Introduction
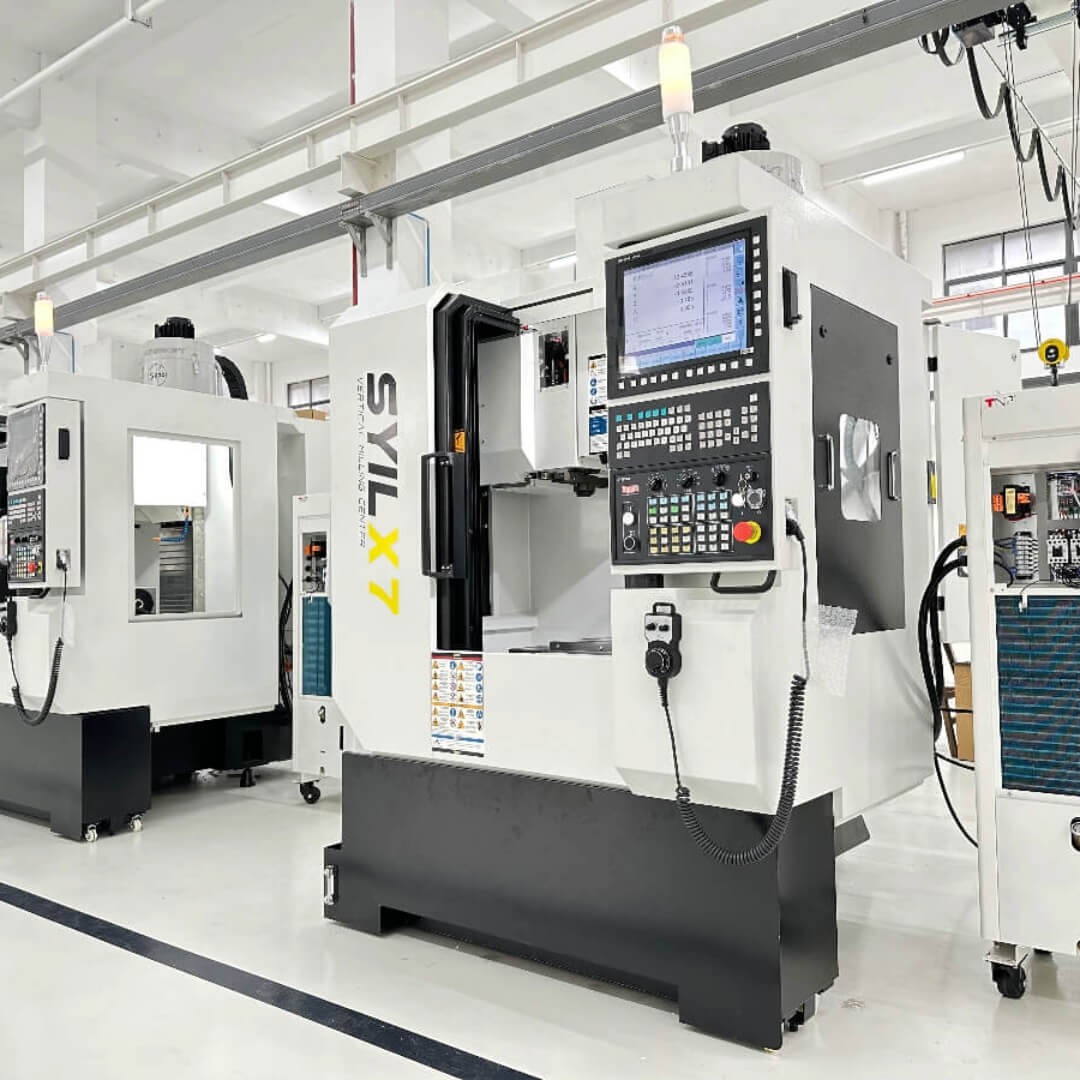
When it comes to aerospace CNC machined parts, precision is key. These parts are essential for the functioning of aircraft and must meet strict standards for quality and accuracy. In the world of aerospace machining, companies rely on advanced technology to ensure that every component meets these rigorous requirements. This is where SYIL CNC machines play a crucial role, providing the precision and reliability needed for aerospace CNC machining projects.
Understanding Aerospace CNC Machined Parts
Aerospace CNC machined parts are components used in the construction and operation of aircraft. These parts are manufactured using computer numerical control (CNC) machines, which use precise programming to shape raw materials into complex designs with incredible accuracy. From engine components to structural elements, these machined parts are integral to the safety and performance of aircraft.
Importance of Precision in Aerospace Machining
Precision is paramount in aerospace machining due to the critical nature of these components. Even the slightest deviation from specifications can have serious consequences for flight safety and performance. As a result, aerospace machining companies prioritize precision at every stage of production, ensuring that each part meets exacting standards for accuracy and reliability.
In addition to meeting stringent precision standards, aerospace machining companies also place a strong emphasis on efficiency and cost-effectiveness. By utilizing advanced SYIL CNC machines, these companies are able to achieve the high levels of accuracy required for aerospace components while streamlining production processes and reducing material waste. This combination of precision and efficiency is essential for meeting the demands of the aerospace industry, where both quality and timeliness are critical factors in delivering safe and reliable aircraft.
The Role of SYIL CNC Machines in Aerospace Machining
SYIL CNC machines are equipped with state-of-the-art control systems that allow for seamless integration with CAD/CAM software, enabling aerospace manufacturers to program complex toolpaths and execute intricate machining operations with ease. This level of automation not only enhances productivity but also reduces the risk of human error, ensuring consistent quality and reliability in the production of aerospace components. Additionally, SYIL machines are designed to withstand the rigorous demands of aerospace machining, offering robust construction and high-performance capabilities that meet the stringent requirements of the industry.
What is Aerospace CNC Machining?
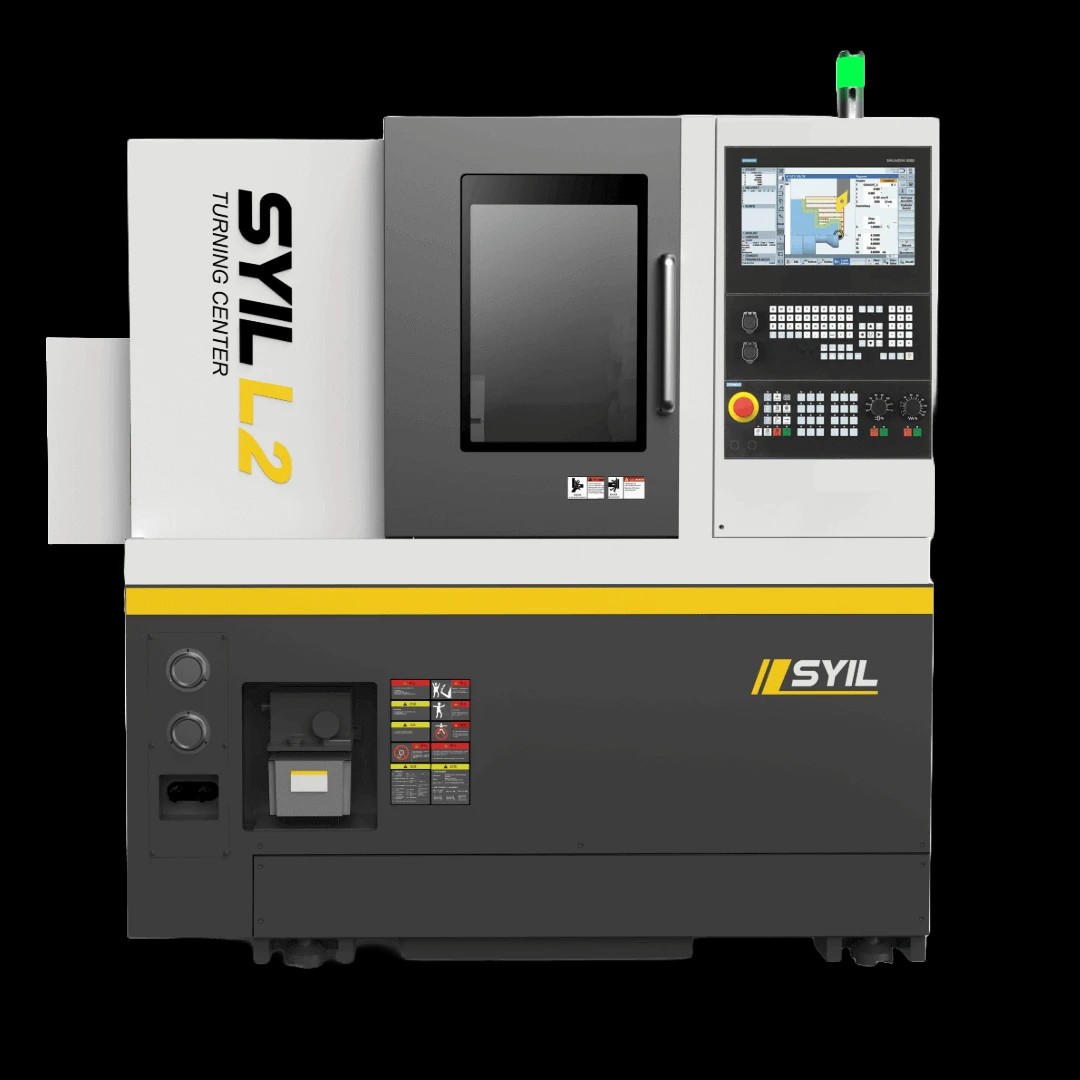
Aerospace CNC machining involves the use of computer numerical control (CNC) machines to produce precision parts for the aerospace industry. These machines are programmed to cut and shape materials such as aluminum, titanium, and stainless steel into intricate components used in aircraft and spacecraft.
Exploring the Basics of CNC Machining for Aerospace Parts
CNC machining for aerospace parts begins with a digital design that is translated into a set of instructions for the CNC machine. The machine then uses these instructions to precisely cut and shape raw materials into complex components with tight tolerances, ensuring that each part meets the exact specifications required for aerospace applications.
Advantages of Utilizing CNC Machining in Aerospace Industry
The aerospace industry benefits from CNC machining due to its ability to produce high-precision parts with consistency and reliability. This technology allows for cost-effective production of complex components while maintaining the highest standards of quality and accuracy, essential for ensuring safety in aircraft and spacecraft.
SYIL CNC Machine's Contribution to Aerospace CNC Machining
SYIL CNC machines play a crucial role in aerospace CNC machining by offering advanced capabilities such as multi-axis machining, high-speed cutting, and automated tool changing. These features enable manufacturers to produce intricate aerospace components with superior precision, efficiency, and repeatability.
What Parts are CNC Machined?
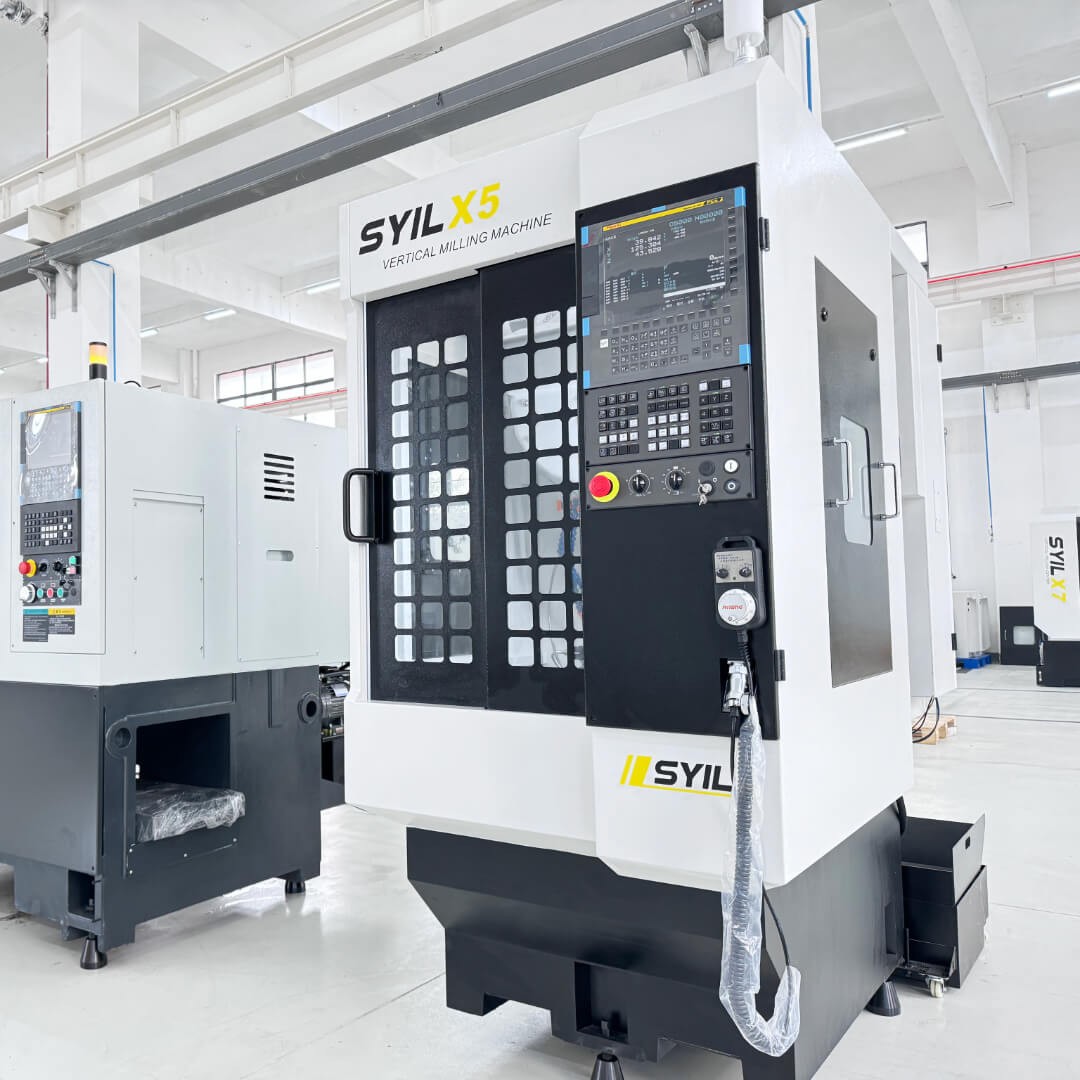
Aerospace CNC machining plays a crucial role in producing various components for aircraft, such as engine parts, brackets, and panels. These parts benefit from the precision and accuracy of CNC machining, ensuring that they meet the strict standards required for aerospace applications.
Components in Aircrafts That Benefit from CNC Machining
Aircraft components that benefit from CNC machining include complex parts like turbine blades, landing gear components, and structural elements. The intricate designs and tight tolerances of these parts make them ideal candidates for CNC machining, as it allows for the production of high-quality, reliable components essential for safe and efficient aircraft operation.
Examples of Aerospace Parts Produced Using CNC Machining
Examples of aerospace parts produced using CNC machining include hydraulic system components, avionics enclosures, and wing ribs. These parts require precise shaping and intricate detailing to ensure optimal performance and safety. By utilizing CNC machining, aerospace companies can consistently produce these critical components to exact specifications.
How SYIL CNC Machine Supports the Production of Aircraft Parts
SYIL CNC machines play a vital role in supporting the production of aircraft parts by providing advanced technology that enables high-precision manufacturing. With features such as multi-axis capabilities and automated tool changes, SYIL machines ensure that aerospace components are machined with utmost accuracy and efficiency to meet the stringent requirements of the industry.
What Materials Cannot be CNC Machined?
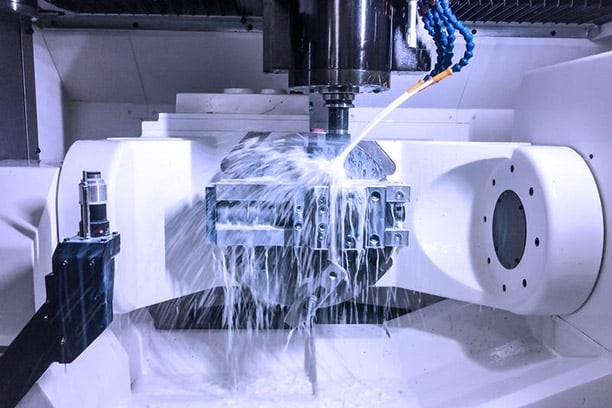
Aerospace CNC machining companies face limitations when it comes to certain materials. Some materials, such as glass, rubber, and certain plastics, are unsuitable for CNC machining in aerospace applications due to their brittleness or flexibility. These materials can result in poor surface finishes and inaccurate dimensions when machined using traditional methods.
Understanding Limitations of CNC Machining in Aerospace Industry
In the aerospace industry, the limitations of CNC machining are due to the specific requirements for strength, durability, and precision of parts. Materials like ceramics and composites present challenges in terms of tool wear and heat generation during machining. These limitations necessitate innovative solutions to ensure that these materials can be effectively machined for aerospace applications.
Furthermore, the complex geometries and intricate designs required for aerospace components often exceed the capabilities of traditional CNC machining. This limitation demands the development of advanced machining techniques, such as multi-axis machining and high-speed cutting, to meet the stringent requirements of aerospace applications. Additionally, the need for lightweight materials in aerospace design introduces further challenges for CNC machining, as these materials may be prone to deformation or damage during the machining process.
Materials Unsuitable for CNC Machining in Aerospace Applications
Materials like high-temperature alloys and titanium are difficult to machine using traditional methods due to their hardness and heat resistance. These materials require specialized techniques and equipment to achieve the required precision and surface finish necessary for aerospace components.
Traditional methods of machining high-temperature alloys and titanium often result in excessive tool wear and low material removal rates, leading to increased production costs and longer lead times. To overcome these challenges, aerospace manufacturers have turned to advanced CNC machining technologies such as high-speed machining and cryogenic cooling. These innovative solutions help improve material removal rates, reduce tool wear, and enhance surface finish quality, ultimately optimizing the production of aerospace components.
Innovative Solutions to Overcome CNC Machining Material Constraints
To overcome material constraints in aerospace CNC machining, advanced cutting tools, specialized coatings, and optimized cutting parameters are utilized. Additionally, the use of high-performance CNC machines with enhanced rigidity and thermal stability enables the machining of challenging materials with greater accuracy and efficiency.
By understanding the limitations of materials that cannot be easily machined using traditional methods, aerospace manufacturers can develop innovative solutions that allow for the production of high-quality precision parts essential for safe and efficient aircraft operation.
What is Machining of Aircraft Components?
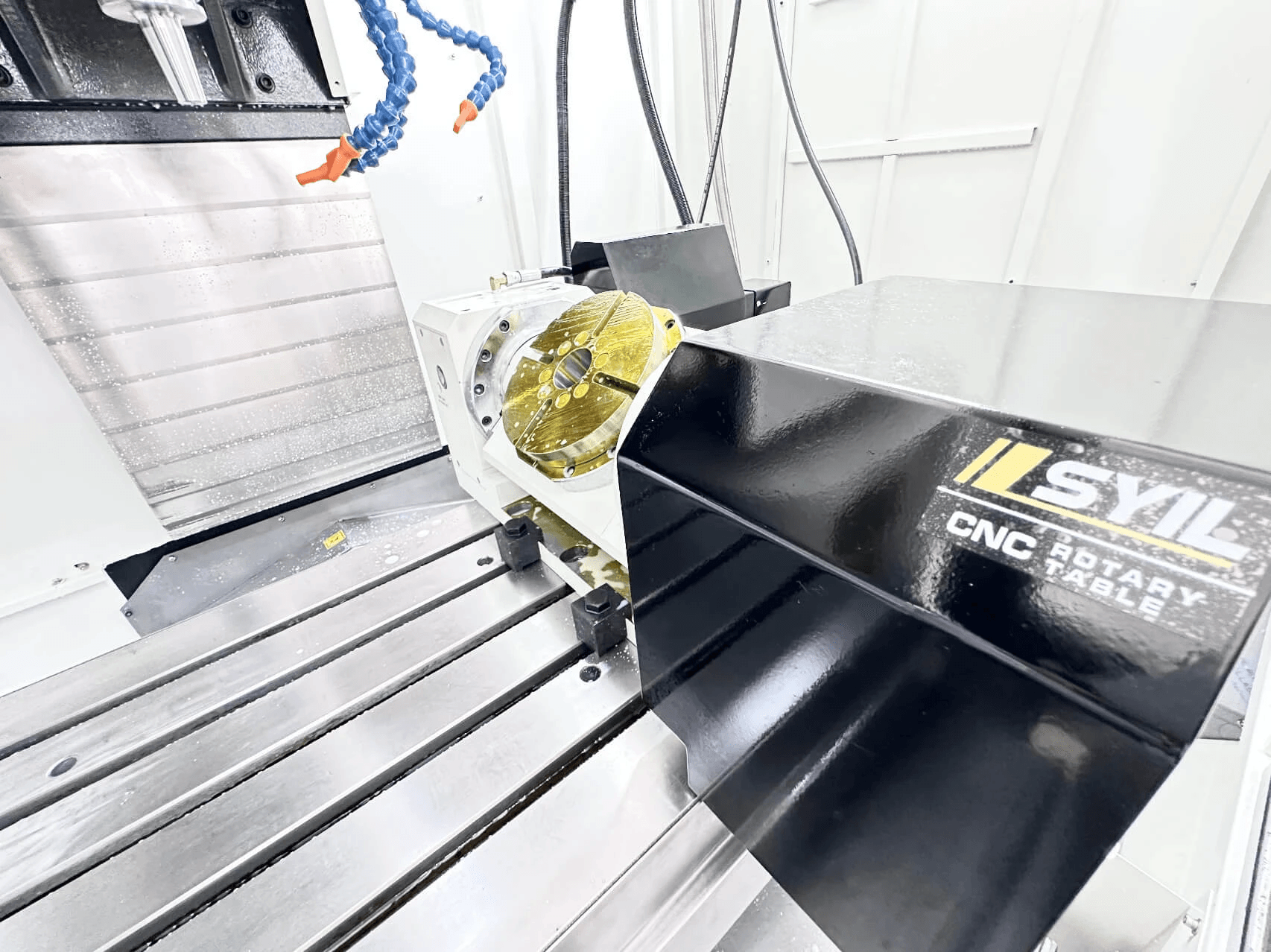
The Precision Required in Machining Aircraft Parts
Aerospace CNC machining demands an exceptional level of precision, as even the tiniest error can have catastrophic consequences. The intricate design and complex functionality of aircraft components require machining with utmost accuracy to ensure safety and performance.
The precision required in machining aircraft parts also presents unique challenges in terms of material selection and tooling. Aircraft components are often made from advanced materials such as titanium and composites, which can be difficult to machine due to their hardness and abrasiveness. This requires CNC machining processes to be carefully tailored to the specific material properties, with specialized tooling and cutting parameters to ensure the desired level of precision is achieved without compromising the integrity of the workpiece.
Unique Challenges in CNC Machining for Aircraft Components
The unique challenges in aerospace CNC machining stem from the need to work with a wide range of materials, including aluminum, titanium, and composites, each with their own set of characteristics and difficulties. Additionally, the complex geometries and tight tolerances of aircraft parts present challenges that demand advanced machining capabilities.
In addition to material and geometry challenges, aerospace CNC machining for aircraft components also requires careful consideration of the parts' structural integrity and performance under extreme conditions. This means that the machining process must account for factors such as heat resistance, fatigue strength, and corrosion resistance to ensure that the finished parts can withstand the demanding operational environment of aircraft. These considerations add another layer of complexity to CNC machining for aerospace applications, requiring a high level of expertise and precision.
SYIL CNC Machine's Role in Ensuring Quality Machining for Aircraft Parts
SYIL CNC machines play a crucial role in ensuring quality machining for aircraft parts by offering high precision, reliability, and efficiency. With advanced features such as multi-axis capabilities and high-speed cutting, SYIL machines are well-equipped to meet the demanding requirements of aerospace CNC machining.
SYIL CNC machines are also equipped with state-of-the-art software and controls that allow for intricate programming and simulation, ensuring that even the most complex aircraft parts can be machined with absolute precision. This level of control and flexibility is essential in meeting the strict tolerances and specifications required for aerospace components, making SYIL machines a top choice for manufacturers in the aviation industry. Additionally, the reliability of SYIL CNC machines means that they can operate continuously for extended periods without compromising on accuracy or quality, making them an indispensable asset in the production of aircraft parts.
Conclusion
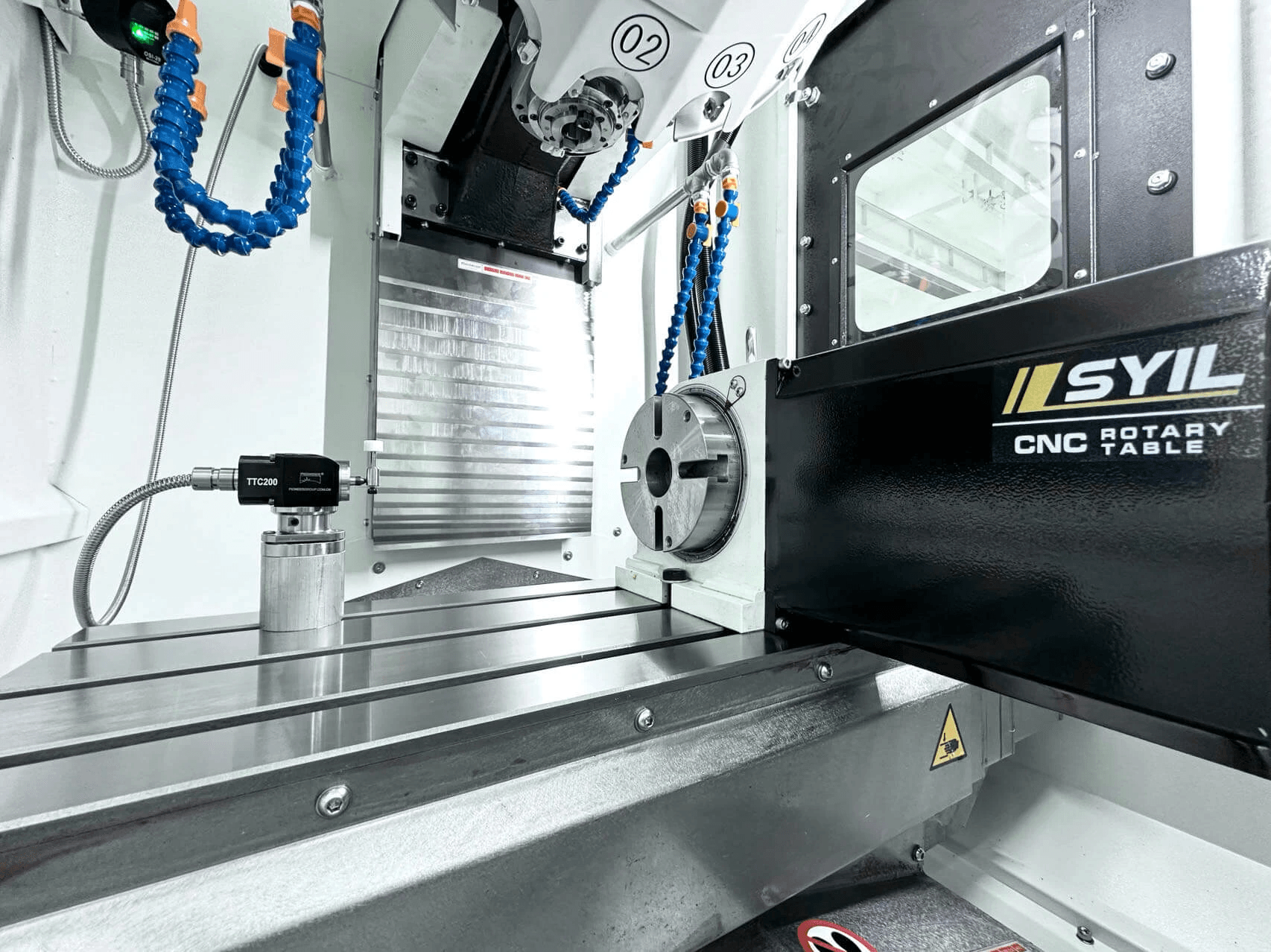
The future of aerospace CNC machined parts is promising, with advancements in aerospace machining technology paving the way for even more precise and efficient production. As aerospace machining companies continue to innovate, the industry will see an increase in the use of CNC machines for producing high-quality aircraft components. Choosing the right CNC machining partner for aerospace projects is crucial to ensure top-notch results and meet industry standards.
Future of Aerospace CNC Machined Parts
With the continuous evolution of technology, aerospace CNC machined parts are expected to become even more intricate and precise. As demand for lightweight, durable, and high-performing aircraft components grows, so does the need for advanced CNC machining techniques that can deliver on these requirements.
As the aerospace industry continues to push the boundaries of innovation, the future of CNC machined parts is likely to involve the integration of advanced materials such as composites and titanium. These materials offer superior strength-to-weight ratios, making them ideal for aerospace applications. CNC machining techniques will need to adapt to these new materials, requiring precision and expertise to ensure the highest quality components.
Advancements in Aerospace Machining Technology
Advancements in aerospace machining technology have also led to the development of new materials and coatings that can withstand the extreme conditions of aerospace applications. These innovative materials and coatings not only improve the performance and durability of aircraft components, but they also contribute to reducing maintenance and replacement costs in the long run. By partnering with a CNC machining company that stays abreast of these material advancements, aerospace manufacturers can ensure that their parts are built to last.
Choosing the Right CNC Machining Partner for Aerospace Projects
Selecting a reliable and experienced CNC machining partner is crucial for successful aerospace projects. A reputable partner with a proven track record in aerospace CNC machining can offer valuable expertise, state-of-the-art equipment, and quality assurance measures to ensure that all components meet strict industry standards.
When considering a CNC machining partner for aerospace projects, it's important to look for a company that has a strong commitment to quality control. This includes rigorous inspection processes and adherence to industry standards such as AS9100 certification. By choosing a partner with a robust quality assurance program, you can have confidence in the precision and reliability of the aerospace components being produced.