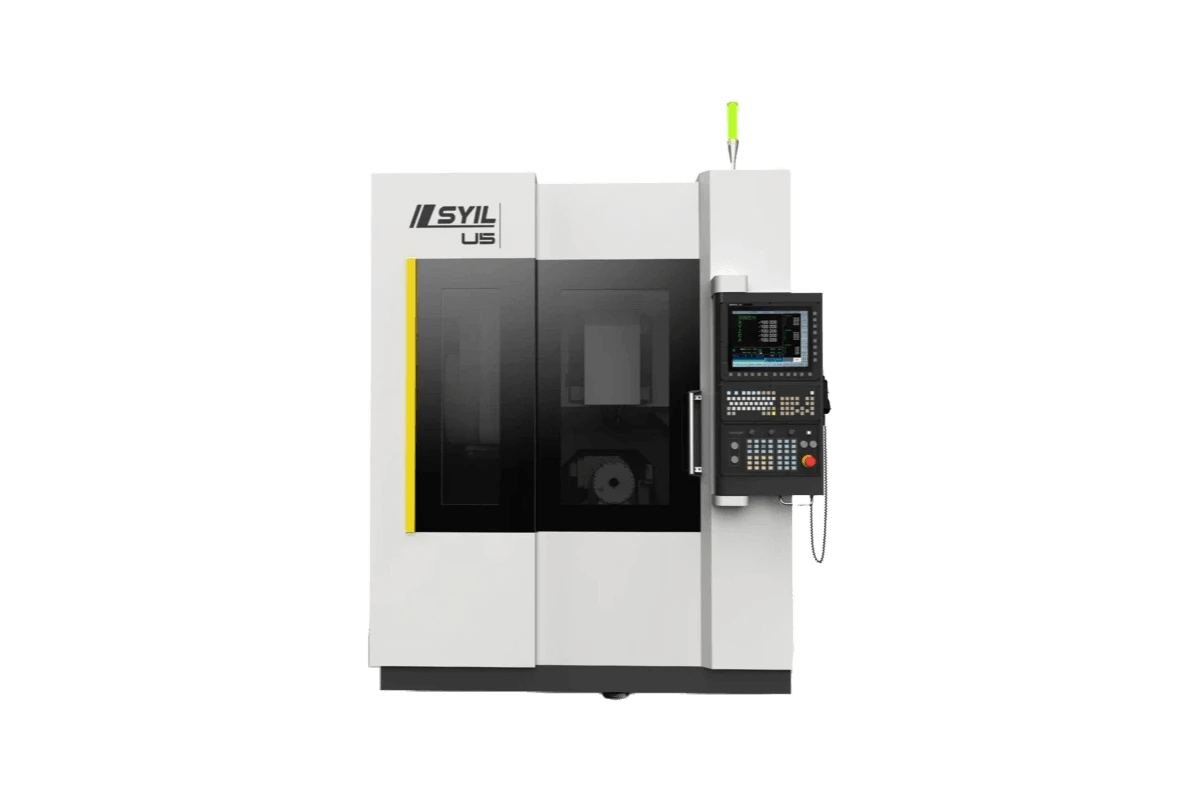
In conclusion, the adoption of Computer Numerical Control (CNC) has revolutionized modern manufacturing, making it an indispensable part of various industries. The advantages of computer numerical control include increased precision, reduced waste, and enhanced productivity. As we look ahead, it’s clear that CNC technology will continue to evolve and shape the future of manufacturing.
Advantages of Adopting Computer Numerical Control
One major advantage of adopting computer numerical control is its ability to produce complex shapes with incredible accuracy that would be nearly impossible with manual methods. This precision translates directly into cost savings by minimizing material waste and reducing errors in production processes. Moreover, CNC machines can operate continuously with minimal human intervention, allowing businesses to enhance their output while lowering labor costs.
Real-World Computer Numerical Control Examples
Real-world examples of computer numerical control applications are abundant across various sectors. For instance, in the automotive industry, CNC machines are used for cutting intricate parts that fit together seamlessly in vehicles. Similarly, the aerospace sector relies heavily on CNC technology for crafting lightweight yet robust components essential for flight safety and efficiency.
Future Trends in CNC Technology
Looking towards the future, trends in computer numerical control technology suggest a shift towards greater automation and integration with artificial intelligence (AI). This evolution will likely make it easier for operators to learn how to use CNC machines effectively—addressing the question: Is it hard to learn CNC? Additionally, advancements may lead to more sophisticated types of CNC machines that increase versatility across different applications while further bridging the gap between NC and CNC methodologies.