Introduction
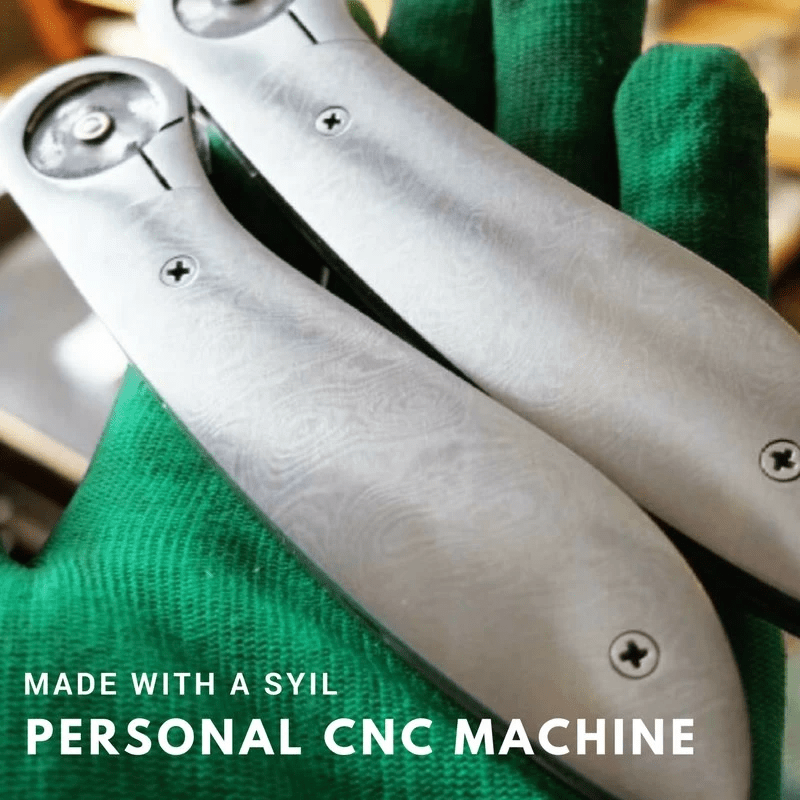
Are you intrigued by the art of cnc knife making? Whether you're a seasoned knife maker or just starting out, CNC technology has revolutionized the process of crafting high-quality knives. With the right tools and materials, safety precautions, and a bit of inspiration, you can create stunning knives with precision and efficiency.
The Basics of CNC Knife Making
CNC knife making involves using computer-controlled machines to cut and shape metal into intricate knife designs. This modern approach allows for precise and consistent results, making it a popular choice among knife makers looking to elevate their craft.
Tools and Materials for CNC Knife Making
To get started in CNC knife making, you'll need a quality CNC machine capable of cutting metal with precision. Additionally, having the right tools such as grinders, sanders, and polishing equipment is essential for finishing your knives to perfection.
Safety Precautions for CNC Knife Making
Working with metal and powerful machinery requires strict adherence to safety protocols. Always wear protective gear such as gloves, goggles, and ear protection when operating a CNC machine for knife making to prevent accidents or injuries.
Finding Inspiration for Your CNC Knife Designs
From traditional patterns to modern innovations, there's no shortage of inspiration when it comes to designing your own custom knives. Explore different styles, shapes, and materials to spark creativity in your CNC knife designs.
Tips for Getting Started in CNC Knife Making
If you're new to the world of cnc machine cutting for knife making, start by familiarizing yourself with the basics of CAD/CAM software and programming techniques. Practice on scrap metal before tackling your first official project to build confidence in your skills.
Choosing the Right CNC Knife Cutting Machine
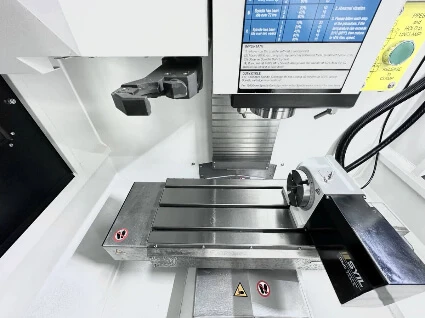
When it comes to CNC knife making, choosing the right cutting machine is crucial for achieving precision and efficiency. There are different types of CNC knife cutting machines available, including plasma, waterjet, and laser cutters. Each type has its own advantages and limitations, so it's important to understand the differences before making a decision.
Understanding the Different Types of CNC Knife Cutting Machines
Plasma cutters are ideal for cutting through electrically conductive materials like steel and aluminum, while waterjet cutters use a high-pressure stream of water mixed with abrasive particles to cut through a variety of materials. Laser cutters, on the other hand, use a focused beam of light to melt or vaporize material in a precise pattern. Understanding these differences will help you choose the right machine for your specific needs in CNC knife making.
Features to Look for in a CNC Knife Cutting Machine
When selecting a CNC knife cutting machine, there are several key features to consider. Look for machines with high precision and accuracy, as well as advanced control systems that allow for intricate designs and complex cuts. Additionally, consider the size and capacity of the machine to ensure it can accommodate your desired projects.
Benefits of Using a SYIL CNC Machine for Knife Making
Using a SYIL CNC machine for knife making offers numerous benefits such as high-speed cutting capabilities, exceptional accuracy, and ease of operation. SYIL machines are designed to handle metal cutting with precision, making them an ideal choice for creating custom knives with intricate designs. With their user-friendly interface and advanced features, SYIL machines streamline the process of CNC knife making.
Designing and Programming Your CNC Knife
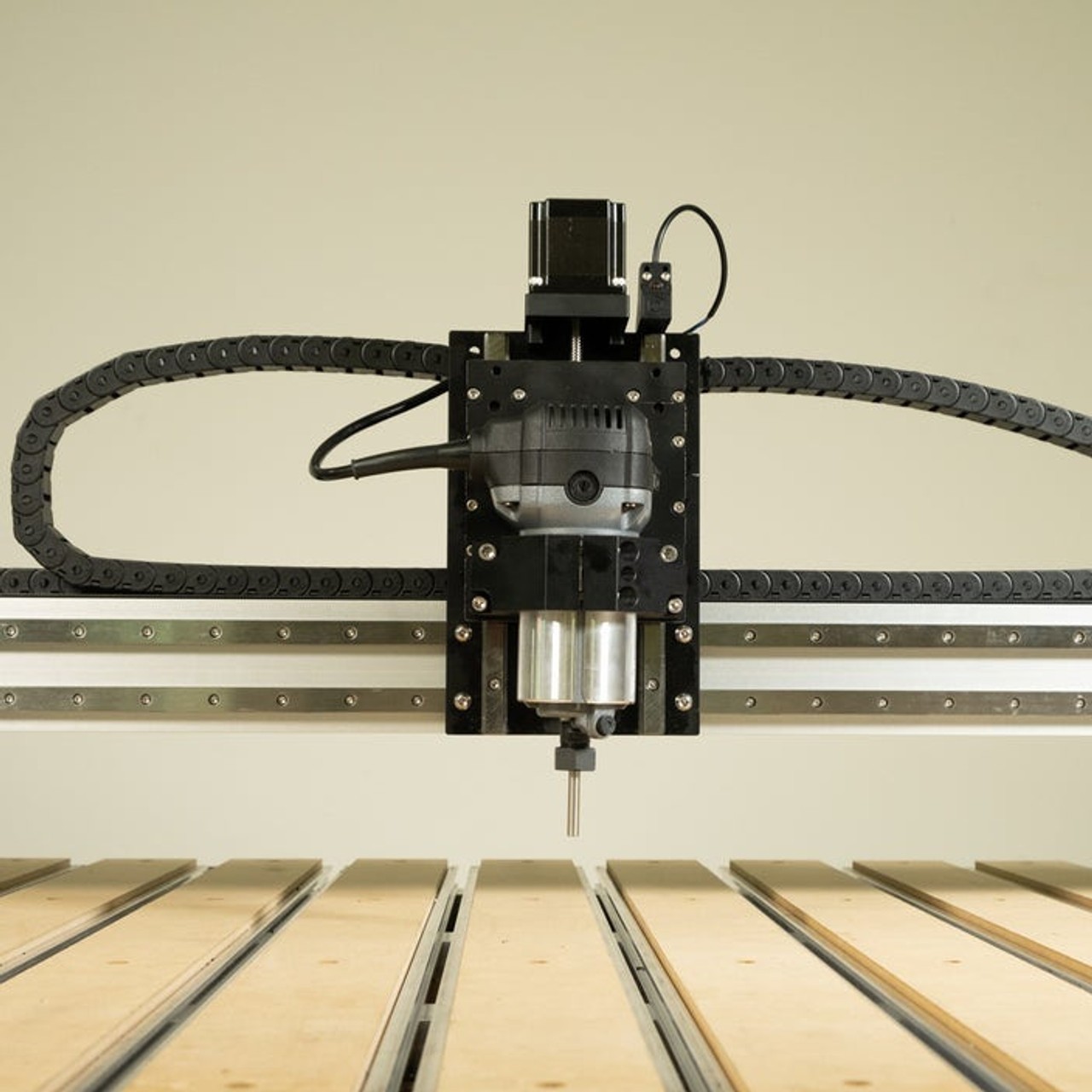
When it comes to designing and programming your CNC knife, there are several software options available that cater specifically to the needs of knife makers. Programs like Fusion 360, SolidWorks, and AutoCAD offer a wide range of design and programming features that can help bring your knife designs to life with precision and efficiency.
Software Options for Designing and Programming CNC Knives
Fusion 360 is a popular choice for its user-friendly interface and comprehensive design tools, making it ideal for creating intricate designs for CNC knives. SolidWorks is another great option known for its powerful modeling capabilities, while AutoCAD offers precise drafting tools perfect for programming your CNC knife cutting machine.
Tips for Creating Intricate Designs for CNC Knives
When creating intricate designs for your CNC knives, consider the functionality and aesthetics of the blade while also paying attention to the ergonomics of the handle. Utilize the software's advanced features like parametric modeling and simulation to ensure that your designs are not only visually appealing but also practical and functional.
Maximizing Efficiency in CNC Knife Programming
To maximize efficiency in CNC knife programming, take advantage of the software's automation capabilities such as toolpath optimization and nesting features. This will help streamline the cutting process, minimize material waste, and ultimately save time and resources in producing high-quality knives with your CNC machine.
Material Selection for CNC Knife Making
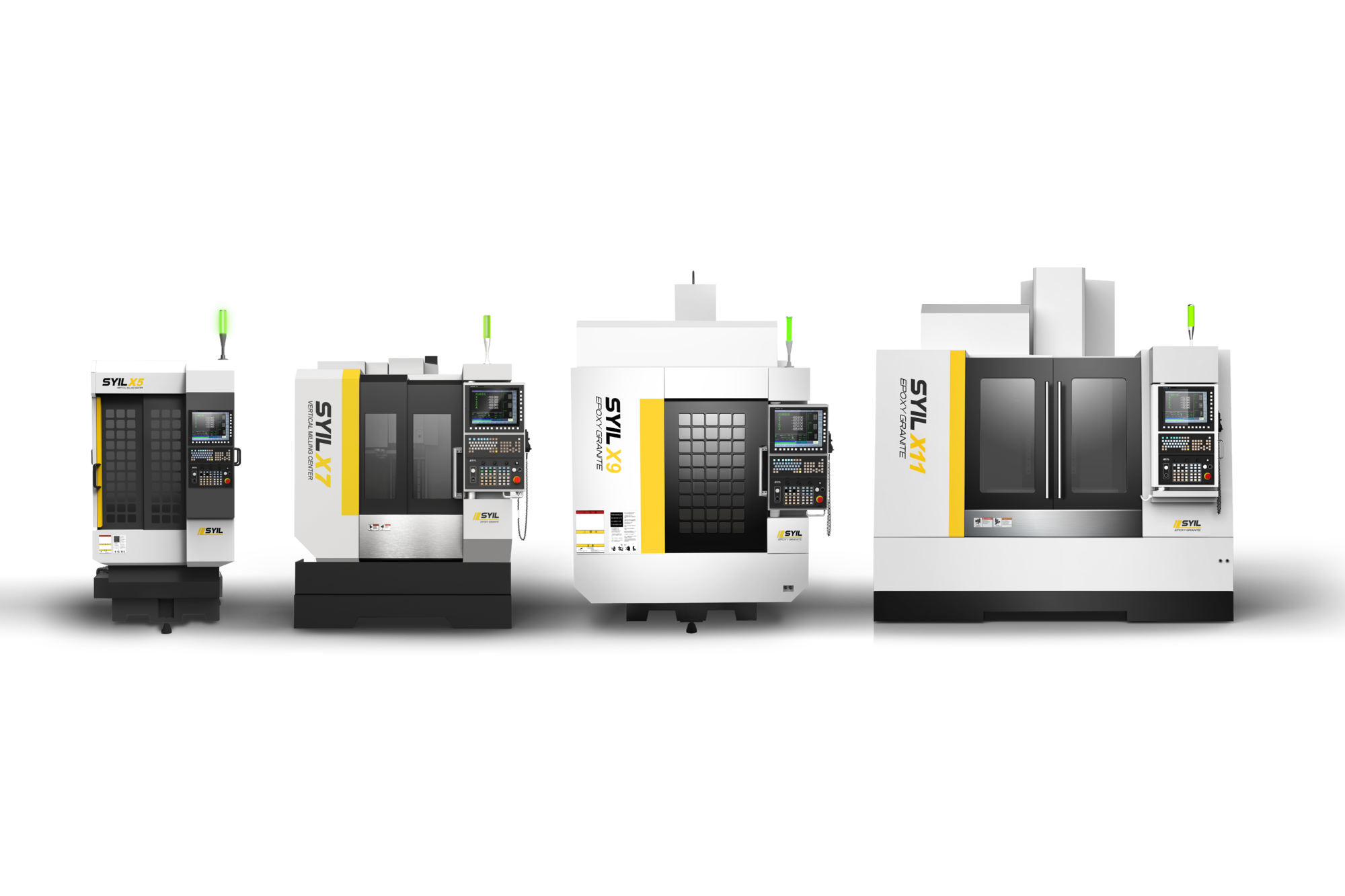
When it comes to choosing the right metal for your CNC knife, it's important to consider factors such as durability, edge retention, and corrosion resistance. Stainless steel is a popular choice for its strength and resistance to rust, while high carbon steel offers excellent edge retention. Titanium is another option known for its lightweight yet durable properties, making it ideal for EDC (everyday carry) knives.
Choosing the Right Metal for Your CNC Knife
When selecting a metal for your CNC knife, consider the intended use of the knife and the properties of different metals. For example, if you're making a kitchen knife, you may want to prioritize corrosion resistance and ease of sharpening. On the other hand, if you're crafting a hunting or survival knife, you might prioritize toughness and edge retention.
Understanding the Properties of Different Metals for Knife Making
Different metals have unique properties that can greatly impact the performance and longevity of your CNC knife. For instance, stainless steel is known for its resistance to corrosion and staining, while high carbon steel offers superior hardness and edge retention. Understanding these properties will help you make informed decisions when selecting materials for your CNC knives.
Tips for Cutting Metal with a SYIL CNC Machine
When using a SYIL CNC machine to cut metal for your knives, it's important to ensure that the machine is equipped with the appropriate cutting tools and settings. Proper tooling selection and machine calibration are crucial in achieving precise cuts without damaging the material or compromising its integrity.
Precision Cutting Techniques for CNC Knife Making
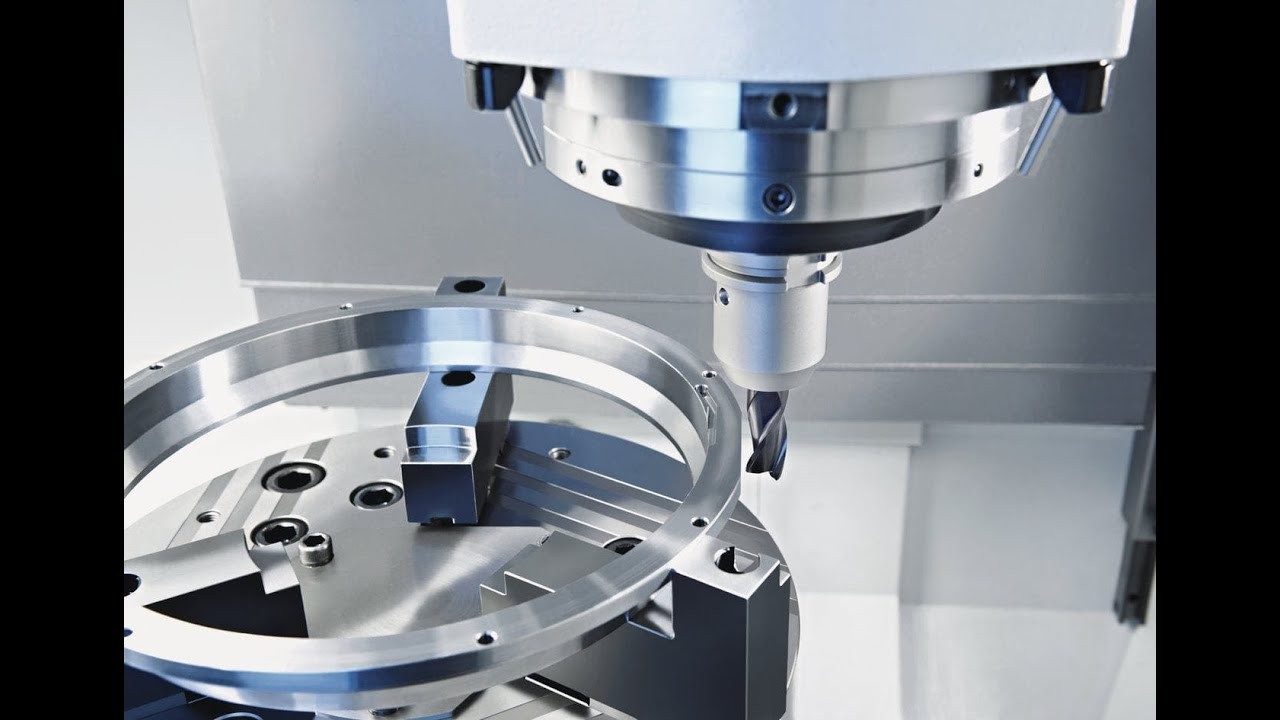
Fine-tuning Your CNC Knife Cutting Process
To ensure the highest quality in your CNC knife making, it's crucial to fine-tune your cutting process. This involves adjusting the cutting speed, feed rate, and depth of cut to achieve the desired results. By experimenting with different settings on your CNC machine, you can optimize the cutting process for each specific knife design.
Once you have found the optimal settings for your CNC machine, it's important to regularly maintain and calibrate the equipment to ensure consistent performance. Regularly checking and replacing worn-out cutting blades, as well as keeping the machine clean and free of debris, will help prevent any issues that could affect the quality of your knife cuts. Additionally, conducting routine checks on the machine's lubrication and cooling systems will help prolong its lifespan and maintain its precision.
Achieving Smooth and Clean Cuts with a CNC Machine
One of the key advantages of using a CNC machine for knife making is its ability to achieve incredibly smooth and clean cuts. By using high-quality cutting tools and maintaining them properly, you can ensure that your CNC machine consistently delivers precise and flawless cuts on various metals used for knife making. This results in professional-looking knives that are ready for finishing and assembly.
Another benefit of using a CNC machine for knife making is the ability to maximize accuracy in the cutting process. The precision and consistency of the machine allow for intricate designs and complex shapes to be cut with ease, resulting in knives that are not only visually appealing but also functional. This level of accuracy ensures that each knife meets the highest standards, making them stand out in a competitive market.
Maximizing Accuracy in CNC Knife Cutting
Accuracy is paramount when it comes to CNC knife making, as even the slightest deviation from the design specifications can affect the functionality and aesthetics of the final product. To maximize accuracy in CNC knife cutting, regularly calibrate your machine, use proper fixturing techniques, and pay close attention to toolpath planning to minimize errors and achieve precise cuts every time.
In addition to machine calibration and fixturing techniques, it is essential to use high-quality cutting tools and materials to ensure precision in CNC knife cutting. Investing in sharp, durable blades and premium-grade materials can significantly reduce the risk of errors and produce cleaner, more accurate cuts. By prioritizing the quality of your tools and materials, you can elevate the overall craftsmanship of your CNC knife making process and deliver exceptional results that meet or exceed design specifications.
Finishing and Assembly of CNC Knives
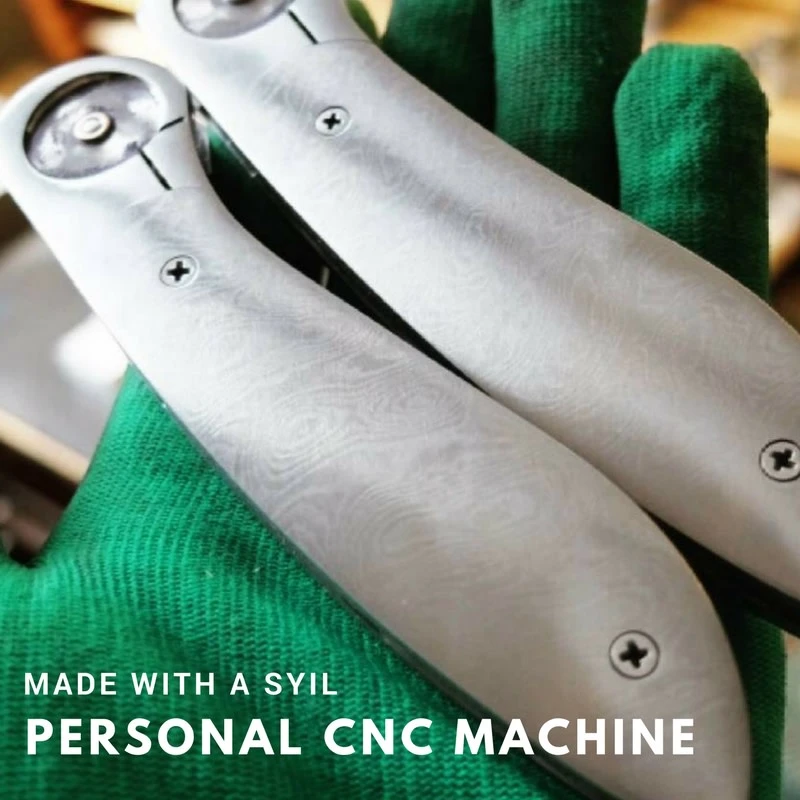
When it comes to finishing the blades of your CNC knives, there are several techniques you can use to achieve a polished and professional look. Consider using sandblasting or acid etching to create unique textures and patterns on the metal. Additionally, you can experiment with different surface finishes such as satin, mirror, or stonewash for a personalized touch.
Surface Finishing Techniques for CNC Knife Blades
To achieve a smooth and refined finish on your CNC knife blades, you can utilize sandblasting to remove any imperfections and create a uniform texture. Another technique is acid etching, which allows you to create intricate designs and patterns on the metal surface. Experimenting with different surface finishes such as satin, mirror, or stonewash can add a unique touch to your finished CNC knives. Additionally, you can consider using tumbling or vibratory finishing methods to further enhance the appearance and feel of the blades. These techniques help in smoothing out any rough edges and creating a polished look that is both visually appealing and functional.
Assembling and Testing Your Finished CNC Knife
Once you have completed the cutting and finishing processes, it's time to assemble your finished CNC knife. Carefully attach the blade to the handle using high-quality adhesive or mechanical fasteners. After assembly, perform rigorous testing to ensure that the knife is structurally sound and functions as intended before moving on to the final step.
After assembling your CNC knife, it's crucial to perform rigorous testing to ensure its structural integrity and functionality. This involves checking for any loose components, ensuring the blade is securely attached to the handle, and testing the sharpness of the blade. Additionally, make sure that the knife opens and closes smoothly if it's a folding knife, and that all mechanisms are working properly. By conducting thorough testing, you can identify any potential issues and make necessary adjustments before moving on to the final step.
Tips for Maintaining and Caring for CNC Knives
Proper maintenance is essential for ensuring the longevity of your CNC knives. Regularly clean the blades with mild soap and water to remove any dirt or residue. Additionally, consider applying a thin layer of oil to prevent corrosion and maintain sharpness. Store your knives in a dry environment away from moisture to preserve their quality over time.
After cleaning and oiling your CNC knives, it's important to handle them with care during use. Avoid using excessive force or twisting the blades, as this can cause damage and reduce their effectiveness. Additionally, be sure to use the right knife for the task at hand to prevent unnecessary wear and tear. By treating your CNC knives with respect and using them appropriately, you can extend their lifespan and maintain their cutting edge.
Conclusion
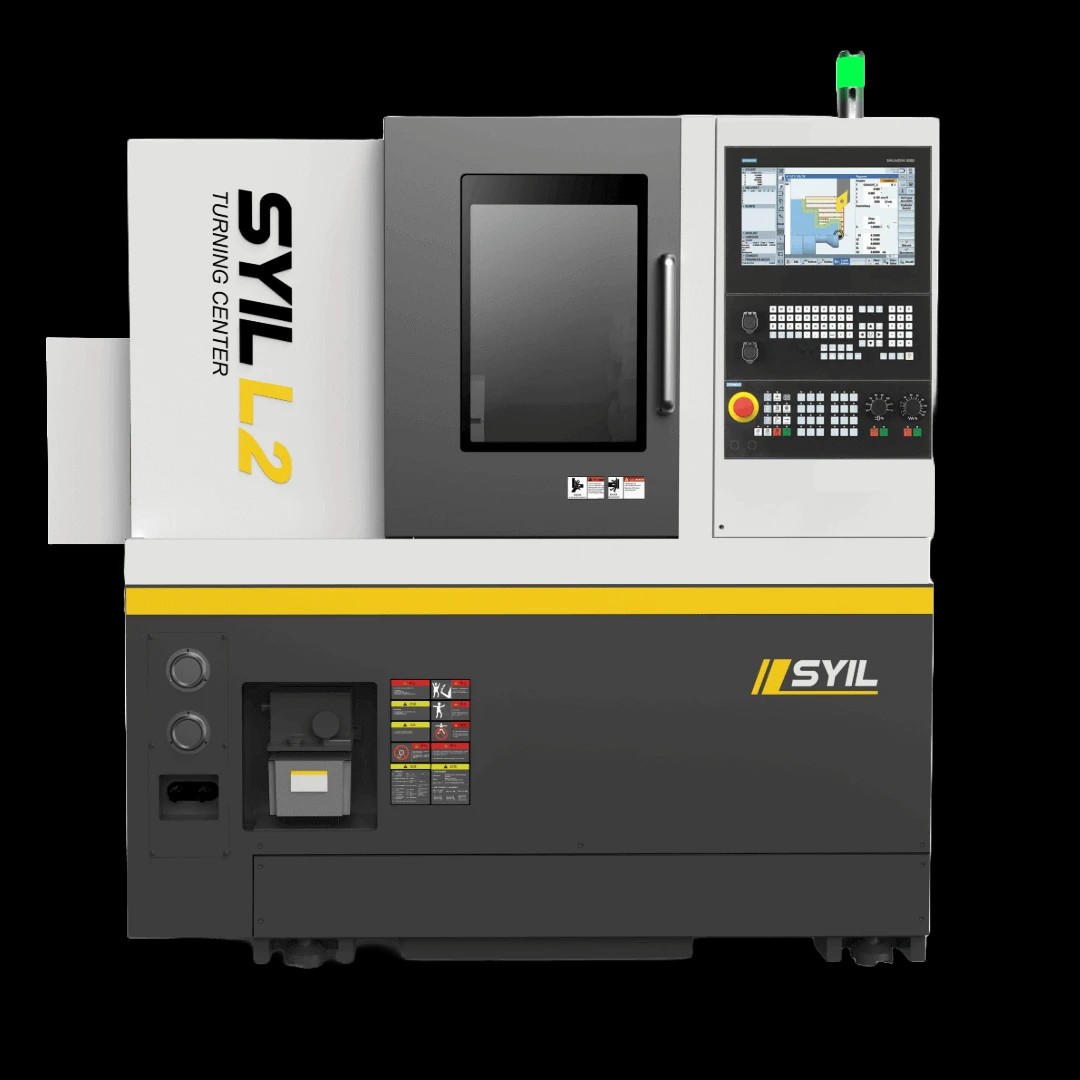
Embracing Innovation in CNC Knife Making
In the world of CNC knife making, embracing innovation is key to staying ahead of the curve. With the rapid advancements in technology, it's important to stay updated on the latest tools and techniques for creating high-quality knives. By constantly seeking new ways to improve your craft, you can elevate your CNC knife making skills to new heights.
In addition to staying updated on the latest tools and techniques, exploring creativity in CNC knife designs can set your work apart from the competition. By experimenting with unique shapes, patterns, and materials, you can create knives that are not only functional but also visually striking. This creative approach can help you establish a distinct brand identity and attract a wider audience of knife enthusiasts who appreciate the artistry behind your designs.
Exploring Creativity in CNC Knife Designs
Creativity is at the heart of CNC knife making. Whether you're designing a sleek modern blade or a traditional masterpiece, there's no limit to what you can create with a CNC machine. By exploring different design ideas and experimenting with unique concepts, you can push the boundaries of what's possible in knife making and set yourself apart from the competition.
Creativity is the driving force behind innovation in CNC knife making. By constantly challenging yourself to think outside the box and come up with new and unique designs, you can stay ahead of the curve in this competitive industry. Embracing creativity also allows you to cater to a wider range of customers, from those who appreciate modern, cutting-edge designs to those who prefer more traditional styles. With a CNC machine at your disposal, the only limit to what you can achieve is your own imagination.
Mastering the Art of CNC Knife Cutting
Mastering the art of CNC knife cutting takes time and dedication. It's about honing your skills, perfecting your technique, and striving for precision in every cut. With a SYIL CNC machine for knife making, you have the power to achieve unparalleled accuracy and finesse in your cuts, allowing you to create flawless knives that stand out from the rest.
With these essential tips and techniques for CNC knife making, you're well-equipped to embark on an exciting journey into the world of precision craftsmanship. Whether you're just starting out or looking to take your skills to the next level, there's always something new to learn and explore in this dynamic field. So go ahead, unleash your creativity, embrace innovation, and master the art of CNC knife cutting!