Introduction

Metal CNC cutting presents unique challenges that require precision and expertise to overcome. Understanding these challenges is crucial for achieving optimal results in the field. CNC routers play a vital role in metal cutting, offering advanced technology and automation to streamline the process. This article will introduce SYIL CNC Machines, a leading provider of precision and sustainable solutions for metal CNC cutting.
Understanding the Challenges of Metal CNC Cutting
Metal CNC cutting involves intricate processes that demand attention to detail. Factors such as material selection and thickness considerations can significantly impact the cutting process's outcome. Heat generation and thermal expansion further complicate matters, requiring careful management to avoid distortions or damage during cutting. Precision and tolerances are critical factors that must be addressed to achieve accurate results.
The Role of CNC Routers in Metal Cutting
CNC routers have revolutionized metal cutting by offering advanced automation and control capabilities. These machines utilize computer numerical control (CNC) technology to precisely execute programmed instructions for cutting operations. By following complex toolpaths with high accuracy, CNC routers ensure consistent results in metal-cutting processes.
SYIL CNC Machines: Precision and Sustainability
SYIL Machine Tools develops and manufactures precision CNC machines for milling and drilling. With over 12k machines supplied globally, they prioritize quality and sustainability. SYIL's range of CNC machines is designed to meet the demands of metal CNC cutting, providing reliable performance, exceptional precision, and eco-friendly features.
In the following sections, we will explore the limitations of metal CNC cutting and how laser cutting services can overcome these challenges. We will also delve into the advantages of metal laser cutting and provide insights on optimizing efficiency in metal CNC cutting processes.
The Limitations of Metal CNC Cutting
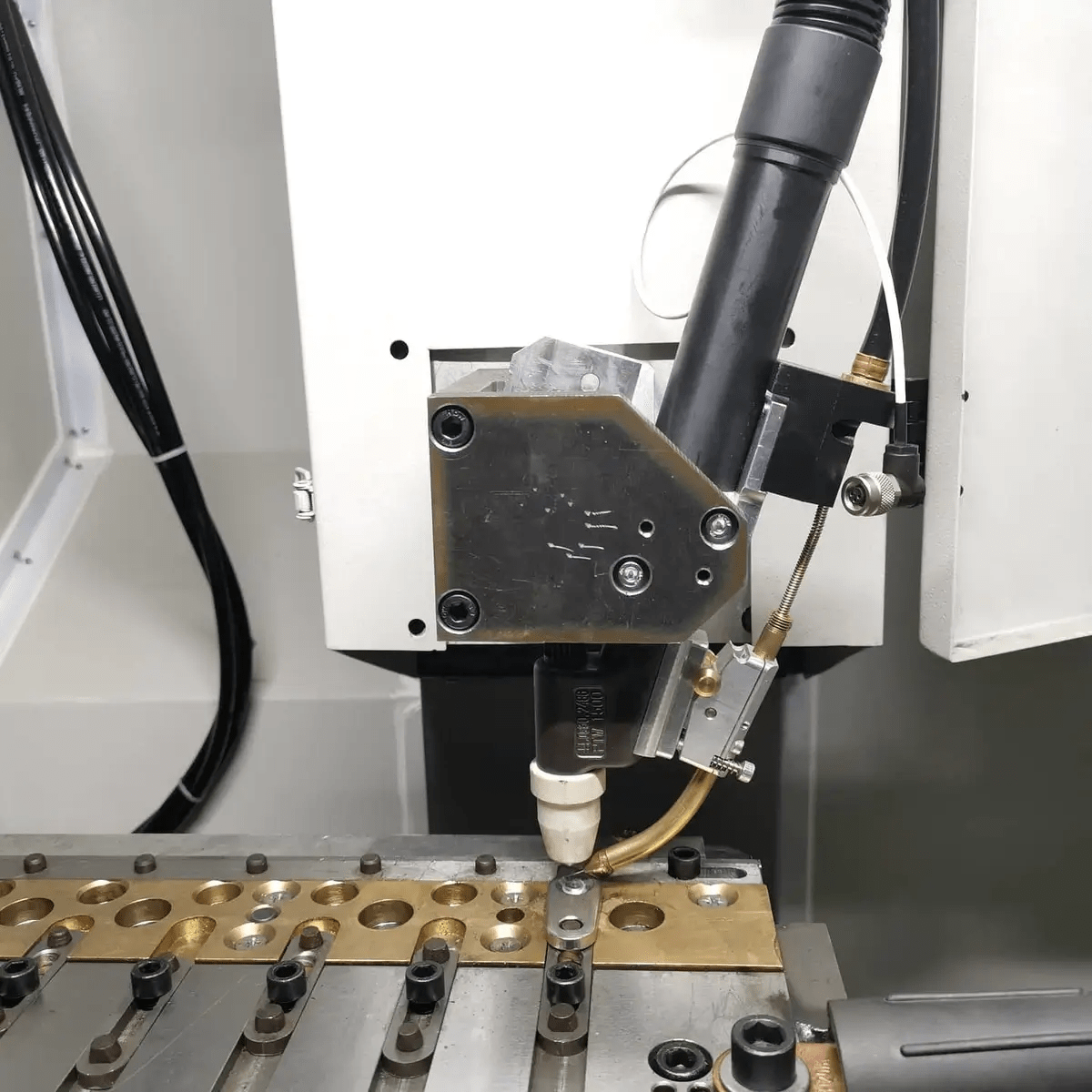
Metal CNC cutting, while a valuable tool in the manufacturing industry, does have its limitations that need to be considered. These limitations include material selection and thickness considerations, heat generation and thermal expansion, and precision and tolerances in metal cutting.
1. Material Selection and Thickness Considerations
When it comes to metal CNC cutting, the choice of material is crucial. Different metals have varying properties that can affect the cutting process. For example, harder metals like stainless steel or titanium may require more powerful machines or specialized tools to achieve the desired results. Additionally, the thickness of the metal being cut significantly determines the appropriate cutting techniques and tools needed for optimal results.
2. Heat Generation and Thermal Expansion
One limitation of metal CNC cutting is heat generation during the cutting process. As the machine cuts through the metal, friction occurs between the tool and the workpiece, resulting in heat buildup. This heat can cause thermal expansion in the tooling and workpiece, leading to potential inaccuracies in the final product. Proper cooling techniques and lubrication are essential to minimize these effects and maintain precision.
3. Precision and Tolerances in Metal Cutting
Another challenge in metal CNC cutting is achieving precise cuts with tight tolerances. The accuracy of each cut is vital for ensuring parts fit together correctly during assembly or fabrication processes. Factors such as machine calibration, tool wear, programming errors, or vibration can all impact precision levels. Implementing best practices such as proper programming optimization and regular quality control inspections can help mitigate these challenges.
Exploring Laser Cutting as an Alternative
Laser cutting utilizes a high-powered laser beam to cut through various materials, including metals. The laser beam is focused and directed by computer-controlled mirrors, allowing for precise and intricate cuts. This technology eliminates physical contact between the cutting tool and the workpiece, reducing heat generation and thermal expansion risks.
Benefits of Laser Cut Metal
Laser cutting offers many advantages for metal fabrication, making it a preferred method over traditional CNC cutting techniques.
- Unmatched Precision: The focused laser beam allows for incredibly precise cuts, enabling intricate details and complex shapes to be produced with minimal margin for error. This reduces the need for rework and improves overall part quality.
- Material Efficiency: Due to laser cutting's high precision, minimal material is wasted during the process. This translates to cost savings for manufacturers, who can utilize more of the raw materials they purchase.
- Reduced Tool Wear: Laser cutting is contactless, unlike traditional cutting methods that rely on physical contact. This eliminates tool wear and tear, ensuring consistent quality throughout the production run and reducing maintenance costs.
Laser-cutting metal offers a combination of precision, material efficiency, and consistent quality, making it a valuable tool for modern metal fabrication.
Precision and Efficiency with Laser Cutting Service Providers
Collaborating with laser cutting service providers can enhance precision and efficiency in metal cutting processes. These specialized companies have state-of-the-art equipment and expertise in handling various metals, thicknesses, and design intricacies. By outsourcing laser cutting services, manufacturers can focus on other aspects of production while ensuring high-quality results.
SYIL Machine Tools develops and manufactures precision CNC machines for milling and drilling. With over 12k machines supplied globally, they prioritize quality and sustainability. SYIL CNC machines offer solutions specifically for metal cutting, including laser CNC cutting options. By utilizing SYIL CNC machines, manufacturers can optimize their metal-cutting efficiency and achieve the desired precision and accuracy in their production processes.
Overcoming Challenges with Laser Cutting Services
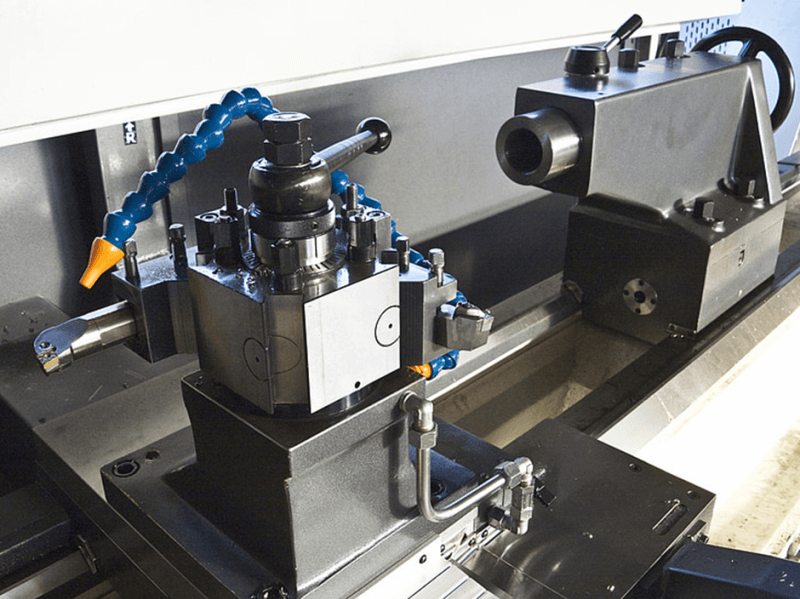
Laser cutting is a viable alternative to traditional metal CNC cutting methods. Using a high-powered laser beam, laser cutting services offer several advantages in precision and efficiency.
Exploring Laser Cutting as an Alternative
When it comes to metal CNC cutting, exploring laser cutting as an alternative can provide manufacturers with numerous benefits. Laser cutting employs a focused laser beam to cut through various metals, offering greater accuracy and flexibility than conventional methods. It can handle intricate designs and complex shapes, opening up new possibilities for metal fabrication.
Benefits of Laser Cut Metal
Laser-cut metal offers several advantages over other cutting techniques. Its precision ensures clean and precise edges, minimizing the need for additional finishing processes. The narrow kerf width allows for minimal material waste, making it a cost-effective option for manufacturers. Additionally, laser-cut metal exhibits minimal distortion and heat-affected zones, preserving the structural integrity of the material.
Precision and Efficiency with Laser Cutting Service Providers
Collaborating with professional laser cutting service providers can enhance precision and efficiency in metal CNC cutting projects. These providers have state-of-the-art equipment that can accurately handle a wide range of materials and thicknesses. Their programming and toolpath optimization expertise ensures optimal results while minimizing production time.
As an industry leader in CNC machine development and manufacturing, SYIL Machine Tools understands the importance of precision and sustainability. With over 12k machines supplied globally, SYIL prioritizes quality and sustainability, offering innovative CNC solutions for milling and drilling. Embrace the future of metal CNC cutting with SYIL's advanced laser CNC machines.
The Advantages of Metal Laser Cutting

Metal laser cutting offers several advantages over traditional CNC cutting methods. These advantages include enhanced cutting speed and accuracy and the versatility of the laser cutting process. SYIL CNC Machines also offers laser CNC cutting solutions, further enhancing the benefits of this technology.
Enhanced Cutting Speed and Accuracy
One key advantage of metal laser cutting is its enhanced cutting speed and accuracy. Laser cutters use a highly focused beam of light to melt or vaporize the cut material, resulting in precise and clean cuts. This process is much faster than traditional CNC cutting methods, allowing for increased productivity and efficiency.
The laser beam can be controlled precisely, ensuring that cuts are made exactly where needed. This level of accuracy is particularly important when working with intricate designs or complex shapes. Manufacturers can achieve precise cuts with minimal errors or wastage with metal laser cutting.
Versatility of Metal Laser Cutting
Another advantage of metal laser cutting is its versatility. Laser cutters can work with various materials, including steel, aluminum, brass, and copper. They can also handle various thicknesses, making them suitable for thin sheets and thick plates.
In addition to their material versatility, laser cutters can easily create intricate designs and patterns. The high level of control provided by the laser beam allows for precise detailing and complex shapes that would be difficult to achieve using other cutting methods.
SYIL CNC: Offering Laser CNC Cutting Solutions
SYIL Machine Tools develops and manufactures precision CNC machines for milling and drilling. With over 12k machines supplied globally, they prioritize quality and sustainability. SYIL CNC Machines also offers various laser CNC cutting solutions that leverage the abovementioned advantages.
By incorporating metal laser cutting technology into its machines, SYIL provides manufacturers with faster production times, higher accuracy levels, and increased design flexibility. These features can significantly improve the efficiency and quality of metal-cutting processes.
Optimizing Metal CNC Cutting Efficiency
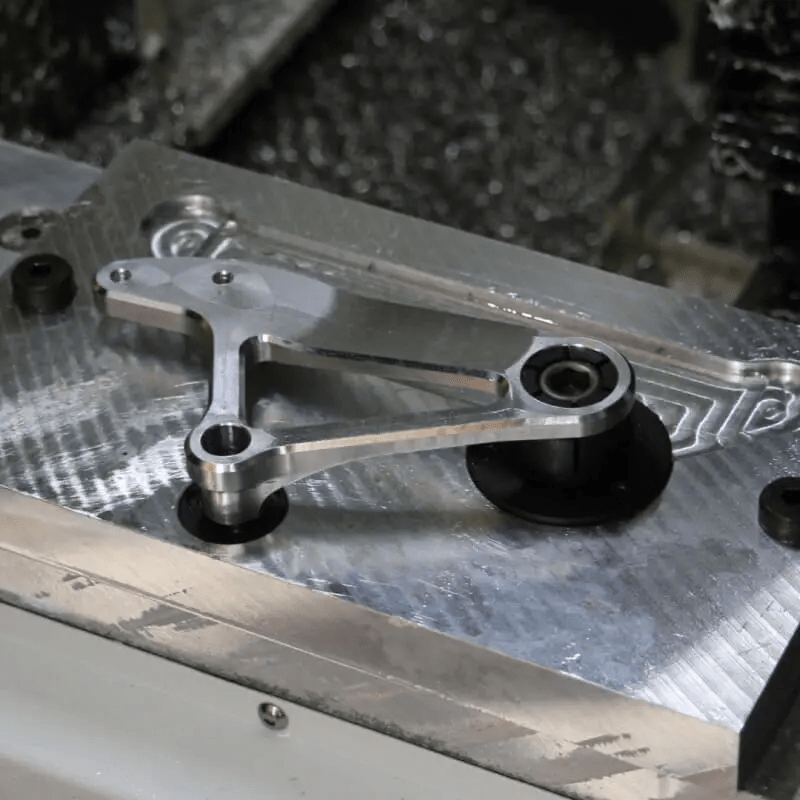
To achieve optimal efficiency in metal CNC cutting, the right cutting tools and techniques must be considered. The choice of tools depends on factors such as the type of metal being cut, its thickness, and the desired precision. High-quality cutting tools with sharp edges and appropriate coatings can significantly improve the cutting process.
Additionally, advanced techniques like high-speed machining or trochoidal milling can enhance efficiency by reducing cycle times and improving chip evacuation. These techniques involve optimizing toolpaths to minimize tool wear and maximize material removal rates.
Proper cooling and lubrication are also essential for optimizing metal CNC cutting efficiency. Cooling helps dissipate heat generated during cutting, preventing tool damage and ensuring dimensional accuracy. Lubrication reduces friction between the tool and workpiece, resulting in smoother cuts and extended tool life.
SYIL CNC Machines offer excellent solutions for milling and drilling in metal cutting applications. Their precision-engineered machines are designed to deliver superior performance while maintaining sustainability standards. With over 12k machines supplied globally, SYIL Machine Tools is a trusted name in the industry.
Implementing Best Practices in Metal CNC Cutting
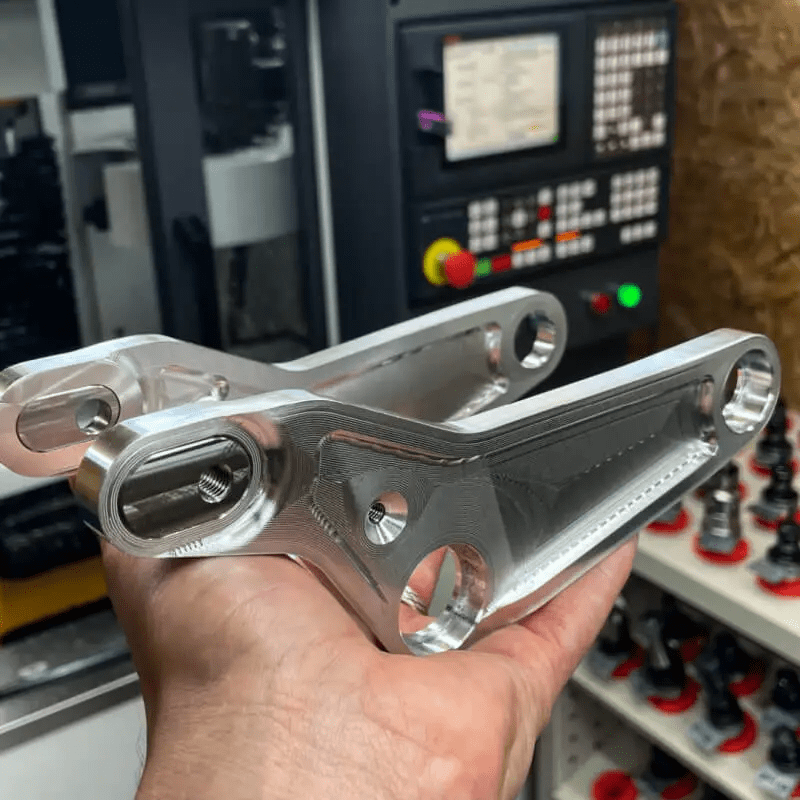
Implementing best practices that encompass proper programming, toolpath optimization, quality control, and inspection processes is crucial to ensuring optimal results in metal CNC cutting. By following these guidelines, manufacturers can achieve precision and efficiency in their cutting operations.
Proper Programming and Toolpath Optimization
Proper programming is vital in metal CNC cutting. It involves creating precise instructions for the machine, ensuring accurate cuts, and minimizing errors. By utilizing advanced software and CAD/CAM systems, manufacturers can generate efficient toolpaths that optimize cutting speed and reduce material waste.
Toolpath optimization is another essential aspect of metal CNC cutting. It involves strategically planning the cutting tool's path to achieve the desired shape or design. By optimizing toolpaths, manufacturers can minimize unnecessary movements, reduce machining time, and enhance overall productivity.
Quality Control and Inspection Processes
Maintaining high-quality standards is crucial in metal CNC cutting to ensure accurate and consistent results. Implementing rigorous quality control measures throughout manufacturing helps identify deviations or defects early on.
Inspection processes involve conducting thorough checks on both raw materials and finished products. This includes verifying material composition, dimensions, surface finish, and quality. Manufacturers can deliver superior products that meet customer expectations by adhering to strict inspection protocols.
SYIL CNC: Supporting Manufacturers in Metal CNC Cutting
SYIL Machine Tools develops and manufactures precision CNC machines for milling and drilling. With over 12k machines supplied globally, they prioritize quality and sustainability. SYIL's range of CNC machines offers advanced features such as high-speed machining capabilities, precise tool positioning accuracy, and user-friendly interfaces.
By partnering with SYIL CNC Machines, manufacturers gain access to cutting-edge technology that enhances their metal CNC cutting operations. With SYIL's expertise in providing reliable solutions for various industries like aerospace, automotive, and electronics, manufacturers can achieve exceptional precision and efficiency in their cutting processes.
Conclusion
The future of metal CNC cutting is bright and promising. With the advancements in technology and the introduction of laser cutting services, manufacturers now have more options to achieve precision and efficiency in metal cutting.
By embracing laser cutting and utilizing SYIL CNC machines, manufacturers can take advantage of the benefits offered by this innovative technology. Laser-cut metal provides enhanced cutting speed and accuracy, allowing for intricate designs and complex shapes to be achieved easily.
SYIL Machine Tools develops and manufactures precision CNC machines for milling and drilling. With over 12k machines supplied globally, they prioritize quality and sustainability. Their laser CNC cutting solutions offer versatility and efficiency in metal cutting processes.
To optimize metal CNC cutting efficiency, choosing the right cutting tools and techniques is crucial. Additionally, proper cooling and lubrication play vital roles in ensuring smooth operations and prolonging tool life. SYIL CNC machines provide milling and drilling solutions that cater specifically to metal cutting needs.
Implementing best practices such as proper programming, toolpath optimization, quality control, and inspection processes can further enhance the results of metal CNC cutting. SYIL CNC supports manufacturers' quest for precision by providing reliable machines that deliver consistent performance.