Introduction

In the world of manufacturing, CNC machining has revolutionized how we produce intricate parts and components. With the ability to automate processes and achieve high precision, understanding the basics of CNC machining is essential for anyone looking to delve into this field. This introduction will explore critical aspects of CNC technology, focusing on the differences between 3 axis and 5 axis configurations.
Understanding CNC Machining Basics
CNC stands for Computer Numerical Control, a technology that automates machine tools through computer programming. At its core, it allows for precise control over various machinery by converting designs into commands that dictate movement and operation. Familiarity with these basics sets the stage for understanding more complex systems like 3 axis vs 5 axis CNC machines.
The Importance of Axis Configuration
Axis configuration plays a pivotal role in determining a CNC machine's capabilities and versatility. The number of axes a machine can operate on directly influences its precision and complexity in handling various tasks. When comparing 3 axis vs 5 axis CNC machines, it's crucial to recognize how these configurations affect production efficiency and overall cost.
Overview of 3 Axis and 5 Axis CNC
3 axis CNC machines operate along three primary axes—X, Y, and Z—allowing for straightforward milling operations ideal for simpler components. On the other hand, 5 axis CNC machines add two additional rotational axes, enabling them to create more complex geometries with higher accuracy. Understanding these differences is vital when considering factors such as price; while a typical 3 Axis CNC machine price may be lower than that of a sophisticated 5-axis model, the investment in advanced technology often pays off in efficiency and versatility.
What is 3 Axis CNC?
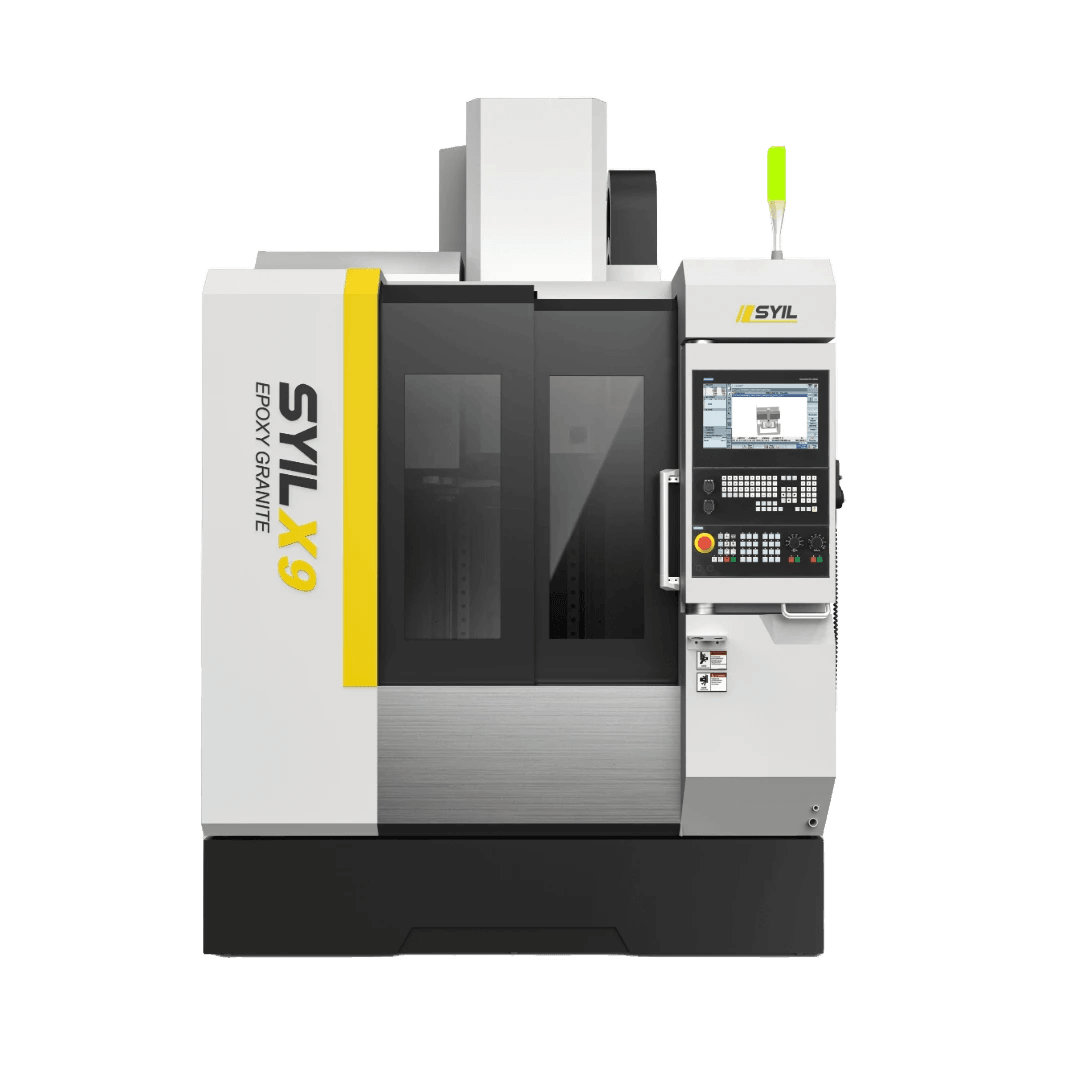
3 Axis CNC refers to a type of computer numerical control machining that operates along three primary axes: X, Y, and Z. This configuration allows the cutting tool to move in three-dimensional space, providing sufficient flexibility for various manufacturing tasks. While it may not be as advanced as its 5-axis counterpart, a 3 Axis CNC machine is often the go-to choice for simpler projects and straightforward geometries.
Mechanism and Functionality
The mechanism behind a 3 Axis CNC machine involves precise movements along the X (left-right), Y (forward-backward), and Z (up-down) axes. The cutting tool is mounted on a spindle that moves according to programmed instructions, allowing for accurate shaping of materials like metal, wood, or plastic. This functionality makes it ideal for tasks such as drilling holes or milling flat surfaces—essentially anything that doesn’t require complex angles or orientations.
Advantages of 3 Axis CNC
One of the most significant advantages of using a 3 Axis CNC machine is its simplicity in operation and programming. Compared to more intricate systems like 4-axis or 5-axis machines, it requires less setup time and offers lower costs—making it an attractive option for small businesses or hobbyists.
Typical Applications in Manufacturing
In manufacturing settings, the versatility of a 3 Axis CNC machine shines through in various applications such as creating prototypes, machining small parts, and producing intricate designs on flat surfaces. Industries like woodworking often utilize these machines for crafting furniture components or decorative elements due to their efficiency and precision in handling simpler tasks.
A Deep Dive into 5 Axis CNC
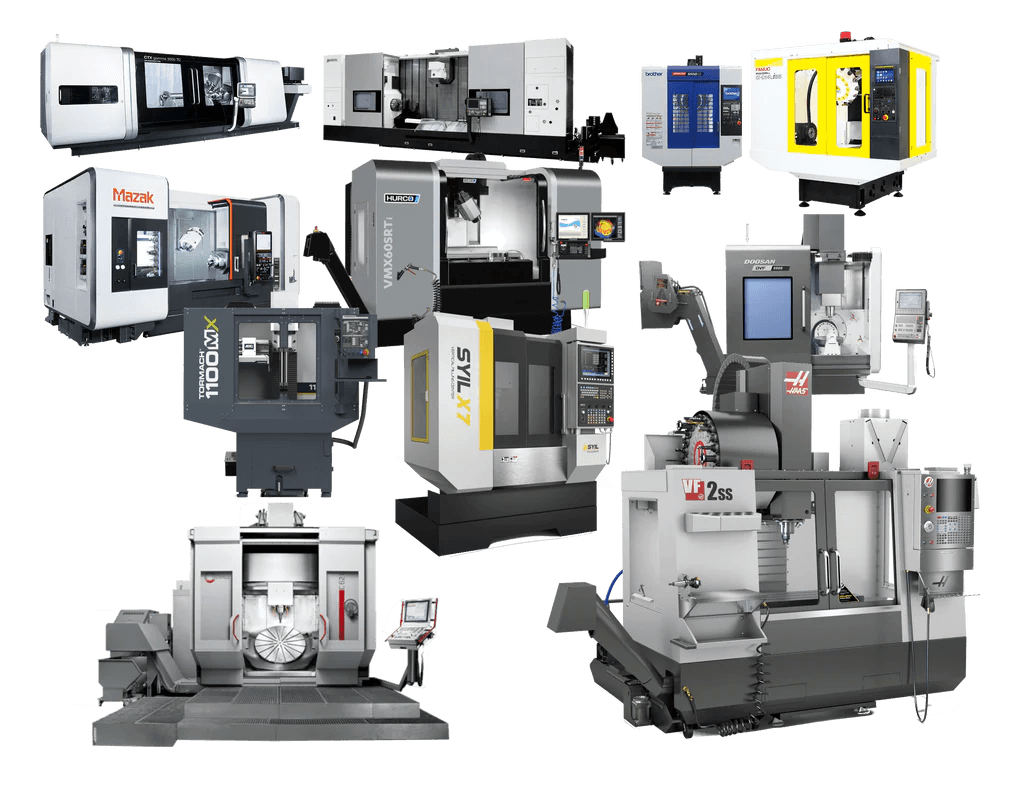
Unlike its 3-axis counterpart, which can only move along three linear paths (X, Y, and Z), a 5 Axis CNC machine adds two additional rotational axes. This capability allows for more complex geometries and reduces the need for multiple setups, ultimately enhancing efficiency.
How 5 Axis CNC Works
At its core, a 5 Axis CNC machine operates by manipulating the cutting tool on five different axes simultaneously. This is achieved through a combination of linear movements (the standard X, Y, Z) and rotational movements around two additional axes—often referred to as A and B or sometimes C. By allowing the tool to approach the workpiece from virtually any angle, manufacturers can achieve intricate designs that would be impossible with traditional 3-axis or even 4-axis machines.
The setup of a typical job on a 5 Axis CNC can be more complex than that of a simple 3 axis setup; however, once configured correctly, it significantly minimizes repositioning time during machining operations. This feature not only enhances productivity but also maintains high levels of accuracy throughout the process.
3 Axis vs 5 Axis CNC: The Key Differences
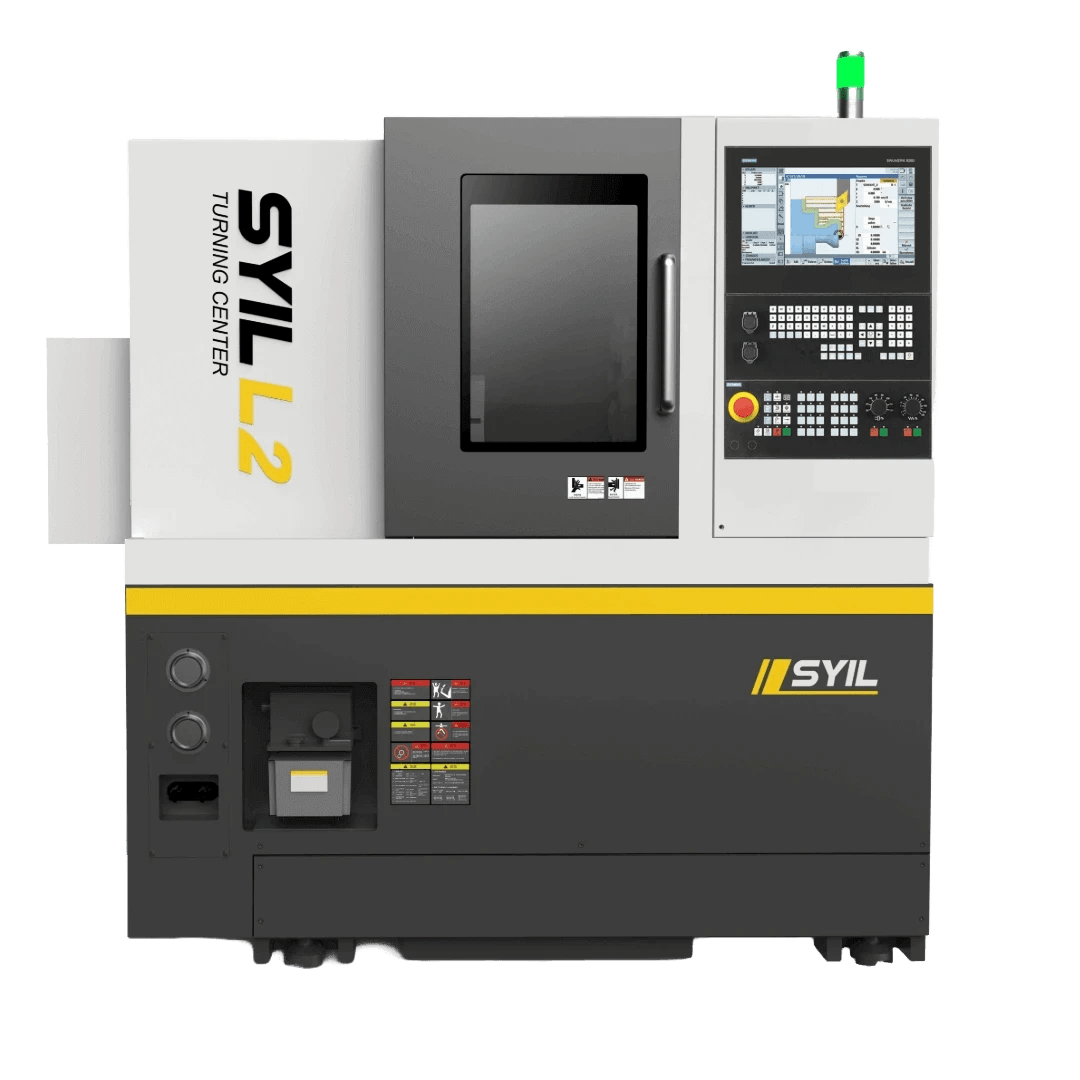
When it comes to CNC machining, the choice between 3 axis and 5 axis systems can significantly impact precision, complexity, and overall manufacturing efficiency. Understanding the key differences helps businesses make informed decisions tailored to their specific needs. Let's dive into the nuances of these two configurations to see how they stack up against each other.
Precision and Complexity
Precision is often the name of the game in CNC machining, and this is where the debate of 3 axis vs 5 axis CNC really heats up. A 5 axis CNC machine can achieve intricate geometries that a traditional 3 axis setup simply cannot handle due to its limited movement. This added complexity allows for tighter tolerances and more complex designs, making it a go-to for industries like aerospace where precision is non-negotiable.
On the flip side, while a 3 axis CNC machine may not offer the same level of detail as its five-axis counterpart, it excels in simpler tasks that don’t require extensive maneuvering. Its straightforward operation means fewer points of failure, which can be crucial for maintaining production schedules in high-volume manufacturing environments. Thus, when considering precision and complexity, it's essential to evaluate your project's specific requirements before deciding between a 3-axis or a more advanced configuration like a 4-axis or even a full-fledged 12-axis CNC machine.
Setup Time and Cost Analysis
Setup time is another critical factor when comparing 3 axis vs 5 axis CNC systems. Generally speaking, setting up a job on a 5-axis machine takes longer due to its complicated tooling requirements and alignment processes. In contrast, a standard setup on a 3-axis machine tends to be quicker and more user-friendly—ideal for those who prioritize speed over versatility.
Real-World Examples of 3 Axis and 5 Axis CNC
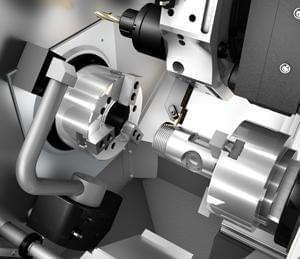
CNC machining is not just a buzzword; it's the backbone of modern manufacturing across various industries. To understand the practical implications of 3 axis vs 5 axis CNC, let’s explore some compelling case studies and applications that highlight their unique advantages. From aerospace to automotive, the choice between different CNC configurations can make all the difference in efficiency and precision.
Case Studies: Aerospace Component Manufacturing
The aerospace industry is a prime example where precision engineering meets cutting-edge technology. In this field, manufacturers often rely on 5 axis CNC machines for complex components like turbine blades and structural parts that require intricate geometries. The ability to machine multiple sides of a workpiece without repositioning enhances accuracy significantly—an aspect where 3 axis vs 5 axis CNC truly shines.
For instance, companies producing aircraft frames have found that utilizing a 5 axis setup reduces production time by up to 30%. This efficiency translates into lower costs per unit when you consider the savings in labor and setup time compared to traditional methods or even a basic 3 Axis CNC machine. The investment in advanced technology pays off handsomely in high-stakes environments like aerospace, where every millimeter counts.
Automotive Industry Applications
In the fast-paced automotive sector, manufacturers are constantly seeking ways to streamline production while maintaining high-quality standards. Here, both 3 axis and 5 axis CNC machines play vital roles but serve different purposes based on complexity and cost considerations. For simpler components such as brackets or housings, a reliable 3 Axis CNC machine is often sufficient; however, for more intricate designs like engine blocks or custom chassis parts, manufacturers turn to the superior capabilities of a 5 Axis system.
A notable trend is the increasing adoption of hybrid setups—where both types coexist—to maximize versatility without breaking the bank on machining costs. The comparison between options also extends into price analysis; while a standard 3-axis CNC machine price may be lower upfront, investing in a more sophisticated system can reduce long-term operational costs significantly when factoring in speed and accuracy improvements.
How SYIL CNC Machines Stand Out
When it comes to distinguishing features among various brands, SYIL machines have carved out a niche with their blend of affordability and advanced functionality. Their offerings include options for both traditional setups like the popular 4-axis models as well as cutting-edge configurations that rival even high-end competitors at competitive prices—making them an attractive choice for small-to-medium enterprises.
With SYIL's focus on user-friendly interfaces combined with robust performance metrics, businesses can easily transition from basic operations using a simple 3-axis CNC vs more complex tasks requiring additional axes without feeling overwhelmed by complexity or cost increases associated with other brands' models. This flexibility allows companies to future-proof their operations as they grow into larger projects requiring either enhanced precision or expanded capabilities.
Choosing the Right CNC for Your Needs
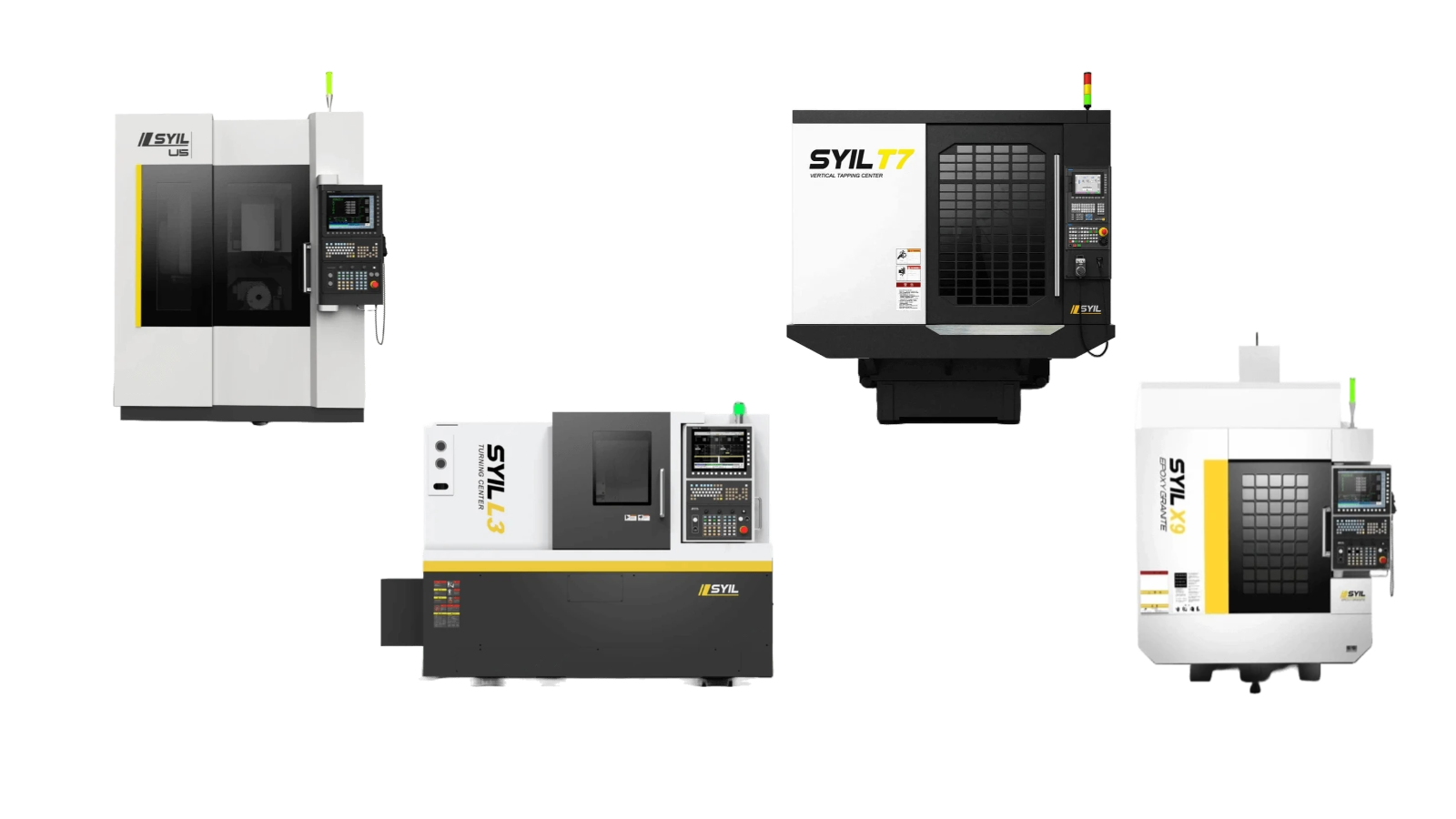
Navigating the world of CNC machining can feel like a maze, especially when deciding between 3 axis and 5 axis CNC configurations. With various factors at play, including project requirements, budget constraints, and future scalability, making an informed choice is crucial. Let’s dive into how to evaluate these aspects effectively.
Evaluating Project Requirements
The first step in choosing between a 3 axis CNC and a 5 axis CNC machine is to assess your specific project needs. If your projects involve simple geometries or straightforward drilling and milling tasks, a 3 Axis CNC might suffice. However, for more intricate designs requiring complex angles and curves, investing in a 5 Axis CNC could be the way to go.
Consider the materials you'll be working with as well; harder materials often benefit from the precision that a 5 Axis setup offers. Additionally, think about production volume—high-volume runs may justify the investment in advanced machinery like a 12 axis CNC machine for enhanced efficiency. Ultimately, aligning your machine choice with project complexity will lead to better outcomes.
Budget Considerations and Cost-Effectiveness
When it comes to budget considerations in the debate of 3 axis vs 5 axis CNC price, it’s essential to factor in both initial investment and long-term operational costs. Generally speaking, while a 3 Axis CNC machine price is lower upfront than its 5 Axis counterpart, you might end up spending more on secondary operations if your projects require additional setups or fixtures.
Moreover, consider maintenance costs associated with each type of machine; higher complexity often means higher upkeep expenses. In this light, analyzing the total cost of ownership rather than just purchase price can provide clearer insights into which option offers better cost-effectiveness over time.
Future-Proofing with Advanced CNC Technology
In an ever-evolving manufacturing landscape, future-proofing your investment becomes paramount—especially when comparing options like a 4-axis vs 5-axis CNC setup. Investing in advanced technology not only enhances current capabilities but also prepares you for future demands as industries evolve towards more complex machining tasks.
A versatile machine such as a multi-axis configuration allows you to adapt quickly without needing substantial reinvestment down the line. As technology progresses and customer expectations rise for precision-engineered products, having that flexibility can set you apart from competitors who are still relying on older machines like traditional 3-axis setups.
Conclusion
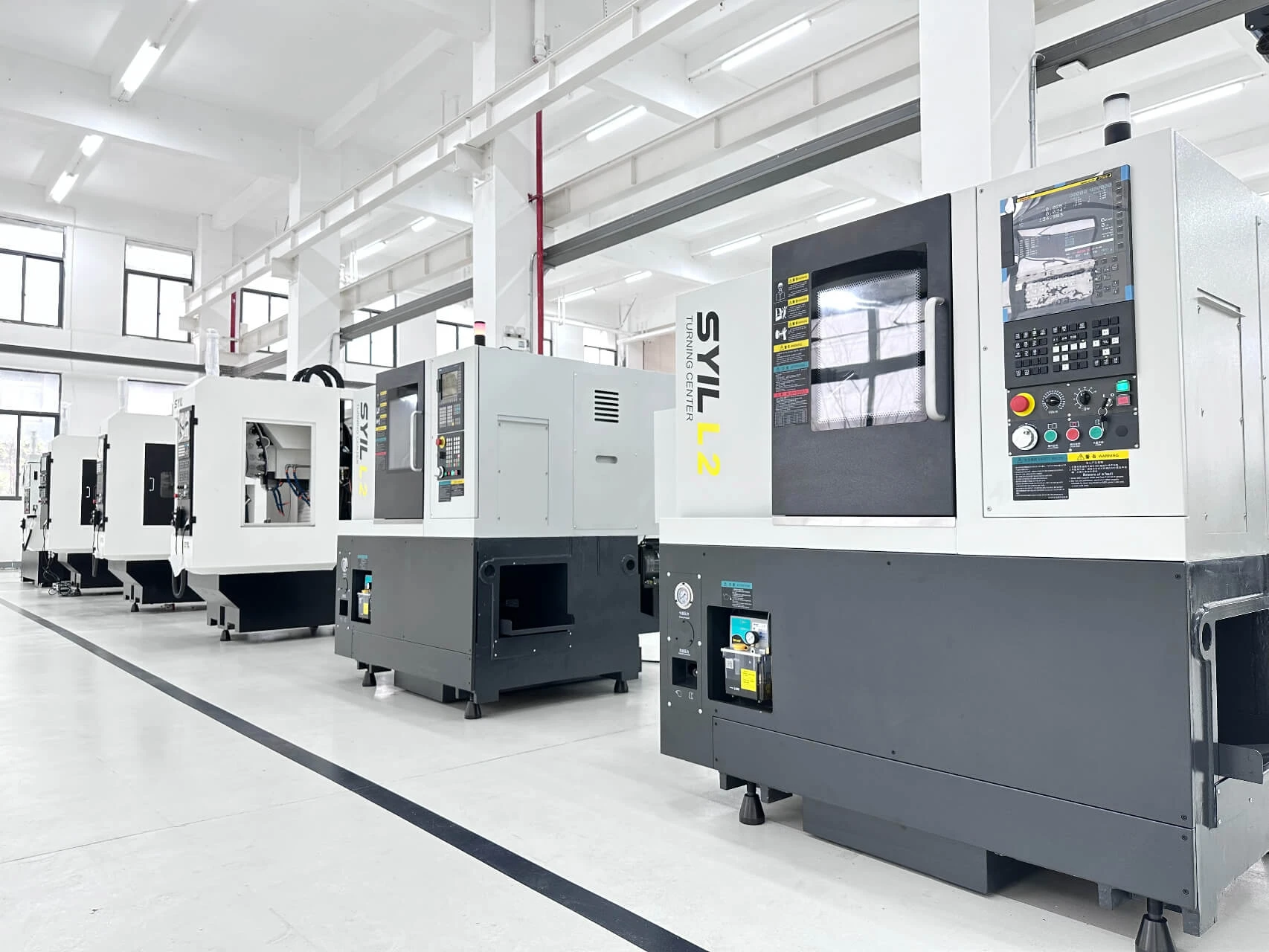
In the world of CNC machining, understanding the nuances between different configurations is crucial for optimizing production processes. The debate of 3 axis vs 5 axis CNC isn't just a matter of numbers; it reflects varying capabilities that cater to distinct manufacturing needs. As we wrap up, let's take a closer look at the advantages of 3 Axis CNC, the superiority of its 5 Axis counterpart, and how you can make informed decisions for your machining projects.
Summarizing 3 Axis CNC Advantages
The primary allure of a 3 Axis CNC machine lies in its simplicity and cost-effectiveness. With straightforward operations limited to moving along three axes—X, Y, and Z—it is often more affordable than its more complex siblings. This makes it an excellent choice for basic tasks like drilling or milling where intricate geometries are not required.
Additionally, the ease of setup and programming allows manufacturers to quickly adapt to changing project requirements without significant downtime or training costs. When considering the 3 axis vs 5 axis CNC price debate, many find that investing in a reliable 3 Axis CNC machine can yield substantial returns for simpler applications. Thus, while it may lack some advanced features, its advantages make it a staple in many workshops.
Highlighting the Superiority of 5 Axis CNC
On the other hand, when we pivot to discuss the superiority of 5 Axis CNC technology, it's clear why many industries are embracing this innovation. The ability to manipulate workpieces from multiple angles dramatically enhances precision and complexity in machining—qualities essential for high-end applications like aerospace components or intricate automotive parts. In this context of 3 axis vs 5 axis CNC comparisons, one can easily see how versatility becomes paramount.
Moreover, with advancements such as a potential future shift towards even more sophisticated configurations like a 12 axis CNC machine or variations like the emerging trends in 4-axis vs 5-axis setups, manufacturers are poised for greater efficiency and accuracy than ever before. The investment in a higher-end system might be reflected in terms of initial cost but pays dividends through reduced cycle times and improved product quality over time.