Introduction

In the world of machining, the 5 axis lathe stands out as a marvel of engineering, offering unparalleled precision and versatility. As industries demand more complex geometries and tighter tolerances, understanding what a 5-axis lathe can do becomes essential for manufacturers aiming to stay competitive. This introduction will delve into the importance of flexibility in machining and highlight key differences in axis functionality that set 5-axis systems apart from their more traditional counterparts.
Understanding the 5 Axis Lathe
So, what is a 5-axis lathe? Simply put, it is a sophisticated machine tool that can move a cutting tool or workpiece along five different axes simultaneously. This capability allows for intricate shapes and complex parts to be machined with high accuracy and efficiency—something that traditional lathes struggle to achieve. With advancements in technology, the 5 axis lathe has become an indispensable tool for precision engineering applications.
The Importance of Flexibility in Machining
Flexibility in machining is not just a luxury; it’s a necessity in today’s fast-paced manufacturing environment. The ability to perform multiple operations on one machine reduces setup times and enhances productivity, making the 5 axis lathe an attractive option for companies looking to streamline their processes. Moreover, this flexibility enables manufacturers to adapt quickly to changing market demands without investing heavily in additional equipment.
Key Differences in Axis Functionality
When considering how many axes can a lathe have, it's crucial to understand that each additional axis contributes significantly to its capabilities. For instance, while both 3-2 axis and 5-axis configurations allow for multi-directional movement, what is the difference between them? The primary distinction lies in how they handle complex geometries; whereas 3-2 axis machines require repositioning between cuts, 5-axis machines can execute all operations continuously without interruption—leading to enhanced efficiency and reduced production time.
What is a 5 Axis Lathe?
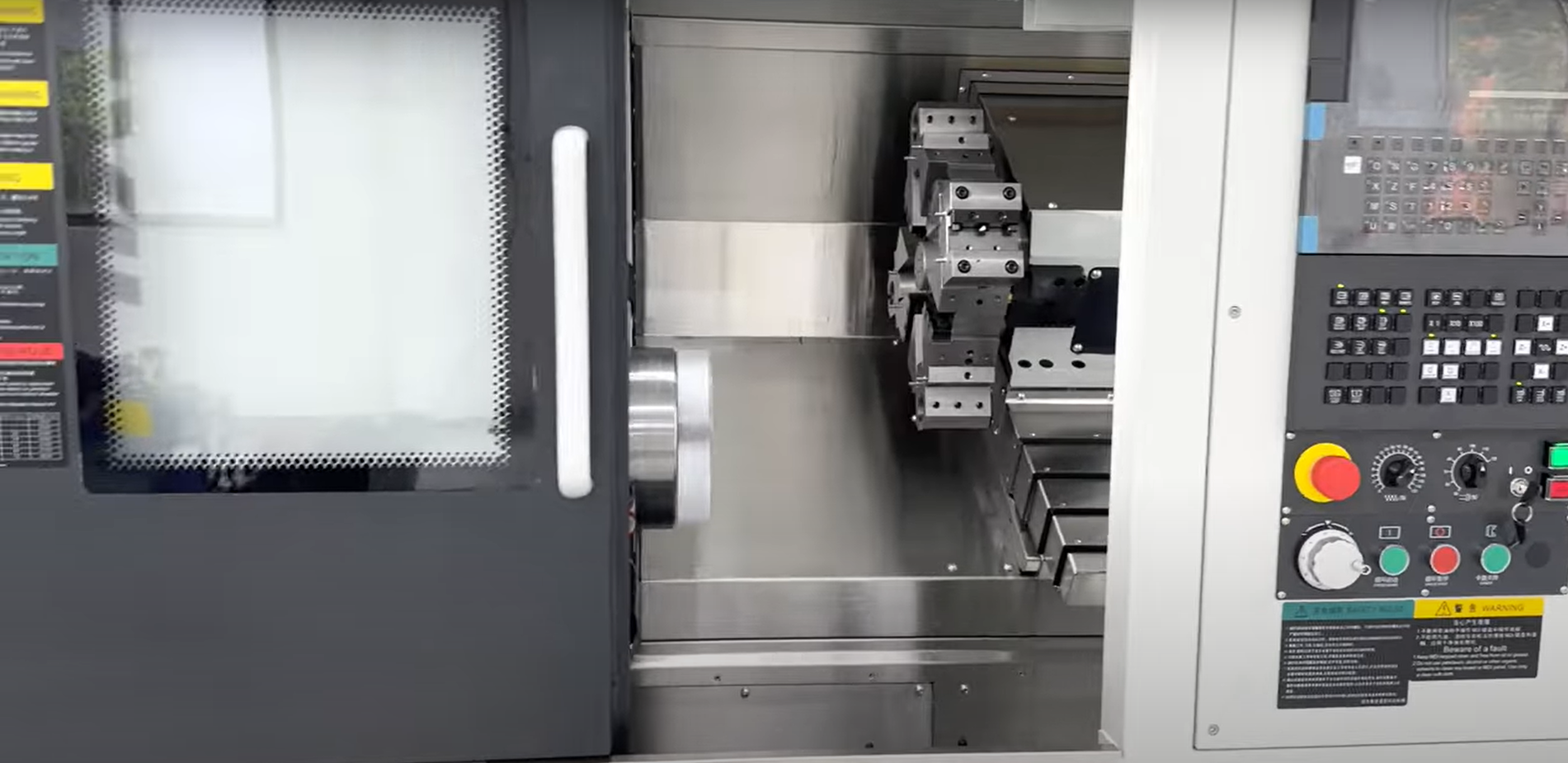
A 5 axis lathe is a sophisticated piece of machinery that allows for enhanced precision and versatility in machining operations. Unlike traditional lathes, which typically operate on two or three axes, the 5 axis lathe integrates additional rotational capabilities, enabling it to perform complex cuts and shapes with greater accuracy. This advancement in technology has transformed how manufacturers approach intricate designs and high-tolerance components.
Basic Principles of Multi-Axis Machining
At its core, multi-axis machining refers to the ability of a machine tool to move along multiple axes simultaneously, which is essential for creating complex geometries. In the case of a 5 axis lathe, this means that it can manipulate the workpiece not just in linear movements (X, Y, Z) but also through rotations (A and B axes). This flexibility allows operators to achieve intricate details without needing to reposition the material repeatedly—a time-saving feature that enhances productivity.
Understanding What is a 5-axis lathe? goes beyond just its mechanics; it's about recognizing how these machines can revolutionize manufacturing processes. For instance, while traditional lathes might require multiple setups for different angles or features, a 5 axis lathe can accomplish all this in one continuous operation. This capability significantly reduces cycle times and improves overall efficiency.
Applications in Precision Engineering
The applications of a 5 axis lathe are vast and varied within precision engineering fields such as aerospace, automotive, and medical device manufacturing. These industries often require components with tight tolerances and complex shapes—tasks perfectly suited for multi-axis machining capabilities. From turbine blades to intricate surgical instruments, the ability to machine parts from multiple angles without manual intervention makes these lathes invaluable.
Moreover, when exploring How many axes can a lathe have?, it's clear that while some applications may only need three or four axes for simple tasks, high-end industries benefit immensely from five-axis technology due to its superior flexibility and precision. As engineers push boundaries on design complexity and performance requirements, having access to advanced machinery like the 5 axis lathe becomes essential for staying competitive.
Benefits Over Traditional Lathes
The benefits of using a 5 axis lathe over traditional models are strikingly evident when you consider factors such as speed, accuracy, and versatility. First off—let's talk speed! With fewer setups required due to its multi-directional capabilities, manufacturers can dramatically reduce production times while maintaining high levels of precision.
Additionally, understanding What is the difference between 3-2 axis and 5-axis? reveals that while both systems allow for some degree of complexity in machining operations—3-2 lathes generally restrict movement compared to full five-axis systems that enable complete freedom of motion around all critical points on the workpiece surface. This leads not only to better quality parts but also opens doors for innovative designs previously deemed too challenging or impossible using conventional methods.
Finally, let's not forget about cost considerations: although initial investments like 5 axis CNC machine price might seem higher than their simpler counterparts at first glance; long-term savings from reduced labor costs combined with improved cycle times often make them worth every penny spent by savvy manufacturers looking at their bottom line!
Axis Count and Functionality
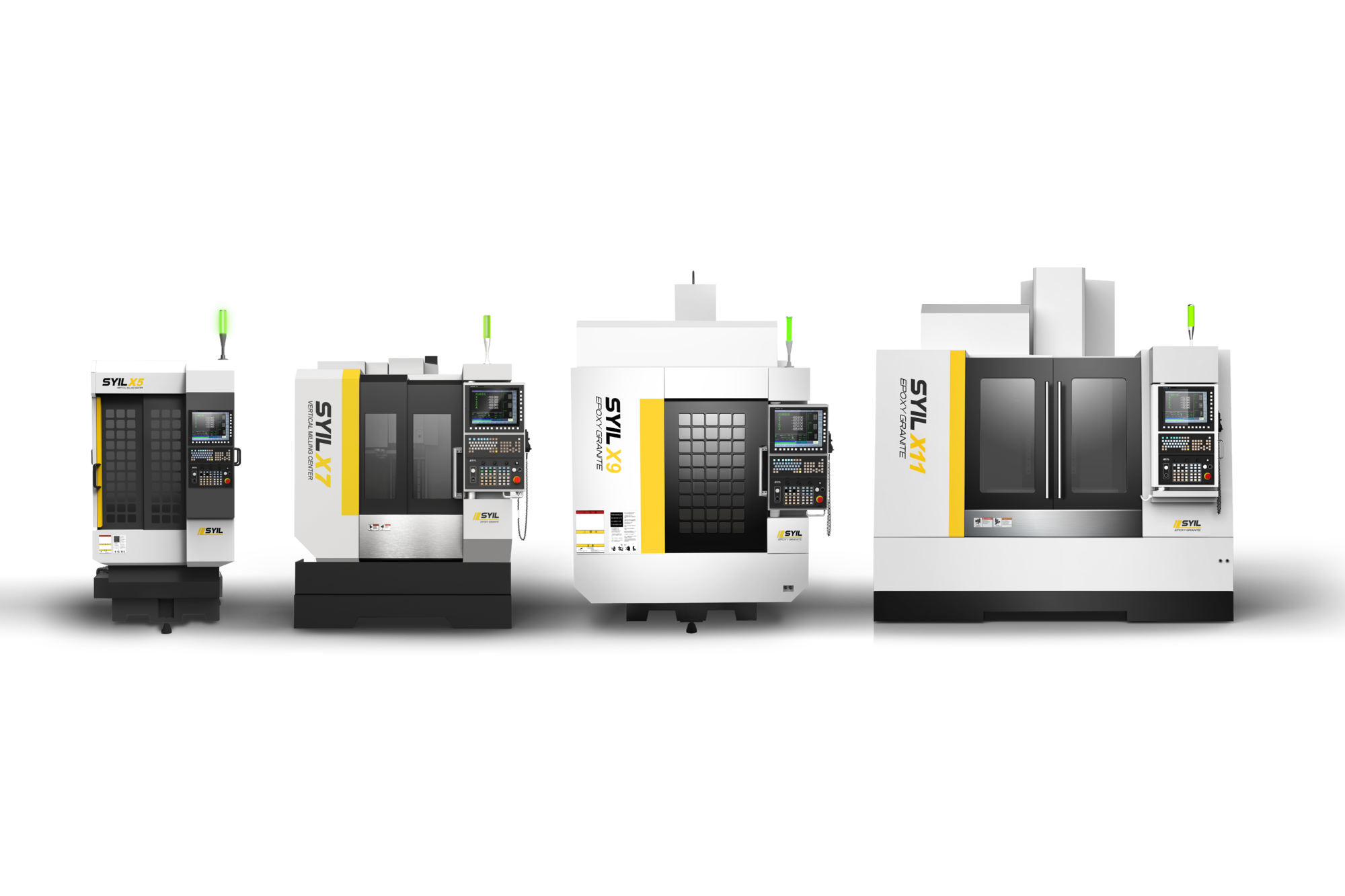
Understanding the axis count and functionality of a lathe is crucial for anyone venturing into advanced machining. The number of axes a lathe can have directly impacts its versatility, precision, and application range. In this section, we will explore how many axis can a lathe have, analyze the differences between 3 2 axis and 5-axis configurations, and discuss the practical implications of adding more axes to your machining arsenal.
How Many Axis Can a Lathe Have?
When it comes to lathes, the axis count can vary significantly based on design and purpose. Most traditional lathes operate on a simple two-axis system—X (horizontal) and Z (vertical)—but modern advancements have led to the development of multi-axis lathes that enhance capabilities dramatically. So, how many axis can a lathe have? Well, you’ll find options ranging from basic two-axis machines to complex five-axis lathes that allow for intricate designs with greater precision.
Analyzing 3 2 Axis vs. 5 Axis
Now let’s dive into what is the difference between 3 2 axis and 5-axis configurations in machining environments. A three-two axis machine allows for movement along three axes but limits some rotational capabilities compared to its five-axis counterpart. In contrast, what is a 5-axis lathe? It enables simultaneous movement along all five axes—X, Y, Z plus two rotational axes—which allows for more complex geometries without needing multiple setups or tool changes.
The key takeaway here is that while both configurations can achieve impressive results, the flexibility offered by a five-axis CNC machine price often justifies its higher cost when compared to simpler models like those with only three or four axes.
Practical Implications of Added Axes
The addition of more axes on your lathe has practical implications that extend beyond mere capability; it influences efficiency and production costs as well. With a 5 axis lathe, you can perform multiple operations in one setup—reducing cycle times and minimizing errors associated with repositioning workpieces. This means not only do you save time but also improve overall part accuracy—a critical factor in industries where precision is paramount.
However, this sophistication does come at an increased investment reflected in the average price of these machines; thus understanding the financial aspects like average 5 axis CNC machine price becomes essential for small businesses looking to make informed decisions about their equipment investments.
Key Features to Evaluate
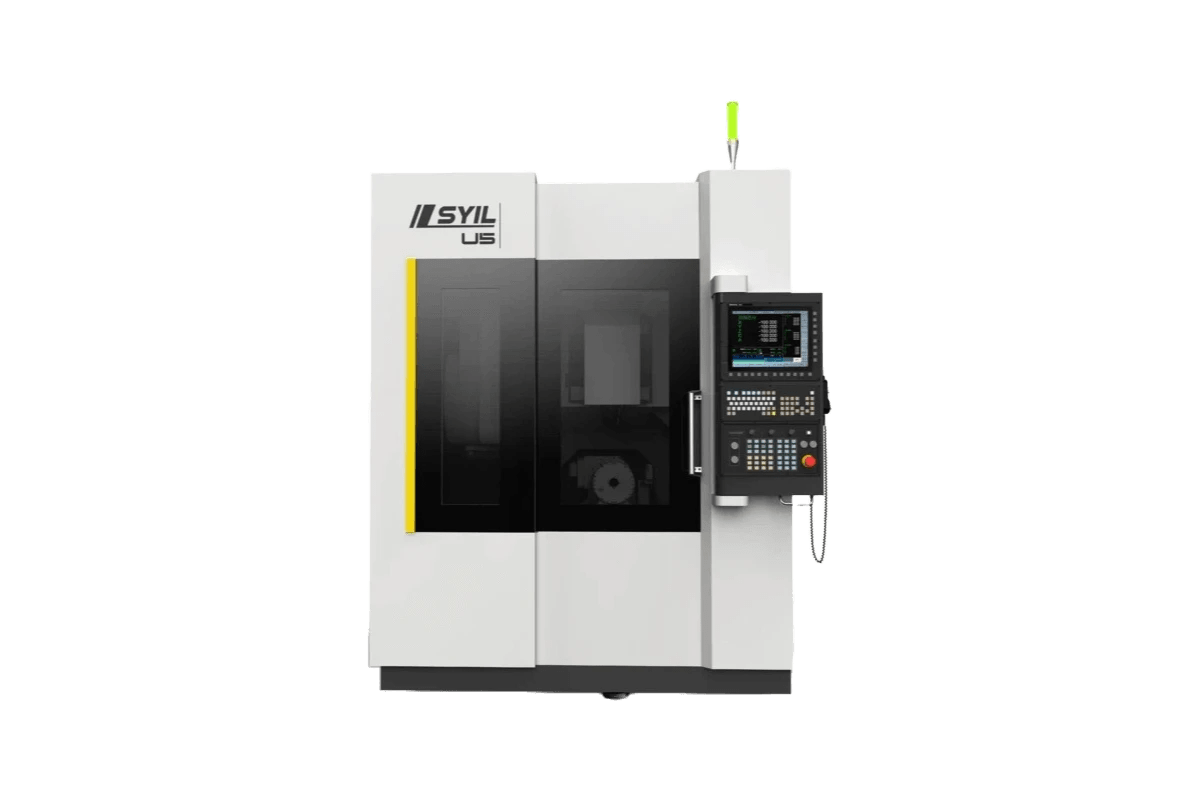
When investing in a 5 axis lathe, it's crucial to consider several key features that can significantly impact performance and productivity. Understanding these elements ensures that you choose a machine that meets your specific needs and enhances your machining capabilities. Here, we will explore the importance of rigidity and stability, control systems and user interfaces, as well as tooling and workholding options.
Importance of Rigidity and Stability
Rigidity and stability are paramount when discussing what is a 5-axis lathe. A machine with high rigidity minimizes vibrations during operation, which can lead to improved precision in machining processes. Stability is equally important; it ensures consistent performance over time, reducing wear on components and prolonging the lifespan of the lathe.
In the context of how many axis can a lathe have, adding more axes increases complexity but also enhances flexibility in machining operations. For instance, when comparing what is the difference between 3 2 axis and 5-axis configurations, it becomes clear that the latter requires robust construction to handle additional forces during cutting operations. Therefore, investing in a well-built machine from reputable 5 axis lathe manufacturers can yield better results.
Additionally, a stable platform allows for higher feed rates without sacrificing accuracy—an essential factor for any precision engineering application using a 5 axis CNC machine price consideration. Ultimately, selecting a lathe that emphasizes rigidity will pay dividends in terms of both quality output and operational efficiency.
Control Systems and User Interface
The control system of a 5 axis lathe plays an integral role in its usability and functionality. A sophisticated control interface not only simplifies programming but also allows machinists to execute complex tasks with ease—essentially answering what is a 5-axis lathe's potential for versatility in applications. An intuitive user interface contributes significantly to minimizing training time for operators while maximizing productivity on the shop floor.
When evaluating control systems, consider how many axis can a lathe have effectively managed by its software capabilities. The difference between various setups often lies within their programming flexibility; machines equipped with advanced controls may offer features such as simulation modes or real-time feedback loops that enhance operational efficiency further than simpler models like those found in what is the difference between 4 and 5-axis CNC machines? The more advanced systems typically facilitate smoother transitions between different axes during operation.
Moreover, understanding these differences helps businesses assess whether they are getting value for their investment relative to their budget constraints—especially important when considering factors like overall 5 axis lathe price versus functionality offered by leading manufacturers.
Tooling and Workholding Options
Tooling versatility is another vital feature when selecting your ideal 5 axis lathe setup—it directly impacts both production speed and quality outcomes! In essence, effective tooling combined with appropriate workholding options allows machinists to tackle diverse projects without needing extensive changes or downtime—a significant advantage over traditional lathes where setups may be cumbersome or limited.
What is the difference between traditional tooling methods versus those designed specifically for multi-axis applications? The latter often includes specialized holders or adapters that enhance accessibility while ensuring secure placements throughout operations—a critical factor given how many axis can a lathe utilize simultaneously! This adaptability becomes particularly valuable when assessing practical implications related to increased axes; having tailored tools means you can maximize productivity without compromising precision.
Finally, evaluating available tooling options also ties into cost considerations associated with owning such machinery—both regarding initial investments (like examining various models’ prices) as well as ongoing maintenance costs linked directly back towards selected tool types used on each project undertaken at any given time!
Price Factors for 5 Axis Lathes
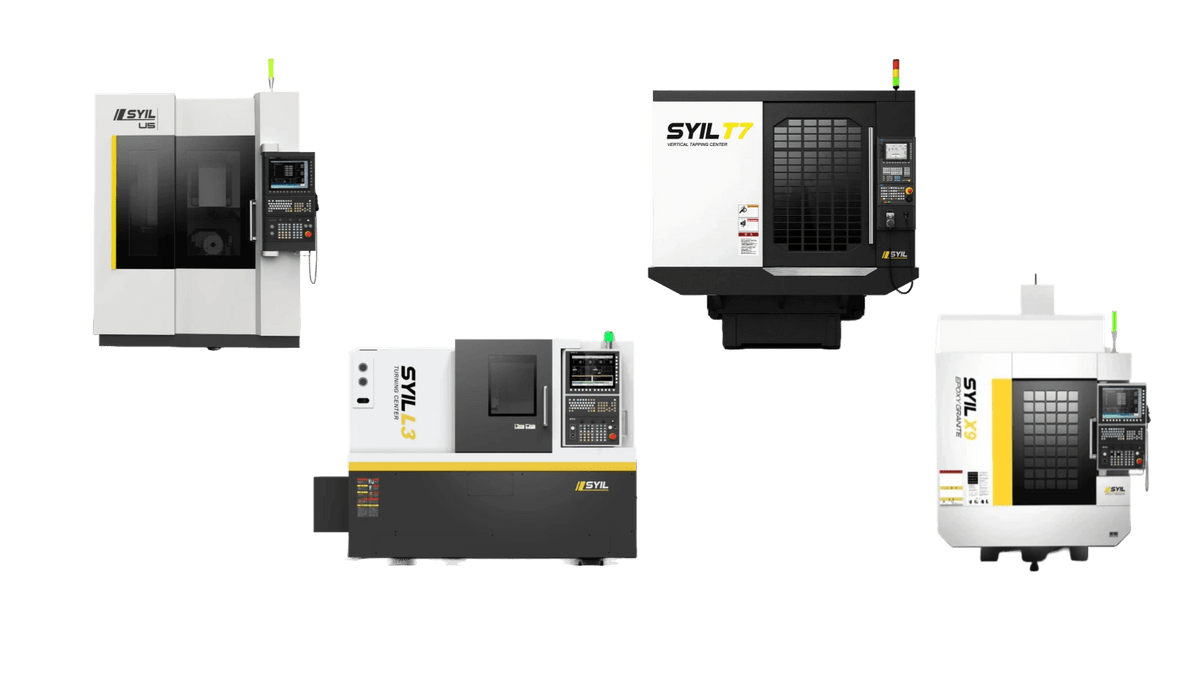
When considering a 5 axis lathe, understanding the price factors involved can be quite the challenge. The prices of these machines are influenced by various elements, including technology, brand reputation, and machine capabilities. By examining these factors, potential buyers can make informed decisions that align with their machining needs and budget.
Understanding 5 Axis Lathe Price Trends
The price trends for a 5 axis lathe have seen significant fluctuations over recent years, primarily driven by advancements in technology and increased demand for precision engineering solutions. As manufacturers innovate and improve their offerings, the cost of high-quality 5 axis CNC machines has become more accessible to a wider range of businesses. However, understanding what constitutes a fair price requires knowledge about features such as rigidity, stability, and control systems—elements that significantly impact the overall value of a 5 axis lathe.
Comparisons in 5 Axis CNC Machine Price
When comparing the prices of different models within the category of 5 axis CNC machines, it is essential to consider not just the base cost but also what you get for your investment. Generally speaking, prices can vary widely based on brand reputation and additional features—such as advanced tooling options or enhanced user interfaces—that improve functionality. For example, while some manufacturers may offer budget-friendly options for entry-level users asking What is a 5-axis lathe?, others may provide premium models designed for high-volume production at higher costs.
Financial Considerations for Small Businesses
For small businesses contemplating investing in a 5 axis lathe, financial considerations are paramount to ensure sustainable growth without breaking the bank. It's crucial to evaluate not only the initial purchase price but also ongoing operational costs—including maintenance and tooling expenses—when determining affordability. Additionally, small businesses should weigh the benefits of acquiring advanced machinery against potential returns on investment through improved efficiency and precision; after all, understanding How many axes can a lathe have? could lead to enhanced productivity that justifies higher upfront costs.
Leading 5 Axis Lathe Manufacturers
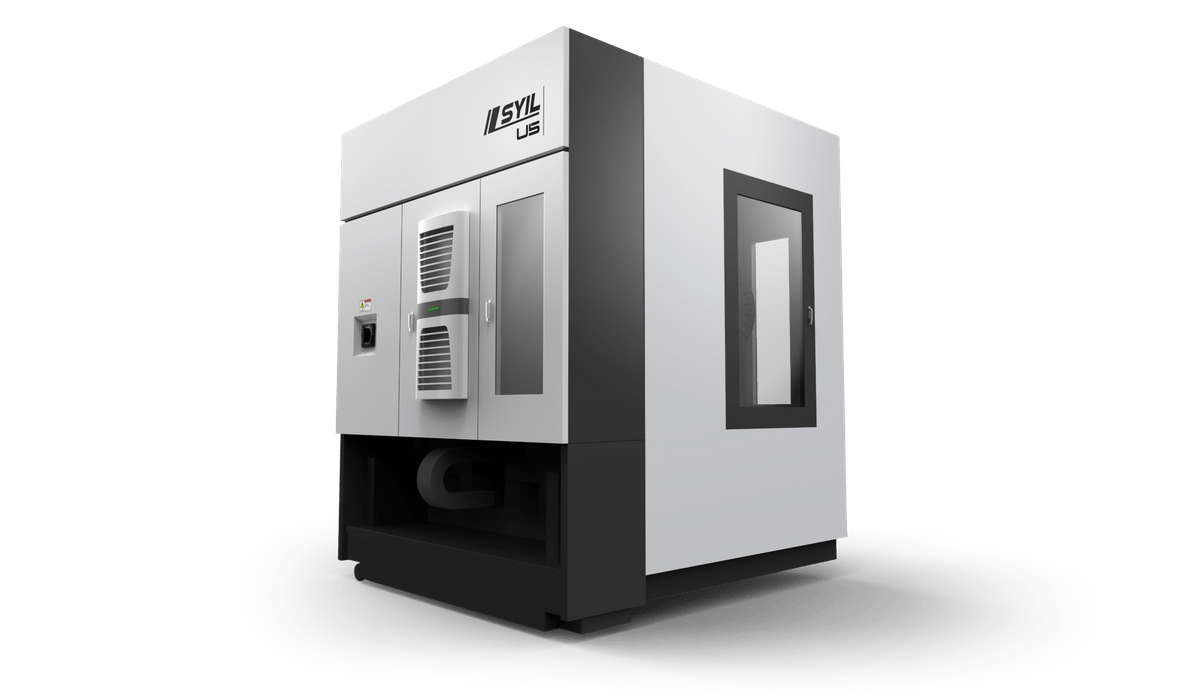
When it comes to investing in a 5 axis lathe, knowing the key players in the market can make all the difference. The landscape of 5 axis lathe manufacturers is filled with companies that offer innovative solutions tailored to various machining needs. Understanding who these manufacturers are and their unique offerings can help you make an informed decision about your next machining investment.
Notable Names in the Industry
The world of 5 axis lathes boasts some heavyweights that have established themselves as leaders in precision engineering. Companies like Haas Automation, DMG Mori, and Mazak are well-known for their high-quality machines that push the boundaries of what is possible in CNC machining. These manufacturers not only provide robust machinery but also extensive support and training, ensuring users get the most out of their investment.
In addition to these giants, there are niche players like Hurco and Okuma that specialize in specific applications or features within the realm of 5 axis lathes. Each manufacturer has its strengths, whether it's advanced control systems or unique tooling options, which can greatly influence your choice based on your specific requirements. When considering What is a 5-axis lathe? or How many axes can a lathe have?, it's essential to look at what each manufacturer offers to find the best fit for your needs.
Innovative Offerings from SYIL CNC Machine
One standout player in the field of 5 axis lathe manufacturing is SYIL CNC Machine, known for its commitment to innovation and affordability. They offer a range of machines designed specifically for small to medium-sized businesses looking to enhance their capabilities without breaking the bank—a crucial consideration when evaluating 5 axis lathe price points. Their models often include user-friendly interfaces and robust construction aimed at maximizing precision while minimizing downtime.
SYIL's focus on versatility allows operators to switch between different machining tasks efficiently, making them ideal for shops looking to diversify their services quickly. If you're pondering What is the difference between 3-2 axis and 5-axis? or What is the difference between 4 and 5-axis CNC?, SYIL's offerings exemplify how increased axes lead to more complex geometries being machined with greater ease than traditional setups could allow.
Evaluating Manufacturer Support and Service
When investing in a sophisticated piece of machinery like a 5 axis lathe, considering manufacturer support and service is just as vital as examining technical specifications or price tags—especially given how much you might be spending on a quality machine! A reliable manufacturer should provide comprehensive training programs, responsive customer service teams, and easy access to replacement parts for maintenance purposes.
Moreover, understanding how manufacturers handle warranty claims can save you from potential pitfalls down the road; after all, nobody wants unexpected costs associated with repairs! As you explore options regarding 5 axis CNC machine price versus features offered by various brands, weigh this support factor heavily—it can make all the difference between smooth operations or costly interruptions later on.
Conclusion
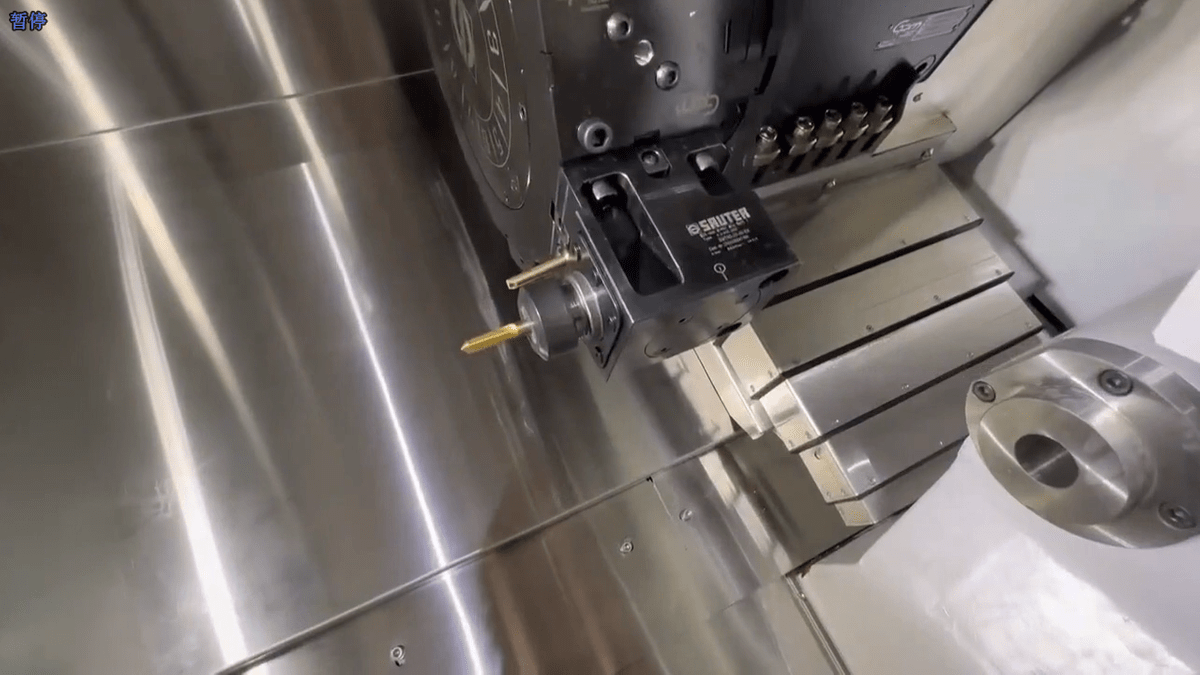
In the fast-paced world of manufacturing, selecting the right machinery can make or break your operation. A 5 axis lathe stands out for its ability to enhance precision and flexibility in machining processes. Understanding what is a 5-axis lathe and how it differs from traditional models is crucial for making an informed decision.
Choosing the Right 5 Axis Lathe for Your Needs
When considering a 5 axis lathe, it's essential to assess your specific machining requirements. Factors such as part complexity, material types, and production volume will dictate which model best fits your needs. Additionally, understanding how many axis can a lathe have will help you determine if a 3 2 axis or a full 5-axis setup is necessary for your projects.
Balancing Cost and Capability
The price of a 5 axis lathe can vary significantly based on features, capabilities, and manufacturer reputation. While high-end models offer advanced functionality, they also come with higher costs; thus, evaluating the 5 axis CNC machine price against your budget is vital. Striking the right balance between cost and capability ensures that you invest wisely without compromising on quality or performance.
Final Thoughts on 5 Axis Machining Advantage
Ultimately, embracing the advantages of a 5 axis lathe can revolutionize your machining processes by enabling intricate designs that were previously unattainable with simpler machines. The difference between 3-2 axis and 5-axis setups lies in their versatility—while both have their merits, opting for a more advanced system often results in superior outcomes. As you explore options among various leading manufacturers of 5 axis lathes, keep these factors in mind to ensure you choose the best fit for your operations.