Introduction
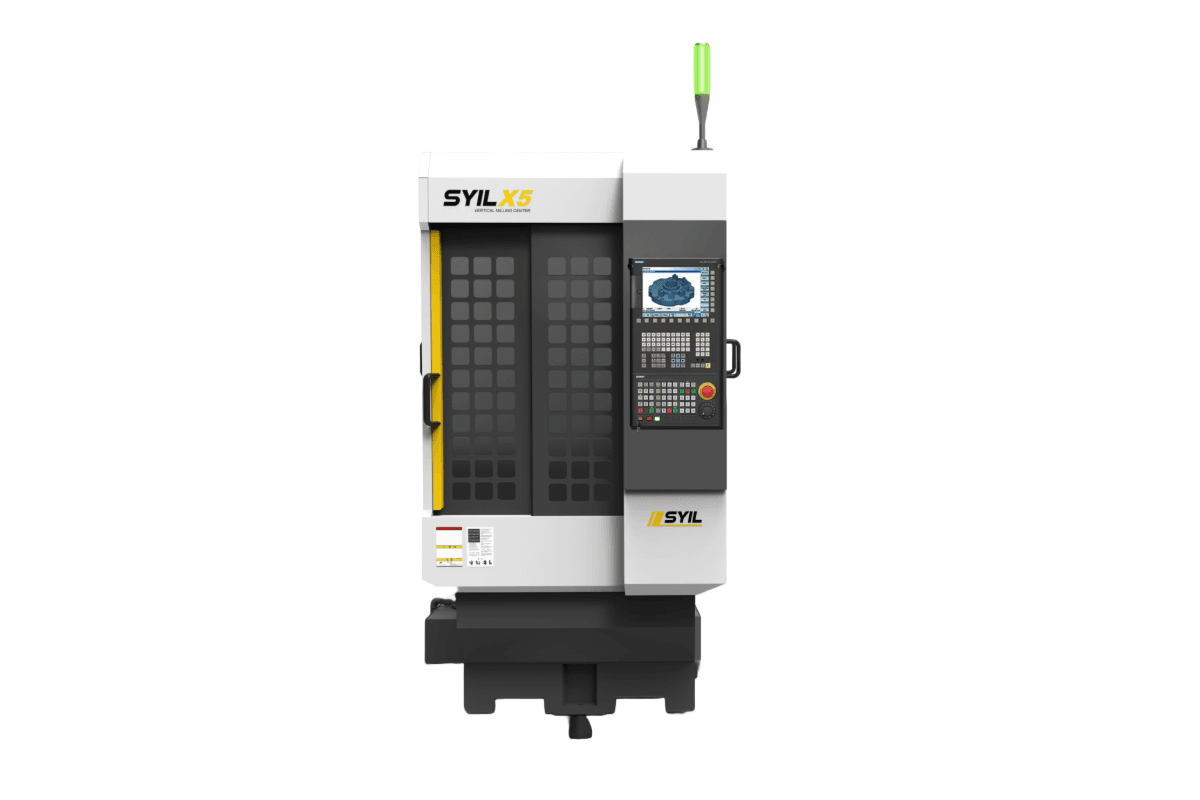
In the fast-paced world of electronics, the evolution of PCB drilling machines has been nothing short of remarkable. These machines have transitioned from rudimentary tools to sophisticated CNC PCB drilling machines equipped with cutting-edge technology. As the demand for precision increases, understanding the nuances of these devices becomes essential for manufacturers aiming to stay competitive in a rapidly changing market.
The Evolution of PCB Drilling Machines
The journey of PCB drilling machines began with manual operations that required significant human intervention and skill. Over time, advancements in technology led to the development of automated CNC PCB drilling machines that dramatically improved efficiency and accuracy. Today, these advanced systems incorporate features such as high-speed spindles and automated tool changers, revolutionizing the PCB drilling process and enabling manufacturers to achieve tighter tolerances than ever before.
Importance of Precision in PCB Drilling
Precision is paramount in PCB manufacturing; even minor inaccuracies can lead to significant functional failures in electronic devices. The quality of the drilled holes directly affects not only the performance but also the reliability of PCBs, making it crucial for manufacturers to invest in high-quality PCB drill sets and bits. With precise drilling, companies can ensure optimal conductivity and effective PCB plating, which are vital for meeting stringent industry standards.
Key Players in the PCB Drilling Market
The landscape of the PCB drilling market is populated by several key players who continuously innovate to meet evolving demands. Leading brands specialize in producing state-of-the-art CNC PCB drilling machines that cater to a variety of applications across industries—from consumer electronics to aerospace. By analyzing their offerings and pricing strategies, especially regarding different models' prices, companies can make informed decisions when investing in their own production capabilities.
Innovative Technologies in PCB Drilling
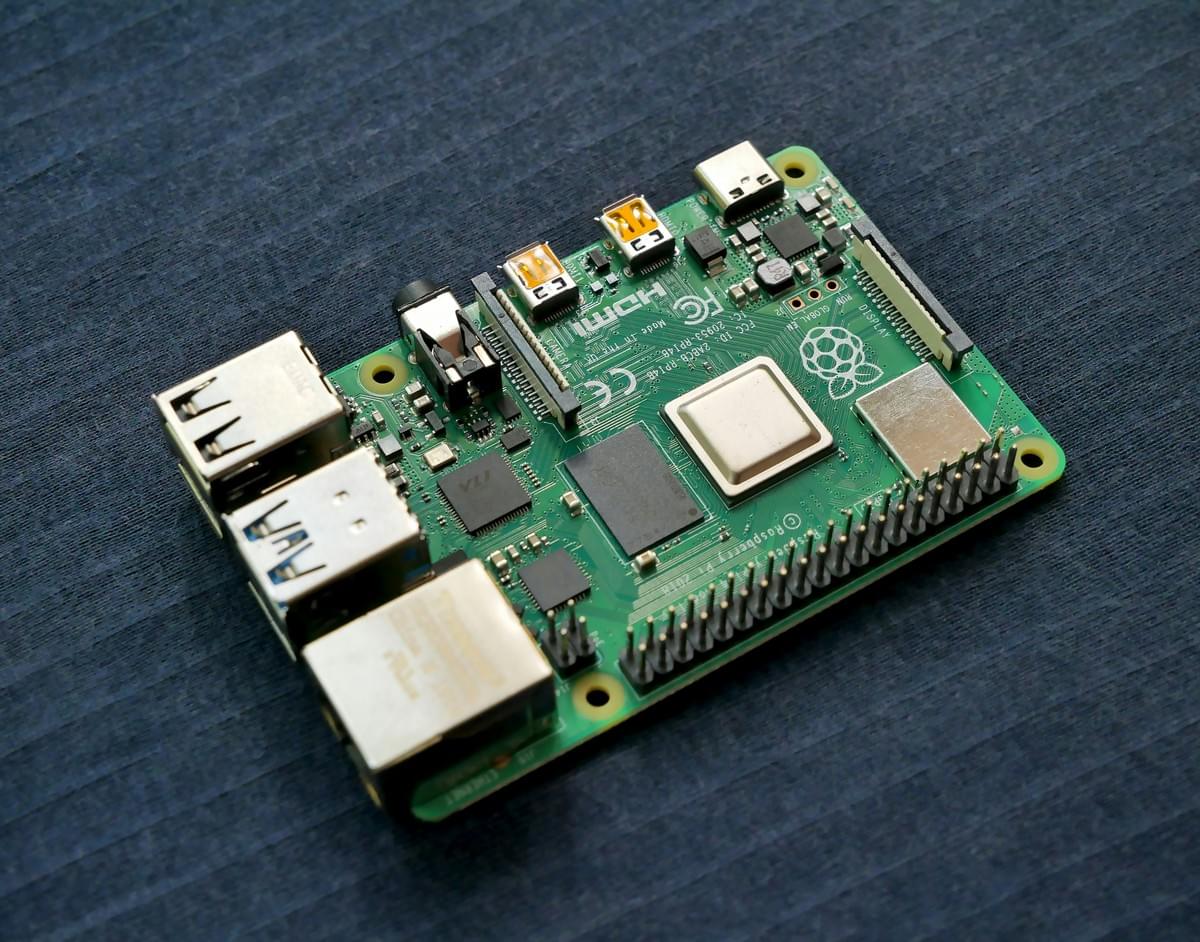
In the fast-paced world of electronics, the evolution of PCB drilling technology is nothing short of remarkable. As manufacturers strive for greater precision and efficiency, innovative technologies have emerged to enhance the capabilities of PCB drilling machines. This section will explore advances in CNC PCB drilling machine capabilities, the integration of AI for better performance, and the role of laser technology in refining the PCB drilling process.
Advances in CNC PCB Drilling Machine Capabilities
CNC (Computer Numerical Control) PCB drilling machines have undergone significant advancements over recent years, enabling them to achieve unprecedented levels of accuracy and speed. These machines can now handle complex designs with multiple layers while maintaining tight tolerances essential for modern electronic applications. Furthermore, improved software interfaces allow operators to program intricate designs more intuitively, reducing setup times and minimizing human error.
The latest CNC models come equipped with advanced features such as automatic tool changers and real-time monitoring systems that enhance productivity during the PCB drilling process. With enhanced spindle speeds and feed rates, these machines can drill through various materials without compromising quality or precision. As a result, manufacturers are increasingly investing in high-performance CNC PCB drilling machines to stay competitive in a demanding market.
Moreover, these technological advancements have also contributed to a decrease in overall production costs. By streamlining operations and reducing waste during the drilling process, companies can optimize their resources while ensuring that they deliver top-quality PCBs at competitive prices. This shift towards automation not only boosts efficiency but also reduces labor costs associated with manual setups.
Integration of AI for Enhanced Efficiency
Artificial Intelligence (AI) is making waves across various industries, and the realm of PCB manufacturing is no exception. By integrating AI into PCB drilling processes, manufacturers can leverage data analytics to predict equipment failures before they occur or optimize drill paths for maximum efficiency. This proactive approach helps minimize downtime and increases overall productivity—two critical factors when considering PCB drilling machine price.
AI-driven algorithms analyze historical data from previous projects to identify patterns that lead to optimal performance outcomes. For example, they can suggest adjustments in speed or feed rates based on material types or specific design requirements—making it easier than ever for operators to achieve precise results with minimal trial-and-error efforts during setup phases. The incorporation of AI not only enhances operational efficiency but also empowers teams by providing valuable insights into workflow improvements.
Furthermore, AI's ability to adapt continuously means that as new technologies emerge or design complexities increase within PCBs themselves, these systems will remain relevant and effective over time. In an industry where staying ahead often hinges on innovation and adaptability, embracing AI technology could be a game-changer for businesses looking to streamline their operations while ensuring product quality remains high throughout every stage of production.
Laser Technology's Role in PCB Drilling Process
These advanced laser systems enable manufacturers to create intricate patterns at micro-scale levels without compromising structural integrity—a crucial factor when designing high-density interconnect (HDI) boards used extensively today across various applications from smartphones to automotive electronics! Additionally; because lasers do not require physical contact with materials being drilled; there’s reduced risk involved regarding contamination issues typically associated with conventional methods involving multiple tools like standard drill bits found within any standard pcb drill set available commercially today!
Moreover; incorporating laser technology reduces waste significantly since it requires less energy than traditional techniques while generating fewer byproducts during operation! By minimizing scrap material generated throughout each cycle—companies benefit financially both immediately through lower costs related directly back towards sourcing new supplies needed regularly plus long-term sustainability goals aimed at reducing environmental footprints overall! Thus highlighting how embracing cutting-edge innovations like this one leads us closer towards achieving both economic viability alongside ecological responsibility simultaneously!
Analyzing PCB Drilling Machine Prices
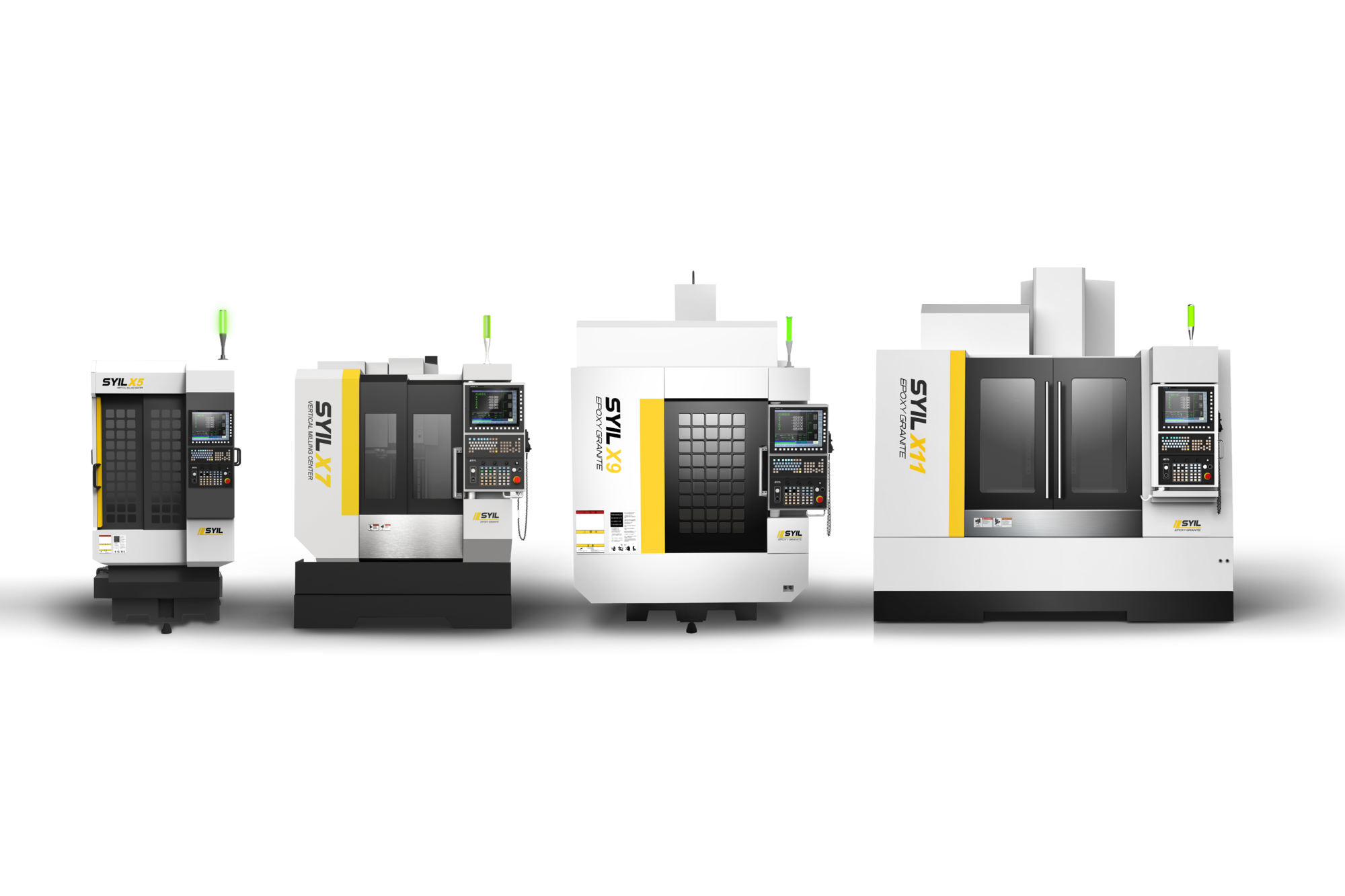
Understanding the pricing of PCB drilling machines is crucial for manufacturers and hobbyists alike. The price of a CNC PCB drilling machine can vary significantly based on various factors, including technology, precision, and brand reputation. By dissecting these elements, potential buyers can make more informed decisions that align with their budget and production needs.
Factors Influencing PCB Drilling Machine Price
Several factors play a pivotal role in determining the price of a PCB drilling machine. First and foremost is the technology used; machines equipped with advanced features like AI integration or laser capabilities typically come at a premium cost. Additionally, the size and complexity of the machine also impact its price—larger machines capable of handling more intricate designs will generally be more expensive than basic models.
Another key factor is brand reputation; established brands often command higher prices due to their reliability and customer support services. Moreover, the materials used in manufacturing the CNC PCB drilling machine influence its durability and performance, which can either justify a higher price tag or lead to budget-friendly alternatives that may not last as long. Finally, market demand can also sway prices; during peak production times, costs may rise due to increased orders for high-quality equipment.
Cost Comparison of Leading Brands
When comparing costs among leading brands in the PCB drilling market, it's essential to look beyond just sticker prices. For instance, while one brand may offer a lower-priced model initially, hidden costs such as maintenance fees or replacement parts could make it less economical in the long run compared to a slightly pricier but more durable option. Additionally, examining features like speed and efficiency can provide insights into which machines offer better value for money over time.
Brands like SYIL stand out not only for their competitive pricing but also for their innovative features that enhance productivity during the PCB drilling process. Other notable competitors might offer specialized models designed for specific applications—these could range from entry-level machines suitable for startups to high-end units intended for large-scale manufacturing operations. Therefore, conducting thorough research into each brand's offerings helps identify which best fits your needs without breaking your budget.
Budget Options for Startups
For startups venturing into PCB production without hefty financial backing, there are several budget-friendly options available that still deliver quality results in the PCB drilling process. Entry-level CNC PCB drilling machines are designed specifically with affordability in mind while maintaining satisfactory performance levels suitable for smaller projects or prototyping tasks. These machines often come bundled with essential components like a basic PCB drill set that includes versatile drill bits tailored to different materials.
Additionally, many manufacturers offer financing options or leasing arrangements that allow startups to access high-quality equipment without upfront capital expenditure concerns—this flexibility can be invaluable when cash flow is tight but demand is high! Furthermore, exploring second-hand markets or refurbished models can yield significant savings while still providing reliable functionality needed for effective production runs.
The Role of PCB Drill Sets in Production
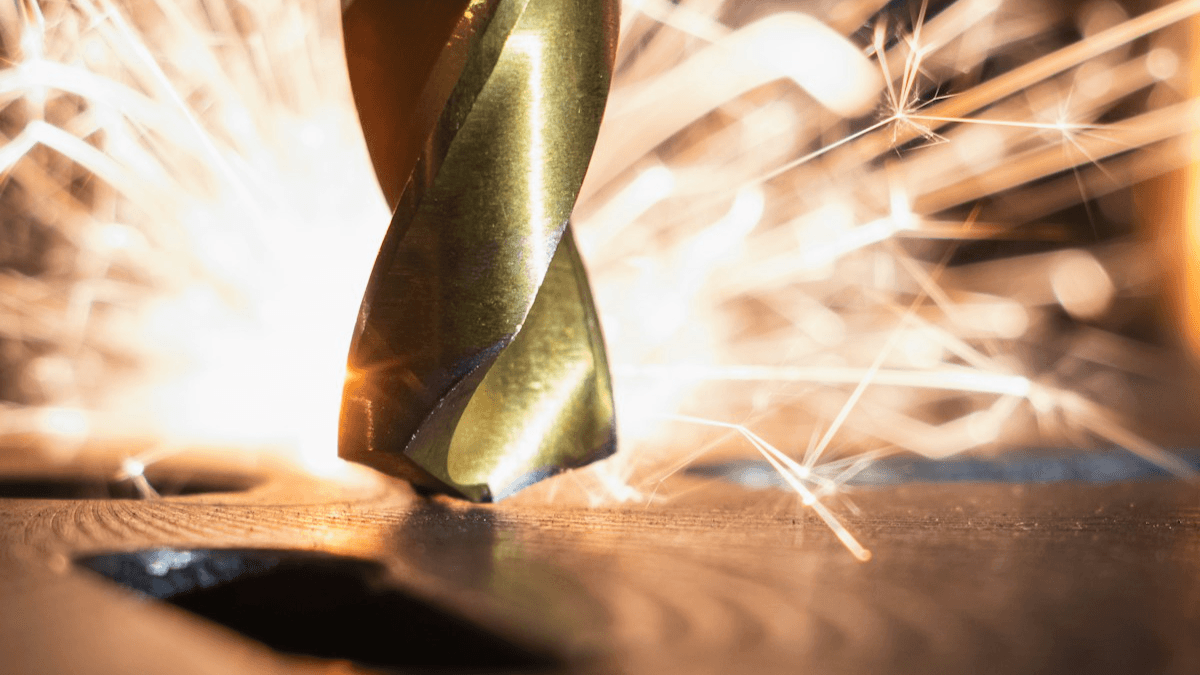
In the world of PCB manufacturing, the importance of a well-equipped PCB drill set cannot be overstated. These sets are crucial for achieving precision and efficiency during the PCB drilling process, directly impacting the overall quality of the final product. A comprehensive understanding of these essential components can significantly enhance production outcomes.
Essential Components of a PCB Drill Set
A typical PCB drill set includes various components that work together to ensure optimal performance. At its core, you'll find specialized PCB drill bits designed for different hole sizes and materials; they are vital for achieving precise drilling results. Additionally, the set usually contains a collet chuck for securing the drill bits firmly in place, ensuring stability during operation with a CNC PCB drilling machine.
Other important elements include depth stops and guide bushings that help maintain consistent hole depths while preventing bit wander during drilling. Each component plays a role in enhancing accuracy and efficiency, which is particularly critical when dealing with intricate designs common in modern PCBs. Investing in high-quality components within your PCB drill set can save time and reduce costs associated with rework or scrapped boards.
Customizing PCB Drill Bits for Different Needs
Customization is key when it comes to selecting PCB drill bits tailored to specific production requirements. Depending on factors such as board thickness, material type, and desired hole diameter, manufacturers may need to adjust their choice of bit accordingly. For example, using carbide-coated bits can significantly improve durability and lifespan when working with tougher materials or high-volume production runs.
Moreover, different coatings can enhance performance by reducing friction and heat buildup during the drilling process. This customization allows companies to achieve better results without compromising on speed or precision—two critical factors that influence overall productivity in any CNC PCB drilling machine setup. Therefore, understanding how to tailor your drill bits effectively is essential for optimizing both quality and cost-effectiveness in your operations.
Best Practices for Maintaining PCB Drill Sets
To ensure longevity and consistent performance from your PCB drill sets, maintenance should be a top priority. Regularly inspecting your drill bits for wear or damage is crucial; dull or chipped bits can lead to inaccuracies in the drilling process that may result in costly errors down the line. It's advisable to keep them clean after each use since debris buildup can affect their performance over time.
Another best practice involves proper storage: keeping your drill bits organized and protected from moisture will help prevent rusting or corrosion that could compromise their integrity. Additionally, calibrating your CNC PCB drilling machine regularly ensures that all components work harmoniously together—this not only maximizes efficiency but also extends the lifespan of both your machine and its accompanying tools like the PCB Drill Set itself. By following these maintenance tips diligently, you’ll keep your production running smoothly while minimizing unexpected costs associated with equipment failure.
Exploring the PCB Drilling Process

The PCB drilling process is a critical step in the production of printed circuit boards, ensuring that all necessary holes are accurately placed for components to be mounted. A thorough understanding of this process can lead to improved efficiency and quality in PCB manufacturing. By mastering the nuances of drilling, manufacturers can enhance their production capabilities while minimizing errors and waste.
Step-by-Step Guide to Effective PCB Drilling
To begin with, effective PCB drilling requires careful preparation and planning. First, ensure that your design files are optimized for the CNC PCB drilling machine; this includes verifying hole sizes and placements as per specifications. Next, select an appropriate PCB drill set that contains the right PCB drill bits for your project—this selection is crucial as different materials may require specific bit types for optimal results.
Once everything is set up, it's time to load the material into the CNC PCB drilling machine securely. The machine should be calibrated correctly to maintain precision throughout the drilling process; any misalignment can lead to costly mistakes down the line. Finally, monitor the operation closely and make adjustments as needed—keeping an eye on drill wear will help you maintain a high standard of quality.
Challenges in the PCB Drilling Process
Despite advancements in technology, several challenges persist within the PCB drilling process that manufacturers must navigate. One common issue is drill bit wear; over time, even high-quality PCB drill bits can degrade, affecting hole accuracy and surface finish. Additionally, managing chip removal effectively during drilling is critical; if chips accumulate too much around holes, they can cause defects or even damage sensitive components.
Another challenge involves maintaining consistent feed rates and speeds across different materials; variations can lead to uneven holes or excessive heat generation that may warp PCBs. Furthermore, operators must remain vigilant about potential misalignments during setup or operation—any slight deviation could result in significant production errors or increased costs due to scrap material. Addressing these challenges requires skilled technicians familiar with both equipment and materials used.
Importance of PCB Plating After Drilling
Once you’ve successfully navigated through the complexities of drilling with your trusty pcb drilling machine, it’s time for an equally important step: plating! The importance of proper pcb plating after drilling cannot be overstated—it enhances conductivity while providing protection against corrosion and mechanical damage. This process also ensures reliable electrical connections between components by filling drilled holes with conductive material.
Moreover, plating serves as a foundation for subsequent processes such as soldering and component attachment; without it, your meticulously drilled holes would be little more than decorative features on a board! Ensuring proper thickness during plating contributes significantly to overall board performance—too thin may not provide adequate conductivity while too thick could affect component placement accuracy negatively. Thus investing in quality plating techniques pays dividends long after initial manufacturing is complete.
Leading Brands and Their Innovations
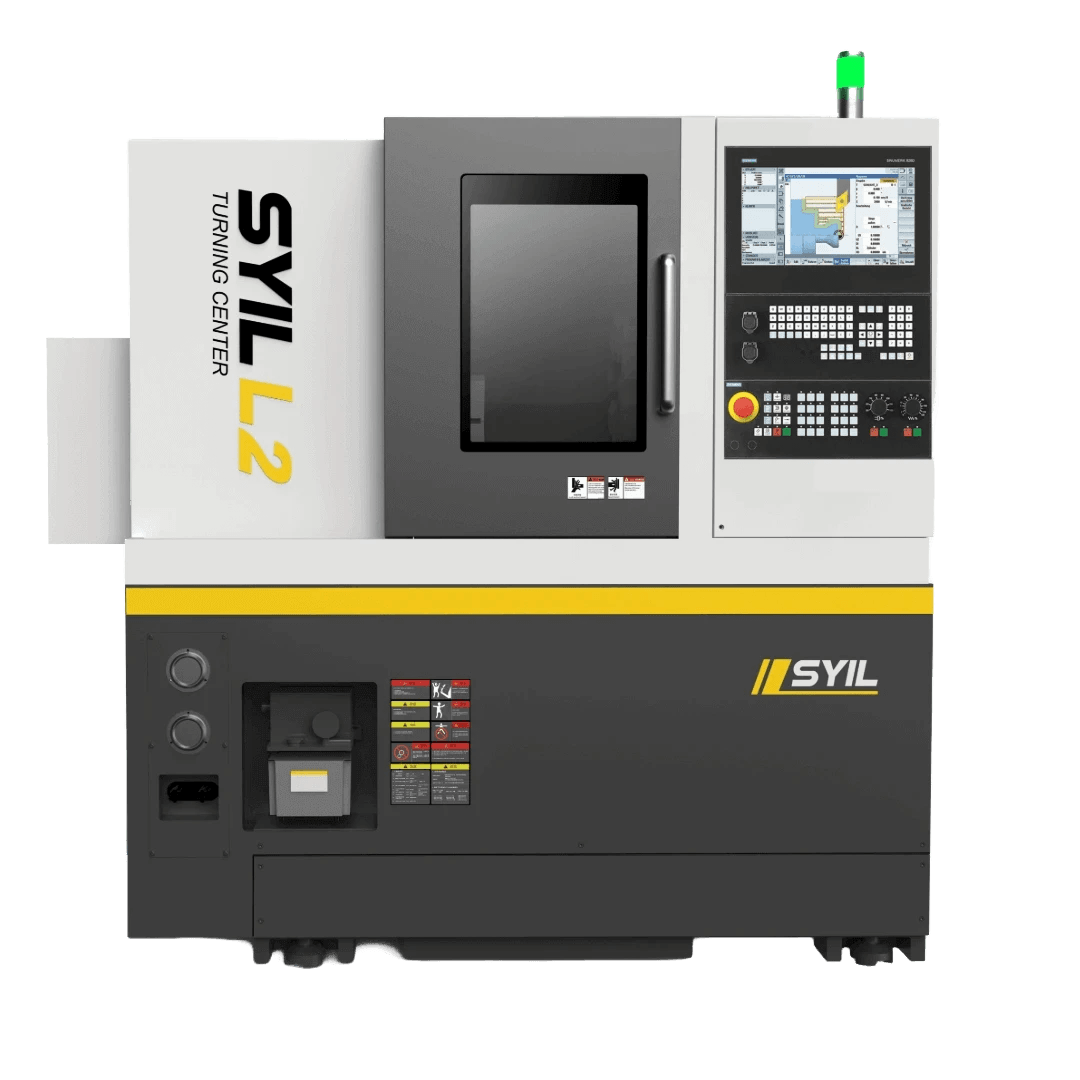
The PCB drilling machine market is bustling with innovative brands that are continually pushing the boundaries of technology and efficiency. Among these, SYIL stands out with its commitment to precision and performance, while other notable brands also contribute significantly to the industry's advancement. As we look toward the future, emerging trends in PCB drilling technologies promise to reshape how manufacturers approach the PCB drilling process.
SYIL CNC Machine Features and Benefits
SYIL CNC machines have earned a stellar reputation in the realm of PCB drilling due to their remarkable features and benefits. These machines are engineered for high precision, ensuring that every hole drilled meets stringent quality standards essential for effective PCB plating. Moreover, SYIL's user-friendly interface allows operators to seamlessly integrate advanced capabilities like automated drill bit changes, enhancing overall productivity while keeping costs manageable—especially when considering the competitive PCB drilling machine price.
Another standout feature is their adaptability; SYIL CNC machines can work with various types of PCB drill bits tailored for different applications, from standard boards to complex multilayer designs. This flexibility not only caters to diverse manufacturing needs but also helps businesses optimize their processes without overspending on multiple specialized machines. In an industry where precision is paramount, investing in a SYIL CNC PCB drilling machine can yield significant returns through improved efficiency and reduced waste.
Other Notable Brands in PCB Drilling
While SYIL is a key player, several other brands have made notable contributions to the evolution of PCB drilling equipment. Companies like Panasonic and Mitsubishi offer robust solutions that combine speed with accuracy—two critical elements when considering a new PCB drill set for your production line. These brands often incorporate cutting-edge technology into their designs, such as enhanced cooling systems for drill bits that prolong lifespan and improve performance during high-volume runs.
Moreover, emerging players like HSD provide budget-friendly options without compromising quality or precision—a crucial factor for startups looking to enter the market without breaking the bank on expensive machinery. The competition among these manufacturers drives innovation forward, resulting in exciting advancements that benefit businesses across various sectors involved in electronics manufacturing. With so many options available on the market today, companies must carefully assess their needs against each brand's offerings before making a decision on which PCB drilling machine will best fit their operations.
Future Trends in PCB Drilling Technologies
As we gaze into the crystal ball of future trends shaping the landscape of PCB drilling technologies, several key developments stand out prominently. One major trend is increased automation within CNC PCB drilling machines; this shift aims not only at enhancing production speed but also at minimizing human error during the delicate pcb drilling process. With integration of AI-driven systems becoming more prevalent, manufacturers can expect smarter machines capable of predictive maintenance—reducing downtime significantly while extending equipment lifespan.
Another exciting trend involves advancements in materials used for drill bits; innovations here promise improved durability and efficiency when tackling various substrates commonly found in PCBs today. Additionally, ongoing research into laser-assisted drilling techniques could revolutionize how manufacturers approach intricate designs by offering unparalleled precision without damaging sensitive components—a game-changer for industries requiring meticulous attention to detail during production phases such as pcb plating.
In conclusion, as technology continues its relentless march forward within this dynamic field of electronics manufacturing—keeping an eye on leading brands' innovations will be essential for businesses aiming not only to survive but thrive amidst competition.
Conclusion
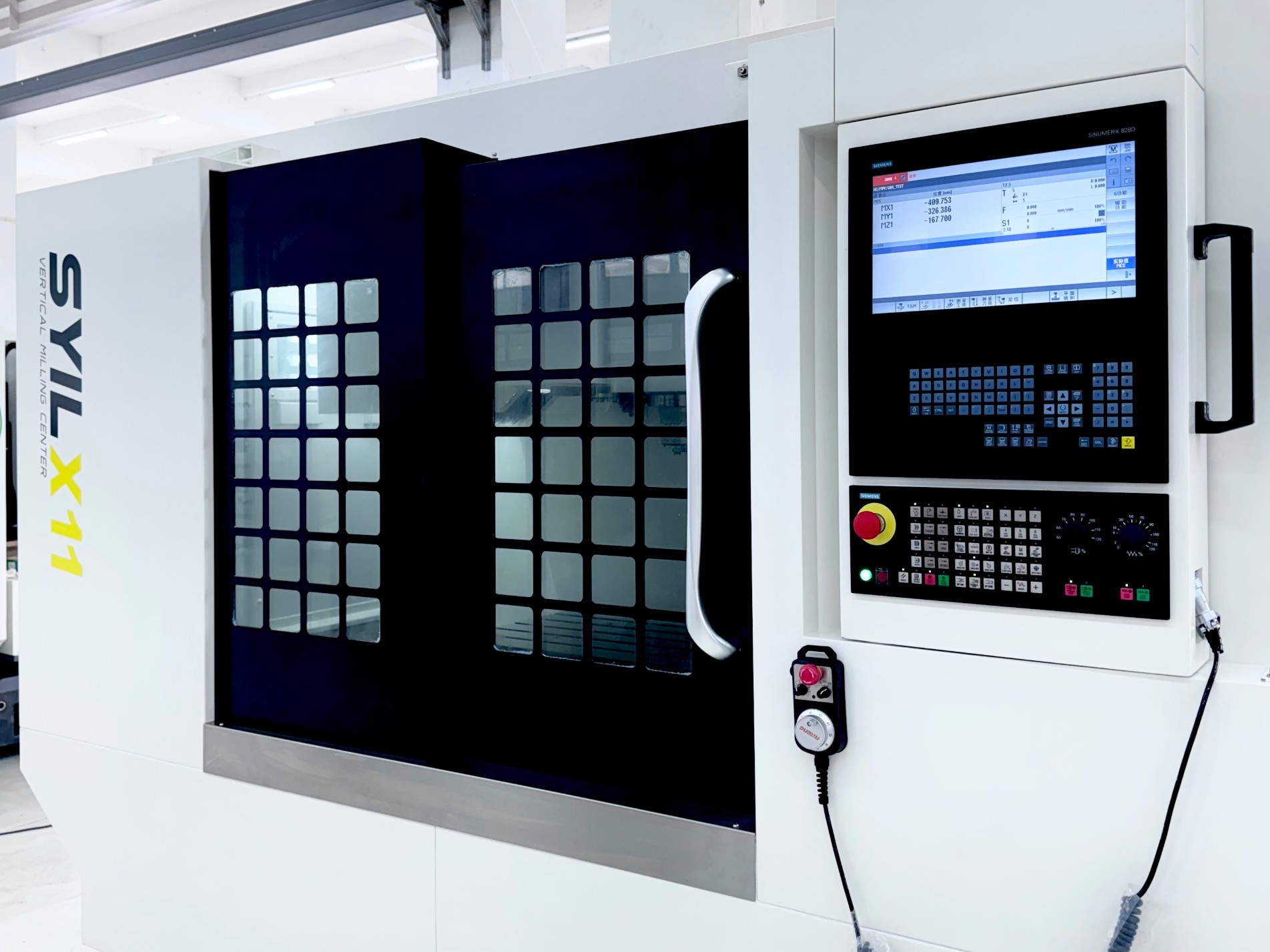
The landscape of PCB drilling machines is set to undergo significant transformations in the coming years. With the integration of innovative technologies and a growing demand for precision, the future looks bright for manufacturers and engineers alike. As companies explore new methods to enhance productivity, the evolution of CNC PCB drilling machines will play a pivotal role in shaping industry standards.
The Future of PCB Drilling Machines
Looking ahead, we can expect advancements in automation and artificial intelligence to redefine how PCB drilling machines operate. These innovations will not only improve efficiency but also ensure higher accuracy in the PCB drilling process, minimizing human error and maximizing output quality. Furthermore, as sustainability becomes a priority across industries, eco-friendly practices in manufacturing processes will gain traction, influencing the development of more energy-efficient PCB drilling machines.
Maximizing Efficiency with Modern Techniques
To maximize efficiency with modern techniques, manufacturers must embrace cutting-edge technologies such as AI-driven analytics and real-time monitoring systems. These tools can optimize workflows during the PCB drilling process by predicting potential issues before they arise and suggesting adjustments on-the-fly. Additionally, investing in high-quality PCB drill bits tailored for specific applications can significantly reduce downtime and improve overall production speed.
Investing Wisely in PCB Drilling Equipment
When it comes to investing wisely in PCB drilling equipment, understanding the factors that influence PCB drilling machine prices is crucial. It's essential to strike a balance between cost-effectiveness and quality; opting for brands that offer reliable performance while fitting within budget constraints is key for startups entering this competitive market. By carefully evaluating options and focusing on long-term value rather than short-term savings, businesses can ensure they make informed decisions that support growth.