Introduction
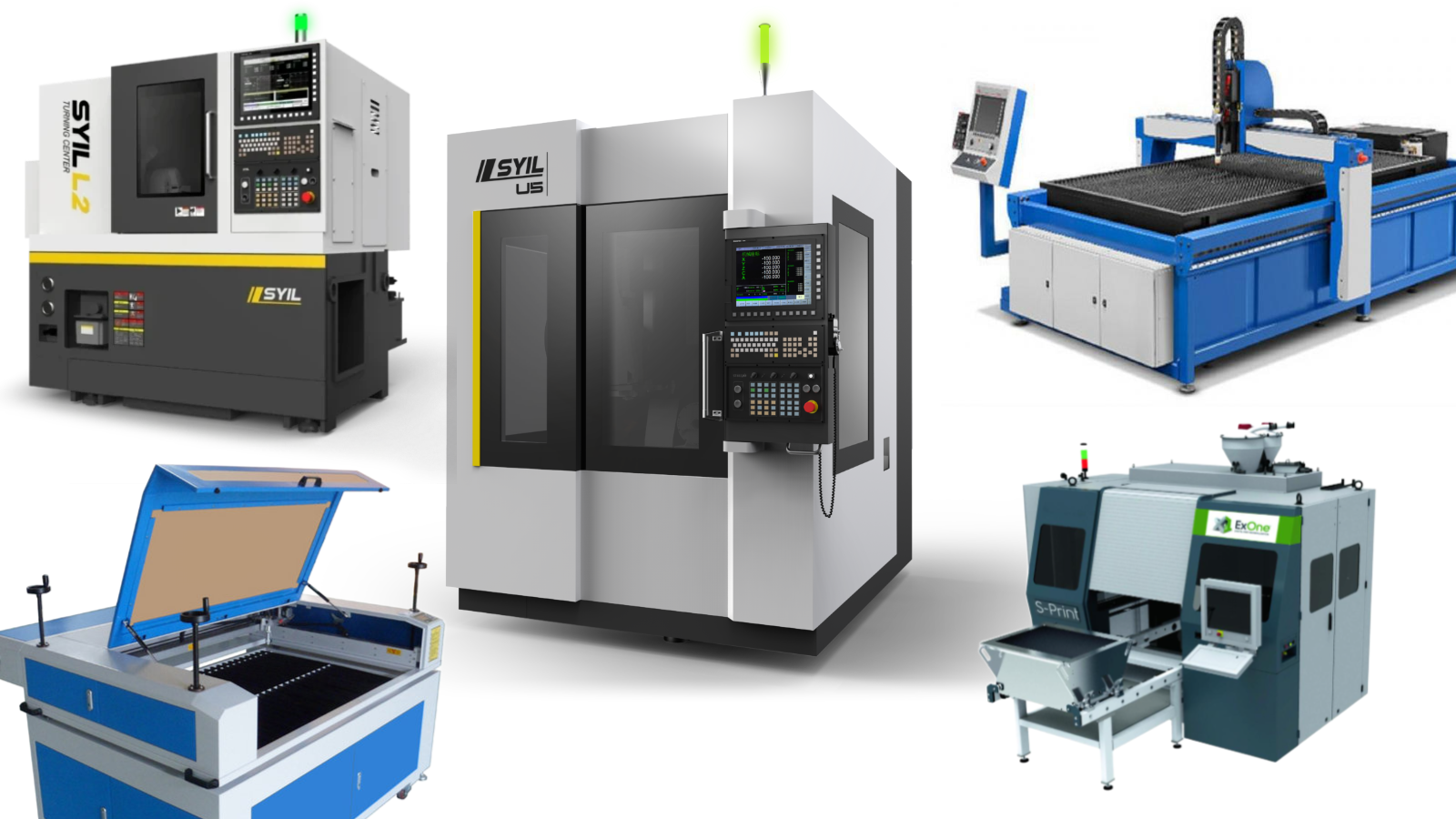
CNC machining has revolutionized the manufacturing landscape, allowing for precision and efficiency in the production of various components. At the heart of this process lies a critical aspect: CNC machining materials. Selecting the right material is not just a technical decision; it can significantly impact the performance, durability, and cost-effectiveness of the final product.
Understanding CNC Machining Materials
CNC machining materials encompass a wide range of options, including metals, plastics, and composites. Each material type has its unique properties that influence how well it can be machined and what applications it is best suited for. Understanding these materials is essential for anyone involved in CNC machining projects to ensure optimal results.
Importance of Material Selection
The choice of material directly affects not only the quality but also the feasibility of any CNC project. For example, different materials respond differently to cutting tools and techniques—leading to variations in precision and finish quality. Therefore, knowing What material is used for CNC machining? becomes a pivotal question that guides designers and engineers in their decision-making process.
Key Factors for Choosing Materials
When selecting materials for CNC machining, several factors come into play: hardness, machinability, thermal stability, and cost are just a few examples. Additionally, understanding What materials cannot be CNC machined? helps avoid costly mistakes during production. Ultimately, making informed choices based on these key factors ensures that projects meet both functional requirements and budget constraints.
Common CNC Machining Materials
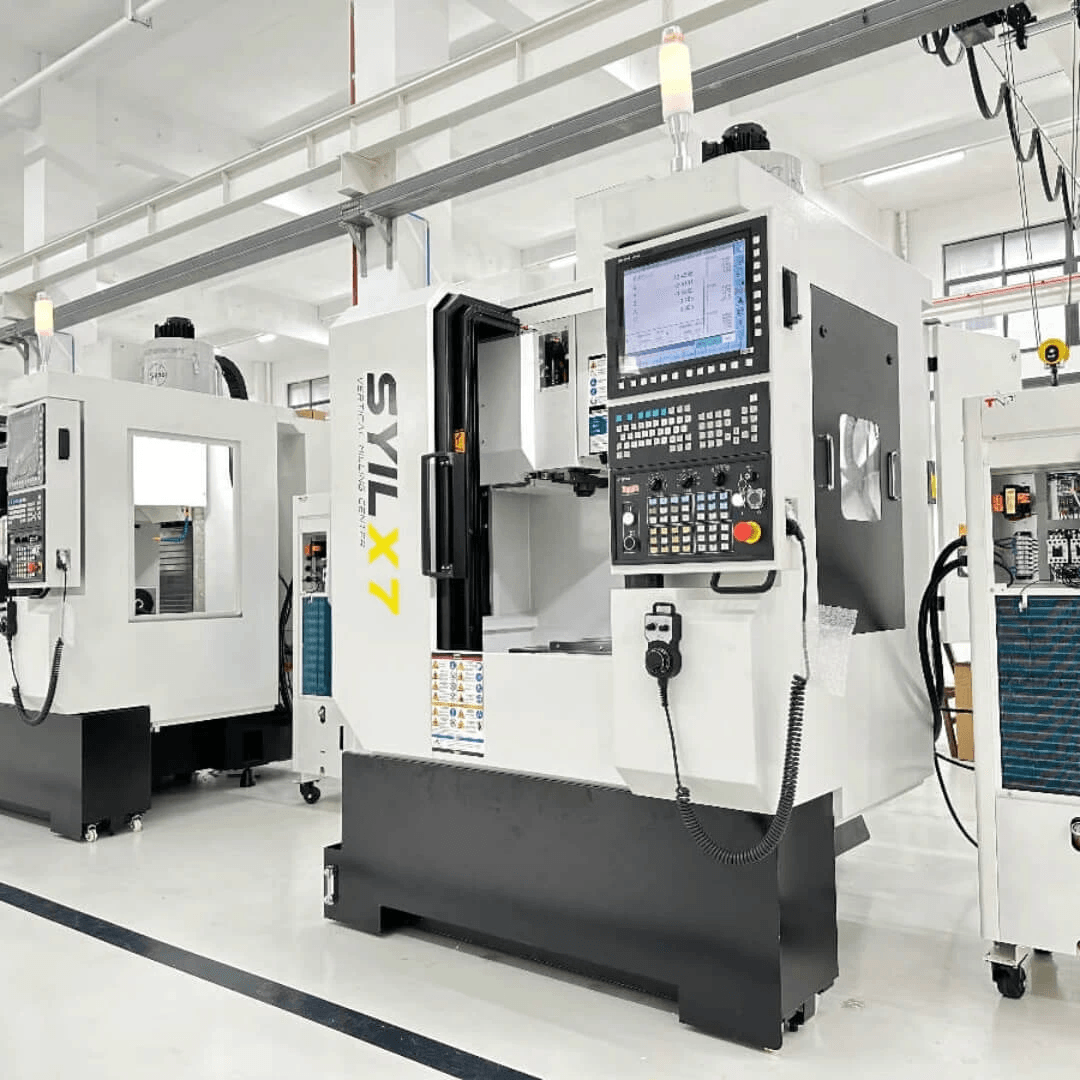
Metals: Aluminum and Steel
Metals are some of the most widely used CNC machining materials due to their strength and durability. Aluminum is favored for its lightweight nature and excellent machinability, making it ideal for intricate designs and high-speed applications. On the other hand, steel provides superior hardness and wear resistance, which is essential for components subjected to heavy loads or harsh conditions.
When considering what material is used for CNC machining, aluminum and steel often top the list because they can be easily shaped into precise forms. Their versatility allows them to be utilized in various industries such as automotive, aerospace, and manufacturing. However, one must also consider factors like cost-effectiveness and availability when selecting between these metals.
Plastics: Acrylic and Nylon
Plastics are another category of common CNC machining materials that offer a different set of advantages compared to metals. Acrylic is known for its clarity and aesthetic appeal; it's often used in applications where visual aspects matter, such as display cases or signage. Nylon, on the other hand, boasts exceptional strength-to-weight ratio along with excellent wear resistance, making it suitable for gears or mechanical parts.
In terms of what materials cannot be CNC machined, softer plastics may pose challenges due to their tendency to deform under pressure during cutting processes. Nonetheless, both acrylic and nylon demonstrate good machinability when handled correctly—making them popular choices in prototyping or low-volume production runs. Thus understanding these characteristics can help you select appropriate plastic types for your CNC projects effectively.
Composites: Carbon Fiber and Kevlar
Composites have gained traction in recent years as advanced CNC machining materials due to their outstanding properties such as high strength-to-weight ratios and superior stiffness. Carbon fiber is particularly renowned in industries like aerospace; its lightweight structure allows it to replace heavier metal components without compromising performance. Kevlar also shines in applications requiring toughness combined with flexibility—commonly found in protective gear or specialized equipment.
However, working with composites does require specialized tooling given their unique characteristics; not all machines are equipped to handle these advanced materials efficiently—hence knowing what materials cannot be CNC machined becomes paramount here too! The right choice of composite can lead you down a path towards innovative designs that push boundaries while maintaining structural integrity.
Properties of Materials for CNC Machining
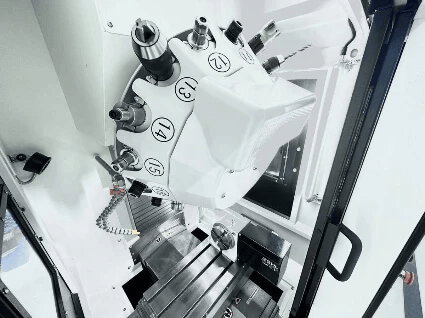
When it comes to CNC machining materials, understanding their properties is crucial for achieving optimal results. Each material has unique characteristics that can significantly influence the machining process, affecting everything from tool wear to the finish quality of the final product. By grasping these properties, manufacturers can make informed decisions about what material is used for CNC machining and enhance productivity.
Hardness and Wear Resistance
Hardness is a fundamental property that determines how well a material can withstand deformation under stress. In CNC machining materials, hardness often correlates with wear resistance; harder materials tend to resist scratches and damage better than softer ones. This is particularly important when considering what materials cannot be CNC machined, as softer materials may degrade too quickly during the machining process, leading to inefficiencies and increased costs.
For example, metals like aluminum offer a good balance of hardness and machinability, making them popular choices in various applications. On the other hand, harder metals such as titanium are more challenging to machine due to their high wear rates on cutting tools. Understanding hardness helps machinists select appropriate tools and speeds for different materials while ensuring longevity in both tools and components.
Machinability and Finishing
Machinability refers to how easily a material can be machined into desired shapes or finishes without compromising its integrity or quality. Different cnc machining materials exhibit varying levels of machinability based on their composition; for instance, carbon steel is generally easier to machine compared to stainless steel due to its lower hardness levels. This leads us back to our query: What are the raw materials for machining? The answer lies in selecting those that not only meet design specifications but also facilitate efficient processing.
Finishing processes also play a vital role in achieving the desired surface quality after machining operations are completed. Some plastics like acrylic provide excellent finishing capabilities with minimal post-processing required, while metals might need additional polishing or coating steps for optimal aesthetics or performance. Therefore, understanding machinability helps manufacturers streamline production processes while maintaining high-quality output.
Thermal Stability and Conductivity
Thermal stability refers to how well a material maintains its properties under varying temperature conditions—an essential factor in CNC machining environments where heat generation is common during cutting operations. Materials with good thermal stability minimize warping or distortion during processing, which ties back into our earlier discussion about what materials cannot be CNC machined effectively due to these limitations.
Additionally, thermal conductivity plays a significant role in dissipating heat generated by cutting tools during operation; higher conductivity can lead to better heat management and reduced tool wear rates. Metals like copper are known for their superior thermal conductivity but may not always be ideal due to other factors such as cost or strength requirements in specific applications. Balancing thermal properties with other characteristics helps ensure successful outcomes when working with various cnc machining materials.
What Material is Used for CNC Machining?
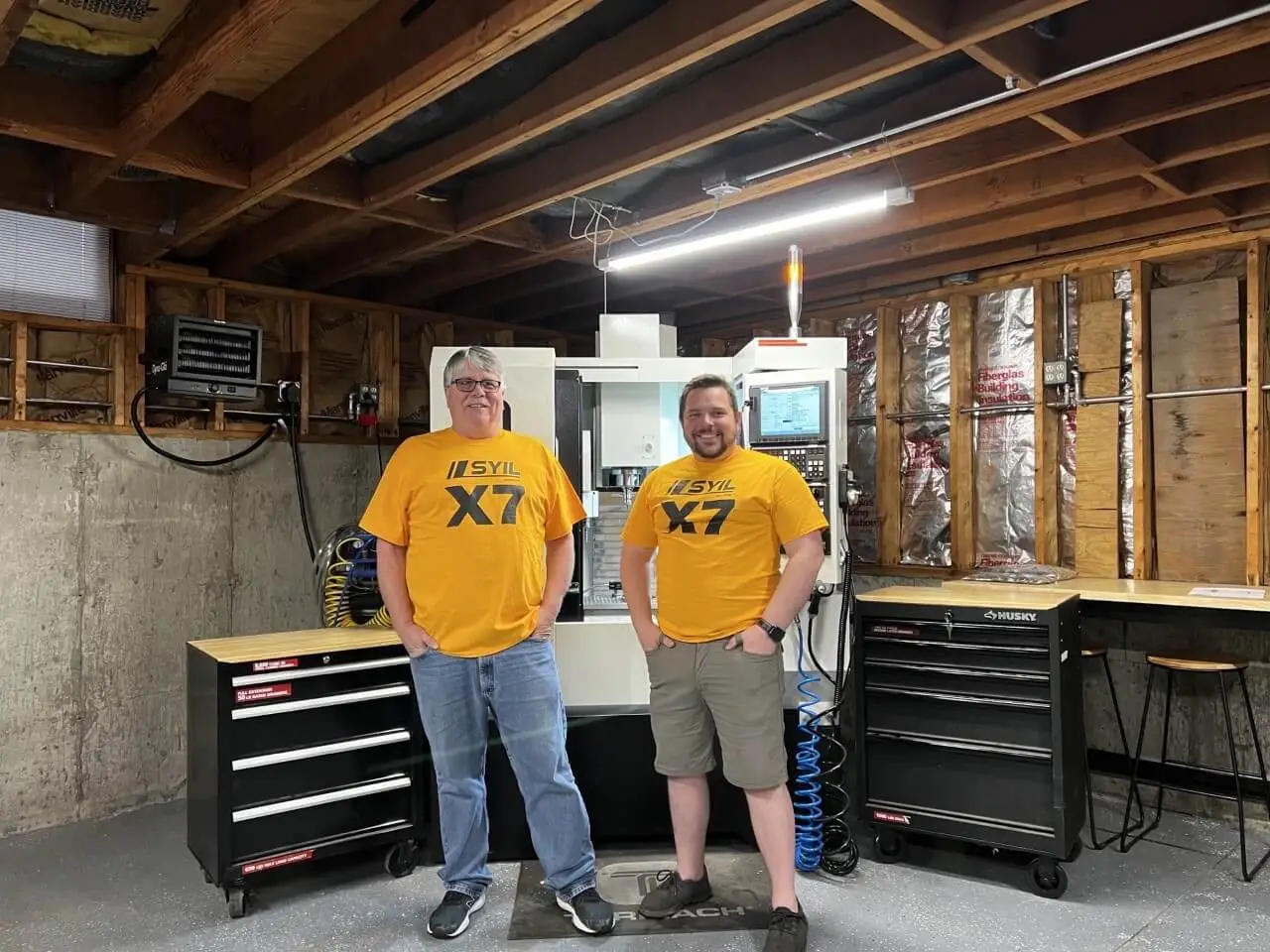
When diving into the world of CNC machining materials, it’s essential to understand the various types that are commonly utilized in this process. The choice of material can significantly influence the final product's performance, durability, and cost-effectiveness. So, what material is used for CNC machining? Let’s explore the different categories of materials that are popular in CNC applications.
Metal Alloys in CNC Applications
Metal alloys stand at the forefront of CNC machining materials due to their strength and versatility. Common alloys like aluminum and steel are favored for their machinability, allowing for intricate designs while maintaining structural integrity. When considering what material is used for CNC machining, metal alloys often take center stage because they can be tailored to meet specific requirements through alloying elements.
Aluminum alloys are particularly popular in industries such as aerospace and automotive due to their lightweight properties combined with excellent corrosion resistance. Steel alloys, on the other hand, offer superior hardness and toughness, making them ideal for heavy-duty applications where durability is critical. Understanding these characteristics helps manufacturers choose the right metal alloy that aligns with their project needs.
Plastic Types for CNC Projects
Plastics also play a significant role among cnc machining materials, offering unique benefits that metals may not provide. Common plastic types like acrylic and nylon are frequently used due to their ease of machining and lightweight nature. In answering what material is used for CNC machining, plastics often emerge as a favorable option when flexibility or aesthetic appeal is paramount.
Acrylic is known for its clarity and ability to mimic glass while being much lighter and shatter-resistant—making it a go-to choice for signage or display components. Nylon offers excellent wear resistance and low friction properties, making it suitable for gears or components requiring smooth operation under stress. These plastic types expand the possibilities within cnc projects by providing alternatives that can meet specific functional needs without sacrificing quality.
Specialty Materials: Ceramics and Composites
For those looking beyond traditional options, specialty materials such as ceramics and composites make an interesting addition to cnc machining materials discussions. Ceramics are prized for their hardness and thermal stability but can be challenging to machine; however, they excel in high-temperature environments where metals might fail. This leads us back to our query about what material is used for CNC machining—ceramics hold a niche position due to their unique properties.
Composites like carbon fiber offer exceptional strength-to-weight ratios along with resistance to environmental factors such as moisture or chemicals—ideal qualities in aerospace or automotive industries where performance matters most. While these specialty materials present some challenges during processing (often requiring specialized tools), they open up new avenues in design innovation by combining lightness with strength effectively.
In conclusion, understanding what materials cannot be CNC machined helps delineate boundaries within this innovative field while appreciating how diverse options exist among cnc machining materials available today—from robust metal alloys through versatile plastics down to cutting-edge composites—each brings its own set of characteristics vital for specific applications.
What Materials Cannot Be CNC Machined?
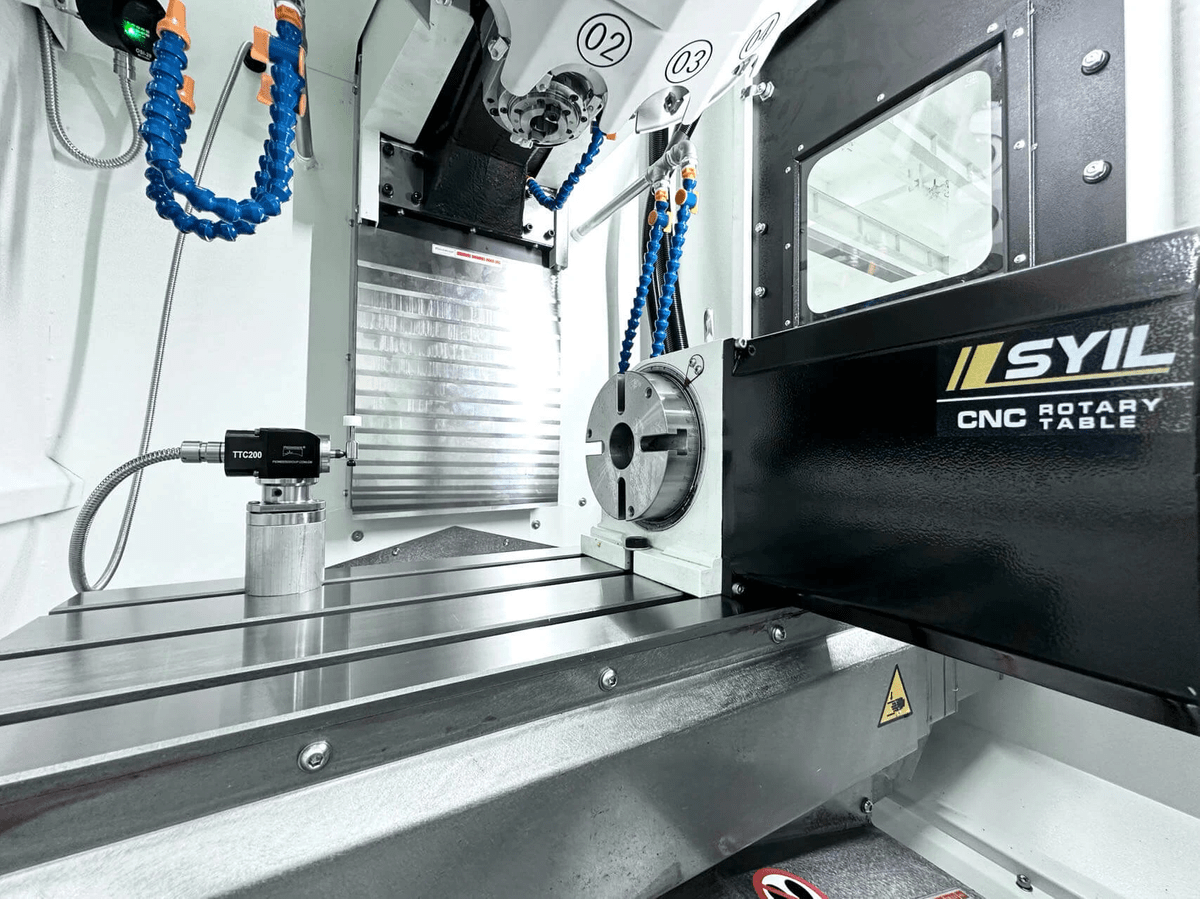
When diving into the world of CNC machining materials, it’s crucial to recognize that not all substances are created equal. Some materials simply don’t play well with the precise nature of CNC processes. Understanding what materials cannot be CNC machined can save time, resources, and a lot of frustration.
Soft Materials and Their Limitations
Soft materials, such as certain types of foam or soft plastics, often pose significant challenges in CNC machining. Their malleability can lead to issues like tool wear or deformation during the cutting process. Additionally, these materials may not hold fine tolerances, making them unsuitable for projects where precision is paramount—after all, nobody wants a wonky part!
Difficult-to-Machine Metals
When asking What material is used for CNC machining?, one might think metals are always a safe bet; however, some metals are notoriously difficult to machine. Titanium and hardened steel are prime examples—they require specialized tools and techniques due to their toughness and tendency to strain cutting tools excessively. If you’re planning a project involving these metals, be prepared for longer machining times and possibly higher costs.
Materials Prone to Warping
Warping is the nemesis of any machinist working with CNC machining materials; it can ruin an otherwise perfect project in no time flat! Materials like wood or certain plastics can warp due to changes in temperature or humidity during the machining process. When considering What are the raw materials for machining?, it's essential to select those that maintain stability under varying conditions—because nobody wants their meticulously crafted piece turning into a pretzel!
Essential CNC Machine Components
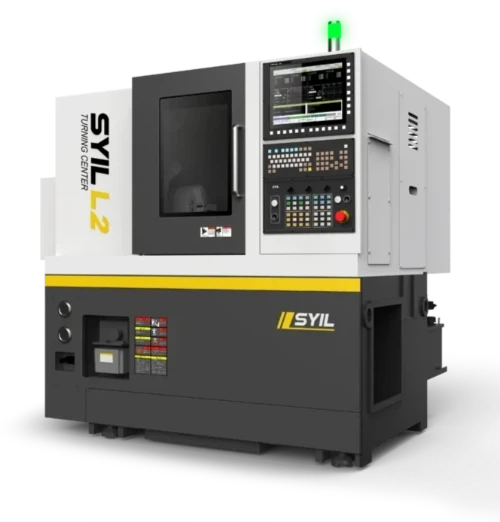
When diving into the world of CNC machining, understanding the essential components of a CNC machine is crucial for optimizing performance and material selection. Each part plays a pivotal role in determining how effectively various cnc machining materials can be manipulated. Whether you're working with metals, plastics, or composites, knowing what makes up a CNC machine will help you make informed decisions about your projects.
Key Parts of a CNC Machine
What are the 7 major parts of a CNC machine? At the heart of any CNC setup are key components such as the control unit, drive motors, spindle, tool holder, work table, coolant system, and frame. The control unit is like the brain of the operation—it interprets design files and sends commands to other parts. The drive motors provide movement along multiple axes while the spindle holds and rotates cutting tools to shape raw materials into desired forms.
The work table supports your cnc machining materials during processing and can often be adjusted for different sizes and shapes. The coolant system is vital for maintaining optimal temperatures during machining processes to prevent overheating and ensure precision cuts. Understanding these components helps in selecting appropriate materials; for instance, harder metals may require more robust spindles compared to softer plastics.
Importance of the SYIL X5 Mini CNC Machine
Among various options available in the market today, the SYIL X5 Mini CNC machine stands out due to its compact size yet powerful capabilities. This machine is particularly suited for small workshops or hobbyists who are exploring what material is used for CNC machining without needing industrial-grade equipment. Its versatility allows users to work with an array of cnc machining materials including aluminum, plastics like acrylic or nylon, and even some composite materials.
The SYIL X5's user-friendly interface makes it accessible for beginners while still offering advanced features that experienced machinists appreciate. With its precise movements and reliability in handling different types of raw materials for machining projects—this mini CNC machine proves that good things come in small packages! As you consider which cnc machining materials to use in your projects, this machine could very well be your best friend.
How Components Affect Material Selection
The interplay between various components of a CNC machine significantly impacts which cnc machining materials can be effectively utilized. For instance, if you're planning on using harder metals or specialty alloys that fall under What materials cannot be CNC machined?, you'll need robust spindles and high-quality cutting tools capable of handling such stressors without failing prematurely. Conversely, softer plastics might require less intense setups that focus more on speed than on power.
Additionally, some machines come equipped with advanced coolant systems that allow them to handle heat-sensitive materials better than others; thus influencing your choices when deciding what material is used for CNC machining tasks at hand. It's essential also to consider how certain raw materials respond under different conditions—some may warp easily while others remain stable even under high-temperature scenarios commonly encountered during milling or drilling processes.
In conclusion, understanding these essential components not only enhances your overall experience but also empowers you with knowledge about which cnc machining materials will yield successful results based on your specific needs!
Conclusion
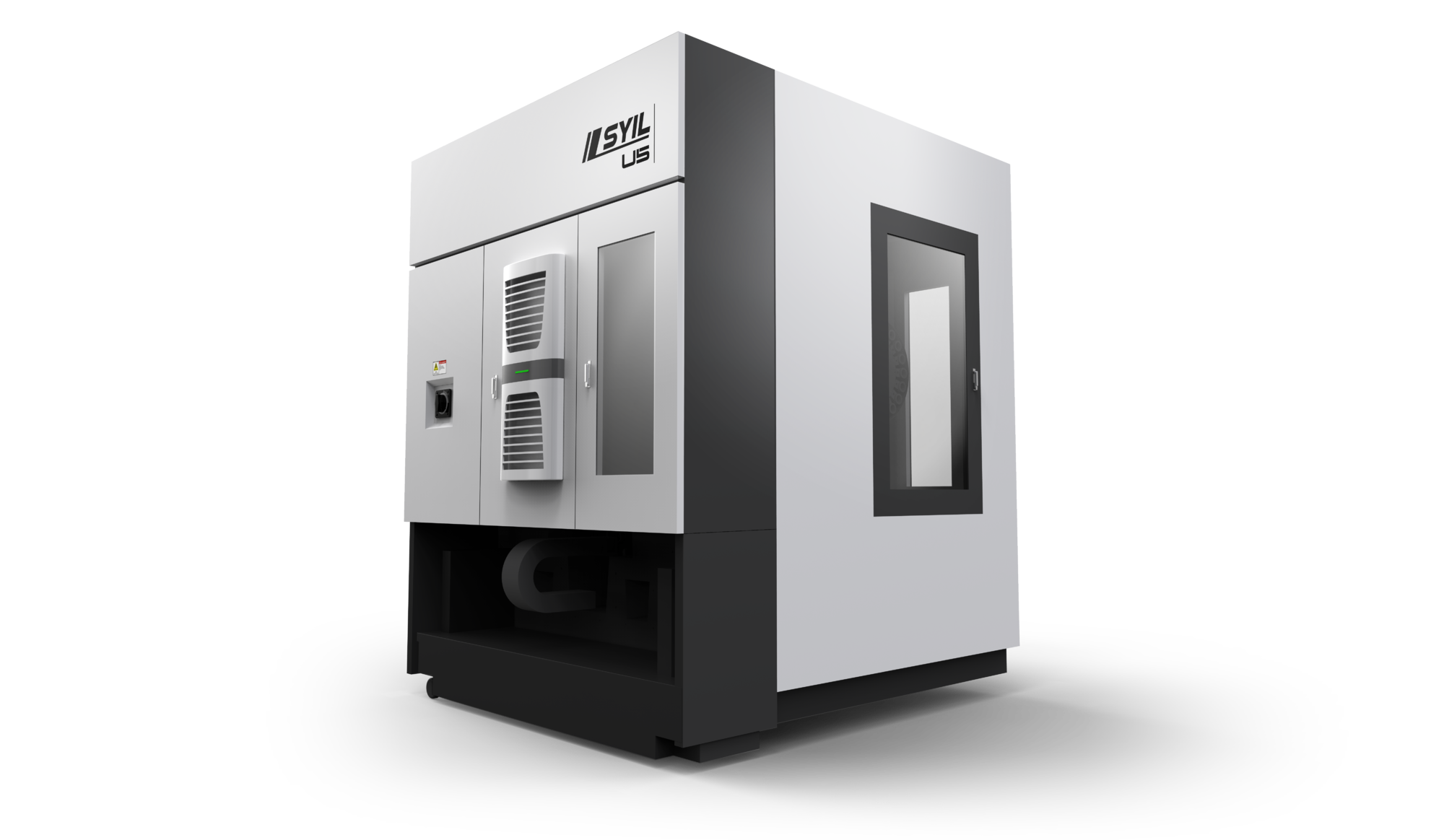
In the ever-evolving world of CNC machining, understanding the right materials is key to achieving optimal results. The selection of CNC machining materials can significantly impact the performance and durability of the final product. By making informed material choices, manufacturers can enhance efficiency and reduce waste, ultimately leading to better outcomes.
Making Informed Material Choices
When it comes to CNC machining, knowing What material is used for CNC machining? is essential for success. From metals like aluminum and steel to plastics such as acrylic and nylon, each material has its own unique properties that influence machinability and end-use applications. Additionally, understanding What materials cannot be CNC machined? helps avoid costly mistakes; soft materials or those prone to warping may not yield satisfactory results.
Choosing the right raw materials for machining involves considering factors like hardness, thermal stability, and machinability. For instance, while some metals are easy to machine, others may require specialized tools or techniques due to their hardness or brittleness. By weighing these considerations carefully against project requirements, manufacturers can ensure they select suitable CNC machining materials that meet both functional and aesthetic needs.
The Role of CNC Machine in Design
The design process in CNC machining heavily relies on the capabilities of the machine itself—this includes knowing What are the 7 major parts of a CNC machine? These components work together seamlessly to transform raw materials into intricate designs with precision. Understanding how each part influences material selection can lead to more effective designs tailored for specific applications.
For instance, a robust spindle may allow for higher speeds when working with harder metals while ensuring smoother finishes on softer plastics. As designers explore new shapes and functionalities in their projects, they must also consider how different cnc machining materials will respond during production processes involving these critical machine components. This synergy between design intent and machine capability is vital for achieving high-quality results.
Future Trends in CNC Machining Materials
Looking ahead, we see exciting trends emerging in the realm of cnc machining materials that promise innovation across various industries. Advanced composites and specialty alloys are gaining traction due to their lightweight yet durable characteristics—perfect for aerospace applications or automotive parts where performance is paramount. Furthermore, biocompatible plastics are becoming increasingly popular as industries shift towards sustainable practices without compromising quality.
As technology advances further into automation and smart manufacturing solutions emerge, we can expect even greater flexibility in material usage within CNC processes. Innovations such as 3D printing integration with traditional cnc machines will expand possibilities beyond conventional limits regarding what can be machined effectively from various raw materials for machining purposes today. Embracing these trends will ensure manufacturers remain competitive while pushing boundaries in design possibilities.