Introduction
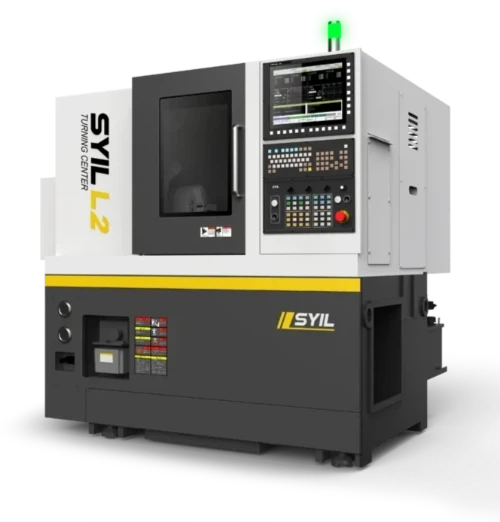
In the ever-evolving world of manufacturing, precision and efficiency are paramount. One technology that has revolutionized machining is the 5 Axis CNC machine. But what is a 5 axis CNC machine, and how does it stack up against its counterparts? This introduction will delve into the core concepts of 5 Axis CNC machining, its key applications across various industries, and the distinct advantages it offers over traditional methods.
Understanding 5 Axis CNC Machining
At its core, 5 Axis CNC machining refers to a process that allows for simultaneous movement along five different axes—three linear (X, Y, Z) and two rotational (A and B). This advanced capability enables manufacturers to create complex geometries with unparalleled precision. By understanding what is a 5 axis CNC machine, one can appreciate how it enhances productivity while reducing setup time compared to simpler systems.
Key Applications of 5 Axis CNC
The versatility of 5 Axis CNC machines opens doors to numerous applications in various sectors. Industries such as aerospace, automotive, and medical rely heavily on this technology for producing intricate parts with tight tolerances. From crafting turbine blades to custom implants, knowing where these machines excel provides insight into their critical role in modern manufacturing processes.
Advantages of Using 5 Axis CNC
One significant advantage of using a 5 Axis CNC machine is its ability to reduce the number of setups required during production. Fewer setups lead to increased efficiency and lower labor costs while maintaining high accuracy levels. Furthermore, when considering what is the difference between 3 and 5-axis CNC technologies, it's clear that the latter offers enhanced flexibility for complex designs that would be challenging or impossible with traditional methods.
What is a 5 Axis CNC Machine?
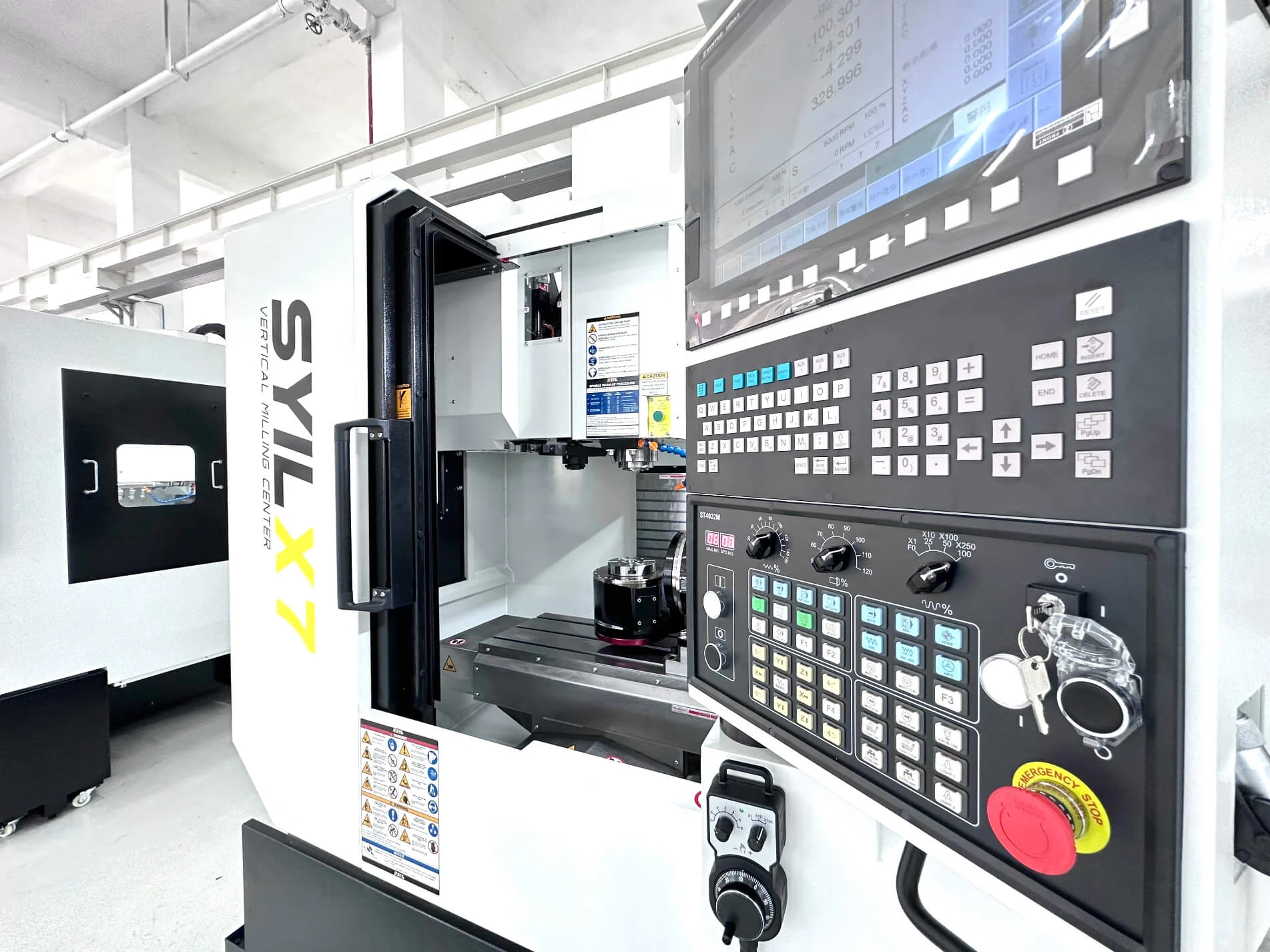
Diving into the world of CNC machining, the term 5 Axis CNC machine often pops up, and for good reason. These machines are designed to move tools or parts along five different axes simultaneously, allowing for intricate and complex shapes that traditional machines struggle to produce. Understanding what a 5 axis CNC machine entails is key to appreciating its transformative impact on industries ranging from aerospace to automotive manufacturing.
Overview of 5 Axis Technology
At its core, 5 axis technology enhances the capabilities of traditional machining by introducing two additional rotational axes to the standard three linear movements (X, Y, Z). This means that a cutting tool can approach a workpiece from virtually any angle, significantly improving precision and reducing the need for multiple setups. The ability to perform intricate cuts in one go not only saves time but also minimizes errors—making it an essential tool for high-stakes applications.
How It Transforms Machining Processes
The transformation brought about by 5 axis CNC machines is nothing short of revolutionary. By allowing simultaneous movement across five axes, these machines streamline production workflows and enhance design flexibility; imagine creating complex geometries without needing extensive manual adjustments or re-clamping! This capability leads to quicker turnaround times and improved surface finishes—key factors in maintaining competitive advantage in various sectors.
Real-World Examples of Use
Real-world applications of what is a 5 axis CNC machine are abundant and varied. In aerospace manufacturing, for instance, components like turbine blades require precise contours that only these advanced machines can deliver efficiently. Similarly, in the medical field, custom implants can be produced with unparalleled accuracy—showcasing just how vital this technology has become across industries.
What is the Difference Between 3 and 5-Axis CNC?
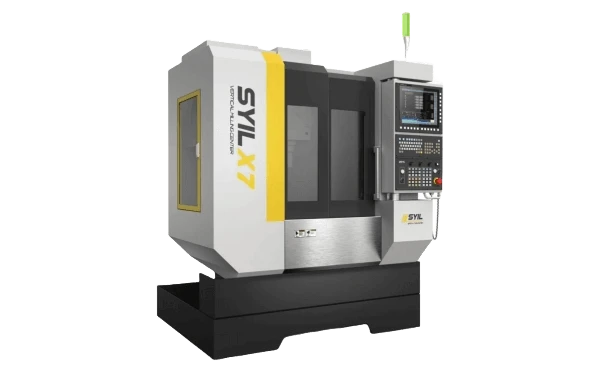
When it comes to CNC machining, understanding the difference between 3-axis and 5-axis CNC machines can significantly impact your production capabilities. At its core, a 3-axis CNC machine operates along three linear axes: X, Y, and Z, allowing for movement in a straightforward manner. In contrast, a 5-axis CNC machine introduces two additional rotational axes, enabling more complex geometries and intricate designs to be machined with precision.
Simplifying the Concepts
To simplify the concepts further, think of a 3-axis CNC machine as a flat surface where you can move your tool up and down (Z), left and right (X), or forward and backward (Y). However, when you add two additional rotational movements—often referred to as A (tilting) and B (spinning)—you unlock new possibilities with what is a 5 axis CNC machine. This added flexibility allows for machining at various angles without needing to reposition the workpiece manually.
For instance, while both machines can perform basic tasks like drilling or milling, only a 5-axis machine can create complex shapes like turbine blades or intricate molds in one setup. This capability minimizes setup time and enhances accuracy by reducing human error associated with transferring parts between different machines.
Applications Where 5 Axis Outshines 3 Axis
In industries where precision is paramount—such as aerospace or medical device manufacturing—the question of What is the difference between 3 and 5-axis CNC? often leads to the realization that versatility matters greatly. A prime application where a 5-axis machine outshines its simpler counterpart is in creating components with multiple angled surfaces that would be nearly impossible to achieve efficiently on a traditional mill.
For example, consider an aerospace manufacturer needing to produce lightweight yet strong components; here’s where what is a 5 axis CNC machine becomes invaluable. The ability to approach the workpiece from various angles reduces tool changes while enhancing surface finish quality—a critical factor in high-performance applications.
Use Cases in Industries
The use cases for these two types of machines differ significantly across industries due to their operational capabilities. In automotive manufacturing, for instance, engineers often rely on both types: using 3-axis machines for simpler parts while reserving their more advanced counterparts for intricate engine components that demand precise tolerances.
Similarly, in artistic applications such as sculpture or custom furniture design, artists may prefer what is a 5 axis CNC machine due to its ability to create detailed curves and contours that are challenging with just three axes alone. Ultimately, understanding these differences helps businesses choose the right technology tailored specifically for their needs—whether they require high-volume production efficiency or bespoke craftsmanship.
Unpacking 4 Axis vs. 5 Axis CNC
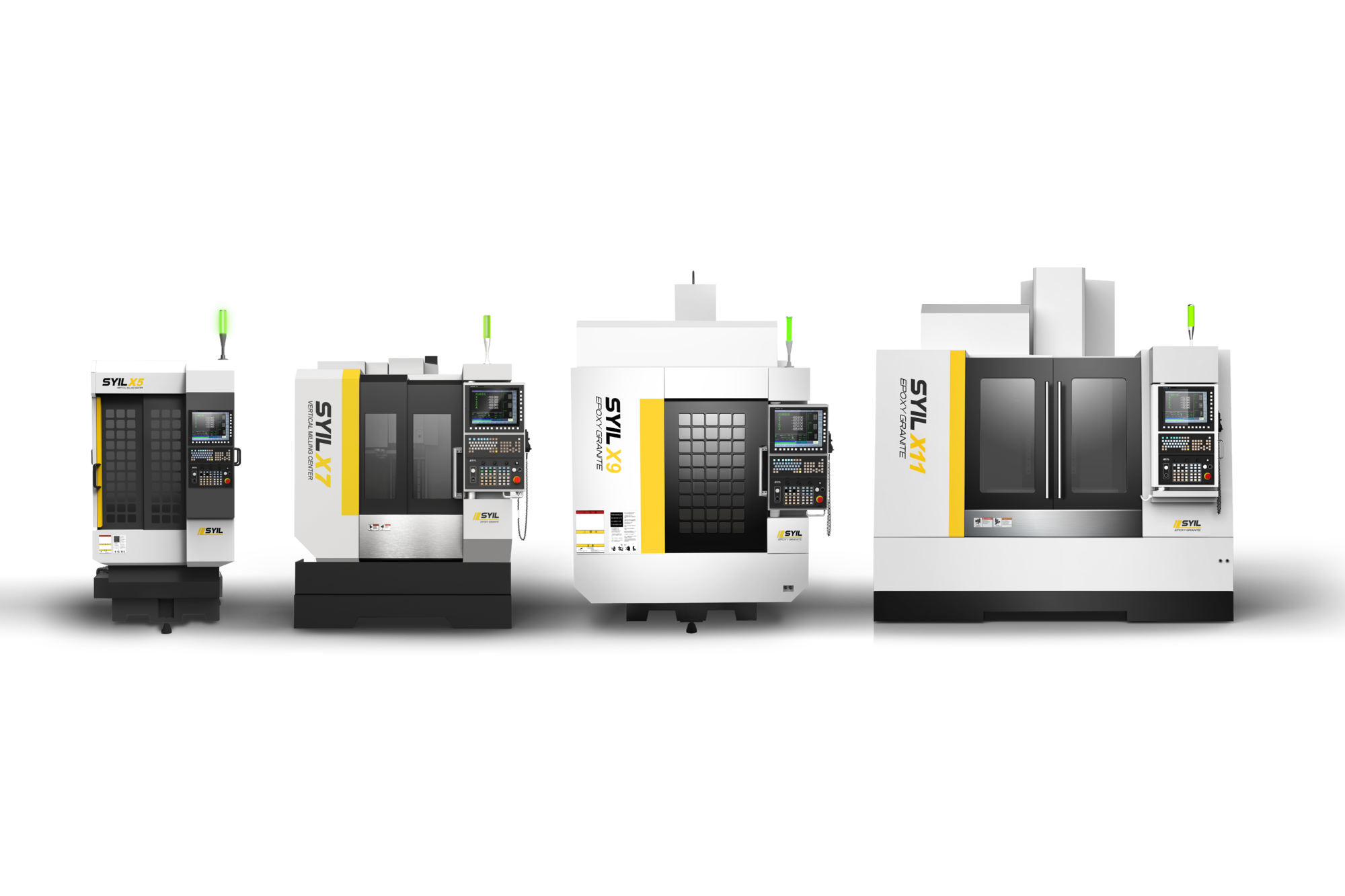
When delving into the world of CNC machining, it's essential to understand the differences between 4-axis and 5-axis machines. Both technologies have their unique features and applications, but what is a 5 axis CNC machine? Simply put, a 5-axis CNC machine can move a tool or workpiece in five different axes simultaneously, allowing for more complex shapes and intricate designs compared to its 4-axis counterpart. This flexibility makes it a popular choice in industries requiring high precision and efficiency.
Understanding the Differentiators
The primary difference between 4 and 5-axis CNC machines lies in their movement capabilities. A 4-axis machine typically adds rotation around one axis to the standard three linear movements (X, Y, Z), while a 5-axis machine introduces an additional rotational axis that allows for more complex geometries without repositioning the workpiece. This means that while both machines can create intricate parts, what is the difference between 4 and 5-axis CNC? The latter provides greater versatility and reduces setup time by allowing multiple sides of a part to be machined in one continuous operation.
Benefits of Moving to 5 Axis
Transitioning from a traditional or even a modernized 4-axis setup to what is a 5 axis CNC machine comes with numerous benefits. One significant advantage is enhanced precision; with simultaneous multi-angle cutting capabilities, manufacturers can achieve tighter tolerances than with simpler systems. Additionally, moving to a five-axis system often leads to reduced cycle times as parts require fewer setups, which ultimately saves time and money in production processes.
Key Use Cases for Each
While both types of machines have their strengths, certain applications are better suited for either technology. For instance, industries like aerospace and medical device manufacturing often rely on what is the difference between 3 and 5-axis CNC? They benefit from the advanced capabilities of five axes when producing complex components such as turbine blades or surgical instruments that require high precision at various angles. Conversely, simpler projects like basic brackets or plates might find adequate performance with a reliable four-axis machine due to its lower cost and sufficient functionality.
Exploring 6 Axis CNC Machines

When it comes to CNC machining, the evolution from 5-axis to 6-axis technology opens up new dimensions of precision and complexity. While a **5 axis CNC machine** allows for movement along five different axes, a 6-axis machine adds an additional rotational axis, enhancing its ability to create intricate geometries. This added flexibility enables manufacturers to tackle more complex parts that were previously challenging or impossible with lower axis machines.
What is the Difference Between 5 and 6 Axis?
The primary distinction between **5 and 6 axis CNC** lies in the additional rotational capability of the latter. While both systems can move in multiple directions, a **6-axis CNC machine** introduces an extra degree of freedom that allows for more versatile machining operations. This means that components can be approached from various angles without needing to reposition the workpiece, drastically reducing setup time and increasing efficiency.
For example, with a **5 axis CNC machine**, you might find limitations when machining certain undercuts or complex curves. In contrast, the sixth axis permits rotation around one of the existing axes, allowing tools to access hidden surfaces with ease. This capability makes **6-axis technology** particularly valuable in industries requiring high precision and detailed work.
Ideal Applications for 6 Axis Technology
The versatility of **6-axis CNC machines** makes them ideal for several applications across various industries. Aerospace manufacturing often utilizes this technology due to its ability to produce intricate components like turbine blades that require precise tolerances and complex shapes. Similarly, automotive production benefits from this technology when creating engine components or custom parts that demand high accuracy.
In addition to aerospace and automotive sectors, medical device manufacturing also finds significant advantages with **6-axis technology**. The ability to create detailed implants or surgical instruments efficiently is crucial in this field where precision is paramount. Moreover, industries involved in artistic sculpture or custom jewelry design leverage these machines for their unmatched capability in crafting unique designs.
The Future of CNC Machining
As we look ahead at the future of CNC machining, it's clear that advancements like **6-axis technology** will play a pivotal role in shaping manufacturing processes globally. With ongoing developments in automation and artificial intelligence integration within these machines, we can expect even greater efficiency levels than ever before. This evolution not only enhances capabilities but also leads toward smart factories where production lines are seamlessly interconnected.
Moreover, as industries continue pushing the boundaries of design innovation, understanding what is a **5 axis CNC machine** versus its advanced counterparts becomes increasingly important for engineers and manufacturers alike. The transition from traditional methods toward advanced multi-axis systems signifies not just technological progression but also a shift towards more sustainable practices by reducing waste through optimized machining processes.
As we embrace these changes, it's essential to consider how they impact various sectors while addressing questions such as: What are the disadvantages of a 5-axis CNC machine? As we innovate further into multi-axis machinery like **6-axis**, understanding limitations will aid businesses in making informed decisions regarding their equipment investments.
The Disadvantages of a 5 Axis CNC Machine
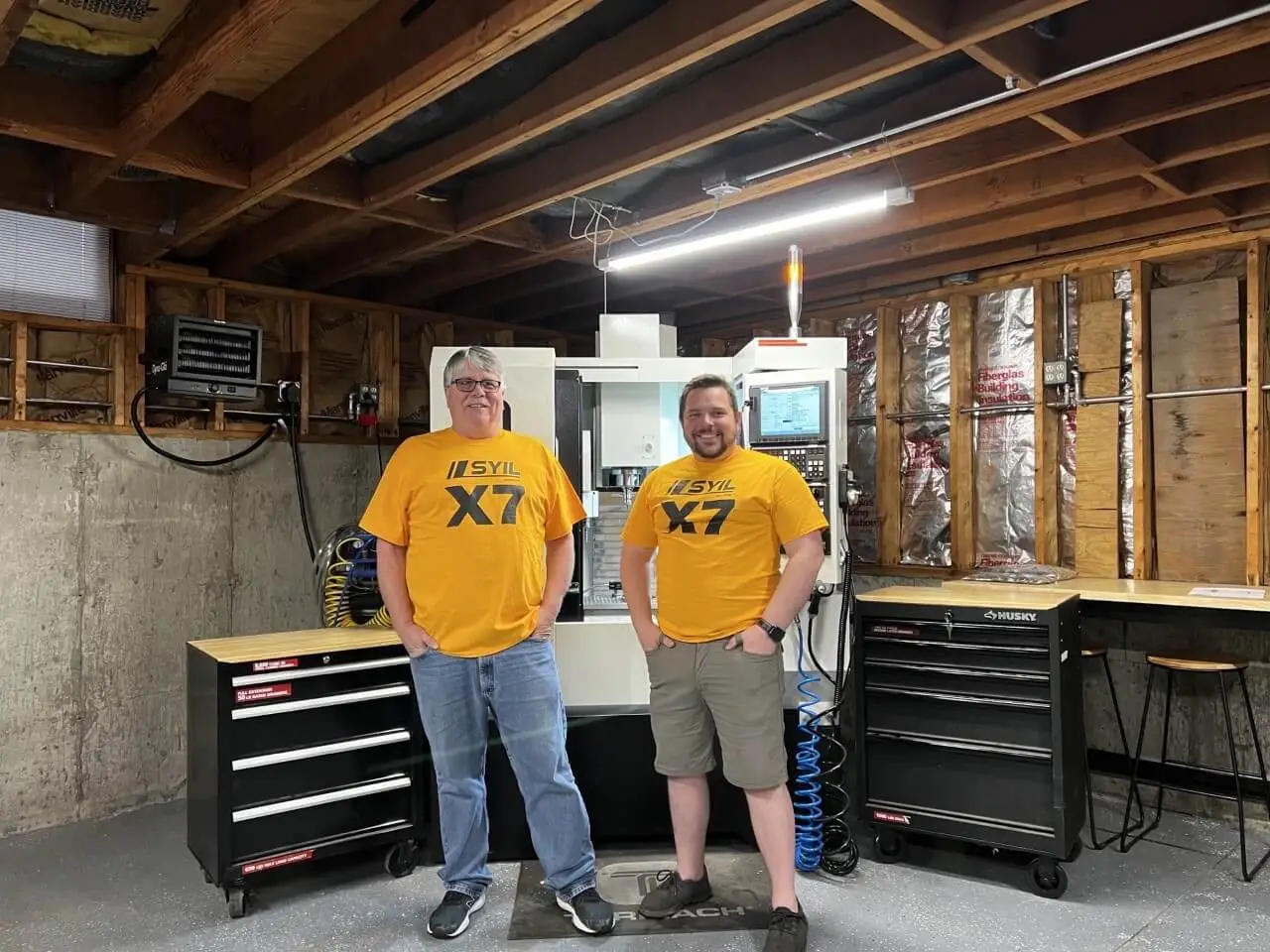
While 5 Axis CNC machines are lauded for their precision and versatility, they are not without their drawbacks. Understanding these limitations is crucial for manufacturers and engineers when considering what is a 5 axis CNC machine for their specific needs. From complexity in programming to the potential for higher maintenance demands, the disadvantages can impact both operational efficiency and project costs.
Potential Drawbacks and Limitations
One of the primary concerns with 5 Axis CNC machines is their complexity. Programming a 5 axis machine requires advanced skills and knowledge, which can be a steep learning curve compared to simpler models like 3-axis machines. Additionally, the intricate design of these machines may lead to more frequent breakdowns or maintenance issues, raising concerns about reliability over time.
Another limitation lies in the size and weight of workpieces that can be handled effectively. While 5-axis machining allows for more complex geometries, it often necessitates larger setups that may not fit within standard machine envelopes. Thus, if your projects involve larger components, you might find yourself asking what is the difference between 4 and 5-axis CNC in terms of size capabilities.
Cost Considerations
Cost is another significant factor when weighing the advantages against what are the disadvantages of a 5-axis CNC machine. The initial investment for purchasing or leasing a 5 axis system can be substantially higher than that of traditional models like 3-axis or even some advanced 4-axis machines. Furthermore, ongoing operational costs—such as maintenance, tooling changes, and skilled labor—can add up quickly.
When comparing costs across different types of CNC technology, it’s essential to conduct a thorough cost-benefit analysis based on your specific production needs. Some businesses might find that while a 5 axis machine offers superior capabilities, those benefits do not justify its expense when simpler technologies could suffice for less complex tasks.
Situations Where 5 Axis Might Not Be Ideal
Despite its many advantages, there are scenarios where utilizing a 5 axis CNC machine may not be ideal. For instance, if your projects primarily involve simple shapes or less intricate designs typically handled by what is the difference between 3 and 5-axis CNC? then investing in such advanced technology could lead to underutilization of resources.
Additionally, smaller shops with limited budgets or those just starting out in precision machining might find better value in mastering simpler systems before advancing to more complex setups like a 5 axis configuration. In cases where production runs are short or highly variable—where quick setup times matter—sticking with traditional machining methods might prove more efficient than navigating the intricacies required by advanced systems.
Conclusion
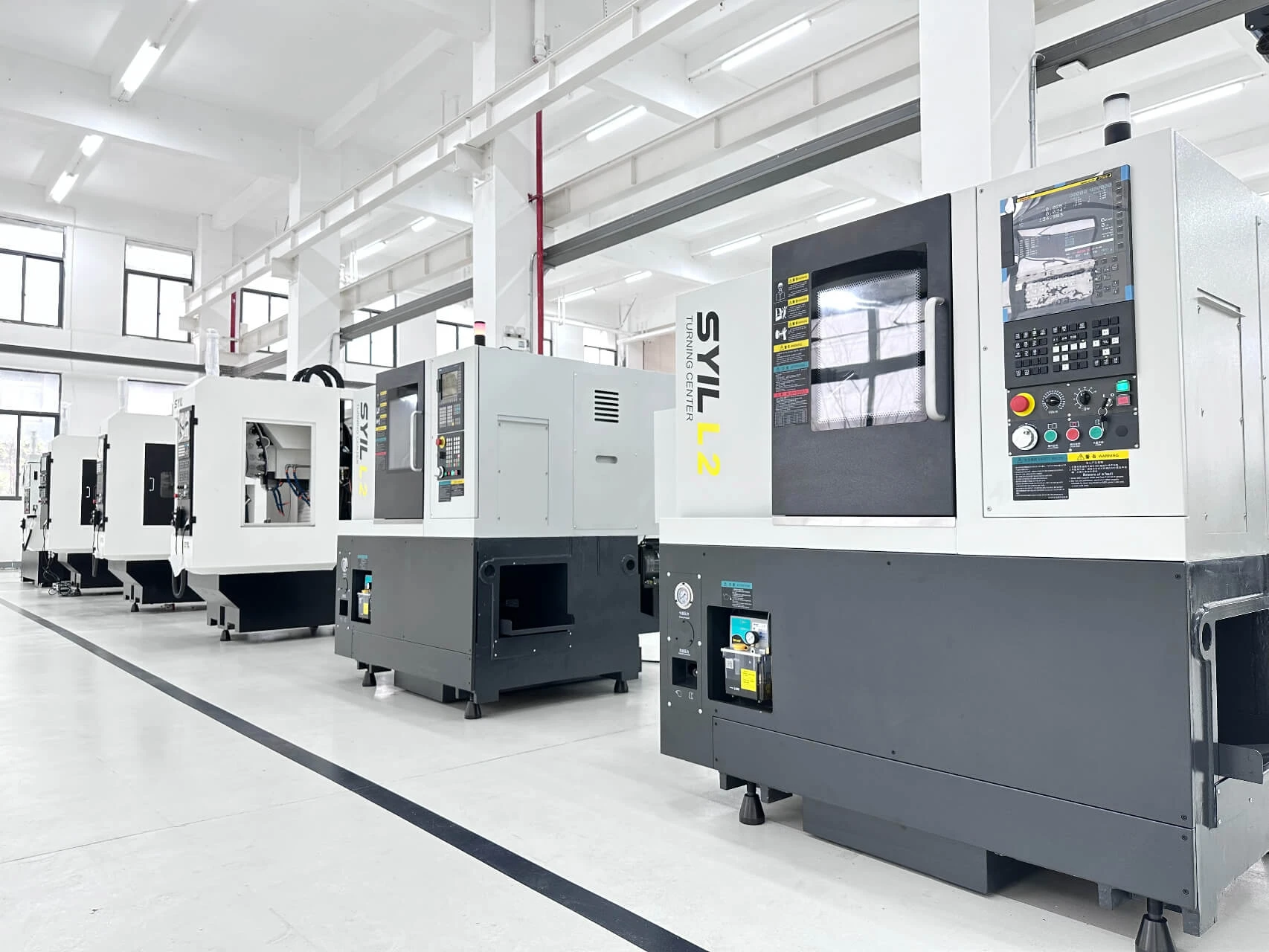
In wrapping up our exploration of 5 Axis CNC machining, it’s clear that these machines are not just tools; they are transformative assets in modern manufacturing. The versatility of a 5 Axis CNC machine allows for complex geometries and intricate designs that would be nearly impossible with traditional methods. Whether it’s aerospace components or artistic sculptures, the adaptability of 5 Axis technology ensures precision in every project.
The Versatility of 5 Axis CNC Machines
So, what is a 5 axis CNC machine? It’s a marvel of engineering that enables simultaneous movement along five different axes, allowing for unparalleled flexibility in machining processes. This versatility means manufacturers can tackle a wide variety of materials and shapes without needing to reposition the workpiece repeatedly—a significant advantage over traditional setups. From intricate parts to large-scale production runs, the capabilities of 5 Axis machines make them indispensable in today’s competitive landscape.
Innovative Applications in Various Industries
The applications for 5 Axis CNC technology stretch across numerous industries, showcasing its innovative potential. In aerospace, automotive, and medical sectors, precision is paramount; thus, understanding what is the difference between 3 and 5-axis CNC becomes crucial when selecting machinery for specific tasks. Not only do these machines allow for more complex designs than their predecessors—like the comparison between what is the difference between 4 and 5-axis CNC—they also enhance efficiency by reducing setup times and improving accuracy.
Why Choose 5 Axis CNC for Precision Work?
Choosing a 5 Axis CNC machine means investing in precision work that stands out from the competition. While there are disadvantages of a 5-axis CNC machine—such as higher costs and complexity—the benefits often outweigh these concerns when quality is on the line. For businesses aiming to elevate their craftsmanship while minimizing errors, understanding what is the difference between 5 and 6 axis CNC also plays an essential role in future-proofing operations as technology continues to evolve.