Introduction
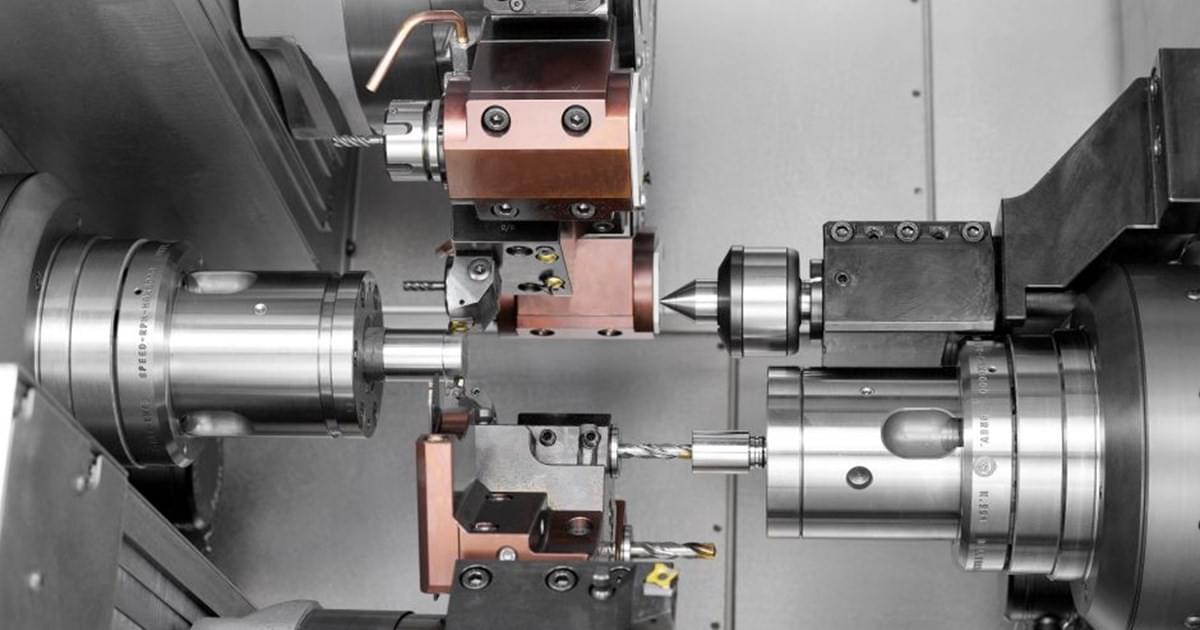
In today's modern manufacturing industry, CNC lathes have become essential tools for precision machining. These advanced machines offer numerous benefits that enhance production efficiency and accuracy. One company at the forefront of developing high-quality CNC machines is SYIL Machine Tools. With its commitment to sustainability and precision, SYIL has established itself as a reliable partner for CNC lathe solutions.
Quality and sustainability are core values at SYIL Machine Tools. They employ rigorous quality control measures throughout the manufacturing process to ensure every machine meets stringent standards of excellence. SYIL also contributes to sustainable manufacturing practices by utilizing advanced technologies and materials responsibly. Their commitment to quality and sustainability makes SYIL CNC machines reliable for businesses seeking long-lasting and environmentally conscious solutions.
Key Components of a CNC Lathe
CNC lathes are complex machines that consist of various key components. Understanding these components is crucial for anyone looking to build or operate a CNC lathe. This section will explore the bed and headstock, spindle and chuck, tailstock and carriage, and the tool turret and tooling systems.
1. Understanding the Bed and Headstock of a Lathe
The bed is the foundation of a CNC lathe and provides stability during machining operations. It is typically made of cast iron or steel and ensures the accuracy and precision of the machine. The headstock at one end of the bed houses the main spindle that rotates the workpiece.
2. The Importance of the Spindle and Chuck in CNC Lathes
The spindle is a critical component in a CNC lathe as it holds and rotates the workpiece during machining operations. It allows precise control over speed and direction while ensuring optimal cutting performance. On the other hand, the chuck securely grips the workpiece to prevent any movement during machining.
3. Exploring the Tailstock and Carriage Features
The tailstock is located at the opposite end of the headstock and provides additional support to the workpiece. It can be adjusted to accommodate different lengths of workpieces and is often used for drilling or other secondary operations. The carriage, on the other hand, moves along the bed and holds various cutting tools.
4. Overview of the Tool Turret and Tooling Systems
The tool turret is an essential component that holds multiple cutting tools, allowing for quick tool changes during machining operations. It eliminates manual tool changes, enhancing efficiency and reducing downtime. The tooling systems consist of tool holders, inserts, and accessories compatible with specific machining applications.
Building your own CNC lathe requires an understanding of these key components. Each component is crucial in ensuring precision and accuracy in machining operations. You can guarantee optimal performance in your CNC lathe construction project by selecting high-quality components like those offered by SYIL Machine Tools.
Setting Up a CNC Lathe for Optimal Performance
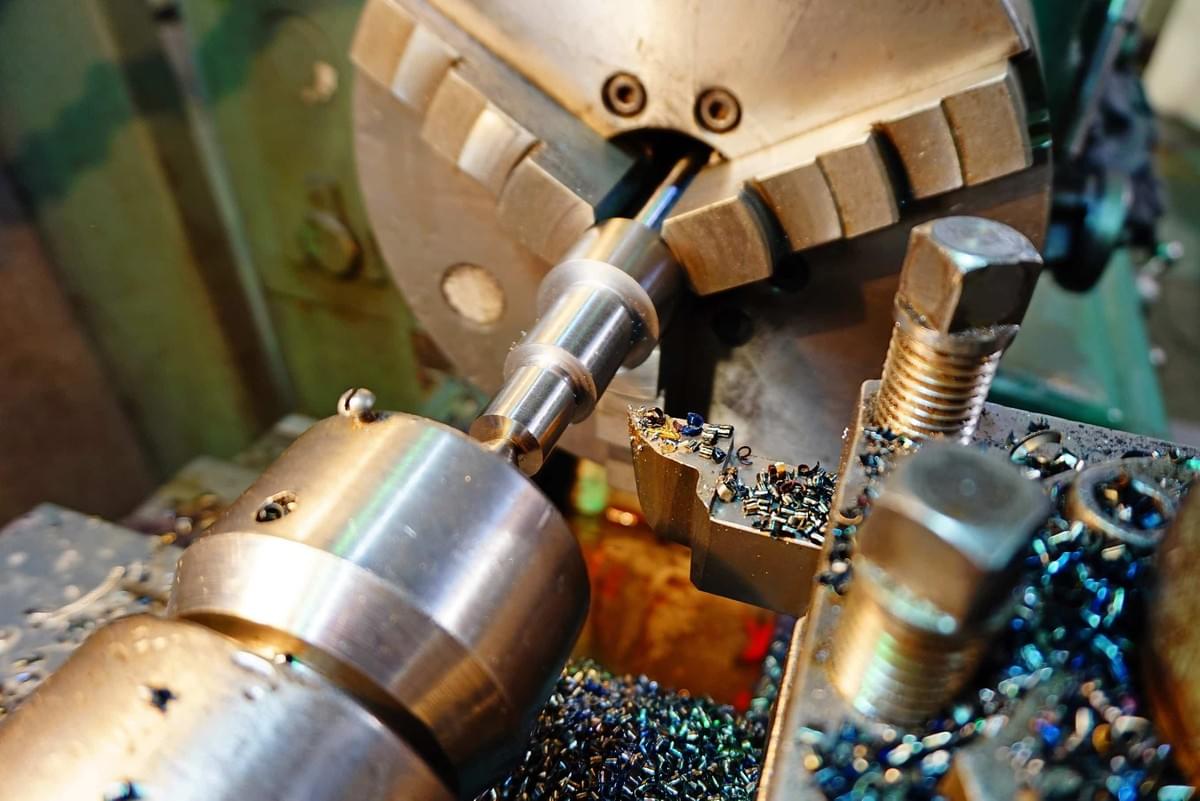
Properly setting up a CNC lathe is crucial to ensure optimal performance and accuracy in machining operations. This section will discuss the key steps in setting up a CNC lathe, including choosing the right location, alignment and calibration, essential maintenance, and optimizing speeds and feeds.
Choosing the Right Location for Your CNC Lathe
Selecting the optimal location for your CNC lathe is crucial for its performance and overall workflow. Here are some key factors to consider:
- Clean and well-ventilated: The environment should be free from excessive dust, debris, and moisture that can harm the machine's sensitive components and compromise machining accuracy.
- Adequate space: Ensure enough space around the lathe for unobstructed operation and maintenance. Consider the swing diameter, travel lengths, and clearance needed for material loading and unloading.
- Level and stable foundation: The lathe must be placed on a stable surface to ensure proper operation and prevent vibrations affecting machining precision.
By carefully considering these factors, you can create the ideal environment for your CNC lathe to operate efficiently and produce high-quality results.
Proper Alignment and Calibration of the Lathe
Proper alignment and calibration of the CNC lathe are crucial to achieve precise machining results. This involves ensuring all components are aligned correctly, including the bed, headstock, spindle, chuck, tailstock, carriage, tool turret, and tooling systems. Regular calibration checks should be conducted to maintain accuracy over time.
Essential Maintenance for Longevity and Precision
Regular maintenance is crucial for ensuring the longevity and precision of your CNC lathe. By following these simple steps, you can keep your machine running smoothly for years to come:
Cleanliness is Key: Regularly clean all machine surfaces to remove dust, debris, and metal shavings that can accumulate and hinder performance. Attention areas around the ways, spindle, and tool changer.
- Proper Lubrication: Lubricate moving parts according to the manufacturer's recommendations. This helps to minimize friction, wear, and tear, ultimately extending the lifespan of your machine and maintaining its accuracy.
- Coolant Care: Regularly check the coolant level and concentration. Change the coolant to prevent bacterial growth and ensure optimal cooling performance.
- Inspect and Tighten: Regularly inspect for loose bolts, screws, or other fasteners and tighten them as needed. This helps to prevent vibrations and maintain machine integrity.
- Keep an Eye on Filters: Clean or replace air and hydraulic filters at recommended intervals to ensure proper system function and prevent contamination.
By following these essential maintenance tips, you can ensure your CNC lathe operates at its peak performance for years, delivering consistent and precise results for all your machining projects.
Optimizing Speeds and Feeds for Efficient Machining
Optimizing speeds and feeds on your CNC lathe can significantly improve machining efficiency. It involves selecting appropriate cutting speeds based on material type and hardness while considering feed rates for smoother cutting operations. Experimentation with different settings may be required to find an optimal balance between speed and precision.
SYIL Machine Tools develops and manufactures precision CNC machines for milling and drilling. With over 12k machines supplied globally, they prioritize quality and sustainability.
Programming and Operating a CNC Lathe
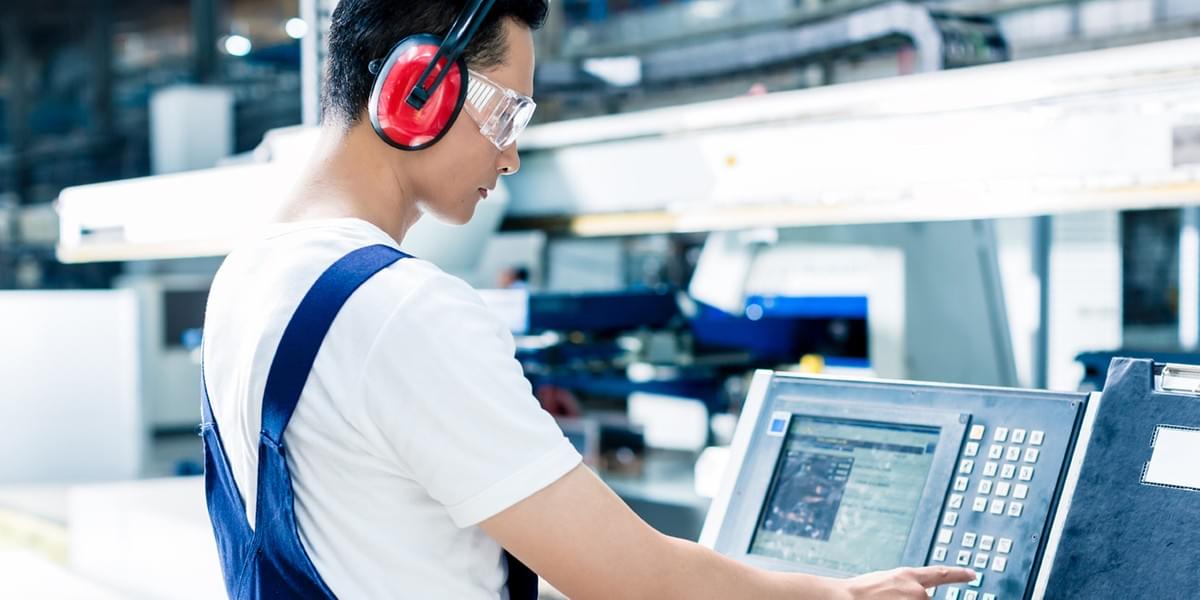
Programming and operating a CNC lathe is a crucial aspect of effectively utilizing this advanced manufacturing tool. This section will explore the overview of CNC programming languages and codes, the process of creating and editing CNC programs for lathe operations, understanding the control panel and user interface, and some operating tips and best practices for CNC lathes.
Overview of CNC Programming Languages and Codes
CNC programming languages and codes are the backbone of controlling the movements and functions of a CNC lathe. Commonly used programming languages, including G-code and M-code, are standardized across various machine manufacturers. G-codes define specific movements such as tool positioning, spindle speed, feed rate, while M-codes control auxiliary functions like coolant flow or tool changes.
Creating accurate programs requires a deep understanding of these programming languages. Fortunately, software tools simplify the process by providing intuitive interfaces to generate code based on desired operations. These tools allow users to visualize their designs in 2D or 3D before generating the necessary code for machining.
Creating and Editing CNC Programs for Lathe Operations
Creating and editing CNC programs is an essential skill for maximizing the capabilities of your lathe machine. To create a program, you need to define each step of the machining process by specifying tool paths, cutting depths, spindle speeds, feed rates, and more.
When editing existing programs, it's crucial to maintain accuracy while making modifications. Small errors in code can lead to significant issues during machining operations. Therefore, it's recommended to use software with built-in simulation features that allow you to verify your program's functionality before running it on your lathe machine.
Understanding the Control Panel and User Interface
The control panel serves as an interface between operators and their CNC lathe machines. It allows users to input commands manually or load pre-programmed instructions for machining operations. The control panel typically consists of a screen, keypad, and various navigation and function selection buttons.
The user interface on modern CNC lathes is designed to be user-friendly and intuitive. It gives operators real-time feedback on machine status, tool positions, and other vital information. Familiarizing yourself with the control panel and user interface is essential to operate the CNC lathe efficiently.
Advanced Techniques and Applications for CNC Lathes
When it comes to advanced techniques and applications, CNC lathes offer a wide range of possibilities. Let's explore some key features and functionalities that take CNC lathe machining to the next level.
Exploring Live Tooling and Multi-Axis Machining
Live tooling is a game-changer in CNC lathe operations. It allows for simultaneous machining operations, such as milling, drilling, and tapping, without additional setups. This capability significantly reduces production time and increases efficiency.
With multi-axis machining, CNC lathes can perform complex operations by moving the workpiece along multiple axes. This enables intricate cuts and shapes that would be impossible with traditional lathes. The result is precise and intricate parts with minimal effort.
Introduction to Sub-Spindles and Bar Feeders
Sub-spindles are an invaluable feature in CNC lathes as they allow for simultaneous front and back-end machining of a workpiece. This means increased productivity by reducing idle time during part transfer.
Bar feeders are another essential component that automates material feeding into the machine. They enable continuous operation without manual intervention, saving time and increasing efficiency.
You can achieve higher productivity levels while maintaining precision by incorporating sub-spindles and bar feeders into your CNC lathe setup.
Performing Threading and Tapered Turning Operations
Threading is a common operation in manufacturing, and CNC lathes excel at it. With precise control over spindle speed, feed rate, and tool movement, CNC lathes can produce accurate and consistent threads. This eliminates the need for manual threading and ensures high-quality results.
Tapered turning is another technique made possible by CNC lathe machines. It involves gradually changing the diameter of a workpiece along its length. This is particularly useful for applications such as creating conical shapes or chamfers.
Customizing CNC Lathes for Specific Manufacturing Needs
One of the significant advantages of CNC lathes is their versatility and adaptability to various manufacturing needs. Whether working with small precision parts or large-scale components, you can customize your CNC lathe to meet specific requirements.
SYIL Machine Tools offers a range of options to tailor your CNC lathe machine precisely to your needs. You can create a customized setup that optimizes efficiency and productivity from different bed sizes to specialized tooling systems.
Safety Precautions and Compliance in CNC Lathe Operations
To ensure a safe working environment and prevent accidents, it is crucial to understand the potential hazards associated with CNC lathe operations. By identifying these risks, operators can take necessary precautions to protect themselves and others.
Understanding Potential Hazards in CNC Lathe Operations
Operating a CNC lathe involves various risks that can result in serious injuries if not properly managed. Some potential hazards include:
- Rotating Machinery: The rotating components of a lathe, such as the spindle and chuck, pose a significant risk of entanglement or getting caught in loose clothing or jewelry.
- Flying Debris: During machining processes, metal chips, and other debris can be ejected at high speeds, causing eye injuries or cuts if operators are not wearing appropriate protective gear.
- Electrical Hazards: Working with powerful electrical systems carries the risk of electrical shocks or fires if proper precautions are not taken.
- Noise and Vibration: The operation of a CNC lathe produces loud noise levels and vibrations that can lead to hearing loss or musculoskeletal disorders if workers are exposed for extended periods without proper protection.
To mitigate these hazards, it is essential to implement safety measures and adhere to industry best practices.
Proper Personal Protective Equipment (PPE) Usage
Wearing appropriate Personal Protective Equipment (PPE) is crucial when operating a CNC lathe. Here are some essential PPE items:
- Safety Glasses: Protecting the eyes from flying debris is critical; therefore, safety glasses with side shields should always be worn.
- Gloves: Operators should wear gloves made from cut-resistant materials to reduce the risk of cuts or lacerations caused by sharp edges or moving parts.
- Ear Protection: Earplugs or earmuffs should be worn to minimize the risk of hearing damage from prolonged exposure to loud noise levels.
- Protective Clothing: Operators should wear close-fitting clothing without loose ends or jewelry that can get entangled in the lathe's moving parts.
Operators can significantly reduce the risk of injuries using the appropriate PPE and ensure a safer working environment.
Implementing Safety Procedures and Lockout/Tagout
To further enhance safety during CNC lathe operations, it is essential to establish and follow proper safety procedures. This includes:
- Training: All operators should receive comprehensive training on safe operating practices, emergency procedures, and the correct use of safety equipment.
- Lockout/Tagout (LOTO): LOTO procedures are crucial for preventing accidental startup of machinery during maintenance or repair work. By locking or tagging out the power source, operators can ensure their safety while performing necessary tasks.
- Clear Workspace: Keeping the workspace clean and free from clutter reduces the risk of slips, trips, and falls while operating the CNC lathe.
- Emergency Stop Buttons: Familiarize yourself with the location and functionality of emergency stop buttons to quickly halt operations in an emergency.
By implementing these safety procedures consistently, operators can minimize risks and create a safer working environment for everyone involved.
The Evolution of CNC Lathe Technology
Over the years, CNC lathe technology has undergone a remarkable transformation. The evolution has revolutionized modern manufacturing from manual lathes to computer-controlled precision machines. Today, CNC lathes offer unparalleled accuracy, efficiency, and versatility in machining operations.
SYIL Machine Tools: Your Reliable CNC Lathe Partner
When it comes to reliable CNC lathe machines, SYIL Machine Tools is a trusted name in the industry. With over 12k machines supplied globally, they have established themselves as leaders in precision engineering. Their commitment to quality and sustainability sets them apart from their competitors.
Building your CNC lathe may seem daunting, but with the right guidance and essential tools, it is an achievable endeavor. Following step-by-step guides and utilizing DIY construction plans can help you bring your vision to life.
Start Building Your Precision with SYIL CNC Machines
If you're ready to build your own CNC lathe machine, look no further than SYIL Machine Tools. Their range of precision CNC machines for milling and drilling will provide you with the reliability and accuracy you need for your projects.