Introduction
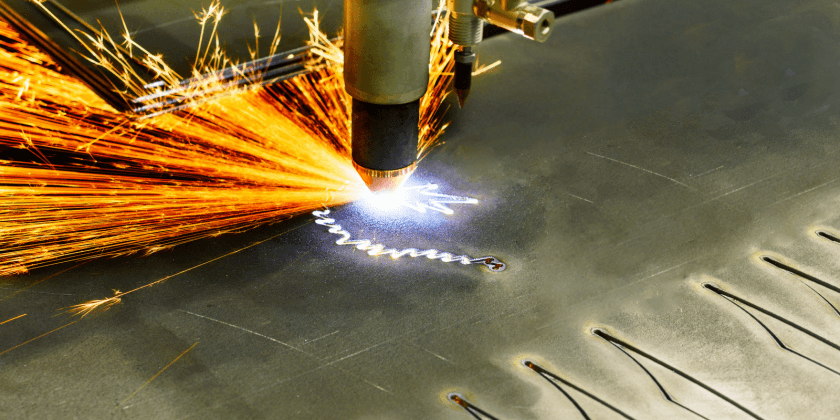
In the world of manufacturing and fabrication, two processes often come to the forefront: milling and welding. While both are essential for creating a variety of products, they serve distinctly different purposes. To truly appreciate their roles, it’s important to explain the difference between milling and welding—two techniques that are both foundational yet unique in their applications.
Understanding the Basics of Milling
Milling is a machining process that involves removing material from a workpiece using rotating cutters. This method allows for high precision in shaping metals, plastics, and even wood into intricate designs. Understanding what is milling in welding contexts can be crucial; while milling itself doesn’t join materials like welding does, it often prepares components that will be welded together later.
Unpacking the World of Welding
Welding is an essential fabrication technique used to join materials together through melting and re-solidifying them at their edges. Key techniques include arc welding, MIG welding, and TIG welding, each with its own unique advantages depending on the materials involved. When discussing what is the difference between welding and fabricating, it's vital to note that while all welds are fabrications, not all fabrications require welding; other methods may be employed based on project needs.
Key Applications in Industry
Both milling and welding have vast applications across various industries—from automotive to aerospace and even art installations. For instance, when we compare and contrast bronze and iron in these contexts, we see how each material's properties dictate whether milling or welding is more suitable for a specific project. In summary, understanding these differences enriches our knowledge about how products are made and highlights why knowing what is the main difference between turning and milling can also be significant for anyone involved in manufacturing.
What Is Milling?
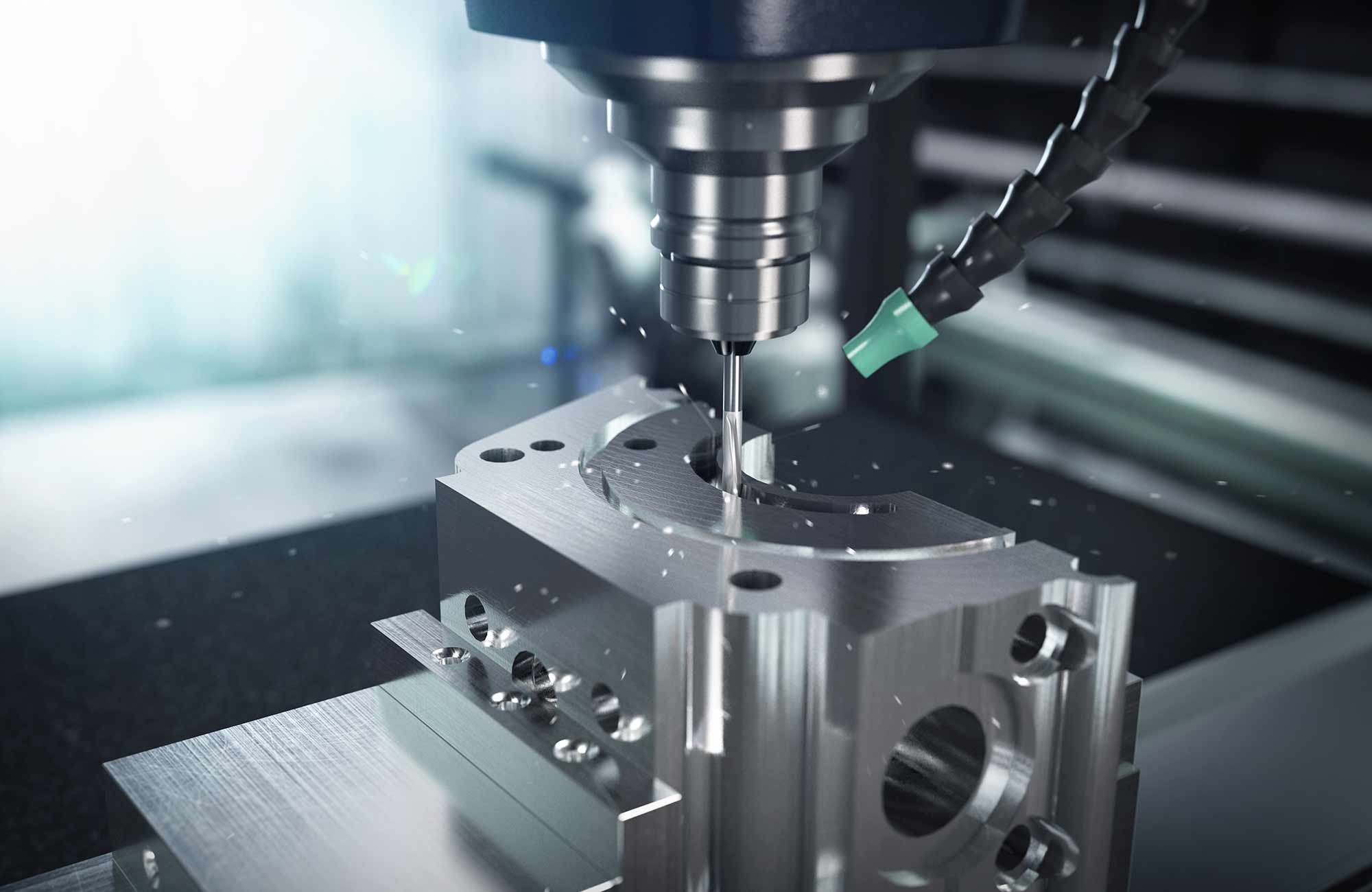
Milling is a fundamental machining process that involves removing material from a workpiece using rotary cutters. It's widely utilized in manufacturing to create precise shapes and features on various materials, including metals, plastics, and wood. Understanding what milling is can help clarify its distinction from other processes like welding.
Definition and Process Overview
At its core, milling is a subtractive manufacturing process that employs rotating tools to cut away material from a solid block or sheet. The workpiece is typically held securely on a machine bed while the cutter moves in multiple directions to achieve the desired shape. In contrast to welding, which fuses materials together, milling focuses on precision shaping and detailing of individual components.
When we explain the difference between milling and welding, we see that milling is all about cutting away material for intricate designs or parts while welding joins materials through heat and pressure. This distinction highlights the unique applications for each technique in various industries. By understanding these processes better, we can appreciate their roles in modern manufacturing.
Common Materials Used in Milling
Milling can be performed on an array of materials ranging from metals like aluminum and steel to softer materials such as plastics and wood. Each material presents different challenges; for instance, harder metals require more robust tooling and machinery settings compared to softer ones. As you explore what is milling in welding contexts, it's essential to recognize that while both processes may involve metalwork, they operate under entirely different principles.
The choice of material significantly affects the tooling used during the milling process—high-speed steel or carbide tools are common for metalwork applications due to their durability. Additionally, when comparing bronze and iron as potential milling materials, one must consider factors like machinability and finish quality; bronze often yields smoother finishes but may be more expensive than iron. Ultimately, selecting the right material for milling ensures optimal results tailored to specific project needs.
Applications Beyond Metalwork
While metalwork dominates the conversation around milling processes, this technique extends far beyond just shaping metals into parts or products. Industries such as woodworking utilize milling machines to craft intricate designs in furniture-making or cabinetry creation—showcasing how versatile this method truly is! From creating molds for casting processes to producing detailed prototypes for product development, milling has found its place across diverse sectors.
In addition to traditional uses in manufacturing environments, modern CNC (Computer Numerical Control) technology has revolutionized how we approach milling tasks today—enabling high levels of precision not achievable by manual methods alone! When considering what is the main difference between turning and milling? Turning focuses on rotating workpieces against stationary tools whereas milling involves fixed workpieces being shaped by moving cutters—a key distinction worth noting!
As you delve deeper into this subject matter with an understanding of both techniques' strengths—milling's precision versus welding's strength—you'll find yourself better equipped when navigating conversations around fabrication techniques within your field!
What Is Welding?
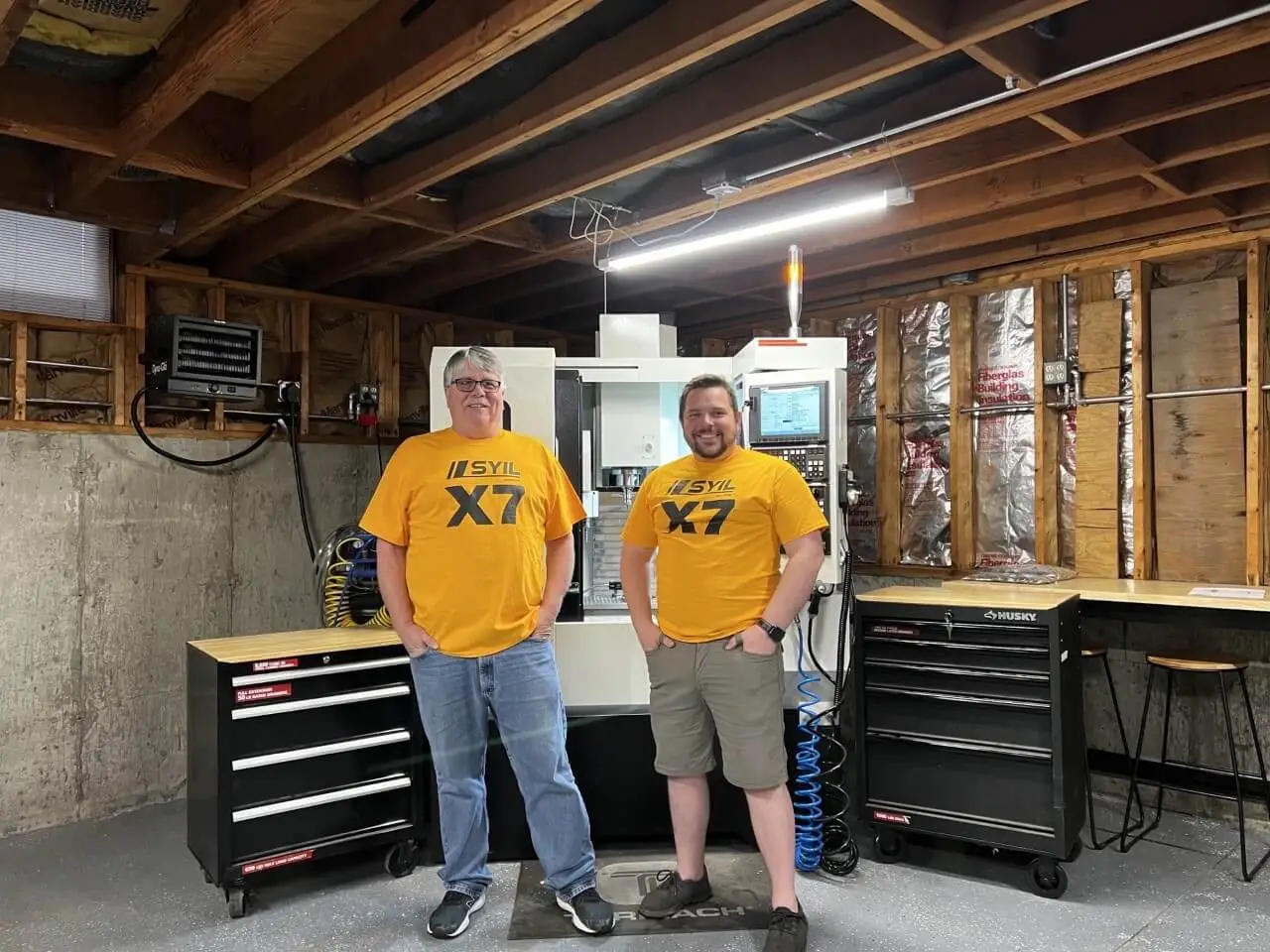
Welding is a fundamental manufacturing process that involves joining materials, typically metals or thermoplastics, by applying heat, pressure, or both. This technique creates a strong bond between the pieces being joined, making it essential in various industries. To fully grasp welding's significance, one must explore its key techniques and applications.
Definition and Key Techniques
At its core, welding is defined as the process of fusing materials together to form a permanent joint. The primary techniques used in welding include arc welding, MIG (Metal Inert Gas) welding, TIG (Tungsten Inert Gas) welding, and spot welding—each with unique applications and benefits. Understanding these techniques helps clarify what is milling in welding; while milling involves removing material to shape objects, welding focuses on joining them.
Types of Welding Processes
There are several types of welding processes that cater to different needs and materials. For instance, arc welding uses an electric arc to melt the base metal and filler material for a secure bond. On the other hand, MIG and TIG processes use inert gases to shield the weld area from contaminants—highlighting the difference between welding and fabricating as well; fabrication often includes additional processes like cutting or assembling parts before finalizing with welds.
Industries That Rely on Welding
Welding plays a vital role across numerous industries such as construction, automotive manufacturing, aerospace engineering, and shipbuilding. Each sector relies on specific techniques tailored to their unique demands—like using aluminum in aerospace versus steel in construction—which illustrates how diverse this field can be. Furthermore, understanding these industrial applications can help explain the difference between milling and welding; while milling shapes components through material removal, welding brings those components together into cohesive structures.
Comparing Milling and Welding Techniques
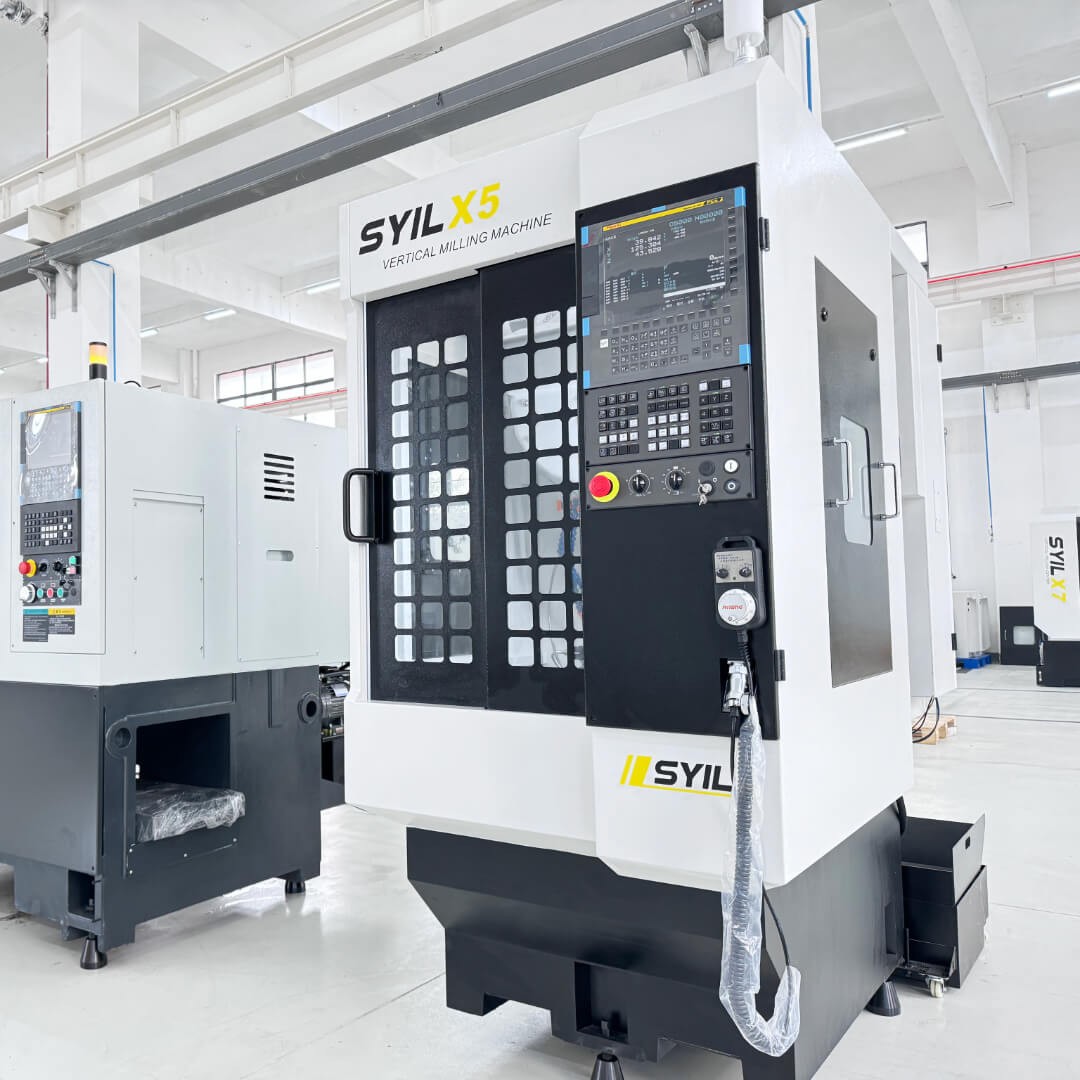
When it comes to manufacturing, milling and welding are two heavyweights that play crucial roles in shaping materials. While they may seem similar at first glance, understanding their core differences can significantly impact project outcomes. So let’s dive into the nitty-gritty of these techniques and explain the difference between milling and welding.
Core Differences in Processes
Milling is a subtractive manufacturing process that involves removing material from a workpiece using rotary cutters, while welding is a joining process that fuses materials together by melting them at high temperatures. In milling, the goal is to create precise shapes and dimensions, often resulting in intricate designs, whereas welding focuses on creating strong bonds between different pieces of metal or other materials. To put it simply: what is milling in welding? It’s not; they serve different purposes altogether!
One common question arises: what is the main difference between turning and milling? Turning involves rotating the workpiece against a stationary cutting tool, while milling rotates the cutting tool against a fixed workpiece. This distinction emphasizes how each technique approaches material manipulation differently.
Precision vs. Strength: A Breakdown
When comparing precision versus strength in these processes, it's essential to recognize their unique strengths and weaknesses. Milling excels in producing highly accurate parts with tight tolerances suitable for applications like aerospace components or intricate jewelry making—where every detail matters! On the flip side, welding provides superior strength by creating robust joints that can withstand immense forces, making it ideal for structural applications.
To further clarify this concept: what is the difference between welding and fabricating? Fabricating encompasses a broader range of processes—including cutting, bending, and assembling—that may involve both welding and other techniques to create final products. Thus, while welding focuses on joining materials together effectively, fabrication includes an entire suite of operations leading up to that point.
Common Mistakes in Both Techniques
Even seasoned professionals can make mistakes when working with either milling or welding techniques—often leading to costly errors! One common pitfall in milling involves not properly securing the workpiece; this can result in vibrations that compromise precision or even damage tools. Meanwhile, one mistake frequently seen in welding is improper heat settings; too much heat can lead to warping or burn-throughs.
For those looking for clarity on how these processes differ: explain the difference between milling and welding brainly will show you just how important understanding each technique's nuances can be! Additionally, when comparing bronze and iron applications within these contexts—bronze typically requires different machining strategies than iron due to its unique properties—it's vital to adapt your approach accordingly.
The Role of SYIL CNC Machines
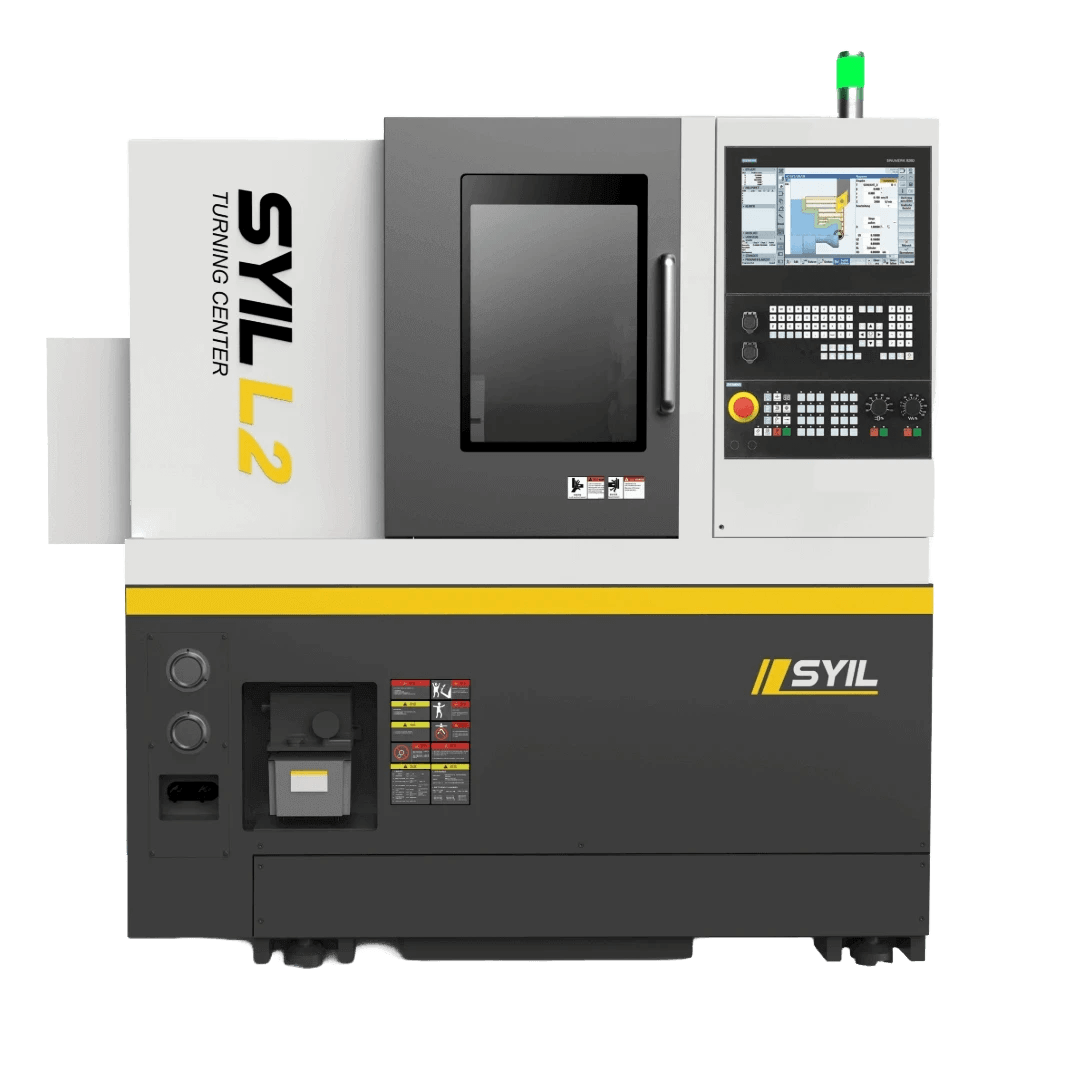
In the realm of modern manufacturing, SYIL CNC machines have carved out a niche that enhances both milling and welding processes. These advanced machines leverage computer numerical control (CNC) technology to bring unparalleled precision and efficiency to milling operations. By understanding how milling benefits from this technology, we can appreciate the significant impact it has on various industries.
How Milling Benefits from CNC Technology
CNC technology revolutionizes milling by automating the process, allowing for intricate designs and consistent results that would be challenging to achieve manually. This automation not only speeds up production but also minimizes human error, making it easier to maintain quality standards across batches. When comparing traditional methods with CNC milling, it's clear that precision is enhanced significantly—this is especially crucial when we explain the difference between milling and welding; while welding focuses on joining materials, milling shapes them with extreme accuracy.
Moreover, CNC milling provides flexibility in design modifications without the need for extensive retooling. This adaptability is essential in industries where rapid prototyping is key to staying competitive. By integrating CNC technology into their operations, businesses can streamline their workflows and respond quickly to market demands.
Precision in Prototyping and Jewelry Making
Milling's precision capabilities shine particularly in prototyping and jewelry making, where detail is paramount. For instance, when creating prototypes for new products or components, manufacturers rely heavily on accurate measurements and fine details—qualities that are hallmarks of SYIL CNC machines. In jewelry making, intricate designs can be milled from precious metals with such finesse that they rival hand-crafted pieces.
The ability to make micro-adjustments during the machining process allows jewelers to experiment with different styles without committing extensive resources upfront. This leads us back to understanding what is milling in welding; while welding joins pieces together at high temperatures for strength, milling carves out specific shapes with meticulous detail—a vital distinction for artisans aiming for perfection in their craft.
Additionally, this level of precision opens doors for unique applications beyond typical manufacturing scenarios—think custom-designed tools or bespoke jewelry pieces that reflect personal style rather than mass production standards.
Real-World Applications of SYIL X5
The SYIL X5 model showcases how advanced features translate into practical applications across various sectors—from aerospace engineering to creative arts like sculpture fabrication. In aerospace manufacturing, components must meet stringent safety regulations; hence using a machine like the SYIL X5 ensures parts are manufactured within exact specifications every time—a critical factor when we discuss what is the main difference between turning and milling: turning involves rotating material against a stationary tool while milling uses a rotating tool against stationary material.
In addition to aerospace applications, artists have begun utilizing these machines for fabricating sculptures from materials like bronze or iron—each requiring different techniques depending on their properties which leads us into our next topic: what is the difference between welding and fabricating? While welding refers specifically to joining materials through melting processes at high temperatures, fabricating encompasses a broader range of techniques including cutting and assembling metal structures where precision plays an equally vital role as strength does.
Understanding these distinctions helps illustrate how technologies like those found in SYIL machines enhance both creative endeavors and industrial applications alike—creating a bridge between artistry and engineering excellence.
Everyday Examples That Highlight Differences
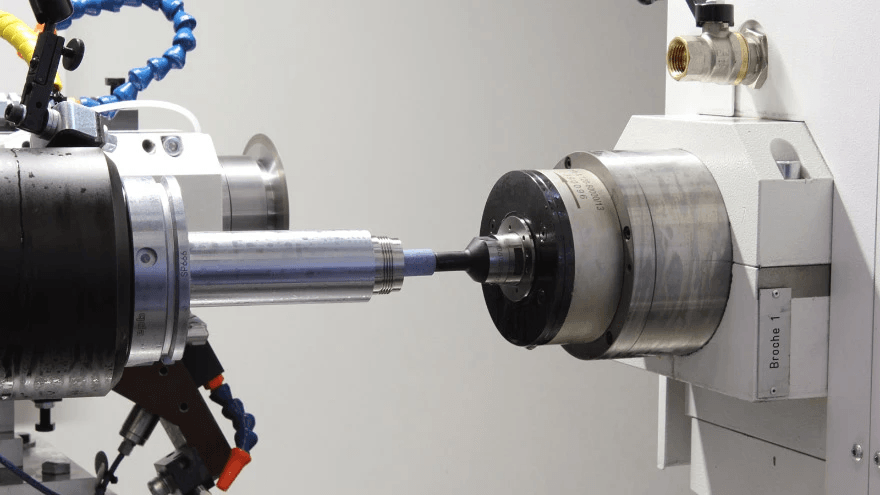
When diving into the practical applications of milling and welding, it's clear that both techniques serve unique purposes across various industries. From creating precision components in manufacturing to crafting intricate art pieces, the versatility of these processes is remarkable. Understanding how they differ can help one appreciate their respective roles in everyday life.
From Manufacturing to Art: Practical Uses
Milling is often associated with precision manufacturing, where it shapes materials like metal and wood into specific designs, making it essential for industries such as aerospace and automotive. Conversely, welding is frequently used in construction and repair work, joining materials together to form strong structures or artistic installations. The difference between milling and welding becomes particularly evident when you consider that milling removes material to create a part, while welding fuses materials together—each technique serving its own purpose in both functional and aesthetic contexts.
What is the Difference Between Welding and Fabricating?
While welding involves joining materials through heat and pressure, fabricating encompasses a broader range of processes including cutting, bending, and assembling parts. Essentially, fabricating can include welding as one of its techniques but extends beyond it to include various methods for creating finished products from raw materials. Therefore, when we explain the difference between milling and welding within the context of fabrication, it's crucial to note that milling focuses on shaping material by removing excess material rather than joining parts together like welding does.
A Look at Bronze and Iron Applications
Bronze and iron are two metals commonly used in both milling and welding applications but with distinct characteristics that affect their processing methods. Bronze is often milled due to its excellent machinability; it produces smooth finishes ideal for decorative items or intricate components like gears or jewelry pieces. On the other hand, iron is frequently welded because of its strength; understanding what is the main difference between turning and milling further emphasizes how turning can also shape iron while retaining its robust properties during fabrication processes.
Conclusion
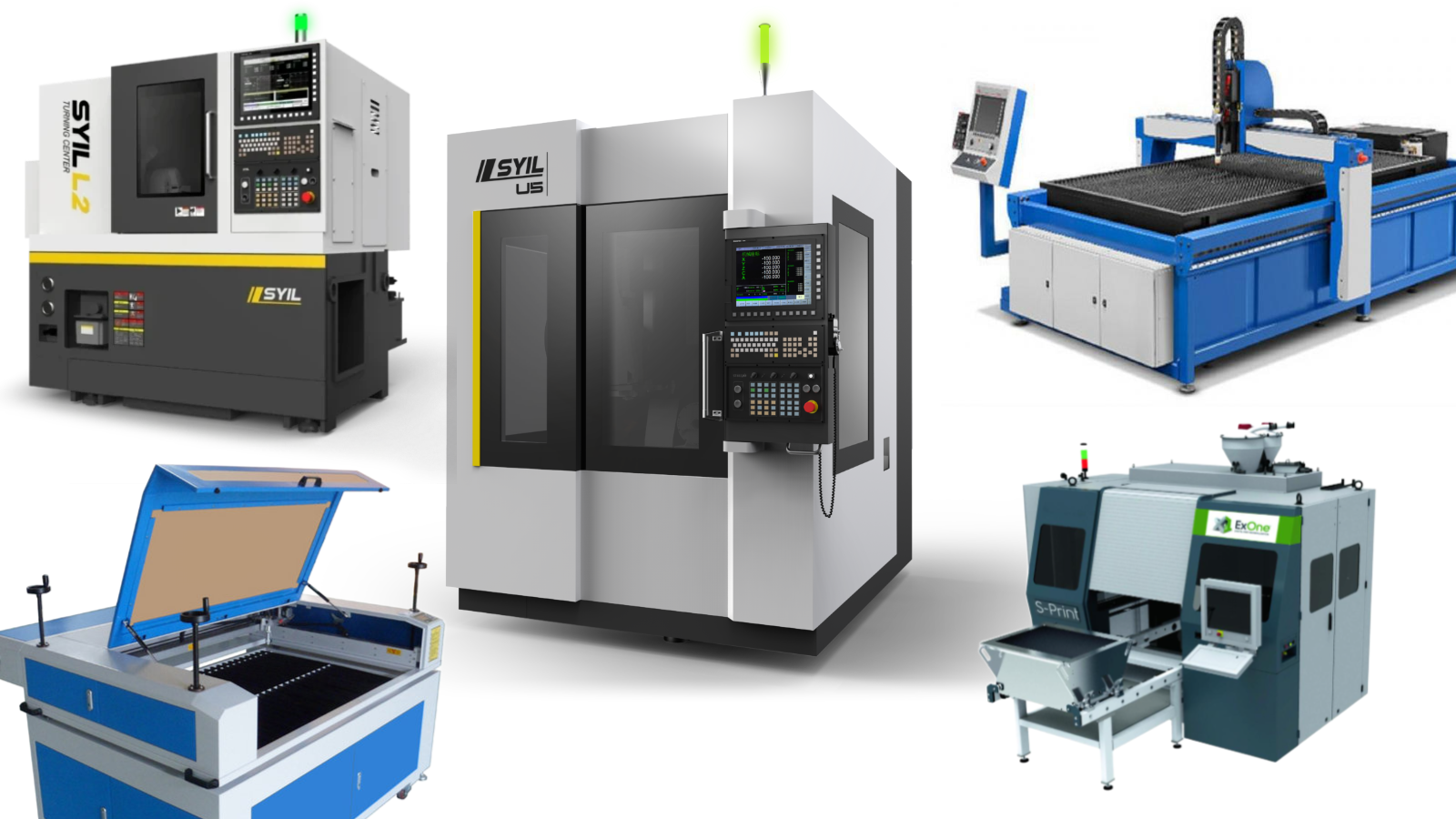
As we wrap up our exploration of milling and welding, it's essential to understand their unique characteristics and applications. Milling is primarily a subtractive manufacturing process that shapes materials by removing excess material, while welding is a joining technique that fuses materials together through heat. Knowing how to explain the difference between milling and welding can significantly impact project outcomes in various industries.
Key Takeaways on Milling and Welding
One of the key takeaways is that milling focuses on precision and detail, making it ideal for creating intricate designs or prototypes. In contrast, welding emphasizes strength and durability, essential for constructing robust structures or machinery. When you ask, What is the main difference between turning and milling? it's important to note that turning involves rotating the workpiece against a cutting tool, while milling uses a stationary workpiece with a rotating tool.
Practical Implications for Industries
The practical implications of understanding these techniques are vast; industries ranging from automotive to aerospace rely heavily on both processes for manufacturing components. For instance, knowing what is milling in welding can help engineers determine when to use each method based on material type and desired strength. Furthermore, when discussing what is the difference between welding and fabricating?, it becomes clear that fabrication encompasses more than just joining materials; it includes cutting, shaping, and assembling parts into finished products.
Future Trends in Machining and Fabrication
Looking ahead, future trends in machining and fabrication are leaning toward automation and smart technologies like CNC machines to enhance precision in both milling and welding processes. Innovations will continue to blur the lines between traditional methods as we explore new materials such as advanced alloys or composites—compare and contrast bronze and iron for instance—to find optimal solutions for specific applications. As industries evolve, being able to explain the difference between milling and welding will remain crucial for professionals seeking efficiency in production.