Introduction
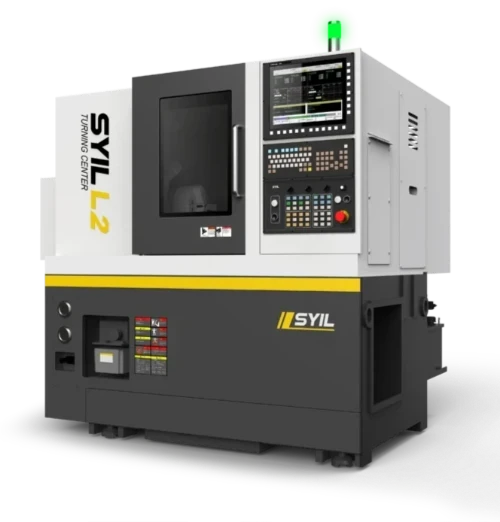
Welcome to the ultimate guide on how machining spindles can revolutionize your productivity! Whether you're in the CNC machining industry or working with a lathe spindle, understanding the power and potential of spindles is crucial for boosting efficiency and achieving outstanding results.
At SYIL Machine Tools, we specialize in developing and manufacturing precision CNC machines for milling and drilling. With over 12k machines supplied globally, we prioritize quality and sustainability. Today, we'll explore how machining spindles can take your productivity to new heights.
Boost Your Productivity with Machining Spindles: The Complete Guide
In this comprehensive guide, we'll delve into everything you need to know about machining spindles – from their definition to their role in various industries. We'll uncover the secrets behind maximizing efficiency, enhancing precision, increasing speed, and optimizing performance through the use of these powerful tools.
Increase Efficiency and Results with Machining Spindles
Efficiency is the backbone of any successful business. By incorporating machining spindles into your operations, you can streamline processes, reduce downtime, and achieve higher output levels than ever before. We'll explore real-life success stories of businesses that have harnessed the power of spindles to increase their efficiency and deliver exceptional results.
Discover the Power of Machining Spindles for Enhanced Productivity
Unleash your full potential with machining spindles! These remarkable devices offer unmatched power and precision that can transform your production capabilities. Throughout this guide, we'll uncover how investing in machining spindles can lead to long-term success and growth for your business.
Understanding Machining Spindles
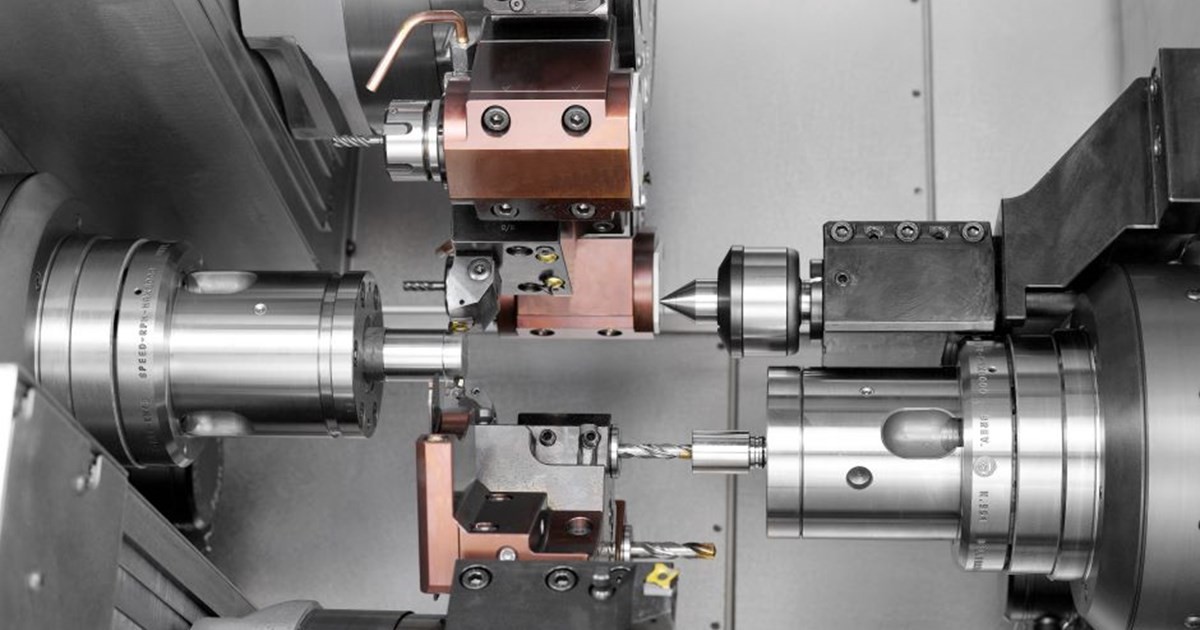
Machining spindles are essential components in CNC machines, such as lathes and milling machines, enabling cutting tools to rotate at high speeds. They consist of a rotating shaft, known as the spindle, which holds the cutting tool securely in place. A motor drives the spindle and provides the necessary power and rotational speed for precision machining operations.
What are Machining Spindles and How Do They Work?
Machining spindles play a crucial role in CNC machining by providing the rotational motion required to cut through various materials with precision. The spindle is mounted on bearings, allowing it to rotate smoothly and with minimal friction. It is typically driven by an electric motor that provides the necessary power to rotate the spindle at high speeds.
The cutting tool, such as an end mill or drill bit, is securely attached to the spindle using a tool holder or collet. As the spindle rotates, it transfers its rotational motion to the cutting tool, allowing it to remove material from the workpiece. This process enables precise shaping, drilling, and milling operations to be accurately performed.
The Different Types of Machining Spindles Explained
There are several types of machining spindles available, each designed for specific applications and requirements. Some common types include belt-driven spindles, direct-drive spindles, air turbine spindles, and electric motor spindles.
- Belt-driven spindles use belts or pulleys to transfer power from an external motor to the spindle. This type of spindle offers flexibility in speed control but may have limitations in maximum speed and torque.
- Direct-drive spindles eliminate the need for belts or pulleys by directly coupling the motor to the spindle shaft. This design provides high torque at low speeds while maintaining accuracy and reliability.
- Air turbine spindles utilize compressed air to drive the spindle, making them ideal for high-speed applications. They are known for compact size, low vibration, and high rotational speeds.
- Electric motor spindles combine an electric motor and a built-in spindle into a single unit. This design offers precise control over speed and torque, making it suitable for various machining operations.
Benefits of Using Machining Spindles in Various Industries
Machining spindles offer numerous benefits across various industries. In the automotive industry, they are used for precision drilling and milling operations to manufacture engine components and body parts. In the aerospace industry, machining spindles enable the production of intricate parts with tight tolerances.
The medical industry relies on machining spindles to manufacture surgical instruments, prosthetics, and dental implants. These spindles ensure precise cutting and shaping of medical devices to meet strict quality standards.
The electronics industry utilizes machining spindles for PCB drilling and milling processes. They enable manufacturers to produce intricate circuit boards with high precision and accuracy.
Choosing the Right Machining Spindle for Your Needs
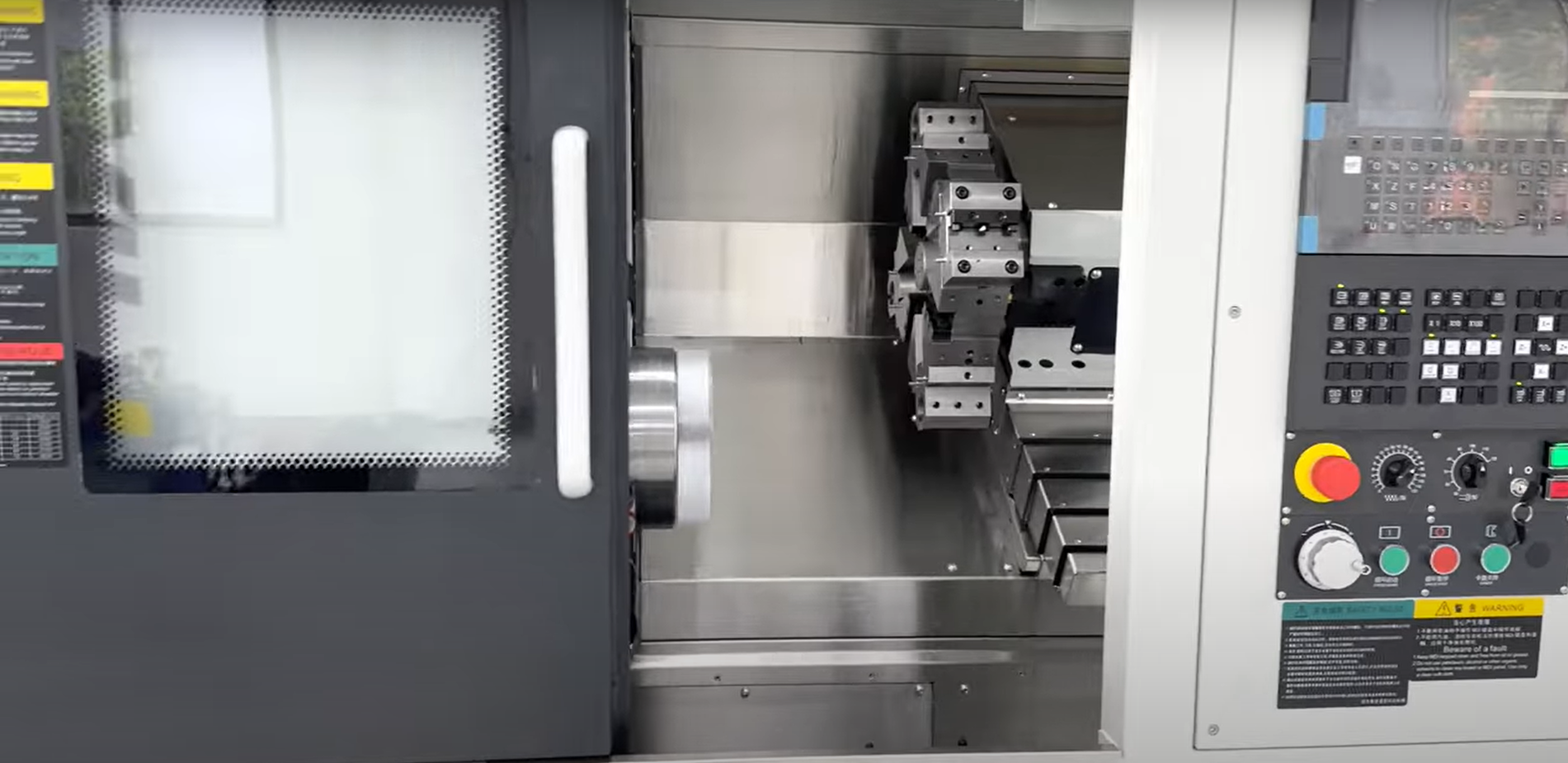
When it comes to selecting the perfect machining spindle for your needs, several important factors must be considered. First and foremost, you need to evaluate the specific requirements of your machining tasks. Consider the materials you will be working with, the desired precision and accuracy, and the required speed and throughput. By understanding these factors, you can narrow your options and find a spindle that will meet your unique needs.
Once you have identified your requirements, it's time to explore different machining spindle options. Various types of spindles are available on the market, each designed for specific applications. For example, CNC spindles are ideal for computer numerical control machines that require high-speed rotation and precise cutting. Lathe spindles, on the other hand, are specifically designed for turning operations.
SYIL Machine Tools offers a wide range of precision CNC machines equipped with different machining spindles to suit your needs. Their machines are known for their quality and sustainability, making them an excellent choice for businesses looking to enhance their productivity.
Let's examine some case studies to understand how choosing the right machining spindle can benefit businesses. Company A struggled with low production speeds and inconsistent quality control until it invested in a high-performance machining spindle from SYIL Machine Tools. The new spindle allowed it to achieve faster production speeds while maintaining superior precision and accuracy.
Company B faced similar challenges but opted for a different type of machining spindle that was better suited to its specific requirements. With this new spindle in place, it was able to significantly increase its throughput without compromising on quality.
By carefully considering factors such as material compatibility, precision requirements, and speed capabilities and exploring different options available in the market, like those offered by SYIL Machine Tools, businesses can choose a machining spindle that perfectly meets their needs.
Optimizing Performance with Machining Spindles
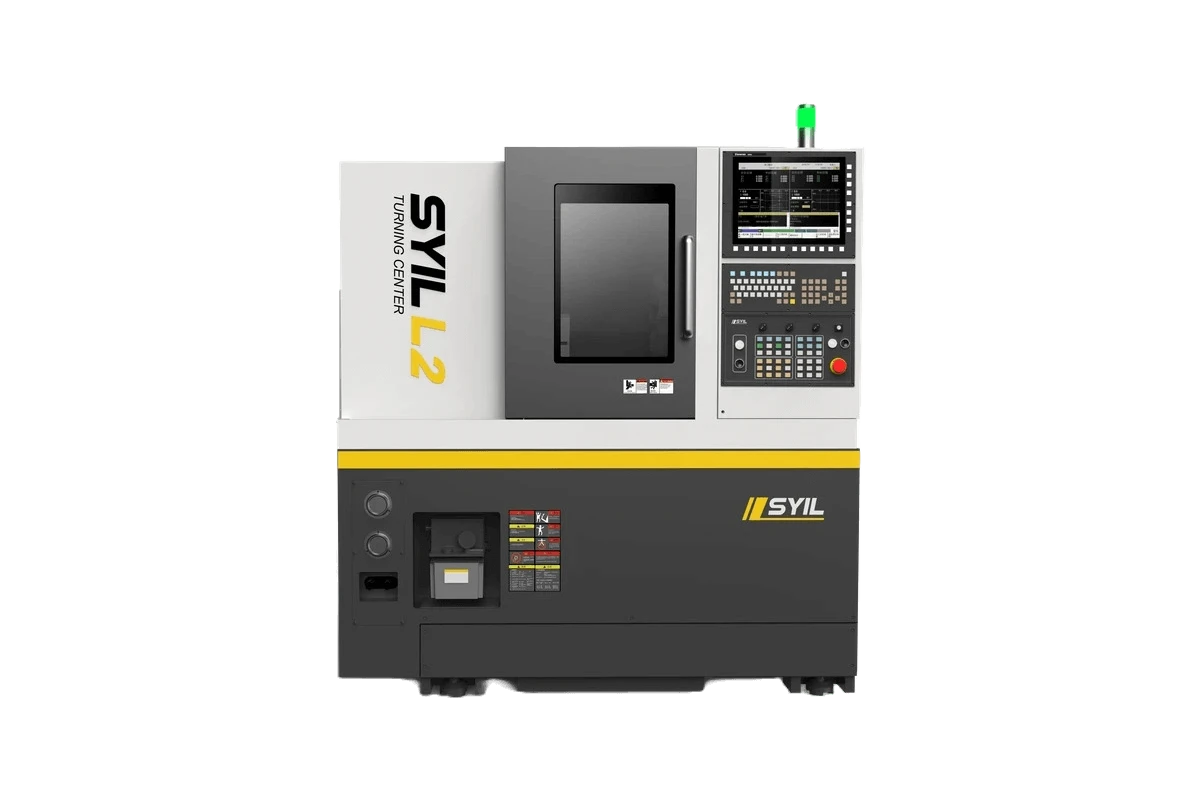
Machining spindles are essential in the manufacturing industry, enabling businesses to achieve maximum efficiency and productivity. By implementing various techniques, businesses can optimize the performance of their machining spindles and reap numerous benefits.
Techniques for Maximizing Efficiency with Machining Spindles
Machining spindles are the heart of any CNC machine, and their efficiency directly impacts production output. Here are several key techniques to maximize spindle efficiency:
- Maintain a Clean and Lubricated Spindle: Regularly clean the spindle to remove debris and contaminants that can hinder performance. Proper lubrication of moving parts reduces friction and extends spindle life.
- Utilize High-Quality Tooling: Invest in precision cutting tools that match your spindle's capabilities. This ensures optimal performance, minimizes tool wear, and extends the lifespan of both the spindle and tools' lifespan.
- Implement Advanced Programming Techniques: Utilize adaptive control systems that adjust cutting parameters based on real-time data. This allows for optimized tool paths and significantly reduces cycle times, boosting overall machining efficiency.
By following these techniques, you can ensure your machining spindles operate at peak performance, leading to increased productivity and reduced downtime.
Tips for Maintaining and Extending the Lifespan of Machining Spindles
Proper maintenance is vital for extending the lifespan of machining spindles. Inspecting and replacing worn-out components such as bearings or belts will prevent unexpected breakdowns and costly repairs.
Additionally, monitoring operating conditions such as temperature and vibration levels can help identify potential issues before they escalate into major problems. Implementing condition monitoring systems enables businesses to address any abnormalities that may arise proactively.
It is also essential to follow manufacturer guidelines regarding operating speeds, feed rates, and coolant usage to prevent excessive wear on the spindle components.
Real-Life Success Stories: How Machining Spindles Have Transformed Businesses
SYIL Machine Tools has witnessed numerous success stories where businesses have experienced remarkable transformations after implementing machining spindles into their operations.
One notable example is a precision engineering company that struggled with low productivity due to outdated equipment. By investing in SYIL's CNC machine with a high-performance spindle, they could significantly increase their production output and achieve superior accuracy. As a result, they gained a competitive edge in the market and witnessed substantial growth.
Another success story involves a manufacturing company that specializes in producing complex components for the aerospace industry. By utilizing advanced machining spindles with innovative features, they could reduce cycle times by 30% while maintaining exceptional precision. This allowed them to meet tight deadlines and secure lucrative contracts, leading to substantial profitability.
By implementing these techniques, tips, and real-life success stories, businesses can harness the power of machining spindles to optimize performance, extend lifespan, and transform their operations. With SYIL Machine Tools' precision CNC machines and state-of-the-art spindles, businesses can achieve unparalleled efficiency and productivity for long-term success and growth.
Enhancing Precision and Accuracy with Machining Spindles
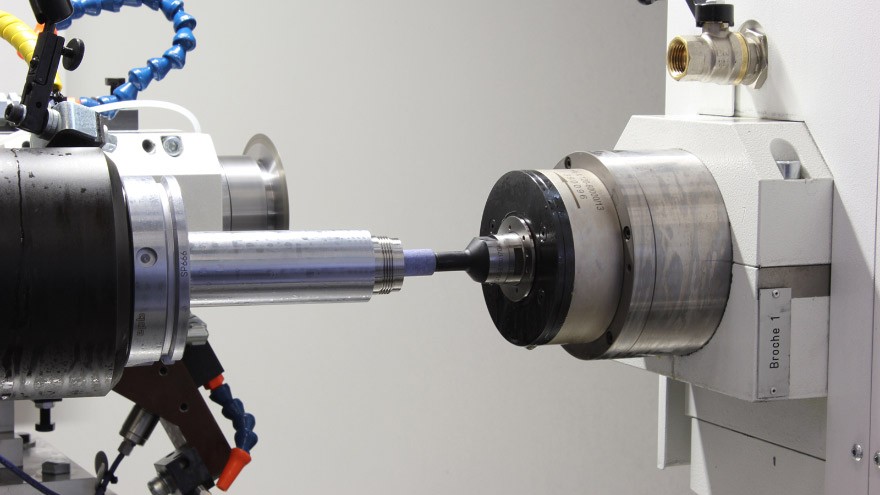
Machining spindles plays a crucial role in achieving precision in various industries. These powerful components rotate cutting tools, such as drills or end mills, at high speeds to remove material from workpieces with accuracy. Spindles ensure precise cuts and measurements by providing the necessary rotational force and stability.
Modern machining spindles have advanced features and technologies that further enhance precision and accuracy. For example, some spindles have built-in sensors that monitor real-time temperature, vibration, and tool wear. This data allows operators to adjust and maintain optimal cutting conditions for consistent precision throughout the machining process.
Additionally, many spindles now incorporate high-speed capabilities, allowing for faster feed rates without sacrificing accuracy. These high-speed spindles can reach rotational speeds of up to 30,000 RPM or more, enabling rapid material removal while still maintaining precise cuts.
One notable case study in the automotive industry showcases how machining spindles have improved quality control. A leading car manufacturer implemented high-precision spindles in its production line to ensure accurate drilling of engine components. The use of these spindles reduced errors and improved overall product quality.
Increasing Speed and Throughput with Machining Spindles
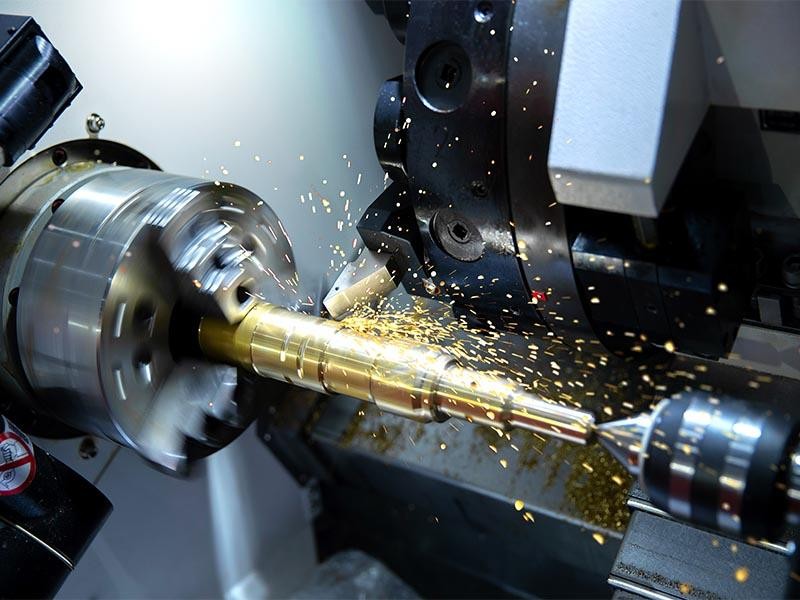
Machining spindles is crucial to boosting production speed and enhancing throughput in various industries. With their high-speed rotation and precision, these spindles enable manufacturers to achieve faster and more efficient manufacturing processes. By harnessing the power of machining spindles, businesses can significantly increase their productivity and stay ahead of the competition.
How Machining Spindles Boost Production Speed
Machining spindles are designed to rotate at high speeds, allowing for rapid material removal during the machining process. This increased rotation speed translates into faster cutting and milling times, ultimately reducing production time and increasing overall speed.
By utilizing CNC spindles, which are computer-controlled, manufacturers can program precise cutting paths and optimize tool movements for maximum efficiency. This automation eliminates human error and ensures consistent high-speed performance.
Furthermore, SYIL's CNC machines have advanced spindle technology that offers variable speed control. This feature allows operators to adjust the spindle's rotational speed according to the specific requirements of each machining task, further enhancing production speed while maintaining accuracy.
Innovative Strategies for Accelerating Manufacturing Processes
In addition to high-speed rotation, several innovative strategies can be employed to accelerate manufacturing processes with machining spindles.
One such strategy is the use of multi-spindle machines. These machines feature multiple independent spindles that simultaneously perform different workpiece operations. Manufacturers can significantly reduce cycle times and increase throughput by dividing tasks among multiple spindles.
Another strategy is implementing high-speed machining techniques. This involves using specialized tooling and cutting parameters to maximize material removal rates while maintaining surface quality. With the right combination of tools, feeds, speeds, and coolant systems, manufacturers can achieve remarkable time savings without compromising on precision or quality.
Success Stories: How Machining Spindles Have Revolutionized Production
SYIL Machine Tools has witnessed numerous success stories where machining spindles have revolutionized production processes. One example is a company that used SYIL's CNC machine with a powerful spindle to manufacture intricate aerospace components. The spindle's high-speed rotation allowed for quick and precise material removal, resulting in significantly reduced manufacturing time and increased productivity.
Another success story involves an automotive manufacturer. By implementing SYIL's lathe spindle technology, they achieved faster turning speeds and optimized their production line. This led to a substantial increase in throughput, allowing them to meet growing customer demands while maintaining exceptional quality standards.
Conclusion
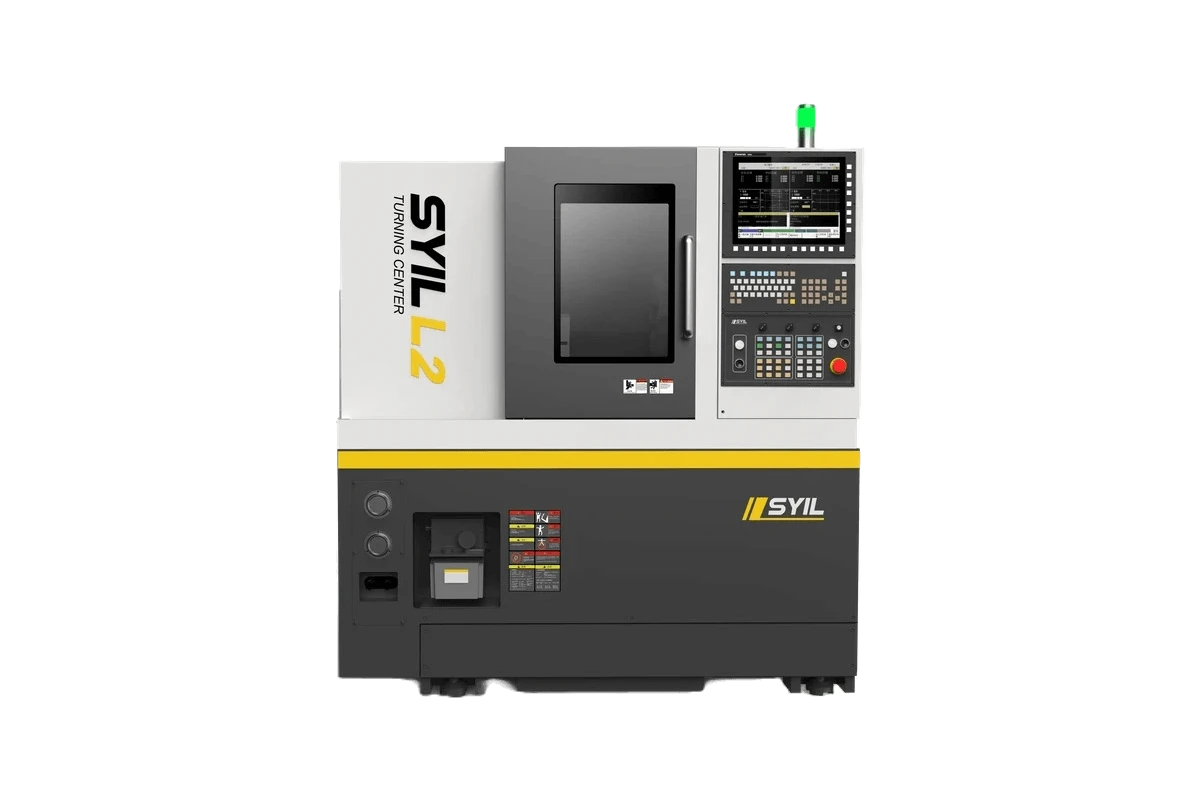
Investing in machining spindles is a game-changer for businesses looking to boost productivity and efficiency. With the power of machining spindles, you can take your productivity to the next level and achieve unparalleled efficiency in your operations. SYIL Machine Tools, a leading manufacturer of precision CNC machines, offers top-quality machining spindles that can revolutionize your manufacturing processes.
By understanding what a spindle is and how it works, you can harness its power to enhance precision, increase speed and throughput, and optimize overall performance. Whether you need a CNC spindle for milling or a lathe spindle for drilling, SYIL has covered you with their reliable and high-performing machines.
Investing in machining spindles is an investment in long-term success and growth. The benefits are undeniable, as seen in real-life success stories from various industries. You can transform your business operations by carefully selecting the right machining spindle for your needs and implementing techniques to maximize efficiency.
So why wait? Take advantage of the power of machining spindles today and elevate your productivity. With SYIL Machine Tools by your side, you can trust in their expertise and commitment to quality and sustainability.