Introduction
The automotive industry has undergone a remarkable transformation with the rise of CNC technology, revolutionizing how vehicles are designed and manufactured. CNC machines have become indispensable tools in creating high-quality automotive parts, allowing for precision engineering that was once thought impossible. As manufacturers strive for efficiency and accuracy, the benefits of automotive CNC machining are becoming increasingly clear, paving the way for innovations in vehicle production.
The Rise of CNC in Automotive
CNC machines have surged to prominence within the automotive sector, providing unparalleled capabilities for producing complex components with exacting standards. This shift towards automation has allowed manufacturers to streamline their operations and reduce human error significantly. With the ability to produce intricate designs and customizations at scale, automotive CNC machines are reshaping traditional manufacturing processes.
Precision Engineering Redefined
Precision engineering has reached new heights thanks to advancements in CNC technology, enabling the creation of highly detailed and consistent cnc auto parts. The integration of computer-controlled machinery allows for tighter tolerances and improved repeatability in manufacturing processes. This redefined precision not only enhances product quality but also contributes to better overall performance in vehicles.
Key Benefits of CNC Machining
Automotive CNC machining offers numerous advantages that elevate it above conventional manufacturing methods. One major benefit is its capacity for rapid prototyping, which accelerates development timelines and brings products to market faster than ever before. Additionally, the versatility of various cnc machines types ensures that manufacturers can tackle a wide range of projects—from small-scale custom jobs to large-scale production runs—efficiently and effectively.
The Role of CNC Machines in Car Production
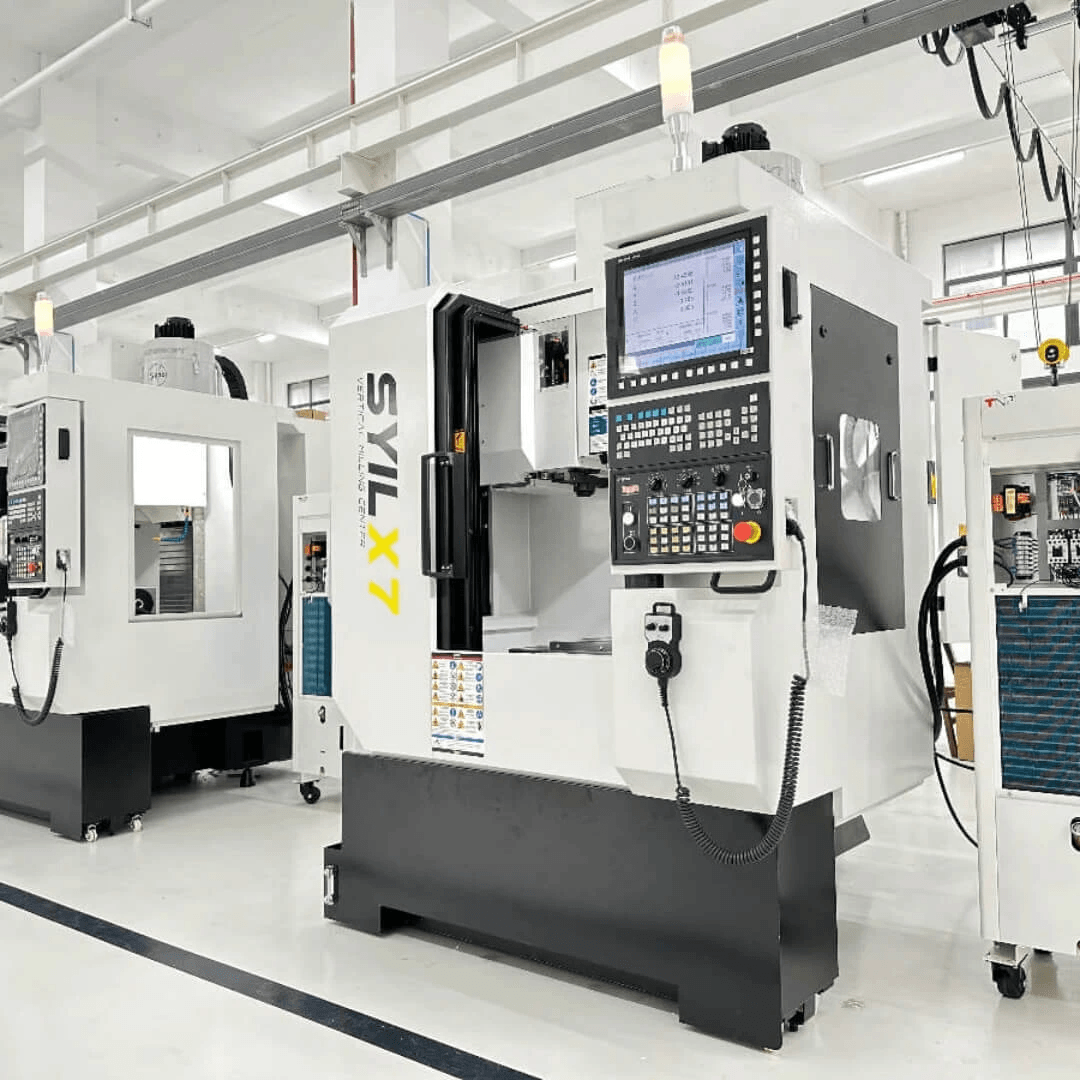
In the realm of automotive manufacturing, CNC machines have become indispensable. They streamline production processes and enhance efficiency, allowing manufacturers to produce high-quality components with remarkable speed. By integrating automotive CNC machining into their workflows, companies can respond to market demands swiftly while maintaining precision.
Streamlined Manufacturing Processes
CNC machines revolutionize the way automotive parts are produced by automating repetitive tasks that were once labor-intensive. With the ability to operate continuously and with minimal downtime, these machines significantly reduce lead times for cnc auto parts production. This streamlined approach not only saves time but also lowers operational costs, making it a win-win for manufacturers.
Moreover, the flexibility of automotive CNC machines allows for quick adjustments in design and production runs without extensive retooling. This adaptability is crucial in an industry where trends can shift overnight and customer preferences evolve rapidly. As a result, manufacturers can maintain a competitive edge while ensuring they meet the diverse needs of their clientele.
Enhancing Production Accuracy
One of the standout features of automotive CNC machining is its unparalleled accuracy in producing components that meet strict tolerances. This precision is vital when creating intricate designs for cnc car parts that must fit together seamlessly within a vehicle’s complex assembly system. With advanced software and programming capabilities, these machines minimize human error and ensure consistent quality across all products.
Additionally, enhanced accuracy leads to improved performance and safety in vehicles manufactured using cnc machining car parts. When every component is crafted with meticulous attention to detail, it contributes positively to overall vehicle reliability and longevity. Thus, investing in automotive CNC machines ultimately translates into better products on the road.
Common CNC Machines Types in Use
Several types of CNC machines are commonly employed in automotive manufacturing, each tailored for specific tasks within the production process. For instance, milling machines are widely used for shaping metal components into precise forms needed for various car parts. Meanwhile, lathes are essential for producing cylindrical shapes that are integral to many engine components.
Laser cutting systems also play a significant role by providing clean edges on intricate designs without compromising material integrity—ideal for lightweight materials often used today. Other common cnc machine types include routers and plasma cutters that offer versatility across different materials like plastics and composites found in modern vehicles. By leveraging these diverse technologies, manufacturers can optimize their operations while enhancing product quality through effective use of automotive CNC machining techniques.
CNC Machining for Automotive Parts
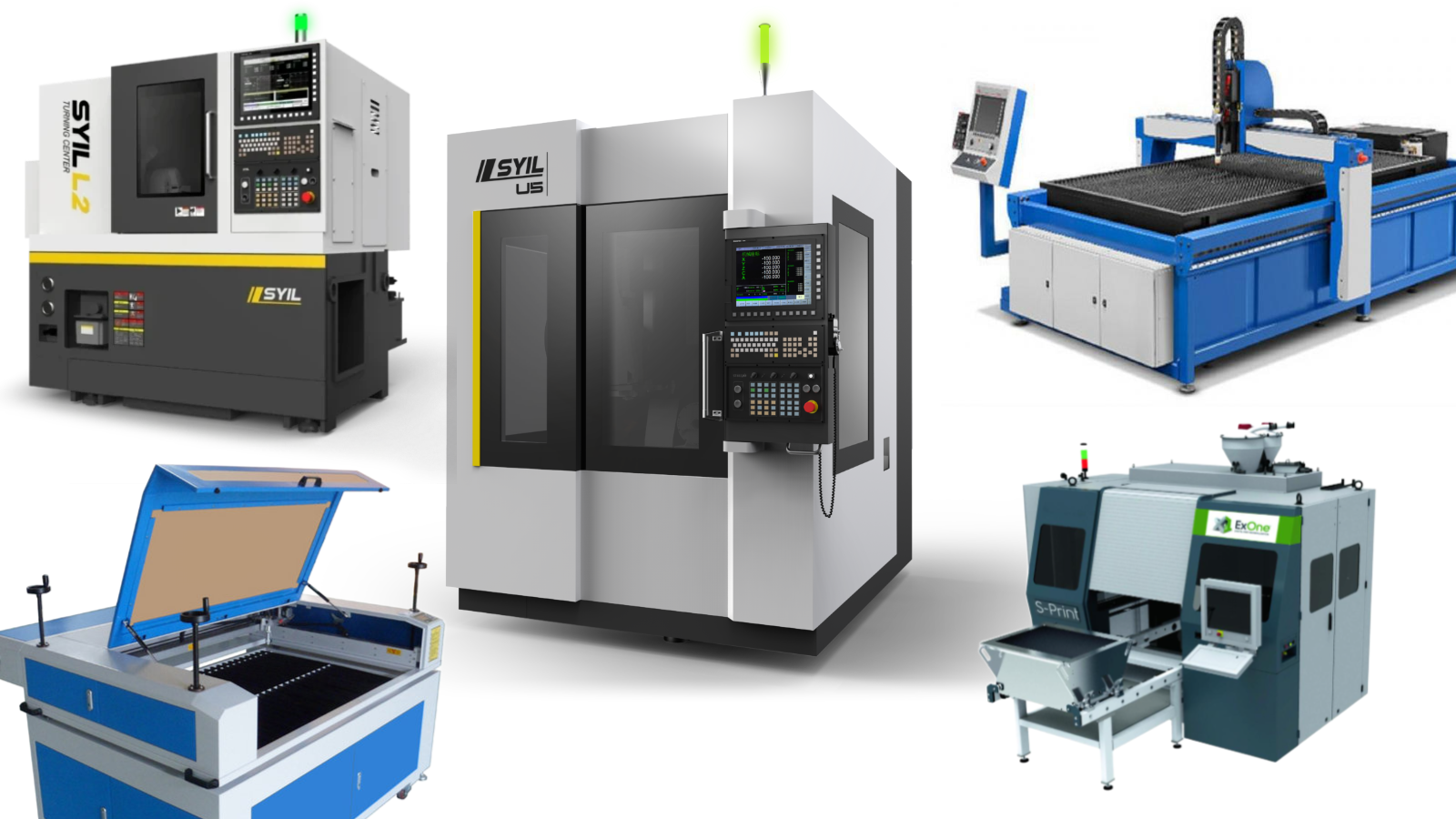
CNC machining has revolutionized the way automotive parts are produced, allowing for the creation of intricate designs and precise specifications. The ability to use CNC machines for automotive parts has not only streamlined production but also enhanced the quality and performance of these components. As manufacturers increasingly rely on advanced automotive CNC machines, the landscape of car part production continues to evolve.
Creating Complex CNC Auto Parts
Creating complex CNC auto parts is where the magic truly happens in automotive manufacturing. With the precision offered by an automotive CNC machine, engineers can design components that were once deemed impossible or too costly to produce. Whether it's a custom bracket or a highly detailed engine component, these CNC machines types enable manufacturers to push boundaries while maintaining high standards of accuracy.
The ability to create complex shapes and geometries with ease makes CNC machining car parts an invaluable asset in today’s competitive market. This technology allows for rapid prototyping and production runs, reducing lead times significantly while ensuring that every part meets stringent quality requirements. In short, when it comes to creating intricate designs in automotive components, nothing beats the capabilities of modern CNC auto parts manufacturing.
Understanding Automotive CNC Machining Techniques
To fully appreciate how automotive CNC machining works, it’s essential to understand the various techniques employed in this process. Techniques such as milling, turning, and grinding are commonly used in producing high-quality car parts with incredible precision. Each method has its strengths; for instance, milling is perfect for creating flat surfaces and complex contours, while turning is ideal for cylindrical shapes.
Automotive CNC machines utilize computer-aided design (CAD) software to translate designs into machine language that guides their operations. This integration ensures that every cut and drill is executed with pinpoint accuracy—crucial when dealing with components that must fit together seamlessly within a vehicle's assembly line. By mastering these techniques, manufacturers can optimize their processes and achieve better results with each run of cnc car parts.
The Importance of Material Selection
When it comes to cnc machining car parts, material selection plays a pivotal role in determining performance and durability. Different materials offer varying levels of strength, weight savings, corrosion resistance, and cost-effectiveness—factors that are critical when designing auto components meant to withstand rigorous conditions on the road. Common materials include aluminum alloys for lightweight applications and steel for strength-critical components.
Choosing the right material not only impacts production efficiency but also affects overall vehicle performance; lightweight materials can enhance fuel efficiency without sacrificing strength or safety features in a vehicle's design. Additionally, advancements in composite materials are opening new avenues for innovation within automotive cnc machining processes—making it easier than ever to create strong yet lightweight components tailored specifically for modern vehicles' needs. Ultimately, thoughtful material selection ensures that each piece produced by an automotive cnc machine meets both functional requirements and customer expectations.
Leading Companies Utilizing CNC Technology
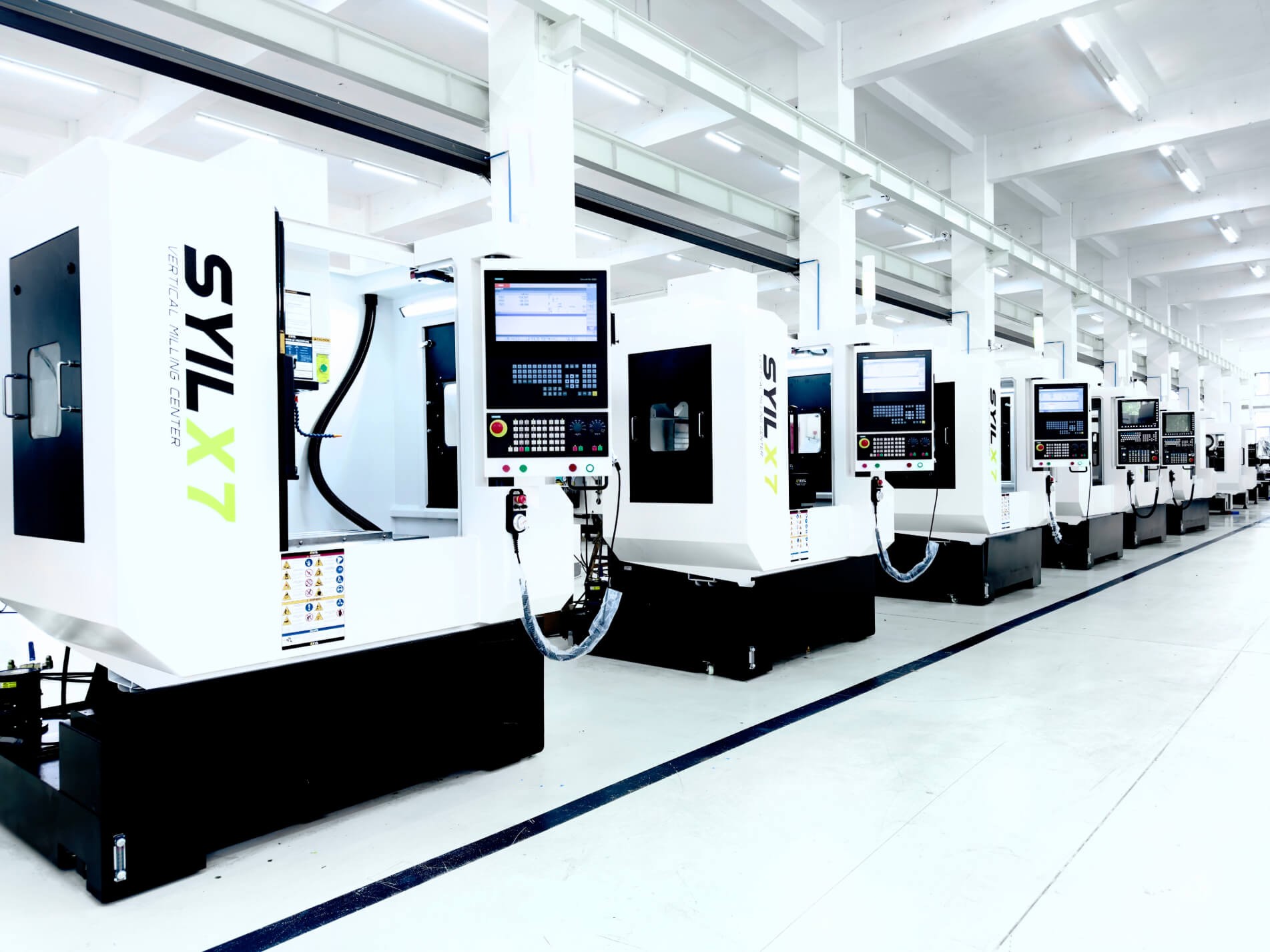
The automotive industry has seen a remarkable transformation with the integration of CNC technology, allowing manufacturers to enhance their production capabilities significantly. Leading companies like Ford, General Motors, and Tesla have embraced automotive CNC machining to refine their processes and improve the quality of their vehicles. This section explores how these industry giants are leveraging CNC machines to produce high-quality car parts efficiently.
Ford and Their CNC Innovations
Ford has been at the forefront of utilizing CNC machines for automotive parts production, pushing the boundaries of precision engineering. Their advanced use of automotive CNC machines enables them to create intricate components that meet stringent quality standards while reducing waste and lead times. By innovating with various types of CNC machines, Ford has managed to streamline its manufacturing processes, resulting in enhanced performance and reliability in their vehicles.
The introduction of robotics alongside CNC machine technology has allowed Ford to automate repetitive tasks, thereby increasing overall productivity in their assembly lines. This integration not only enhances the accuracy of producing complex CNC auto parts but also minimizes human error during manufacturing. As Ford continues to invest in cutting-edge technologies, they remain committed to setting new benchmarks for quality in the automotive sector through effective use of automotive CNC machining.
General Motors’ Adoption of CNC Machines
General Motors (GM) is another key player that has effectively integrated automotive CNC machining into its production strategy. The company employs various types of CNC machines that facilitate the creation of precise components essential for modern vehicles. GM’s commitment to innovation ensures that they can produce high-quality cnc car parts while maintaining efficiency across their manufacturing plants.
By adopting advanced techniques in automotive CNC machining, GM has improved its ability to respond quickly to market demands without compromising on quality or performance. Their focus on precision engineering allows them to develop complex designs that cater specifically to consumer needs while optimizing production costs. With a keen eye on sustainability, GM is also exploring eco-friendly materials and practices within its cnc machining car parts operations.
Tesla’s Integration of CNC for Design
Tesla stands out as a trailblazer in the integration of cutting-edge technology within the automotive sector, particularly through its use of cnc machines types tailored for innovative designs. The company leverages advanced automotive cnc machines not just for mass production but also for prototyping unique components that set them apart from traditional automakers. This approach allows Tesla engineers to push creative boundaries while ensuring high standards are met throughout the design process.
Tesla's dedication to utilizing state-of-the-art machinery enhances their ability to produce custom cnc auto parts quickly and efficiently without sacrificing quality or performance metrics. By integrating sophisticated software with their cnc machine capabilities, they can simulate real-world conditions during design phases—reducing time-to-market significantly compared with conventional methods. As Tesla continues redefining vehicle design paradigms through effective use of automotive cnc machining, it reinforces its position as a leader in sustainable transportation solutions.
The Future of Automotive CNC Machining
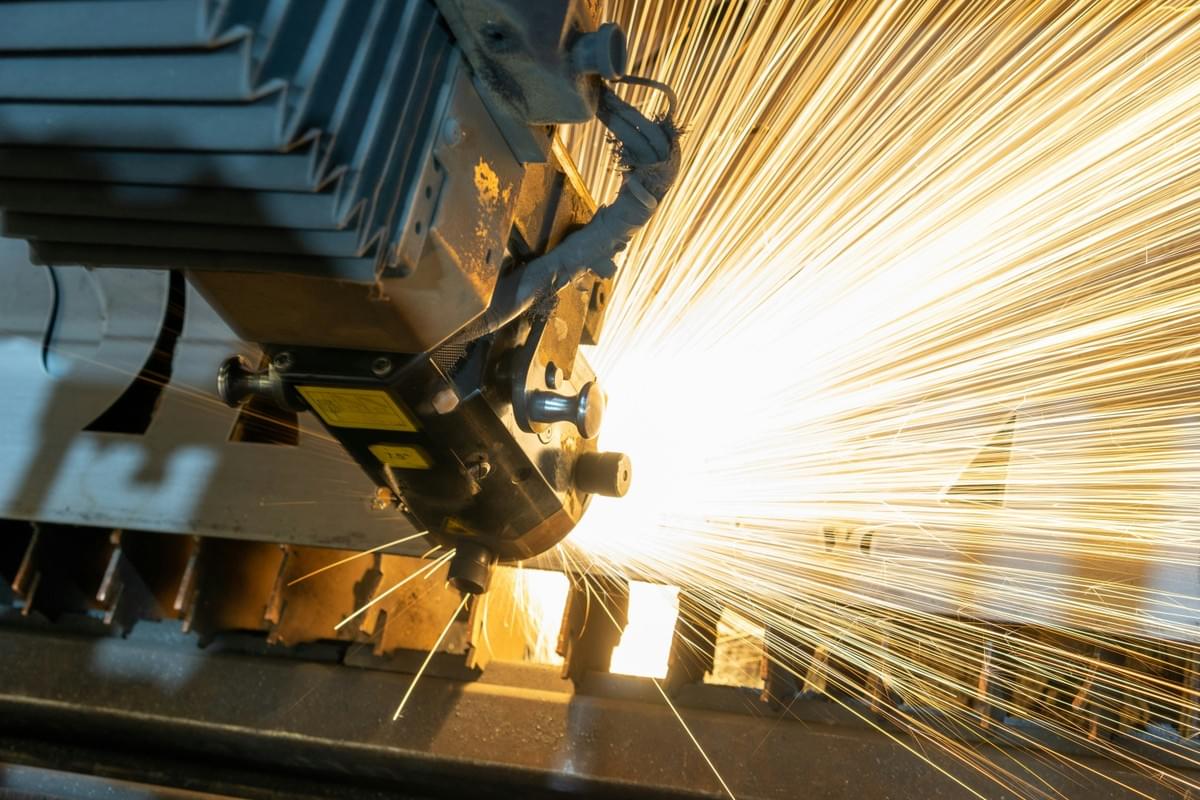
As the automotive industry continues to evolve, the future of CNC machining is looking brighter than ever. With increasing demands for precision and efficiency, automotive CNC machines are becoming essential tools in manufacturing. These machines are not only streamlining production but also setting new standards for quality in the creation of CNC auto parts.
Trends in Automotive CNC Machines
The landscape of automotive CNC machines is witnessing exciting trends that promise to revolutionize manufacturing processes. One major trend is the rise of multi-axis CNC machines, which allow for more complex geometries and intricate designs in automotive CNC machining. This capability enables manufacturers to produce innovative and lightweight components that enhance vehicle performance while reducing material waste.
Another trend gaining traction is automation and integration with Industry 4.0 technologies, such as IoT and AI. By connecting machines to data networks, manufacturers can optimize operations in real-time, improving efficiency and reducing downtime during production cycles of automotive CNC machine components. As these trends continue to develop, we can expect a more dynamic approach to creating high-quality CNC car parts.
Advancements in Technology and Materials
Technological advancements are propelling the capabilities of automotive CNC machines into new realms. Innovations such as advanced software for simulation and programming have made it easier than ever for engineers to design complex parts with precision before any physical work begins on the shop floor. Additionally, high-speed machining technologies are enabling faster production times without compromising quality when fabricating intricate CNC machining car parts.
Moreover, advancements in materials science are allowing manufacturers to explore new composites and alloys that improve durability while maintaining lightweight characteristics essential for modern vehicles. The combination of cutting-edge technology with innovative materials will undoubtedly lead to a new generation of efficient, high-performance automotive components crafted through skilled automotive CNC machining techniques.
Sustainable Practices in CNC Manufacturing
Sustainability has become a cornerstone principle within the future framework of automotive manufacturing processes, including those involving CNC machining car parts. Companies are increasingly adopting eco-friendly practices by optimizing their use of materials through precise cutting techniques that reduce waste significantly during production runs with their advanced automotive CNC machines. This shift not only benefits the environment but also enhances cost-effectiveness by maximizing resource utilization.
Furthermore, many manufacturers are investing in energy-efficient machinery designed specifically for low energy consumption during operations—an important consideration as industries strive toward greener practices amid growing environmental concerns globally. By incorporating sustainable approaches into their workflows, companies can ensure that their contributions toward producing quality cnc machine automotive parts align with broader ecological goals.
Case Studies in CNC Machining Car Parts
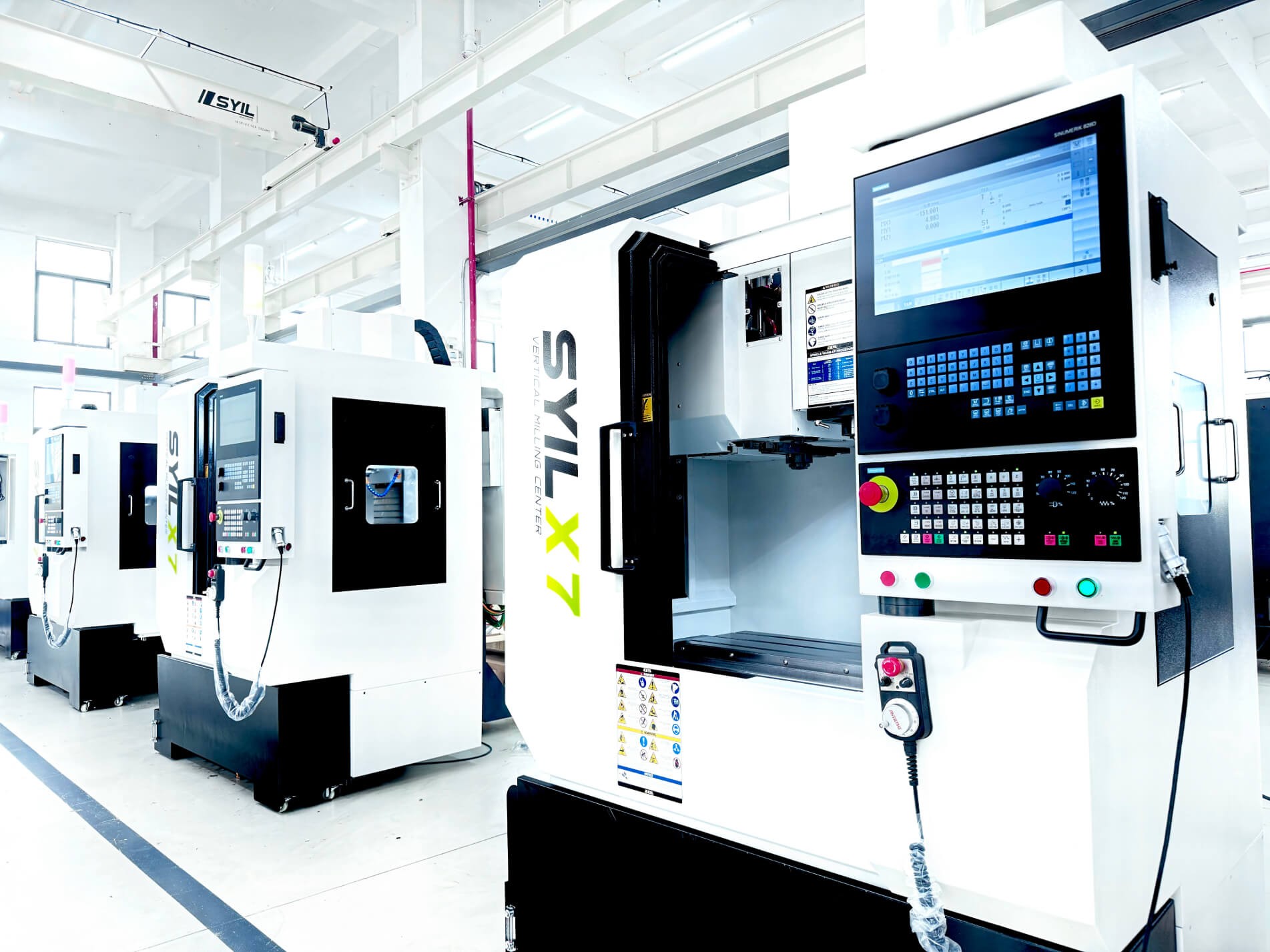
CNC machining has revolutionized the way automotive parts are produced, leading to remarkable success stories and innovations in the industry. From enhancing production efficiency to creating intricate designs, CNC machines have become indispensable tools for manufacturers. In this section, we will explore specific case studies that highlight the effectiveness of CNC technology in automotive applications.
SYIL CNC Machine Success Stories
SYIL has made significant strides in the realm of automotive CNC machining, showcasing how their advanced machines can produce high-quality cnc auto parts with precision and speed. By integrating SYIL's CNC machines into their production lines, manufacturers have reported substantial reductions in lead times and operational costs while maintaining superior accuracy. These success stories illustrate the growing reliance on automotive CNC machines to meet the demands of an evolving market.
In one notable case, a renowned car manufacturer adopted SYIL’s latest models to create complex engine components that were previously challenging to produce with traditional methods. The results were astounding—higher quality parts produced at a fraction of the time compared to older techniques. This transformation not only improved product quality but also allowed for greater design flexibility, showcasing how effective these cnc machines types can be in modern manufacturing.
Custom CNC Car Parts for Performance Vehicles
The demand for custom cnc car parts has surged among performance vehicle enthusiasts looking for a competitive edge on both street and track. Automotive CNC machining enables designers and engineers to create bespoke components tailored specifically for enhanced performance metrics such as weight reduction and aerodynamics. With precise control over material properties and dimensions, these custom parts provide significant advantages over standard offerings.
One example includes specialized intake manifolds designed using advanced automotive cnc machine technology, which optimize airflow efficiency and boost engine power output. By leveraging state-of-the-art machining processes, manufacturers have successfully crafted unique designs that cater specifically to high-performance applications while ensuring durability under extreme conditions. This trend highlights a broader movement toward personalization within the automotive sector facilitated by innovative cnc machining car parts solutions.
Efficiency Gains from CNC in Racing Applications
Racing teams are always hunting for ways to shave off precious seconds from their lap times, making efficiency gains from cnc machining car parts vital in this high-stakes environment. The use of automotive CNC machines allows teams to fabricate lightweight components that enhance speed without compromising structural integrity—a delicate balance crucial for competitive racing performance. As a result, many racing organizations have turned towards cutting-edge 5-axis cnc machines types that offer unparalleled precision during part fabrication.
For instance, one racing team utilized advanced automotive cnc machining techniques to develop custom suspension systems tailored precisely to their vehicle dynamics requirements. The ability to rapidly prototype and produce these specialized components led not only to improved handling but also allowed for last-minute adjustments before critical races—an advantage that could mean victory or defeat on race day! This showcases how integral efficient production processes powered by modern cnc technologies are becoming within competitive motorsports.
Conclusion
The automotive industry is undergoing a significant transformation, largely driven by the integration of CNC technology. CNC machines are revolutionizing how automotive parts are manufactured, allowing for unprecedented levels of precision and efficiency. As these innovations continue to evolve, the landscape of automotive manufacturing will be forever changed.
Transforming the Automotive Manufacturing Landscape
CNC machining has fundamentally altered the way manufacturers approach production, shifting from traditional methods to advanced techniques that emphasize speed and accuracy. With various types of CNC machines now available, automakers can produce complex components with ease, leading to faster turnaround times and reduced costs. This transformation not only streamlines processes but also enhances overall productivity in creating high-quality cnc auto parts.
The Impact of Precision on Vehicle Quality
Precision is paramount in automotive engineering; even the smallest errors can lead to significant performance issues down the line. Thanks to automotive CNC machining, manufacturers can achieve tighter tolerances and more consistent quality across their product lines. This level of precision directly correlates with improved vehicle reliability and safety, ensuring that every component—whether it's a simple bracket or intricate cnc car parts—meets stringent industry standards.
Expanding Applications of CNC Technology
As technology advances, so do the applications for automotive CNC machines beyond traditional manufacturing roles. We are seeing an increase in custom applications tailored for performance vehicles and specialized projects that require unique designs and materials. The future holds exciting possibilities as industries explore new ways to leverage cnc machining car parts for innovation in electric vehicles, autonomous driving technologies, and sustainable practices.