Introduction
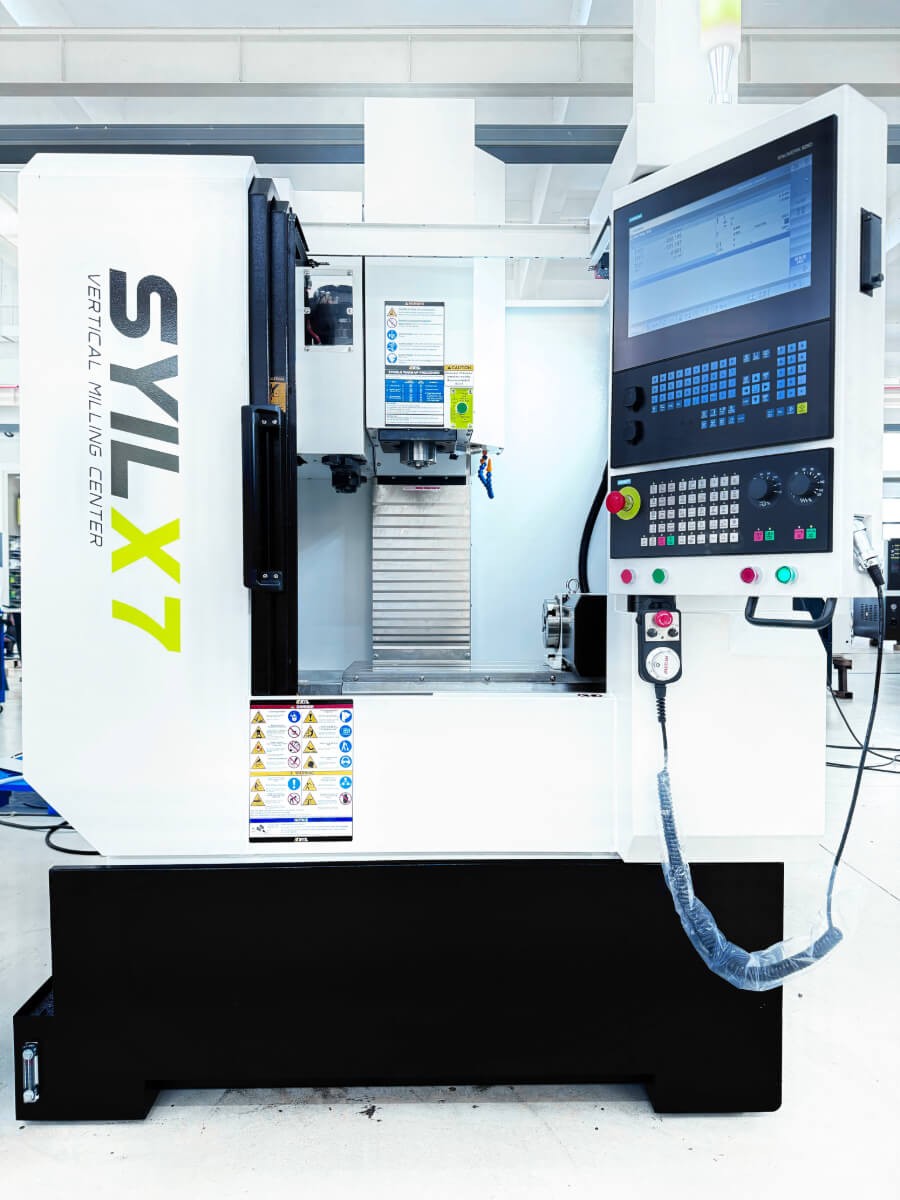
In the world of CNC (Computer Numerical Control) machining, precision is paramount, and one of the key players in achieving that precision is the concept of tool offset in CNC. Tool offsets allow machinists to adjust for variations in tool length and diameter, ensuring that each component is manufactured to exact specifications. Without a solid understanding of what an offset tool is, or how it functions within a CNC lathe, achieving high-quality results can become a daunting task.
Understanding Tool Offset in CNC
At its core, tool offset in CNC refers to the adjustments made to account for differences between the programmed coordinates and the actual position of a cutting tool. This can include factors like wear on tools or differences in their physical dimensions. Understanding what is zero offset in CNC and how it relates to other offsets helps operators maintain accuracy throughout the machining process.
Importance of Tool Offsets in Precision Machining
Tool offsets play a critical role in precision machining by allowing operators to fine-tune their machines for optimal performance. If these offsets are not accurately set, even minor discrepancies can lead to significant errors over time, impacting product quality and manufacturing efficiency. Thus, knowing how to calculate the tool length offset value correctly becomes essential for maintaining high standards in production.
Overview of CNC and its Applications
CNC technology has revolutionized manufacturing across various industries—from automotive to aerospace—by automating complex processes with unparalleled accuracy. The ability to program different types of offsets allows for flexibility and adaptability when working with diverse materials and designs. As we explore further into this topic, we will delve into questions such as: What are the 4 types of offsets? How do they apply specifically within different machines?
Defining Tool Offset in CNC
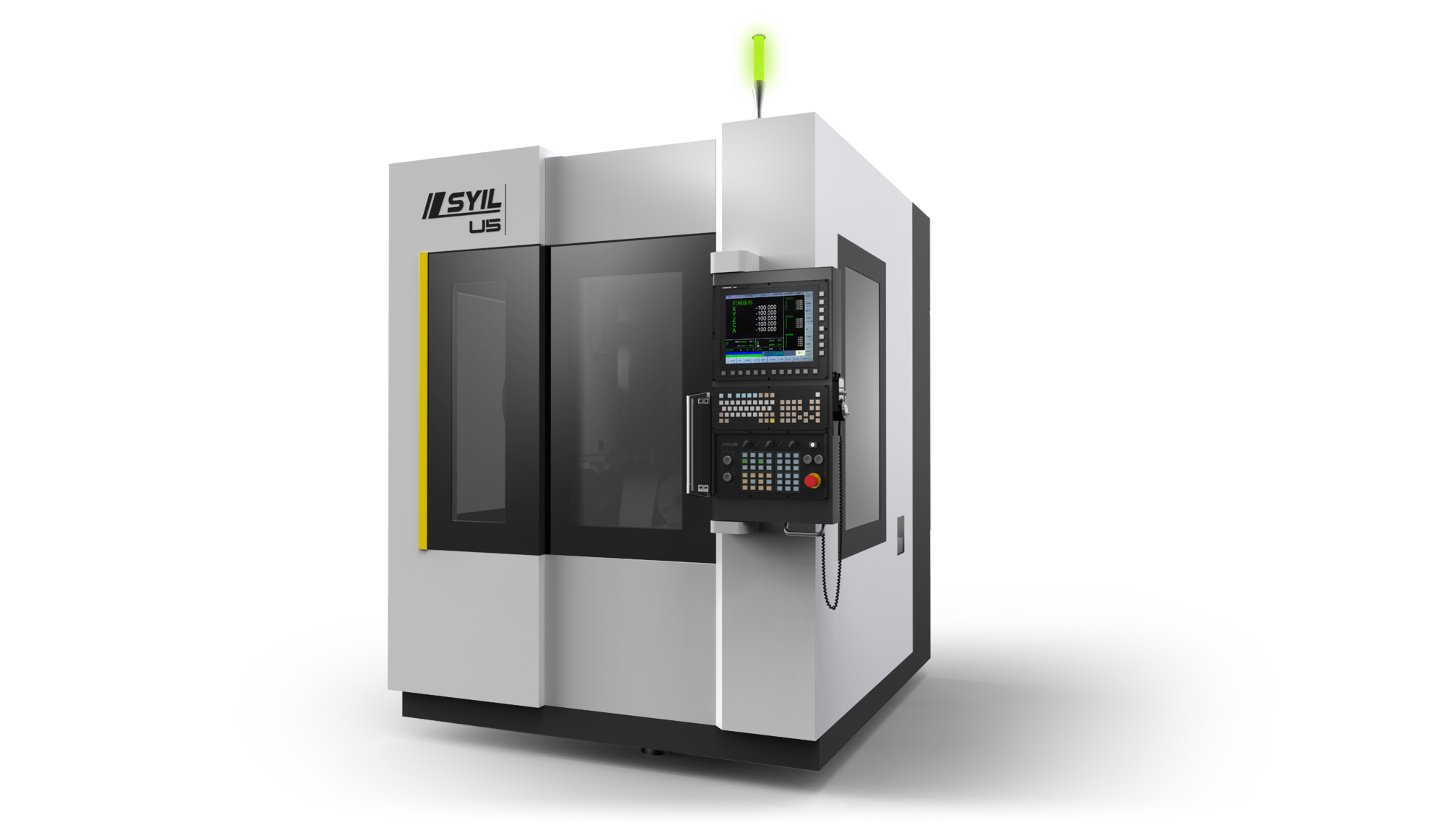
In the realm of CNC machining, understanding tool offset is crucial for achieving precision and accuracy. Tool offset refers to the adjustments made to account for variations in tool dimensions, ensuring that the machine operates effectively. This section will explore what an offset tool is, delve into the specifics of tool length offset, and discuss its implications in CNC lathe operations.
What is an Offset Tool?
An offset tool is a cutting instrument that has been adjusted or calibrated to account for its physical dimensions and position relative to the workpiece. In essence, when we talk about What is an offset tool? we refer to tools that have specific offsets programmed into the CNC system to enhance machining accuracy. These adjustments are essential because even minor discrepancies can lead to significant errors in production.
Offset tools are typically used in various machining processes where precision is paramount. For example, a drill bit might require an adjustment based on its length or diameter to ensure it reaches the intended depth without overshooting or undershooting. By utilizing these tools correctly, machinists can maintain high standards of quality while minimizing waste and rework.
Understanding Tool Length Offset
Tool length offset refers specifically to the measurement taken from a reference point on a CNC machine to the tip of a cutting tool. This value allows operators to adjust for differences in tool lengths when multiple tools are employed during machining operations—essentially answering What is the tool length offset value? It ensures that each tool engages with the workpiece at precisely the right depth.
Understanding this concept can significantly impact production efficiency and quality control. A well-calibrated tool length offset prevents issues such as incorrect cuts or damage to both tooling and workpieces, which could arise from improper settings. Moreover, accurate measurement of this offset contributes directly to maintaining consistent tolerances throughout manufacturing processes.
Implications of Tool Offset in CNC Lathe
The implications of tool offsets extend far beyond mere calculations; they play a vital role in optimizing performance within CNC lathes as well. In these machines, where rotational movement is combined with linear motion, precise adjustments through effective tool offsets are necessary for successful part fabrication. Understanding how tool offset in CNC lathe functions helps machinists avoid common pitfalls associated with poor calibration.
When operators fail to account for appropriate offsets, they risk producing parts that do not meet specifications or tolerances required by clients—leading potentially costly reworks or scrapped materials. Additionally, incorrect offsets can increase wear on both tooling and machines due to excessive force being applied inadvertently during operation. Therefore, mastering these concepts not only enhances productivity but also safeguards equipment longevity.
The Four Types of Offsets
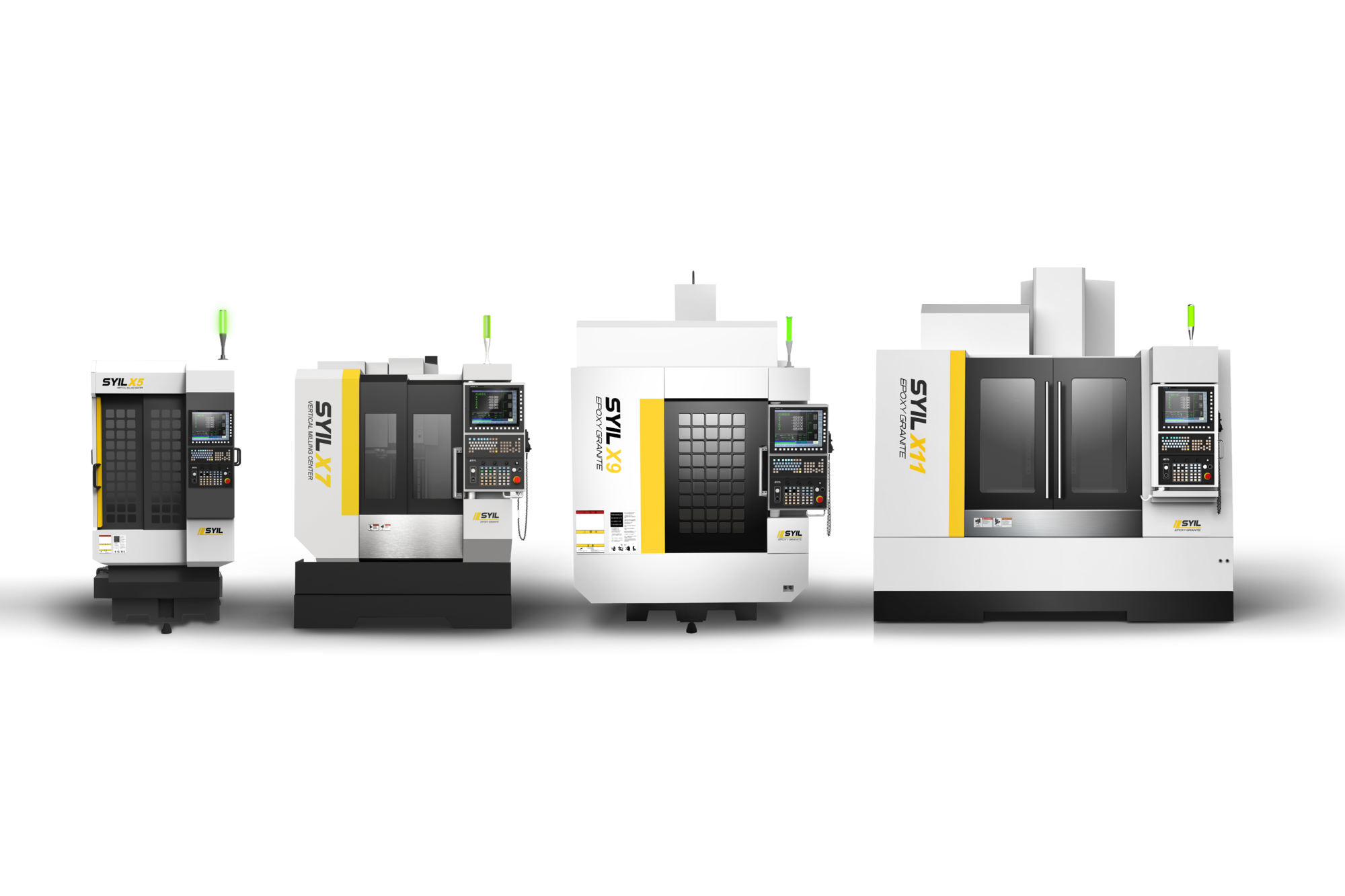
When diving into the world of CNC machining, understanding the different types of offsets is crucial for precision and efficiency. Tool offset in CNC plays a vital role in ensuring that your machine operates accurately, regardless of the complexity of the task at hand. In this section, we’ll explore what these four types are and how they impact your production process.
What Are the 4 Types of Offsets?
The four main types of offsets in CNC machining include tool length offset, tool radius offset, work coordinate offset, and fixture offset. Each type serves a distinct purpose but collectively ensures that the machine knows exactly where to position tools and materials during operation. For instance, while tool length offsets adjust for variations in tool sizes, work coordinate offsets help define where on the workpiece to start cutting.
Understanding these offsets is essential when asking yourself: “What are the 4 types of offsets?” Knowing them not only aids in setup but also minimizes errors during production runs. By mastering these concepts, machinists can achieve higher levels of accuracy and efficiency.
Differences Between Tool Offsets
While all four types serve their purpose within CNC operations, their differences are significant enough to warrant attention. Tool length offsets specifically address variations in how long a tool extends from its holder; this is crucial for achieving precise depths during machining operations like drilling or milling. On the other hand, tool radius offsets focus on compensating for differences between various cutting tools' diameters.
Moreover, understanding what an offset tool is becomes easier when you recognize these differences—each type contributes uniquely to overall machining precision. The distinctions between them also highlight why proper management of each offset type is fundamental for successful CNC operations and can ultimately affect production quality.
Application of Offsets in Production
The application of offsets in production cannot be overstated; they are integral to achieving desired results efficiently and accurately. For example, using a proper tool length offset ensures that machines cut at correct depths without damaging either tools or workpieces—particularly important when working with delicate materials or intricate designs like those often found in CNC lathe operations.
In addition to improving accuracy through calculated adjustments like zero offset in CNC setups, employing these various offsets allows manufacturers to streamline their processes significantly. By leveraging each type effectively—whether it’s for quick adjustments or complex multi-tool setups—machinists can enhance productivity while maintaining high-quality standards throughout their production cycles.
Zero Offset in CNC Explained
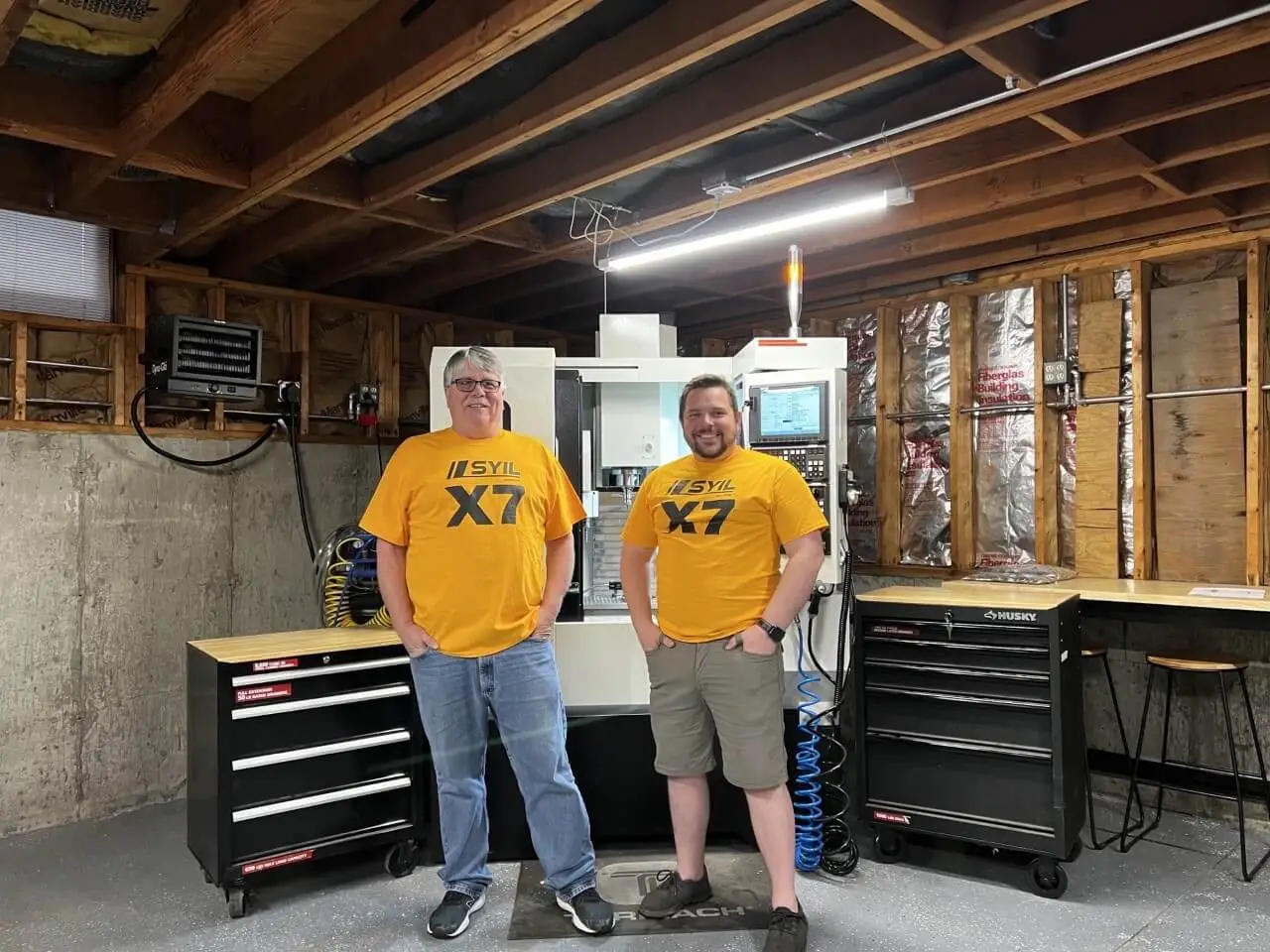
In the world of CNC machining, zero offset is a crucial concept that every machinist should grasp. Essentially, it refers to the established reference point from which all tool movements and measurements are made during machining operations. Understanding what zero offset in CNC means is vital for achieving precision and accuracy in your projects.
What is Zero Offset in CNC?
Zero offset in CNC represents the baseline position of a tool relative to a workpiece or fixture. This means that when you set up your machine, you'll define this zero point so that all subsequent movements are calculated based on it. It plays a significant role when you're dealing with tool offsets in CNC, ensuring that every cut or operation begins from the correct starting point.
When you think about tool offsets, consider how they relate to various types of offsets used in CNC machinery. Knowing what an offset tool is becomes essential here; it's any cutting instrument whose position needs adjustment based on its length or diameter to maintain precision during operations. Thus, understanding zero offset helps you navigate through these concepts seamlessly.
Significance in Setup and Calibration
By establishing a clear reference point at the beginning of each job, you minimize errors that could arise from miscalculations or improper positioning of tools. This ensures that your machine operates efficiently while maintaining high standards for quality.
In practical terms, if you fail to set an accurate zero offset, even minor discrepancies can lead to significant issues down the line—think misaligned cuts or wasted material due to incorrect depths being programmed into the system! Therefore, understanding what is the tool length offset value becomes essential since it relies heavily on accurate zeroing for precise results.
Moreover, proper calibration using zero offsets allows for better repeatability across multiple runs of production parts. This consistency can lead not only to improved productivity but also reduced costs associated with rework due to errors stemming from improper initial setups.
Real-World Examples of Zero Offset Usage
Real-world applications highlight just how integral zero offsets are within various industries utilizing CNC technology. For instance, consider a scenario where you're working with a CNC lathe; without properly setting your zero offset before starting your project, each rotation may yield inconsistent results leading potentially disastrous outcomes like part scrapping or machine damage.
Another example can be found within manufacturing environments where precision components are required—like aerospace parts—where even fractional errors could compromise safety standards! Here again lies the importance of knowing what are the 4 types of offsets as they help differentiate between adjustments needed for different tools and their respective applications.
Lastly, think about how many times you've seen operators double-check their setups before running jobs; this habit stems directly from recognizing how crucial proper management of tool offsets—including understanding both standard and zero offsets—is for achieving optimal performance on any given project!
Calculating Tool Length Offset Value
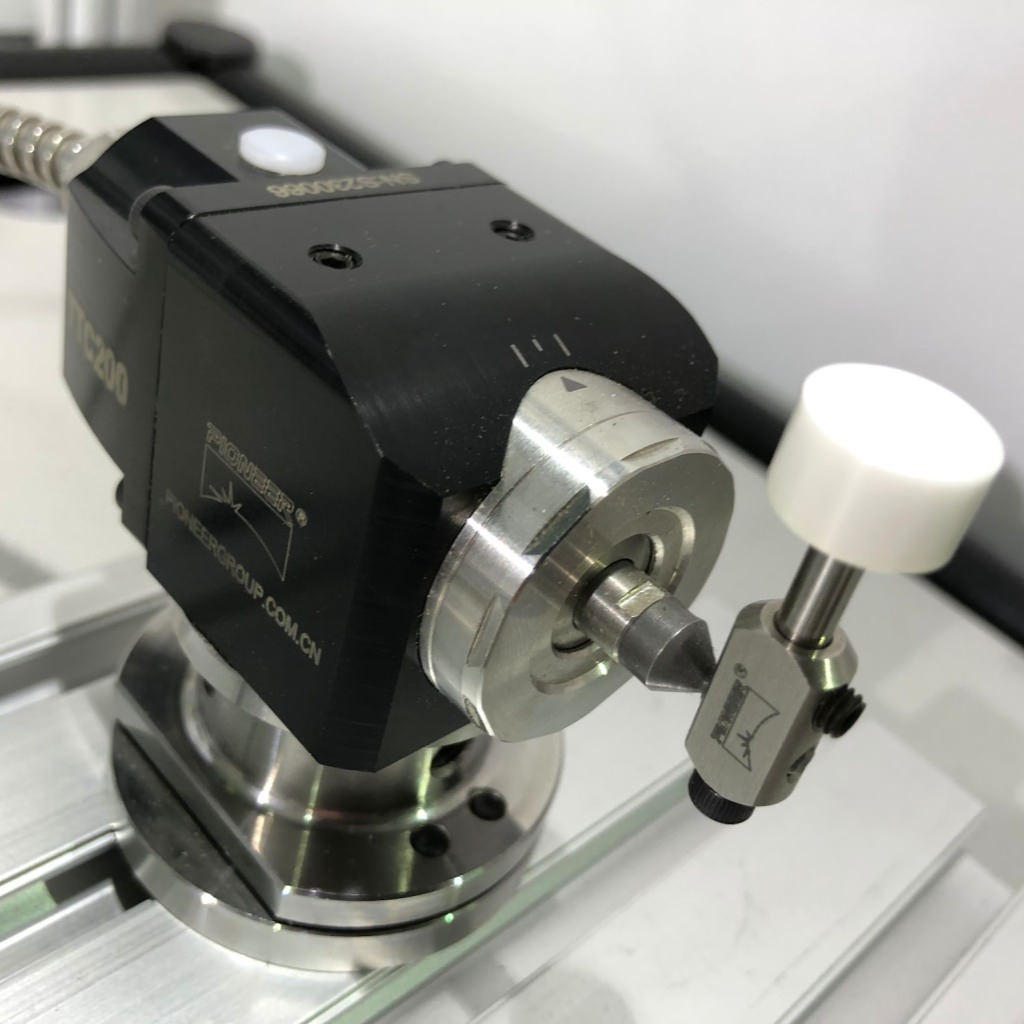
When it comes to CNC machining, understanding how to accurately calculate the tool length offset value is crucial for achieving precision and efficiency. The tool length offset value essentially represents the difference between the programmed tool path and the actual position of the cutting tool. By ensuring that this value is correctly calculated and applied, machinists can avoid costly mistakes and enhance productivity in their operations.
What is the Tool Length Offset Value?
The tool length offset value refers to a specific measurement used in CNC programming that accounts for variations in tool lengths. This ensures that when a CNC machine executes a program, it compensates for any discrepancies between different tools or setups. In essence, it's an essential part of managing tool offsets in CNC, allowing operators to maintain accuracy across various machining tasks.
Methods for Accurate Calculation
Calculating the tool length offset value can be achieved through several methods, each suited for different scenarios. One common approach is using a height gauge or a digital caliper to measure the actual length of each tool directly against a reference point on the machine. Another method involves inputting values based on manufacturer specifications or using software tools designed specifically for calculating offsets in CNC systems; these often simplify what could otherwise be a tedious process.
Additionally, ensuring that your workpiece is correctly set up and secured during measurement will dramatically improve accuracy when determining your offsets. Remember, consistency is key—always use the same reference point and measuring technique to avoid discrepancies across various tools or jobs.
Troubleshooting Common Calculation Errors
Even seasoned machinists can encounter errors when calculating tool length offsets; however, many issues are easily rectified with careful attention to detail. One common error arises from improper zeroing of measuring tools—ensure your height gauge or caliper reads zero before taking measurements! Another frequent mistake involves overlooking variations in tooling due to wear; always inspect tools before use and adjust offsets accordingly.
If you're working with multiple machines or setups, double-checking your entered values against physical measurements can help catch errors early on. Remember: an accurate calculation of your tool length offset value not only saves time but also enhances overall machining quality—because nobody wants their parts coming out looking like they were made by someone who skipped math class!
Tools and Machines Leveraging Tool Offset
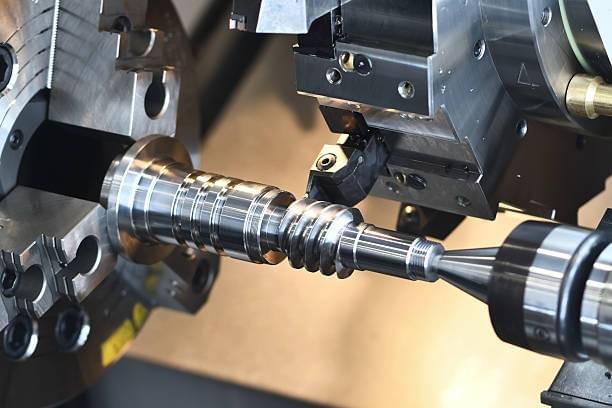
In the world of CNC machining, understanding tool offset is crucial for achieving precision and efficiency. Various machines utilize advanced tool offset systems to enhance their performance, ensuring that operations are carried out with minimal error. Among these machines, the SYIL CNC machine stands out for its innovative features tailored to streamline the machining process.
SYIL CNC Machine and Its Features
The SYIL CNC machine is designed with a focus on versatility and user-friendliness, making it ideal for both beginners and experienced machinists. One of its standout features is its ability to manage multiple tool offsets seamlessly, allowing users to switch between different tools without recalibrating each time. This capability directly addresses the question, What is an offset tool? by providing a practical solution that enhances workflow while maintaining accuracy in operations.
Additionally, the SYIL machine incorporates advanced software that simplifies the input of tool length offsets, making it easier than ever to adjust settings based on specific project requirements. The integration of zero offset in CNC technology further ensures that every cut is precise from start to finish. Overall, the SYIL CNC machine exemplifies how modern technology can leverage tool offsets to improve productivity in machining environments.
Benefits of Advanced Tool Offset Systems
Advanced tool offset systems bring a multitude of benefits to precision machining, particularly when dealing with complex projects involving various materials and geometries. By effectively managing what are the 4 types of offsets—tool length offsets, work offsets, fixture offsets, and geometry offsets—these systems enable operators to achieve greater accuracy while minimizing setup time. This efficiency translates into reduced production costs and enhanced output quality.
Moreover, understanding what is zero offset in CNC becomes essential when setting up these advanced systems since it acts as a reference point for all other adjustments. With accurate calculations of the tool length offset value being central to this process, machinists can ensure their tools are always positioned correctly relative to their workpieces. Ultimately, these benefits lead to improved operational reliability and consistency across various manufacturing applications.
Comparison with Other CNC Machines
When comparing the SYIL CNC machine with other models on the market, it's clear that not all machines handle tool offset in CNC equally well. Many traditional machines may require more manual input or lack intuitive interfaces for managing complex offsets effectively. In contrast, machines equipped with robust software solutions provide seamless integration of features like automatic adjustments based on calculated values derived from previous operations.
Furthermore, other machines may struggle with accurately calculating what is the tool length offset value during rapid changes between different tooling setups or materials—a situation where advanced systems shine through their adaptability and precision capabilities. The difference becomes even more pronounced when considering how effective each system is at leveraging zero offset in CNC setups; those that can't adapt quickly often lead to increased downtime or errors during production runs.
In conclusion, as industries increasingly rely on precision machining technologies like those found in SYIL CNC machines equipped with advanced tool offset management systems, understanding how these components interact will be vital for future success.
Conclusion
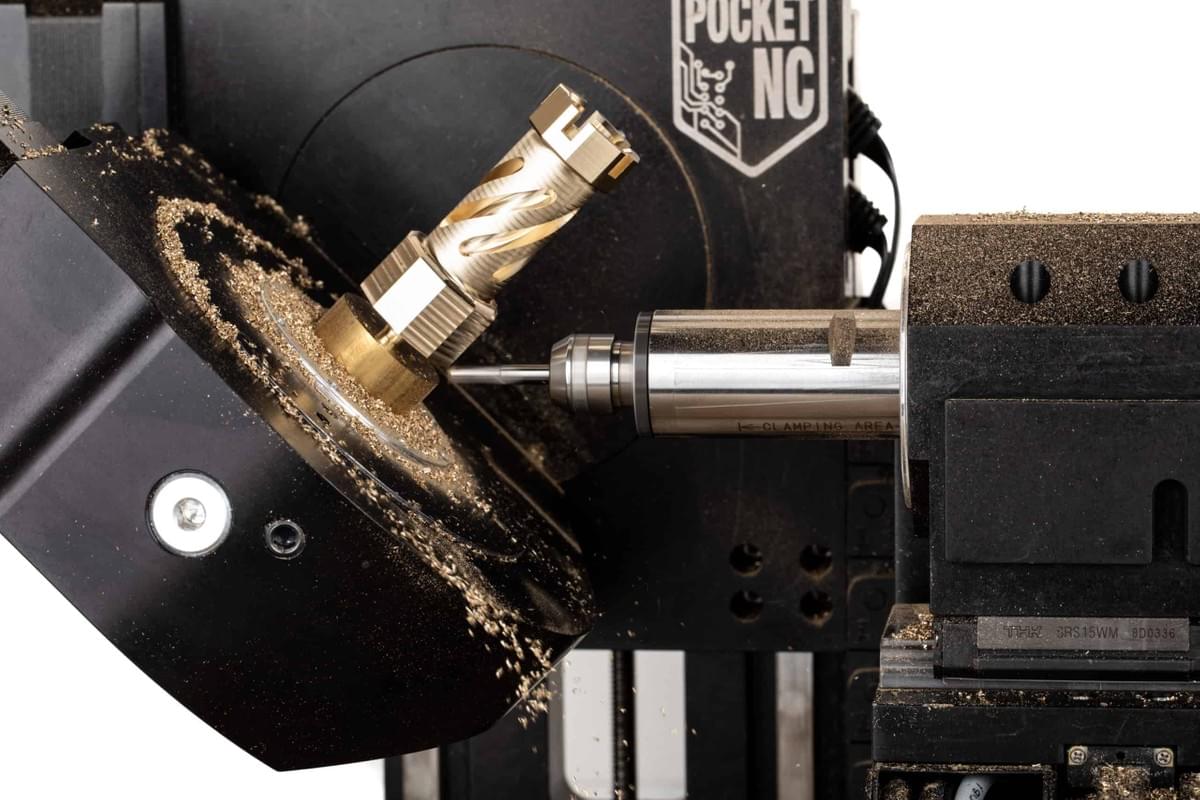
In the world of CNC machining, understanding tool offset is crucial for achieving precision and efficiency. Whether you're working with a CNC lathe or milling machine, knowing the different types of offsets and their applications can significantly enhance production quality. As we've explored, tool offsets are not just technical jargon; they play a vital role in ensuring that your machinery operates smoothly and accurately.
Key Takeaways on Tool Offsets
To recap, tool offset in CNC refers to the adjustments made to account for variations in tool dimensions and positions during machining operations. We discussed that there are four primary types of offsets, including tool length offset, which is essential for determining the correct cutting depth. Additionally, understanding what an offset tool is helps machinists set up their equipment more effectively, leading to improved outcomes in production.
Best Practices for Tool Offset Management
Managing tool offsets effectively requires a systematic approach to ensure accuracy throughout the machining process. Regularly calibrating your CNC machine can help maintain precise measurements for zero offset in CNC setups, preventing costly errors during production runs. Furthermore, documenting changes in the tool length offset value will provide valuable insights into performance trends and assist with troubleshooting any discrepancies that arise.
Future Trends in CNC Tool Offset Technology
Looking ahead, advancements in technology promise to revolutionize how we handle tool offsets in CNC machining environments. Innovations such as automated measurement systems will likely make calculating the tool length offset value faster and more accurate than ever before. Additionally, as artificial intelligence continues to integrate into manufacturing processes, we can expect smarter tools that automatically adjust offsets based on real-time data analysis—ultimately pushing precision machining into new realms of efficiency.