Introduction
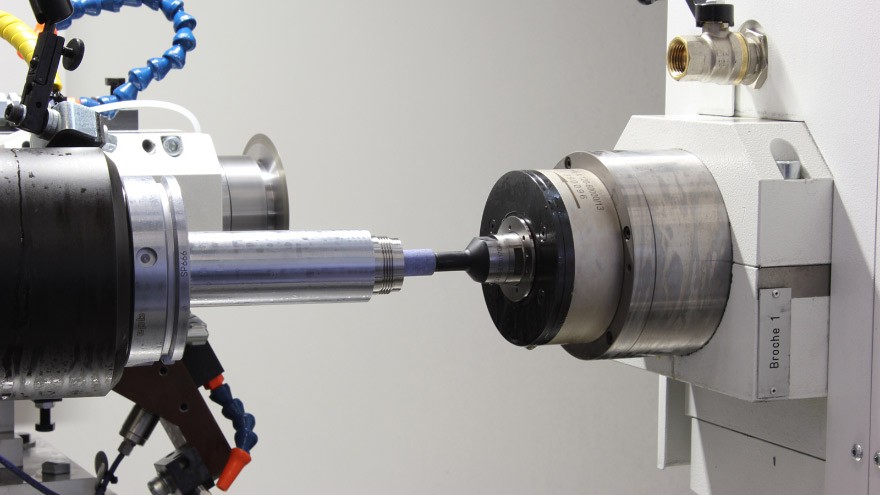
In the world of manufacturing, understanding machining processes is essential for producing high-quality parts and components. Among these processes, turning, milling, and drilling stand out as foundational techniques that have shaped the industry for decades. This introduction will explore the significance of these methods and provide an overview of SYIL CNC machines, which are at the forefront of modern machining technology.
Understanding Machining Processes
Machining processes encompass a variety of methods used to shape materials into desired forms through cutting or removal techniques. These processes can vary widely in complexity and application, from simple manual operations to intricate automated systems. Understanding these various types of machining processes is crucial for manufacturers seeking to optimize production and efficiency.
The Importance of Turning, Milling, and Drilling
Turning, milling, and drilling are three primary types of machining processes that serve distinct purposes yet often complement each other in production environments. Turning is particularly valuable in creating cylindrical parts; milling excels at producing flat surfaces; while drilling focuses on creating holes with precision. Each process has its own unique advantages and applications that make them indispensable in industries ranging from automotive to aerospace.
Overview of SYIL CNC Machines
SYIL CNC machines represent a leap forward in machining technology by providing precision engineering solutions tailored for both hobbyists and professionals alike. These machines offer advanced capabilities for turning, milling, and drilling with enhanced accuracy and speed compared to traditional methods. With features designed for versatility and ease-of-use, SYIL CNC machines are transforming how manufacturers approach their production needs.
What is Turning in Manufacturing Process
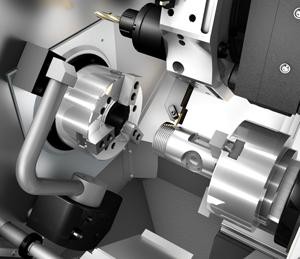
Turning is a fundamental machining process that involves the removal of material from a rotating workpiece to create cylindrical parts. This technique is essential in various manufacturing sectors, providing precision and efficiency. Understanding what turning in manufacturing process entails can help businesses optimize their production methods.
Definition and Purpose of Turning
Turning is defined as a machining process where a cutting tool moves linearly while the workpiece rotates around its axis. The primary purpose of turning is to produce cylindrical shapes with precise dimensions and smooth finishes. This process significantly contributes to the production of components such as shafts, bushings, and fittings, which are vital in numerous applications.
What is Turning in Manufacturing Process with Example
To illustrate what turning in manufacturing process looks like, consider the creation of a simple metal shaft. In this example, a solid piece of metal is mounted on a lathe machine, which rotates the workpiece while a cutting tool removes material along its length. This results in a perfectly cylindrical shaft with specific diameters at various points—showcasing how effective turning can be when producing tailored components for machinery.
What is Turning in Manufacturing Process in Lathe Machine
When we talk about what turning in manufacturing process means specifically in relation to lathe machines, we refer to the unique capabilities these machines offer for shaping materials. A lathe machine securely holds the workpiece and spins it at high speeds while an attached cutting tool carves away excess material. This method not only enhances precision but also allows for intricate designs that would be challenging with other types of machining processes.
Types of Machining Processes
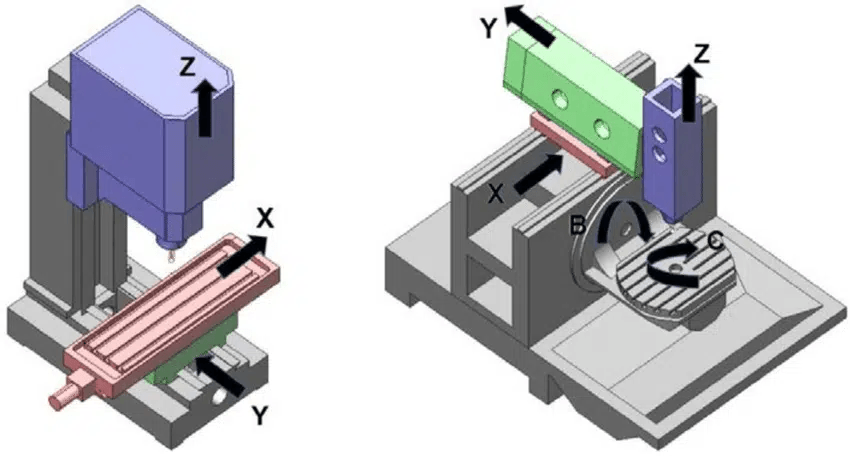
Machining processes play a crucial role in shaping materials into desired forms, and they can be broadly categorized into various techniques. Among these, turning, milling, and drilling are the most common methods used in manufacturing. Each method serves distinct purposes and utilizes different machinery to achieve specific results.
Overview of Milling Techniques
Milling is a versatile machining process that involves removing material from a workpiece using rotary cutters. It can be performed on various types of CNC machines, enabling intricate designs and precise dimensions. There are several milling techniques, including face milling, which cuts flat surfaces; end milling for creating slots or profiles; and contour milling for complex shapes—each technique tailored to meet specific manufacturing needs.
In essence, what is turning in manufacturing process? While turning focuses primarily on rotating the workpiece against a stationary tool to remove material, milling employs multi-directional movement to achieve similar outcomes but with different geometries. Understanding both processes allows manufacturers to choose the right approach based on their project requirements.
Common Drilling Methods in Manufacturing
Drilling is another essential machining process that involves creating holes in solid materials using drill bits. The most common drilling methods include twist drilling for general-purpose applications, reaming for refining hole sizes and finishes, and counterboring for accommodating fasteners or fittings. Each method has its unique advantages depending on the material being drilled and the desired outcome.
When considering what is turning in manufacturing process alongside drilling methods, it becomes clear that both processes complement each other in many applications. For example, after turning a cylindrical part on a lathe machine (what is turning in manufacturing process in lathe machine), subsequent drilling may be necessary to create precise holes for assembly or fastening purposes.
Comparing Turning, Milling, and Drilling
Turning, milling, and drilling each have their unique strengths that make them suitable for different tasks within manufacturing environments. Turning excels at producing symmetrical parts with smooth surfaces due to its rotational nature; it’s often employed when high precision is required (what is turning process). On the other hand, milling offers greater versatility by allowing complex shapes while maintaining accuracy.
Drilling serves as an essential complement to both turning and milling by providing holes necessary for assembly or functionality within components—highlighting how these three processes interconnect within modern production lines. When considering what is turning in manufacturing process alongside these techniques helps clarify their roles: while all involve material removal from workpieces (Types of Machining Processes), they do so through distinct mechanisms tailored to meet varying engineering demands.
The Role of SYIL CNC Machines
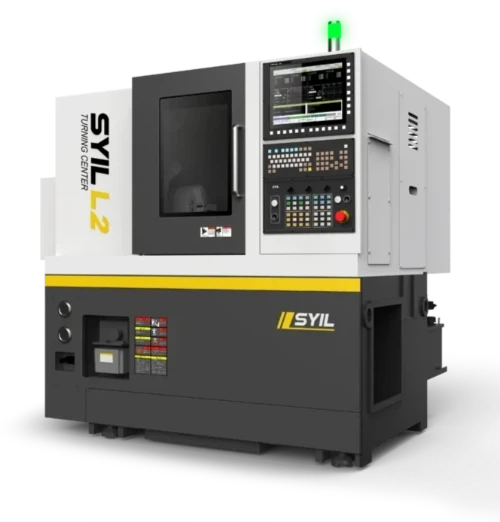
In the world of machining, SYIL CNC machines stand out for their ability to enhance productivity and precision across various applications. Specifically, the SYIL X5 Mini CNC Machine has garnered attention for its compact design and robust capabilities. This section will delve into the advantages of this machine, its applications in prototyping and jewelry making, and its overall precision and versatility in machining processes.
Advantages of the SYIL X5 Mini CNC Machine
The SYIL X5 Mini CNC Machine offers several key advantages that make it a popular choice among manufacturers. First off, its compact size means it can fit comfortably in smaller workshops without sacrificing functionality—a win-win for those limited on space! Additionally, this machine boasts high-speed machining capabilities with impressive accuracy, which is essential when considering what is turning in manufacturing process since precision is paramount.
Another significant advantage lies in its user-friendly interface that allows operators to easily program complex tasks. This accessibility makes it suitable for both seasoned machinists and beginners alike. Furthermore, the machine's durability ensures that it can handle various types of machining processes effectively—be it turning or milling—making it a versatile addition to any workshop.
Applications in Prototyping and Jewelry Making
When discussing what is turning in manufacturing process with examples, one cannot overlook the role of SYIL machines in prototyping and jewelry making. In prototyping, rapid iteration is crucial; thus, the speed and efficiency of the SYIL X5 allow designers to bring their concepts to life quickly without compromising on quality. This capability ensures that prototypes can be tested and refined faster than ever before.
In jewelry making specifically, this mini CNC machine shines by enabling intricate designs that would be nearly impossible to achieve manually. The precision offered by the SYIL X5 allows artisans to create detailed pieces with fine features—perfectly illustrating what is turning process involves when applied creatively in this industry. Moreover, small batch production becomes feasible without incurring excessive costs or time delays.
Precision and Versatility in Machining
The precision offered by SYIL CNC machines makes them indispensable tools within various industries focused on what is turning in manufacturing process today. With advanced technology integrated into these machines, users can achieve tolerances as tight as ±0.01 mm—ideal for demanding applications like aerospace or medical device manufacturing where accuracy cannot be compromised.
Versatility also plays a critical role; whether you're milling aluminum parts or drilling intricate holes into hard steel components, the adaptability of these machines accommodates different types of machining processes seamlessly. By understanding how each technique—including turning—is implemented through programmable software controls on devices like the SYIL X5 Mini CNC Machine, manufacturers can optimize their operations efficiently.
Investing in quality machinery such as this not only enhances productivity but also paves the way for innovation across sectors reliant on precise manufacturing techniques.
What is Turning Process: A Closer Look
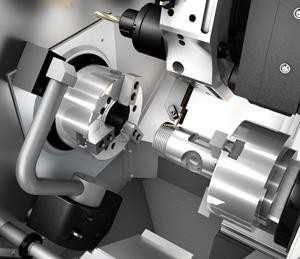
Turning is a fundamental machining process that involves the removal of material from a rotating workpiece to create cylindrical shapes. This technique is widely used in manufacturing for producing components with precise dimensions and smooth finishes. In this section, we will delve deeper into what turning is in the manufacturing process, its advantages across various industries, and some real-world applications that highlight its significance.
Detailed Explanation with a Diagram
To grasp what turning is in the manufacturing process, it's helpful to visualize how it operates. The workpiece is mounted on a lathe machine, which rotates it while a cutting tool moves along its surface to remove material. The diagram below illustrates this relationship: the lathe machine spins the workpiece at high speeds while the cutting tool engages with it, shaping it into desired forms such as shafts or discs.
This method not only defines what turning in manufacturing process entails but also showcases its efficiency when creating complex geometries. For instance, when we discuss what is turning in manufacturing process with an example, think about how automotive parts like crankshafts are produced—turning allows for precision and consistency that other methods may struggle to achieve.
Advantages of Turning in Different Industries
Turning offers numerous advantages that make it invaluable across various sectors. One key benefit lies in its ability to produce high-precision components rapidly; this speed can significantly enhance productivity levels without compromising quality. Additionally, because of its versatility—what is turning in manufacturing process allows for working with different materials such as metals and plastics—it caters to diverse industrial needs ranging from aerospace to medical devices.
Another noteworthy advantage of turning relates to cost-effectiveness; by minimizing waste through efficient material removal processes, manufacturers can save both time and resources. This aspect becomes increasingly important when considering factors such as production volume and material costs within the context of types of machining processes available today. Thus, whether it's creating intricate designs or standard parts at scale, turning remains a go-to choice for many industries.
Real-World Applications of Turning
The practical applications of turning are vast and varied across multiple fields—each showcasing how integral this machining process has become. In automotive engineering alone, components like gears and axles often undergo extensive turning operations due to their need for precision and reliability under stress conditions. Moreover, industries involved in producing medical instruments rely heavily on what is turning in manufacturing processes; surgical tools must meet stringent specifications where accuracy can be life-saving.
Beyond these examples lies the realm of custom fabrication where artisans utilize what is turning in manufacturing processes to craft unique items such as jewelry or bespoke furniture fittings—demonstrating not only functionality but also artistry through design complexity achieved via lathe machines. As we explore further into machining techniques like milling or drilling later on, it becomes clear that while each method has its strengths, the role of turning remains pivotal due to its enduring relevance across diverse applications.
Choosing the Right Machining Process
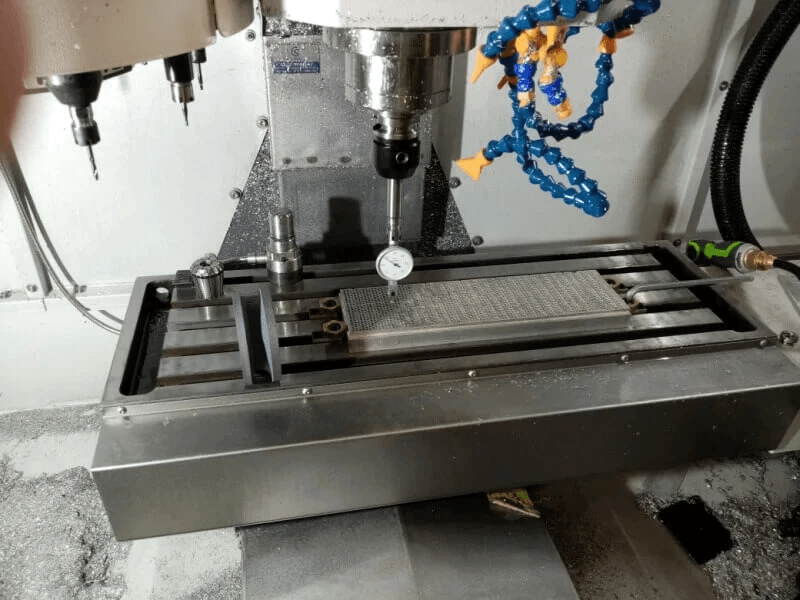
Selecting the appropriate machining process can feel like trying to find a needle in a haystack, especially when you have options like turning, milling, and drilling at your disposal. Each process has its unique strengths and weaknesses, making it crucial to align your choice with specific manufacturing needs. Understanding what is turning in manufacturing process and how it compares to other types of machining processes will help streamline this decision-making journey.
Factors to Consider for Manufacturing Needs
When choosing a machining process, several factors come into play. First, consider the material you are working with; different materials may respond better to certain processes such as turning or milling. Additionally, think about the desired precision and surface finish; for example, what is turning in manufacturing process often yields a smoother finish compared to traditional drilling methods.
Another key factor is production volume—if you're looking at mass production versus prototyping. For instance, what is turning in manufacturing process with example applications like automotive parts may require higher volumes that lend themselves well to automated lathe machines. Lastly, assess your budget constraints; some processes can be more cost-effective than others depending on setup time and tooling costs.
How to Decide Between Turning, Milling, and Drilling
Deciding between turning, milling, and drilling boils down to understanding each method's capabilities in relation to your project requirements. If you're shaping cylindrical parts or creating intricate contours on round surfaces, then what is turning in manufacturing process in lathe machine will likely be your best bet. On the other hand, if flat surfaces or complex shapes are needed—think of those beautiful jewelry designs—the milling technique might take center stage.
Moreover, consider the intricacies involved: while drilling is great for creating holes quickly (and let's face it—who doesn’t love quick results?), it lacks the versatility offered by both milling and turning processes when it comes to shaping materials more broadly. Henceforth evaluating what is turning process compared with these alternatives can illuminate which path fits best for your specific needs.
Cost-Effectiveness of Different Machining Processes
Cost-effectiveness plays an essential role when selecting a machining method; after all, no one wants their project budget going up in smoke! Generally speaking, what is turning in manufacturing process tends to be more economical for producing cylindrical components due to reduced material waste compared with some other techniques like milling or extensive drilling operations.
However, keep an eye on setup times as well—while initial costs might be lower for one method over another (say using a lathe machine), longer setup times can lead to increased labor costs that eat into potential savings. Ultimately weighing these aspects against each other allows manufacturers not only to save money but also optimize productivity across various types of machining processes they employ.
Conclusion
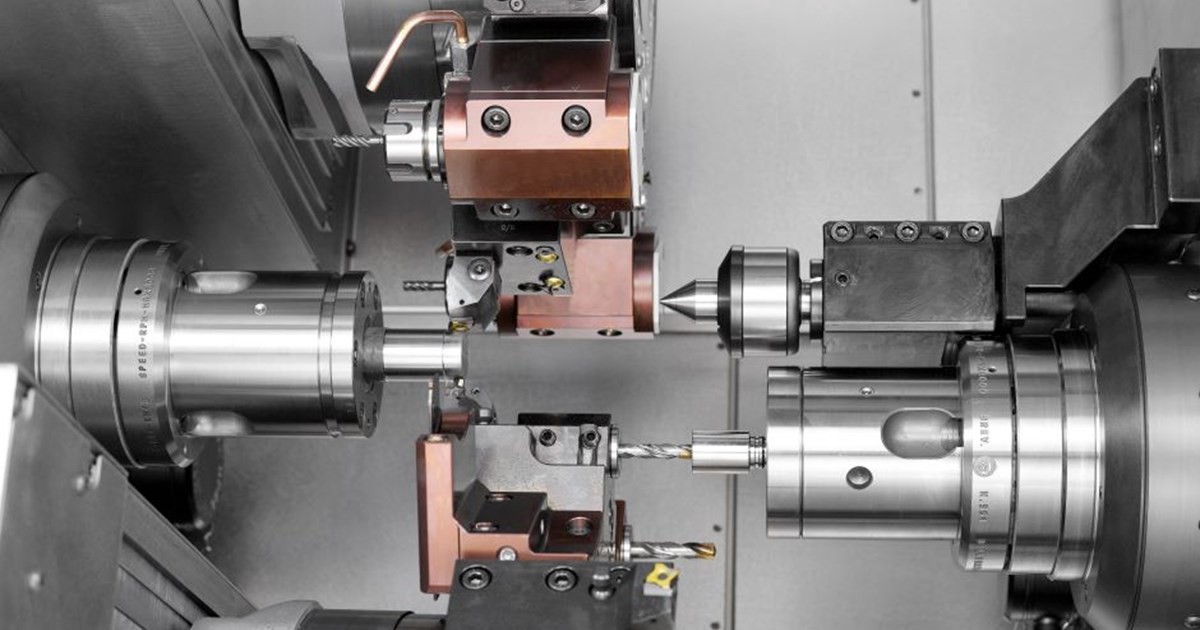
In summary, the machining processes of turning, milling, and drilling each play a vital role in modern manufacturing. Understanding what is turning in manufacturing process is crucial for anyone involved in production, as it offers unique advantages and applications across various industries. By exploring the types of machining processes available, one can make informed decisions that align with their specific needs.
Key Takeaways About Turning, Milling, and Drilling
Turning is a fundamental machining process that involves rotating a workpiece against a cutting tool to achieve desired shapes and sizes; it’s essential to grasp what is turning in manufacturing process with examples to appreciate its versatility. Milling offers precision in creating complex geometries through multi-directional cutting actions, while drilling focuses on producing holes with accuracy. Each process has its distinct characteristics and applications—what is turning in manufacturing process in lathe machines showcases the effectiveness of this technique for cylindrical components.
The Future of Machining Technologies
As technology advances, the future of machining technologies looks promising with innovations like automation and smart machines transforming traditional practices. Understanding what is turning process will become even more critical as manufacturers leverage data-driven insights for improved efficiency and precision. Emerging trends such as additive manufacturing may also complement conventional methods like turning, milling, and drilling by providing hybrid solutions that enhance productivity.
Investing in Quality Machinery like SYIL CNC
Investing in quality machinery such as SYIL CNC machines ensures that manufacturers can keep pace with evolving demands while maintaining high standards of quality and precision. The capabilities offered by these machines make them ideal for exploring what is turning in manufacturing process with diagrammatic representations showcasing their operational mechanics. By choosing reliable equipment tailored to specific needs—whether it's prototyping or large-scale production—businesses can maximize their output while minimizing costs associated with less efficient types of machining processes.