Introduction
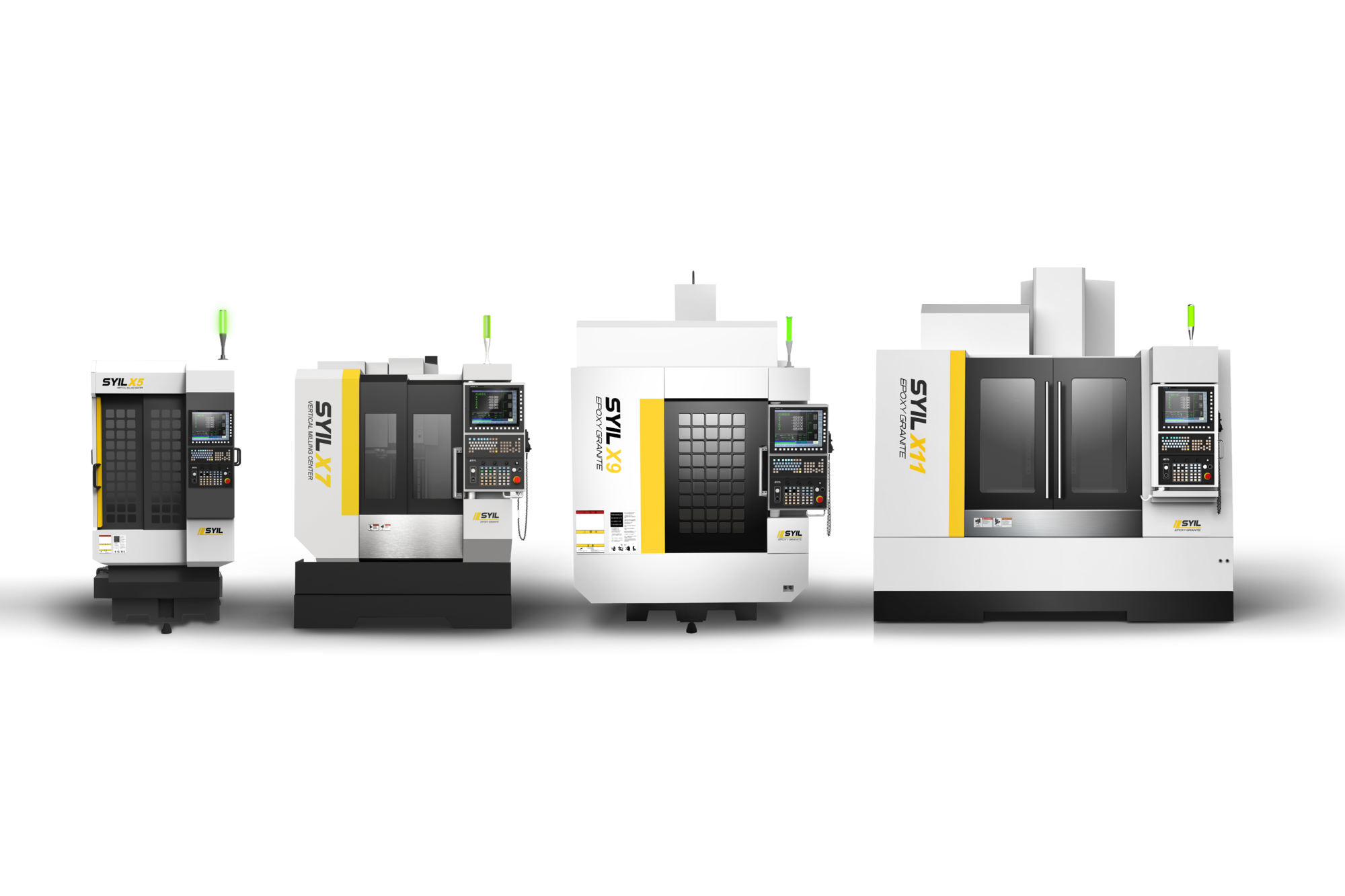
Milling is a cornerstone of modern manufacturing, playing a crucial role in shaping materials and creating components with precision. Understanding milling in manufacturing involves recognizing the various types of milling operations that can be performed, each tailored to specific needs and applications. This knowledge not only enhances efficiency but also ensures that manufacturers can achieve successful milling outcomes.
Understanding Milling in Manufacturing
At its core, milling is a machining process that uses rotating cutting tools to remove material from a workpiece. The different types of milling operations—such as face milling, end milling, and groove milling—allow for diverse applications across industries. By grasping these concepts, manufacturers can better select the appropriate techniques and tools for their projects.
Overview of Common Milling Operations
When we talk about common milling operations, we're referring to a variety of methods that cater to different manufacturing needs. Each type has its own unique set of advantages and applications; for instance, face milling is ideal for flat surfaces while end milling excels at creating intricate shapes. A comprehensive overview helps businesses determine what are the different types of milling operations best suited for their production goals.
The Role of Milling Machines
Milling machines are the heart of any successful machining operation, equipped with various features designed to handle multiple tasks efficiently. The effectiveness of these machines largely depends on how well they utilize specific milling cutters and techniques associated with various types of milling operations. In essence, selecting the right machine can significantly enhance production capabilities and lead to successful milling outcomes.
Face Milling
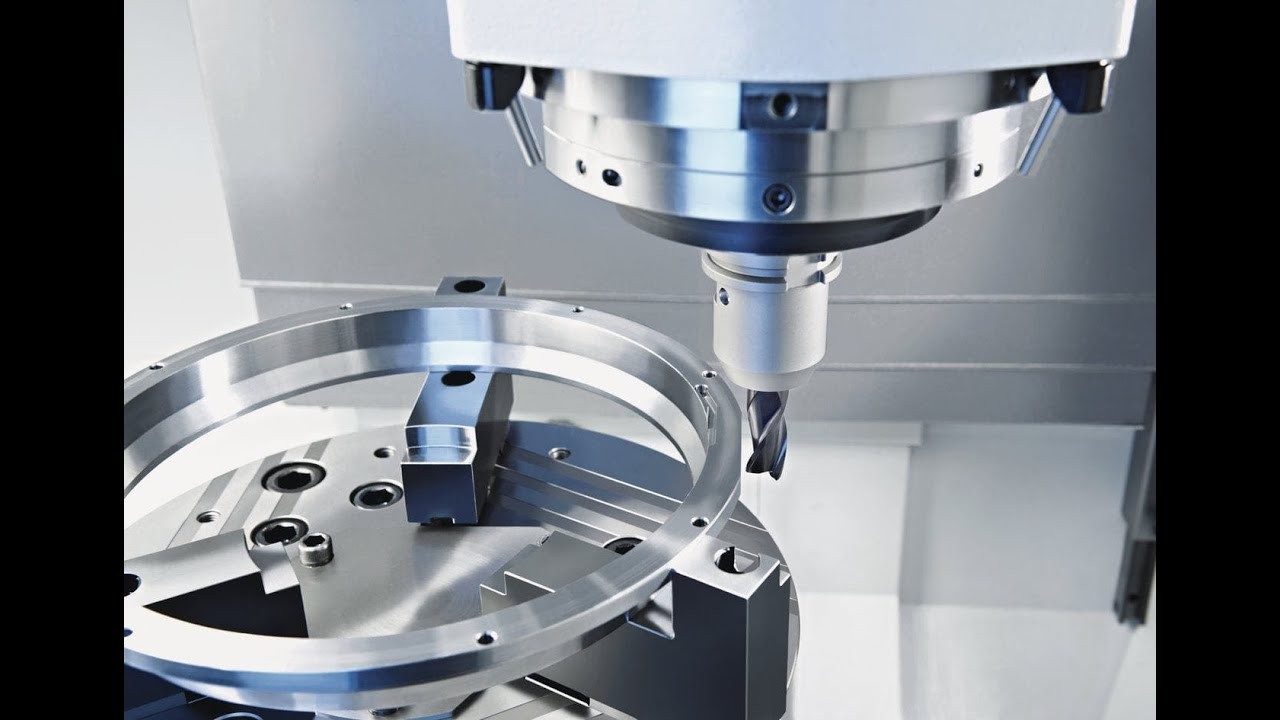
Face milling is a fundamental process in the world of manufacturing, allowing for the creation of flat surfaces on a workpiece. This operation utilizes a rotating cutter that moves across the surface of the material, removing excess material to achieve the desired shape and finish. It's one of the most common milling operations found in various industries, from automotive to aerospace.
Definition and Applications
Face milling is defined as a machining process where a flat surface is produced by cutting with a face mill cutter. This type of milling operation is particularly useful for creating large flat areas or cutting grooves into materials like metal or plastic. Common applications include machining engine blocks, creating precision parts, and preparing surfaces for welding or assembly.
Advantages of Face Milling
The advantages of face milling are numerous, making it one of the preferred types of milling operations in manufacturing. For starters, it offers high productivity due to its ability to remove large amounts of material quickly and efficiently. Additionally, face milling provides excellent surface finishes and dimensional accuracy, which are crucial for many engineering applications.
Tips for Successful Face Milling
To ensure successful face milling, it's essential to select appropriate milling cutters tailored to your specific project requirements. Understanding factors such as feed rate, depth of cut, and spindle speed can significantly enhance your results in milling machine operations. Moreover, maintaining proper tool geometry and ensuring adequate coolant flow can improve cutter lifespan while optimizing performance during various types of milling operations.
End Milling
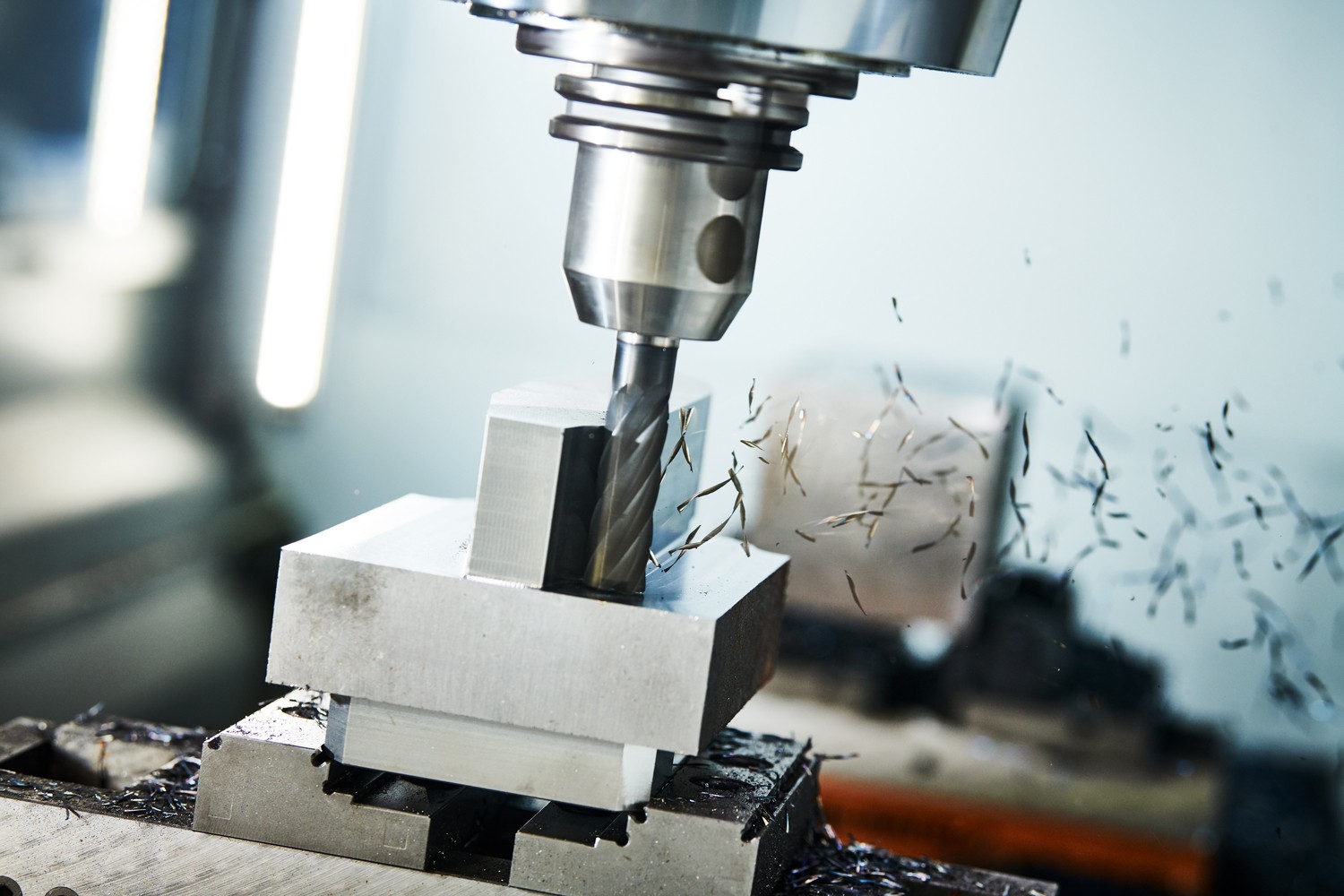
End milling is a pivotal process in the realm of manufacturing, falling under the umbrella of common milling operations. It involves the use of a rotating cutting tool, known as an end mill, to remove material from a workpiece. This operation is particularly effective for creating complex shapes and features, making it an essential technique in various types of milling operations.
What is End Milling?
So, what exactly is end milling? This operation utilizes a cylindrical cutter with teeth on the end and sides to cut into materials like metal or plastic. Unlike other types of milling operations that may focus solely on surface finishing or bulk material removal, end milling can create intricate designs and detailed contours by moving both vertically and horizontally across the workpiece.
End mills are versatile tools that can perform multiple tasks in one setup, such as drilling holes or creating slots and pockets. This flexibility makes them indispensable in machining environments where efficiency and precision are paramount. In essence, successful milling with end mills hinges on selecting the right tool for the job while understanding its capabilities.
Types of End Mills
When discussing end milling, it’s crucial to explore the various types of end mills available in today’s market. From square-end mills suitable for general-purpose machining to ball-end mills designed for contouring surfaces, each type serves unique functions within different types of milling operations. Other specialized options include corner-radius mills that provide rounded edges and taper-end mills used for angled cuts.
Moreover, materials used in manufacturing these cutters vary; high-speed steel (HSS) and carbide are common choices due to their durability and heat resistance. Each type has its advantages depending on the specific application—HSS offers cost-effectiveness while carbide provides superior longevity under high-stress conditions. Understanding these distinctions aids manufacturers in selecting appropriate milling cutters for successful milling processes.
Common Applications for End Milling
End milling finds its way into numerous industries due to its adaptability across various applications. In automotive manufacturing, it’s often employed to create precise engine components or intricate parts requiring tight tolerances; this showcases how critical successful milling can be when producing reliable machinery parts. Additionally, aerospace engineering utilizes end mills for crafting lightweight yet strong components essential for aircraft performance.
The versatility extends beyond heavy industries; even furniture design benefits from end milling techniques when shaping wood elements with complex profiles or decorative features. By leveraging different types of milling operations through effective use of end mills, manufacturers can enhance productivity while maintaining quality standards across their projects.
Peripheral Milling
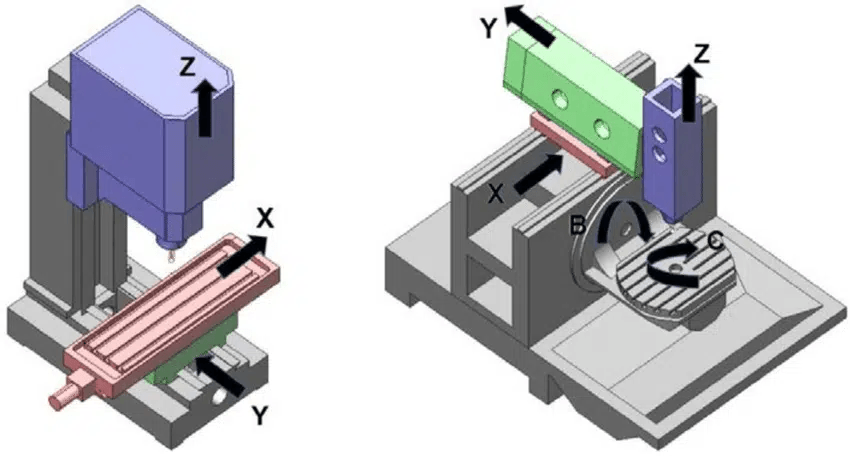
Peripheral milling is one of the essential types of milling operations that focuses on cutting along the periphery of the workpiece. This method effectively removes material and shapes components, making it a popular choice in various manufacturing processes. Understanding peripheral milling is crucial for optimizing machining efficiency and achieving desired outcomes.
Understanding Peripheral Milling
In peripheral milling, the cutting edges of the milling cutter engage primarily with the workpiece's surface, allowing for a more controlled and precise removal of material. This operation typically involves horizontal or vertical configurations, depending on the design of the milling machine used. It's crucial to differentiate peripheral milling from other types of milling operations, as it emphasizes depth and width cuts rather than just surface finishing.
The primary advantage of peripheral milling lies in its ability to handle large workpieces while maintaining accuracy. It is commonly employed to create slots, grooves, and flat surfaces on various materials such as metals and plastics. By harnessing different configurations and cutter designs, manufacturers can achieve diverse results tailored to their specific needs.
Key Techniques and Strategies
Successful peripheral milling requires careful planning regarding tool selection and machining parameters. Choosing appropriate milling cutters is vital; they come in various shapes like slab mills or face mills tailored for specific tasks within this operation type. Additionally, understanding feed rates, cutting speeds, and depth of cut can significantly impact overall efficiency during Milling Machine Operations.
One effective technique involves optimizing cutter geometry to enhance chip removal while minimizing tool wear—this contributes to what is considered successful milling practices in modern manufacturing environments. Regularly monitoring machine vibrations can also help detect potential issues before they escalate into costly downtime or defects in production quality.
Lastly, ensuring proper coolant application during peripheral milling can improve tool life by reducing heat buildup at the cutting edge—another key strategy for maximizing productivity while maintaining quality standards across common milling operations.
Benefits of Peripheral Milling
The benefits associated with peripheral milling are manifold; first among them is its ability to produce complex shapes with high precision quickly. This method is particularly advantageous when dealing with large volumes or intricate designs that require consistent results across multiple pieces—a hallmark feature in many industries today.
Moreover, utilizing advanced tooling systems allows for greater flexibility when transitioning between different types of milling operations without compromising performance or output quality. By embracing these techniques within their workflow, manufacturers can enhance production capabilities while reducing operational costs—ultimately leading to increased profitability.
In summary, understanding how peripheral milling integrates into broader manufacturing processes highlights its significance among various types of machining methods available today—and why selecting suitable tools plays such an essential role in achieving successful outcomes across all facets of Milling Cutters and Milling Operations.
Slab Milling
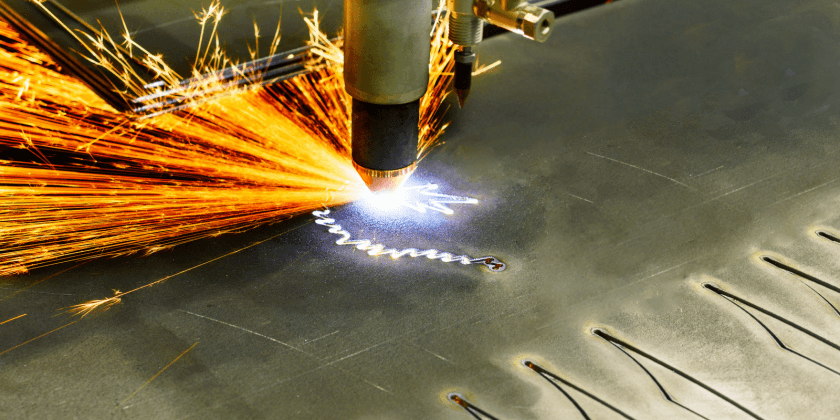
Slab milling is one of the fundamental types of milling operations used in the manufacturing industry. It involves using a flat, wide cutter to remove material from a workpiece's surface, effectively creating a smooth and even finish. This method is particularly useful for producing flat surfaces, making it an essential technique in various machining applications.
Introduction to Slab Milling
In slab milling, the cutter is mounted on the spindle of a milling machine, rotating against the workpiece. This operation is primarily aimed at generating flat surfaces or taking off large amounts of material quickly. When considering what are the different types of milling operations, slab milling stands out due to its efficiency and ability to handle large components with ease.
Tools Used in Slab Milling
The primary tool used in slab milling is known as a slab cutter or face mill, which features multiple cutting edges for optimal performance. These cutters come in various sizes and configurations depending on the specific requirements of the job at hand; larger cutters can tackle more extensive areas while smaller ones are better suited for precision work. Understanding different types of milling operations means recognizing how essential these milling cutters and their designs are for successful milling outcomes.
Best Practices for Slab Milling
To achieve successful slab milling results, it's crucial to adhere to best practices that enhance efficiency and quality. First and foremost, selecting the right cutting speed and feed rate will significantly impact your results; too fast can lead to tool wear while too slow may cause inefficiencies. Additionally, ensuring proper alignment between the workpiece and cutter helps prevent issues that could arise during common milling operations—like chatter or uneven finishes—ultimately leading to smoother production processes.
Groove Milling
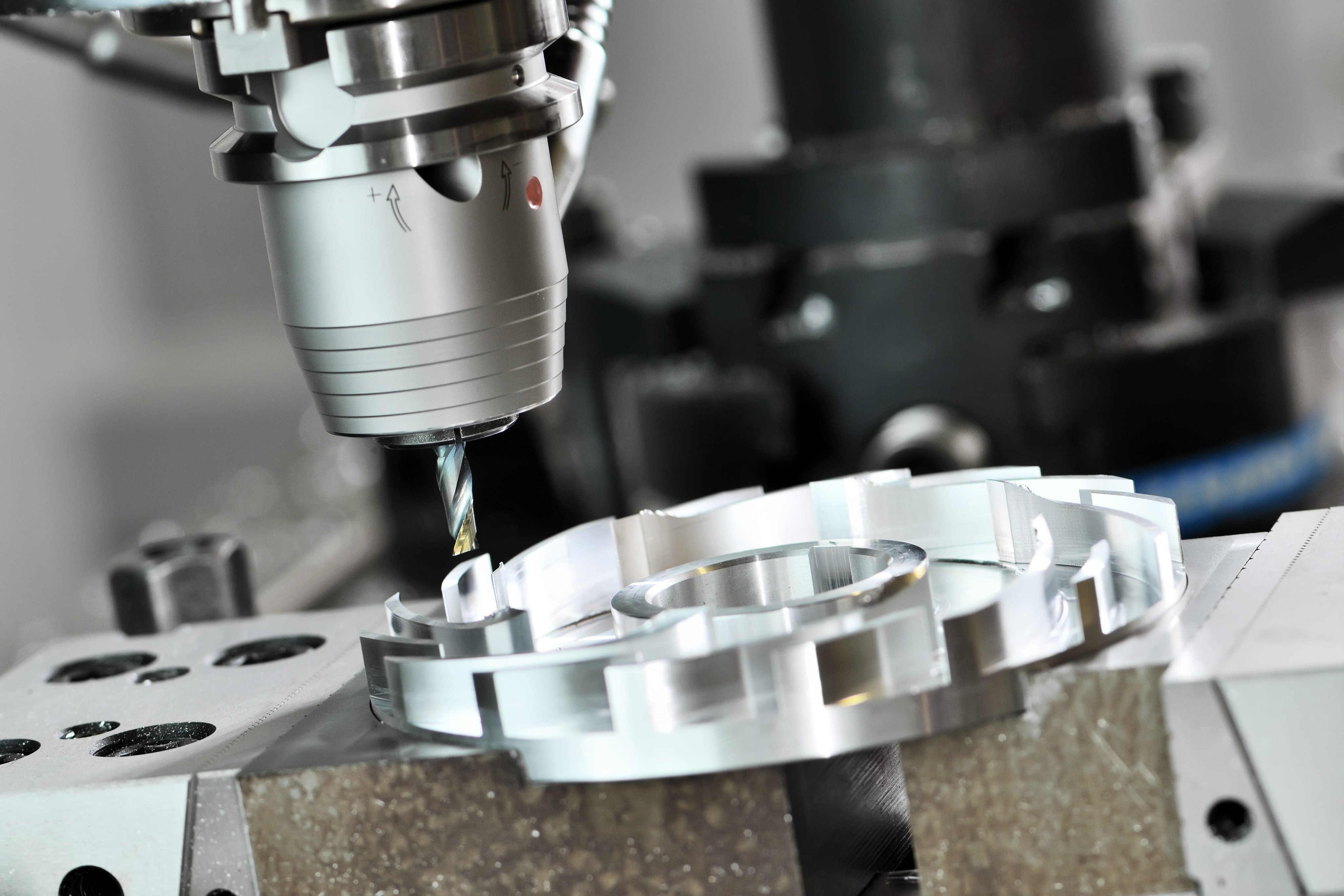
Groove milling is a specialized type of milling operation that involves creating grooves or channels in a workpiece. This process is essential for producing features like slots, keyways, and other indentations necessary for assembly or function. Understanding groove milling is crucial for optimizing various manufacturing processes, as it falls under the umbrella of common milling operations.
What is Groove Milling?
At its core, groove milling refers to the process of using a milling machine to cut specific shapes or grooves into materials like metal, plastic, or wood. It typically employs specialized milling cutters designed for precision and efficiency in creating these features. By using different types of milling operations and varying cutter designs, manufacturers can achieve desired geometries and tolerances critical to their projects.
Applications in Different Industries
Groove milling finds applications across various industries such as automotive, aerospace, and construction. For instance, in the automotive sector, groove milling creates keyways in shafts that allow for secure fittings with gears or pulleys. Similarly, aerospace components often require precise grooves to accommodate fasteners or seals that ensure structural integrity during flight.
Optimizing Groove Milling for Efficiency
To achieve successful milling outcomes when performing groove operations, it's essential to optimize both tool choice and machining parameters. Selecting the right type of cutter from the range of available milling cutters can significantly impact efficiency and finish quality. Additionally, fine-tuning feed rates and spindle speeds based on material properties ensures that groove milling processes are not only effective but also economically viable.
Conclusion
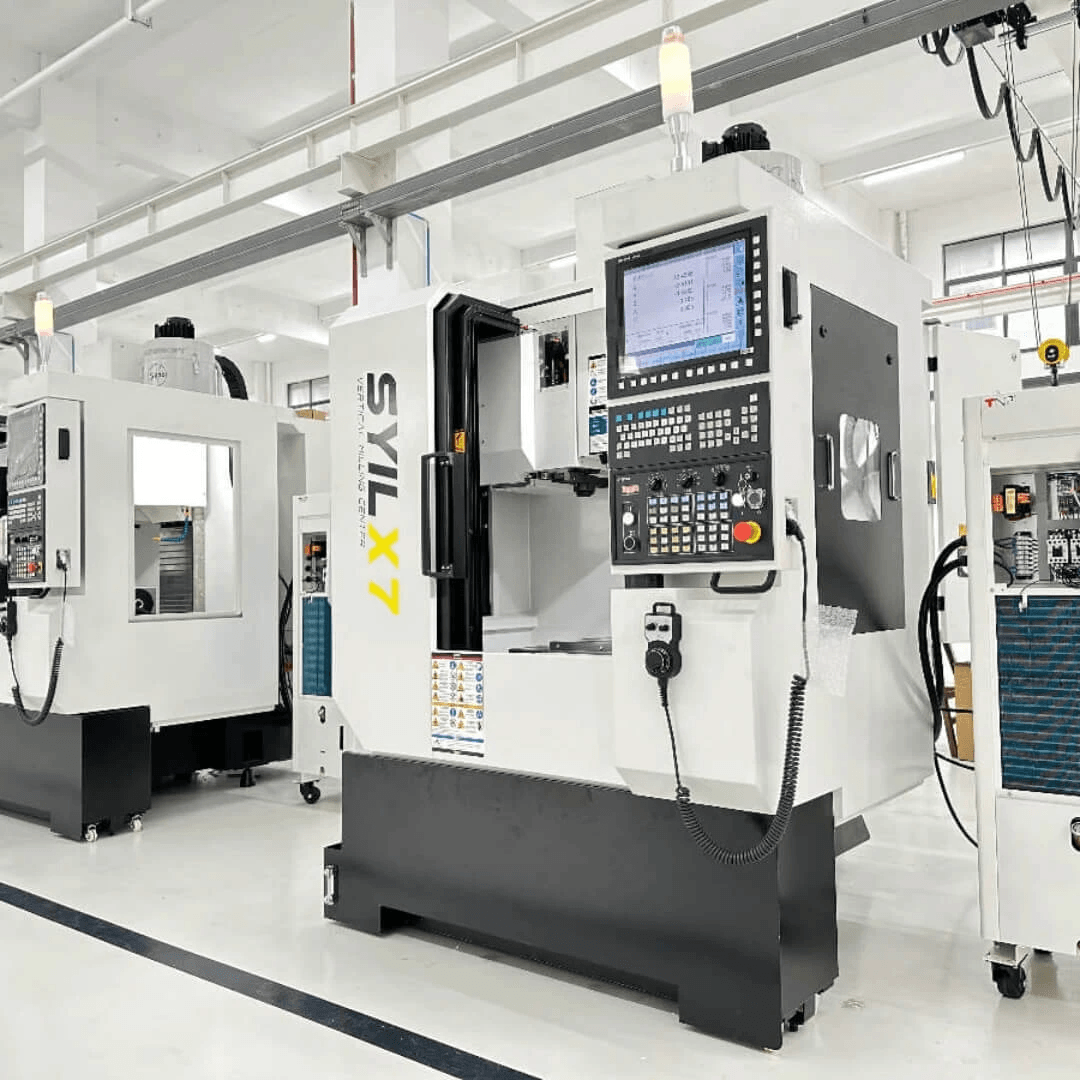
In wrapping up our exploration of milling operations, it's clear that understanding the various types of milling operations is essential for optimizing manufacturing processes. From face milling to groove milling, each type offers unique benefits and applications that can significantly impact production efficiency. Moreover, the right choice of milling cutters and machines plays a pivotal role in ensuring successful milling outcomes.
Key Takeaways on Milling Operations
When considering what are the different types of milling operations, it becomes evident that each serves a specific purpose in manufacturing. Face milling is ideal for creating flat surfaces, while end milling excels in producing intricate shapes and contours. Understanding these distinctions enables manufacturers to select the most suitable method for their specific needs, ultimately enhancing their overall productivity.
Importance of Selecting the Right Machine
Selecting the right machine is crucial when evaluating milling machine operations. The capabilities of different machines can greatly influence the quality and efficiency of the finished product. By aligning machine specifications with project requirements—whether it's precision or speed—manufacturers can avoid costly mistakes and ensure successful milling processes.
Enhancing Production with Successful Milling
Successful milling hinges on not just choosing the right type but also optimizing every aspect of your operation—from tool selection to machining strategies. By leveraging advanced techniques alongside appropriate tools like specialized milling cutters, businesses can streamline their production lines effectively. Ultimately, focusing on common milling operations allows manufacturers to boost output while maintaining high standards of quality.