Introduction
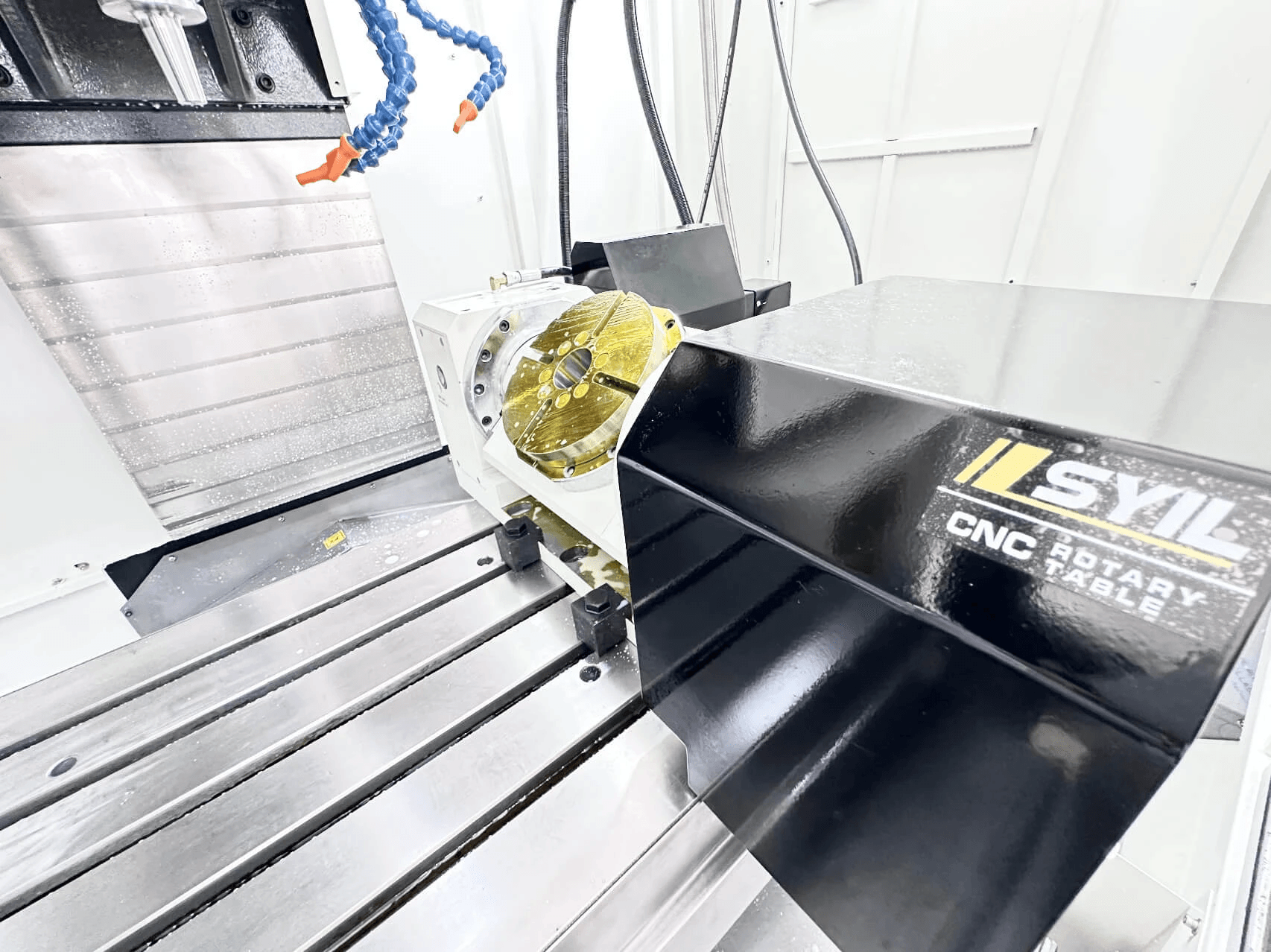
Milling is an essential process in the world of manufacturing, serving as a backbone for many industries. Understanding milling machine operations is crucial for anyone looking to delve into CNC machining or precision machining. Whether you're crafting intricate components or bulk parts, the milling machine plays a pivotal role in transforming raw materials into functional products.
Understanding the Basics of Milling
At its core, milling involves removing material from a workpiece using rotary cutting tools. This process can be performed on various types of milling machines, including traditional and CNC milling machines, each offering unique capabilities and precision levels. By grasping the basics of how these machines operate, one can appreciate their efficiency and versatility in producing high-quality components.
Importance of Milling in Manufacturing
Milling is not just another manufacturing technique; it’s a critical element that enhances productivity and quality across various sectors. With the advent of CNC machining, manufacturers can achieve unprecedented levels of accuracy and repeatability in their operations. The significance of milling machine operations extends beyond simple part creation; it also influences design flexibility and overall production efficiency.
Overview of Milling Machine Operations
Milling machine operations encompass a range of techniques used to shape materials through controlled cutting processes. From setting up the machine to selecting appropriate cutting tools, every step is vital for achieving desired outcomes in CNC manufacturing. Understanding these operations allows operators to optimize performance, ensuring that each piece meets strict quality standards while minimizing waste and downtime.
What is Milling?
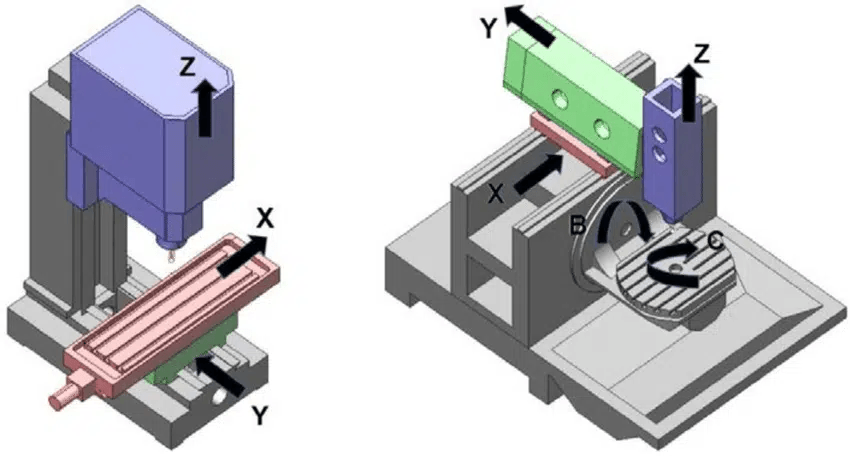
Milling is a vital process in manufacturing that involves the removal of material from a workpiece using rotary cutting tools. This technique shapes and finishes parts to precise specifications, making it essential for various industries, including aerospace, automotive, and medical. Understanding milling machine operations can significantly enhance the efficiency and quality of production.
Definition and Purpose of Milling
At its core, milling refers to the machining process where a rotating cutting tool removes material from a stationary workpiece. The purpose of milling is to create complex shapes, slots, holes, and contours that are often impossible to achieve with other methods. In the realm of CNC machining metal, precision is key; thus, milling serves as an indispensable technique for producing high-quality components.
History and Evolution of Milling
The history of milling dates back centuries, with early versions utilizing simple hand-cranked devices for grain processing. As industrialization progressed in the 19th century, the introduction of mechanized milling machines revolutionized manufacturing capabilities by increasing speed and accuracy. Today’s CNC milling machines represent the pinnacle of this evolution—integrating advanced technology that allows for automated precision machining at unprecedented levels.
Key Components of a Milling Machine
A typical milling machine consists of several key components that work together to facilitate complex machining tasks. The main parts include the spindle (which holds the cutting tool), table (where the workpiece is mounted), and various controls that dictate movement and speed settings for precision machining operations. Understanding these components helps operators maximize their efficiency during CNC milling processes while ensuring optimal results in their projects.
Types of Milling Machines
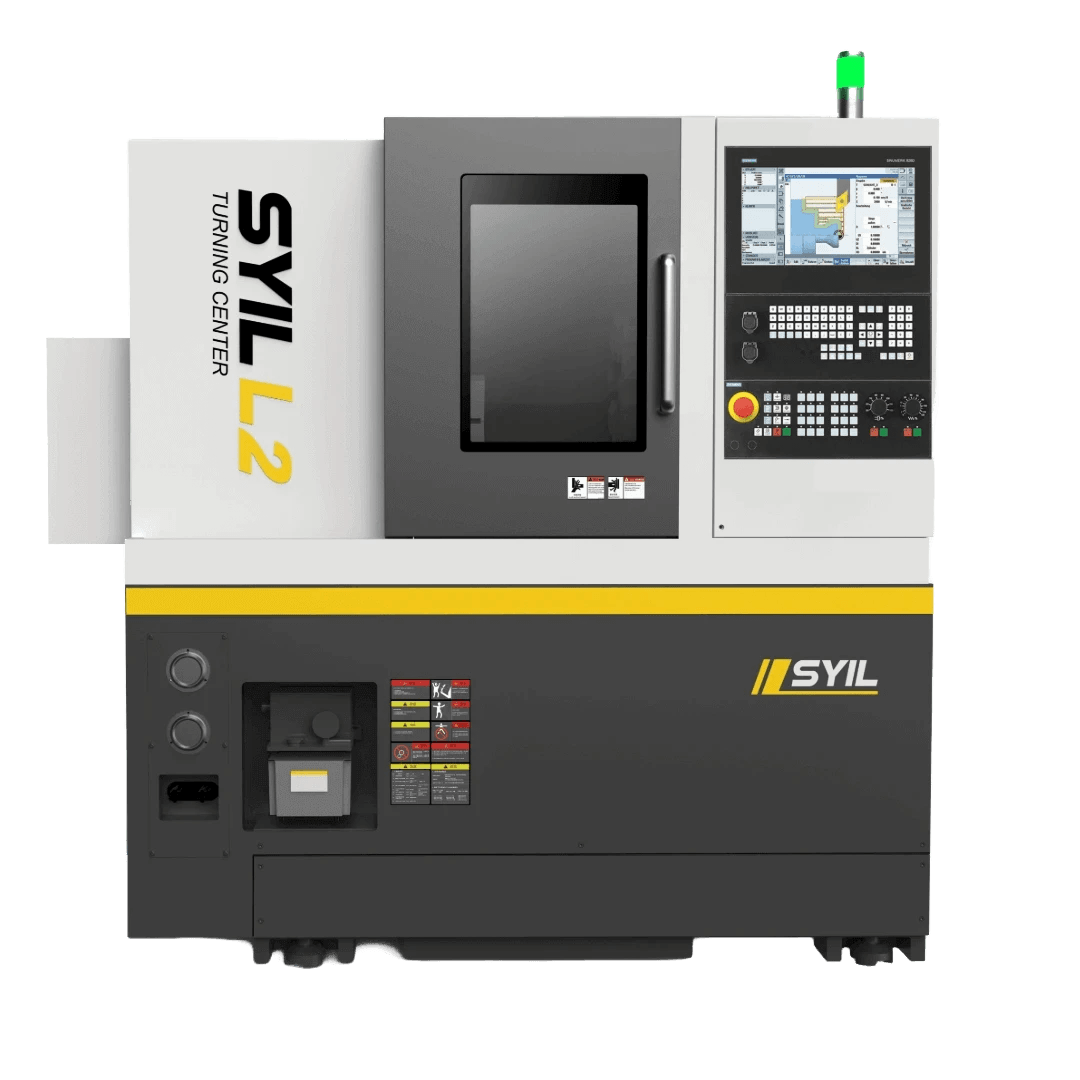
When it comes to milling machine operations, understanding the various types of milling machines is essential for any manufacturer or hobbyist. Each type has its own unique characteristics, advantages, and applications that cater to different needs in precision machining and CNC manufacturing. Here, we’ll delve into the most common types: vertical and horizontal milling machines, as well as CNC milling machines.
Vertical and Horizontal Milling Machines
Vertical and horizontal milling machines represent the two primary configurations in the world of milling machine operations. Vertical milling machines have a spindle that is oriented vertically, allowing for intricate cuts and detailed work on materials like metal and wood; they excel at producing complex shapes with high precision. On the other hand, horizontal milling machines feature a horizontally oriented spindle which is ideal for larger workpieces and can handle heavier cutting tasks with ease.
Both types come equipped with various cutting tools designed to achieve specific results in machining projects. For example, vertical mills are often used for drilling or making keyways, while horizontal mills are preferred for tasks like slab cutting or gear manufacturing. Understanding these differences helps operators choose the right machine based on project requirements in CNC machining.
Overview of CNC Milling Machines
CNC (Computer Numerical Control) milling machines take traditional milling to a whole new level by automating the process through computer programming. This innovation allows for enhanced precision machining capabilities where complex designs can be executed with minimal human intervention—making them indispensable in modern manufacturing environments. With CNC technology, operators can create intricate parts consistently while reducing waste material during production.
CNC milling machines come equipped with advanced features such as multi-axis movement, allowing them to perform diverse operations without needing to reposition workpieces manually. This versatility makes CNC machining metal incredibly efficient compared to conventional methods where manual adjustments are necessary frequently. The ability to produce high-quality components at scale has made CNC technology a game-changer in industries ranging from aerospace to automotive.
Advantages of SYIL CNC Machines
SYIL CNC machines stand out among other options available on the market due to their robust design and user-friendly interface tailored towards both professionals and enthusiasts alike. One major advantage is their affordability without compromising on quality—making them an attractive choice for small businesses looking to invest in reliable CNC machinery for precision machining tasks. Additionally, SYIL offers various models that cater specifically to different applications within CNC manufacturing.
Another significant benefit lies in their compatibility with various cutting tools which enhances operational flexibility during different projects; whether it’s aluminum or steel parts being machined, SYIL's range adapts seamlessly to meet diverse demands effectively. Moreover, their emphasis on customer support ensures users can optimize their milling machine operations without feeling overwhelmed by technical challenges often associated with advanced machinery setups.
In conclusion, understanding the types of milling machines available—including vertical and horizontal models along with specialized SYIL CNC options—provides a solid foundation for anyone interested in diving deeper into the world of precision machining and effective production techniques.
The Milling Process Explained
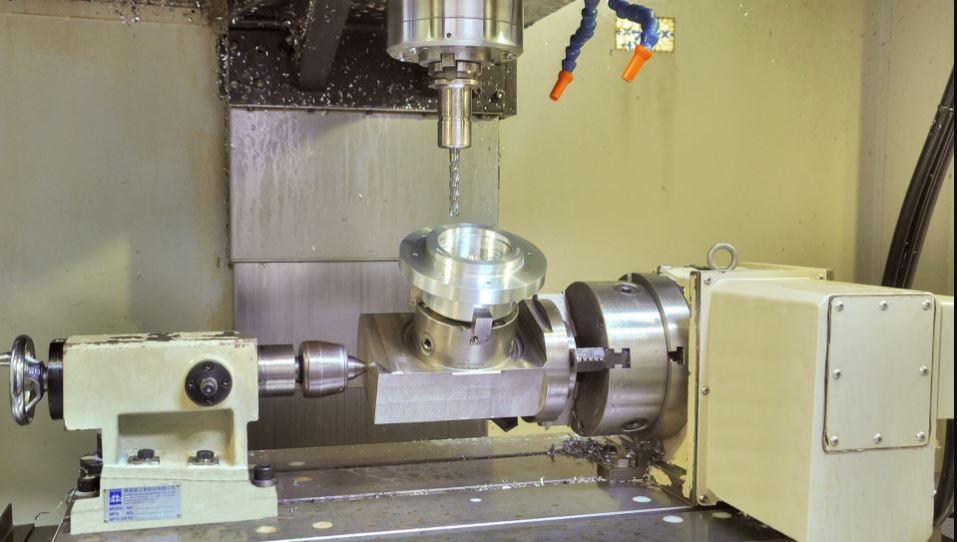
Milling machine operations are a fascinating blend of art and science, where precision meets creativity. Understanding the milling process is crucial for anyone involved in CNC manufacturing, as it lays the foundation for producing high-quality components. From selecting the right milling machine to mastering feeds and speeds, each step plays a vital role in achieving optimal results.
Steps in the Milling Process
The milling process begins with careful planning and design, which often includes creating detailed blueprints or CAD models of the desired part. Once the design is finalized, it's time to set up the milling machine by securing the workpiece and selecting appropriate cutting tools based on material type and required tolerances. The actual machining phase follows, where the CNC milling machine executes programmed commands that guide cutting tools through various motions to shape the material into its final form.
After machining, inspection comes next; this step ensures that all dimensions meet specifications through rigorous quality control checks. Any necessary adjustments can be made at this stage before proceeding with finishing processes such as sanding or polishing to achieve a smooth surface finish. Finally, once everything meets quality standards, parts are cleaned and prepared for assembly or shipment—completing a well-orchestrated dance of milling machine operations.
The Role of Cutting Tools
Cutting tools are at the heart of any successful milling operation; they determine not only how efficiently material is removed but also influence precision machining outcomes significantly. Different types of cutting tools—such as end mills, face mills, and ball nose cutters—are designed for specific applications and materials to maximize effectiveness during CNC machining metal processes. Selecting the right tool can mean the difference between a flawless finish or an expensive mistake.
Moreover, cutting tool geometry plays a crucial role in how effectively they perform during milling machine operations; factors like rake angle and flute design affect chip removal and surface finish quality. Regular maintenance of these tools is essential since wear can lead to inaccuracies in dimensions over time. By understanding their importance within CNC manufacturing contexts, operators can enhance productivity while minimizing waste.
Understanding Feeds and Speeds
When it comes to CNC milling operations, understanding feeds and speeds is akin to mastering an intricate dance routine—each element must harmonize perfectly for optimal performance! Feed rate refers to how quickly the cutting tool advances through material while spindle speed determines how fast it rotates; together they play critical roles in ensuring effective cuts without damaging either tool or workpiece.
Getting these parameters right involves considering several factors including material type, tooling specifications, and desired surface finish—all of which directly impact productivity levels during precision machining tasks. Too slow a feed may lead to inefficient production times while too fast could cause excessive wear on your cutting tools or even catastrophic failure! Thus balancing these elements allows machinists not only to achieve better results but also prolongs equipment lifespan—a win-win situation!
Precision Machining Techniques
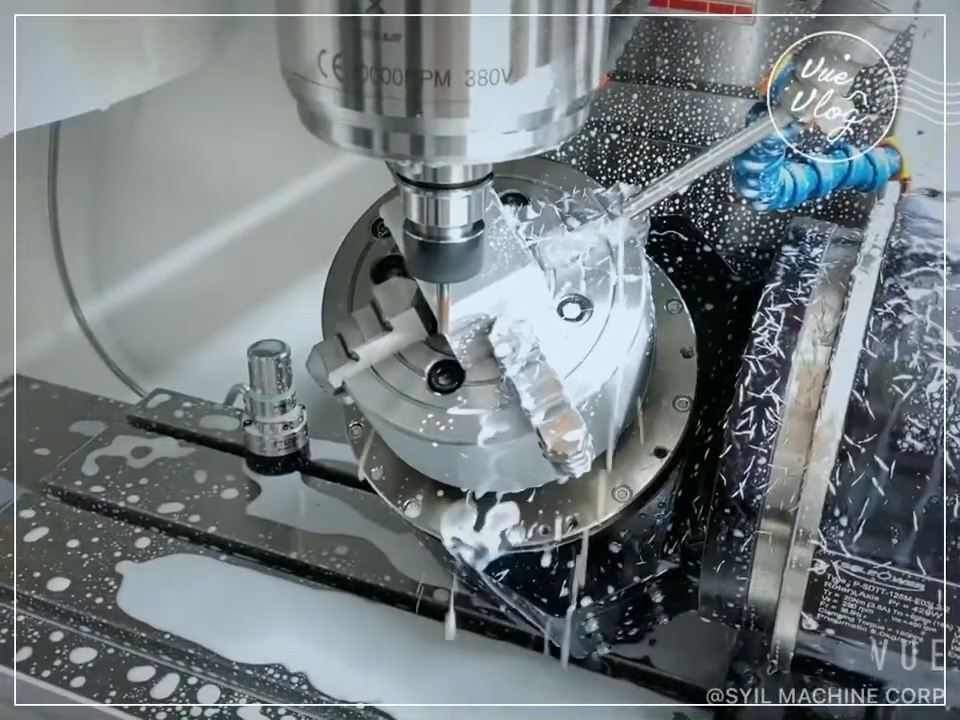
Precision machining is the backbone of effective milling machine operations, ensuring that every component produced meets stringent specifications. In the world of manufacturing, precision is not just a luxury; it’s a necessity that determines the quality and functionality of the final product. As industries demand tighter tolerances and higher quality standards, understanding precision machining becomes essential for anyone involved in CNC milling.
Importance of Precision in Milling
When it comes to milling machine operations, precision is paramount. A slight deviation can lead to significant issues down the line, affecting both performance and safety. This is especially true in applications like aerospace or medical device manufacturing, where even minor inaccuracies can have catastrophic consequences.
Moreover, precision machining enhances efficiency by reducing waste material and rework costs. By using precise measurements and techniques, manufacturers can optimize their processes and ensure that every cut made by the CNC milling machine contributes positively to the overall outcome. Ultimately, maintaining high precision levels not only elevates product quality but also boosts customer satisfaction.
Different Cutting Tools for Precision Machining
The cutting tools used in CNC milling play a crucial role in achieving precision machining standards. Various types of cutting tools are designed for specific tasks—end mills for face milling, ball nose cutters for contouring, and reamers for finishing holes are just a few examples. Each tool has its own unique geometry and material composition tailored to different materials being machined.
Material selection also matters; carbide tools are popular due to their hardness and heat resistance while HSS (high-speed steel) tools offer versatility at a lower cost. Understanding these differences helps machinists select the right tool for their specific needs during milling machine operations. This knowledge translates into better performance and longer tool life, ultimately contributing to more efficient CNC machining metal processes.
Applications of Precision Machining in CNC Manufacturing
Precision machining finds its applications across various sectors within CNC manufacturing—from automotive parts to intricate electronics components. For instance, when creating complex geometries or tight tolerances required in modern automobiles or aircraft components, precise cutting tools are indispensable during the milling process.
Additionally, industries such as medical device manufacturing rely heavily on precision machining techniques due to regulatory compliance requirements that dictate strict adherence to specifications—ensuring patient safety is always prioritized through meticulous production practices using advanced CNC milling machines. As technology continues evolving with innovations like 5-axis CNC machines becoming mainstream, we can expect even greater advancements in how precision machining enhances efficiency across all areas of manufacturing.
CNC Milling in Action
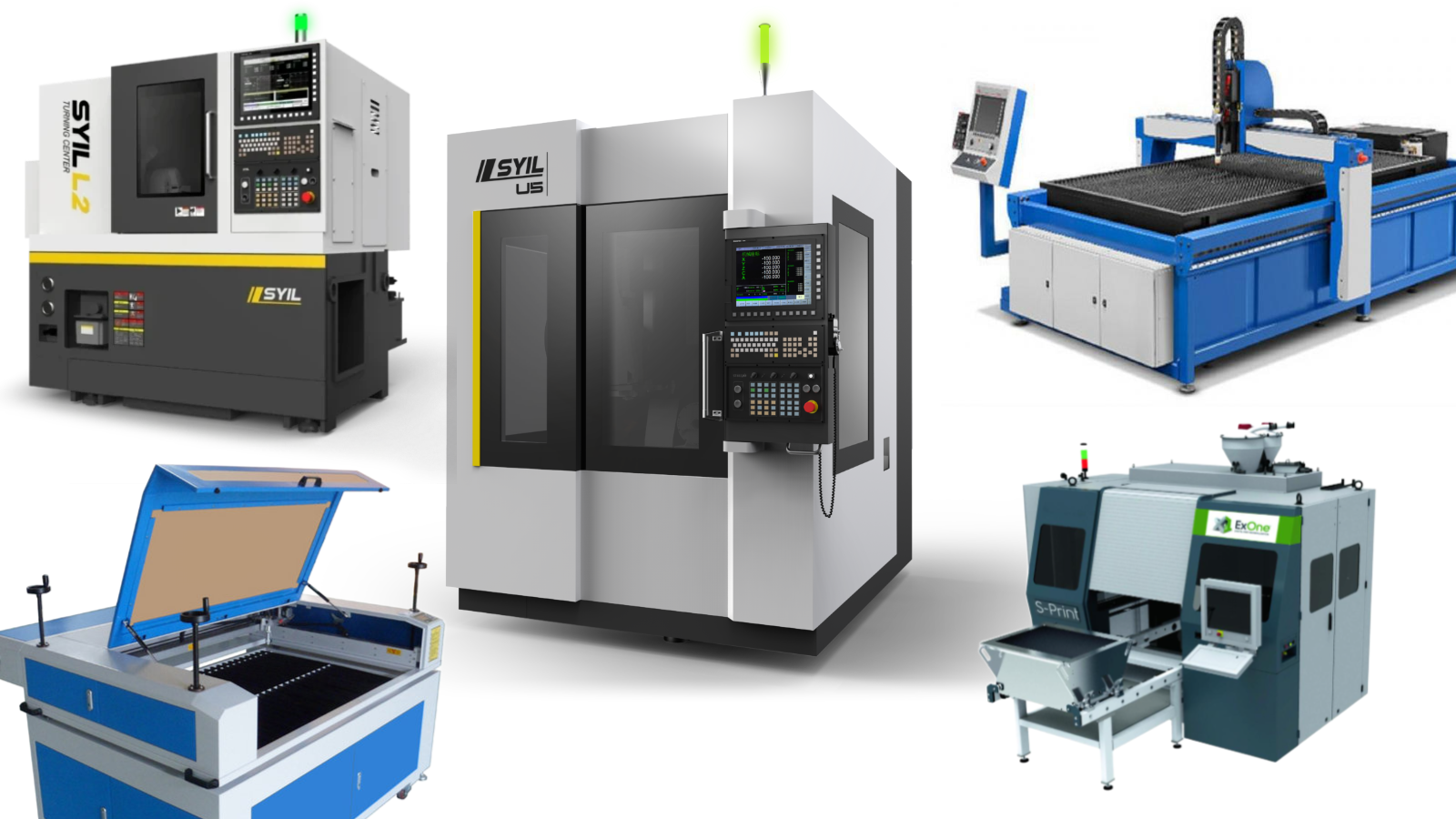
CNC milling is where the magic happens, transforming raw materials into intricate parts with precision and efficiency. This process utilizes a computer-controlled milling machine to automate the cutting process, allowing for consistent results and complex geometries that manual machining simply can't match. By integrating advanced software and precise cutting tools, CNC milling has revolutionized manufacturing across various industries.
How CNC Milling Operates
At its core, CNC milling operates by translating digital designs into physical components through a series of programmed movements. The operator inputs specifications into the CNC machine's computer software, which then directs the milling machine to cut the material according to precise parameters. The combination of high-speed rotation and accurate positioning of cutting tools enables the creation of detailed shapes and patterns that are essential in modern manufacturing.
The beauty of this operation lies in its repeatability; once programmed, a CNC milling machine can produce identical parts with minimal human intervention. This not only enhances productivity but also significantly reduces the risk of errors associated with manual operations. Consequently, understanding these milling machine operations is crucial for anyone looking to delve into precision machining or CNC manufacturing.
Benefits of CNC Machining Metal
One of the standout benefits of CNC machining metal is its unparalleled accuracy compared to traditional methods. With advanced cutting tools and precise controls, manufacturers can achieve tolerances that were previously thought impossible, making it ideal for industries requiring high-quality components such as aerospace and automotive sectors. Additionally, this level of precision translates into reduced waste and lower production costs—two factors every manufacturer appreciates.
Another significant advantage is versatility; a single CNC milling machine can be programmed to create various parts from different metals like aluminum, steel, or titanium without needing extensive retooling or setup changes. This flexibility allows manufacturers to respond quickly to market demands or custom orders while maintaining efficiency in their milling machine operations. Furthermore, as technology advances, so do the capabilities of these machines—leading to even more efficient processes in metalworking.
Real-World Applications of CNC Milling
CNC milling finds applications across an impressive range of industries—from creating intricate medical devices to producing robust automotive components. In aerospace engineering, for instance, precision machining ensures that each part meets strict regulatory standards while also being lightweight and durable enough for flight conditions. Similarly, in electronics manufacturing, finely crafted components produced through cnc machining metal play critical roles in device functionality.
Moreover, businesses are increasingly adopting this technology for prototyping purposes due to its speed and accuracy; engineers can rapidly develop models before committing them to full-scale production using traditional methods. This aspect not only accelerates product development cycles but also fosters innovation by allowing designers more freedom when experimenting with new ideas or concepts within their projects involving cutting tools like end mills or drills used on a cnc milling machine.
In summary, understanding how cnc milling operates reveals just how transformative it can be within various sectors—making it an indispensable tool in modern manufacturing practices today!
Conclusion
In summary, milling machine operations are a cornerstone of modern manufacturing, playing a crucial role in creating precise components across various industries. Understanding the intricacies of milling machines, from their types to the cutting tools involved, equips manufacturers with the knowledge needed to optimize production processes. As we look ahead, the evolution of CNC milling and precision machining promises even greater advancements in efficiency and accuracy.
Key Takeaways on Milling Machine Operations
Milling machine operations encompass a wide range of techniques that are essential for producing high-quality parts with precision. The choice between vertical and horizontal milling machines can significantly impact the outcome of projects, depending on specific requirements and desired finishes. Additionally, understanding cutting tools and their applications is vital for achieving optimal results in CNC machining metal processes.
Future of Milling in Technology
The future of milling technology is bright, with innovations such as smart CNC milling machines that incorporate artificial intelligence and automation to enhance efficiency further. These advancements not only streamline production but also improve quality control measures through real-time monitoring and adjustments during machining processes. As industries embrace more sophisticated methods like precision machining, we can expect continued growth in CNC manufacturing capabilities that redefine what is possible in engineering.
Getting Started with Your Own CNC Milling Journey
Embarking on your own CNC milling journey requires careful planning and consideration of your specific needs regarding equipment and materials. Investing time in learning about various cutting tools and their applications will set a strong foundation for mastering milling machine operations effectively. Whether you're aiming to create intricate designs or robust components, understanding the principles behind CNC machining metal will empower you to take full advantage of this transformative technology.