Introduction
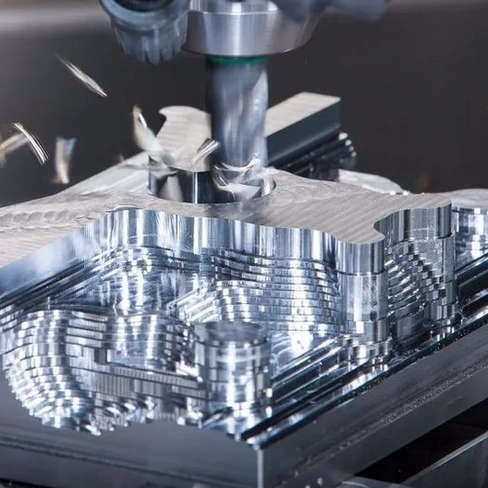
CNC titanium parts have gained significant popularity in various industries due to their strength, lightweight properties, and resistance to corrosion. However, the complexity involved in producing custom titanium parts can be daunting for manufacturers. Understanding the intricacies of titanium machining is essential for achieving high-quality results while navigating its unique challenges.
Understanding CNC Titanium Parts Complexity
Titanium is known for its toughness and ability to withstand extreme conditions, making it an excellent choice for aerospace, medical, and automotive applications. However, these same qualities contribute to questions like Can titanium be CNC machined? The answer is yes, but it requires specialized techniques and tools tailored specifically for this resilient metal.
Key Factors Affecting Titanium Machining
Several key factors play a crucial role in successful titanium machining. Firstly, understanding why machining titanium is difficult helps identify potential pitfalls during production; its low thermal conductivity can lead to excessive heat generation at the cutting edge if not managed properly. Additionally, selecting appropriate cutting tools is vital—what is the best material to cut titanium with? Carbide tools are often recommended due to their durability and resistance against wear.
The Role of Technology in Production
The evolution of technology has transformed how we approach CNC titanium parts production. Advanced software solutions facilitate precise programming and simulation of machining processes, ensuring optimal outcomes with minimal waste. Furthermore, innovations in tool design and manufacturing techniques enhance efficiency and accuracy when creating custom titanium parts that meet specific requirements while overcoming challenges associated with this unique material.
Importance of Selecting the Right CNC Machine
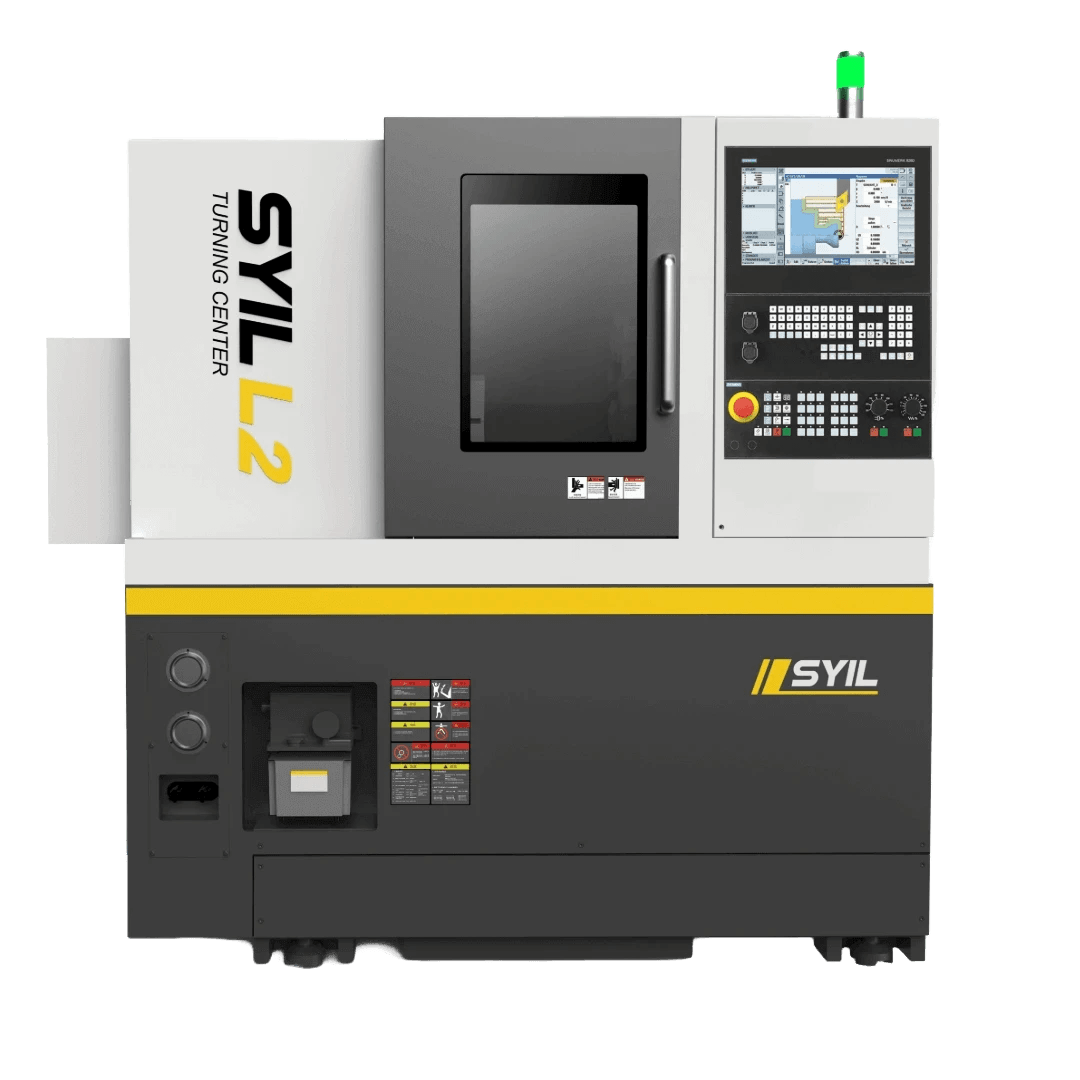
Selecting the right CNC machine is crucial for producing high-quality CNC titanium parts. The intricacies involved in machining titanium require machines that can handle its unique properties, ensuring precision and efficiency. With a variety of options available, understanding the performance and capabilities of different machines can make all the difference in custom titanium parts production.
Evaluating Performance of SYIL X5 Mini CNC
The SYIL X5 Mini CNC is a compact powerhouse designed for precision machining, making it an excellent choice for fabricating CNC titanium parts. This machine boasts impressive rigidity and stability, which are essential when tackling tough materials like titanium. When evaluating whether can titanium be CNC machined? the SYIL X5 proves its worth with its ability to maintain tight tolerances and deliver consistent results.
Moreover, this machine’s user-friendly interface and advanced features allow operators to optimize their workflow seamlessly. Its capability to handle various cutting tools ensures that users can select what is best suited for their specific projects, including those involving challenging materials like titanium alloys. Ultimately, investing in a reliable machine like the SYIL X5 can significantly enhance your production quality while reducing downtime.
Versatility for Custom Titanium Parts Production
One standout feature of modern CNC machines is their versatility—especially when it comes to custom titanium parts production. With adjustable settings and multiple tooling options, these machines can accommodate a wide range of designs and specifications without compromising on quality or speed. This flexibility allows manufacturers to cater to diverse client needs while maintaining efficiency in their operations.
Additionally, customizability extends beyond just part design; it encompasses various applications across industries such as aerospace, automotive, and medical devices where lightweight yet strong components are essential. The ability to produce tailored solutions makes selecting a versatile CNC machine even more critical when working with demanding materials like titanium. After all, what is the best material to cut titanium with? often depends on how well your chosen machine adapts to different cutting tools and techniques.
Comparing CNC Machines for Titanium
When comparing different CNC machines for machining titanium alloys, it's essential to consider several key factors: performance specifications, cost-effectiveness, and user-friendliness among them. Not all machines are created equal; some may excel at speed but fall short on accuracy or vice versa—especially important given that why is machining titanium difficult? often stems from its strength-to-weight ratio and heat sensitivity during cutting processes.
Moreover, understanding which materials cannot be CNC machined will also inform your decision-making process when selecting machinery capable of handling specific tasks effectively without causing tool wear or breakage over time. By carefully weighing these considerations against your project requirements—be it prototyping or large-scale production—you'll ensure you choose a machine that's not only suitable but also enhances your overall output quality in crafting exceptional cnc titanium parts.
Challenges in Machining Titanium Alloys
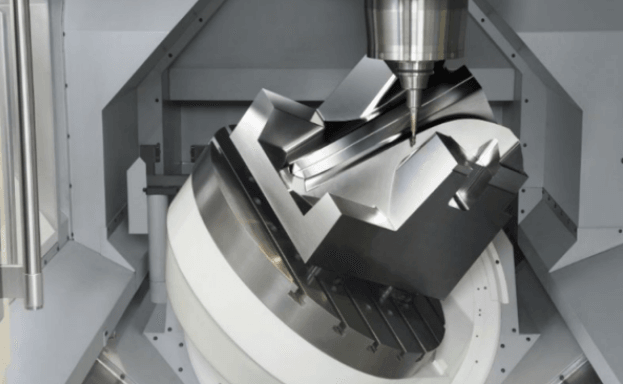
Machining titanium alloys presents unique challenges that can perplex even the most seasoned machinists. The material's properties, such as its strength-to-weight ratio and resistance to corrosion, make it a popular choice for various applications, including aerospace and medical devices. However, these same properties contribute to the difficulties faced when producing custom titanium parts through CNC machining.
Why is Machining Titanium Difficult?
Why is machining titanium difficult? The answer lies in its physical characteristics. Titanium has a low thermal conductivity, which means that heat generated during cutting tends to stay localized at the cutting edge of the tool rather than dissipating quickly. This leads to rapid tool wear and potential breakage if not managed properly. Additionally, titanium’s high strength makes it more resistant to cutting forces, requiring more power and precision from CNC machines.
Identifying the Best Tools for Cutting Titanium
When considering what is the best material to cut titanium with, it's essential to focus on tool selection. Carbide tools are often recommended due to their hardness and ability to withstand high temperatures during machining processes. Furthermore, specialized coatings such as TiAlN (Titanium Aluminum Nitride) can enhance tool performance by reducing friction and improving durability when working with CNC titanium parts.
Understanding Material Properties and Limitations
To effectively tackle challenges in machining titanium alloys, understanding material properties is crucial. Titanium exhibits unique characteristics like low density combined with high tensile strength; this makes it ideal for applications where weight savings are critical but also complicates the machining process itself. Moreover, recognizing what materials cannot be CNC machined helps avoid costly mistakes—materials that are too brittle or soft may not hold up well against titanium's robust nature during production.
Technology and Techniques for Optimizing Production
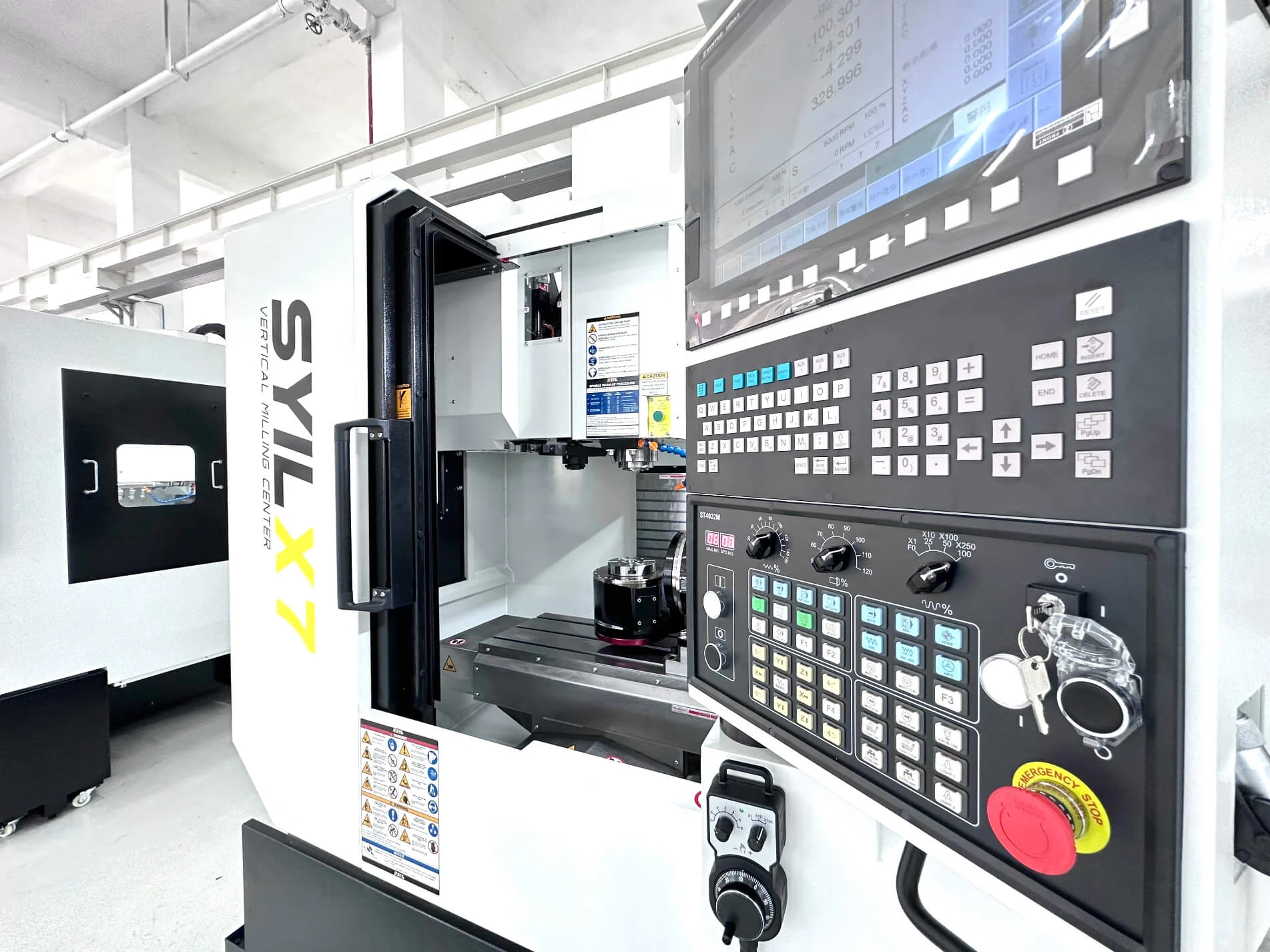
In the world of CNC titanium parts production, leveraging advanced technology and innovative techniques is crucial for achieving high-quality outcomes. The unique properties of titanium make it a challenging material to work with, prompting manufacturers to adopt cutting-edge methods for effective machining. By employing these techniques, companies can enhance their production capabilities while addressing the complexities associated with custom titanium parts.
Innovative CNC Techniques for Titanium Parts
Techniques such as high-speed machining and adaptive control systems allow for more efficient removal of material while minimizing the risk of deformation or tool wear. Furthermore, utilizing multi-axis CNC machines enables manufacturers to create intricate designs that would be nearly impossible with traditional methods—making them indispensable in industries like aerospace and medical device manufacturing.
The question often arises: can titanium be CNC machined? The answer is a resounding yes, but only when the right techniques are employed. For instance, using peck drilling instead of continuous drilling can significantly reduce heat buildup, which is one reason why machining titanium is notoriously difficult. By implementing these innovative approaches, manufacturers can ensure that they produce high-quality components without compromising on precision or durability.
Utilizing Software for Enhanced Precision
In addition to innovative machining techniques, software plays a vital role in enhancing precision during the production of CNC titanium parts. Advanced CAD/CAM software allows engineers to design complex geometries and convert them into machine-readable code seamlessly. This not only streamlines the production process but also ensures that every cut made on the titanium aligns perfectly with design specifications.
Moreover, simulation software enables manufacturers to visualize how their machines will perform before even touching the material—essential when dealing with tough metals like titanium. This foresight helps identify potential issues early on and allows teams to adjust parameters accordingly before actual machining begins. Ultimately, utilizing cutting-edge software solutions leads to improved accuracy in creating custom titanium parts while reducing waste and saving time.
Importance of Tool Path Optimization
Tool path optimization is another critical aspect when it comes to effective CNC machining of titanium alloys. Properly optimized tool paths minimize unnecessary movements and reduce cycle times significantly—key factors in increasing productivity without sacrificing quality in custom titanium parts production. When tooling paths are meticulously planned out based on part geometry and material characteristics, they help mitigate challenges such as excessive tool wear or breakage.
But why is machining titanium difficult? One primary reason lies in its propensity for work hardening during cutting operations; thus making tool path optimization even more essential than ever before. Choosing what materials cannot be CNC machined becomes easier too; understanding how different tools interact with various types of materials allows operators to select optimal options tailored specifically for working with hard-to-machine metals like titanium.
In conclusion, embracing innovative techniques alongside advanced software solutions lays a solid foundation for optimizing production processes related to CNC titanium parts manufacturing—ensuring businesses remain competitive while navigating this challenging landscape successfully.
Common Mistakes in CNC Machining Titanium
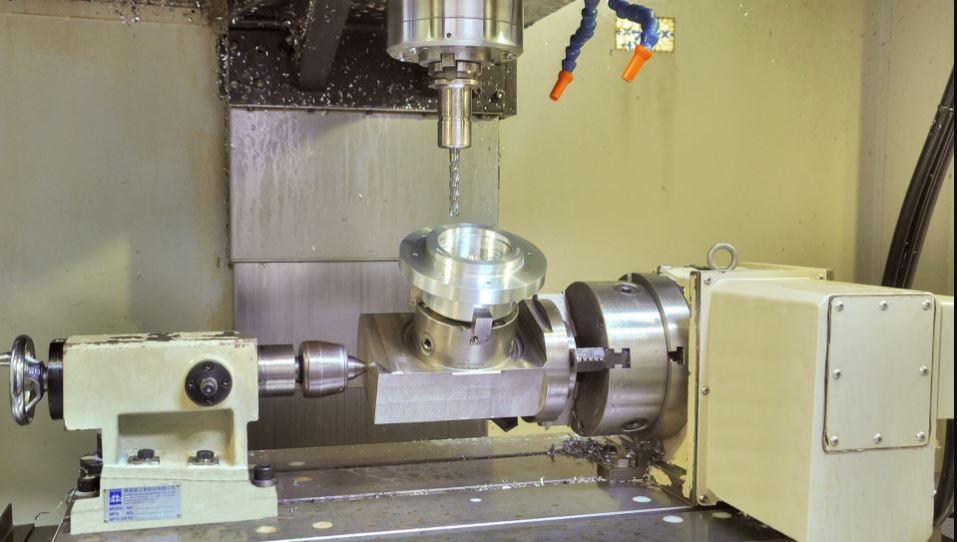
What Materials Cannot Be CNC Machined?
Not all materials play nice with CNC machining, especially when it comes to titanium alloys. While titanium is a popular choice due to its strength-to-weight ratio, certain materials like ceramics or some high-density plastics cannot be effectively machined using traditional CNC methods. This leads to the question: Can titanium be CNC machined? The answer is a resounding yes! However, it's essential to know what other materials might cause issues during the process.
Certain metals like lead or soft aluminum can also pose challenges when mixed with titanium in a machining environment. These materials may not hold up well against the rigidity and toughness of titanium, leading to tool wear and ineffective cutting processes. Understanding which materials cannot be CNC machined alongside titanium helps streamline production and maintain quality.
Avoiding Tool Wear and Breakage
Machining titanium is notoriously difficult; it requires specialized tools that can withstand high temperatures generated during the cutting process. One common mistake is using standard cutting tools instead of those specifically designed for titanium machining, which leads to premature tool wear or even breakage. To combat this issue, manufacturers should invest in high-quality carbide or ceramic tools tailored for cutting tough metals.
Another factor contributing to tool wear is improper feed rates and spindle speeds during operation; if these settings are not optimized for the specific type of custom titanium parts being produced, it can result in excessive friction and heat buildup. It's crucial to find that sweet spot between speed and efficiency—too fast could lead you down a path of destruction (for your tools), while too slow could make production painfully sluggish.
Lastly, regular maintenance checks on machinery are vital in preventing unexpected breakdowns that could halt production altogether. Ensuring your equipment is running smoothly not only extends tool life but also boosts overall productivity when working with demanding materials like titanium.
Learning from Industry Best Practices
Learning from industry best practices can significantly improve outcomes in CNC machining operations involving titanium alloys. One key takeaway is adopting a systematic approach toward selecting appropriate tooling based on specific project requirements—what works best for one set of custom titanium parts may not suit another design perfectly! This emphasizes the importance of research before diving into production.
Additionally, staying updated on technological advancements related to CNC machines will help keep operations efficient while minimizing mistakes associated with outdated techniques or equipment choices. Implementing software solutions that enhance precision during design phases allows engineers greater flexibility when creating intricate designs from durable metals like titanium.
Finally, fostering an environment where knowledge sharing among team members occurs regularly helps everyone stay informed about what works best—and what doesn’t—in terms of processing various materials including our favorite: cnc titanium parts!
Future Trends in CNC Titanium Parts Production
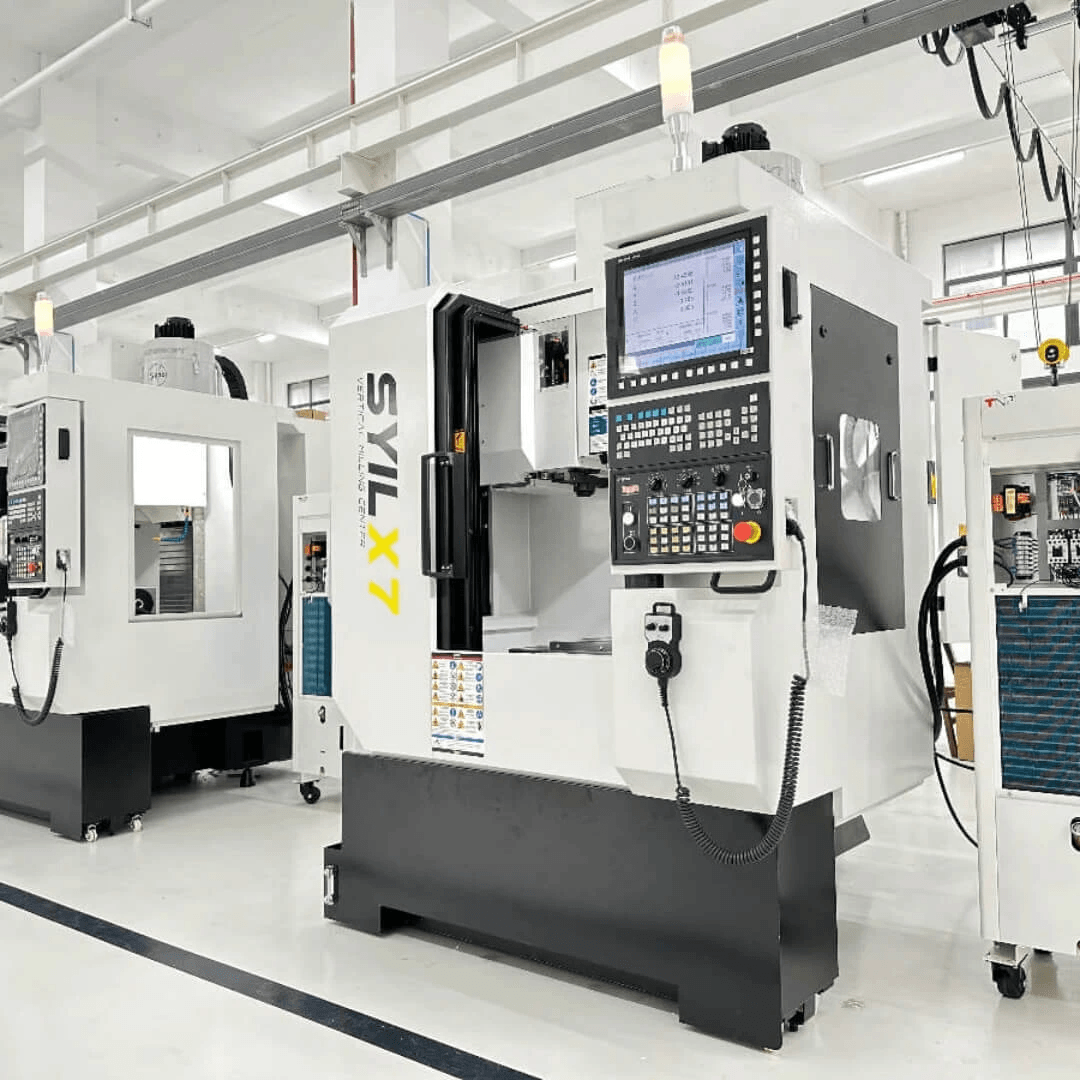
The landscape of CNC titanium parts production is evolving rapidly, driven by technological advancements and shifting market demands. Manufacturers are increasingly exploring innovative techniques to enhance efficiency and precision in creating custom titanium parts. As industries seek to optimize their operations, understanding these trends becomes essential for staying competitive.
Advancements in Titanium Machining Technology
Recent advancements in titanium machining technology have revolutionized the production of CNC titanium parts. New cutting tools and techniques are being developed that specifically address the question: Can titanium be CNC machined? These innovations allow for faster machining speeds, improved surface finishes, and greater accuracy, making it easier to tackle the challenges associated with why machining titanium is difficult.
Moreover, the introduction of high-speed machining centers equipped with advanced cooling systems has significantly reduced tool wear and breakage during the cutting process. This not only extends the lifespan of tools but also minimizes downtime—a critical factor when producing custom titanium parts at scale. As technology continues to progress, manufacturers can expect even more efficient solutions tailored for handling tough materials like titanium.
The Rise of Customization in Manufacturing
In today's manufacturing landscape, customization is becoming a key driver for success across various sectors. The demand for custom titanium parts has surged as companies look to differentiate their products and meet specific client needs. This trend reflects a broader shift towards personalized solutions that can provide competitive advantages in industries ranging from aerospace to medical devices.
With advancements in CNC technology, manufacturers can now produce highly intricate designs without sacrificing quality or efficiency. This capability allows them to respond quickly to market demands while ensuring that each component meets stringent specifications—answering queries like what is the best material to cut titanium with? Ultimately, embracing customization not only enhances product offerings but also fosters customer loyalty through tailored solutions.
Sustainability Practices in Titanium Machining
Sustainability has emerged as a crucial consideration within the realm of CNC machining, including when working with challenging materials like titanium. Manufacturers are increasingly adopting sustainable practices aimed at reducing waste and energy consumption during production processes. By implementing environmentally friendly methods, they not only comply with regulations but also appeal to eco-conscious consumers who prioritize sustainable sourcing.
One effective practice involves recycling scrap metal generated during the machining process—ensuring that nothing goes to waste while lowering material costs over time. Additionally, utilizing advanced software for optimizing tool paths can lead to significant reductions in energy usage throughout production runs. As sustainability becomes more ingrained within manufacturing culture, it will play an essential role in shaping future trends within CNC titanium parts production.
Conclusion
In the ever-evolving landscape of CNC titanium parts production, understanding the intricacies of machining titanium is essential for success. By implementing strategic solutions and embracing technological advancements, manufacturers can overcome the unique challenges presented by this remarkable metal. The future of custom titanium parts lies in innovation, precision, and efficiency.
Solutions for Effective CNC Titanium Machining
To achieve effective CNC titanium machining, selecting the right tools and techniques is paramount. High-performance cutting tools specifically designed for titanium can significantly enhance productivity while minimizing common issues like tool wear and breakage. Additionally, employing advanced software solutions can streamline processes and ensure that custom titanium parts are produced with outstanding accuracy.
Moreover, it’s crucial to understand why machining titanium is difficult due to its unique material properties—its strength-to-weight ratio makes it a challenging candidate for traditional machining methods. By investing in training and resources tailored to these specific challenges, manufacturers can elevate their capabilities and optimize their production processes. Ultimately, a proactive approach to identifying what materials cannot be CNC machined will help avoid costly mistakes and ensure successful outcomes.
Embracing Technology for Better Results
The integration of cutting-edge technology into CNC machining practices has revolutionized the production of custom titanium parts. Innovations such as automated tool changers and real-time monitoring systems allow for greater efficiency while reducing human error during the manufacturing process. With these advancements at their disposal, manufacturers can achieve higher levels of precision in their work.
Additionally, utilizing sophisticated software solutions enhances design capabilities by allowing engineers to simulate machining processes before actual production begins. This not only saves time but also helps in identifying potential challenges early on—addressing questions like Can titanium be CNC machined? with confidence? As technology continues to evolve, staying updated on trends will empower businesses to remain competitive in an increasingly demanding market.
Navigating the Challenges of Titanium Production
Navigating the complexities associated with producing cnc titanium parts requires a multifaceted approach that addresses both technical and operational hurdles. Understanding why machining titanium is difficult provides insight into necessary adjustments in technique or tooling choices—like determining what is the best material to cut titanium with effectively. This knowledge allows manufacturers to create strategies that mitigate risks associated with this resilient metal.
Furthermore, fostering a culture of continuous improvement within organizations encourages teams to learn from industry best practices while avoiding common pitfalls such as improper tooling or inadequate machine settings. By sharing insights on what materials cannot be CNC machined alongside practical experiences from past projects, companies can build a robust framework for tackling future endeavors confidently. Ultimately, embracing these strategies will pave the way for sustainable growth within the realm of custom titanium parts manufacturing.