Introduction
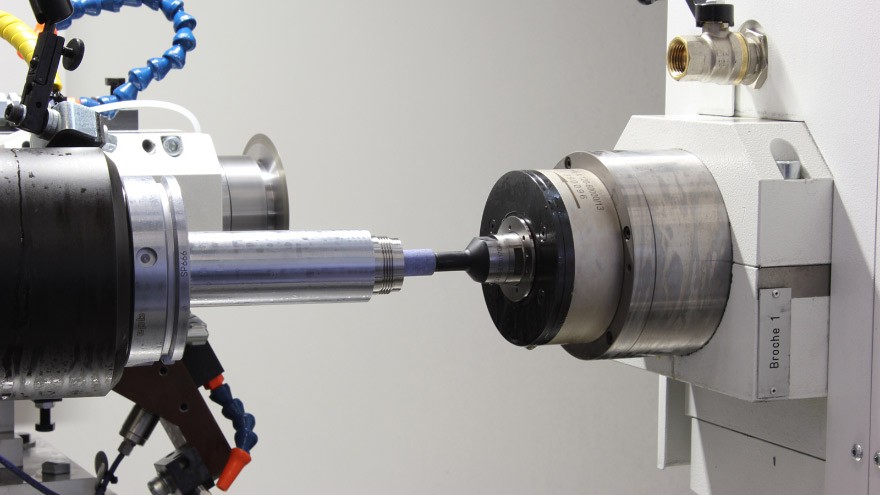
Turning is a fundamental process in engineering and manufacturing that involves shaping materials into desired forms. But what is turning in engineering, and why does it matter? This introduction will guide you through the essentials of turning, its significance in the manufacturing world, and its varied applications across different industries.
Understanding the Basics of Turning
At its core, turning refers to a machining process where a workpiece is rotated against a cutting tool to remove material and create cylindrical shapes. What does turning mean in manufacturing? It’s about precision; by controlling the speed, feed rate, and depth of cut, manufacturers can achieve intricate designs with exact specifications. So what is this turning? Essentially, it's a dance between tool and material that results in beautifully crafted components.
The Importance of Turning in Manufacturing
Turning plays a critical role in modern manufacturing by enabling the production of complex parts efficiently. Not only does it enhance productivity, but it also ensures high levels of accuracy—an essential factor when creating components for industries like aerospace or automotive. As we explore what is turning and grinding later on, you'll see how these processes complement each other to meet diverse manufacturing needs.
Key Applications of Turning Techniques
The versatility of turning techniques allows their application across various fields—from automotive parts to intricate jewelry designs made with CNC machines. Understanding these applications helps manufacturers leverage turning effectively for specific projects while maximizing efficiency and quality. With such broad usage, one might wonder: what is it turning? It’s not just about making things round; it's about crafting precision-engineered solutions tailored to industry demands.
What is Turning in Engineering?
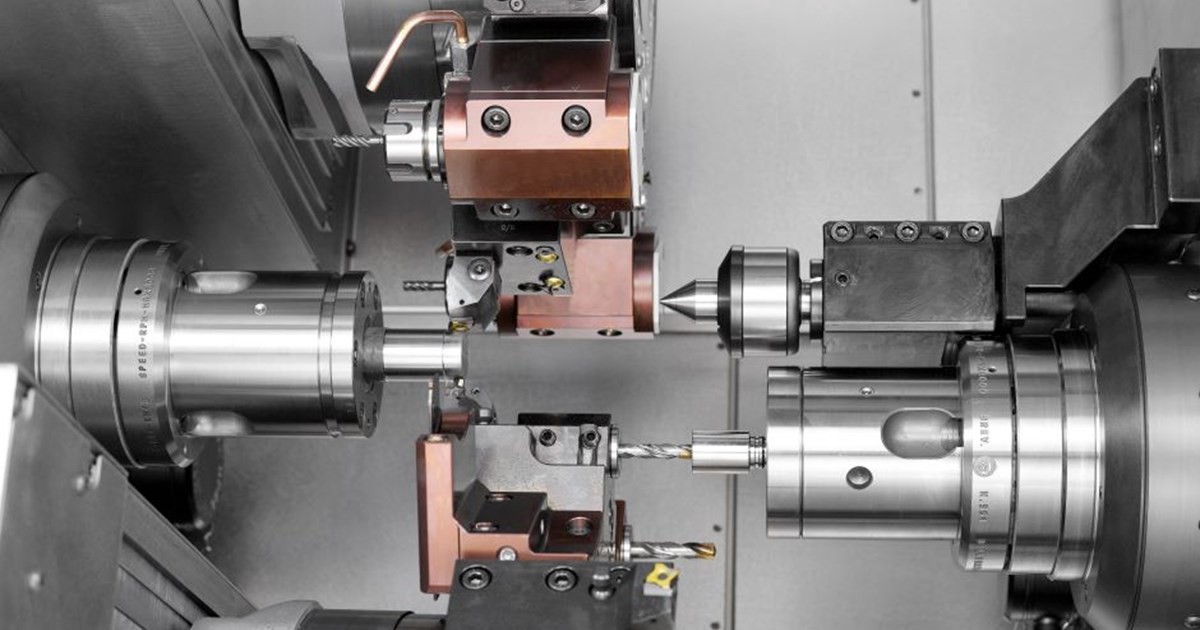
Turning is a fundamental machining process that plays a pivotal role in manufacturing. It involves rotating a workpiece against a cutting tool to create cylindrical shapes, which is essential for producing parts with precise dimensions and smooth finishes. So, what does turning mean in manufacturing? Simply put, it’s the art of material removal through rotation.
Defining Turning in Manufacturing
At its core, turning is about transforming raw materials into usable components through the application of cutting techniques. This method is primarily used to produce symmetrical shapes like shafts, pulleys, and other cylindrical items that are commonplace in various industries. Understanding what is turning in engineering helps clarify its significance: it’s not just about shaping materials; it’s about achieving accuracy and efficiency.
The Process Behind Turning
The process of turning involves several key steps that ensure precision and quality in the final product. Initially, the workpiece is securely mounted on a lathe machine where it spins at high speeds while a stationary cutting tool removes material from its surface. This dynamic interaction between the rotating object and the cutting tool defines what this turning process achieves—smooth finishes and exact dimensions tailored to specific requirements.
Common Tools Used in Turning
To carry out effective turning operations, various tools are employed that cater to different tasks within the machining realm. The most common tools include lathes (both manual and CNC), cutting bits made from high-speed steel or carbide, and tool holders designed for stability during operation. Each of these tools contributes uniquely to what is turning and grinding—creating efficient workflows that enhance productivity while maintaining high standards of quality.
What is This Turning?
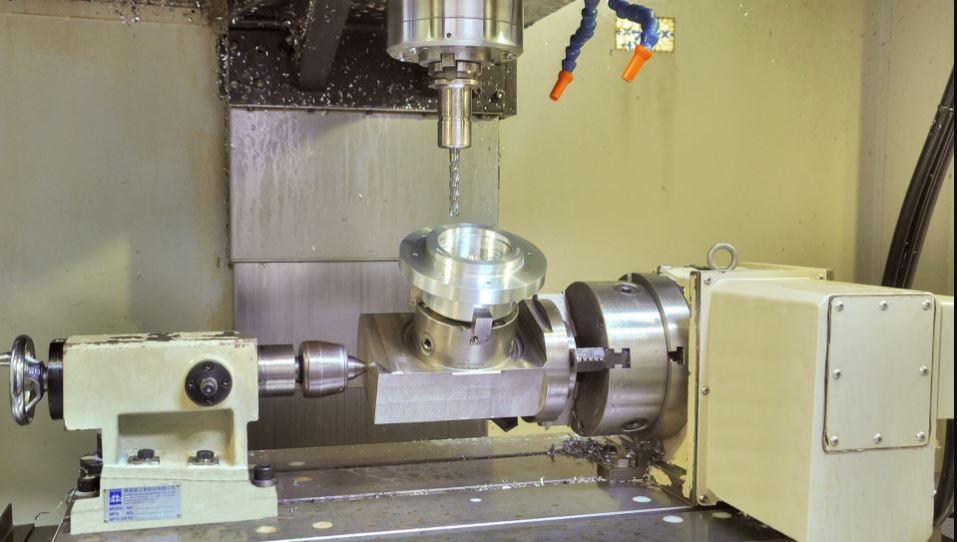
Turning is a fundamental manufacturing process that involves rotating a workpiece while a cutting tool removes material to create cylindrical shapes. But what is turning in engineering, and how does it differ from other machining processes? Understanding this distinction is crucial for manufacturers seeking to optimize their production methods and improve efficiency.
Differentiating Between Turning and Other Processes
When we ask, What does turning mean in manufacturing? we need to recognize that turning is primarily focused on producing parts with rotational symmetry. Unlike milling, which involves moving the workpiece against a stationary tool, turning rotates the material against the cutting tool, allowing for precise shaping of cylindrical components. Other processes like drilling or grinding serve different purposes; for instance, drilling creates holes while grinding refines surfaces—both of which are distinct from the primary goal of turning.
The Role of CNC Machines in Turning
In today’s advanced manufacturing environment, CNC (Computer Numerical Control) machines have revolutionized what is this turning? These sophisticated machines automate the turning process by precisely controlling the movement of both the workpiece and cutting tool based on programmed instructions. With CNC technology, manufacturers can achieve higher accuracy and repeatability than traditional manual techniques, making it easier to produce complex geometries efficiently.
Benefits of Using CNC Turning
So why should manufacturers consider CNC turning? First off, it offers unparalleled precision and consistency across large production runs—ideal for industries like aerospace or automotive where tolerances are critical. Additionally, CNC machines can be programmed to execute complex designs that would be nearly impossible with manual methods; this flexibility allows businesses to adapt quickly to changing market demands while maintaining quality standards.
What is Turning and Grinding?
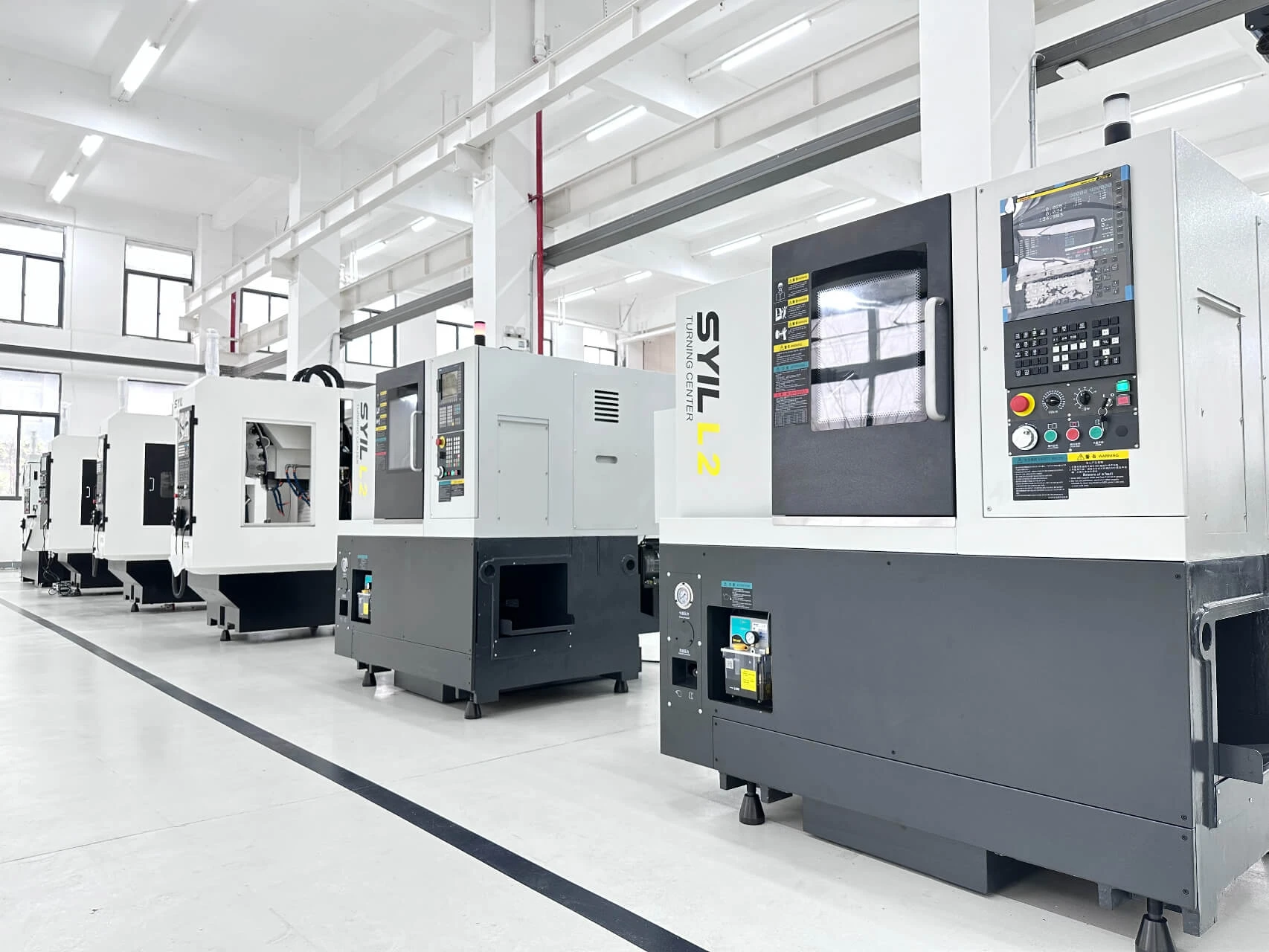
Turning and grinding are two fundamental machining processes that play critical roles in manufacturing. While both aim to shape materials, they do so using different techniques and tools. Understanding the nuances of these methods can help manufacturers optimize their production processes.
Exploring the Relationship Between Turning and Grinding
At its core, turning is a process where a cutting tool removes material from a rotating workpiece, resulting in cylindrical shapes. In contrast, grinding involves the use of an abrasive wheel to achieve fine finishes on surfaces or to shape materials with precision. So, what is turning in engineering? It’s often the first step before grinding, especially when larger material removal is required.
The relationship between turning and grinding lies in their complementary nature; while turning efficiently removes bulk material, grinding refines the finish for tighter tolerances. This synergy allows manufacturers to produce high-quality components that meet stringent specifications. In essence, understanding what this turning entails helps engineers appreciate how it sets up for subsequent grinding operations.
Applications of Grinding in Manufacturing
Grinding finds its place across various industries due to its ability to create intricate details and smooth finishes on parts that have already been turned or machined by other means. For example, it's commonly used in automotive manufacturing for components like gears and crankshafts where precise dimensions are critical. Additionally, aerospace engineering often employs grinding techniques for turbine blades or landing gear components that require exceptional surface integrity.
In jewelry creation with SYIL CNC machines, grinding can enhance aesthetic qualities by providing a polished look to intricate designs after initial shaping through turning processes. This highlights how understanding what does turning mean in manufacturing extends into numerous applications where both methods are crucial for achieving desired results.
Pros and Cons of Each Technique
When considering what is turning and grinding as individual techniques, it’s essential to weigh their advantages against their drawbacks. Turning boasts quick material removal rates and efficiency when shaping large volumes of raw stock; however, it may not achieve the same level of surface finish as grinding provides. On the other hand, while grinding excels at creating smooth surfaces with high precision, it generally takes longer than turning due to its more intricate process.
Ultimately, choosing between these two methods hinges on project requirements such as tolerances needed and production volume considerations—what is it turning? It’s about finding balance! By understanding both techniques' strengths and weaknesses within manufacturing contexts, engineers can make informed decisions that enhance productivity without sacrificing quality.
Techniques and Methods in Turning
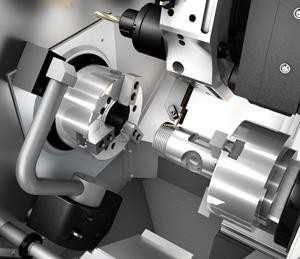
Turning is a vital process in engineering that involves shaping materials to create precise components. Understanding what turning means in manufacturing is crucial for anyone involved in the production of parts, as it directly impacts quality and efficiency. Various techniques have emerged over the years, each tailored to meet specific needs and applications.
Various Turning Techniques Explained
When we ask, What is turning in engineering? we're diving into a world filled with diverse techniques that can transform raw materials into finished products. Conventional turning methods include straight turning, taper turning, and contour turning, each serving unique purposes based on design specifications. Additionally, advanced techniques like hard turning are gaining traction due to their ability to machine hardened materials without requiring grinding.
Another exciting area is live tooling, which integrates milling capabilities into the lathe for enhanced versatility. This means that while performing what does turning mean manufacturing tasks, operators can also execute complex shapes and features without switching machines. Ultimately, understanding these various turning techniques can significantly elevate manufacturing processes and outcomes.
How Workpiece Material Affects Turning
The material being turned plays a critical role in determining the appropriate technique and tools used during the process. Different metals—like aluminum or steel—require distinct approaches due to their varying hardness levels and machinability characteristics. For instance, when considering what is this turning? it becomes evident that softer materials may allow for faster cutting speeds compared to harder alloys that necessitate slower feeds to prevent tool wear.
Moreover, workpiece material also influences tool selection; high-speed steel (HSS) tools may be suitable for softer materials while carbide tools are often preferred for tougher metals due to their durability. Understanding how workpiece material affects turning helps manufacturers optimize their processes by selecting the right combination of speed, feed rate, and tooling strategy tailored specifically for each job at hand.
Innovations in Turning Technology
The landscape of what is turning and grinding has evolved dramatically thanks to technological advancements like CNC (Computer Numerical Control) systems which automate precision machining tasks with exceptional accuracy. These innovations not only enhance efficiency but also reduce human error—a significant advantage when considering what does turning mean manufacturing today compared to traditional methods.
Additionally, recent developments such as adaptive control technology allow lathes to automatically adjust parameters during machining based on real-time feedback from sensors monitoring cutting conditions. This level of sophistication highlights how manufacturers are continually seeking ways to improve productivity while maintaining high-quality standards across various applications of what is it turning?
In conclusion, staying abreast of innovations within the realm of turning technology ensures manufacturers remain competitive within an ever-evolving industry landscape.
Real-World Applications of Turning
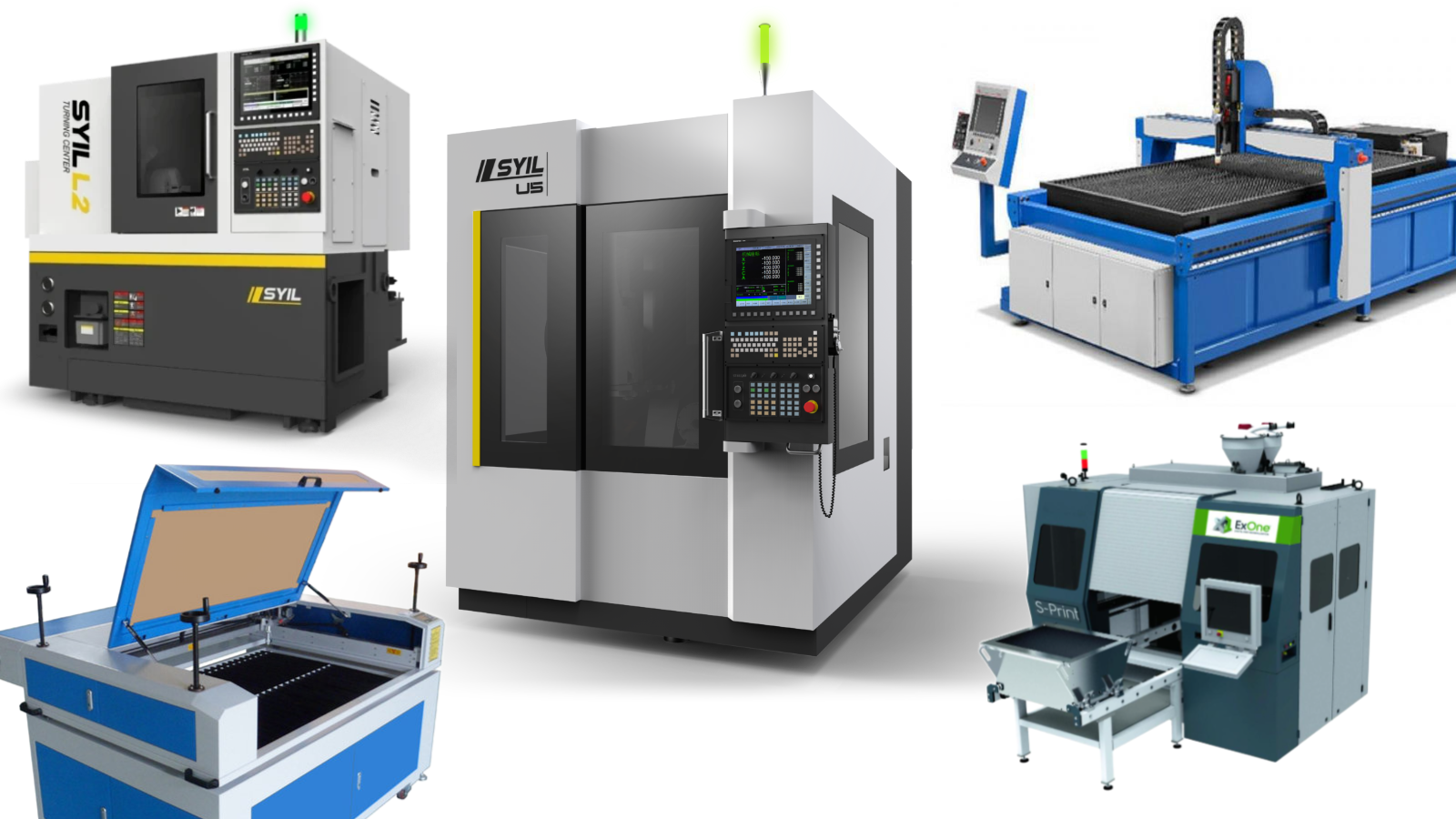
Turning is a versatile machining process that finds its way into various industries, showcasing its importance in engineering and manufacturing. From creating complex aerospace components to crafting intricate jewelry, the applications of turning are vast and diverse. Understanding what turning means in manufacturing can help us appreciate its role in these fields.
Turning in Aerospace Engineering
In aerospace engineering, precision is paramount. Components such as turbine blades and landing gear require exact specifications, making the question What is turning in engineering? particularly relevant here. The turning process allows for the creation of cylindrical parts with tight tolerances, ensuring safety and performance in flight.
The use of CNC (Computer Numerical Control) machines has revolutionized how aerospace components are manufactured. These machines can execute complex designs with high accuracy, reducing human error and increasing productivity—factors crucial for the demanding aerospace sector. By leveraging advanced turning techniques, engineers can produce lightweight yet robust parts that meet stringent regulations.
Moreover, the integration of new materials like composites into aerospace design has expanded the scope of what does turning mean manufacturing-wise. Turning techniques must adapt to handle these materials effectively while maintaining quality standards. Thus, understanding what this turning entails is essential for engineers working on cutting-edge aircraft technologies.
The Role of Turning in Automotive Manufacturing
Turning plays a critical role in automotive manufacturing as well, where efficiency and precision drive production lines forward. What does turning mean manufacturing when it comes to car parts? It’s about creating everything from engine components to transmission housings with utmost accuracy—ensuring vehicles operate smoothly and reliably.
Automakers utilize CNC turning machines to produce parts at scale without sacrificing quality or speed. These machines allow manufacturers to create complex geometries that fit perfectly within a vehicle's assembly line requirements while minimizing waste material during production processes. Consequently, this innovative approach not only enhances productivity but also reduces costs—a win-win situation for manufacturers.
Furthermore, understanding what is it turning involves recognizing how advancements in technology continue to shape automotive design trends. With electric vehicles on the rise, manufacturers need adaptable techniques that can accommodate new designs and materials efficiently—turning remains at the forefront of these changes by enabling rapid prototyping and customization.
Turning in Jewelry Creation with SYIL CNC Machines
Turning isn't just confined to industrial applications; it's also making waves in creative fields like jewelry making! Jewelers increasingly turn to CNC technology for their intricate designs because they offer precision that handcrafting simply cannot match—what is this turning doing for artisans? It's transforming how they approach their craft!
SYIL CNC machines have become popular among jewelers looking to elevate their creations through advanced machining techniques. With these tools, artisans can create delicate rings or stunning pendants with remarkable detail while ensuring consistency across multiple pieces—a feat that's difficult when relying solely on traditional methods. This fusion of art and technology highlights how versatile what is turning really is!
However, while exploring what is turning and grinding reveals both processes serve distinct purposes within manufacturing contexts; jewelers often leverage both techniques depending on their design needs—turning for shaping intricate forms and grinding for fine finishing touches! So whether you’re crafting a bespoke piece or mass-producing fashion jewelry lines, understanding these processes opens up a world of creative possibilities.
Conclusion
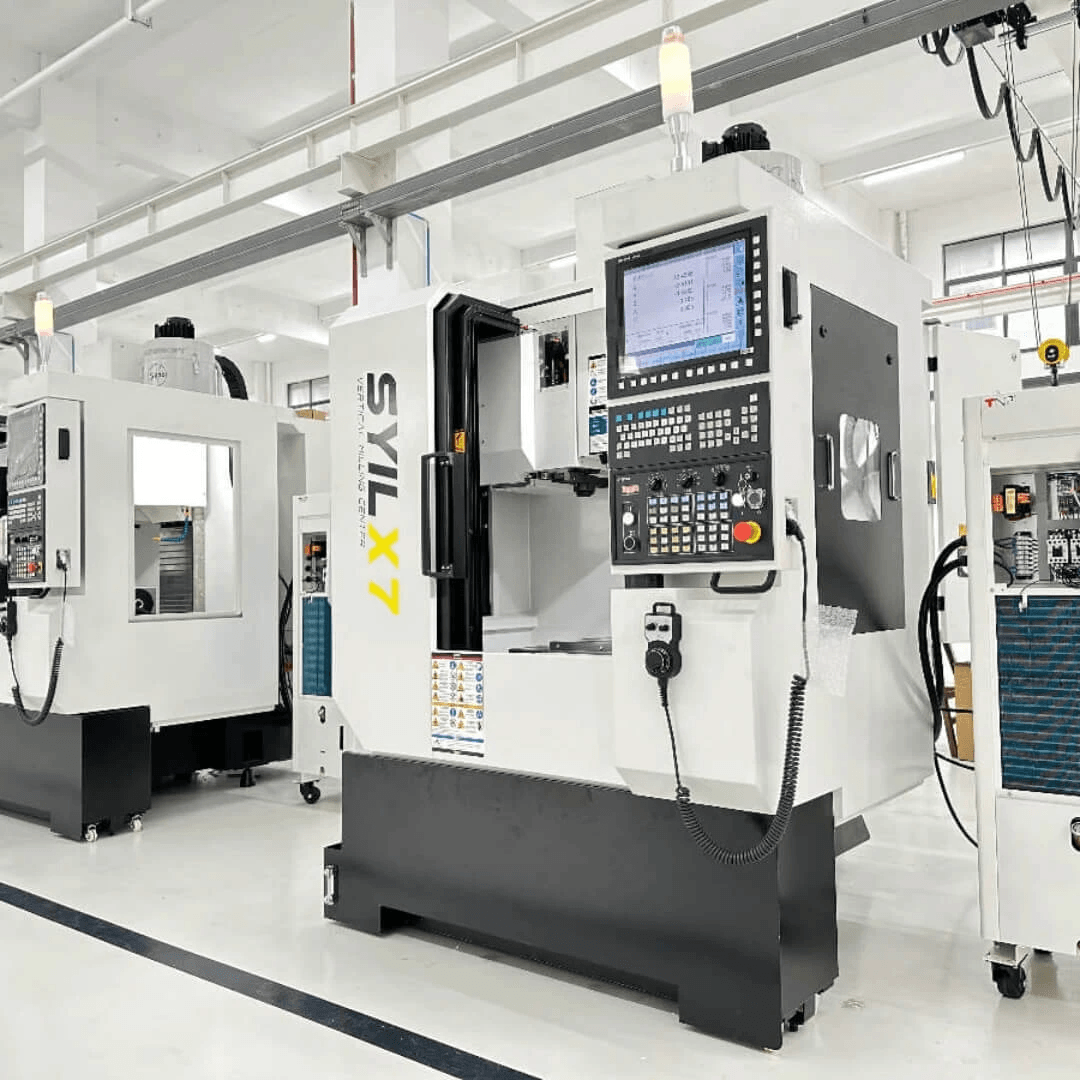
In wrapping up our exploration of turning, it’s clear that this technique is not just a manufacturing process; it’s a cornerstone of modern engineering. The future of turning in engineering looks promising, driven by advancements in technology and the ever-increasing demand for precision and efficiency. As industries evolve, understanding what is turning in engineering will be crucial for manufacturers striving to stay competitive.
The Future of Turning in Engineering
The landscape of manufacturing is changing rapidly, with innovations shaping how we approach traditional processes like turning. What is this turning? It’s becoming increasingly automated through CNC (Computer Numerical Control) technology, which enhances precision and reduces human error. As we look forward, the integration of smart technologies and AI into turning processes will redefine efficiency and capabilities.
Why Understanding Turning Matters for Manufacturers
For manufacturers, grasping the nuances of what does turning mean in manufacturing can significantly impact production quality and cost-effectiveness. Understanding these techniques allows companies to optimize their operations, reduce waste, and improve product quality—all essential factors in today’s competitive market. Moreover, knowing what is turning and grinding helps manufacturers choose the right processes for their specific needs.
Getting Started with Turning Projects
If you're intrigued by the world of turning and eager to dive into your own projects, it's essential to start with a solid foundation. Familiarize yourself with what it is turning entails—research various techniques and tools available at your disposal. Whether you're working on a small-scale project or aiming for industrial applications like aerospace or automotive components, understanding how to effectively apply these methods will set you on the path to success.