Introduction
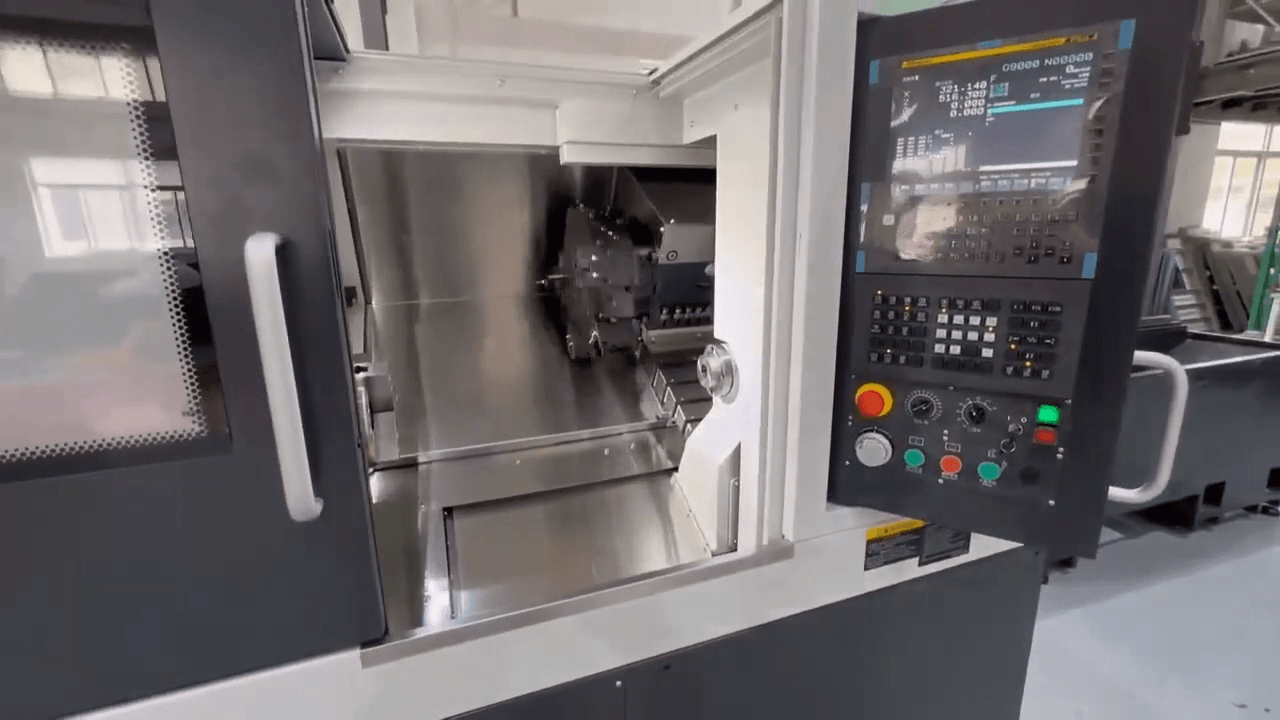
In the world of CNC machining, understanding CNC lathe tolerances is crucial for achieving high-quality results. Tolerances dictate how closely a machined part can match its intended design specifications, which directly impacts the performance and functionality of the final product. As industries increasingly rely on precision engineering, mastering these tolerances becomes essential for manufacturers aiming to maintain competitive advantages.
Importance of CNC Lathe Tolerances
CNC lathe tolerances are not just numbers; they are the backbone of precision machining. The ability to adhere to tight tolerances can mean the difference between a successful project and costly rework or failure. In applications ranging from aerospace to automotive, where every millimeter counts, understanding what is the accuracy of CNC lathe machine becomes vital for ensuring safety and reliability.
How Tolerances Affect Machining Quality
Tolerances significantly affect machining quality by influencing aspects such as fit, function, and durability of components. Poor tolerance management can lead to misalignment or improper fitting parts that compromise overall performance. By knowing what is the tolerance for CNC wood and metal alike, manufacturers can optimize their processes to enhance product quality while minimizing waste.
Overview of CNC Lathe Machines
CNC lathe machines are sophisticated tools that automate the process of shaping materials through precise rotational movements. These machines utilize advanced technology to achieve high levels of accuracy and repeatability in production runs. Familiarity with standard machining tolerances in mm allows operators to set appropriate expectations for their projects while leveraging CNC tolerance standards effectively to meet industry requirements.
What Are CNC Lathe Tolerances?
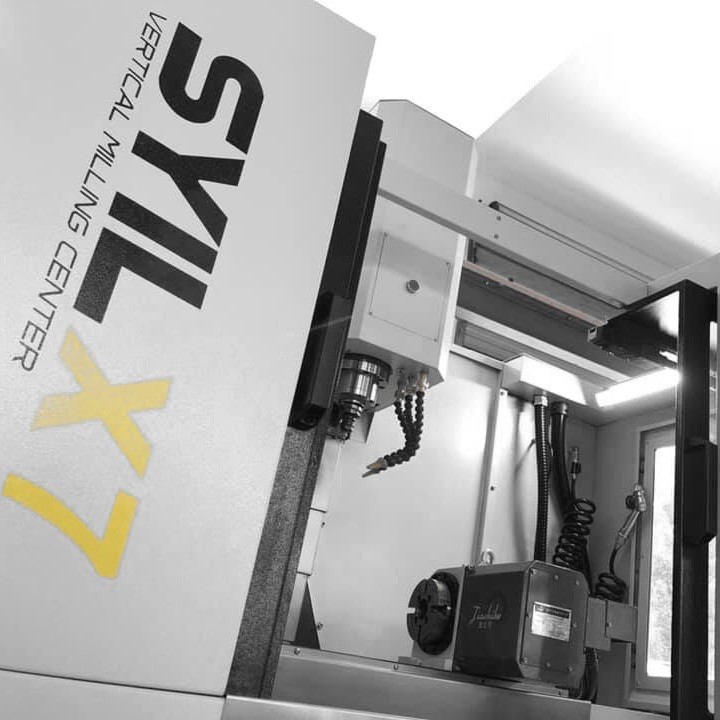
CNC lathe tolerances are crucial specifications that dictate how closely a machined part can conform to its intended design. These tolerances help ensure that the finished product meets the required dimensions and performance standards. Understanding CNC lathe tolerances is essential for achieving high-quality machining results, whether you're working with metals or wood.
Defining CNC Lathe Tolerances
At its core, CNC lathe tolerances refer to the allowable variations in dimensions during the machining process. These variations can be influenced by factors such as machine capabilities, material properties, and tool wear. By defining these tolerances clearly, manufacturers can ensure that their products not only fit together properly but also function as intended within larger assemblies.
Common Types of Tolerances
There are several common types of CNC lathe tolerances that machinists need to be familiar with. Some of these include linear tolerance (which measures the allowable deviation in length), angular tolerance (which pertains to angle measurements), and geometric tolerance (which addresses form, orientation, and location). Each type plays a significant role in determining what is considered acceptable for a given project and helps guide machinists in achieving desired outcomes.
The Role of Tolerances in CNC Machining
Tolerances play an integral role in the overall quality and functionality of CNC machined parts. They influence not only how parts fit together but also their durability and performance under various conditions. Inadequate management of CNC lathe tolerances can lead to costly rework or even product failure, making it essential for manufacturers to understand what is the accuracy of CNC lathe machine capabilities and how they align with industry standards.
What is the Accuracy of CNC Lathe Machine?
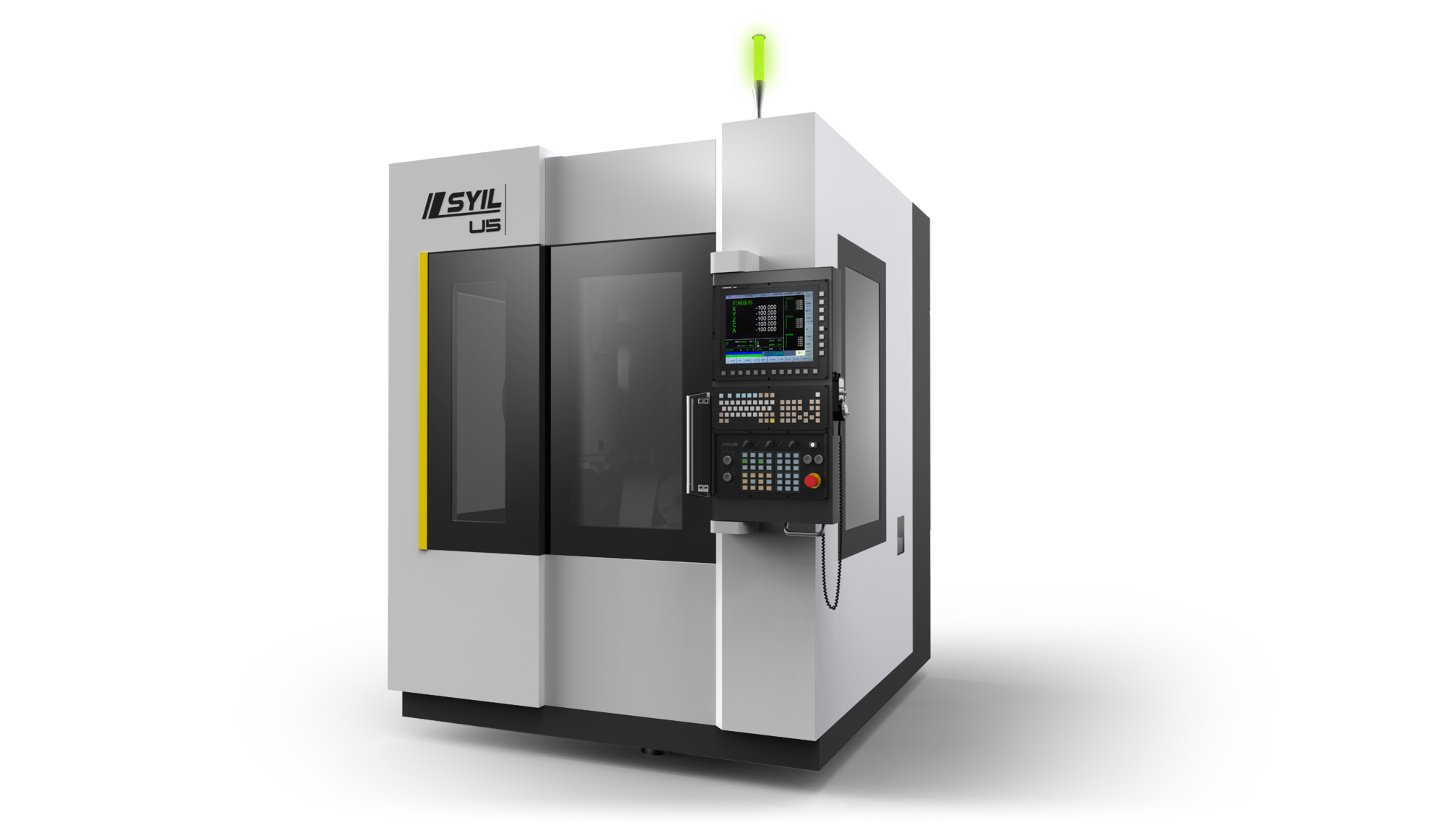
When we talk about CNC lathe machines, accuracy is a critical factor that directly impacts the quality of the finished product. The question What is the accuracy of CNC lathe machine? often arises among manufacturers and machinists alike, as it determines how closely a machined part can adhere to specified dimensions and tolerances. Achieving high accuracy in machining ensures that parts fit together correctly, function as intended, and meet customer expectations.
Factors Influencing Accuracy
Several factors influence the accuracy of CNC lathe machines, including machine design, tool wear, and environmental conditions. The structural integrity of the machine itself plays a vital role; any flex or vibration can lead to inaccuracies in machining operations. Additionally, tool wear over time can affect how well tools maintain their cutting capabilities, which directly ties into maintaining proper cnc lathe tolerances during production.
Another critical factor is thermal expansion; changes in temperature can cause materials to expand or contract, altering dimensions and affecting precision. Moreover, operator skill and programming errors can also contribute significantly to deviations from desired specifications. Understanding these factors helps manufacturers implement strategies for enhancing their processes while adhering to standard machining tolerances in mm.
Measuring and Achieving Precision
To ensure high levels of precision in CNC lathe operations, accurate measuring tools are essential. Instruments such as calipers, micrometers, and laser measurement systems are commonly used to assess whether parts meet specified tolerances set by ISO standards for machining tolerances. Regular calibration of these measuring devices is crucial; even minor discrepancies can lead to significant errors over time.
Achieving precision also involves meticulous attention during setup processes—ensuring that workpieces are securely held in place reduces movement that could compromise accuracy. Furthermore, utilizing advanced software for simulation and verification before actual machining can help identify potential issues related to cnc lathe tolerances early on in the process. This proactive approach not only saves time but also enhances overall product quality.
Real-World Accuracy Examples
Real-world examples illustrate just how pivotal accuracy is when working with CNC lathes across various industries. For instance, aerospace components often require extremely tight tolerances—sometimes within microns—to ensure safety and functionality; thus understanding What is the tolerance for CNC wood? becomes secondary when dealing with metals where precision reigns supreme.
In contrast, woodworking applications might allow for slightly looser tolerances due to material variability but still benefit from precise machining practices outlined by ISO standards for machining tolerances—demonstrating that even within different materials like wood versus metal there’s an emphasis on maintaining quality through accurate measurements.
Ultimately, success hinges on understanding industry-specific requirements while continually refining processes based on real-world feedback—this way companies remain competitive by producing high-quality parts with minimal waste due to poor tolerance management or inaccuracies.
What is the ISO Standard for Machining Tolerances?
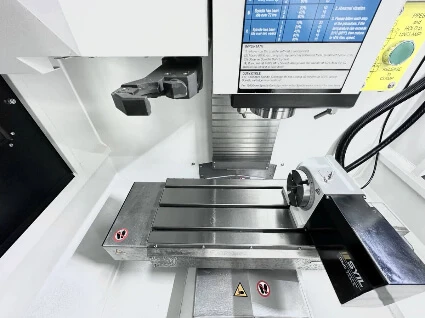
When it comes to CNC lathe tolerances, understanding the ISO standards is crucial for ensuring that parts are manufactured with precision and consistency. The International Organization for Standardization (ISO) has established a set of guidelines that define acceptable tolerances in machining processes, impacting everything from quality control to cost efficiency. By adhering to these standards, manufacturers can achieve a higher level of accuracy and reliability in their products.
Understanding ISO Tolerance Standards
ISO tolerance standards provide a framework for defining how much deviation from a specified dimension is permissible in machined components. These standards help engineers and machinists determine acceptable limits on dimensions, ensuring compatibility and interchangeability between parts. For instance, when considering the question What is the accuracy of CNC lathe machine? one must look at how closely these machines can adhere to ISO tolerances to truly gauge their performance.
Importance for Manufacturers
For manufacturers who rely on CNC lathe tolerances, adhering to ISO standards is not just about compliance—it's about maintaining competitiveness in the market. Following these guidelines helps reduce waste, minimizes rework, and enhances customer satisfaction by delivering products that meet precise specifications. Moreover, understanding What is the tolerance for CNC wood? versus metal machining highlights how different materials may require tailored approaches while still aligning with overarching ISO principles.
How to Implement ISO Standards
Implementing ISO standards requires a systematic approach that begins with training personnel on the importance of these guidelines in relation to standard machining tolerances in mm. Manufacturers should invest in calibration tools and software that align with ISO requirements while also regularly reviewing their machining tolerance chart to ensure ongoing compliance with industry benchmarks. By integrating these practices into their operations, companies can enhance their overall quality assurance processes and improve product reliability significantly.
Standard Machining Tolerances in mm
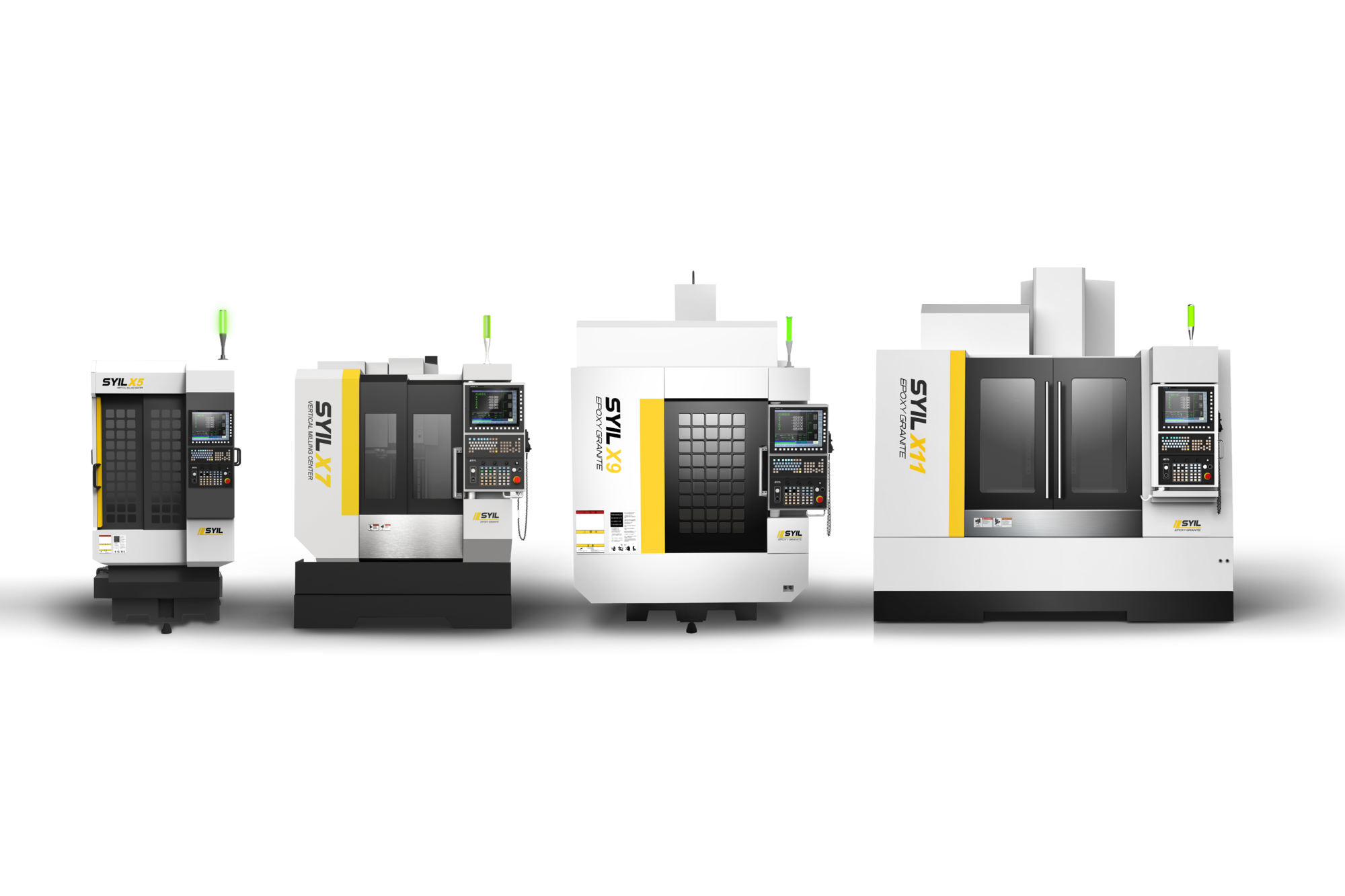
When it comes to CNC lathe tolerances, understanding the standard machining tolerances in millimeters is crucial for achieving precision and quality in manufacturing. Tolerances dictate how much variation is permissible in the dimensions of machined parts, which directly impacts functionality and performance. This section will delve into the overview of standard tolerance ranges, how to interpret tolerance charts, and their practical applications across various industries.
Overview of Standard Tolerance Ranges
Standard machining tolerances in mm are established guidelines that define acceptable limits for dimensions during the CNC machining process. These ranges vary based on factors such as material type, part complexity, and intended application. For instance, typical tolerances for metals might range from ±0.01 mm to ±0.5 mm, while wood may have broader tolerances due to its natural variability—often around ±0.5 mm to ±1 mm, reflecting what is the tolerance for CNC wood.
Understanding these standard tolerance ranges is essential for manufacturers aiming to meet specific quality standards while minimizing waste and rework. When considering what is the accuracy of a CNC lathe machine, it's important to note that tighter tolerances usually necessitate more advanced machinery and techniques but yield higher-quality outputs. Therefore, aligning your production goals with appropriate tolerance levels can greatly enhance efficiency and product reliability.
How to Interpret Tolerance Charts
Interpreting a machining tolerance chart can feel like deciphering a secret code at times; however, once you grasp the basics of CNC tolerance standards, it becomes much more manageable! These charts typically list various dimensions alongside corresponding tolerances that indicate acceptable variations from those dimensions—essentially serving as a roadmap for machinists.
To read these charts effectively, start by identifying the nominal dimension—the target measurement you aim for—and then look at the associated upper and lower limits defined by the specified tolerances. For example, if a part has a nominal diameter of 50 mm with a tolerance of ±0.1 mm, this means that any diameter between 49.9 mm and 50.1 mm would be considered acceptable quality per CNC lathe tolerances guidelines.
Moreover, familiarity with ISO standards can further streamline this process since many charts are designed according to what is the ISO standard for machining tolerances? This creates consistency across different manufacturing sectors while ensuring compliance with international quality benchmarks.
Practical Applications in Various Industries
Standard machining tolerances have far-reaching implications across diverse industries—from automotive and aerospace to woodworking and electronics—each requiring different levels of precision based on their unique applications. In automotive manufacturing, where components must fit together seamlessly under rigorous conditions, maintaining tight CNC lathe tolerances is paramount; even minor deviations can lead to significant performance issues or safety hazards.
Conversely, industries like furniture production may allow broader variabilities due to materials' inherent characteristics—like wood grain patterns—which leads us back to understanding what is the tolerance for CNC wood? Here again lies an opportunity: recognizing when tighter or looser tolerancing will best suit project requirements can save both time and resources during production runs.
Ultimately, knowing how standard machining tolerances in mm apply within your industry not only enhances product quality but also fosters better communication between engineers and machinists regarding design specifications—a win-win situation all around!
CNC Tolerance Standards and Their Impact
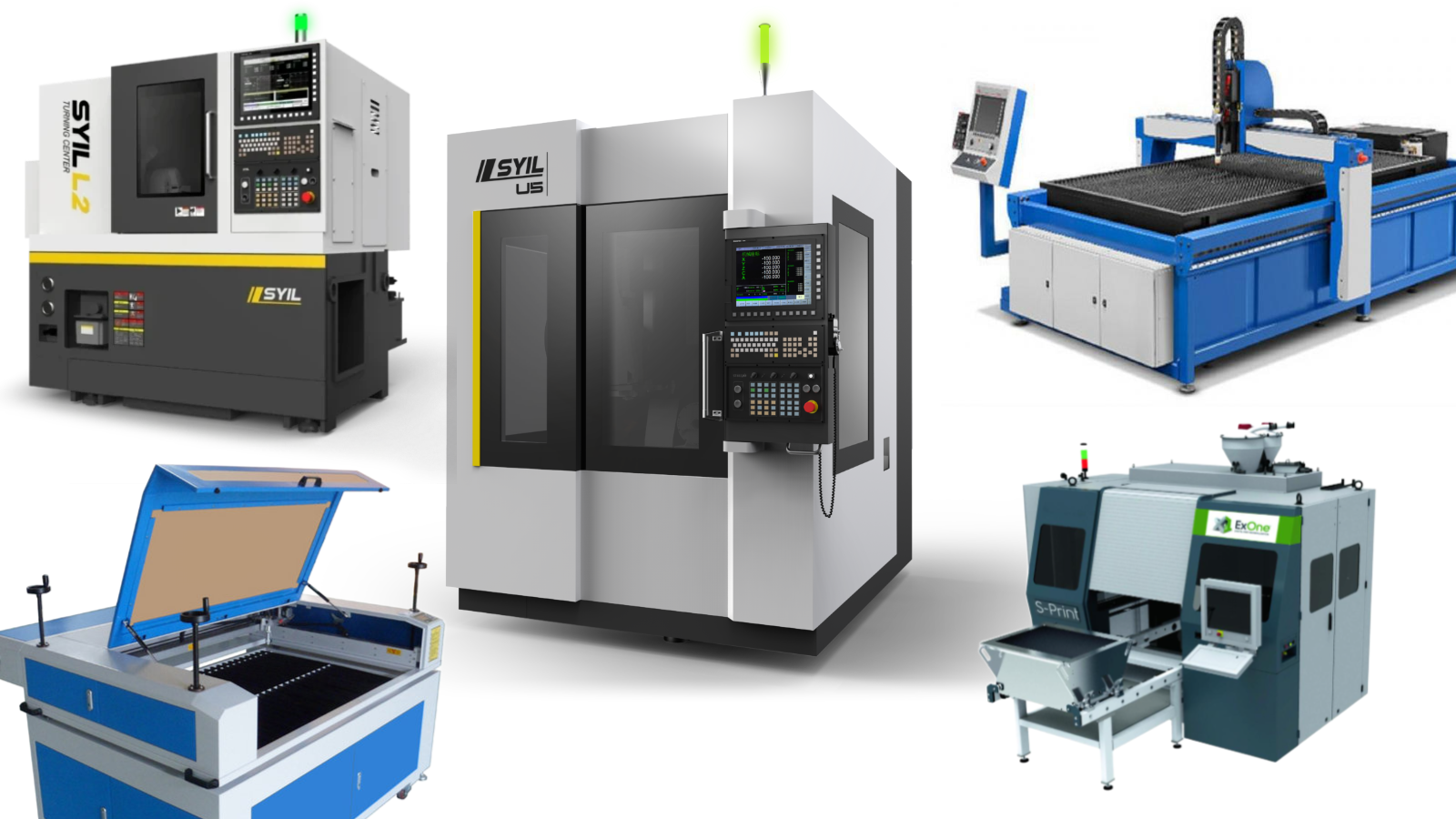
In the world of CNC machining, understanding CNC lathe tolerances is crucial for maintaining quality and precision across various industries. Different sectors have distinct requirements when it comes to tolerances, which can significantly affect production efficiency and product reliability. By adhering to industry-specific tolerance standards, manufacturers can ensure that their products meet regulatory demands while optimizing performance.
Industry-Specific Tolerance Standards
Each industry has its own set of CNC tolerance standards tailored to the specific materials and applications involved. For example, aerospace components often require tighter tolerances compared to automotive parts due to safety concerns and performance expectations. Similarly, when considering what is the accuracy of CNC lathe machines in different sectors, it becomes clear that industries such as medical device manufacturing demand higher precision than others like furniture making.
Understanding these industry-specific standards is essential for manufacturers who want to remain competitive in their field. Utilizing a machining tolerance chart can help identify the appropriate tolerances needed for various applications, ensuring compliance with industry regulations while also enhancing product quality. Ultimately, recognizing these nuances allows businesses to streamline their production processes effectively.
How to Choose the Right Tolerance
Selecting the right tolerance involves balancing several factors including functionality, material properties, and cost-effectiveness. It’s important first to assess what is the tolerance for CNC wood if you're working with wood-based projects versus metal components where tighter tolerances might be necessary due to different expansion rates and structural characteristics. The decision should factor in not only the material but also how critical a component's fit or function is within an assembly.
Consulting standard machining tolerances in mm provides a good starting point for determining acceptable limits based on specific material types and intended use cases. Manufacturers should also consider customer specifications or industry regulations that may dictate stricter requirements beyond general guidelines. In doing so, companies can avoid unnecessary rework or scrap while ensuring high-quality output.
Consequences of Poor Tolerance Management
Neglecting proper management of CNC lathe tolerances can lead to a cascade of issues that impact both productivity and profitability. Components produced outside specified tolerances may result in increased assembly difficulties or complete failure during operation—especially critical when considering what is the accuracy of CNC lathe machines in high-stakes environments like aerospace or medical fields. This not only affects customer satisfaction but also tarnishes a manufacturer's reputation over time.
Moreover, poor tolerance management often leads to higher operational costs due to wasted materials and labor associated with reworking defective parts or addressing customer complaints related to quality issues. Companies must be vigilant about implementing effective strategies for monitoring and maintaining tolerances throughout their production processes; otherwise, they risk falling behind competitors who prioritize precision engineering as part of their operational ethos.
In conclusion, understanding how CNC tolerance standards impact manufacturing practices cannot be overstated; it's essential for achieving high-quality results while minimizing waste and maximizing efficiency across diverse applications.
Conclusion
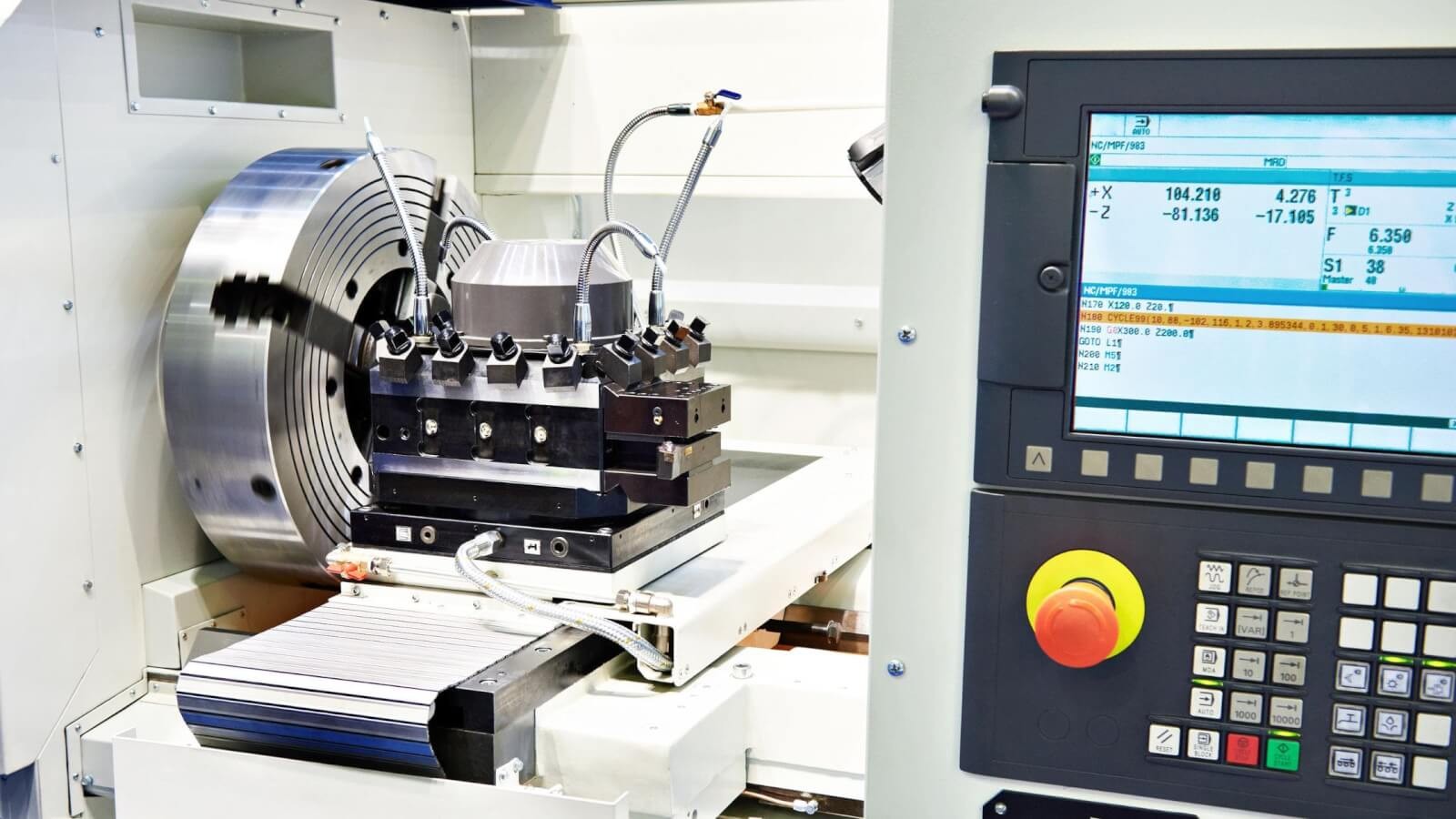
In the realm of CNC machining, understanding and managing CNC lathe tolerances is crucial for achieving high-quality results. These tolerances not only determine the precision of machined parts but also have a significant impact on the overall efficiency of manufacturing processes. By grasping concepts like what is the accuracy of CNC lathe machines and how various materials, including wood, are treated under different tolerance standards, manufacturers can enhance their production capabilities.
Key Takeaways on CNC Lathe Tolerances
CNC lathe tolerances are essential for ensuring that components fit together perfectly and function as intended. From metal to wood, each material has specific tolerances that must be adhered to; for instance, what is the tolerance for CNC wood? Understanding these differences allows manufacturers to optimize their processes and avoid costly mistakes. Moreover, familiarity with standard machining tolerances in mm helps engineers design parts that meet both performance requirements and industry standards.
Enhancing Precision with Proper Tolerances
Achieving precision in machining requires a deep understanding of how to apply CNC tolerance standards effectively. Utilizing tools like machining tolerance charts can assist engineers in selecting appropriate tolerances based on specific project needs. Additionally, by implementing ISO standards for machining tolerances, manufacturers can ensure consistency across production lines while enhancing quality control measures.
The Future of Tolerance Standards in CNC Machining
As technology advances, so too will the expectations around CNC lathe tolerances and accuracy levels. The future promises more sophisticated machinery capable of tighter tolerances than ever before—pushing boundaries in industries ranging from aerospace to automotive manufacturing. Embracing these changes while adhering to established guidelines will be key for companies looking to stay competitive in an increasingly demanding market.