Introduction
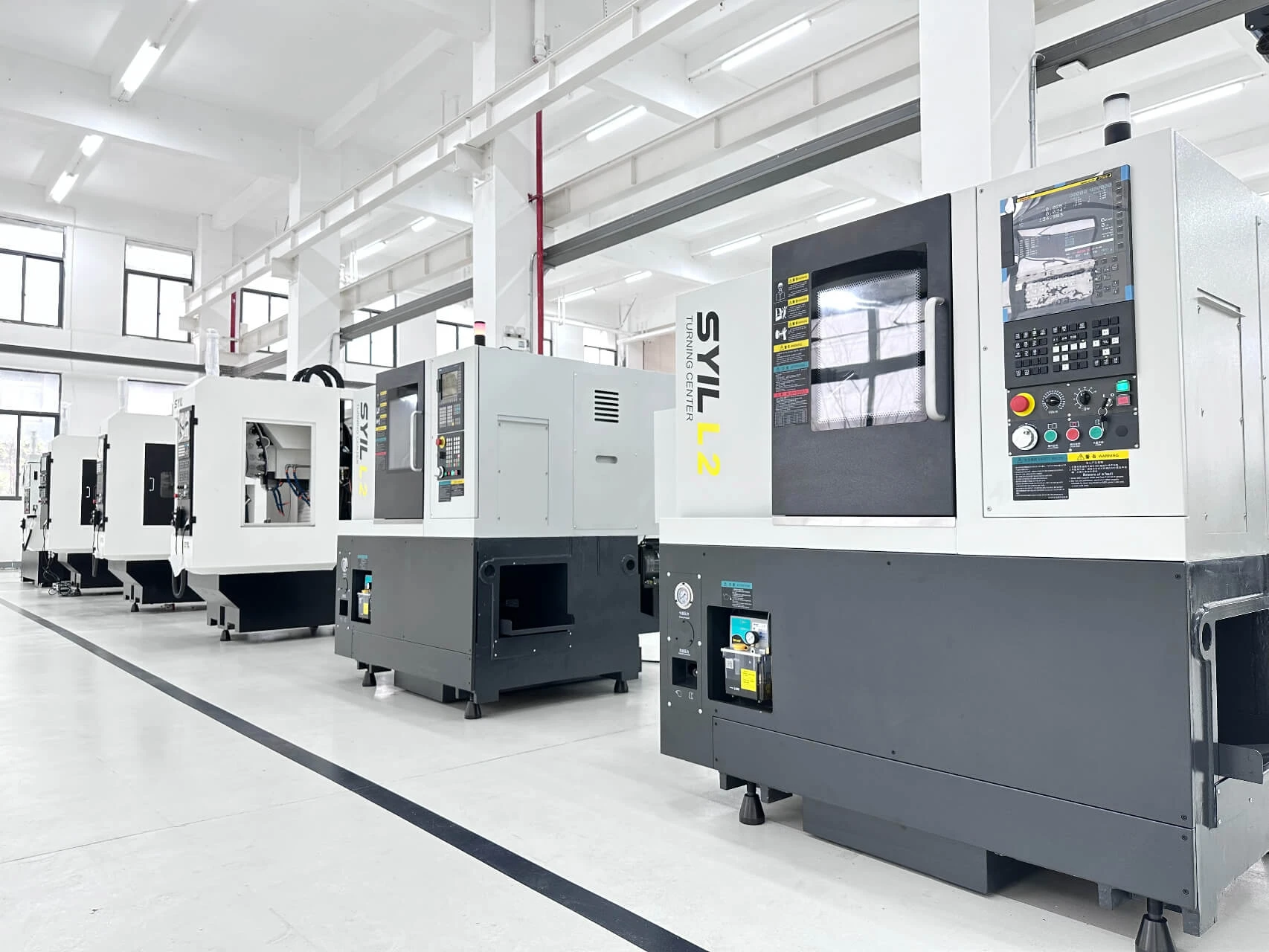
In the ever-evolving landscape of healthcare, CNC (Computer Numerical Control) technology has carved out a significant niche, particularly in medical device machining. This innovative approach allows for precision and efficiency in the manufacturing of critical medical devices, ensuring they meet stringent quality standards. As we delve into the world of CNC in the medical field, it becomes clear that understanding its role is essential for anyone involved in healthcare manufacturing.
Overview of CNC in the Medical Field
CNC technology has revolutionized how we think about medical device machining, enabling manufacturers to create complex components with unparalleled accuracy. In medical terms, CNC refers to automated machinery that uses programmed commands to control tools and processes for fabricating devices such as surgical instruments and implants. This method not only enhances production speed but also significantly reduces human error, making it a game-changer for the industry.
Importance of Precision in Medical Device Machining
Precision is paramount when it comes to medical device machining because even the slightest deviation can lead to serious consequences for patient safety. What is CNC in medical terms? It’s all about achieving exact specifications that align with regulatory standards while ensuring optimal performance during use. The intricate details required for these devices underscore why precision engineering is not just beneficial but essential in this high-stakes environment.
Key Regulations Impacting Medical Machining
Navigating through key regulations impacting medical machining is crucial for manufacturers aiming to maintain compliance and uphold safety standards. Regulatory bodies like the FDA impose strict guidelines on what constitutes acceptable practices within CNC medical applications, ensuring that every aspect from design to production meets rigorous safety criteria. Understanding these regulations helps manufacturers not only avoid costly penalties but also fosters trust among healthcare providers and patients alike.
Understanding CNC Machining
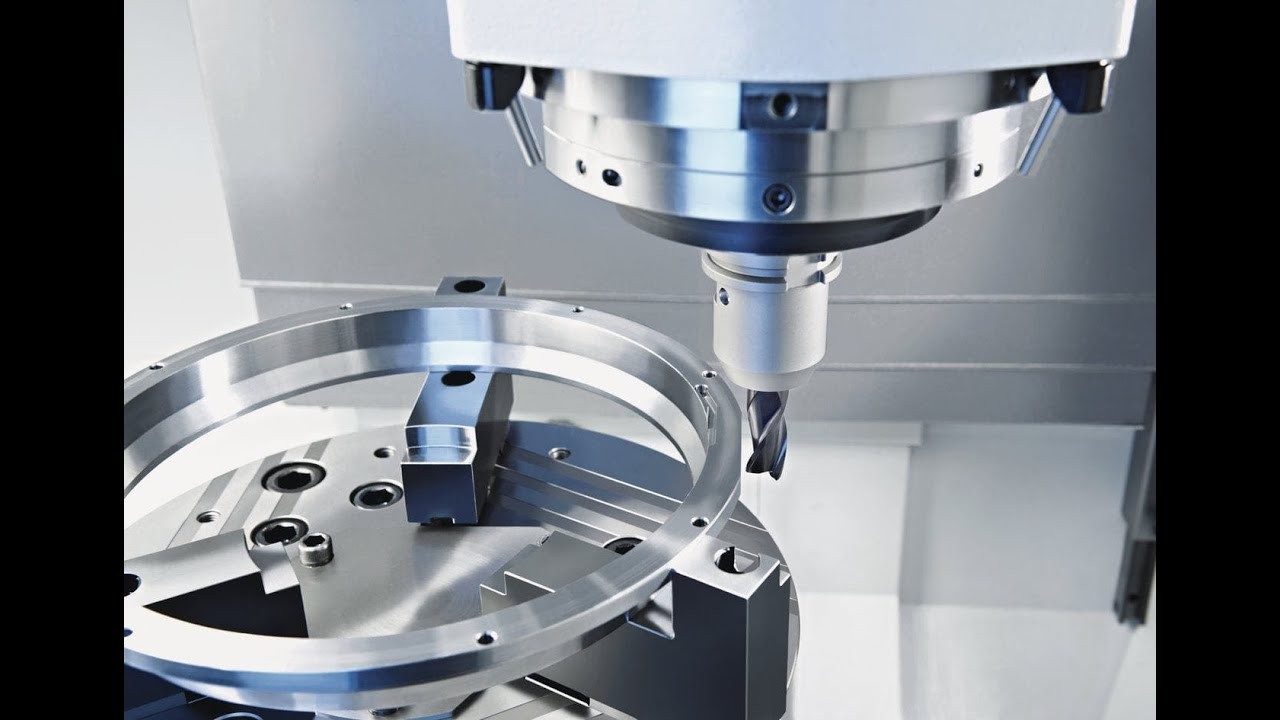
CNC machining has revolutionized the medical field, offering unprecedented precision and efficiency in medical device machining. But what exactly is CNC in medical terms? At its core, CNC stands for Computer Numerical Control, a technology that allows machines to be controlled digitally to produce intricate parts required in various medical applications.
What is CNC in Medical Terms?
In the context of medical device machining, CNC refers to the automated control of machining tools through programmed commands interpreted by a computer. This process enables manufacturers to create complex geometries with high accuracy, which is crucial for devices like surgical instruments and implants. Essentially, when we ask What is a CNC medical? we’re exploring how this technology enables the production of life-saving equipment with minimal human error.
The manufacturing process for medical devices heavily relies on this technology due to its ability to maintain tight tolerances and repeatability across multiple units. As healthcare demands evolve, understanding what CNC means in this sector becomes vital for ensuring that devices meet stringent quality standards while enhancing patient safety.
The Role of CNC Machines in Medical Device Manufacturing
CNC machines play a pivotal role in the manufacturing process for medical devices by automating tasks that were once labor-intensive and prone to human error. These machines can produce components from various materials such as metals and plastics, which are essential in creating everything from prosthetics to diagnostic equipment like CNC medical tests. The precision offered by these machines ensures that each component meets exact specifications necessary for optimal performance.
Moreover, their ability to work continuously without fatigue means that production rates can be significantly increased without sacrificing quality—an essential factor when scaling up operations to meet market demands. In summary, CNC machines are indispensable tools within the realm of medical machining as they enhance both efficiency and product reliability.
Benefits of CNC Technology for Medical Applications
The benefits of adopting CNC technology in medical applications are manifold and extend beyond mere efficiency gains; they include enhanced precision, reduced waste material, and improved safety standards. For instance, using automated processes minimizes human involvement during critical stages of production—this not only reduces the risk of errors but also aligns with stringent regulatory requirements governing medical device machining.
Additionally, manufacturers can achieve greater design flexibility thanks to advanced CAD/CAM software integrated with these machines; this allows rapid prototyping and iteration based on real-time feedback from healthcare professionals about what works best clinically. Ultimately, embracing CNC technology translates into better-performing products that can adapt swiftly to changing healthcare needs while promoting sustainability through reduced resource consumption.
The Manufacturing Process for Medical Devices
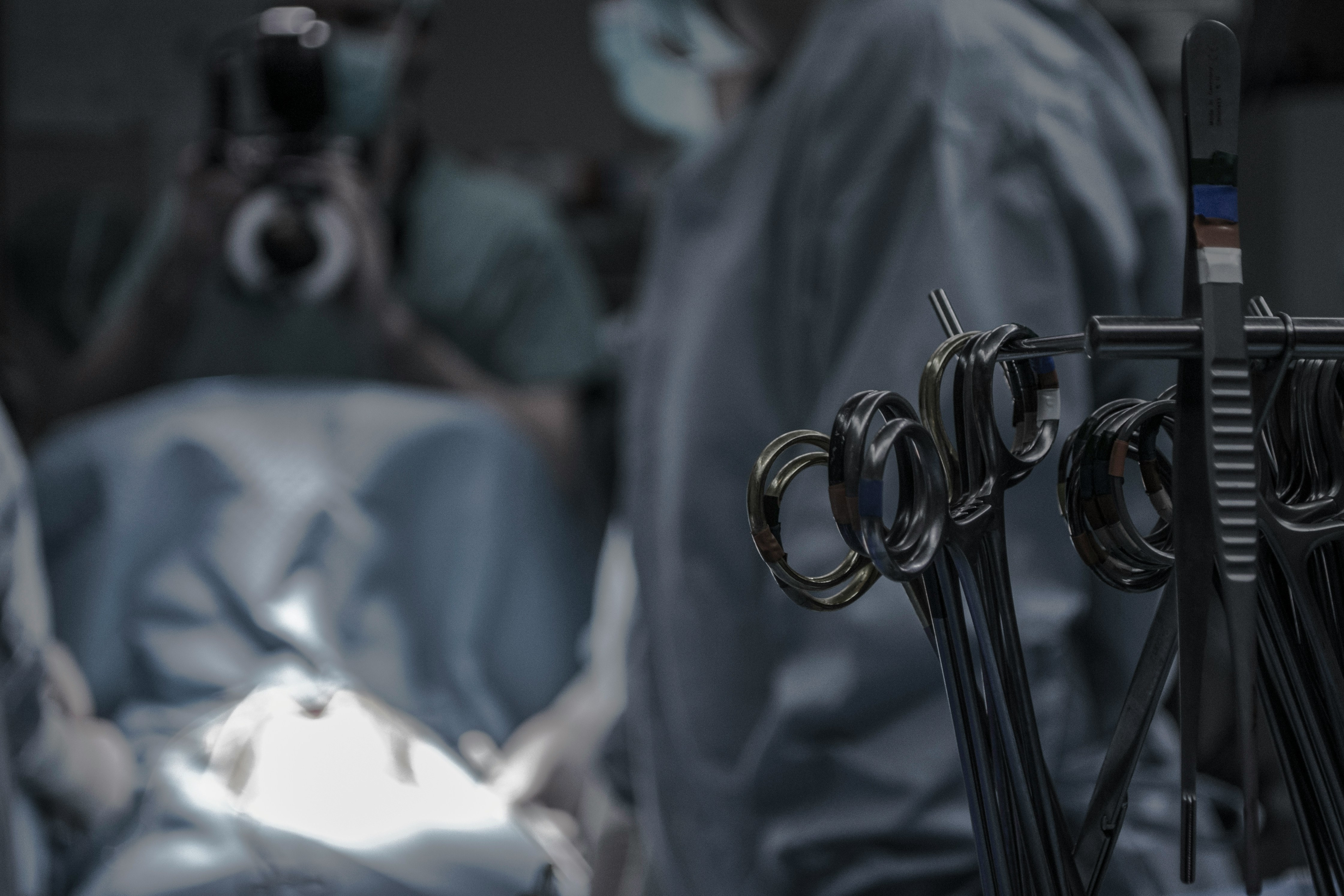
The manufacturing process for medical devices is a complex and highly regulated endeavor, crucial for ensuring patient safety and device efficacy. Understanding this process is essential, especially when discussing what is CNC in medical terms and its role in enhancing precision. In this section, we will explore the steps involved in medical device machining, the materials commonly used in CNC medical manufacturing, and the quality control measures that are indispensable in this field.
Steps Involved in Medical Device Machining
The first step in medical device machining typically involves designing the product using advanced CAD software. This design phase is critical because it lays the groundwork for what will ultimately become a life-saving device; after all, what is the manufacturing process for medical devices without a solid blueprint? Once the design is finalized, it’s time to move on to selecting appropriate materials and preparing them for CNC machining, where precision meets innovation.
Next comes the actual machining phase, where CNC machines take center stage. These machines utilize computer numerical control to shape materials with incredible accuracy—this is where understanding what does CNC stand for in the pharmaceutical industry becomes vital. After machining, devices undergo various finishing processes such as polishing or coating to enhance their functionality and appearance before they are assembled.
Finally, assembly of components takes place along with rigorous testing procedures to ensure that every part meets strict regulatory standards. This step emphasizes why quality control measures are integral throughout medical device machining; even minor errors can lead to significant consequences when lives are at stake.
Materials Commonly Used in CNC Medical Manufacturing
In CNC medical manufacturing, material selection plays a pivotal role that cannot be overstated. Common materials include stainless steel, titanium alloys, plastics like PEEK (polyether ether ketone), and even specialized ceramics; each chosen based on specific application needs within healthcare settings. For example, titanium's biocompatibility makes it an ideal choice for implants while stainless steel offers strength needed for surgical instruments.
Moreover, these materials must meet stringent industry standards which dictate their use within various applications of medical device machining. The choice of material not only impacts durability but also influences factors like weight and ease of sterilization—critical considerations when producing equipment such as surgical tools or prosthetics. Hence knowing what is a CNC medical becomes imperative as these machines can handle diverse materials effectively while maintaining high precision levels.
Additionally, advancements continue to emerge regarding new composite materials designed specifically for complex applications within healthcare contexts; staying updated on these innovations enhances efficiency during production runs while ensuring compliance with regulations surrounding safety and efficacy.
Quality Control Measures in Medical Machining
Quality control measures are non-negotiable aspects of any successful medical machining operation; they serve as safeguards against potential defects that could compromise patient safety or product functionality. These measures begin at the design phase where specifications must align with regulatory requirements—ensuring that every aspect of production adheres strictly to established guidelines related to both performance and safety standards.
Once production begins using advanced techniques such as statistical process control (SPC), ongoing monitoring occurs throughout each stage of manufacturing—from initial material selection through final inspection before packaging. By utilizing methods like automated inspections via CNC machines paired with human oversight during critical phases ensures comprehensive evaluation across all facets involved in creating reliable products from start to finish.
Furthermore, post-production testing remains paramount; devices undergo rigorous assessments including stress tests or biocompatibility evaluations depending on their intended use case scenarios within healthcare settings—this guarantees adherence not just to internal benchmarks but also external certifications required by governing bodies overseeing health-related industries worldwide!
Applications of CNC in the Medical Industry
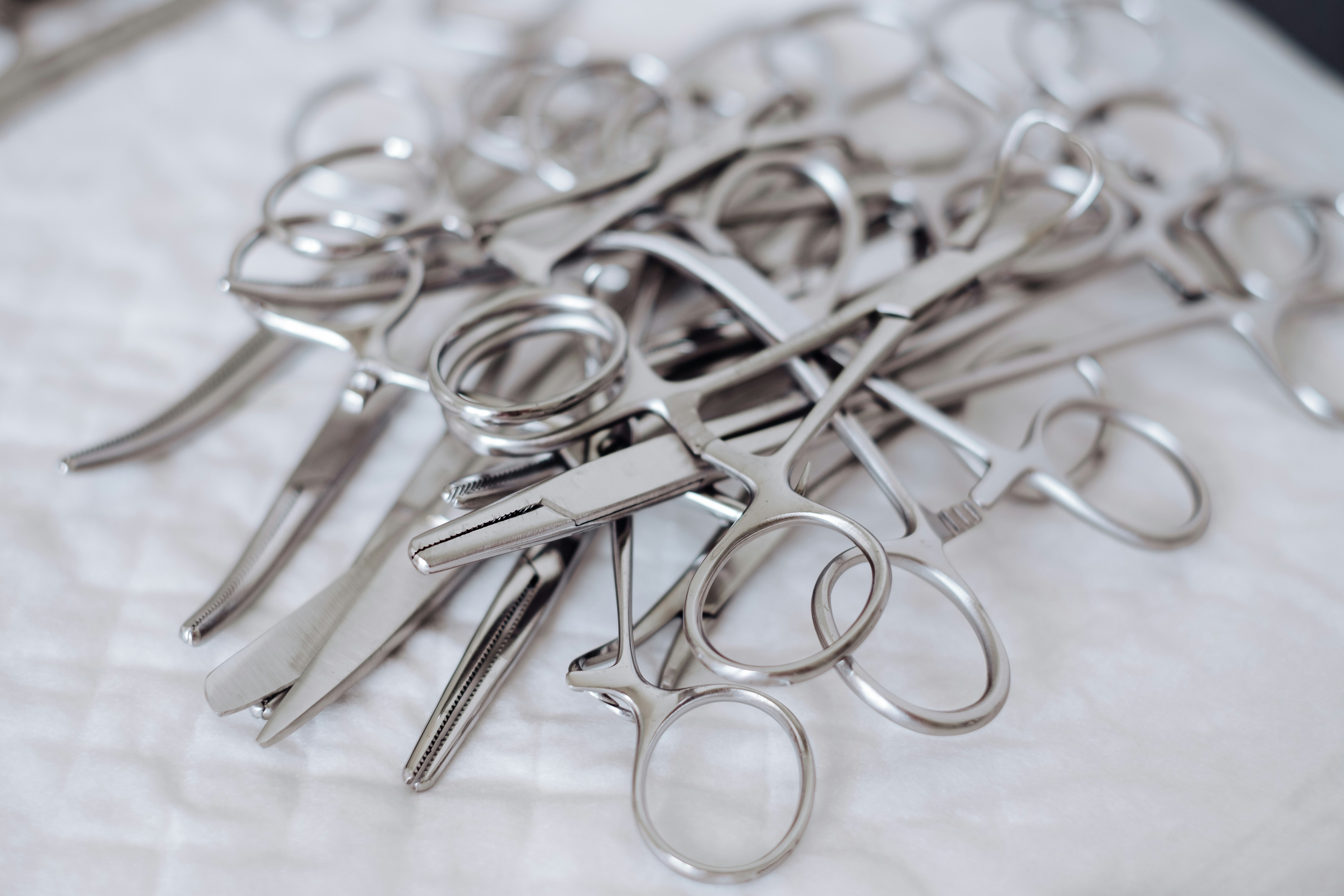
CNC machining has transformed various sectors, and the medical industry is no exception. From precision instruments to custom prosthetics, CNC technology plays a pivotal role in enhancing the quality and efficiency of medical device machining. Let’s explore some specific applications that highlight its importance.
CNC Medical Test Equipment
CNC medical test equipment is essential for ensuring accuracy in diagnostic procedures and patient care. These devices are manufactured with extreme precision, as even the slightest error can lead to significant consequences in a clinical setting. What is CNC in medical terms? It refers to computer numerical control, which allows for meticulous machining processes that produce reliable and repeatable results in medical test equipment.
The manufacturing process for medical devices involves several stages, including design validation and rigorous testing protocols. Advanced CNC machines facilitate this by producing test equipment that meets stringent regulatory standards while maintaining high levels of quality control. With features like automated calibration and real-time monitoring, CNC technology enhances the reliability of these critical tools, making it indispensable for modern healthcare.
Custom Surgical Instruments Fabrication
Custom surgical instruments fabrication is another area where CNC shines brightly. Surgeons often require specialized tools tailored to specific procedures or patient needs; this is where CNC medical machining comes into play. By utilizing advanced CAD/CAM software alongside CNC machines, manufacturers can create bespoke surgical instruments that improve surgical outcomes.
What does CNC stand for in the pharmaceutical industry? While primarily known for its application in manufacturing devices, it also plays a crucial role in producing pharmaceutical equipment used during surgeries or treatments. The customization capabilities offered by CNC technology allow manufacturers to respond swiftly to changing demands within surgical environments while ensuring compliance with safety regulations.
Moreover, custom fabrication through CNC not only enhances tool effectiveness but also contributes to overall cost-efficiency by reducing lead times and waste during production processes. This adaptability makes it an invaluable asset in today’s dynamic healthcare landscape.
Prosthetics and Implants Production
The production of prosthetics and implants has been revolutionized by medical device machining techniques powered by CNC technology. These applications require unparalleled precision since they directly impact patients' mobility and quality of life; hence, what is a CNC medical process if not one that prioritizes accuracy? Through sophisticated modeling software coupled with advanced machinery, manufacturers can produce prosthetic limbs and implants tailored specifically to individual anatomical requirements.
The manufacturing process for medical devices like prosthetics involves intricate design considerations followed by meticulous machining operations—ensuring each piece fits perfectly while offering maximum functionality. The use of biocompatible materials further underscores the importance of quality control measures during production; any oversight could lead to complications post-implantation.
As we move forward into an era where personalization becomes paramount in healthcare solutions, the role of CNC technology will only grow more significant—making it easier than ever before to deliver high-quality prosthetics designed uniquely for each patient’s needs.
Choosing the Right CNC Machine
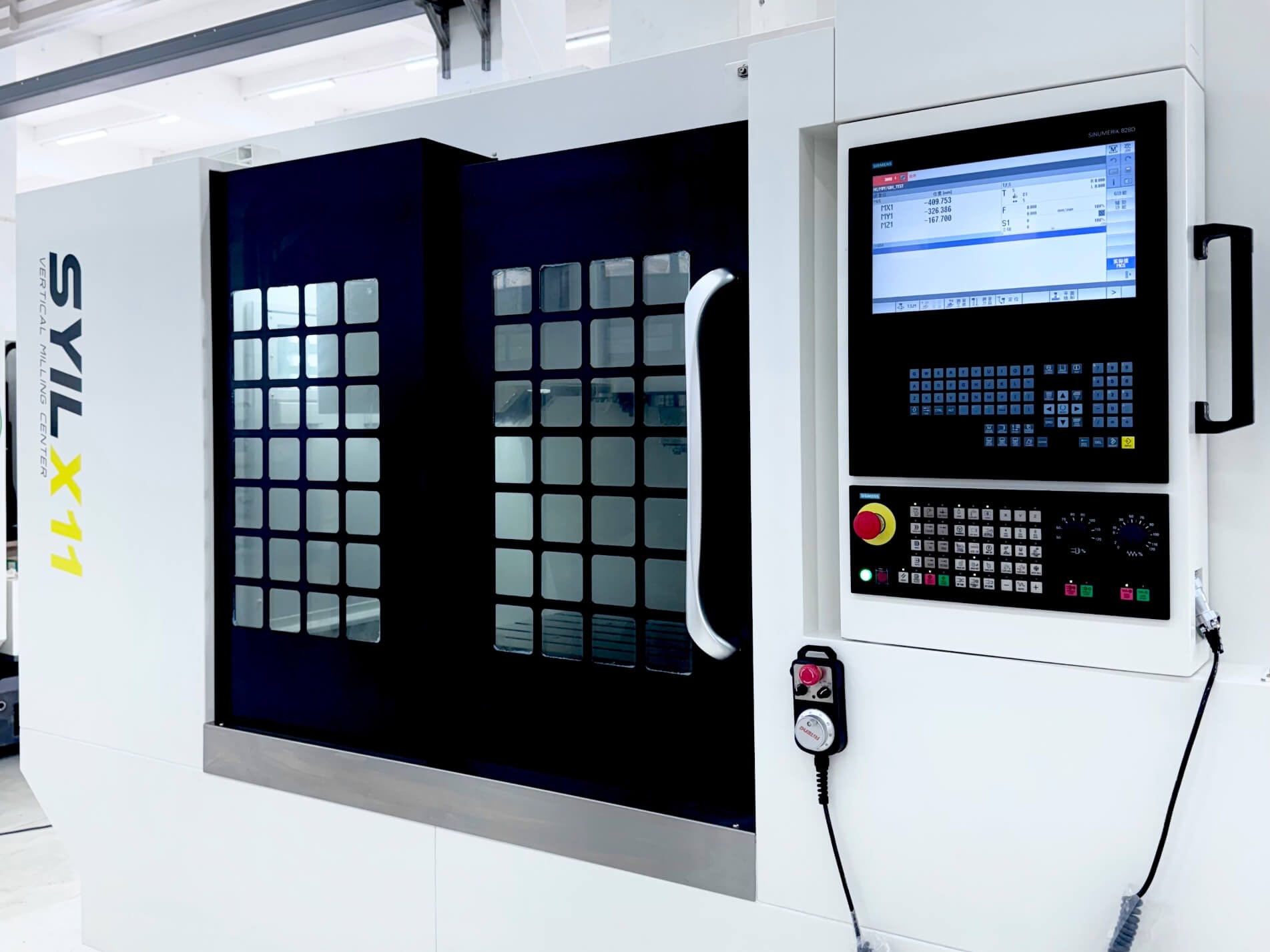
Selecting the right CNC machine for medical device machining is crucial for ensuring precision, efficiency, and compliance with industry standards. With a plethora of options available, it’s essential to understand what sets specific machines apart, particularly when considering their application in medical contexts. This section will delve into the features of SYIL CNC machines tailored for medical use, factors to consider when selecting CNC equipment, and how to compare different CNC machines for optimal medical applications.
Features of SYIL CNC Machines for Medical Use
SYIL CNC machines are designed with the unique demands of medical device machining in mind. These machines boast high precision and repeatability, which are vital attributes when crafting components that require exact specifications. Additionally, they feature advanced software integration that simplifies programming and enhances workflow efficiency—perfect for those asking, What is a CNC medical?
Moreover, SYIL machines offer robust material compatibility; they can handle a variety of materials commonly used in the manufacturing process for medical devices. From titanium to biocompatible plastics, these machines ensure that every component meets stringent quality standards. Their compact design also allows them to fit seamlessly into existing production lines without requiring extensive modifications.
Factors to Consider When Selecting CNC Equipment
When selecting CNC equipment for medical machining applications, several factors should be at the forefront of your decision-making process. First and foremost is precision; any deviation can lead to significant issues in patient safety or product efficacy. Therefore, understanding what does CNC stand for in the pharmaceutical industry becomes vital—it stands not just for Computer Numerical Control but also denotes reliability in producing critical components.
Another key consideration is regulatory compliance; manufacturers must ensure that their equipment meets FDA regulations and ISO standards applicable to medical device machining. This ensures not only quality but also minimizes liability risks associated with non-compliance. Finally, evaluating the machine's ease of use and maintenance can save time and resources over its lifespan—after all, efficiency is paramount in a field where precision matters most.
Comparing CNC Machines for Medical Applications
When it comes to comparing different CNC machines specifically designed for medical applications, several criteria come into play that can help streamline your choice effectively. Start by assessing accuracy levels; look at specifications such as tolerances and repeatability metrics since these will directly impact your output quality during manufacturing processes like surgical instruments fabrication or prosthetics production.
Next up are features tailored towards ease of operation—some models may offer intuitive interfaces or enhanced automation capabilities that simplify training requirements while boosting productivity levels during busy production runs involving various types of equipment like CNC medical test setups or custom instrument fabrication systems.
Lastly, consider after-sales support options from manufacturers; reliable customer service ensures quick resolutions should issues arise post-purchase—a crucial aspect when investing in technology meant to uphold rigorous safety standards across all facets of healthcare delivery systems reliant on effective medical device machining practices.
Future Trends in Medical Device Machining
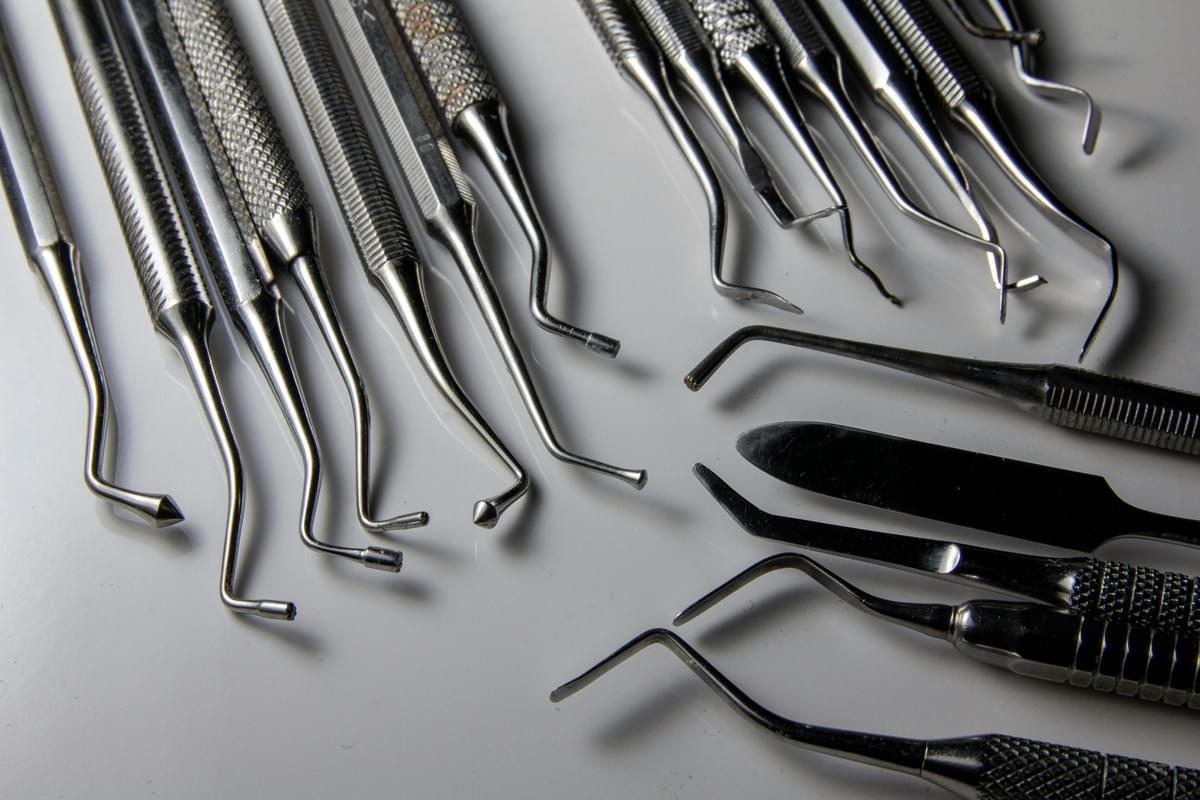
The landscape of medical device machining is rapidly evolving, driven by innovations in technology and the increasing demand for precision and efficiency. As the healthcare sector continues to expand, understanding what is CNC in medical terms becomes crucial for manufacturers aiming to stay competitive. This section explores the latest trends shaping the future of CNC medical applications.
Innovations in CNC Technology
Innovations in CNC technology are transforming how we approach medical device machining. Newer machines boast enhanced capabilities, such as multi-axis machining and advanced software integration, which streamline what is the manufacturing process for medical devices. These advancements enable manufacturers to produce complex geometries with unparalleled accuracy, making it easier to create components that meet stringent regulatory requirements.
Moreover, developments like additive manufacturing combined with traditional CNC methods are pushing boundaries further. This hybrid approach allows for rapid prototyping and customization of parts, essential for creating tailored solutions like custom surgical instruments or unique prosthetics. As we delve deeper into what is a CNC medical application, it’s clear that these innovations will lead to improved patient outcomes through better-designed devices.
The Push for Automation in Medical Manufacturing
The push for automation in medical manufacturing is reshaping how facilities operate and produce goods at scale. Automation technologies such as robotics and AI-driven systems enhance efficiency while minimizing human error—critical factors when considering what does CNC stand for in the pharmaceutical industry? By automating routine tasks within medical machining processes, companies can focus their skilled labor on more complex challenges that require human oversight or creativity.
Additionally, automated quality control measures are becoming increasingly integral to maintaining high standards in production environments focused on precision medicine. These systems can quickly identify defects or inconsistencies during what is the manufacturing process for medical devices, ensuring only compliant products reach healthcare providers and patients alike. The combination of automation with advanced CNC machinery promises a future where speed does not compromise quality.
Sustainability in Medical Machining Practices
Sustainability is becoming a central theme across various industries, including medical device machining, as companies strive to reduce their environmental footprint while meeting regulatory demands. The adoption of eco-friendly materials and energy-efficient practices helps mitigate waste during production processes—a significant concern given the volume of materials used in making surgical instruments or implants through CNC technology.
Moreover, innovative recycling methods are being implemented to repurpose scrap materials generated from machining operations effectively. Companies are also exploring biodegradable options within their supply chains as they seek alternatives that align with sustainability goals without sacrificing performance or safety standards critical to healthcare applications like prosthetics production or custom surgical instruments fabrication.
In conclusion, embracing these trends not only enhances operational efficiencies but also fosters a culture of responsibility within the industry—one where advancements serve both patients' needs and our planet's health.
Conclusion
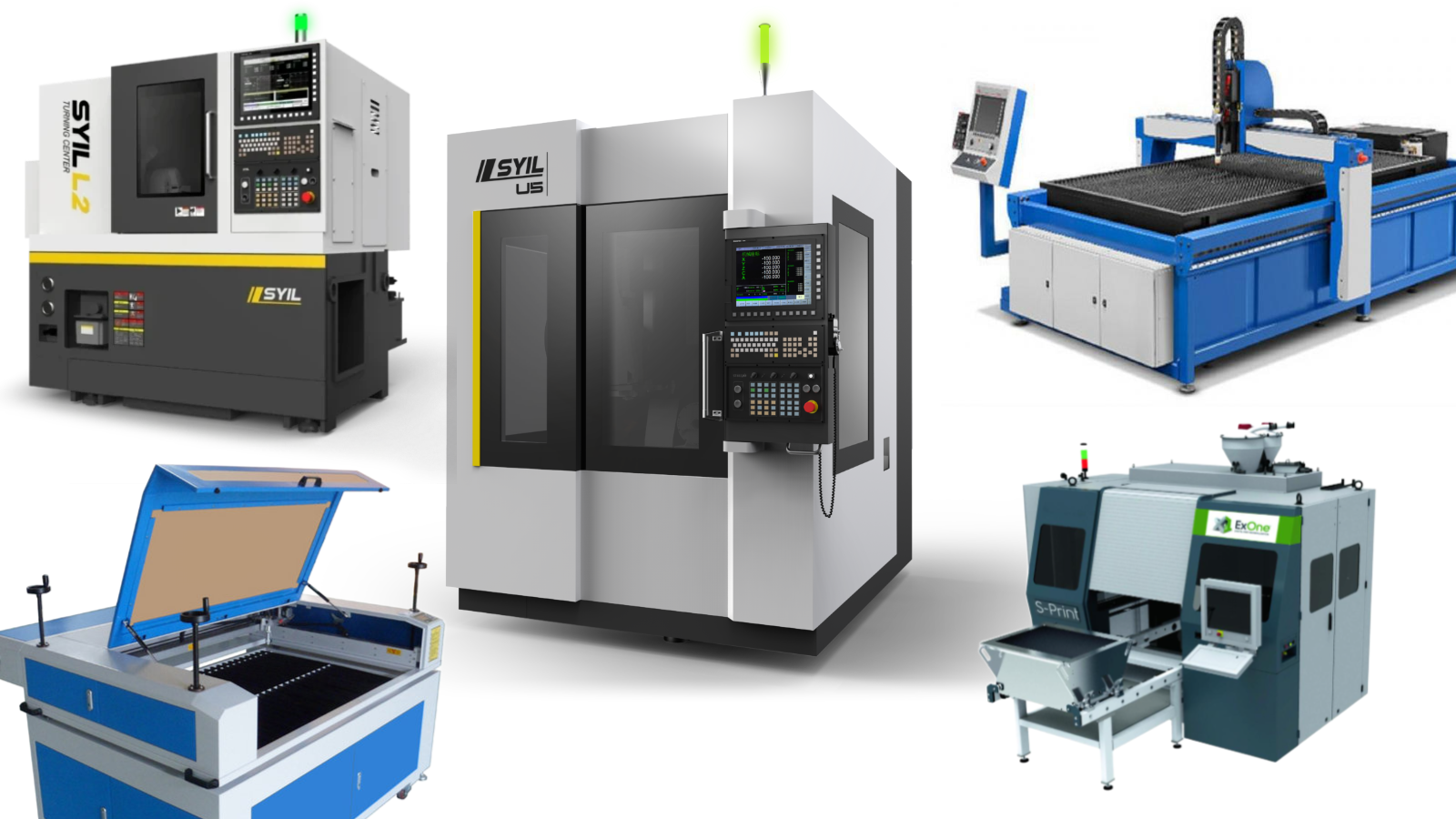
In conclusion, CNC machining plays a pivotal role in the medical field, significantly enhancing the precision and efficiency of medical device machining. By leveraging advanced technology, manufacturers can create complex components that meet stringent regulations and high-quality standards. As we look to the future, the importance of CNC in medical device manufacturing will only continue to grow.
Recap of CNC Machining's Role in Medicine
CNC stands for Computer Numerical Control, which revolutionizes how we approach medical device machining. What is CNC in medical terms? It refers to the automated process of controlling machine tools through computer programming, allowing for unmatched precision and repeatability in producing intricate parts used in healthcare applications. From surgical instruments to diagnostic equipment, CNC machines ensure that every component meets rigorous specifications essential for patient safety.
The Evolution of Medical Device Manufacturing
The manufacturing process for medical devices has transformed dramatically over the years due to advancements like CNC technology. Initially labor-intensive and prone to human error, today's processes are streamlined and efficient, thanks to automation and sophisticated software integration. This evolution not only improves production speed but also enhances quality control measures within the realm of medical machining.
Final Thoughts on the Future of CNC in Healthcare
Looking ahead, it’s clear that innovations such as 3D printing and artificial intelligence will further enhance what is a CNC medical landscape already rich with possibilities. The push for automation will likely lead to even more sophisticated methods for creating custom solutions tailored specifically for individual patients' needs—think personalized prosthetics or bespoke surgical instruments! As sustainability becomes increasingly important in all industries, including pharmaceutical manufacturing, integrating eco-friendly practices into CNC operations will be essential as we strive for a healthier future.