Introduction
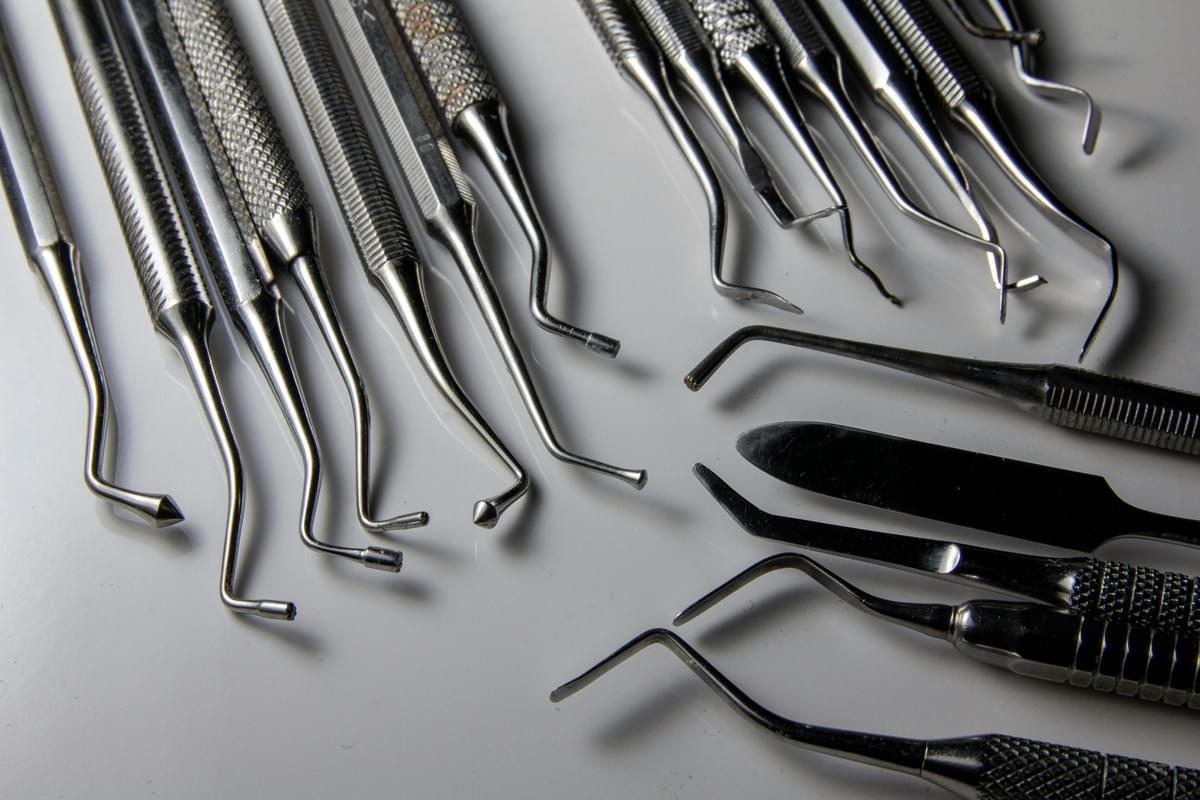
In the rapidly evolving landscape of healthcare, **Medical CNC Machining** stands out as a game-changer, revolutionizing how medical devices and pharmaceuticals are manufactured. This advanced technology employs computer numerical control (CNC) to enhance precision and efficiency in the production process. As we delve into this exciting field, it's essential to explore what CNC means in healthcare and how it is reshaping the medical industry.
Overview of Medical CNC Machining
Medical CNC machining refers to the use of computerized systems to control machine tools that create intricate components for medical applications. This technology allows for the production of highly detailed parts with exceptional accuracy, which is crucial in fields where even minor deviations can lead to significant consequences. By employing CNC machining for the medical industry, manufacturers can ensure that devices meet stringent regulatory standards while optimizing their production processes.
Importance in Healthcare and Pharmaceuticals
The importance of CNC machining in healthcare cannot be overstated; it plays a vital role in producing everything from surgical instruments to custom implants. In addition, this technology significantly contributes to the pharmaceutical industry by enabling precise manufacturing processes that adhere to strict quality controls. Understanding what CNC stands for in the pharmaceutical industry highlights its pivotal role in ensuring patient safety and enhancing treatment outcomes.
Innovations Shaping the Future
As we look toward the future, innovations driving advancements in **Medical CNC Machining** promise exciting developments that will further enhance its capabilities. From integrating artificial intelligence into machining processes to employing advanced materials that improve product durability, these innovations are set to redefine manufacturing standards within healthcare. The question remains: is there a future in CNC machining? The answer is a resounding yes, as ongoing advancements continue to push boundaries and improve efficiencies across various sectors.
Understanding CNC Machining in Healthcare
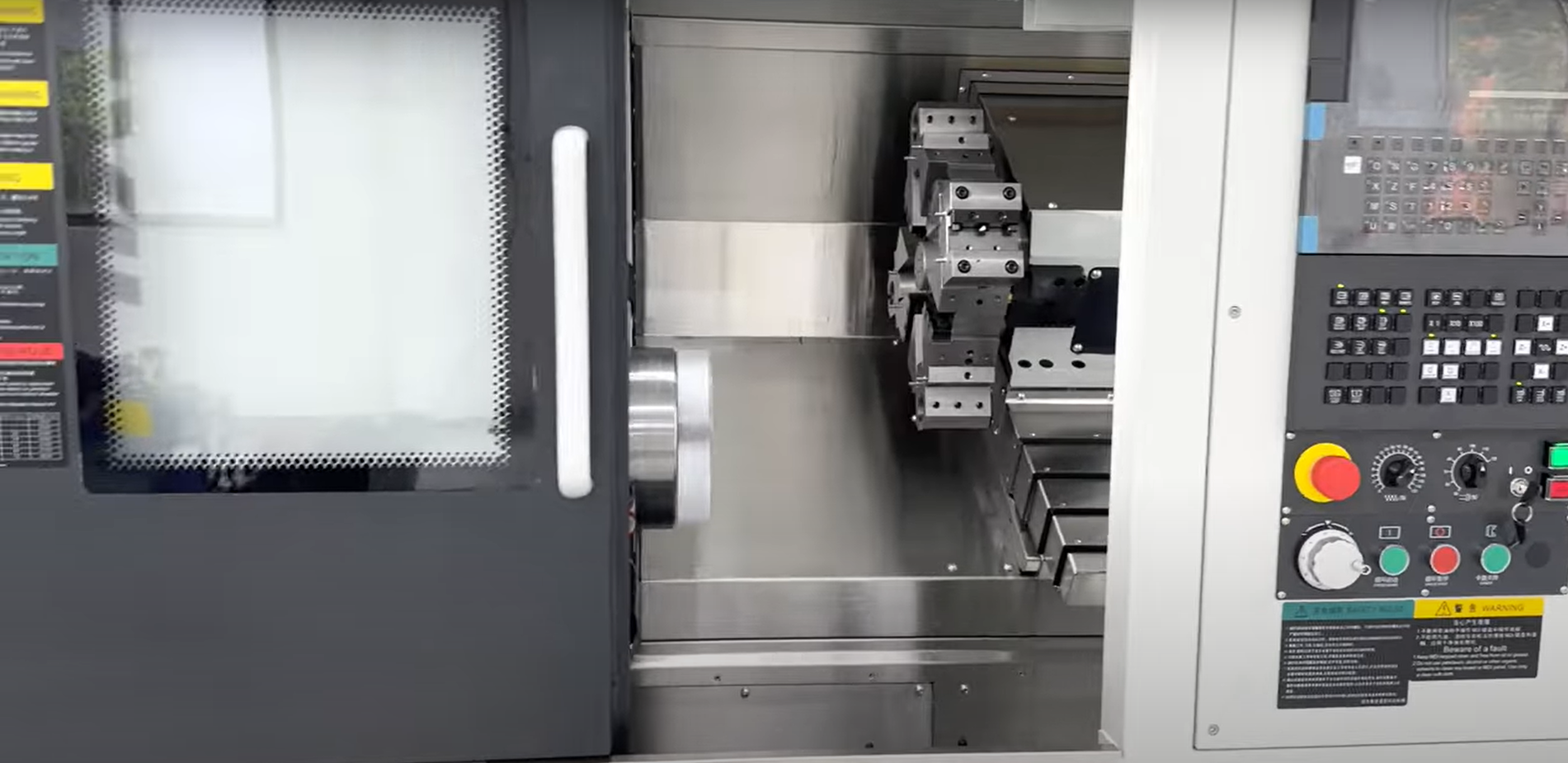
CNC machining has emerged as a cornerstone in the medical industry, transforming how devices and instruments are manufactured. It stands for Computer Numerical Control, which means that the machines operate through programmed commands rather than manual intervention. This level of precision is critical in healthcare, where even the smallest error can lead to significant consequences.
What does CNC mean in healthcare?
In healthcare, CNC refers to the use of computer-controlled machines to produce medical devices with remarkable accuracy and reliability. Essentially, it allows manufacturers to create complex components that meet stringent regulatory standards while ensuring patient safety. By automating the machining process, CNC machining for the medical industry enhances consistency and quality across various products.
How CNC machines revolutionize medical manufacturing
CNC machines have revolutionized medical manufacturing by enabling rapid prototyping and production of intricate designs that were previously impossible to achieve with traditional methods. With their ability to work with a variety of materials—like metals, plastics, and ceramics—these machines cater to diverse applications within healthcare. Moreover, they significantly reduce lead times and improve overall efficiency in manufacturing processes.
Key components of a Medical CNC Machining process
The Medical CNC Machining process involves several key components that ensure high-quality output tailored for healthcare applications. First is the design phase, where CAD (Computer-Aided Design) software creates detailed models of medical devices or instruments. Next comes the machining phase itself, where tools precisely cut or shape materials according to those designs using advanced CNC technology—a crucial step for achieving what does CNC stand for in the pharmaceutical industry? Lastly, quality control measures are implemented throughout production to guarantee that each item meets rigorous standards before reaching end-users.
Methods Employed in Medical CNC Machining
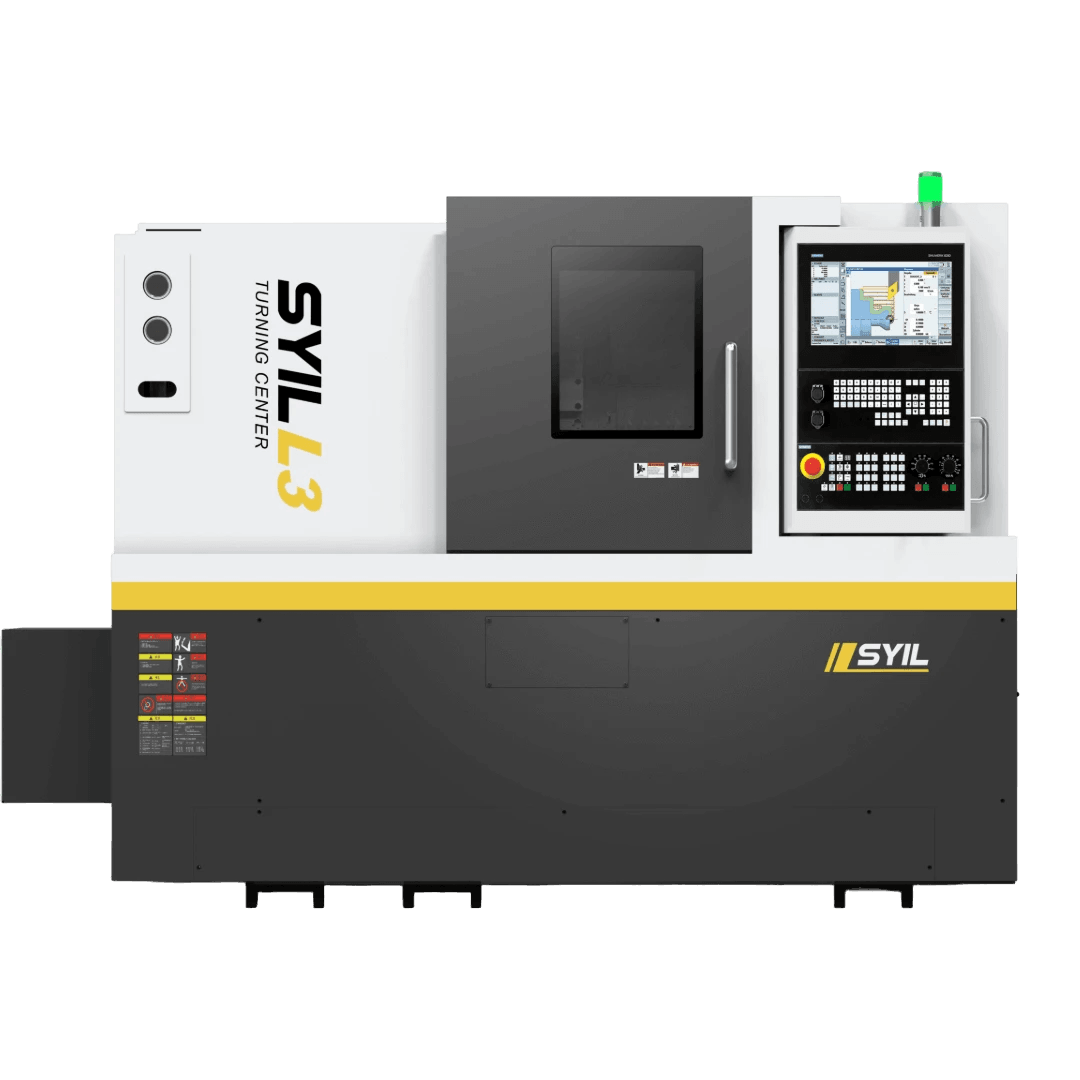
In the realm of healthcare, CNC machining has become a game-changer, bringing forth innovative methods that enhance precision and efficiency in medical manufacturing. Understanding the various techniques employed in this field is crucial for grasping how these machines are revolutionizing the production of medical devices and equipment. This section delves into the different CNC machining techniques used, highlights the role of SYIL CNC machines in ensuring precision, and compares traditional machining methods with modern CNC approaches.
Different CNC machining techniques used
CNC machining for the medical industry employs several specialized techniques tailored to meet stringent quality standards and regulatory requirements. Techniques such as milling, turning, and 3D printing are pivotal in creating intricate components that are essential for medical applications. Each method offers unique advantages; for instance, milling allows for complex shapes while turning is ideal for cylindrical parts, showcasing how versatile CNC technology can be in healthcare manufacturing.
Furthermore, additive manufacturing—a technique often associated with 3D printing—has gained traction within the pharmaceutical industry as it allows for rapid prototyping and customization of drug delivery systems. The ability to produce bespoke implants or surgical instruments through these advanced methods underscores their significance in improving patient outcomes. As we explore what does CNC mean in healthcare, it becomes evident that these diverse techniques contribute substantially to innovation within the sector.
The role of SYIL CNC machines in precision
When discussing precision within medical CNC machining, SYIL CNC machines stand out as exemplars of accuracy and reliability. These machines are designed specifically to meet high tolerances required by medical device manufacturers while maintaining cost-effectiveness—a critical factor given the competitive nature of the industry. With features such as advanced control systems and robust construction, SYIL machines ensure that every component produced adheres to rigorous specifications.
The integration of SYIL technology into production processes enables manufacturers to produce intricate designs with minimal waste, thereby enhancing overall efficiency. In a field where even minute discrepancies can lead to significant consequences, having precise machinery is indispensable for maintaining quality standards. As inquiries about is there a future in CNC machining? arise frequently among industry stakeholders, it’s clear that advancements like those offered by SYIL will play a pivotal role moving forward.
Comparing traditional machining to CNC methods
The comparison between traditional machining methods and modern CNC approaches reveals stark contrasts that highlight why many industries—including pharmaceuticals—are shifting towards automation. Traditional methods often rely on manual processes which can introduce variability due to human error; however, when we ask how are CNC machines used in industry?, it becomes clear they automate these tasks with high precision consistently across production runs.
CNC machining offers enhanced speed compared to its traditional counterparts; lead times are significantly reduced thanks to automated setups that require less downtime between jobs. Additionally, while traditional machining might struggle with complex geometries or tight tolerances required by modern medical applications—such as custom implants—CNC technology excels at producing sophisticated designs efficiently without compromising quality or accuracy.
Ultimately, understanding what does CNC stand for in the pharmaceutical industry emphasizes its critical role: Computer Numerical Control not only streamlines processes but also elevates product reliability across various applications within healthcare settings.
Benefits of CNC Machining for Medical Industry
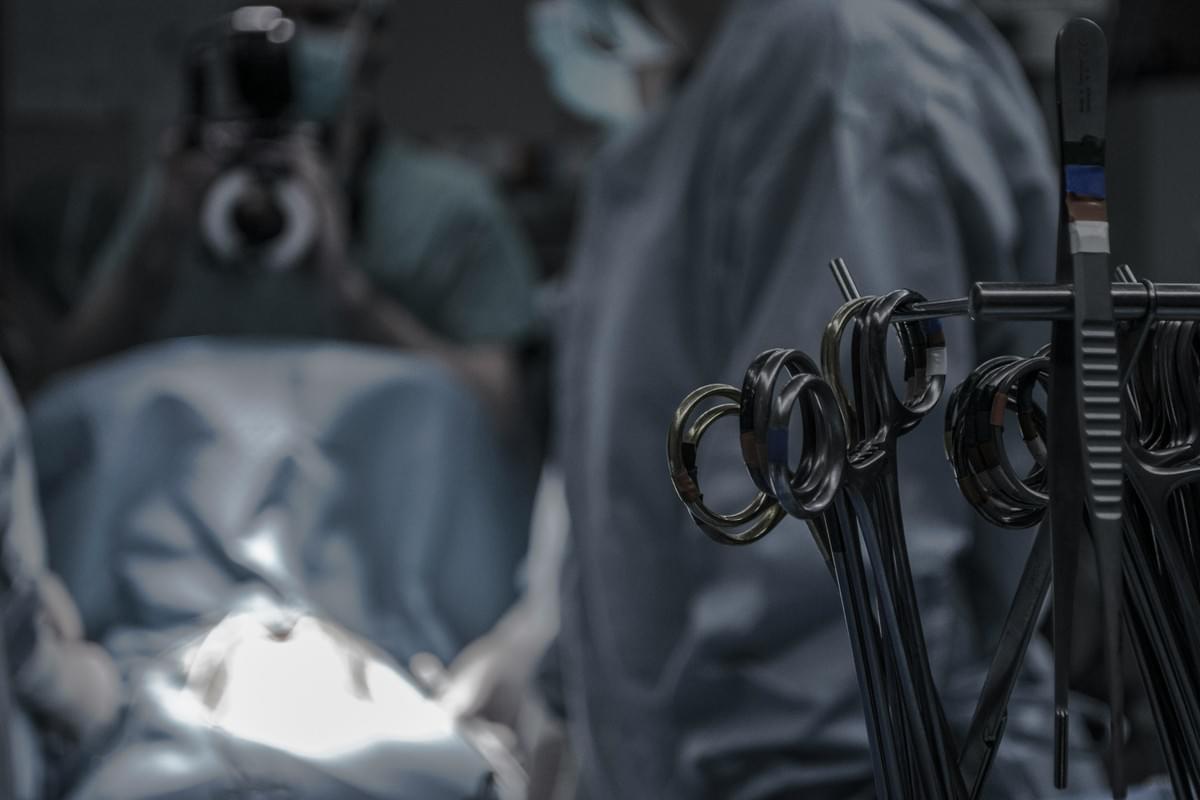
CNC machining for the medical industry is transforming how healthcare products are manufactured, offering a plethora of advantages that improve both quality and efficiency. From enhanced precision to cost savings, the benefits of using CNC technology in medical applications are making waves across the sector. As we delve into these benefits, it's clear that CNC machining is not just a trend; it's a revolution.
Enhanced precision and accuracy in production
When it comes to manufacturing medical devices, precision is paramount. CNC machining for the medical industry ensures that every component meets stringent specifications with incredible accuracy. This level of detail reduces the risk of errors, which is crucial when considering that even minor discrepancies can lead to significant health risks.
Moreover, understanding What does CNC mean in healthcare? becomes essential here; it refers to Computer Numerical Control technology that automates processes with high fidelity. With Medical CNC Machining, parts can be produced repeatedly without variance, ensuring consistency across batches. This kind of reliability is vital in surgical instruments and implants where exact measurements are non-negotiable.
In summary, enhanced precision and accuracy through CNC machining not only elevate product quality but also contribute significantly to patient safety and outcomes.
Reduced lead times and increased efficiency
One of the standout features of CNC machines in industry is their ability to drastically cut down production times while maintaining high-quality standards. By automating processes like cutting and milling, manufacturers can produce parts faster than traditional methods allow. This reduction in lead times means quicker turnaround for essential medical devices—an aspect that's especially critical during emergencies or public health crises.
Additionally, with less manual intervention required in operations like programming and monitoring, staff can focus on other important tasks within healthcare facilities or manufacturing plants. The result? Increased efficiency across the board! In an industry where time truly equates to life-saving capabilities, this benefit cannot be overstated.
As we ponder whether Is there a future in CNC machining?, it's clear that its ability to streamline production will play an integral role moving forward.
Cost-effectiveness in manufacturing medical devices
Cost-effectiveness remains a cornerstone advantage when discussing CNC machining for the medical industry. Traditional manufacturing techniques often involve higher labor costs due to manual handling and oversight; however, with Medical CNC Machining systems running efficiently around the clock, expenses drop significantly over time. The initial investment may be substantial but pays off through reduced operational costs as well as minimized waste due to precise material usage.
Furthermore, understanding What does CNC stand for in the pharmaceutical industry? reveals its applicability beyond just device manufacturing—it's also about optimizing processes involved in producing medications and packaging them effectively at lower costs too! By employing advanced technologies like CAD/CAM integration alongside CNC systems, companies can innovate while keeping budgets under control.
In conclusion, embracing cost-effective solutions through advanced machinery not only boosts profitability but also allows more resources to be allocated towards research and development—a win-win scenario for everyone involved!
Applications of CNC Machining in Healthcare
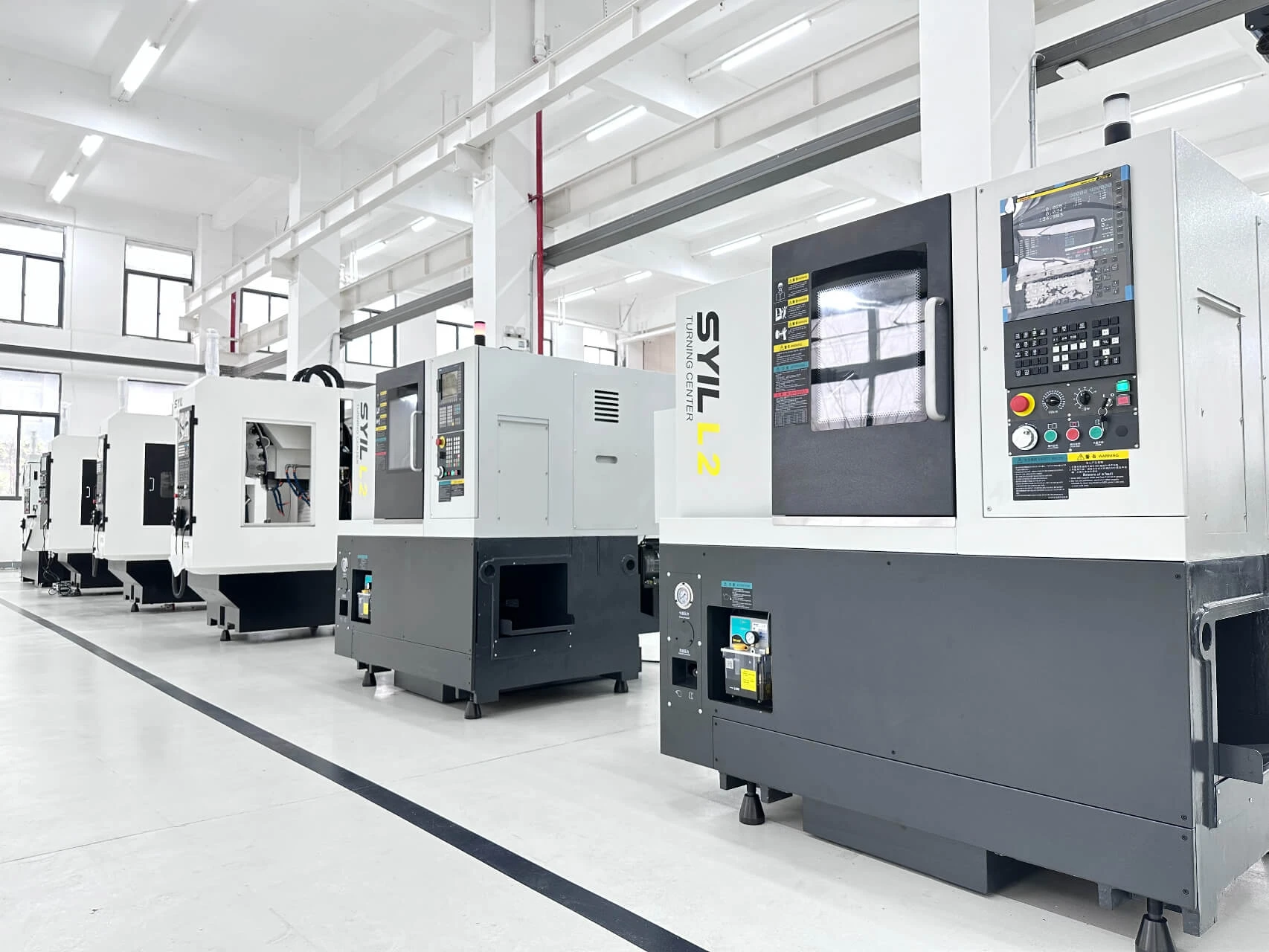
CNC machining for the medical industry is transforming how healthcare professionals create and utilize various devices. From custom implants to surgical instruments, the precision and efficiency of CNC technology are making a significant impact. Let’s dive into some of the key applications that highlight its importance in the field.
Custom implants and prosthetics production
One of the standout applications of CNC machining for the medical industry is in the production of custom implants and prosthetics. These devices require a high level of personalization to ensure a perfect fit for individual patients, which traditional manufacturing methods often struggle to achieve. With Medical CNC Machining, manufacturers can create tailored solutions that enhance comfort and functionality, ultimately improving patient outcomes.
The ability to design complex geometries is another advantage offered by CNC machines. This capability allows for intricate designs that mimic natural anatomy, which is crucial when crafting custom implants. As a result, patients benefit from enhanced mobility and reduced recovery times—an essential consideration in modern healthcare.
Moreover, advancements in materials science have enabled CNC machines to work with biocompatible materials effectively. This means that not only can these devices be tailored for individual needs, but they can also be made from materials that are safe for long-term implantation within the human body.
Manufacturing of surgical instruments
CNC machining plays a pivotal role in manufacturing surgical instruments used across various medical procedures. The precision offered by these machines ensures that tools are crafted with exact specifications, which is vital when performing intricate surgeries where every millimeter counts. What does CNC mean in healthcare? It means reliability—surgeons can trust their instruments will perform flawlessly under pressure.
Additionally, using CNC technology allows manufacturers to produce complex shapes and designs that would be challenging or impossible with traditional methods. This innovation leads to better ergonomic designs for surgical tools, reducing fatigue during lengthy procedures while enhancing overall performance. The accuracy achieved through Medical CNC Machining directly translates into improved safety and efficacy during surgeries.
Furthermore, as hospitals increasingly demand high-quality instruments at lower costs, CNC machining offers an efficient solution by streamlining production processes while maintaining quality standards. By reducing lead times associated with instrument production, healthcare providers can ensure they have ready access to essential tools when needed most.
CNC applications in the pharmaceutical industry
In addition to its applications within direct patient care settings, what does CNC stand for in the pharmaceutical industry? It signifies innovation and efficiency through precise manufacturing processes utilized in drug formulation equipment and packaging solutions. The pharmaceutical sector benefits greatly from Medical CNC Machining as it enables manufacturers to produce highly accurate components necessary for drug delivery systems.
CNC machines are instrumental in creating specialized equipment like tablet presses or filling machines where precision is paramount—any deviation could affect dosage accuracy or product safety significantly! Furthermore, these machines help streamline operations by producing parts faster than traditional methods while ensuring conformity with stringent regulatory standards common within pharmaceuticals.
Is there a future in CNC machining? Absolutely! As regulatory requirements continue evolving alongside technological advancements, we can expect an even greater reliance on precision-engineered components produced via advanced machining techniques throughout the pharmaceutical landscape.
Future Trends in CNC Machining
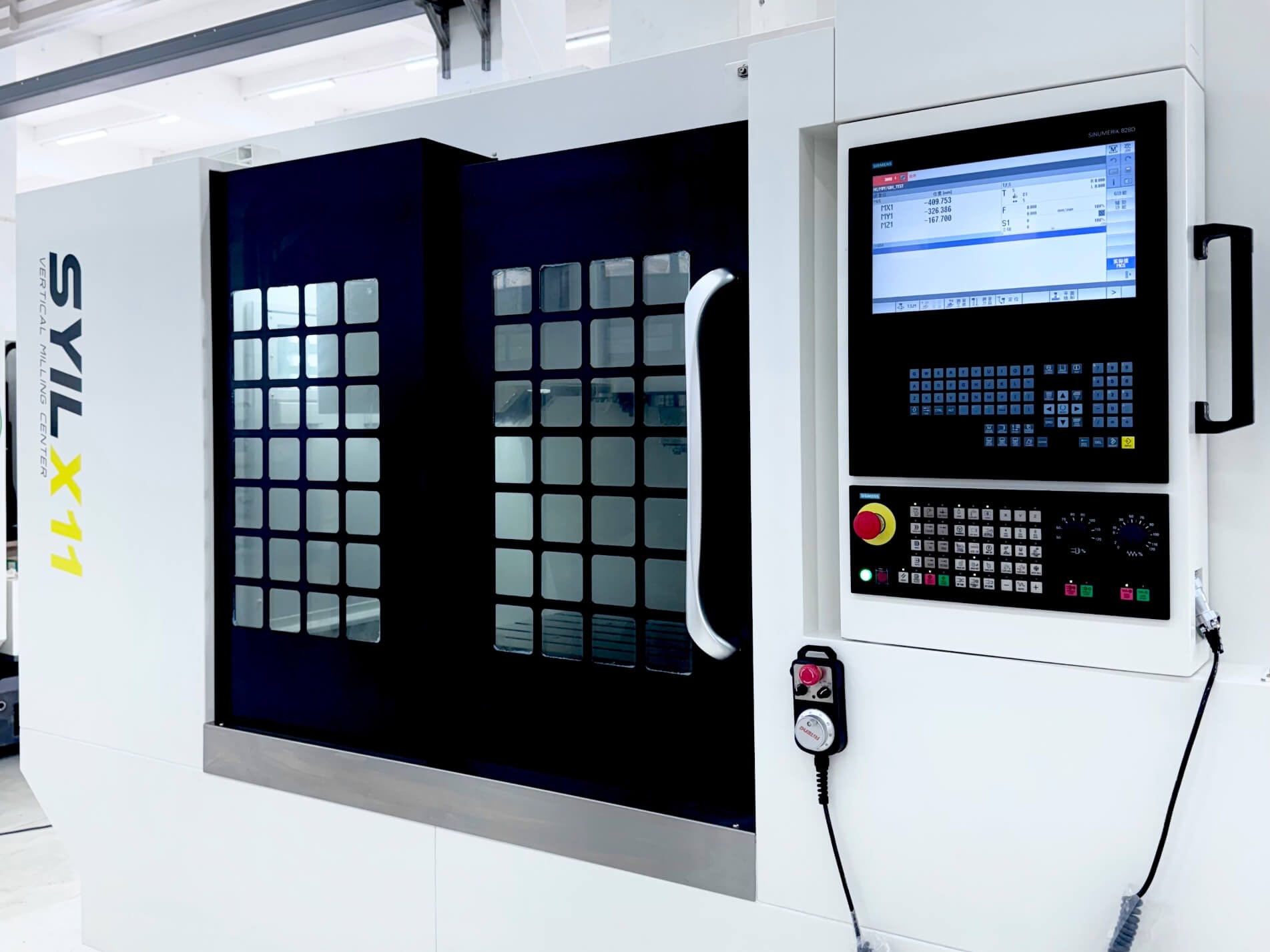
The landscape of CNC machining for the medical industry is evolving rapidly, driven by technological advancements and a growing demand for precision. With the integration of artificial intelligence and machine learning, CNC machines are becoming smarter, allowing for greater customization and efficiency in manufacturing. As healthcare continues to innovate, the future of CNC machining looks promising, poised to enhance patient care and outcomes.
Is there a future in CNC machining?
Absolutely! The future in CNC machining is not just bright; it's dazzling with potential. With increasing automation and the rise of Industry 4.0, which emphasizes interconnected machinery and smart manufacturing systems, we can expect to see even more sophisticated applications in medical settings. As healthcare demands higher precision and faster production times, CNC technology will undoubtedly play a critical role in meeting these needs.
Innovations driving the evolution of CNC technology
Several innovations are propelling the evolution of CNC technology forward. For instance, advancements in materials science have led to the development of biocompatible materials that can be efficiently machined using modern CNC techniques—essential for producing implants or devices that interact with human tissue. Additionally, improvements in software capabilities allow for more complex designs and simulations before actual production begins, ensuring that what does CNC stand for in healthcare truly embodies innovation.
How will CNC impact healthcare advancements?
CNC machining is set to revolutionize healthcare advancements significantly by facilitating rapid prototyping and personalized medicine solutions. Imagine custom implants tailored specifically to a patient's anatomy or surgical instruments designed with unique specifications—this is where Medical CNC Machining shines brightest! As we embrace these technologies, we can expect enhanced treatment options that improve patient outcomes while reducing costs across the board.
Conclusion
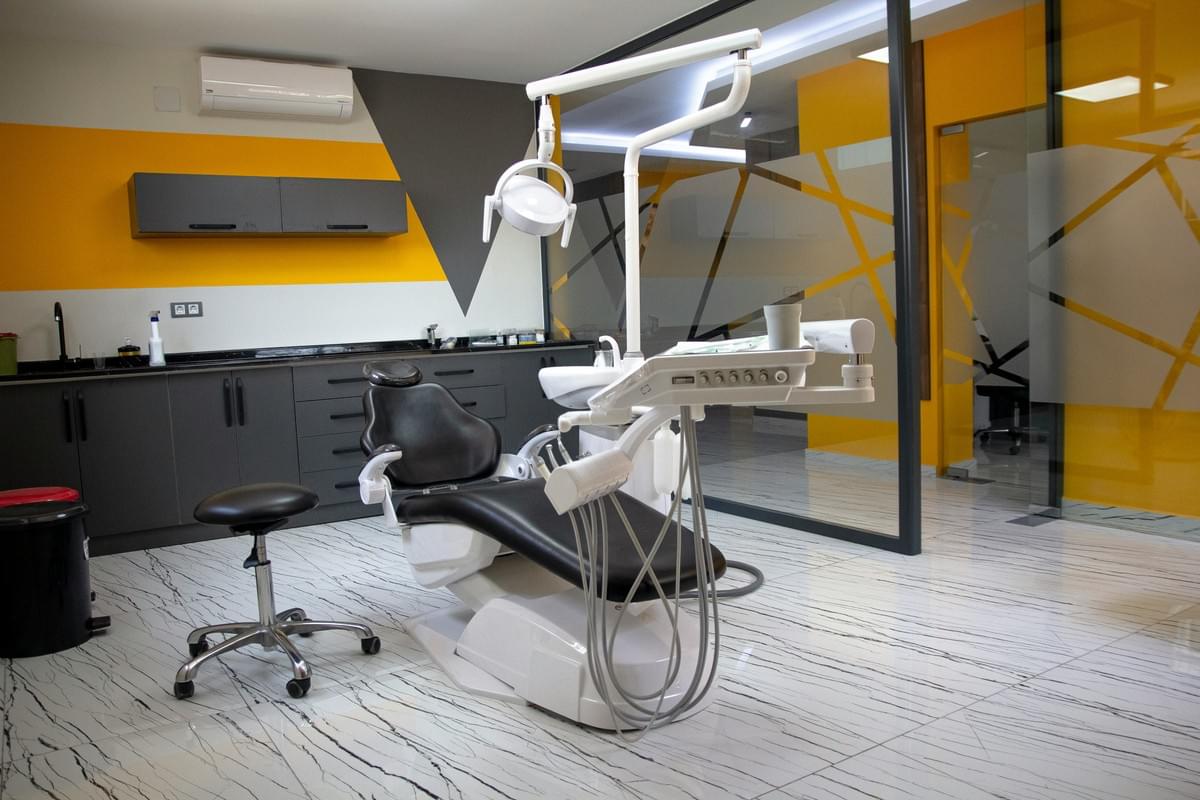
In the ever-evolving landscape of healthcare, the role of CNC machining for the medical industry cannot be overstated. Precision in medical devices is paramount; even the smallest deviation can have significant consequences for patient safety and treatment efficacy. As we look toward the future, it’s clear that CNC technology will continue to play a critical role in enhancing healthcare outcomes.
The significance of precision in medical devices
When we ask, What does CNC mean in healthcare? we're really delving into its core principle: unparalleled precision. Medical devices like implants and surgical instruments require meticulous accuracy to ensure they function as intended within the human body. With CNC machining, manufacturers can achieve tolerances that were once thought impossible, thus elevating patient care standards.
Precision also extends beyond just manufacturing; it encompasses design and testing phases as well. By utilizing advanced CNC machines, companies can produce prototypes with exact specifications, allowing for thorough testing before mass production begins. This iterative process not only minimizes risks but also enhances overall product reliability and safety.
CNC machining's role in the pharmaceutical landscape
So what does CNC stand for in the pharmaceutical industry? It's about more than just cutting metal; it's about creating solutions that improve lives through precision engineering. In pharmaceuticals, CNC machining is integral to producing high-quality equipment such as custom molds and components used in drug manufacturing processes.
The ability to manufacture intricate parts with high accuracy means that pharmaceutical companies can streamline their operations while adhering to stringent regulatory standards. This efficiency translates into faster production times and ultimately quicker access to essential medications for patients worldwide. Thus, CNC machining serves as a backbone for innovation within this critical sector.
Embracing the future of Medical CNC Machining
Is there a future in CNC machining? Absolutely! The advancements we are witnessing today are just a glimpse into what lies ahead—think AI integration, automation enhancements, and even biocompatible materials becoming commonplace in production processes. As healthcare demands grow more complex, so too will the capabilities of Medical CNC Machining evolve to meet these challenges head-on.
How are CNC machines used in industry? They’re not merely tools; they’re catalysts for change across various sectors including healthcare and pharmaceuticals alike. By embracing these innovations now, we set ourselves up for groundbreaking developments that will redefine how medical devices are designed and manufactured—ultimately leading to improved patient outcomes across the globe.