Introduction
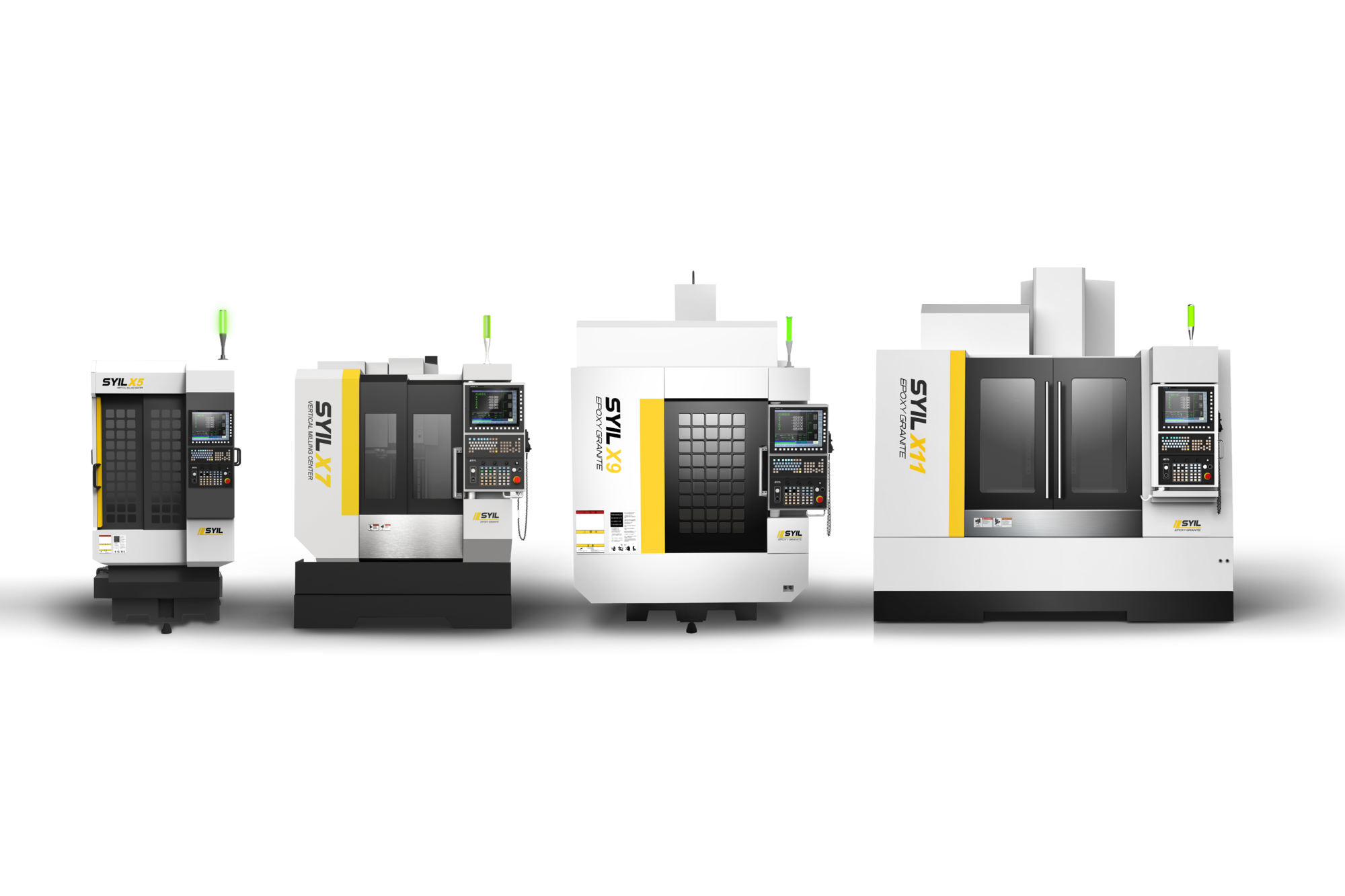
Milling operations are at the heart of modern manufacturing, transforming raw materials into precisely shaped components. Understanding the basics of these processes is essential for anyone venturing into the world of machining. From traditional milling machines to cutting-edge CNC technology, milling encompasses a variety of techniques that cater to diverse industrial needs.
Discover the Basics of Milling Operations
Milling operations involve removing material from a workpiece using rotary cutters, which can create intricate shapes and designs. The versatility of milling machines allows for different types of milling operations, including face milling and peripheral milling, each serving unique purposes in precision machining. Grasping these fundamentals sets the stage for exploring more advanced concepts like CNC lathing and CNC milling.
Explore Different Types of Milling Operations
There’s a whole universe within types of milling operations, ranging from simple tasks to complex processes that require sophisticated machinery. Face milling machines are designed to cut flat surfaces, while peripheral mills focus on cutting along the circumference—each technique has its own applications in manufacturing. By delving into these distinctions, one can appreciate how various approaches contribute to effective production workflows.
Understand CNC Machines in Milling
CNC machines have revolutionized the landscape of milling operations by offering unparalleled precision and automation capabilities. A CNC milling machine operates through computer programming, allowing for intricate designs and consistent results that traditional methods might struggle to achieve. Moreover, understanding how CNC lathing complements these processes enhances your grasp on modern machining techniques and their significance in today’s industrial realm.
What Are Milling Operations?
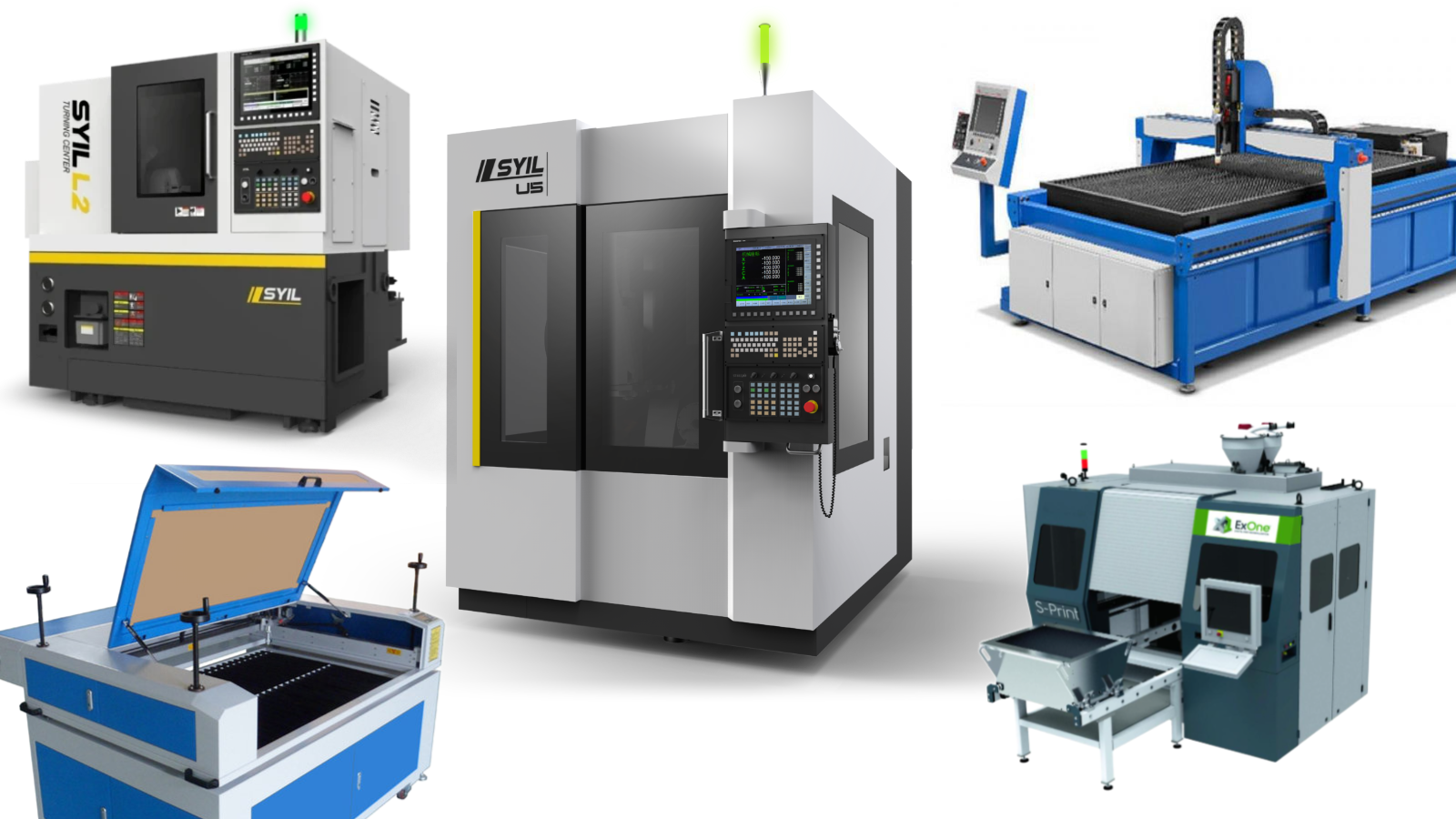
Milling operations are a vital component of modern manufacturing, shaping materials into precise components through various techniques. This process involves the use of a milling machine, which employs rotating cutting tools to remove material from a workpiece. Understanding the types of milling operations is essential for anyone looking to delve into the world of CNC machining and precision engineering.
Definition and Importance of Milling
Milling can be defined as a machining process that utilizes rotary cutters to remove material from a workpiece. It plays an indispensable role in producing intricate parts with high accuracy, which is crucial in industries ranging from aerospace to automotive. The importance of milling lies in its ability to create complex geometries and fine tolerances that are often required in precision machining.
Overview of Common Milling Machines
Common milling machines include vertical and horizontal models, each serving distinct purposes based on the type of milling operation being performed. The face milling machine is particularly notable for its ability to cut flat surfaces and create grooves or slots efficiently. Understanding these common machines helps operators choose the right equipment for their specific needs, whether they are engaging in CNC milling or traditional methods.
Benefits of Precision Machining in Milling
Precision machining through milling offers numerous benefits that enhance both productivity and product quality. One significant advantage is the consistency achieved across multiple parts; CNC machines can replicate exact specifications repeatedly without human error. Additionally, utilizing advanced techniques like CNC lathing alongside traditional milling can significantly expand design capabilities while ensuring optimal performance across various applications.
Types of Milling Operations
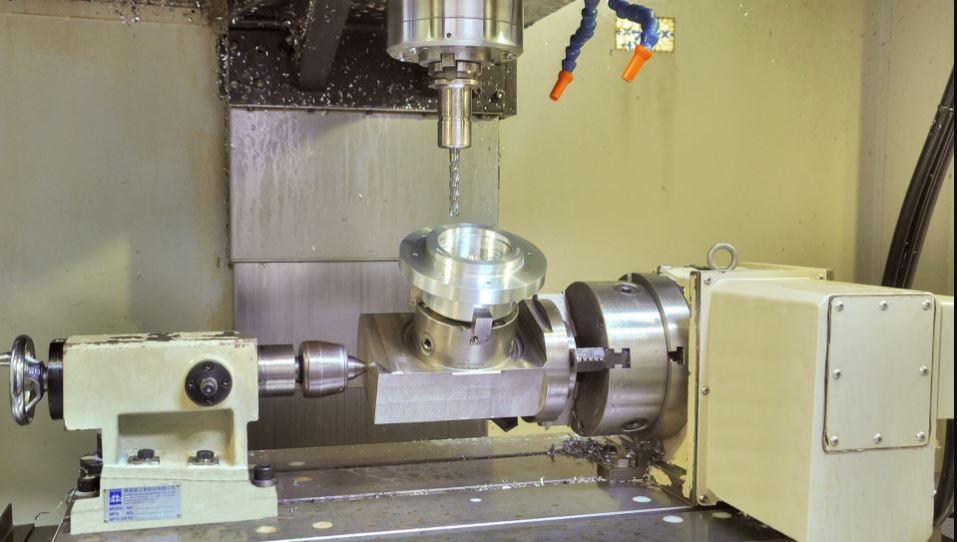
When diving into the fascinating world of milling operations, understanding the various types is crucial. Each type serves unique purposes and utilizes different techniques, making them indispensable in precision machining. Whether you're operating a CNC machine or a traditional milling machine, knowing these distinctions can significantly enhance your projects.
Face Milling Techniques
Face milling is one of the most common types of milling operations and involves cutting flat surfaces with a face milling machine. This technique uses a rotating cutter that approaches the workpiece at a perpendicular angle, ensuring clean and precise finishes on flat surfaces. The versatility of face milling makes it ideal for creating pockets, slots, and even contours on a variety of materials.
In precision machining, face milling is often favored for its ability to produce smooth finishes while removing material efficiently. CNC milling machines take this operation to the next level by automating movements with high accuracy and repeatability. With advancements in technology, modern face milling techniques have become faster and more efficient than ever before.
Peripheral Milling Explained
Peripheral milling is another essential type among the various types of milling operations that focuses on generating features along the sides of the workpiece rather than its surface. In this process, cutters are mounted on the periphery of a rotating disk or cylindrical tool, allowing for deeper cuts into materials like metals or plastics. This method is particularly effective for producing grooves and profiles that require high precision.
Unlike face milling, which primarily targets surface finishing, peripheral milling excels in cutting deep slots or intricate shapes where depth matters more than width. When using CNC machines for peripheral operations, you can achieve remarkable accuracy while reducing cycle times significantly—making it perfect for mass production environments in precision machining industries. The synergy between peripheral techniques and CNC technology has revolutionized how manufacturers approach complex designs.
Combination of Milling Operations
Combining different types of milling operations can yield impressive results by leveraging their individual strengths to create intricate designs or fulfill specific project requirements. For instance, one might start with face milling to establish flat surfaces before switching to peripheral methods for detailed work like engraving or shaping edges—this flexibility enhances productivity without sacrificing quality.
Utilizing both CNC lathing and CNC milling within one project allows machinists to maximize efficiency through seamless transitions between operations without manual intervention. By carefully planning these combinations within your workflow, you can exploit each operation's advantages while minimizing downtime between processes—a key factor in maintaining competitiveness in today's fast-paced manufacturing landscape.
In conclusion, understanding these types of milling operations equips you with essential knowledge that translates directly into improved results in your projects—whether you're operating a simple manual mill or an advanced CNC machine designed specifically for precision machining tasks.
CNC Milling: The Game Changer
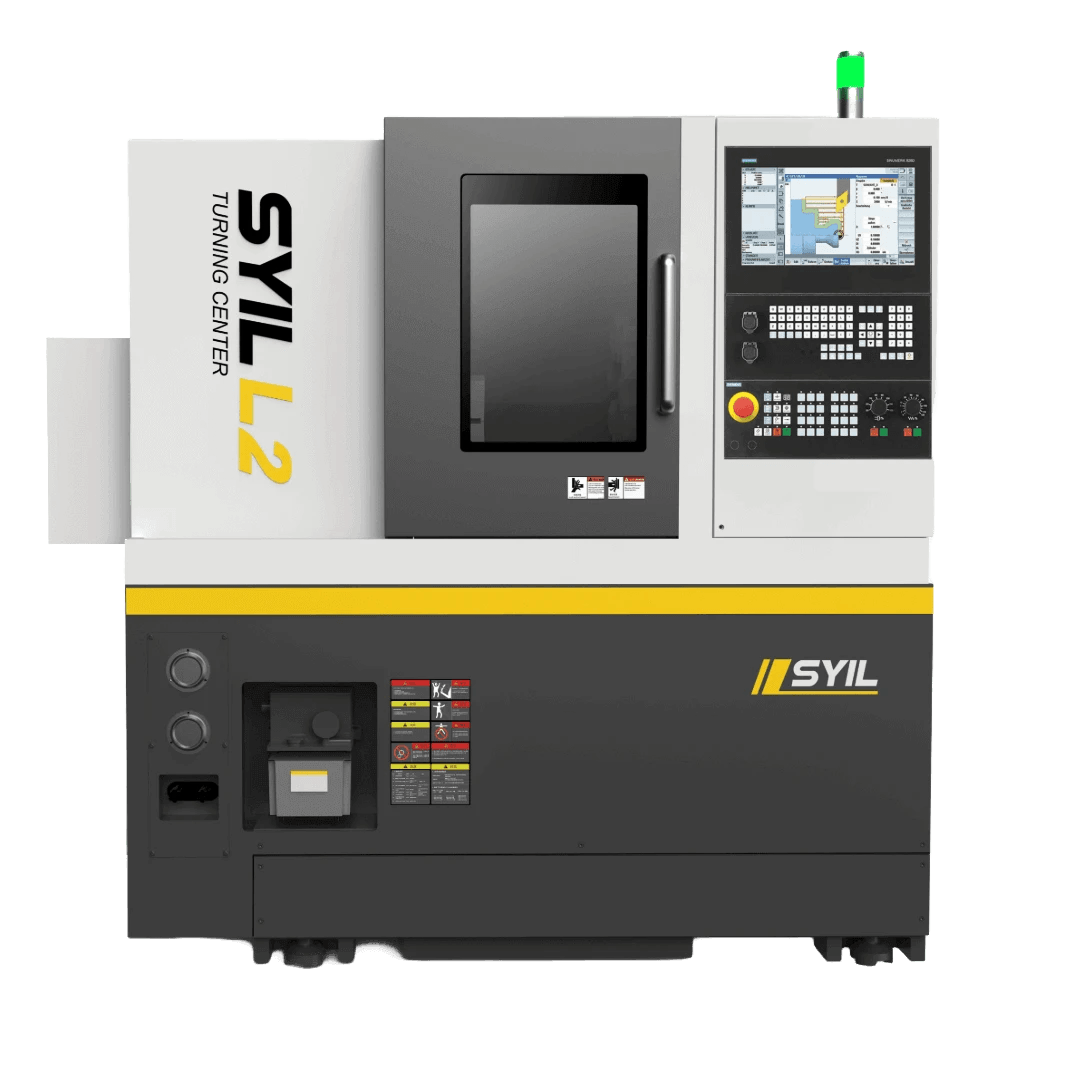
CNC milling has revolutionized the landscape of manufacturing and precision machining, offering unparalleled accuracy and efficiency. Unlike traditional milling methods, CNC machines operate with a computer-controlled system that significantly reduces human error and increases productivity. As a result, CNC milling machines have become indispensable tools in various industries, making complex types of milling operations more accessible than ever before.
Advantages of CNC Milling Machines
The advantages of CNC milling machines are numerous, but let's spotlight the key benefits that make them stand out in the world of manufacturing. First off, precision machining is taken to new heights with these machines; they can produce intricate designs with minimal tolerance levels. Additionally, the speed at which a CNC machine operates allows for rapid production cycles without compromising quality—ideal for industries where time is money.
Moreover, flexibility is another feather in the cap of CNC milling machines. They can easily be programmed to perform various types of milling operations such as face milling or peripheral milling without needing extensive reconfiguration. This adaptability not only saves time but also reduces costs associated with tool changes and setups.
SYIL X5 Mini CNC Machine Overview
When it comes to compact yet powerful options in the realm of CNC machinery, the SYIL X5 Mini CNC machine takes center stage. Designed for both hobbyists and professionals alike, this machine packs a punch despite its smaller size—making it perfect for precision machining projects that require meticulous detail without occupying too much space. With its user-friendly interface and robust construction, even those new to CNC technology can quickly get up to speed.
Equipped with advanced features like high-speed spindle options and precise linear guides, the SYIL X5 excels at executing various types of milling operations efficiently. Its ability to handle both aluminum and harder materials makes it versatile enough for different applications—from creating custom parts to prototyping designs effectively. Notably, this face milling machine ensures consistent results every time you hit that start button.
Applications of CNC in Precision Machining
The applications of CNC in precision machining are vast and varied; industries ranging from aerospace to automotive heavily rely on these technologies for their intricate needs. For instance, components requiring high tolerances are often produced using a combination of types of milling operations facilitated by advanced CNC machines like the SYIL X5 Mini. This capability allows manufacturers to meet stringent industry standards while maintaining cost-effectiveness.
In addition to traditional manufacturing sectors, emerging fields such as medical device fabrication also benefit greatly from advancements in CNC technology—enabling intricate designs that would be nearly impossible with manual methods alone. Furthermore, as businesses continue adopting automation trends through tools like cnc lathing alongside cnc milling processes, we can expect enhanced efficiency across multiple domains.
Key Components of a Milling Machine
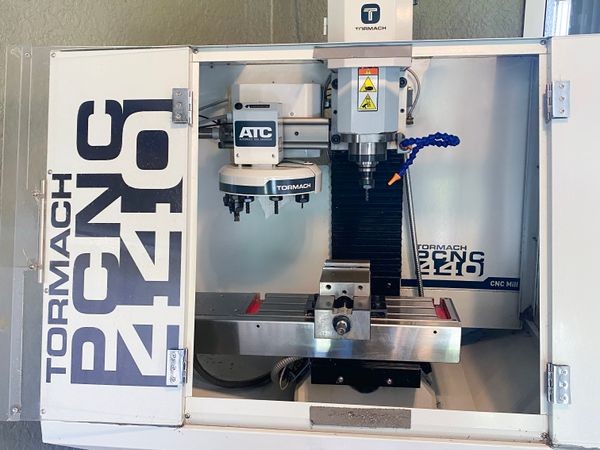
Understanding the key components of a milling machine is crucial for anyone involved in precision machining. A CNC milling machine, for instance, relies on various parts working in harmony to achieve high levels of accuracy and efficiency. Recognizing these essential elements can enhance your knowledge and skills in operating different types of milling operations.
Essential Parts of a CNC Milling Machine
A CNC milling machine comprises several essential parts that contribute to its functionality. The most notable components include the spindle, which houses the cutting tool; the table, where the workpiece is secured; and the axes that control movement—X, Y, and Z. Each part plays a vital role in ensuring that the machine performs optimally during various types of milling operations such as face milling or peripheral milling.
How Each Component Functions
Each component of a CNC milling machine has its unique function that contributes to overall performance. The spindle rotates at high speeds to cut materials with precision while the table allows for stable support during machining processes. The movement along different axes enables intricate designs to be crafted efficiently, making it easier to switch between various types of milling operations without compromising quality.
Importance of Maintenance for Longevity
Regular maintenance is key to ensuring the longevity and optimal performance of your CNC milling machine. By routinely checking components like bearings, belts, and lubrication systems, you can prevent costly breakdowns that could halt production. Furthermore, maintaining your face milling machines and other equipment not only extends their lifespan but also enhances precision machining capabilities across all types of milling operations.
The Process of CNC Lathing
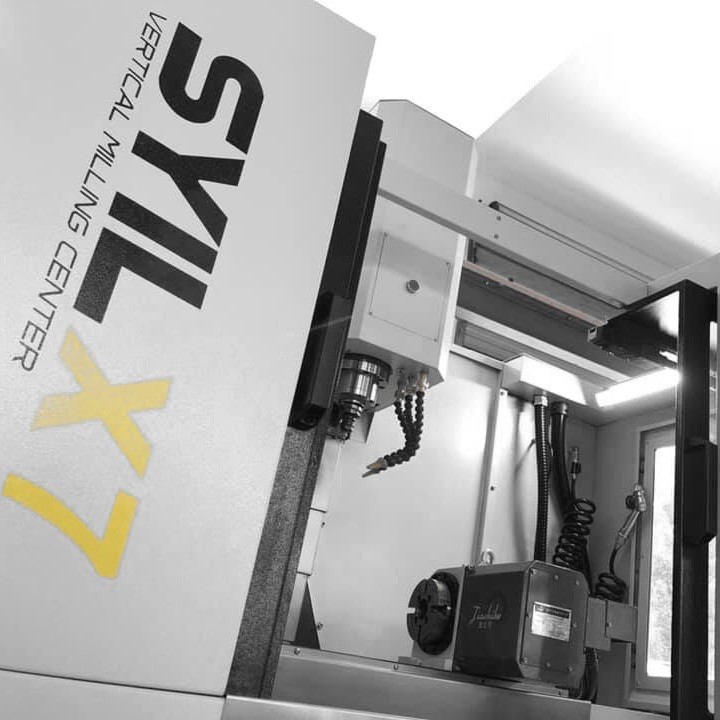
CNC lathing is a pivotal process in the realm of precision machining, allowing for the creation of intricate and accurate components. This technique involves rotating a workpiece against a cutting tool, enabling the production of cylindrical parts with exceptional precision. As industries increasingly demand high-quality results, understanding CNC lathing techniques becomes essential for those involved in various types of milling operations.
Overview of CNC Lathing Techniques
CNC lathing techniques encompass several methods that vary based on the desired outcome and material being machined. One common approach is turning, where the cutting tool moves linearly while the workpiece rotates, effectively shaping it into precise dimensions. Other techniques include facing and grooving, which are crucial for achieving specific features on cylindrical components—each technique plays a unique role in enhancing the overall functionality of CNC machines.
Incorporating advanced software into CNC lathing allows operators to program complex designs with ease, ensuring consistency across multiple productions. This level of automation not only improves efficiency but also minimizes human error—a significant advantage over traditional manual methods. As businesses continue to embrace technology, mastering these techniques will be vital for maintaining a competitive edge in precision machining.
Differences Between CNC Milling and Lathing
While both CNC milling and lathing fall under the umbrella of computer numerical control (CNC) operations, they serve distinct purposes in manufacturing processes. In essence, milling machines use rotating tools to remove material from stationary workpieces, making them ideal for creating flat surfaces or intricate shapes through various types of milling operations like face milling or peripheral milling. Conversely, CNC lathing focuses on shaping materials by rotating them against fixed cutting tools—perfect for producing cylindrical parts such as shafts or bushings.
Another key difference lies in their operational setup: CNC milling typically involves multiple axes (often 3 or more) that allow for complex movements across different planes; whereas CNC lathes usually operate around two axes (X and Z), centering around rotational symmetry. This fundamental distinction influences how each machine is utilized within an industrial setting—while a face milling machine might excel at creating detailed contours on flat surfaces, a lathe shines when crafting uniform cylindrical shapes.
Ultimately, understanding these differences helps manufacturers choose the right equipment for their needs—whether they require a versatile CNC milling machine or a specialized lathe to tackle specific projects effectively.
Applications of CNC Lathing in Industry
The applications of CNC lathing span numerous industries due to its versatility and precision capabilities. In automotive manufacturing, for instance, engineers rely on CNC lathes to produce critical components like engine blocks and transmission housings that require exact dimensions to ensure optimal performance. Similarly, aerospace companies utilize this technology to create lightweight yet durable parts that meet stringent safety standards while maintaining efficiency.
Beyond automotive and aerospace sectors, medical device manufacturers have embraced CNC lathing as well; producing intricate components such as surgical instruments or implantable devices requires unparalleled accuracy that only modern machines can deliver consistently. Additionally, industries dealing with custom fabrication benefit from this technology by allowing rapid prototyping without compromising quality—a crucial factor when meeting tight deadlines.
As businesses continue exploring innovative solutions within their respective fields, it's clear that the relevance of CNC lathing will only grow stronger; its ability to adapt alongside advancements in technology ensures it remains an integral part of modern manufacturing processes.
Conclusion
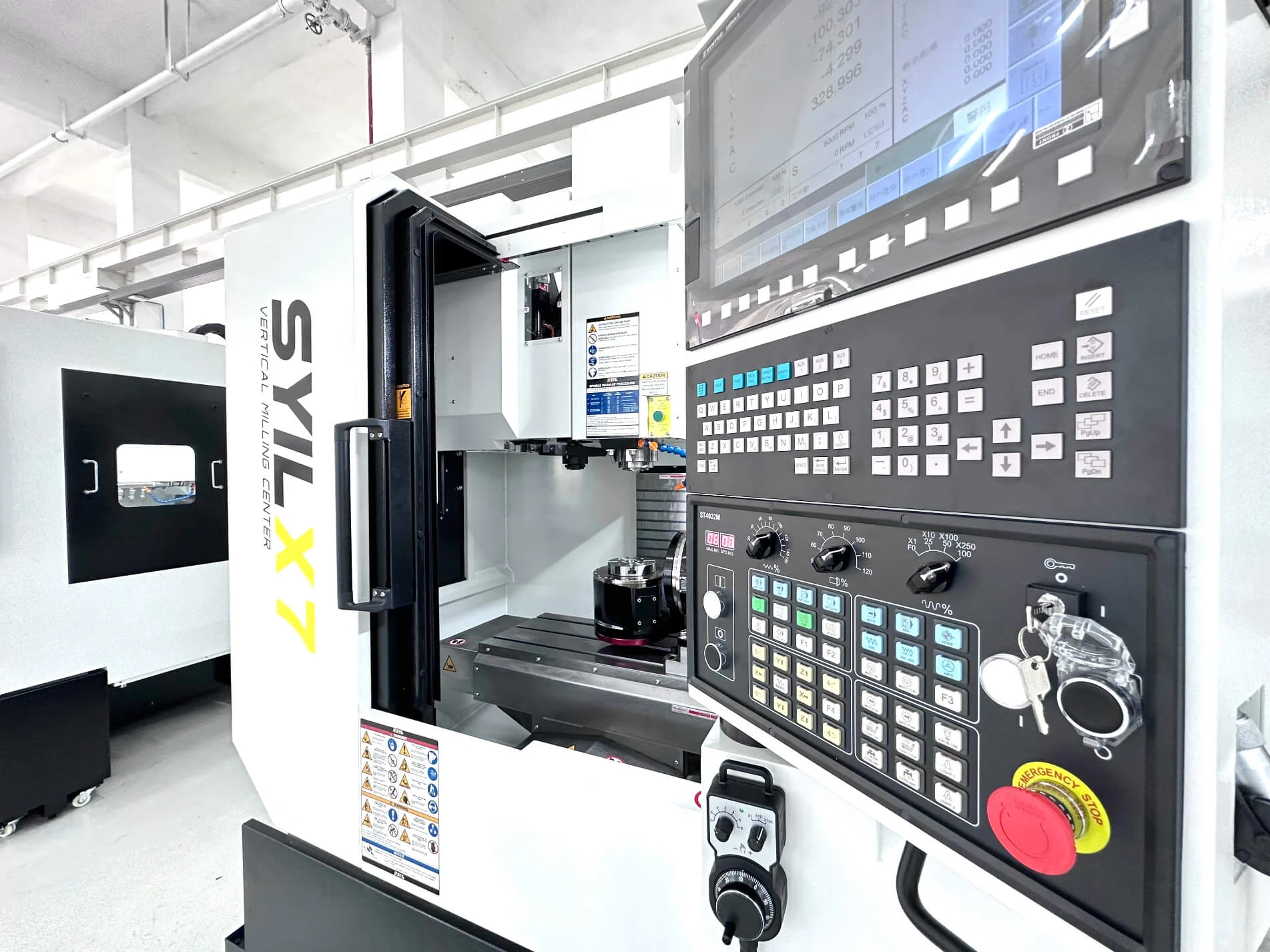
As we wrap up our exploration of milling operations, it's clear that this field is evolving at a rapid pace. The future of milling operations will likely be driven by advancements in technology, particularly in CNC machines and precision machining techniques. Innovations promise to enhance efficiency and accuracy, making it an exciting time for both seasoned professionals and newcomers alike.
The Future of Milling Operations
Looking ahead, the landscape of milling operations is set to change dramatically with the integration of smart technologies and automation. CNC milling machines are becoming more sophisticated, allowing for greater customization and versatility in various applications. This evolution not only boosts productivity but also opens doors to new types of milling operations that were previously unimaginable.
Choosing the Right Milling Machine
Selecting the right milling machine can feel like navigating a maze filled with options—each promising to be the best fit for your needs. It's essential to consider factors such as the types of materials you'll be working with, desired precision levels, and specific applications like face milling or CNC lathing. Investing time in research will pay off; understanding your project requirements will help you choose a CNC machine that enhances your production capabilities.
Enhancing Projects with SYIL CNC Technology
Incorporating SYIL CNC technology into your projects can significantly elevate the quality and efficiency of your work. With robust features tailored for precision machining, SYIL's offerings stand out among various milling machines available today. Whether you're focusing on face milling or exploring other types of milling operations, leveraging advanced tools from SYIL ensures that you stay ahead in this competitive industry.