Introduction
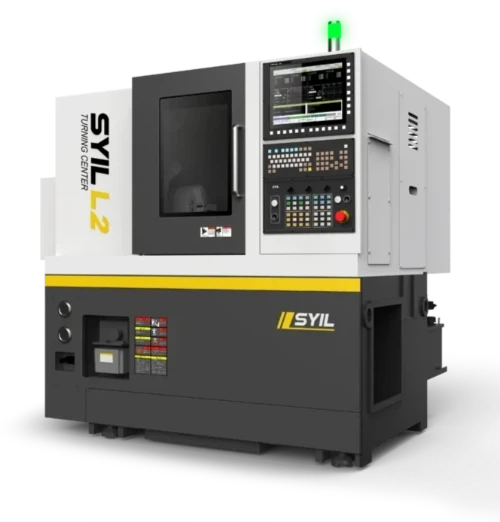
In the world of precision manufacturing, CNC lathe machines stand out as essential tools that revolutionize the way we create intricate parts and components. Understanding what CNC lathe meaning encompasses is vital for anyone involved in machining or engineering. These machines not only enhance productivity but also ensure high levels of accuracy, making them indispensable in various industries.
Understanding CNC Lathe Machines
CNC lathe machines are sophisticated devices that automate the process of turning materials into precise shapes and sizes. By utilizing computer numerical control (CNC), these machines can execute complex designs with minimal human intervention, ensuring consistent quality across production runs. The integration of technology in CNC lathing parts has significantly transformed traditional machining practices, allowing for greater efficiency and flexibility.
Importance of CNC Lathe Work
The importance of CNC lathe work cannot be overstated; it plays a crucial role in manufacturing everything from automotive components to aerospace parts. With their ability to produce highly detailed and accurate pieces, CNC lathe machines contribute significantly to reducing waste and improving material utilization. Moreover, the speed at which these machines operate allows manufacturers to meet tight deadlines while maintaining high standards of quality.
Key CNC Lathe Parts Explained
To fully grasp how a CNC lathe functions, it's essential to understand its key components, often referred to as CNC lathe parts. Each part plays a specific role in the overall operation, from spindles that hold the workpiece securely to tool holders that enable various cutting operations. Familiarity with these cnc turning machine parts not only aids in effective operation but also helps in troubleshooting and maintenance tasks down the line.
What is CNC Lathe Meaning
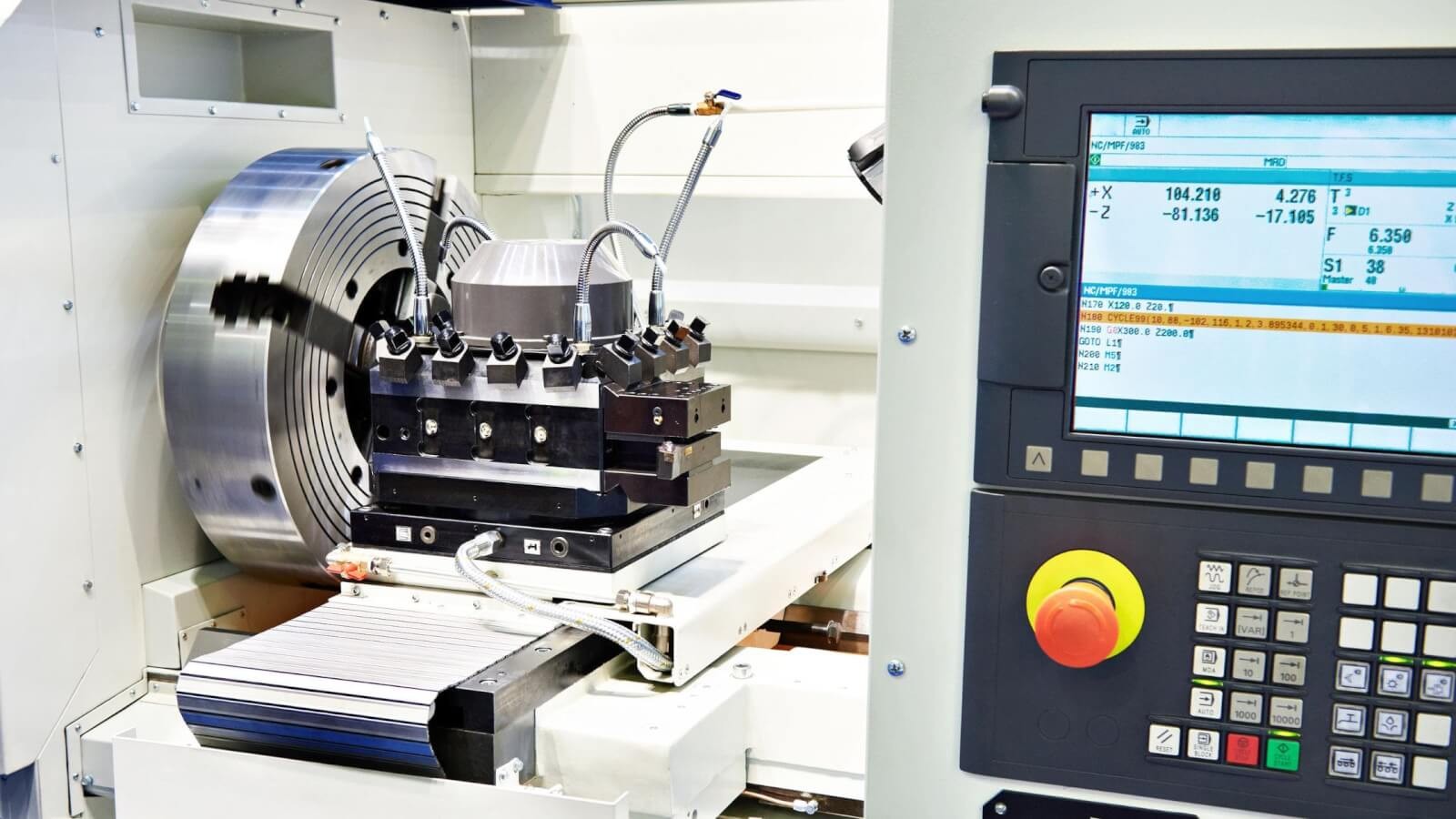
CNC lathe machines have revolutionized the manufacturing landscape, providing precision and efficiency that traditional lathes simply cannot match. At its core, the CNC lathe meaning encapsulates a computer-controlled machining process that shapes materials into cylindrical forms. This advancement in technology has not only streamlined production but also enhanced the quality of CNC lathe work across various industries.
Definition of CNC Lathe
A CNC lathe is a sophisticated machine tool that utilizes computer numerical control (CNC) to automate the turning process of materials like metal or plastic. Unlike manual lathes, which require constant operator input, CNC lathes execute complex designs with high precision through programmed instructions. This automation allows for consistent results and significantly reduces human error in machining operations.
Key Components and Their Functions
Understanding the key components of CNC lathe machines is essential for grasping their functionality. The main parts include spindles, which rotate the workpiece; tool holders, which secure cutting tools; and control systems that interpret programming commands. Each component plays a vital role in ensuring that the CNC lathe machining parts operate smoothly and effectively during production.
How CNC Lathe Machines Operate
The operation of a CNC lathe begins with a design fed into the machine's computer system via CAD/CAM software, translating intricate designs into precise movements. Once programmed, the machine automatically adjusts its speed and tool position to carry out tasks such as cutting or drilling with remarkable accuracy. This seamless operation not only improves productivity but also allows for complex shapes to be produced efficiently, showcasing the true potential of modern cnc turning machine parts.
Essential Features to Look For
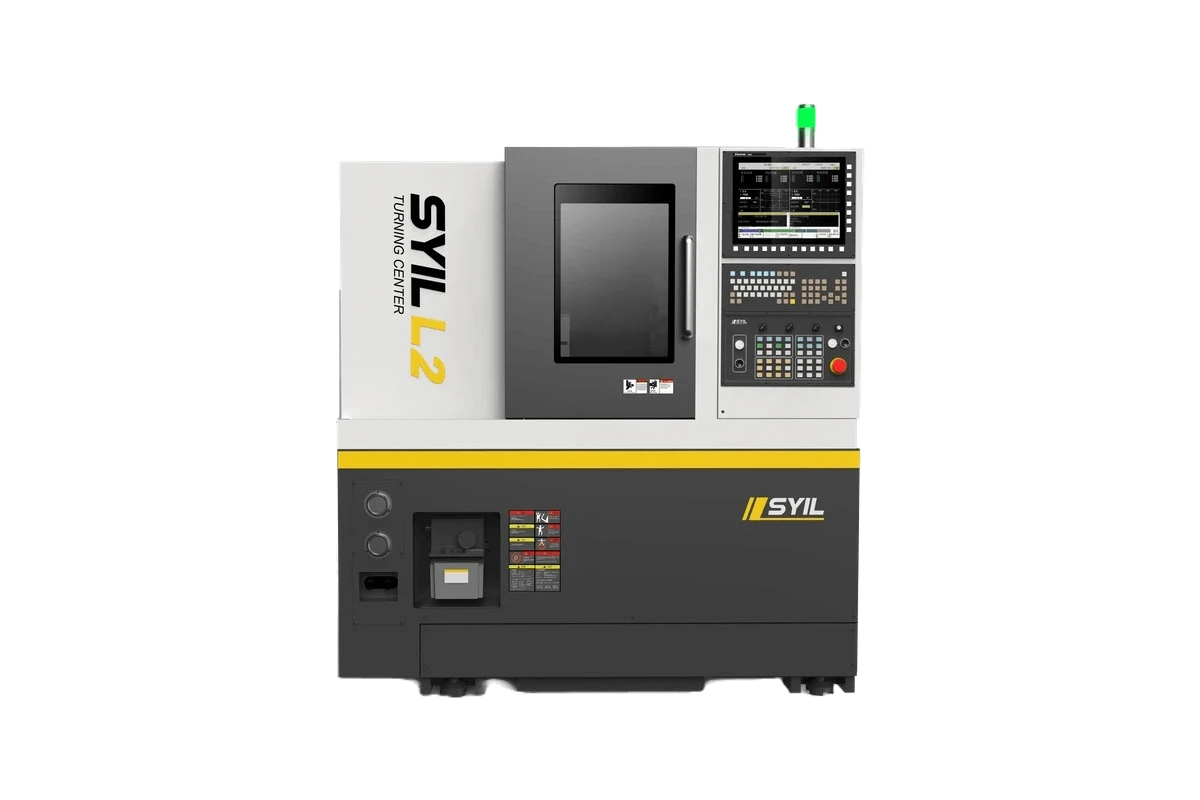
When diving into the world of CNC lathe machines, it's crucial to know what features can make or break your machining experience. The right combination of precision, speed, and user-friendliness can dramatically enhance your cnc lathe work, ensuring that you get the most out of your investment. Let’s explore these essential features that every savvy operator should consider.
Precision and Accuracy in Machining
Precision and accuracy are the cornerstones of effective CNC lathe machining parts. A machine that boasts high precision ensures that even the most intricate designs are replicated flawlessly, reducing waste and rework. When evaluating cnc lathe machines, look for models equipped with advanced feedback systems and high-resolution encoders that guarantee tight tolerances in every cut.
Moreover, accurate machining is not just about achieving perfect dimensions; it also contributes to better overall quality in finished products. This means fewer defects and a higher level of customer satisfaction—an outcome every business strives for! With precise CNC lathing parts at your disposal, you can confidently tackle complex projects without a hitch.
Speed and Efficiency in Production
In today's fast-paced manufacturing environment, speed is crucial for staying competitive. CNC turning machine parts designed for rapid operation can significantly reduce cycle times while maintaining quality standards. When shopping for cnc lathe machines, consider those with powerful spindles and optimized tool paths that enhance efficiency without sacrificing performance.
Additionally, efficient production processes lead to reduced operational costs over time. By investing in a machine capable of quick setups and minimal downtime between jobs, businesses can maximize output while keeping overheads low—a winning combination! Remember: faster production doesn’t have to mean compromising on quality when you choose the right cnc lathe machining parts.
User-Friendly Control Systems
A user-friendly control system is essential for maximizing productivity in any CNC operation. The best cnc machine lathes come equipped with intuitive interfaces that simplify programming and operation, allowing operators to focus on their craft rather than wrestling with complicated software. Look for systems featuring touchscreen controls or graphical displays that make navigation a breeze!
Moreover, robust control systems often include simulation capabilities which allow users to visualize their operations before executing them on actual materials—this minimizes costly mistakes during production runs! Investing in easy-to-use technology not only boosts efficiency but also empowers operators at all skill levels to harness the full potential of their cnc lathe work.
Types of CNC Lathe Machines
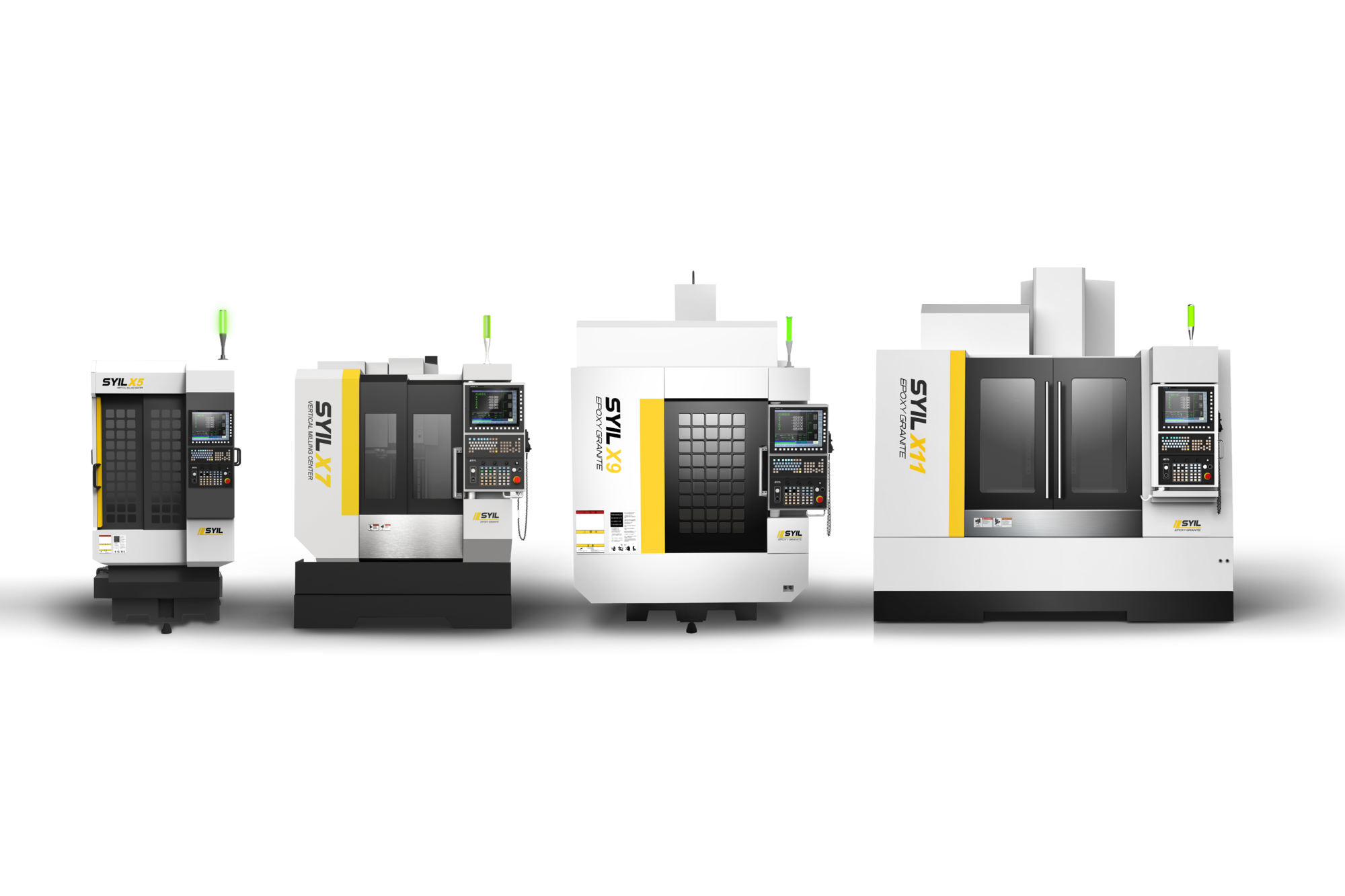
When it comes to CNC lathe machines, the variety available can be overwhelming. Each type of machine serves specific needs in the world of precision machining and manufacturing. Understanding these different types can help you make informed decisions for your CNC lathe work.
Vertical Vs. Horizontal Lathes
Vertical and horizontal lathes are two primary configurations found in CNC lathe machines. Vertical lathes are designed to handle larger workpieces, offering a stable platform for heavy-duty machining tasks; they excel in operations requiring high torque and rigidity. On the other hand, horizontal lathes are more versatile, making them ideal for a wide range of applications, particularly when dealing with smaller parts that require intricate details.
The choice between vertical and horizontal lathes often boils down to the specific requirements of your project. If you're focused on large components or heavy materials, a vertical setup might be your best bet; however, if your work involves precision cutting on smaller pieces, then horizontal models could be the way to go. Ultimately, understanding how each type operates will enhance your efficiency and effectiveness in using CNC lathe parts.
Swiss-Type CNC Lathes
Swiss-type CNC lathes are revolutionizing the way small precision parts are manufactured; they offer unparalleled accuracy and speed for producing complex components. These machines utilize a sliding headstock mechanism that allows material to move through multiple tools simultaneously—ideal for high-volume production runs where consistency is key. The design enables manufacturers to produce intricate shapes with minimal waste while ensuring tight tolerances.
One of the standout features of Swiss-type machines is their ability to perform multiple operations without needing to change setups frequently; this significantly reduces downtime during production runs. As such, they have become indispensable in industries like medical device manufacturing or aerospace engineering where precision is non-negotiable. By integrating advanced technology into their design, Swiss-type CNC lathes exemplify how modern machinery can elevate traditional cnc lathe work.
Multi-Axis CNC Turning Machine Parts
Multi-axis CNC turning machines take versatility to another level by allowing simultaneous movement along several axes—typically three or more—to create complex geometries that would be impossible with traditional lathes alone. These machines incorporate advanced cnc lathe machining parts that enable them to perform tasks like drilling or milling while turning a part on its axis—truly an all-in-one solution! This capability not only saves time but also enhances accuracy by minimizing manual handling between operations.
The real magic happens when you consider how multi-axis systems can reduce setup times and increase productivity significantly; this means shorter lead times and higher output without compromising quality—a win-win situation! As industries continue pushing towards automation and efficiency, investing in multi-axis cnc turning machine parts becomes increasingly essential for staying competitive in today’s market landscape. With these advancements at our fingertips, it's clear that multi-axis capabilities represent the future of cnc lathe machines.
CNC Lathe Machining Parts Overview
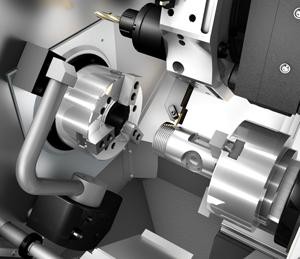
CNC lathe machining parts are the heart and soul of any CNC lathe machine, ensuring precision and efficiency in every turn. Understanding these components is crucial for anyone involved in CNC lathe work, whether you're a seasoned machinist or just starting out. From spindles to tool holders, each part plays a vital role in the overall performance of the machine.
Understanding CNC Lathing Parts
CNC lathing parts encompass a variety of components that work together to execute complex machining tasks with high accuracy. These parts include not only the obvious like the bed and carriage but also intricate elements such as bearings and motors that drive the entire system. Familiarity with these CNC lathe parts is essential for troubleshooting issues and optimizing workflows in any machining operation.
In essence, understanding CNC lathing parts means grasping how each piece contributes to the functionality of CNC lathe machines. For example, knowing how different materials affect wear on specific components can lead to better maintenance practices and longer machine life. This knowledge not only enhances your skills but also boosts productivity by minimizing downtime during operations.
The Role of Spindles and Tool Holders
Spindles are often regarded as one of the most critical components in CNC turning machine parts; they provide the rotational force necessary for cutting tools to shape materials accurately. The spindle's quality directly impacts both speed and precision, making it essential for effective CNC lathe work. Coupled with tool holders, which securely grip cutting tools during operation, they form a dynamic duo that drives successful machining processes.
Tool holders come in various styles suited for different applications—be it collet chucks or quick-change systems—each designed to enhance versatility while maintaining stability during operations. Their ability to quickly swap tools without losing accuracy is invaluable when dealing with multiple setups or intricate designs on a single project. Thus, understanding both spindles and tool holders is key for anyone looking to master their craft using CNC lathe machines.
Importance of Tool Changers in Operations
Tool changers are an often-overlooked yet indispensable part of modern CNC lathes that significantly enhance operational efficiency. By automating the process of switching between different tools, they minimize manual intervention and reduce cycle times during production runs—a game-changer for high-volume manufacturing settings! This automation allows machinists to focus on more complex tasks rather than tedious tool management.
The integration of tool changers into CNC lathe machines also supports increased flexibility in production capabilities; you can easily switch from one type of operation to another without extensive setup times or interruptions. This adaptability is especially beneficial when working on projects requiring diverse machining operations or rapid prototyping needs within limited timelines. In short, investing time into understanding how tool changers function can yield substantial productivity gains across various applications involving cnc lathe machining parts.
Best Brands in CNC Lathe Technology
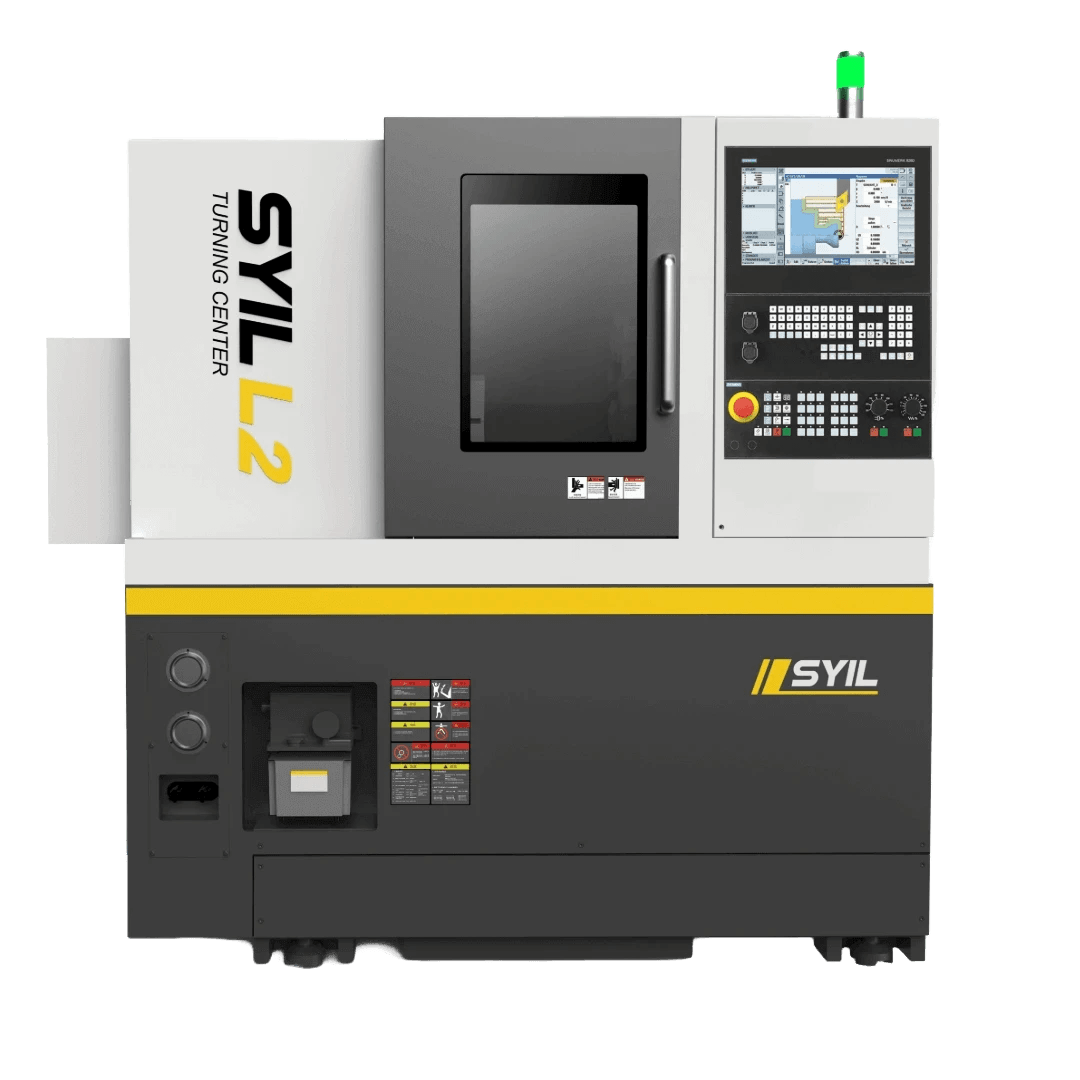
When it comes to CNC lathe machines, not all brands are created equal. The right choice can make a significant difference in your CNC lathe work, impacting everything from precision to efficiency. In this section, we'll spotlight some of the standout brands in the industry and what makes them unique.
Spotlight on SYIL CNC Machines
SYIL CNC machines have carved out a niche for themselves in the competitive world of CNC lathe technology. Known for their high-quality construction and user-friendly features, SYIL lathes are ideal for both small-scale operations and larger manufacturing setups. Their commitment to innovation ensures that their CNC lathe parts are designed with advanced functionality and reliability in mind, making them a favorite among machinists.
What sets SYIL apart is their focus on customization; customers can often tailor their cnc turning machine parts to meet specific needs. This flexibility allows users to optimize their machining processes while maintaining high standards of accuracy with every turn of the spindle. With an impressive range of models available, SYIL continues to be a leading choice for those seeking dependable cnc lathing parts.
Comparing Renowned CNC Lathes
When comparing renowned CNC lathes, several factors come into play that can affect your decision-making process. Brands like Haas Automation and Okuma offer robust options that cater to varying levels of complexity within cnc lathe machining parts. While Haas is celebrated for its innovative control systems, Okuma shines with its advanced thermal stability features that enhance performance under demanding conditions.
Another key consideration is the price-to-performance ratio; some brands may offer lower initial costs but compromise on quality or longevity—something you definitely want to avoid when investing in cnc machine lathe technology! Additionally, customer support and service availability should factor heavily into your comparison since downtime can be costly during production runs. Ultimately, understanding what each brand brings to the table can help you choose the best fit for your specific cnc lathe work requirements.
Innovations from Haas Automation
Haas Automation has consistently pushed boundaries in the world of cnc lathe machines through cutting-edge innovations tailored for modern manufacturing needs. Their latest models boast enhanced speed capabilities and improved user interfaces designed specifically for ease-of-use—perfect for operators at any skill level! Furthermore, Haas is known for integrating smart technologies that allow real-time monitoring and diagnostics of cnc turning machine parts.
One notable innovation is their intuitive control software which simplifies programming tasks while ensuring precision machining across various materials—a critical factor when dealing with intricate designs or prototypes using different cnc lathing parts. Additionally, Haas continually invests in research and development aimed at increasing energy efficiency within their machines; this not only reduces operating costs but also supports sustainable manufacturing practices.
In conclusion, whether you're considering SYIL's customizable offerings or exploring innovations from Haas Automation, there's no shortage of exceptional brands leading the charge in CNC lathe technology today!
Conclusion
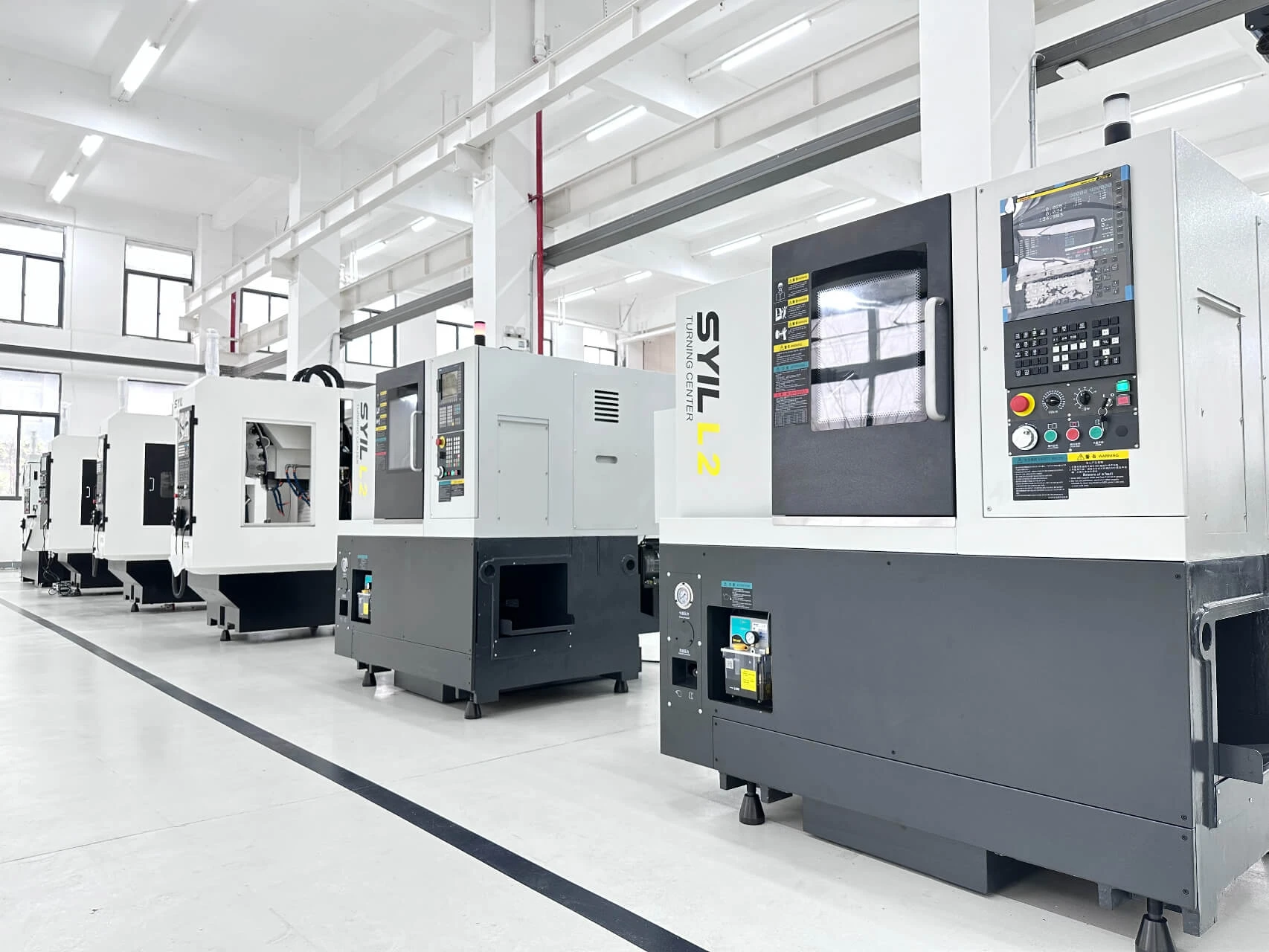
In the world of manufacturing, understanding CNC lathe machines is crucial for making informed decisions about production capabilities. The significance of CNC lathe work cannot be overstated, as it shapes the efficiency and precision of many industries. By grasping the essentials of CNC lathe meaning and components, you can better navigate your options in this ever-evolving field.
Choosing the Right CNC Lathe Machine
Selecting the right CNC lathe machine involves a careful consideration of your specific needs and production goals. Factors like size, speed, and capability play a pivotal role in ensuring that you choose a machine suited for your projects. Additionally, understanding the various cnc turning machine parts can help you identify which features are essential for your operations.
When evaluating cnc lathe parts, it’s important to consider not just performance but also reliability and support from manufacturers. The right choice can significantly enhance your machining processes while minimizing downtime and maintenance costs. Ultimately, investing time in research will lead to a well-informed decision that aligns with your business objectives.
Future Trends in CNC Lathe Technology
The future of cnc lathe technology is bright as innovations continue to emerge at an impressive pace. Advancements such as automation integration and smart technology are poised to revolutionize how we think about cnc lathing parts and their applications in various industries. As manufacturers adopt these technologies, they’ll experience increased flexibility and adaptability in their production lines.
Moreover, sustainability is becoming a focal point within the industry; eco-friendly practices are being integrated into machine design and operation processes. This shift not only benefits the environment but also appeals to consumers who prioritize sustainable products. Keeping an eye on these trends will be vital for businesses aiming to stay competitive in an increasingly conscious market.
Enhancing Productivity with CNC Solutions
To enhance productivity using cnc lathe machining parts effectively requires more than just acquiring advanced technology; it involves optimizing workflows too. Streamlining operations through proper training on control systems ensures that operators maximize efficiency while minimizing errors during production runs. Furthermore, regular maintenance of cnc lathing parts helps maintain high levels of performance over time.
Incorporating software solutions that complement machinery can further boost productivity by providing real-time data analysis for informed decision-making processes. This integration allows businesses to swiftly adapt to changing demands while maintaining quality standards across all outputs produced by their cnc machines. Ultimately, embracing these strategies will lead to enhanced operational efficiency and greater overall success.