Introduction
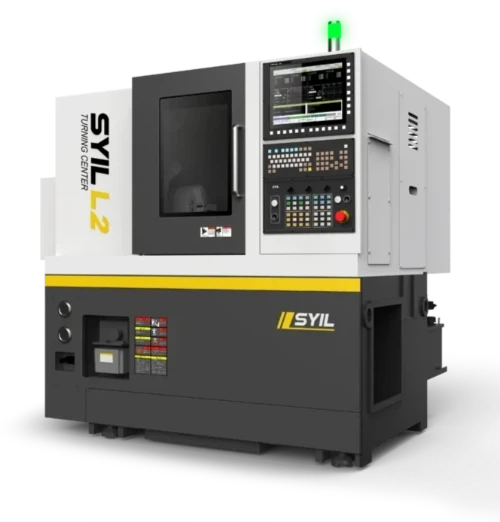
Overview of Surface Milling Machines
A surface milling machine is engineered to perform a variety of tasks, from cutting and shaping materials to producing smooth finishes on metal and other substrates. Unlike other types of milling machines, this specific category focuses on achieving high precision in surface treatment and finishing processes. With various models available, each offers unique features that cater to different machining and milling needs.
Importance of Choosing the Right Manufacturer
Selecting the right manufacturer for your surface milling machine can significantly impact your production efficiency and product quality. A reputable manufacturer not only provides reliable machinery but also offers support in terms of maintenance and upgrades, ensuring your milling machine remains at peak performance. The right choice can lead to enhanced productivity and reduced operational costs in your machining operations.
Key Features to Consider
When evaluating different milling machine models, it's essential to consider key features such as spindle speed, feed rate, cutting tool compatibility, and overall build quality. These attributes determine how effectively a milling machine can handle various materials while maintaining precision during operation. Additionally, advanced technologies like CNC capabilities are becoming increasingly important in modern machining and milling applications.
Leading Manufacturers in Surface Milling
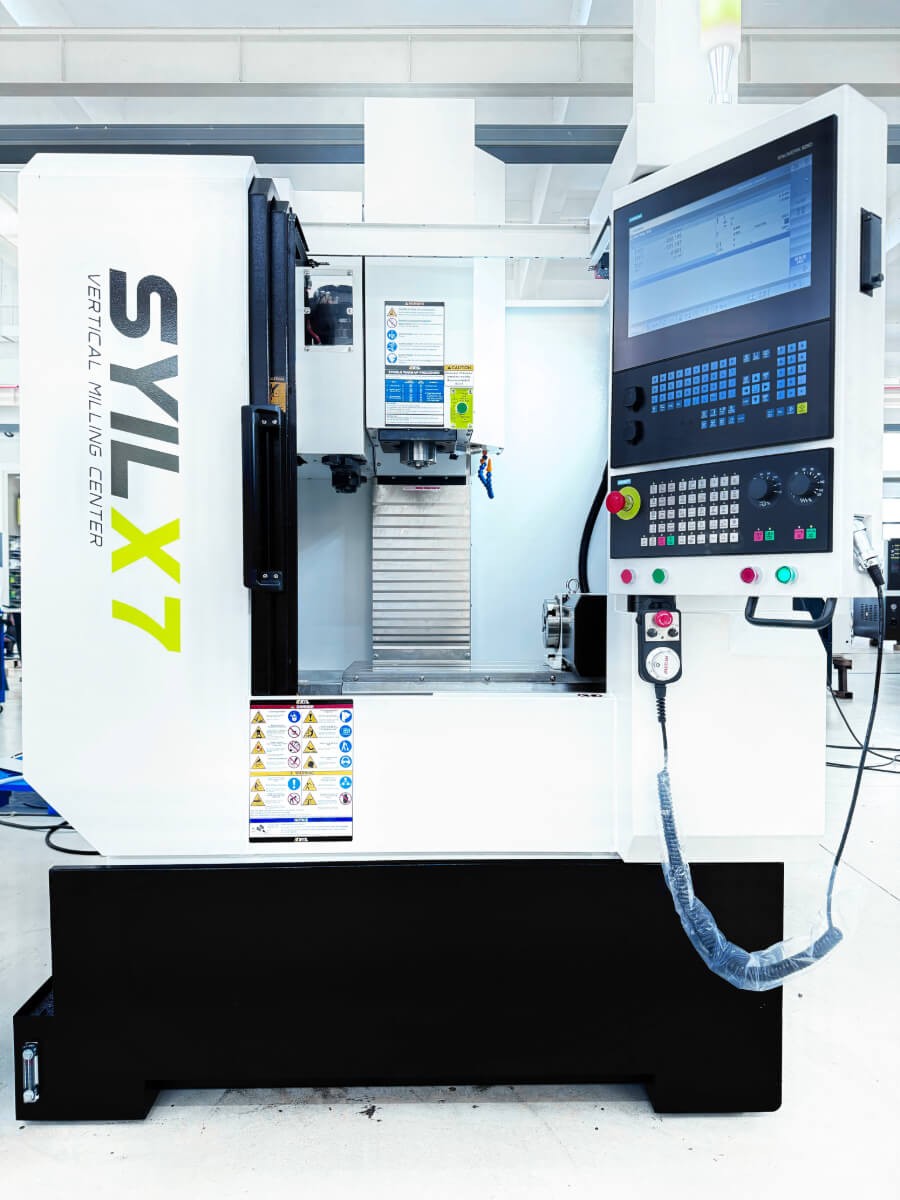
When it comes to surface milling machines, the choice of manufacturer can significantly influence the quality and efficiency of milling machining. The right milling machine model not only enhances productivity but also ensures precision in machining and milling operations. In this section, we delve into three leading manufacturers that are making waves in the world of surface milling: SYIL CNC Machines, Haas Automation, and DMG MORI.
SYIL CNC Machines: Revolutionizing Milling
SYIL CNC Machines has carved a niche for itself by revolutionizing the concept of surface milling machines with its innovative designs and advanced technology. Known for their user-friendly interface and robust performance, SYIL's offerings cater to both small workshops and large manufacturing facilities alike. The emphasis on high-quality components ensures that every milling machine machine they produce meets rigorous industry standards while delivering exceptional precision.
What sets SYIL apart is their commitment to affordability without sacrificing quality; their machines are designed for efficiency in machining and milling processes. With a focus on customization, customers can tailor their milling machine models to meet specific needs, making it easier than ever to achieve desired outcomes in various applications. This adaptability makes SYIL an attractive choice for businesses looking to invest in reliable surface milling solutions.
Haas Automation: Precision at Its Best
Haas Automation is synonymous with precision engineering when it comes to surface milling machines. Their extensive range of products showcases state-of-the-art technology that enhances accuracy in every cut made by their milling mc systems. With a reputation built on years of experience, Haas continues to lead the market by providing machines that excel in both performance and reliability.
The company's commitment to innovation is evident through its continuous advancements in CNC programming capabilities, which streamline operations while maximizing output efficiency. Moreover, Haas's dedication to customer support ensures that users can make the most out of their investments in machining and milling equipment. For those seeking top-tier performance from a trusted brand, Haas Automation stands out as a premier option.
DMG MORI: Innovating in Milling Technology
DMG MORI takes pride in being at the forefront of innovation within the realm of surface milling technology. Renowned for integrating cutting-edge features into their machinery, DMG MORI offers solutions that push the boundaries of what’s possible with traditional machining methods. Their commitment to research and development has resulted in some truly remarkable advancements tailored specifically for modern manufacturing challenges.
With an extensive portfolio encompassing various types of machines—including some highly specialized models—DMG MORI caters to diverse industries requiring precision-driven solutions for complex tasks. The integration of automation within their systems enhances productivity while reducing manual intervention during machining processes—a win-win situation for any business looking to optimize operations! As they continue innovating within this space, DMG MORI remains a key player shaping the future landscape of surface milling machinery.
Understanding Surface Milling Machines
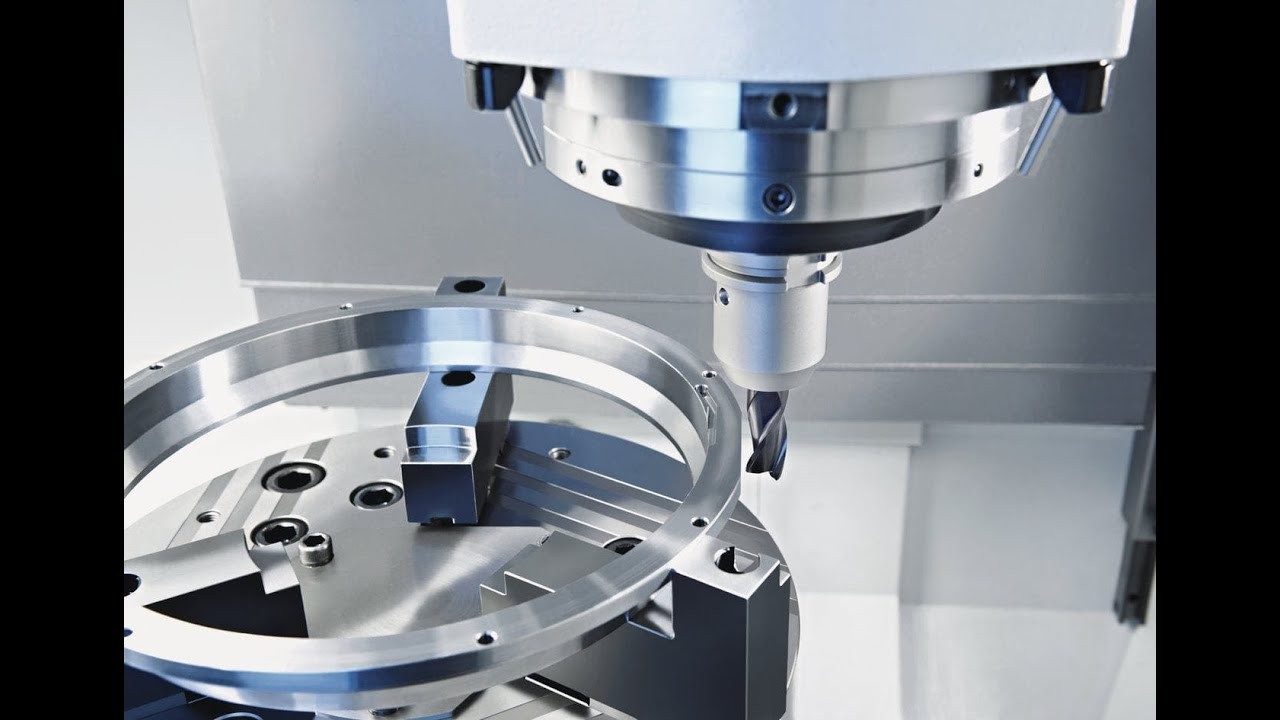
Surface milling machines are essential tools in the world of manufacturing, designed to create flat surfaces on workpieces. These machines utilize a rotating cutting tool that removes material from the surface of the workpiece, ensuring precision and uniformity. With their versatility and efficiency, surface milling machines play a crucial role in various machining processes.
What is a Surface Milling Machine?
A surface milling machine is a type of milling machine specifically engineered to produce flat surfaces on metal or other materials. It typically features a horizontal spindle with cutting tools that move across the workpiece, allowing for precise depth and width adjustments during machining and milling operations. The design of these machines enables them to handle large workpieces efficiently while maintaining exceptional accuracy—an essential aspect in any milling machine model.
Applications in Diverse Industries
Surface milling machines find applications across numerous industries, including automotive, aerospace, and manufacturing sectors. They are used to create components such as engine blocks, brackets, and various other parts requiring flat surfaces for assembly or further processing. The versatility of these machines allows them to adapt to different materials—be it steel, aluminum, or plastics—making them indispensable in modern milling machining practices.
Comparison with Other Milling Machines
When comparing surface milling machines with other types of milling machines, several factors come into play—such as functionality and precision capabilities. While vertical mills may excel at drilling operations or creating complex shapes, surface milling machines primarily focus on achieving smooth finishes on flat surfaces. Additionally, they often offer greater stability during machining due to their robust construction compared to some lighter models found in the broader category of the milling machine machine family.
The Role of Machining and Milling in Industry
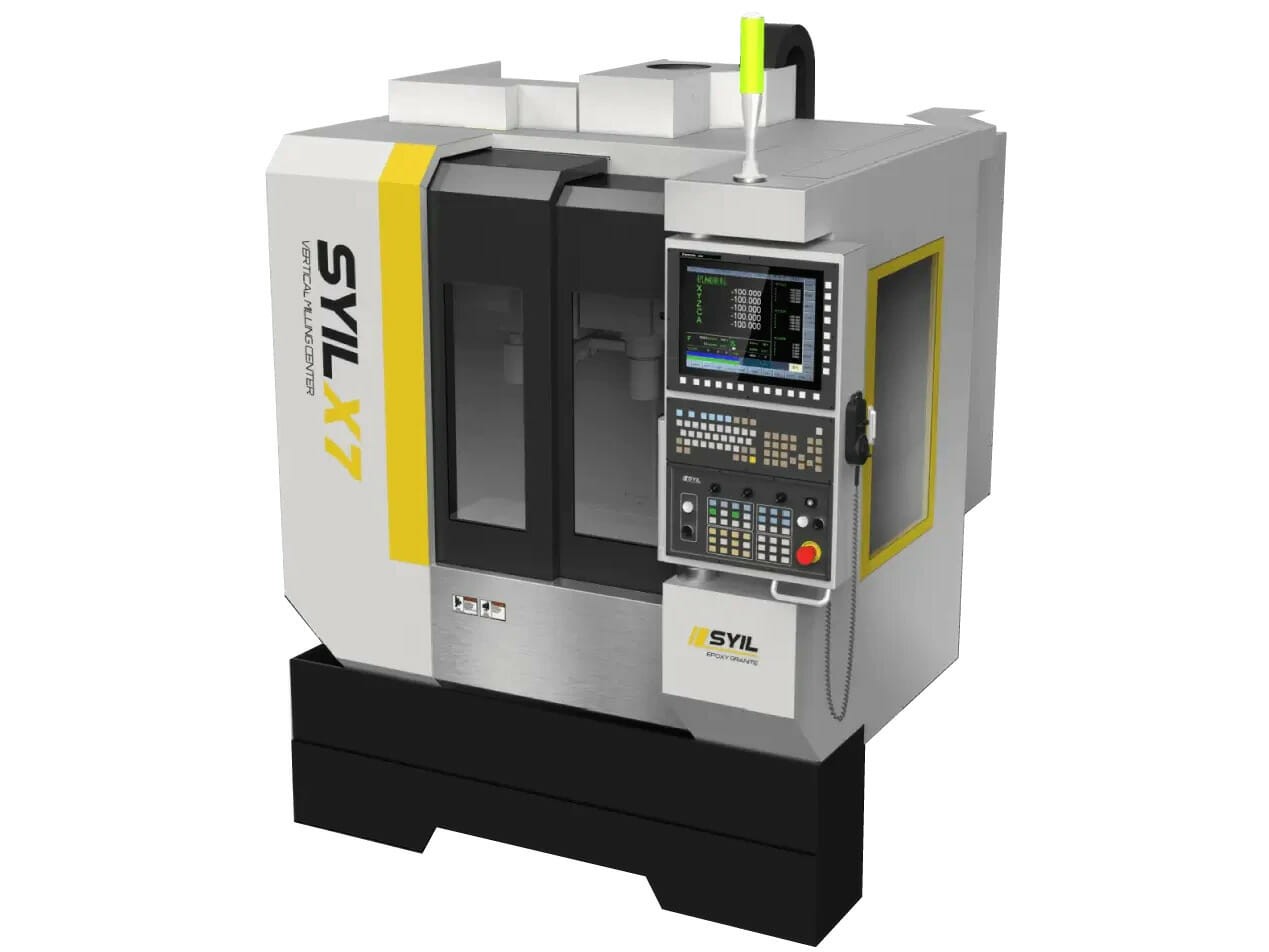
Machining and milling play pivotal roles in the manufacturing landscape, driving efficiency and precision across a multitude of sectors. The surface milling machine is at the forefront, optimizing production processes and ensuring high-quality outputs. As industries evolve, understanding how these technologies enhance operations becomes essential for manufacturers aiming to stay competitive.
How Milling Enhances Manufacturing Efficiency
Milling enhances manufacturing efficiency by streamlining processes that once took hours or even days to complete. With the advent of advanced milling machine models, tasks that require intricate cuts and shapes can now be executed swiftly and with minimal waste. This not only saves time but also reduces material costs, allowing businesses to allocate resources more effectively.
Moreover, the integration of CNC technology into milling machining has revolutionized how manufacturers approach production. Automated systems can operate continuously with little human intervention, leading to increased output rates without sacrificing quality. Ultimately, the efficiency gained through modern surface milling machines translates into higher profit margins for companies willing to invest in cutting-edge technology.
Innovations in Milling Machining Techniques
The world of machining and milling is witnessing rapid innovations that are reshaping traditional practices. New techniques such as 5-axis milling allow for complex geometries to be machined in a single setup, vastly improving workflow efficiency compared to older methods. These advancements enable manufacturers to tackle more challenging designs while maintaining accuracy—something that's crucial when working with high-tolerance components.
Additionally, developments in tooling materials have enhanced the capabilities of milling machines significantly. Tools made from advanced composites or coated with specialized materials can withstand higher temperatures and resist wear better than ever before. This means that the lifespan of tools increases while performance remains top-notch—an absolute win-win for any operation relying on a reliable milling machine model.
The Importance of Precision in Machining
Precision is non-negotiable when it comes to machining and milling; even the slightest deviation can lead to costly errors down the line. Surface milling machines are engineered for high accuracy, ensuring that every cut adheres strictly to specifications set by engineers and designers alike. This level of precision is especially critical in industries such as aerospace or medical device manufacturing where tolerances are razor-thin.
Furthermore, achieving consistent precision requires not only top-of-the-line equipment but also skilled operators who understand their machinery inside out—the perfect marriage between man and machine! Continuous training on new technologies helps operators maximize their use of various milling machine models while ensuring they adhere to best practices in quality control measures throughout production runs.
In conclusion, as we delve deeper into how machining enhances industry standards through innovations like those found within modern surface milling machines, it becomes evident that this field will continue evolving rapidly—a trend no manufacturer can afford to ignore!
Choosing the Right Milling Machine Model
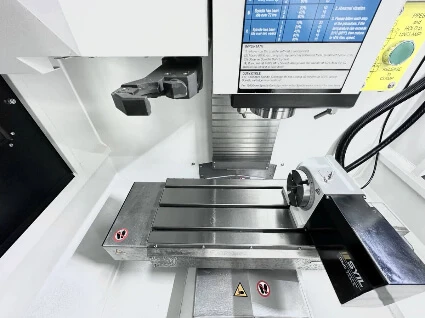
Selecting the right milling machine model is crucial for optimizing your machining and milling processes. With a variety of options available, understanding your specific needs can make all the difference in productivity and efficiency. Whether you’re a seasoned machinist or just starting out, knowing what to look for will help you find the perfect surface milling machine.
Factors to Consider in Model Selection
When choosing a milling machine model, several factors come into play that can significantly impact your operations. First and foremost, consider the size and complexity of the parts you'll be machining; different models are designed for various scales of production and types of materials. Additionally, pay attention to the precision requirements; a high-precision surface milling machine may be necessary for intricate designs, while simpler tasks might allow for more basic models.
Another critical aspect is the type of control system used in the milling machine; CNC (Computer Numerical Control) systems often offer greater flexibility and repeatability compared to manual machines. You should also evaluate maintenance needs and availability of parts from manufacturers—after all, a reliable support system can save you time and money in the long run. Lastly, don’t forget about budget constraints; balancing cost against features is key when investing in a quality milling machine.
Popular Milling Machine Models
Several milling machine models have gained popularity due to their reliability and versatility in machining applications. The SYIL X5 series, known for its compact design and user-friendly interface, has become a favorite among small-to-medium enterprises looking to enhance their capabilities without breaking the bank. On the other hand, Haas Automation's VF Series offers robust performance with advanced features suitable for heavy-duty machining tasks.
For those seeking cutting-edge technology, DMG MORI’s DMU series provides an exceptional blend of speed and precision that appeals to high-end manufacturing environments. Other notable mentions include Bridgeport’s Series I knee mill—an industry classic—and newer entrants like Tormach’s PCNC series that cater specifically to hobbyists and small businesses needing affordable yet capable machines. Each model has its own strengths tailored toward specific applications within machining.
Tailoring Machines for Specific Applications
Tailoring your choice of surface milling machine to specific applications can greatly enhance productivity in machining tasks. For instance, if you're involved primarily in aerospace or automotive industries where precision is paramount, investing in high-accuracy CNC models would be wise as they deliver exceptional results on complex geometries while maintaining tight tolerances during production runs.
Conversely, if your work revolves around prototyping or smaller-scale projects requiring flexibility over volume production, consider versatile machines that allow quick setup changes—these are invaluable when dealing with diverse materials or designs on-the-fly. Moreover, integrating automation features into your chosen model can streamline operations further by reducing manual intervention during repetitive tasks—a significant boon for efficiency-focused facilities.
Ultimately, understanding how different features align with your specific needs will guide you toward selecting an ideal milling machine model that not only meets but exceeds expectations within your unique operational context.
Future Trends in Surface Milling Technology
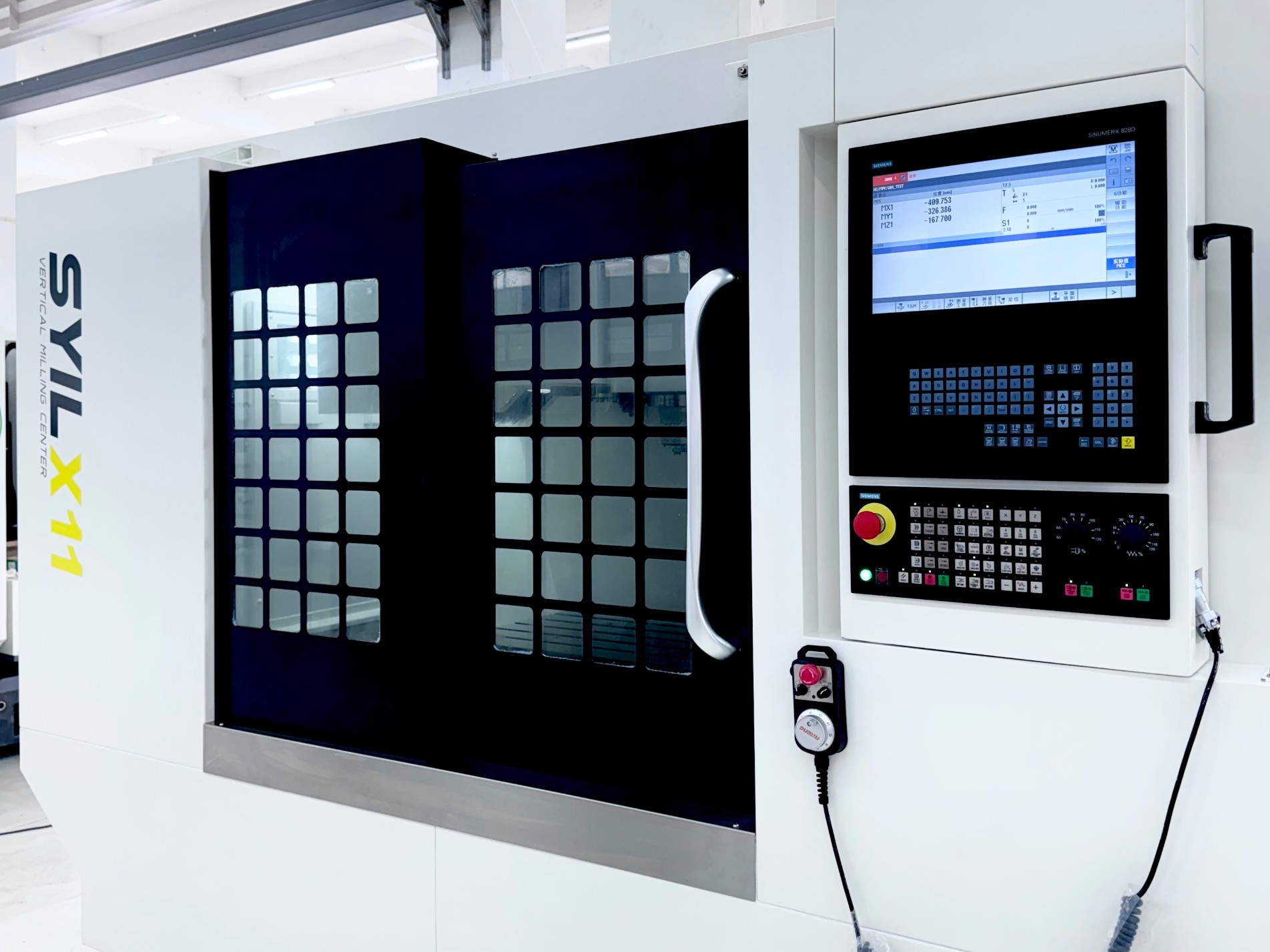
In the ever-evolving landscape of manufacturing, surface milling machines are at the forefront of innovation. These machines are not just tools; they're gateways to enhanced efficiency and precision in machining and milling. As we look ahead, several key trends are shaping the future of milling technology, ensuring that it remains a critical component in various industries.
Advancements in CNC Milling Machines
CNC (Computer Numerical Control) technology has revolutionized the way we approach surface milling machines. With advancements such as enhanced software algorithms and improved hardware components, modern CNC milling machines offer unprecedented levels of accuracy and repeatability. These innovations enable manufacturers to produce complex parts with intricate designs, making the milling machine model more versatile than ever before.
Moreover, new features like adaptive machining allow these machines to adjust their operations based on real-time feedback from sensors. This adaptability not only boosts efficiency but also minimizes waste during production—a win-win for both manufacturers and the environment. As CNC technology continues to advance, we can expect even more sophisticated capabilities that will redefine what’s possible in milling machining.
The Rise of Automation in Milling
Automation is no longer just a buzzword; it’s becoming a cornerstone of modern manufacturing processes, particularly in milling operations. The integration of robotics with surface milling machines is streamlining workflows and reducing human error significantly. With automated systems taking over repetitive tasks, operators can focus on more complex aspects of machining and milling, thus enhancing overall productivity.
Additionally, automated systems can operate around the clock without fatigue or breaks—something that manual labor simply cannot compete with! This shift towards automation is driving down costs while simultaneously increasing output quality across various sectors using the milling machine machine for production purposes. The future clearly points toward an era where smart factories leverage automation to optimize every aspect of their operations.
Sustainability in Machining and Milling
As industries become increasingly aware of their environmental impact, sustainability is emerging as a critical trend within machining and milling practices. Manufacturers are exploring eco-friendly materials and energy-efficient technologies that minimize waste during production processes involving surface milling machines. The emphasis on sustainable practices not only meets regulatory requirements but also appeals to environmentally conscious consumers.
Furthermore, advancements in cutting tool technology have led to longer-lasting tools that require less frequent replacement—reducing both material waste and costs associated with tooling maintenance for various milling machine models. By prioritizing sustainability within their operations, businesses can enhance their reputation while contributing positively to global efforts aimed at reducing carbon footprints associated with traditional manufacturing methods.
Conclusion
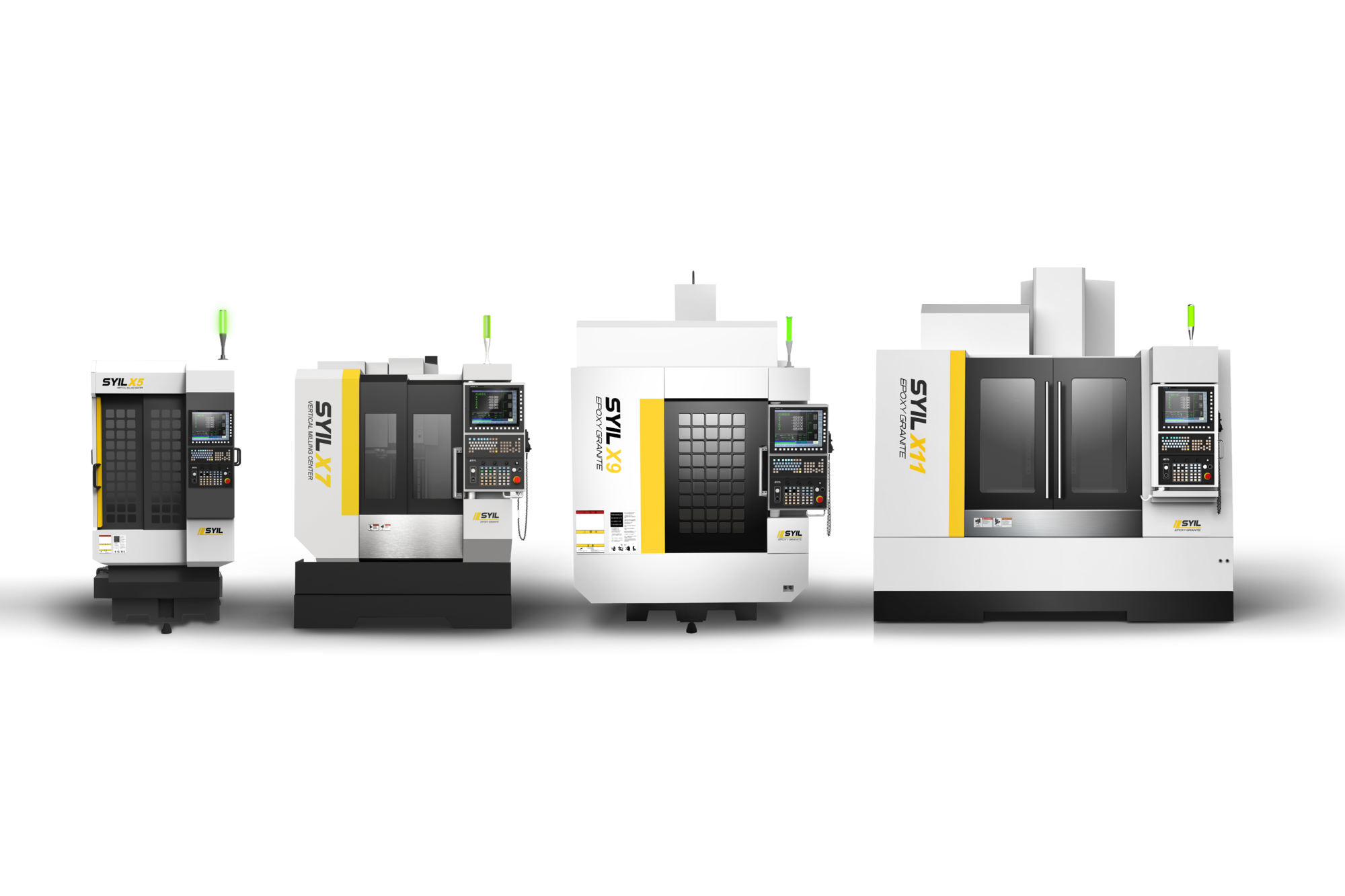
As we wrap up our exploration of surface milling machines, it’s clear that choosing the right manufacturer is crucial for achieving optimal results in machining and milling. From SYIL CNC Machines’ innovative approaches to Haas Automation’s precision engineering, and DMG MORI’s technological advancements, there are standout players in the market. Each of these manufacturers brings unique strengths to the table, making them worthy considerations for anyone looking to invest in a milling machine.
Recap of Top Surface Milling Machine Manufacturers
In summary, SYIL CNC Machines has been revolutionizing the industry with their user-friendly designs and robust performance. Haas Automation continues to be synonymous with precision and reliability in milling machining, while DMG MORI pushes boundaries with its cutting-edge technology and innovative solutions. When selecting a surface milling machine, evaluating these manufacturers can significantly impact your machining efficiency and product quality.
Key Takeaways for Buyers
For buyers entering the market for a new milling machine model, it’s essential to assess various factors such as precision, durability, and application versatility. Understanding your specific needs will help you narrow down options that best suit your production requirements in machining and milling. Additionally, staying informed about the latest trends can give you an edge when making decisions about which milling machine to invest in.
Looking Ahead: The Future of Milling Technology
The future of surface milling technology looks bright with advancements like CNC integration enhancing automation capabilities within the industry. As sustainability becomes increasingly important in manufacturing processes, innovations aimed at reducing waste while improving efficiency are on the rise. Embracing these changes will be vital for businesses looking to stay competitive in a rapidly evolving landscape of milling in machining.