Introduction
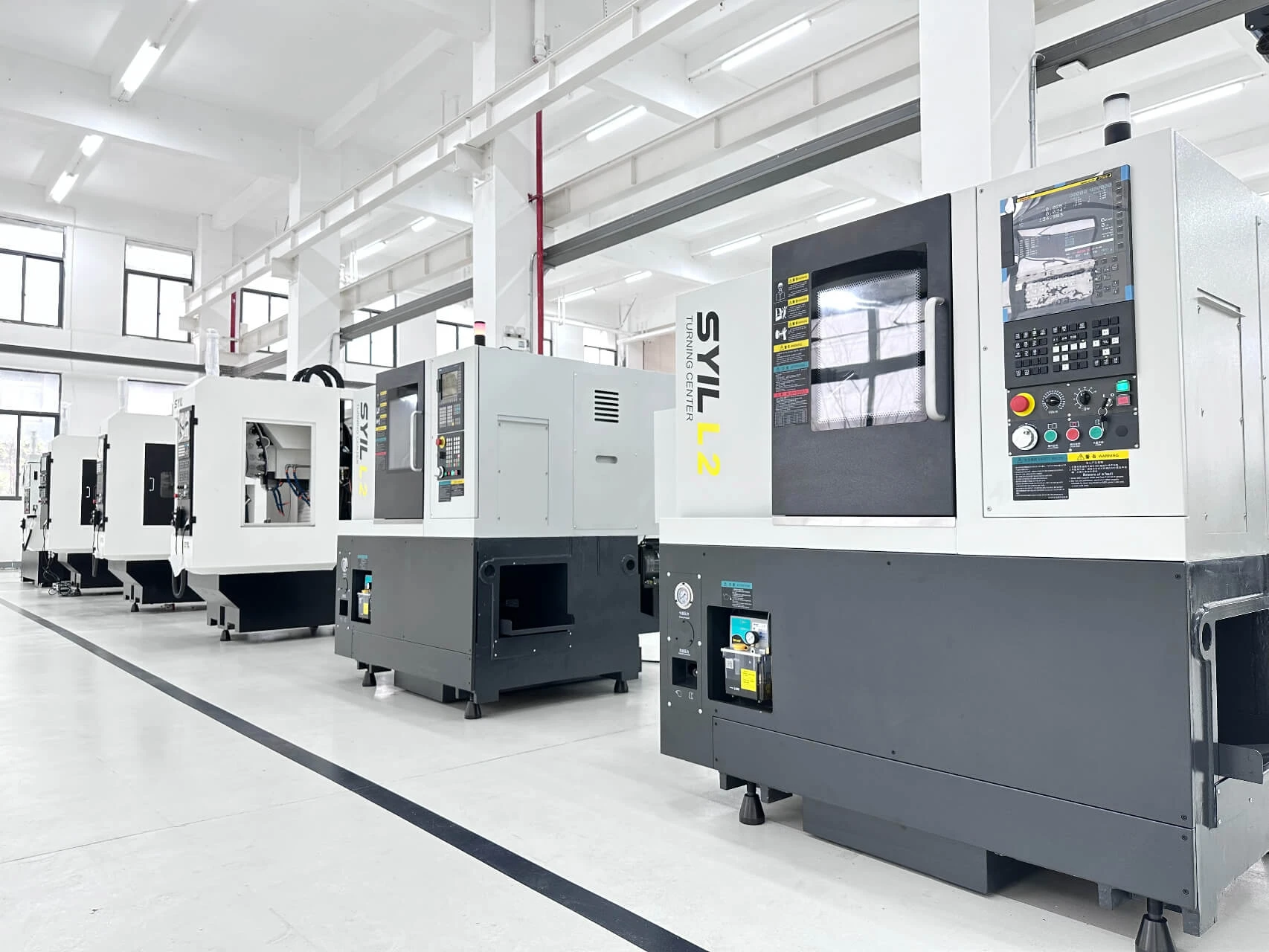
In an era where precision and efficiency reign supreme, the milling auto parts industry is undergoing a transformative revolution. Vehicle parts manufacturers are increasingly adopting advanced technologies, leading to significant enhancements in the automotive production process. As we delve into the intricacies of this evolution, it becomes clear that innovation is not just a buzzword; it's a necessity for success.
Revolutionizing the Milling Auto Parts Industry
The milling auto parts sector is experiencing a seismic shift driven by technological advancements and evolving consumer demands. Traditional methods are being challenged by more efficient processes, prompting machining parts manufacturers to rethink their strategies. This revolution not only improves production rates but also enhances the quality of automotive components, ensuring they meet rigorous standards.
The Rise of CNC Machining in Automotive
CNC machining has emerged as a game-changer in the automotive industry process, offering unparalleled precision and repeatability. Automotive CNC machines have become essential tools for vehicle parts manufacturers striving to maintain competitive edges while managing cnc machining costs effectively. As these machines continue to evolve, they facilitate innovative designs and complex geometries that were once deemed impossible.
Key Strategies for Improvement
To thrive in this competitive landscape, vehicle parts manufacturers must adopt key strategies that focus on efficiency, quality control, and technological integration. Embracing automation and smart manufacturing techniques can significantly streamline the automotive production process while reducing operational costs. By prioritizing these strategies, companies can enhance their overall performance and secure their positions as leaders in the milling auto parts industry.
Understanding the Milling Auto Parts Process
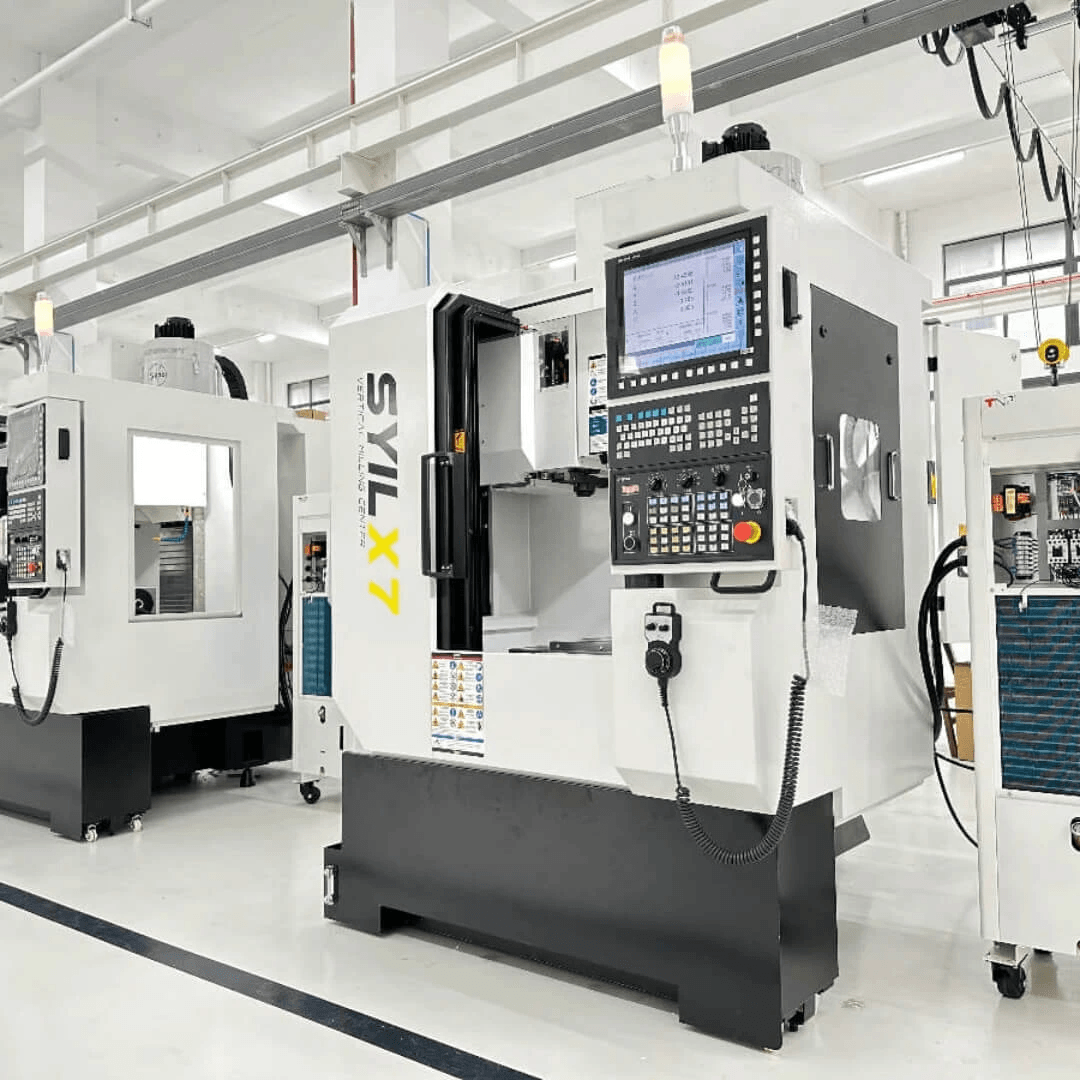
The milling auto parts process is a crucial aspect of the automotive industry, where precision and efficiency are paramount. Vehicle parts manufacturers play a vital role in ensuring that every component meets stringent quality standards while adhering to tight production schedules. This section delves into the intricacies of this process, highlighting how machining parts manufacturers operate and the innovations shaping modern car manufacturing.
The Role of Vehicle Parts Manufacturers
Vehicle parts manufacturers serve as the backbone of the automotive industry, producing essential components that ensure vehicles function optimally. These manufacturers focus on delivering high-quality milling auto parts that meet both safety and performance standards. With advancements in technology, they streamline their operations to reduce lead times and enhance product reliability, ultimately benefiting consumers and automakers alike.
How Machining Parts Manufacturers Operate
Machining parts manufacturers utilize sophisticated techniques to transform raw materials into precise components through processes like CNC machining. By leveraging advanced machinery, such as automotive CNC machines, these manufacturers can achieve remarkable accuracy while minimizing waste—a critical factor in today’s competitive market where CNC machining cost can significantly impact profitability. The integration of automation ensures that production runs smoothly, allowing for quicker turnaround times without sacrificing quality.
Innovations in the Car Manufacturing Process
The car manufacturing process has undergone significant transformations due to technological advancements and innovative practices within the industry. From 3D printing prototypes to employing robotics in assembly lines, vehicle parts manufacturers continually seek ways to enhance efficiency and reduce costs associated with traditional methods of production. These innovations not only improve productivity but also contribute to creating more sustainable practices within the automotive industry process—an essential consideration as environmental concerns become increasingly prominent.
The Advantages of CNC Machining
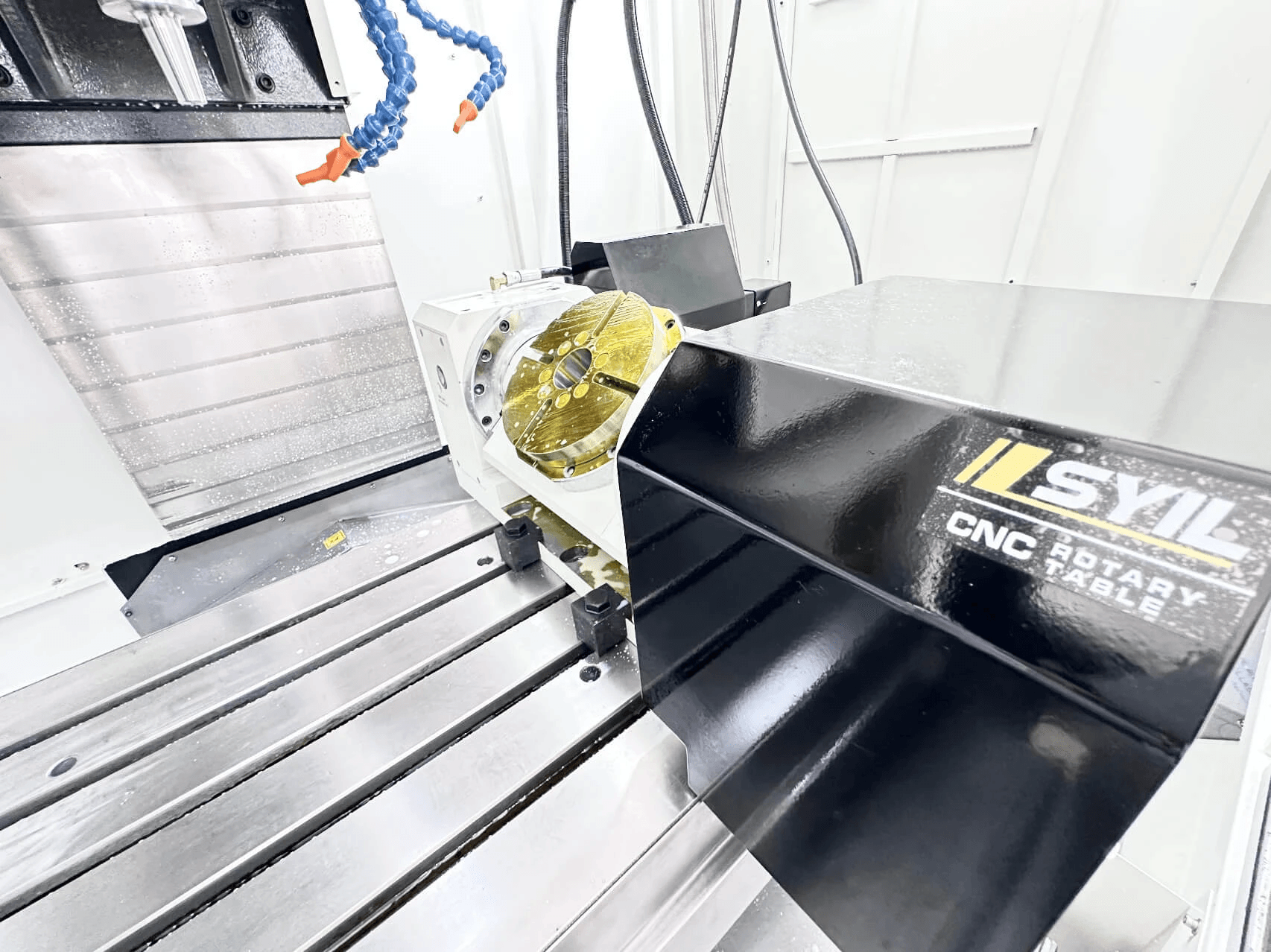
CNC machining is revolutionizing the milling auto parts industry, offering a plethora of advantages that traditional methods simply can't match. For vehicle parts manufacturers, the transition to an automotive CNC machine signifies not just a technological upgrade but a strategic move towards efficiency and precision. This section delves into the myriad benefits of CNC machining, comparing costs with traditional methods and highlighting its role in enhancing precision within the automotive production process.
Benefits of Using an Automotive CNC Machine
The primary benefit of using an automotive CNC machine is its unmatched precision in producing milling auto parts. With computer-controlled operations, these machines can achieve tolerances that are often impossible with manual machining, ensuring that each component fits perfectly within the car manufacturing process. Additionally, CNC machines operate continuously without fatigue, significantly increasing productivity for machining parts manufacturers while reducing human error.
Moreover, the flexibility offered by CNC machining allows vehicle parts manufacturers to easily switch between different product designs without extensive setup changes. This adaptability is crucial in today's fast-paced automotive industry process where consumer demands can shift rapidly. Lastly, the automation inherent in CNC technology leads to reduced labor costs and increased safety on the shop floor as machines take over repetitive tasks.
Comparing CNC Machining Cost to Traditional Methods
When evaluating cnc machining cost versus traditional manufacturing methods, it’s essential to consider both short-term investments and long-term savings. Initially, setting up a CNC machine might seem expensive for vehicle parts manufacturers; however, this cost can quickly be offset by lower labor expenses and faster production times. Traditional methods often require more manual intervention and longer lead times—factors that can inflate overall production costs.
Additionally, while maintenance costs for an automotive CNC machine may rise over time due to complex electronics and software updates, these expenses pale in comparison to potential losses from inefficient production processes associated with conventional techniques. By minimizing waste through precise material removal processes inherent in milling auto parts with CNC technology, companies can also enjoy significant savings on raw materials over time. The long-term financial benefits thus make a compelling case for investing in advanced manufacturing technologies.
Enhancing Precision in Automotive Production Process
Precision is paramount in the automotive industry process; even minor discrepancies can lead to performance issues or safety concerns down the line. With their ability to execute intricate designs with high accuracy consistently, automotive CNC machines play a vital role in enhancing precision during the milling auto parts production phase. This level of accuracy not only improves product quality but also establishes trust among consumers regarding vehicle reliability.
Furthermore, integrating advanced software solutions with these machines allows for real-time monitoring and adjustments during production runs—ensuring that any deviations from specifications are corrected immediately before they become larger issues during assembly or operation phases of vehicles. As such innovations continue to evolve within machining parts manufacturers' operations, we’re likely to see even greater advancements in precision engineering across all facets of car manufacturing processes.
Innovations in Material Selection
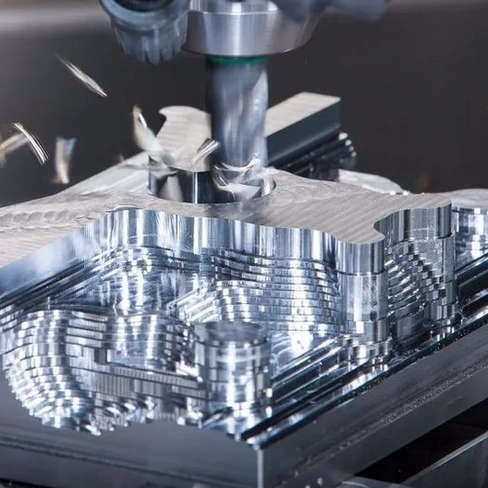
In the ever-evolving landscape of the automotive industry, material selection has become a critical factor in the production of milling auto parts. Vehicle parts manufacturers are continuously exploring advanced materials that not only enhance performance but also reduce costs and environmental impact. The right materials can significantly influence the durability, weight, and efficiency of components, making them essential to modern car manufacturing processes.
Advanced Materials in Milling Auto Parts
Advanced materials such as carbon fiber composites, aluminum alloys, and high-strength steels are increasingly being utilized by machining parts manufacturers to create more efficient and lightweight vehicle components. These materials offer superior strength-to-weight ratios compared to traditional steel or plastic options, which is vital for improving fuel efficiency in vehicles. Moreover, automotive CNC machines can easily work with these advanced materials, allowing for intricate designs that were once deemed impossible.
The adoption of such innovative materials not only enhances the performance of milling auto parts but also aligns with the industry's shift towards sustainability. By reducing weight through advanced material choices, vehicle parts manufacturers can contribute to lower emissions during operation—a win-win for both manufacturers and environmentally conscious consumers.
Sustainable Practices Among Vehicle Parts Manufacturers
Sustainability is no longer just a buzzword; it’s a necessity in today’s automotive industry process. Many vehicle parts manufacturers are now implementing sustainable practices by selecting eco-friendly materials and optimizing their production processes to minimize waste. This includes using recycled metals and bio-based composites that reduce reliance on fossil fuels while still maintaining high standards for quality.
Additionally, advancements in CNC machining technology allow for more precise cuts and less material waste during production runs. As automotive CNC machines become more efficient, they help machining parts manufacturers not only save on costs but also support broader sustainability goals within the car manufacturing process.
Ultimately, these sustainable practices lead to a significant reduction in overall environmental impact while still meeting consumer demand for high-quality products—proof that green initiatives can go hand-in-hand with profitability.
The Impact of Material Choice on Performance
The choice of material plays a pivotal role in determining how well milling auto parts perform under various conditions. For instance, using lightweight yet strong materials can improve acceleration and handling while enhancing fuel efficiency—critical factors that consumers consider when purchasing vehicles today. Furthermore, specific alloy compositions can enhance resistance to wear and corrosion, extending the lifespan of components produced by machining parts manufacturers.
Moreover, as automotive technology continues to advance with innovations like electric vehicles (EVs) gaining traction, material selection becomes even more critical due to differing performance requirements compared to traditional combustion engines. The right combination of advanced materials allows vehicle parts manufacturers to adapt quickly to market changes while ensuring their products remain competitive within an ever-evolving automotive industry process.
In conclusion, innovations in material selection not only drive improvements in milling auto parts but also foster sustainability within manufacturing practices—both essential elements for future success in this dynamic field.
Integrating Technology in the Manufacturing Process
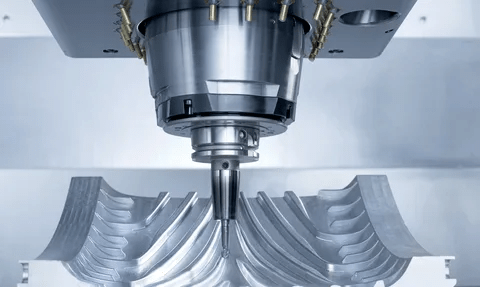
In today's rapidly evolving automotive landscape, integrating technology into the manufacturing process is not just a luxury; it's a necessity. The rise of smart CNC machines and IoT (Internet of Things) innovations are transforming how vehicle parts manufacturers operate, enhancing efficiency and precision in milling auto parts. As these technologies become more prevalent, they are reshaping the entire automotive production process, allowing machining parts manufacturers to stay competitive in a demanding market.
Smart CNC Machines and Their Benefits
Smart CNC machines are revolutionizing the way vehicle parts manufacturers approach production. These advanced systems offer real-time monitoring and automation capabilities that significantly reduce downtime and enhance productivity in machining processes. By minimizing human error and optimizing workflows, automotive CNC machines can lower overall cnc machining costs while ensuring high-quality outputs that meet stringent industry standards.
Moreover, smart CNC machines facilitate data collection and analysis, enabling manufacturers to make informed decisions about their operations. This data-driven approach leads to continuous improvement in the car manufacturing process by identifying bottlenecks and inefficiencies. Ultimately, investing in these cutting-edge technologies positions machining parts manufacturers for long-term success in an increasingly competitive automotive industry.
The Influence of IoT in Automotive Industry Process
The Internet of Things (IoT) is making waves across various sectors, but its impact on the automotive industry process is particularly noteworthy. By connecting machinery, tools, and systems through smart devices, IoT enhances communication between different elements of manufacturing operations. This interconnectedness allows vehicle parts manufacturers to monitor performance metrics closely and streamline their milling auto parts production processes.
IoT applications enable predictive maintenance by alerting manufacturers about potential equipment failures before they occur. This proactive approach minimizes disruptions during production runs and reduces unexpected cnc machining costs associated with repairs or replacements. Additionally, real-time data sharing among machinery fosters collaboration among teams working on different aspects of the automotive production process.
How SYIL CNC Machine is Shaping the Future
SYIL CNC machines are at the forefront of this technological revolution within the milling auto parts sector. Known for their precision engineering and user-friendly interfaces, SYIL machines empower machining parts manufacturers to achieve unparalleled accuracy while maintaining cost-effectiveness in their operations. As these machines continue to evolve with innovative features like AI-driven analytics and enhanced connectivity options, they set new benchmarks for quality within the automotive industry.
Furthermore, SYIL's commitment to sustainability aligns with modern practices among vehicle parts manufacturers seeking environmentally friendly solutions without compromising performance or efficiency. By adopting SYIL technology into their workflows, companies can optimize resource usage while producing high-quality components essential for today’s vehicles. As we look ahead to future trends in manufacturing processes, it’s clear that advancements like those offered by SYIL will play a pivotal role in shaping a more efficient and sustainable automotive landscape.
Quality Control and Assurance Techniques
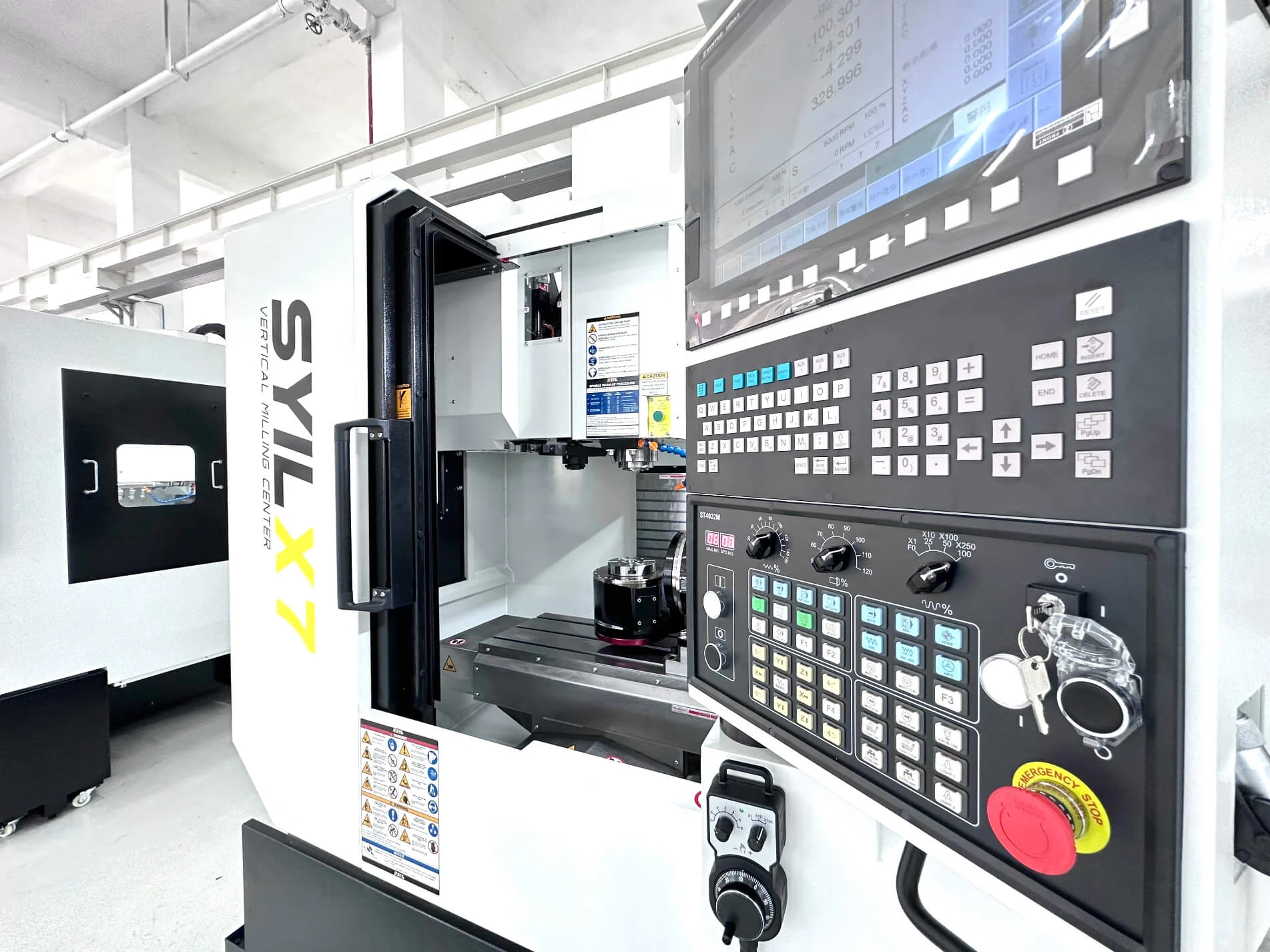
In the competitive landscape of the automotive industry, maintaining high-quality standards is crucial for machining parts manufacturers. The precision required in milling auto parts directly impacts vehicle performance, safety, and reliability. Therefore, a robust quality control system is not just an add-on; it’s a fundamental part of the car manufacturing process.
Importance of Quality in Machining Parts Manufacturers
Quality assurance is paramount for machining parts manufacturers, as even minor defects can lead to significant failures in vehicles. The reputation of vehicle parts manufacturers hinges on their ability to produce reliable and durable components that meet stringent safety regulations. By prioritizing quality control measures, these manufacturers can ensure that their milling auto parts contribute positively to the overall automotive production process.
Moreover, high-quality standards help reduce waste and rework costs associated with defective parts. This not only minimizes cnc machining cost but also enhances customer satisfaction by delivering superior products consistently. In an era where consumers are increasingly discerning about vehicle performance, maintaining quality has become more critical than ever.
Techniques to Enhance Automotive Production Process
To enhance the automotive production process, several techniques can be implemented by machining parts manufacturers. One effective approach is utilizing statistical process control (SPC) methods to monitor production variables in real-time. This allows for immediate adjustments during the milling of auto parts, ensuring that any deviations from quality standards are promptly addressed.
Another technique involves incorporating advanced inspection technologies such as laser scanning and 3D imaging systems into the manufacturing workflow. These tools enable precise measurements and defect detection at various stages of production, thus ensuring that each component meets design specifications before moving forward in the car manufacturing process. Additionally, adopting lean manufacturing principles can streamline operations and reduce waste while enhancing overall product quality.
Standards and Certifications for Vehicle Parts
Adhering to established standards and certifications is essential for vehicle parts manufacturers aiming to excel in the automotive industry process. Organizations like ISO (International Organization for Standardization) provide guidelines that help ensure consistent quality across all stages of production for milling auto parts. Achieving certifications such as ISO 9001 demonstrates a commitment to excellence and can significantly boost a manufacturer’s credibility in a competitive market.
Furthermore, compliance with industry-specific regulations—such as those set forth by IATF 16949—ensures that machining parts manufacturers meet customer requirements effectively while minimizing risks associated with product recalls or failures. By investing time and resources into obtaining these certifications, companies not only enhance their operational capabilities but also build trust with clients who prioritize quality when selecting suppliers.
Conclusion
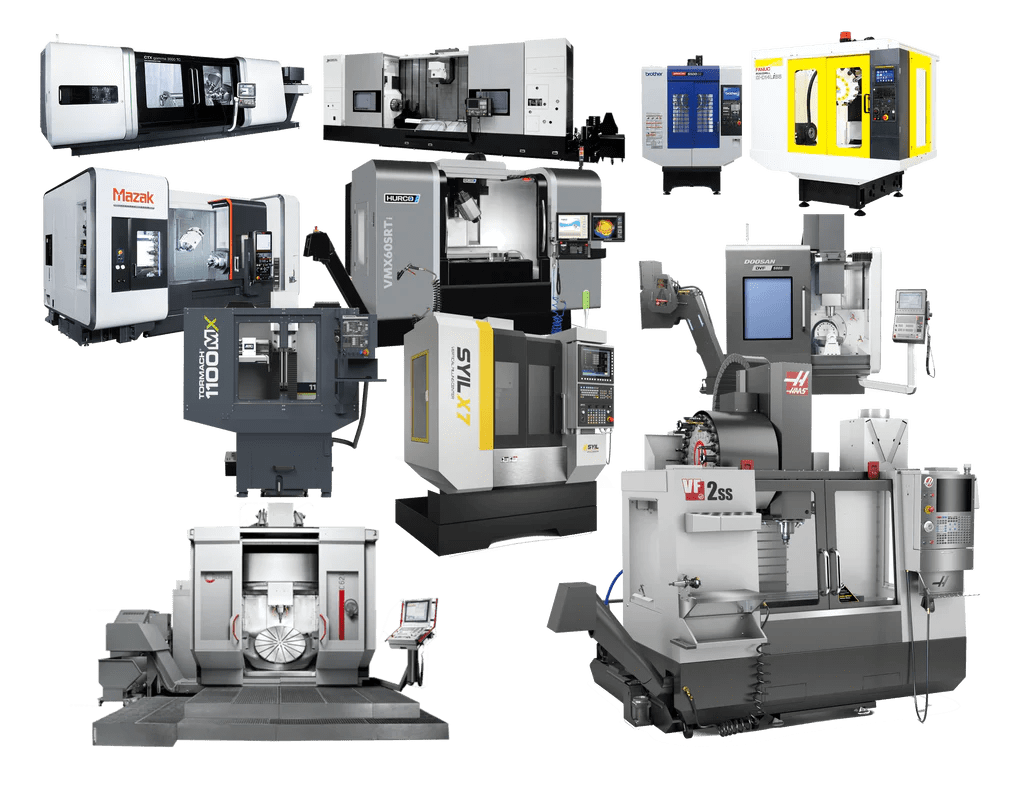
As we wrap up our exploration of the milling auto parts industry, it’s clear that the future holds exciting developments. The integration of advanced technologies and innovative materials will reshape how vehicle parts manufacturers operate, driving efficiency and precision in the automotive production process. With CNC machining at the forefront, the landscape of manufacturing is set for a significant transformation.
Future Trends in Milling Auto Parts
The future of milling auto parts is poised to be defined by automation and smart technologies that enhance productivity and reduce costs. Vehicle parts manufacturers are increasingly adopting CNC machining techniques to streamline their operations while ensuring high-quality outcomes. As these innovations continue to evolve, we can expect a shift towards more sustainable practices that not only improve performance but also minimize environmental impact.
The Evolving Role of Technology in Manufacturing
Technology's role in the automotive industry process cannot be overstated; it’s a game changer for machining parts manufacturers everywhere. From IoT connectivity to advanced software solutions, technology is enhancing every aspect of production—from design to delivery. Automotive CNC machines are becoming smarter and more efficient, allowing manufacturers to adapt quickly to market demands while maintaining top-notch quality.
Best Practices for Automotive Industry Success
To thrive in this competitive landscape, vehicle parts manufacturers must embrace best practices that prioritize quality control and innovation in their automotive production process. Implementing robust quality assurance techniques ensures that every component meets stringent standards, ultimately leading to greater customer satisfaction. By staying ahead of trends and investing in cutting-edge technology, businesses can secure their place as leaders in the milling auto parts sector.