Introduction
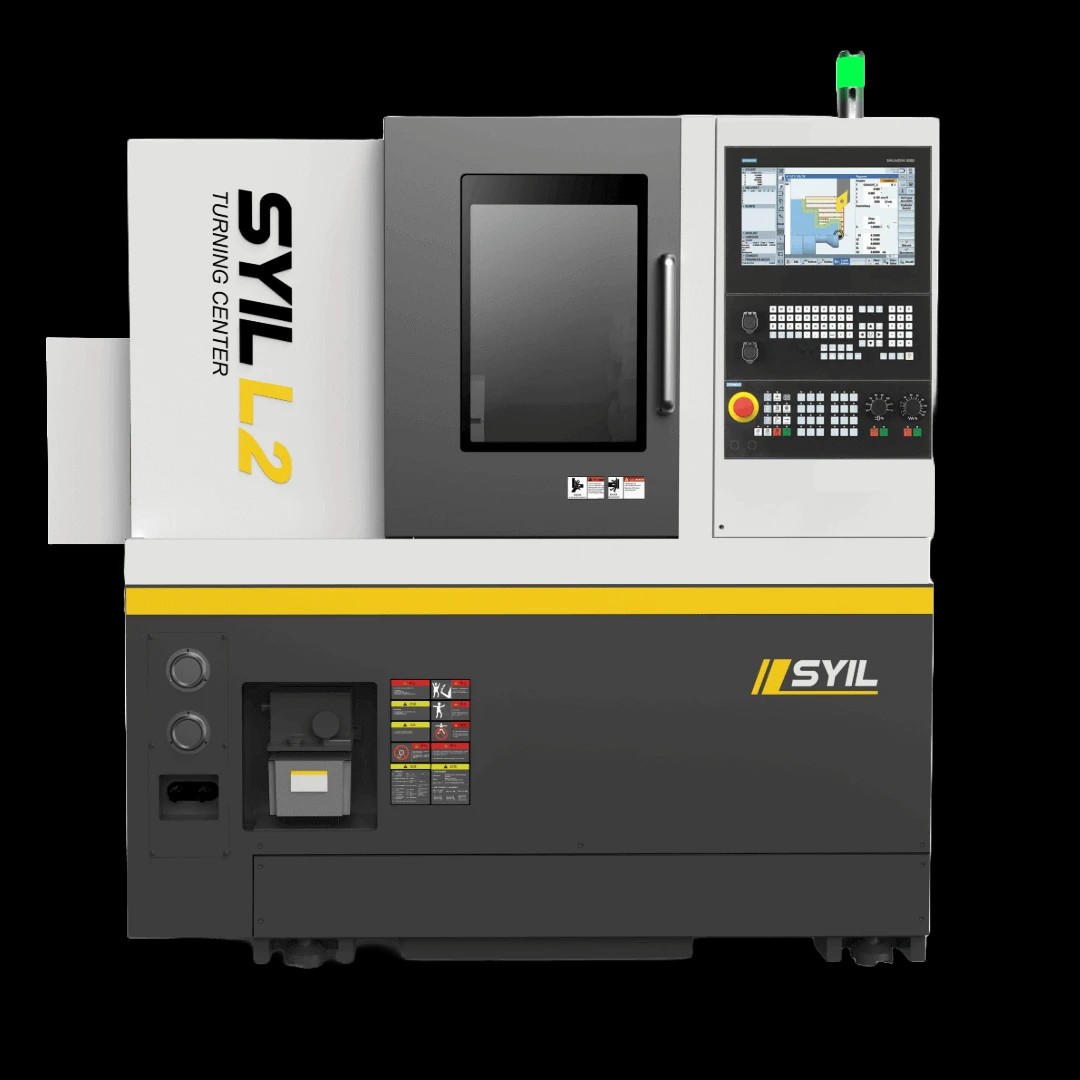
In the fast-paced world of aerospace manufacturing, precision is paramount. Aerospace machining involves the use of advanced technology and techniques to create components that meet the stringent requirements of the aerospace industry. What is an aerospace machinist? An aerospace machinist is a skilled professional who uses specialized tools and equipment to fabricate parts for aircraft and spacecraft. What is aerospace machining technology? Aerospace machining technology refers to the cutting-edge methods and machinery utilized in the production of aerospace components.
Importance of Precision Aerospace Machining
When it comes to aerospace manufacturing, precision is non-negotiable. The smallest error in a component can have catastrophic consequences, making precision machining absolutely essential in this industry. What is CNC in aerospace? CNC (Computer Numerical Control) plays a crucial role in aerospace machining, allowing for high levels of accuracy and repeatability in the production of complex parts.
SYIL CNC Machine for Aerospace Machining
The SYIL CNC machine has revolutionized aerospace machining with its advanced capabilities and precise control over cutting operations. This state-of-the-art equipment enables manufacturers to achieve the exacting standards required for aerospace components, ensuring reliability and safety in every part produced.
Key Factors for Successful Aerospace Machining
In order to achieve success in aerospace machining, several key factors must be considered. These include choosing the right materials and tools, understanding tolerances and specifications, implementing advanced machining strategies, managing chips and coolant effectively, as well as achieving surface finish and dimensional accuracy.
Choosing the Right Tools and Materials
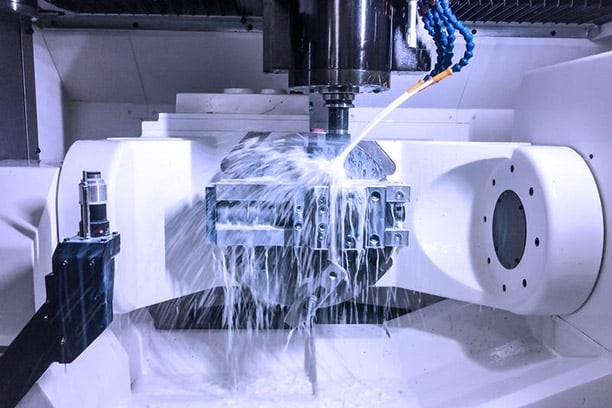
When it comes to aerospace machining, selecting high-quality cutting tools is crucial for achieving precision and accuracy in the manufacturing process. Aerospace machinists rely on tools such as end mills, drills, and reamers that are specifically designed to withstand the demands of machining aerospace-grade materials. These cutting tools are engineered to deliver superior performance and longevity, ensuring that each component meets the stringent requirements of the aerospace industry.
Aerospace-grade materials play a pivotal role in the success of aerospace machining projects. These materials are known for their exceptional strength, durability, and resistance to extreme conditions, making them ideal for use in aircraft and spacecraft components. From titanium alloys to high-strength aluminum, aerospace-grade materials undergo rigorous testing and certification processes to meet the exacting standards of the aerospace industry. Machining these materials requires specialized techniques and expertise to ensure precise dimensions and surface finishes.
Precision machining techniques are essential for producing complex aerospace components with tight tolerances and intricate geometries. Aerospace machinists utilize advanced CNC machines equipped with multi-axis capabilities to achieve unparalleled accuracy in their manufacturing processes. By employing sophisticated toolpaths and cutting strategies, they can create intricate features while maintaining dimensional integrity throughout the machining operation.
Understanding Tolerances and Specifications
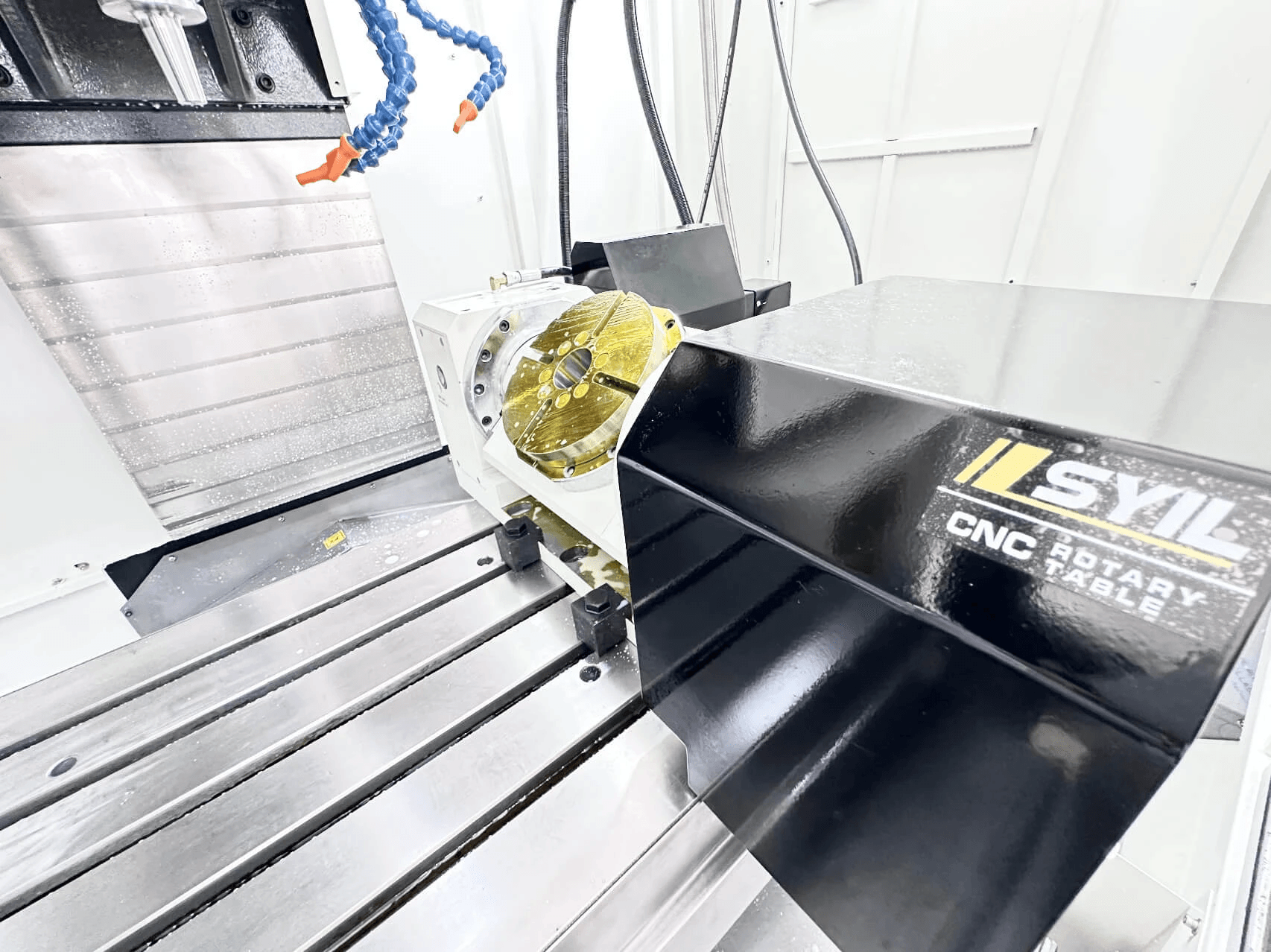
When it comes to aerospace machining, meeting tight tolerances is crucial for ensuring the safety and reliability of aircraft components. Aerospace machinists are tasked with producing parts that adhere to strict dimensional specifications, often within microns. This requires a high level of precision and expertise in machining techniques.
Meeting Tight Tolerances in Aerospace Machining
Aerospace machinists use advanced CNC machines to achieve the precise tolerances required for aerospace components. These machines are equipped with cutting-edge technology that allows for intricate and accurate machining processes. By utilizing these capabilities, aerospace machinists can produce parts with exceptional accuracy, meeting the stringent requirements of the industry.
Adhering to Aerospace Industry Standards
In aerospace machining, adherence to industry standards is non-negotiable. The aerospace sector has established rigorous guidelines for manufacturing processes and material specifications to ensure the highest levels of safety and performance. Machinists must be well-versed in these standards and consistently apply them throughout the production process to guarantee compliance.
Importance of Quality Control in Aerospace Machining
Quality control is paramount in aerospace machining to verify that parts meet exact specifications and performance requirements. Rigorous inspection protocols are implemented at every stage of production to identify any deviations from tolerances or defects that could compromise the integrity of the component. This meticulous approach ensures that only top-quality parts are used in aerospace applications.
Advanced Machining Strategies
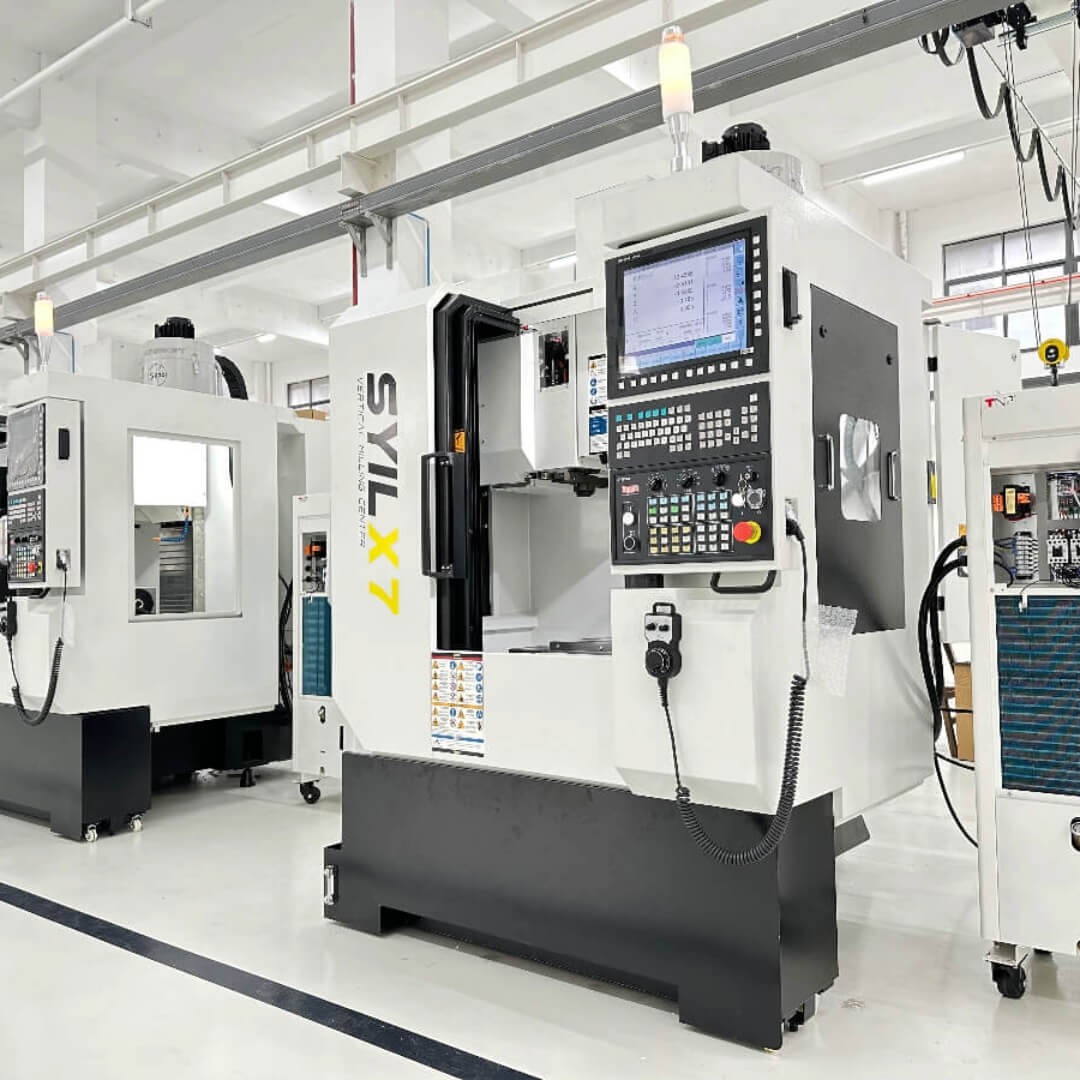
As technology continues to advance, high-speed machining has become a game-changer in aerospace machining. With the ability to rapidly remove material while maintaining precision, high-speed machining is crucial for producing aerospace components with intricate designs and tight tolerances. This innovative approach allows aerospace machinists to optimize production time without sacrificing quality, making it a must-have technique in modern aerospace manufacturing.
High-Speed Machining for Aerospace Components
Utilizing multi-axis machining has revolutionized the production of complex aerospace parts. By enabling simultaneous cutting from multiple angles, multi-axis machining enhances efficiency and accuracy, reducing the need for multiple setups and minimizing human error. This advanced strategy empowers aerospace machinists to create intricate components with unparalleled precision, meeting the stringent demands of the aerospace industry with ease.
Multi-axis Machining for Complex Aerospace Parts
In today's aerospace manufacturing landscape, CAD/CAM software has become an indispensable tool for achieving precision in machining operations. By providing a digital platform for designing, simulating, and programming CNC machines, CAD/CAM software streamlines the entire process of creating aerospace components. With its ability to generate complex toolpaths and optimize cutting strategies, this technology plays a vital role in enhancing productivity and maintaining strict tolerances in aerospace machining.
Utilizing CAD/CAM Software for Precision Aerospace Machining
By incorporating high-speed machining, multi-axis techniques, and CAD/CAM software into their operations, aerospace machinists can elevate their capabilities and meet the evolving demands of the industry with confidence.
Effective Chip and Coolant Management
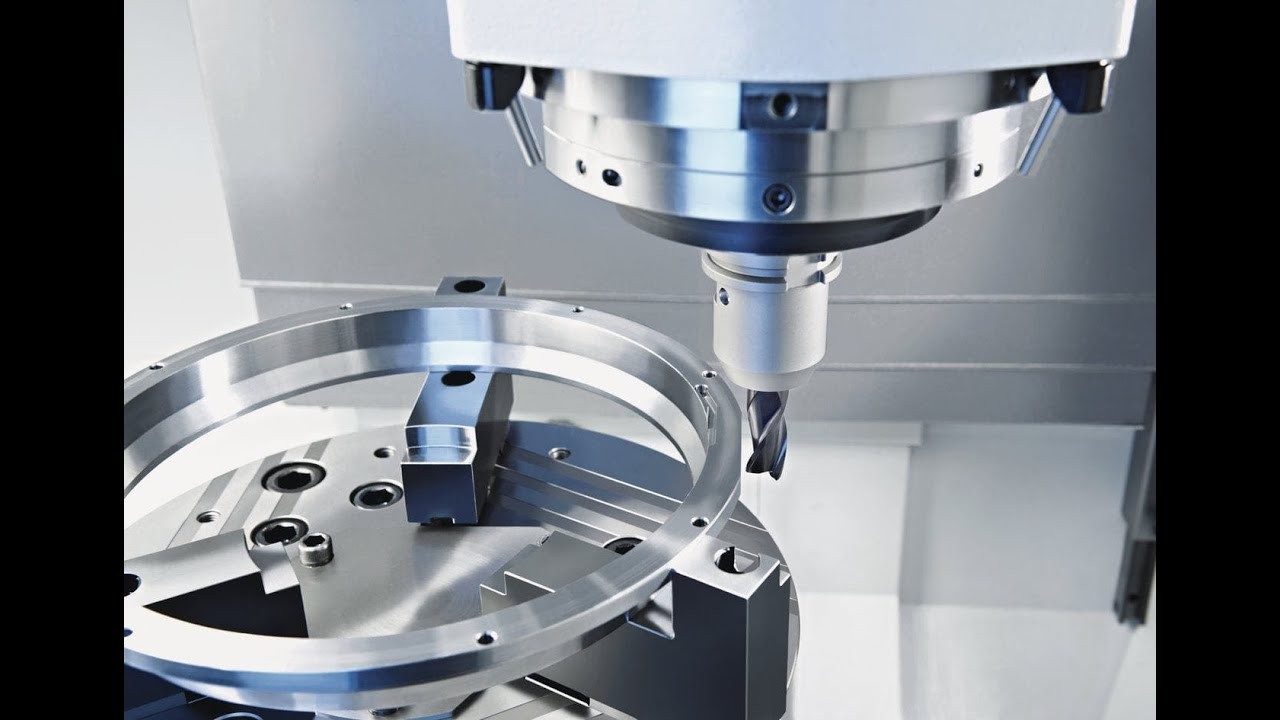
Effective chip and coolant management is crucial in aerospace machining to ensure the quality and precision of the components. Efficient chip evacuation in aerospace machining is essential to prevent tool damage, maintain accuracy, and ensure smooth operations. The removal of chips from the workpiece and cutting tools is necessary to avoid interference with the machining process, which could lead to defects in the final product.
Importance of Efficient Chip Evacuation in Aerospace Machining
In aerospace machining, efficient chip evacuation plays a vital role in preventing re-cutting of chips, reducing heat generation, and improving surface finish. An aerospace machinist needs to employ effective chip evacuation techniques such as using high-pressure coolant systems, through-spindle coolant delivery, and strategic toolpath planning to optimize chip removal during the machining process. These practices help minimize tool wear, extend tool life, and enhance overall productivity in aerospace manufacturing.
Furthermore, efficient chip evacuation also contributes to the overall safety of the machining process in aerospace manufacturing. By preventing the accumulation of chips, there is a reduced risk of tool breakage and potential damage to the workpiece. This is particularly crucial when working with high-value aerospace components where any mishap can result in significant financial losses and project delays. Therefore, prioritizing effective chip evacuation techniques not only improves productivity but also safeguards the integrity of the entire machining operation.
Coolant Strategies for Aerospace Machining
Coolant strategies for aerospace machining involve selecting the right type of coolant based on the material being machined and the specific requirements of the application. Aerospace-grade materials often require specialized coolants that provide lubrication, cooling, and corrosion protection while meeting stringent industry standards. Proper coolant selection and application are critical for achieving dimensional accuracy, surface finish quality, and overall efficiency in aerospace machining operations.
Additionally, sustainable coolant solutions are gaining popularity in aerospace machining due to their environmental and cost-saving benefits. These solutions often use bio-based or synthetic lubricants that minimize waste and reduce the environmental impact of machining operations. By implementing sustainable coolant solutions, aerospace manufacturers can improve their sustainability credentials and reduce overall operating costs, making it a win-win situation for both the environment and the bottom line.
Benefits of Sustainable Coolant Solutions for Aerospace Machining
Sustainable coolant solutions offer numerous benefits for aerospace machining, including cost savings, environmental responsibility, and improved workplace safety. By implementing sustainable coolants made from biodegradable or renewable resources, aerospace manufacturers can reduce their environmental impact while maintaining high performance levels in machining processes. These solutions contribute to a more eco-friendly approach to aerospace manufacturing while ensuring compliance with regulations governing coolant usage.
Achieving Surface Finish and Dimensional Accuracy
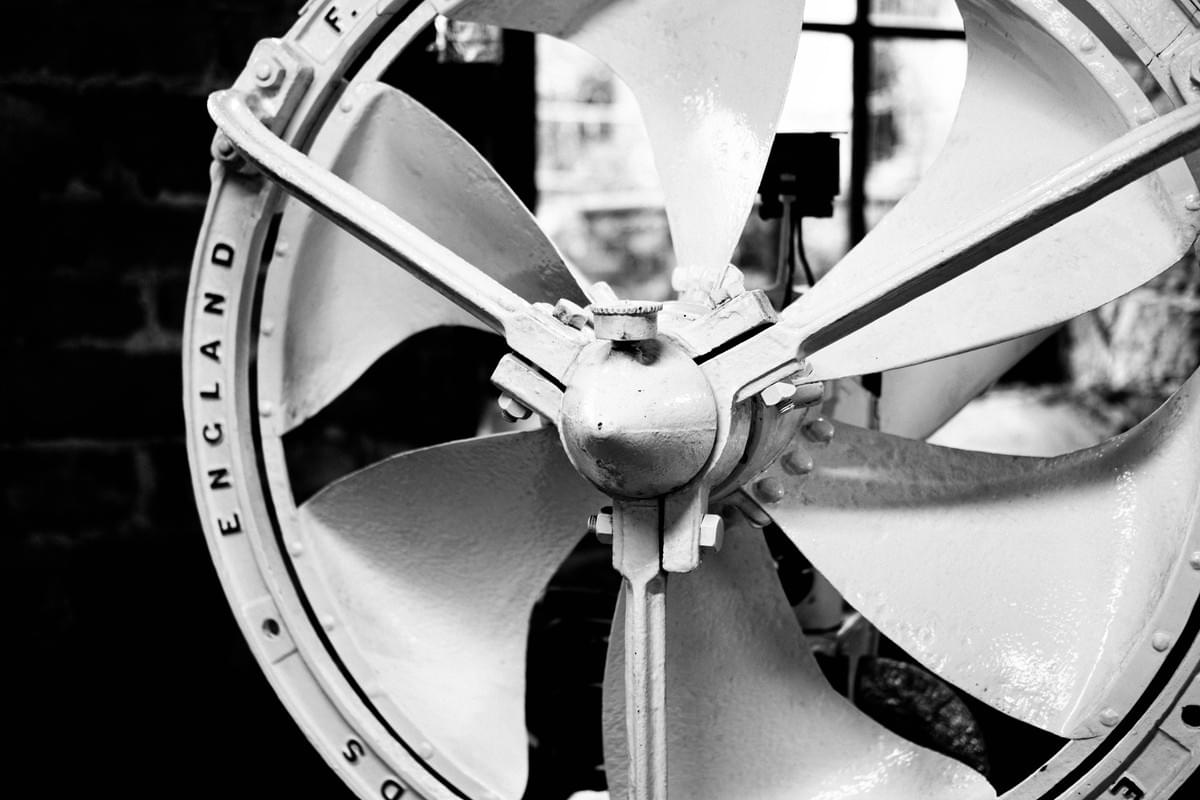
When it comes to aerospace machining, achieving the perfect surface finish is crucial for the performance and safety of aerospace components. Advanced techniques such as abrasive flow machining and chemical etching are commonly used to achieve the required surface finish for aerospace components. These methods ensure that the surfaces are smooth, free from imperfections, and have the necessary texture to meet aerospace industry standards.
Surface Finish Techniques for Aerospace Components
One of the most effective techniques for achieving precise surface finishes in aerospace machining is abrasive flow machining (AFM). AFM uses a polymer media mixed with abrasive particles to remove material from the component's surface, resulting in a consistent and uniform finish. Additionally, chemical etching is another widely used method in aerospace machining to achieve specific surface textures and finishes required for aerodynamic performance.
In addition to AFM and chemical etching, another surface finish technique commonly used in aerospace machining is shot peening. Shot peening involves bombarding the component's surface with small spherical media, such as steel shot or glass beads, to create compressive residual stresses that improve fatigue life and resistance to stress corrosion. This process can also help to reduce the risk of cracking and enhance the overall durability of aerospace components, making it an essential technique for achieving high-quality surface finishes in aerospace machining.
Precision Measurement Tools for Aerospace Machining
In order to ensure dimensional accuracy in aerospace machining, precision measurement tools such as coordinate measuring machines (CMM) and laser scanning systems are employed. These tools allow aerospace machinists to accurately measure and inspect complex components with tight tolerances, ensuring that they meet the exact specifications required for aerospace applications.
Tips for Achieving Dimensional Accuracy in Aerospace Machining
To achieve dimensional accuracy in aerospace machining, it is essential to carefully select cutting tools, materials, and machining strategies that can consistently produce precise dimensions within tight tolerances. Additionally, implementing stringent quality control measures throughout the manufacturing process is crucial to verify that each component meets the specified dimensional requirements.
Furthermore, it is important to consider the thermal stability of the materials being machined, as temperature fluctuations can affect dimensional accuracy. Choosing materials with high thermal conductivity and stability can help minimize the impact of heat on the machining process. Additionally, utilizing cutting tools with advanced coatings and designs that can withstand high temperatures and maintain their sharpness will contribute to achieving precise dimensions in aerospace components.
Conclusion
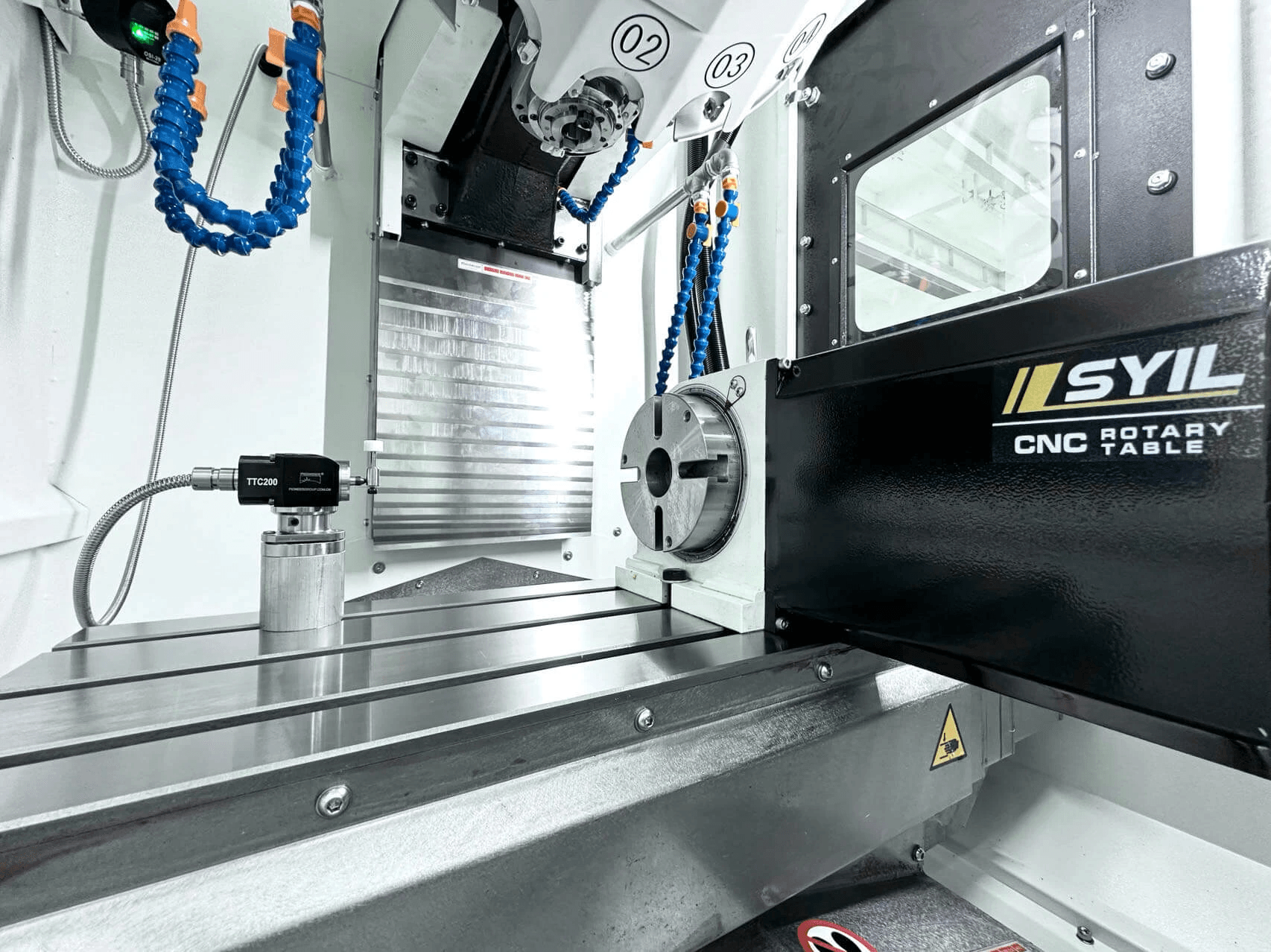
Innovations in Aerospace Machining Technology have revolutionized the industry, allowing for more precise and efficient production of aerospace components. From advanced CNC machines to cutting-edge materials, the aerospace machining field continues to push the boundaries of what is possible.
Continuous Improvement in Precision Aerospace Machining is essential for meeting the increasingly stringent demands of the aerospace industry. With a focus on quality control, tighter tolerances, and advanced machining strategies, aerospace machinists are constantly striving for perfection.
Future Trends in Aerospace Machining Technique are likely to be driven by advancements in automation, robotics, and artificial intelligence. As technology continues to evolve, we can expect to see even greater levels of precision and efficiency in aerospace manufacturing processes.
With a strong emphasis on innovation and continuous improvement, the future of aerospace machining looks incredibly promising. As new technologies emerge and existing ones are refined, the possibilities for creating complex and high-quality aerospace components are truly endless.