Introduction
Using a milling machine offers numerous benefits for both professionals and hobbyists.
- It enables precise and accurate cuts, ensuring high-quality results.
- Milling machines provide versatility regarding material compatibility, allowing users to work with metals, plastics, wood, and more.
- They offer increased productivity by automating certain processes and reducing manual labor.
This beginner's guide provides comprehensive information on how to use a milling machine effectively. Whether new to machining or looking to enhance your skills, this guide covers everything from setup to advanced techniques. By following this guide, you will gain the knowledge needed to operate a milling machine safely and efficiently.
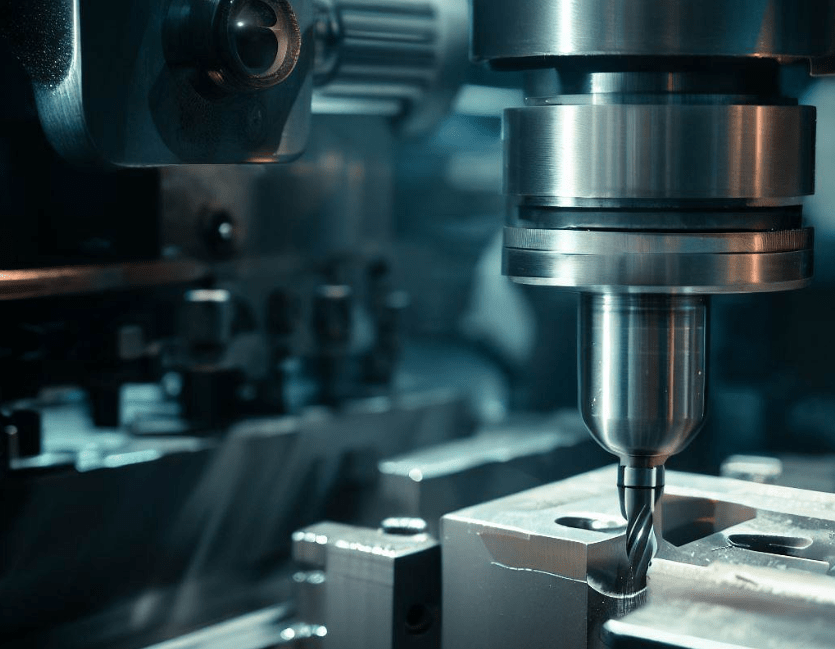
Getting Started with a Milling Machine
Milling machines are versatile tools used in various industries for cutting and shaping solid materials. Before diving into milling, it's important to understand the different types of machines available.
Understanding the Different Types of Milling Machines
There are several types of milling machines, each designed for specific purposes.
- One common type is the vertical milling machine, which has a vertically oriented spindle and can perform tasks such as face milling, end milling, and drilling.
- Another type is the horizontal milling machine, which has a horizontally oriented spindle and is ideal for heavier cutting operations.
For those looking for precision engineering, there are CNC (Computer Numerical Control) milling machines available. These machines use computer-aided design (CAD) software to control the cutting process with high accuracy and repeatability.
Overview of the Basic Components Of A Milling Machine
To understand how a milling machine works, it's important to familiarize yourself with its basic components. The main parts include:
- Spindle: This rotating component holds the cutting tool and performs the actual cutting operation.
- Table: The workpiece is placed on this flat surface and secured during machining.
- Knee: This adjustable vertical component supports the table and adjusts the height.
- Saddle: It moves along the knee and supports other components like the table.
- Column: This vertical support structure houses various mechanisms and controls.
- Power feed mechanism: It enables the workpiece's or cutting tool's automatic movement in different directions.
Understanding these components will help you navigate a milling machine more effectively.
SYIL Milling Machine Models and Features
SYIL Machine Tools develops and manufactures precision CNC machines for milling and drilling. With over 12,000+ machines supplied globally, they prioritize quality and sustainability. Operating in multiple countries, SYIL is becoming a recognized brand in the industry.
SYIL offers a range of milling machine models, each designed to cater to different needs and budgets. Their machines are known for their robust construction, high precision, and user-friendly interface. Whether you're a beginner or an experienced machinist, SYIL has a milling machine that suits your requirements.
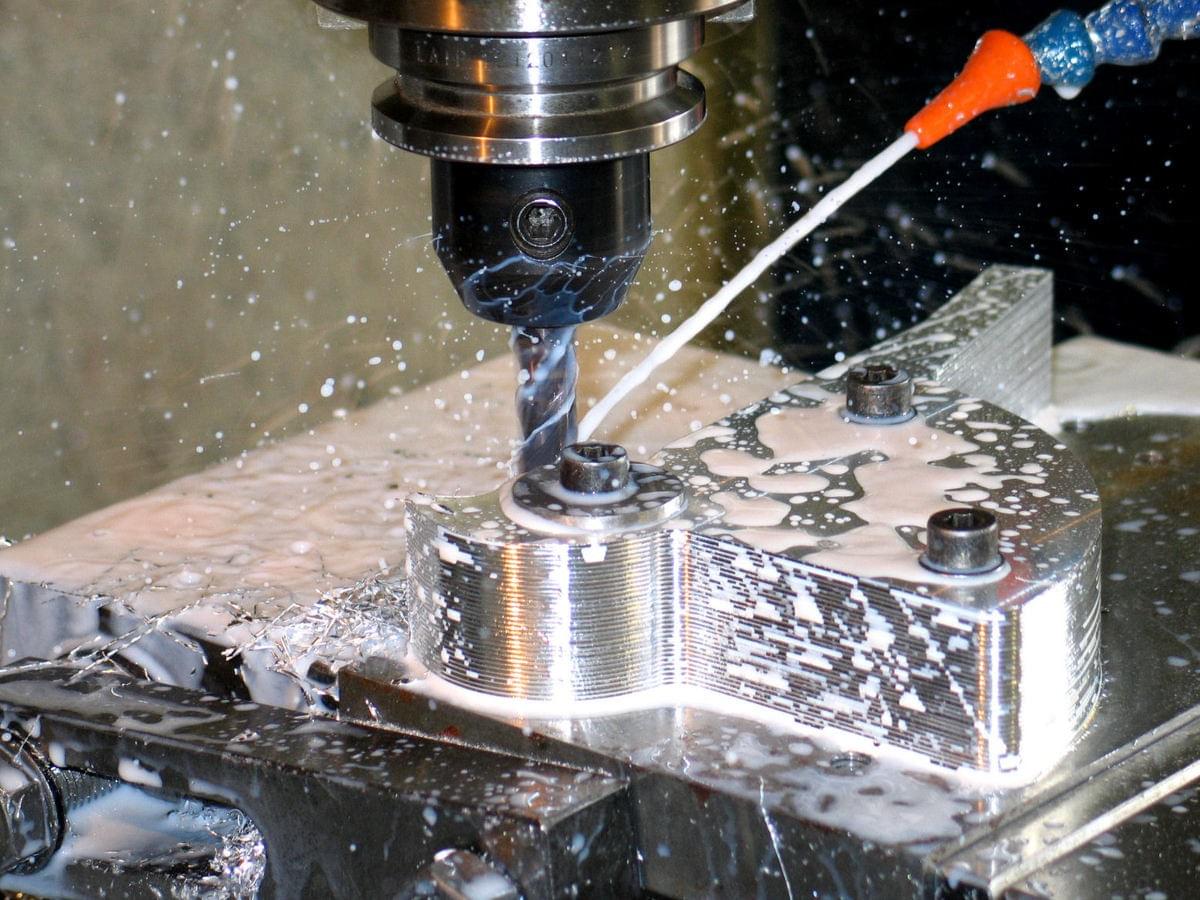
Setting Up the Milling Machine
Setting up a milling machine is an essential step before you can start using it for your machining projects. In this section, we will guide you through choosing the right location, assembling the machine, adjusting and aligning its components, and understanding the necessary tools for setup.
Choosing the Right Location for Your Milling Machine
When selecting a location for your milling machine, it is crucial to consider factors such as space availability, stability of the surface, and accessibility to power sources. You want to ensure enough room around the machine for easy movement and operation. Additionally, a level and sturdy surface is necessary to prevent vibrations affecting precision during milling.
Step-by-Step Guide to Assembling the Milling Machine
Although assembling a milling machine may initially seem daunting, it can be straightforward with proper guidance.
- Begin by unpacking all the components carefully and organizing them according to their respective sections in the instruction manual provided by SYIL Machine Tools.
- Follow each step diligently, from attaching the base to mounting the table and securing all other major components such as the spindle head and motor.
- Pay close attention to any instructions or precautions mentioned in the manual to ensure accurate assembly.
Adjusting and Aligning the Milling Machine Components
Once you have assembled your milling machine, it is crucial to adjust and align its various components properly. This step ensures that everything is in perfect alignment for precise machining operations.
Start by checking if all axes are perpendicular or parallel as required for your specific machining needs. Use precision measuring tools like dial indicators or laser alignment systems recommended by SYIL Machine Tools for accurate adjustments.
Next, focus on aligning the worktable with respect to both X-axis (longitudinal) and Y-axis (cross) movements. This alignment plays a vital role in achieving accurate cuts during milling operations.

Operating a Milling Machine
Milling machines are versatile tools that can perform a wide range of operations, making them essential in various industries. In this section, we will explore the basic operations of a milling machine, understand the different types of milling cutters and their uses, provide a step-by-step guide to starting and stopping the machine, and give an overview of different milling techniques for various materials.
Introduction to the Basic Operations of a Milling Machine
Operating a milling machine involves several fundamental operations that allow users to shape and manipulate workpieces with precision. These operations include:
- Facing: This operation involves removing material from the face of a workpiece using a face mill cutter. It helps create flat surfaces and clean up rough edges.
- End Milling: End mills are used to cut slots or grooves into the surface of a workpiece. This operation is commonly used for creating keyways or pockets.
- Drilling: Milling machines can also drill holes in workpieces using drill bits specifically designed for milling machines.
- Contouring: Specialized cutting tools such as ball-nose end mills or chamfer mills can create intricate shapes and contours on the surface of a workpiece.
Understanding the Different Types of Milling Cutters and Their Uses
To perform these operations effectively, it is crucial to understand the different types of milling cutters available and their specific uses:
- Face Mills: Face mills are ideal for facing large flat surfaces on workpieces. They feature multiple cutting edges that can remove material quickly and efficiently.
- End Mills: End mills are versatile cutting tools used for various operations such as slotting, profiling, contouring, and plunging into materials.
- Fly Cutters: Fly cutters consist of a single-point cutting tool mounted on a rotating spindle. They are commonly used for facing large surfaces and producing a smooth finish.
- Shell Mills: Shell mills are similar to face mills but have larger diameters. They are often used for heavy-duty operations such as roughing or removing large amounts of material.
Understanding the differences between these milling cutters will help you choose the right tool for your specific milling needs.
Step-by-Step Guide to Starting and Stopping the Milling Machine
Starting and stopping a milling machine correctly ensures safe and efficient operation. Here is a step-by-step guide:
Starting the Machine
1. Ensure all safety precautions, such as wearing appropriate personal protective equipment, are in place.
2. Check that the machine's power supply is connected and turned on.
3. Familiarize yourself with the machine's control panel and locate the power switch.
4. Turn on the power switch, allowing the machine to initialize.
Preparing the Workpiece
5. Securely clamp or fasten the workpiece onto the milling machine table using appropriate fixtures or vises.
6. Ensure the workpiece is aligned and centered according to your desired milling operation.
Setting Up Speeds and Feeds
7. Consult the manufacturer's guidelines or machining data sheets to determine optimal cutting speeds, feeds, and depth of cut for your specific material and cutter combination.
8. Adjust these settings on your milling machine accordingly.
Starting Milling Operations
9. Gradually engage the cutter into contact with your workpiece.
10. Depending on your machine's capabilities, feed your workpiece into the cutter using a manual or automatic feed mechanism.
11. Monitor cutting forces, sounds, and vibrations during operation to ensure smooth cutting performance.
Stopping the Machine
12. Once you have completed your milling operations, gradually reduce cutting forces and disengage the cutter from the workpiece.
13. Turn off the power switch on the machine.
14. Clean up any debris or chips left on the milling machine and surrounding area.
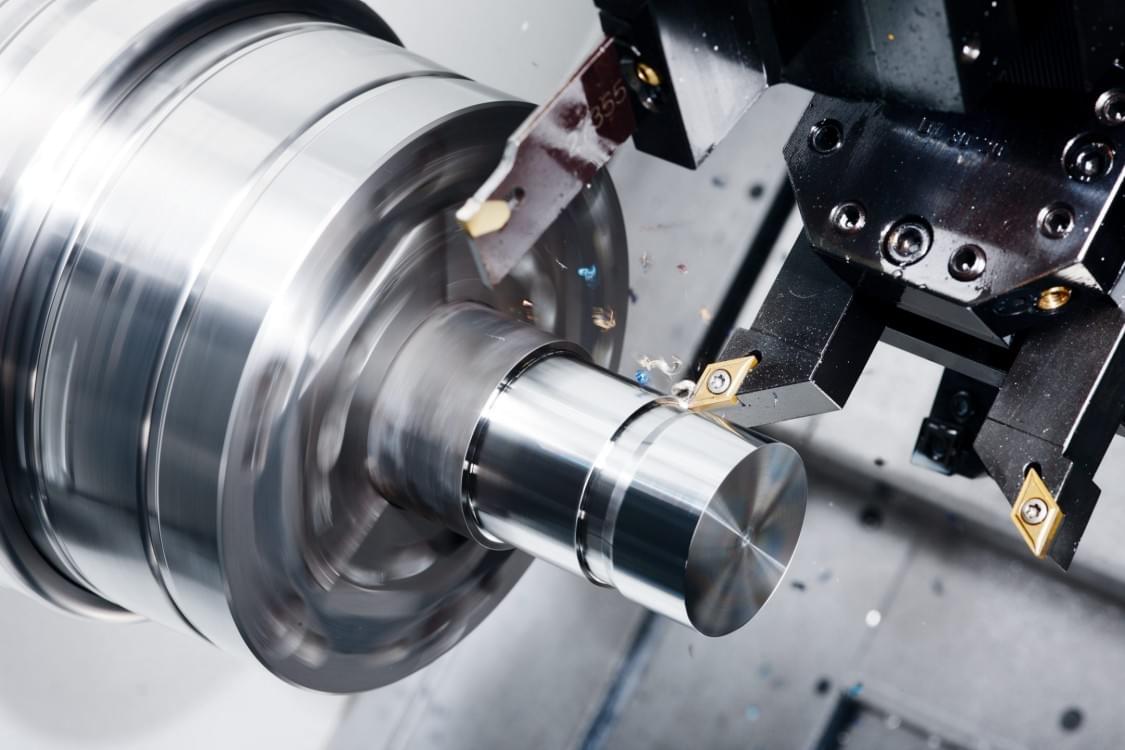
Maintenance and Troubleshooting
Regular maintenance is crucial for ensuring a milling machine's longevity and optimal performance. By implementing a routine maintenance schedule, you can prevent potential issues and extend the lifespan of your equipment. Neglecting maintenance can lead to costly repairs and downtime, affecting your workshop's productivity.
To maintain your milling machine, start by cleaning and lubricating its components regularly. This helps to remove any debris or dirt that may accumulate during operation. Use a soft brush or compressed air to clean hard-to-reach areas, ensuring that all surfaces are free from contaminants.
Lubrication is essential for reducing friction and preventing wear on moving parts. Apply lubricant to the appropriate points as recommended by the manufacturer. This will help ensure smooth operation and prevent premature component failure.
In addition to regular cleaning and lubrication, it is important to identify common issues that may arise with your milling machine. This includes understanding how to troubleshoot problems such as motor malfunctions, inaccurate cutting results, or abnormal noises during operation.
Troubleshooting techniques may involve checking electrical connections, inspecting belts and pulleys for wear or damage, or adjusting the alignment of the milling machine components. If you encounter any issues beyond your expertise, it is important to consult the machine's manual or seek professional assistance.
For more complex problems or professional assistance with maintenance or troubleshooting, contact SYIL Machine Tools. Their team of experts can provide guidance and support to ensure that your milling machine operates at its best.
Remember, regular maintenance and proper troubleshooting techniques will help keep your milling machine in optimal condition for years to come.
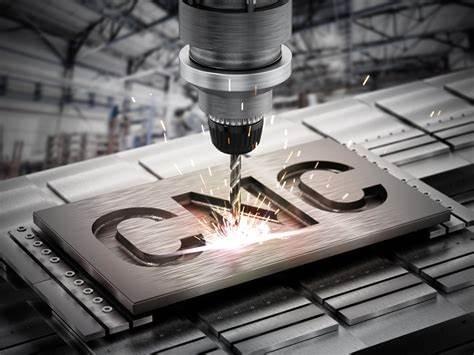
Advanced Techniques and Tips
When it comes to precision engineering, advanced milling techniques are crucial for achieving accurate results. By exploring these techniques, you can elevate your milling skills to the next level of craftsmanship.
To begin with, one technique that stands out is using a face mill cutter. This tool is specifically designed for facing operations and can create flat surfaces with exceptional precision. By utilizing a face mill cutter, you can achieve smooth finishes and maintain tight tolerances in your workpiece.
Another important consideration is choosing between an end mill and a face mill. While both tools are commonly used in milling operations, they serve different purposes. An end mill is ideal for creating detailed cuts and profiles, while a face mill excels at removing large amounts of material quickly. Understanding the strengths of each tool will help you optimize your milling process.
In addition, it's worth mentioning the benefits of using a fly cutter over a face mill. A fly cutter is a single-point cutting tool that can produce excellent surface finishes on large workpieces. Its simplicity and versatility allow for efficient material removal while maintaining accuracy.
When comparing shell mills to face mills, it's important to consider their specific applications. Shell mills are primarily used for larger cutting tasks and heavy-duty machining operations. They excel at quickly removing significant amounts of material while delivering precise results.
By incorporating these advanced techniques into your milling process, you can maximize your machine's efficiency and productivity. Experimenting with different tools and approaches will allow you to find the best methods for your specific projects.
Conclusion
Recap of the Key Points Covered in the Beginner's Guide
In this beginner's guide to using a milling machine, we have covered the essential aspects of getting started, setting up, operating, and maintaining one. We discussed the different types of milling machines and their components, as well as the importance of safety precautions. We also explored the basic operations and techniques involved in milling various materials.
Milling machines are versatile tools that offer immense potential for precision engineering projects. From creating intricate designs to producing complex parts with high accuracy, these machines open up a world of possibilities. We encourage readers to embrace their creativity and push the boundaries of what can be achieved with a milling machine.
SYIL's Commitment to Customer Satisfaction and Industry Excellence
SYIL Machine Tools develops and manufactures precision CNC machines for milling and drilling. With over 12k machines supplied globally, they prioritize quality and sustainability. Operating in multiple countries, SYIL is becoming a recognized brand in the industry.
At SYIL Machine Tools, customer satisfaction is paramount. They strive to provide reliable machines that meet the highest standards while offering excellent customer support throughout your journey with their products.