Introduction
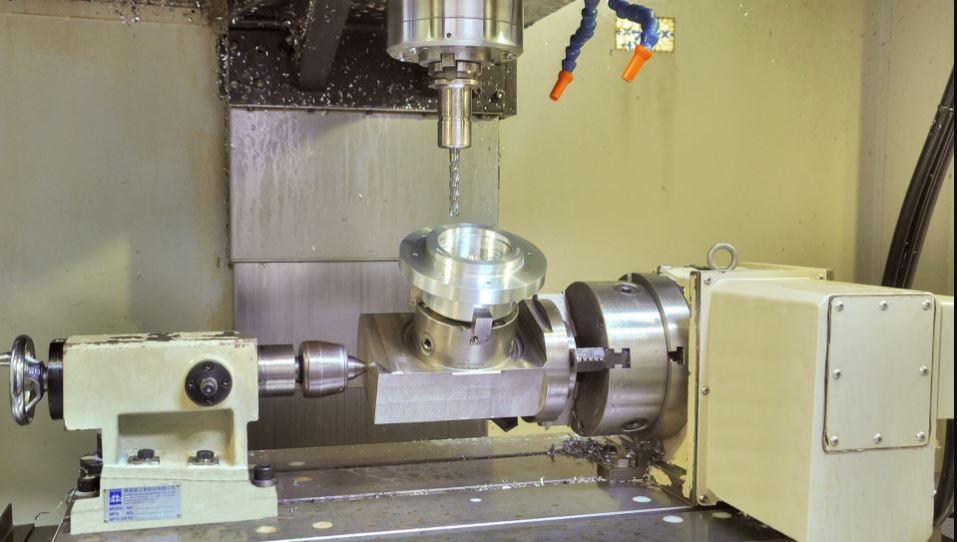
Milling is a fundamental process in the realm of manufacturing, playing a crucial role in shaping materials into desired forms. But what is the milling process? Essentially, it involves removing material from a workpiece to create intricate designs and precise dimensions. This introduction will delve into the importance of milling in manufacturing and provide an overview of milling operations.
Understanding the Milling Process
To grasp what is the process of milling, one must recognize that it combines both artistry and engineering. Milling machines utilize rotating cutters to shave off material from various surfaces, allowing for versatility in production. By understanding this dynamic process, manufacturers can enhance their production capabilities and ensure high-quality outcomes.
Importance of Milling in Manufacturing
The significance of milling cannot be overstated; it serves as a backbone for numerous industries including automotive, aerospace, and electronics. What is the purpose of milling? It not only enhances material shape and size but also contributes to better surface finishes that are essential for functional components. As such, milling operations are integral to achieving precision-engineered products that meet rigorous industry standards.
Overview of Milling Operations
Milling operations encompass several stages that transform raw materials into finished products through meticulous planning and execution. So, what are the five steps in the milling process? From preparing the workpiece to conducting quality inspections post-milling, each step is critical for ensuring optimal results. Understanding these operations allows manufacturers to streamline their processes and improve overall efficiency.
What is the Milling Process?
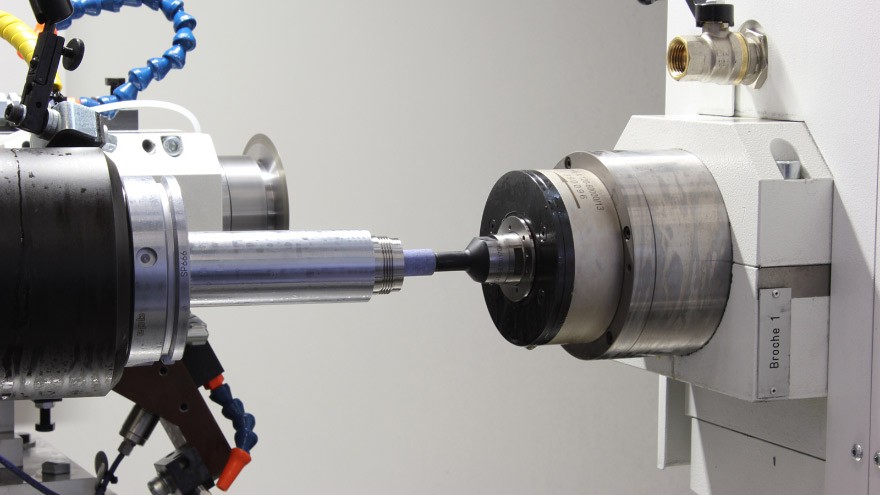
Milling is a fundamental manufacturing process that involves the removal of material from a workpiece using rotary cutters. This process is essential in shaping and finishing materials to meet specific design requirements. But what is the milling process, you ask? Simply put, it’s the art of transforming raw materials into precise components through controlled material removal.
Definition of Milling
So, what is the process of milling? At its core, milling refers to a machining operation where a rotating cutter removes material from a stationary workpiece. The movement can be either horizontal or vertical, depending on the machine setup and desired outcome. This definition captures not just the mechanics but also the versatility that milling offers across various sectors.
The Role of Material Removal
Material removal plays a pivotal role in defining what is the purpose of milling. It allows manufacturers to achieve specific dimensions and tolerances required for their products. By carefully controlling how much material is removed during each pass, operators can create intricate shapes and features that would otherwise be impossible with other manufacturing methods.
Applications in Various Industries
When exploring what are the five steps in the milling process, one must first understand its diverse applications across industries like aerospace, automotive, and medical devices. From crafting engine components to producing surgical instruments, milling operations are integral to creating high-quality products that require precision and reliability. The adaptability of milling techniques makes it an essential part of modern manufacturing processes worldwide.
What is the Purpose of Milling?
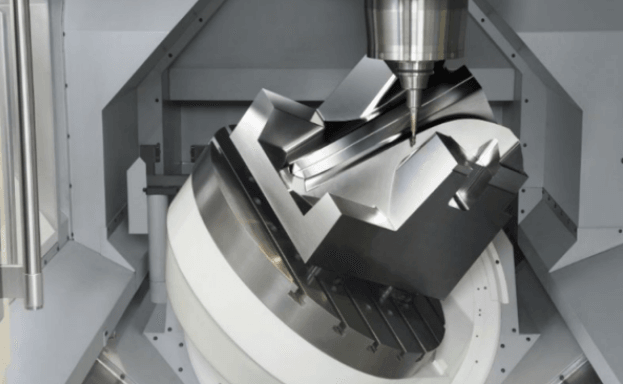
Milling plays a crucial role in transforming raw materials into usable components, serving various industries with precision and efficiency. But what is the purpose of milling? It’s not just about cutting; it's about enhancing material properties, achieving desired shapes and sizes, and preparing for subsequent processes that ensure the final product meets quality standards.
Enhancing Material Shape and Size
One of the primary purposes of milling is to enhance the shape and size of a workpiece. By removing excess material, milling allows manufacturers to achieve specific dimensions and geometries that meet design specifications. When we ask, What is the process of milling? it becomes clear that it involves intricate movements that sculpt materials into their intended forms.
The ability to fine-tune shapes through milling operations makes it indispensable in industries such as aerospace, automotive, and manufacturing. With precise control over depth and angle during cutting, operators can create complex features like grooves, slots, or even intricate patterns on surfaces. This capability not only improves functionality but also contributes to overall aesthetics in product design.
Improving Surface Finish
Another significant purpose of milling is improving surface finish. The process can reduce roughness on a workpiece's surface by utilizing various tooling options tailored for different finishes. So when we ponder What is the explanation of milling? it's essential to recognize how it enhances both performance and appearance through meticulous surface treatment.
A smoother finish achieved through milling operations results in better adhesion for coatings or paints while minimizing friction between moving parts in mechanical assemblies. This improvement leads to increased durability and longevity of components across many applications—from high-speed machinery to consumer electronics. Ultimately, achieving an optimal surface finish can be just as critical as meeting dimensional tolerances.
Preparing for Secondary Operations
Milling also plays a pivotal role in preparing workpieces for secondary operations—those additional processes needed after initial machining to achieve final specifications or functionalities. Understanding what are the five steps in the milling process helps clarify how this preparatory phase fits into broader manufacturing workflows.
For example, after completing initial shaping through milling, a part may require drilling holes or applying heat treatments to enhance its properties further. By providing an accurately shaped base component with a refined surface finish, milling lays down a solid foundation for these secondary operations—ensuring they are executed with precision and efficiency. In essence, effective milling streamlines production lines by reducing time spent on subsequent tasks while maintaining high-quality standards across all phases.
What are the Five Steps in the Milling Process?
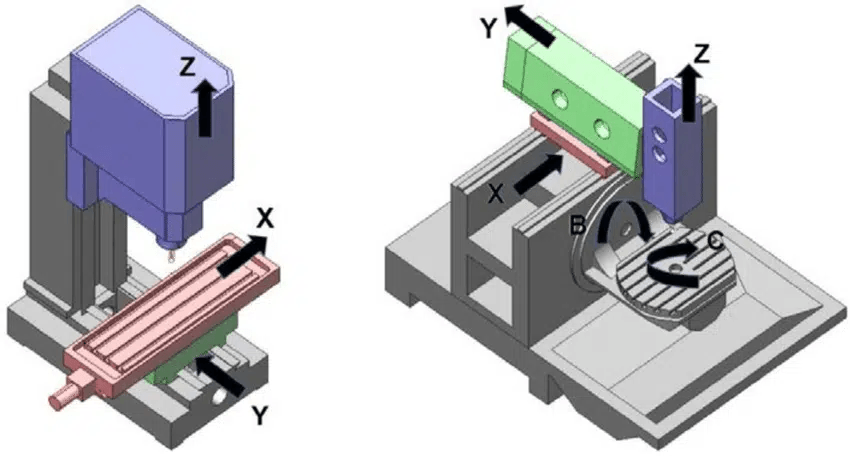
When diving into what is the milling process, it's essential to break it down into manageable steps. Understanding these five steps not only clarifies what is the process of milling but also highlights its efficiency and precision in manufacturing. Each step plays a crucial role in ensuring that milling operations yield high-quality results.
Step One: Workpiece Preparation
The first step in any milling operation involves workpiece preparation, which sets the foundation for a successful outcome. This entails selecting and securing the material that will undergo machining, ensuring it is free from defects and appropriately sized. Proper workpiece preparation directly influences what is the purpose of milling, as it ensures that subsequent processes can be carried out smoothly and accurately.
Step Two: Tool Selection
Next up is tool selection, a critical phase where machinists choose the appropriate cutting tools based on material type and desired finish. The right tool can significantly impact what is the process of milling by enhancing efficiency and precision during operations. Factors like tool geometry, material composition, and coating are considered to optimize performance during this step.
Step Three: Actual Milling Operation
Now we reach the heart of what is the milling process: the actual milling operation itself! During this phase, selected tools engage with the prepared workpiece to remove material according to specified designs or dimensions. This step showcases how effective milling operations can transform raw materials into precise components while achieving desired shapes and surface finishes.
Step Four: Finishing Touches
Once primary machining is complete, it’s time for finishing touches—an essential aspect of ensuring quality outcomes in any project involving what is the purpose of milling. This may involve additional passes with finer tools or adjustments to improve surface finish or dimensional accuracy further. The goal here is to elevate parts from functional to exceptional through meticulous attention to detail.
Step Five: Quality Inspection
Finally, we arrive at quality inspection—the last line of defense before products leave production floors! This crucial step involves assessing finished components against specifications using various measurement techniques to ensure they meet required standards—essentially answering what are the five steps in the milling process? By identifying any discrepancies early on, manufacturers can address issues before they escalate into costly problems.
Explanation of Milling Techniques
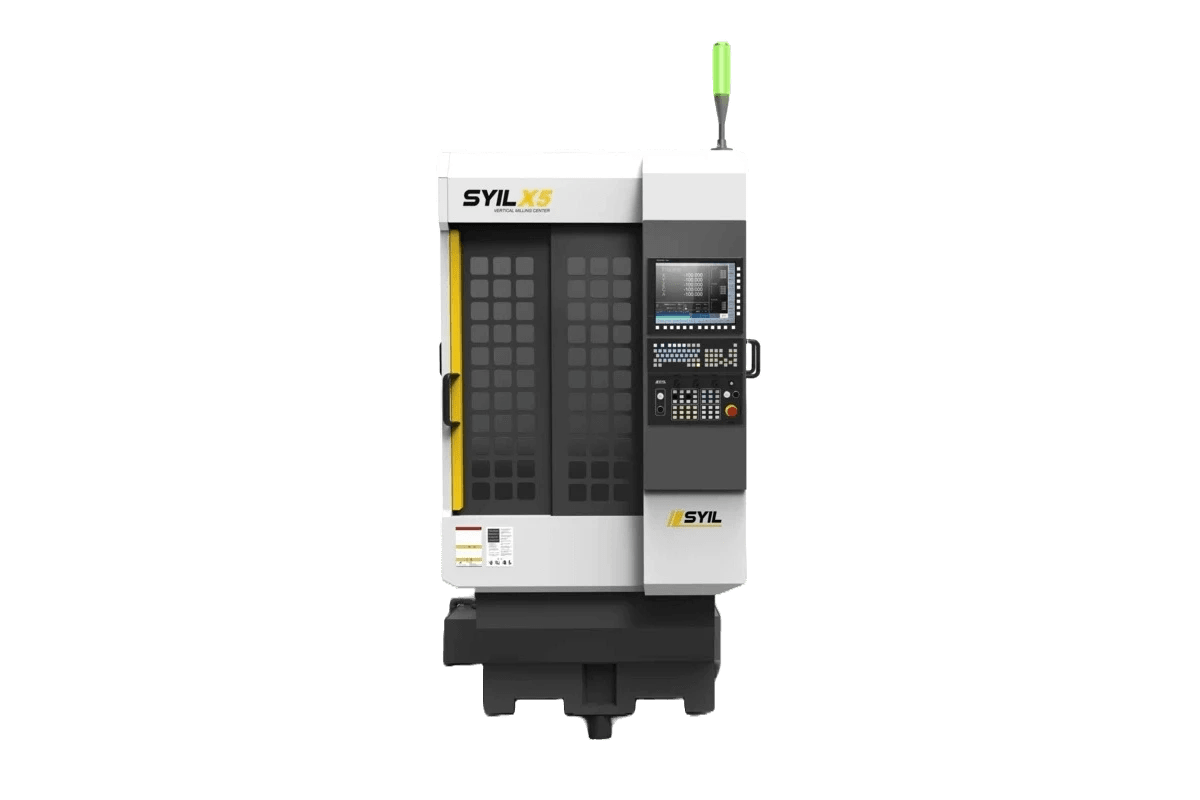
Milling techniques are essential to understanding what is the milling process and how it operates in various manufacturing environments. The choice of milling technique can significantly influence the quality of the final product, making it crucial for manufacturers to grasp these differences. By delving into conventional versus climb milling, types of machines like SYIL CNC, and the importance of precision, we can better appreciate what is the process of milling.
Conventional Vs. Climb Milling
When exploring what is the process of milling, one must consider two primary techniques: conventional and climb milling. In conventional milling, the cutter rotates against the direction of feed; this method tends to create a more significant surface finish but may lead to increased tool wear over time. Conversely, climb milling involves moving with the feed direction, which often results in superior finishes and reduced tool wear—a key consideration when evaluating what is the purpose of milling.
Understanding these two techniques helps clarify why different applications may favor one method over another based on factors like material type and desired finish quality. For instance, climb milling is generally preferred for softer materials due to its efficiency in removing material quickly while maintaining precision. Ultimately, knowing what are the five steps in the milling process allows operators to select appropriate techniques that align with their production goals.
Types of Milling Machines: Understanding SYIL CNC
When discussing types of machines within this context, SYIL CNC stands out as a robust option for modern manufacturing needs. These machines are designed with advanced features that enhance their versatility across various applications—an important factor when considering what is the purpose of milling in today’s industry landscape. With high-speed capabilities and user-friendly interfaces, SYIL CNC machines make it easier for operators to execute precise cuts efficiently.
In addition to their user-friendliness, SYIL CNC machines offer compact designs without sacrificing power or performance—critical attributes when space or budget constraints come into play during manufacturing operations. This adaptability allows businesses to scale their operations while ensuring they maintain quality standards that meet customer expectations consistently. Furthermore, understanding what is the explanation of milling through these machines highlights how technology continues to evolve within this field.
Importance of Precision in Milling Operations
Precision plays an indispensable role in all aspects related to what is the process of milling; it directly impacts product quality and operational efficiency. Accurate measurements ensure that components fit together seamlessly during assembly processes—a vital aspect when addressing what is the purpose of milling overall. Additionally, achieving high levels of precision minimizes waste and reduces costs associated with rework or scrap material.
Incorporating advanced technologies such as computer numerical control (CNC) into machining processes significantly enhances precision levels compared to traditional methods alone—this evolution speaks volumes about how far we've come regarding what are the five steps in the milling process today! As manufacturers strive for tighter tolerances and improved surface finishes across industries from aerospace engineering to medical device production, understanding these intricacies becomes paramount for success.
Ultimately, mastering precision not only leads to higher-quality outputs but also fosters innovation by allowing engineers greater freedom when designing complex parts—demonstrating just how essential it truly is within any discussion surrounding millings operations!
Benefits of Using SYIL CNC Machines
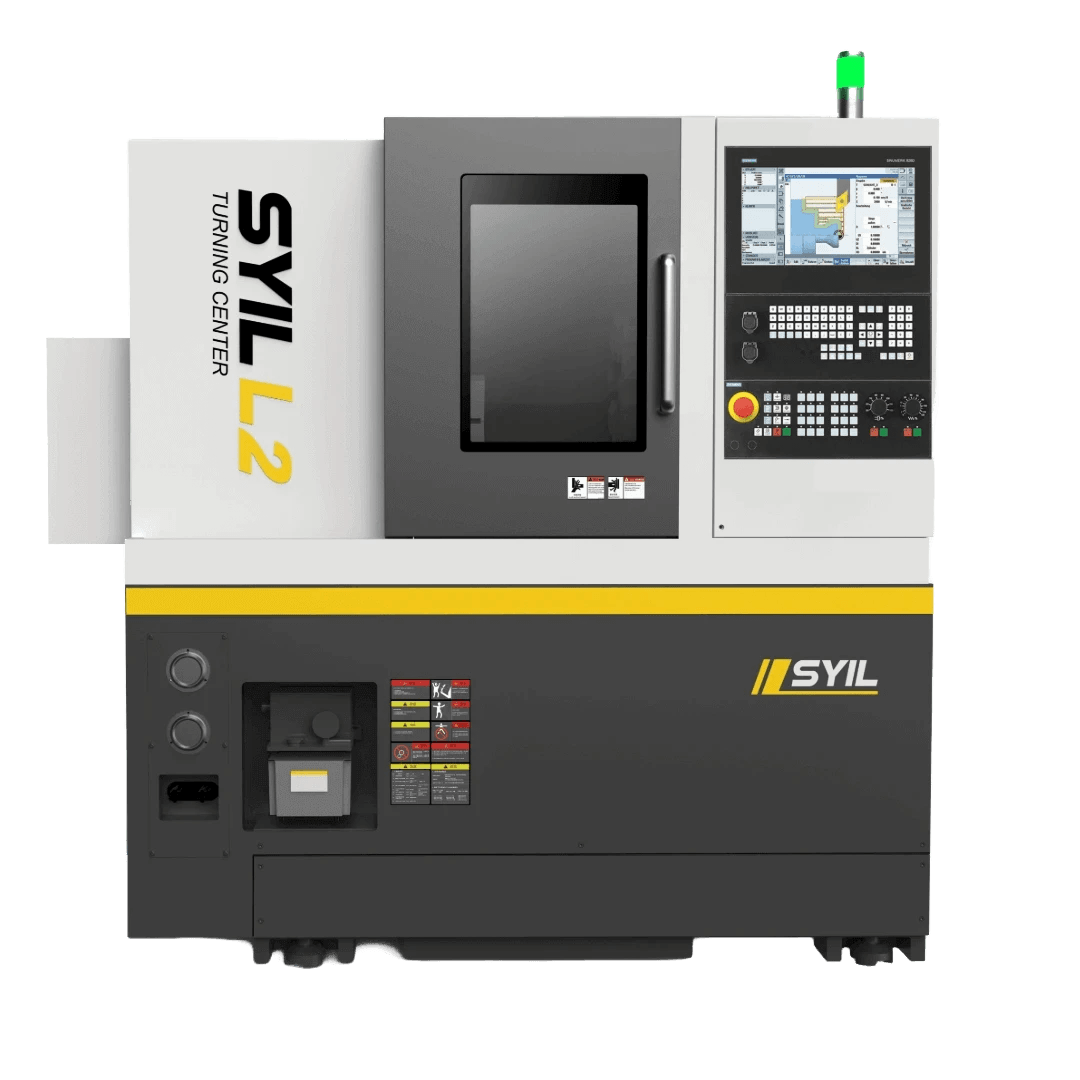
Compact and Powerful Design
One of the most striking features of SYIL CNC machines is their compact yet powerful design. This combination allows manufacturers to maximize floor space without sacrificing performance, a crucial consideration in any workshop setting. By reducing the machine's footprint while maintaining robust capabilities, users can efficiently utilize resources while answering What is the purpose of milling?—to enhance material shape and size effectively.
The compact nature also means that these machines are easier to integrate into existing setups or small workshops, making them accessible for businesses at various scales. With high-performance motors and precision engineering, SYIL machines provide a level of power that ensures optimal cutting speeds during milling operations. Thus, they embody what modern machining should achieve: efficiency without compromise.
High Rigidity and Thermal Stability
Milling operations require stability to ensure precision; this is where SYIL CNC machines excel with their high rigidity and thermal stability. These features minimize vibrations during operation, allowing for smoother cuts and better surface finishes—key factors in answering What are the five steps in the milling process? The solid construction helps maintain accuracy over extended periods, which is vital for large production runs.
Thermal stability further enhances performance by preventing distortion caused by heat generated during machining processes. When materials expand unevenly due to temperature fluctuations, it can severely affect outcomes; however, with SYIL's robust design, such issues are mitigated effectively. This reliability fosters confidence in achieving consistent results across different projects.
User-Friendly Maintenance and Operation
Operating a CNC machine shouldn't feel like rocket science; that's why user-friendly maintenance and operation are integral benefits of SYIL machines. They come equipped with intuitive interfaces that make it easy for operators to navigate functions without extensive training or experience—perfectly addressing What is an explanation of milling? as it relates to accessibility in manufacturing environments.
Moreover, routine maintenance has been simplified thanks to thoughtful engineering that allows quick access to key components without disrupting workflow significantly. This ease-of-use translates into less downtime for repairs or adjustments, ensuring that production schedules remain intact while maximizing output quality throughout all stages of milling operations. Ultimately, user-friendliness enhances productivity while ensuring that businesses can keep pace with evolving demands in manufacturing.
Conclusion
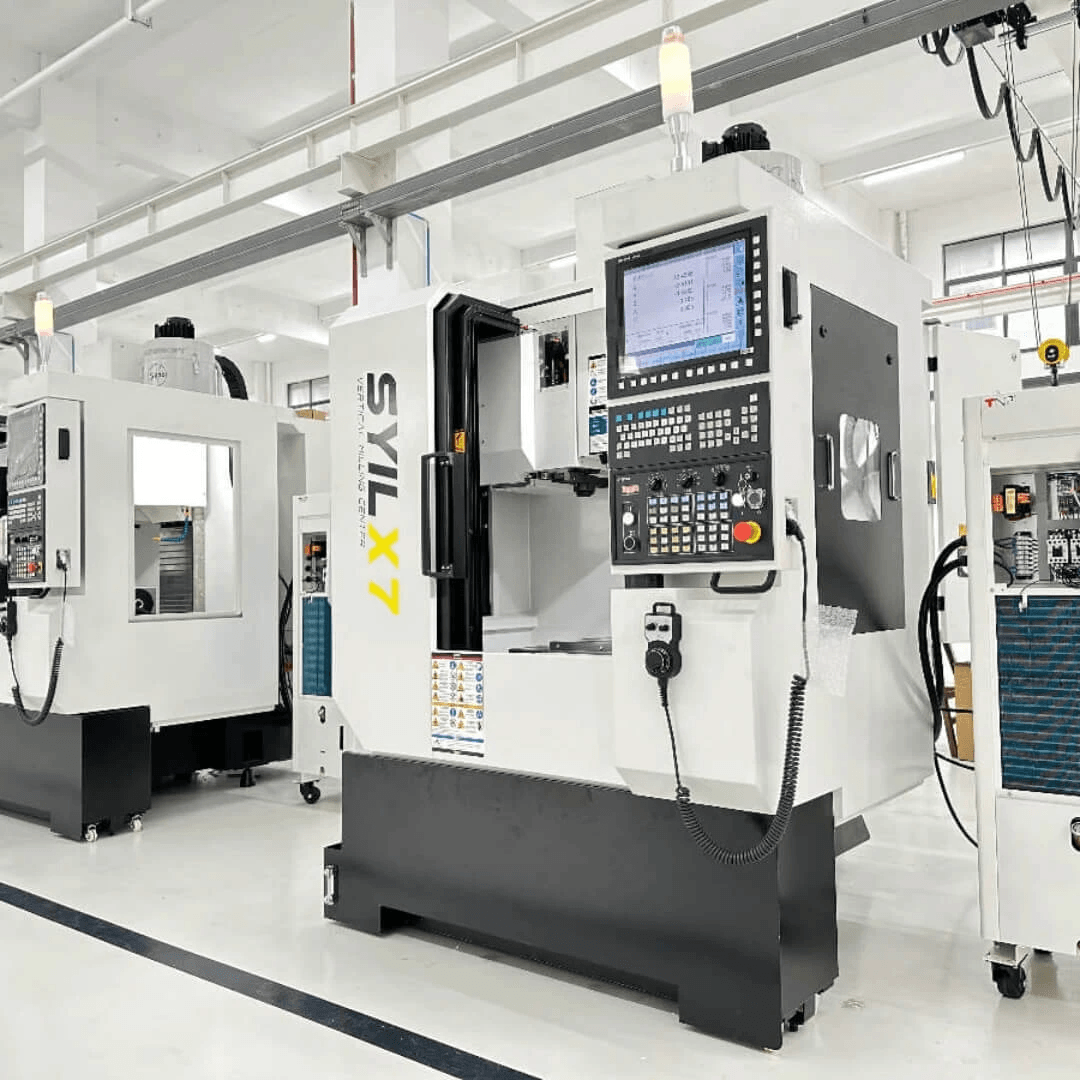
In summary, milling is a fundamental process in manufacturing that plays a crucial role in shaping materials for various applications. By understanding what is the milling process and its significance, we can appreciate how it enhances product quality and efficiency. The milling operations not only improve the surface finish but also prepare materials for further processing, making it an essential step in production.
Key Takeaways About Milling
What is the purpose of milling? At its core, milling serves to remove material from a workpiece to achieve desired dimensions and surface characteristics. The five steps in the milling process—workpiece preparation, tool selection, actual operation, finishing touches, and quality inspection—are vital for ensuring precision and reliability in manufactured products.
Furthermore, understanding what is the process of milling allows manufacturers to select appropriate techniques tailored to their specific needs. From enhancing shapes to improving functional attributes of components, effective milling operations are indispensable across industries ranging from aerospace to automotive.
The Impact of CNC Technology on Milling
CNC technology has revolutionized what is the milling process by introducing automation and precision at unprecedented levels. With computer-controlled machines like SYIL CNC, operators can achieve intricate designs and complex shapes with minimal manual intervention. The impact of this technology extends beyond mere efficiency; it enhances accuracy while reducing waste and production time.
As we explore what are the five steps in the milling process within a CNC framework, it's clear that each step benefits from advanced programming capabilities. This evolution not only streamlines operations but also elevates output quality significantly compared to traditional methods.
Future Trends in Milling Operations
Looking ahead, several trends are shaping the future of milling operations that could redefine industry standards. Innovations such as smart manufacturing systems will likely enhance what is the process of milling through real-time monitoring and adaptive machining techniques. As manufacturers increasingly embrace sustainability practices, eco-friendly materials and processes will become more prevalent within milling applications.
Moreover, advancements in AI-driven technologies will provide insights into optimizing what is the purpose of milling by predicting maintenance needs or suggesting operational adjustments based on data analytics. Ultimately, these developments promise to make future milling operations more efficient while meeting evolving market demands.