Introduction
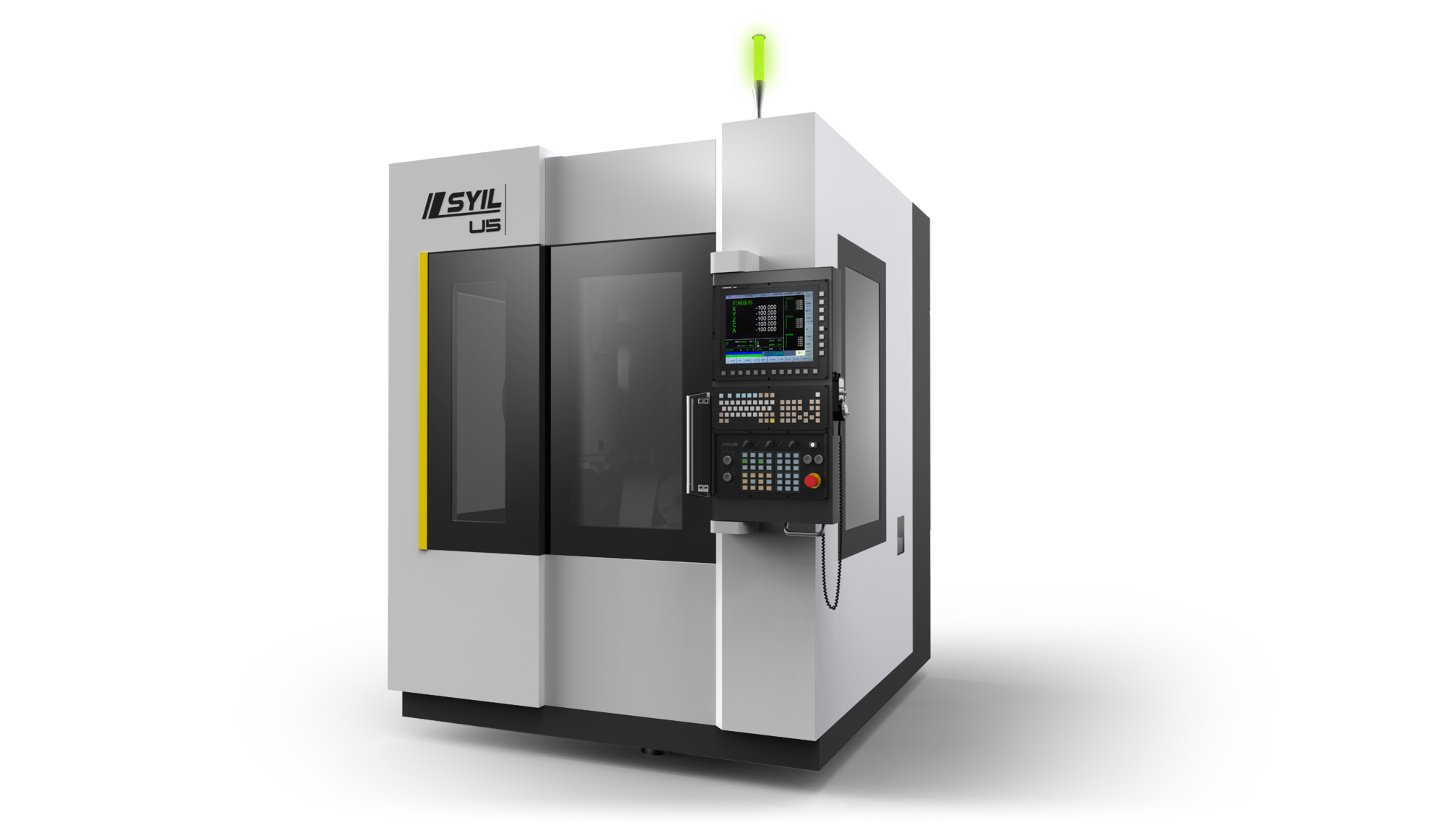
In the world of manufacturing, precision CNC milling has emerged as a game-changer, offering unparalleled accuracy and efficiency. This advanced technology not only streamlines production processes but also ensures that even the most intricate designs are executed with remarkable precision. With the rise of automation and computer-controlled machinery, understanding what precision milling entails has never been more critical for businesses aiming to stay competitive.
Understanding Precision in CNC Milling
So, what is precision milling? At its core, it refers to the ability of a CNC mill to produce parts that meet strict tolerances and specifications consistently. The precision of a CNC mill is determined by various factors including machine calibration, tool condition, and material selection—all crucial elements that contribute to achieving high-quality results in every project.
The Importance of Accuracy in Manufacturing
Accuracy in manufacturing is not just a nice-to-have; it's essential for ensuring product reliability and performance. When manufacturers adopt precision CNC machining processes, they significantly reduce waste and rework costs while enhancing customer satisfaction through consistent quality outputs. In an industry where even minor deviations can lead to catastrophic failures, understanding the importance of accuracy cannot be overstated.
Overview of CNC Machining Processes
CNC machining encompasses a variety of processes designed to create complex shapes from raw materials using computer-controlled machines. Among these processes, precision CNC milling stands out due to its ability to deliver intricate designs with tight tolerances effectively. By leveraging advanced software and cutting-edge technologies, manufacturers can optimize their production workflows while maintaining high standards for quality assurance.
What is Precision CNC Milling?
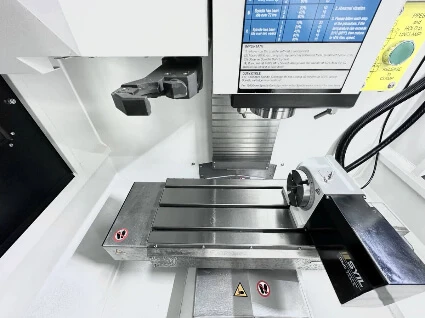
Precision CNC milling is a sophisticated manufacturing process that leverages computer numerical control (CNC) technology to achieve high levels of accuracy and repeatability in machining. This technique allows manufacturers to create intricate parts with exact specifications, making it essential for industries where precision is paramount. By employing advanced software and precise machinery, precision CNC milling transforms raw materials into finely-tuned components.
Defining Precision in CNC Context
In the context of CNC machining, precision refers to the ability of a machine to produce parts that meet exact dimensional tolerances consistently over time. This means that when we ask, What is the precision of a CNC mill? we're really inquiring about how closely the output matches the intended design specifications. Achieving high precision requires not just advanced technology but also meticulous attention to detail throughout the entire manufacturing process.
Key Features of CNC Milling Machines
CNC milling machines are equipped with several key features that contribute to their precision capabilities. These machines utilize high-speed spindles, multi-axis movement, and robust tooling systems to create complex shapes with minimal human intervention. Additionally, features such as automated tool changers and real-time feedback systems enhance efficiency while maintaining tight tolerances—making them indispensable for anyone asking, What is precision milling?
Benefits of Using Precision CNC Milling
The benefits of using precision CNC milling are numerous and impactful for modern manufacturing processes. First and foremost, this method significantly reduces human error by automating intricate tasks that require meticulous attention—allowing for consistent quality across large production runs. Furthermore, investing in a **precision CNC machine** can lead to long-term cost savings through reduced waste and improved production efficiency; after all, who wouldn't want their projects executed flawlessly while keeping an eye on **precision CNC milling costs**?
What is the CNC Precision Machining Process?
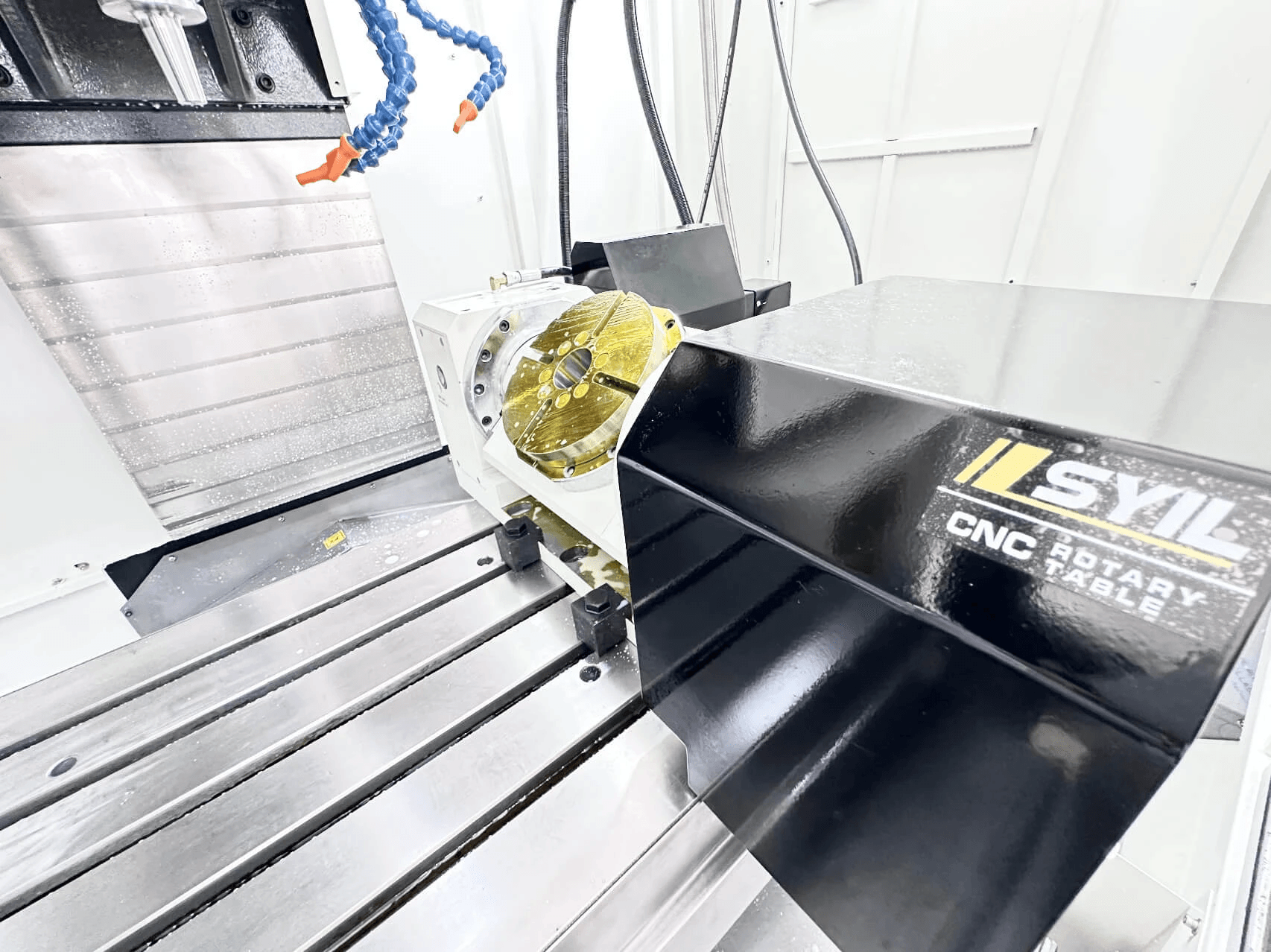
The CNC precision machining process is a systematic approach to creating intricate parts with high accuracy and repeatability. This process utilizes computer numerical control (CNC) technology to guide machines that cut, mill, and shape materials according to precise specifications. Understanding this process is essential for anyone delving into precision CNC milling, as it lays the groundwork for achieving exceptional results.
Stages of the CNC Machining Process
The stages of the CNC machining process can be broken down into several critical steps that ensure precision and efficiency. First, design engineers create a detailed CAD (Computer-Aided Design) model of the part to be machined, which serves as the blueprint for production. Next, this model is translated into G-code—a language that tells the CNC machine how to move—allowing for high precision in milling operations.
Once the G-code is generated, it’s time for setup and calibration of the CNC machine. This involves selecting appropriate tools and materials while ensuring everything is aligned correctly to maintain accuracy throughout production. Finally, during the machining stage itself, operators monitor progress closely to ensure consistency in each cycle, making adjustments as necessary to uphold quality standards.
Tools Used for Precision Machining
Precision machining relies on an array of specialized tools designed specifically for tasks like cutting, drilling, and milling. Commonly used tools include end mills, drills, lathes, and routers—all engineered to deliver exact dimensions with minimal tolerance errors. The choice of tool directly influences what is considered the precision of a CNC mill, as different materials require specific cutting techniques and tool geometries.
In addition to traditional cutting tools, advanced technologies such as laser cutters and water jets are increasingly utilized in precision CNC milling applications. These innovative tools can achieve extraordinary levels of detail that traditional methods may struggle with while also enhancing overall efficiency in production processes. Ultimately, selecting the right tool not only impacts accuracy but also affects production speed—key factors when considering precision CNC milling costs.
Ensuring Consistency in Machining
One way this consistency is maintained is through regular maintenance schedules that keep machines calibrated and functioning optimally over time; neglecting maintenance can lead to deviations from intended specifications during milling operations.
Another significant factor involves operator training; skilled machinists understand how subtle changes in technique or material can impact final product quality dramatically—making their expertise invaluable in any production environment focused on precision milling efforts. Furthermore, implementing quality control measures throughout each stage helps identify potential issues early on before they escalate into costly mistakes or rework situations.
Ultimately, understanding what constitutes precision milling goes beyond just machinery; it's about creating a culture where accuracy reigns supreme at every level—from design through execution—to ensure long-term success in producing finely crafted components.
Factors Affecting CNC Milling Accuracy
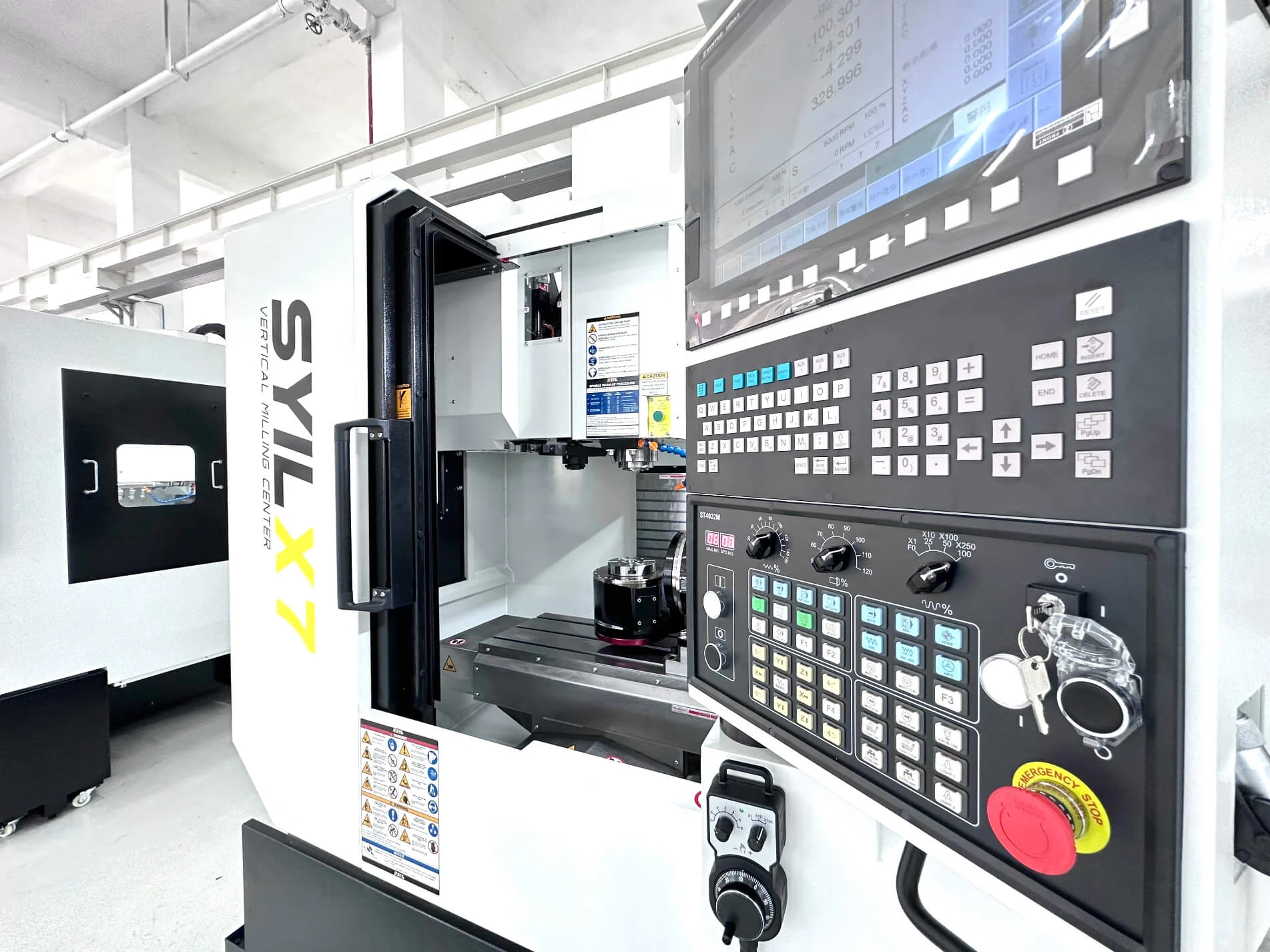
Material Selection and Its Impact
Material selection is one of the most critical aspects influencing precision milling outcomes. Different materials have varying mechanical properties, which can affect how they respond to cutting forces during the CNC precision machining process. For instance, harder materials may cause more wear on tools, while softer materials might not hold tolerances as tightly, leading to questions like What is precision milling? and how it differs depending on material choice.
Choosing the right material ensures that your precision CNC milling projects yield accurate dimensions and finishes. Additionally, understanding how specific materials behave under machining conditions can help in selecting appropriate cutting speeds and feeds, further optimizing accuracy. Ultimately, the right material leads to better results and fewer unexpected costs associated with inaccuracies.
Role of Machine Calibration
Machine calibration is another crucial factor that directly impacts what is the most precise CNC machine for your needs. Regular calibration ensures that all components of a CNC machine are aligned correctly and functioning as intended, which is essential for maintaining high levels of accuracy in production runs. Without proper calibration, even minor deviations can accumulate over time, leading to significant discrepancies in finished parts.
Incorporating routine checks into your maintenance schedule will help you avoid costly mistakes that stem from misalignment or mechanical failure during precision CNC milling operations. Moreover, understanding what is the CNC precision machining process involves recognizing how critical calibration is at every stage—from setup to execution—to ensure consistent quality across all machined parts.
Importance of Tool Condition
The condition of cutting tools cannot be overlooked when discussing factors affecting accuracy in precision CNC milling projects. Dull or damaged tools can lead to poor surface finishes and dimensional inaccuracies that compromise overall project integrity. Regularly inspecting tools for wear helps maintain optimal performance levels; after all, a sharp tool makes cleaner cuts!
Furthermore, understanding how tool condition affects cutting efficiency allows operators to adjust parameters accordingly for improved results during what is precision milling operations? Operators must stay vigilant about replacing or sharpening tools as needed—this proactive approach not only enhances accuracy but also contributes positively toward overall production costs related to precision machining processes.
What is the Most Precise CNC Machine?
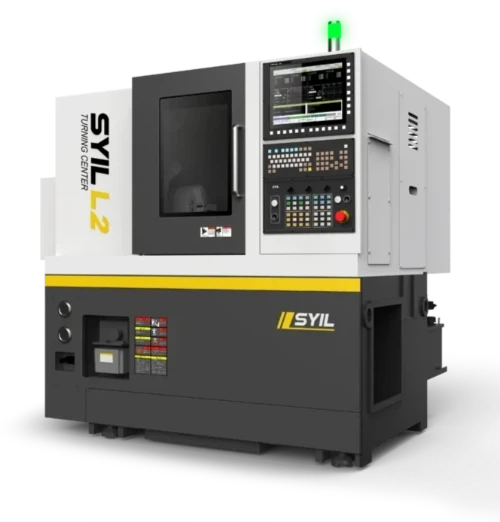
Comparing Top Precision CNC Machines
In the realm of precision CNC machines, several models vie for supremacy, each boasting unique features that enhance their accuracy. Brands such as Haas Automation, DMG Mori, and SYIL have made a name for themselves by delivering machines that excel in precision milling. When evaluating these machines, consider aspects like spindle speed, rigidity, and control systems—these elements play crucial roles in determining what is the precision of a CNC mill.
For instance, some high-end models can achieve tolerances within 0.001 inches or better—an impressive feat for those engaged in intricate projects that require meticulous detail. Furthermore, advancements in software integration allow for real-time adjustments during the machining process to maintain optimal accuracy. Ultimately, comparing these top contenders helps you understand not just what is precision milling but how it translates into tangible benefits for your operations.
Innovations in CNC Technology
The landscape of CNC technology has evolved dramatically over recent years with innovations that redefine what we consider possible in precision machining processes. From advanced CAD/CAM software to AI-driven automation systems, these innovations are making it easier than ever to achieve high levels of accuracy in production runs. For example, some modern machines now feature adaptive control systems that automatically adjust parameters based on real-time feedback from cutting tools.
Moreover, multi-axis machining has emerged as a game-changer; this allows for more complex geometries without sacrificing precision or increasing setup times significantly. As manufacturers continue to invest in cutting-edge technologies and techniques like 3D printing integration with traditional methods, understanding what is the CNC precision machining process becomes vital for staying competitive.
How SYIL CNC Machines Stand Out
Among the leading names in precision CNC milling is SYIL—a company renowned for its commitment to quality and innovation at competitive prices. What sets SYIL apart from other brands? Their machines incorporate features designed explicitly for achieving high tolerances while maintaining user-friendliness; they cater especially well to small- to medium-sized businesses looking to maximize their return on investment.
SYIL’s dedication to precise engineering ensures that their products not only meet but often exceed industry standards when it comes to performance and reliability. Moreover, they offer customization options tailored specifically for clients’ unique needs—a rarity among competitors—and this flexibility can lead directly into cost savings over time when considering overall operational efficiency and reduced waste during production runs involving precision milling processes.
Precision CNC Milling Cost Considerations
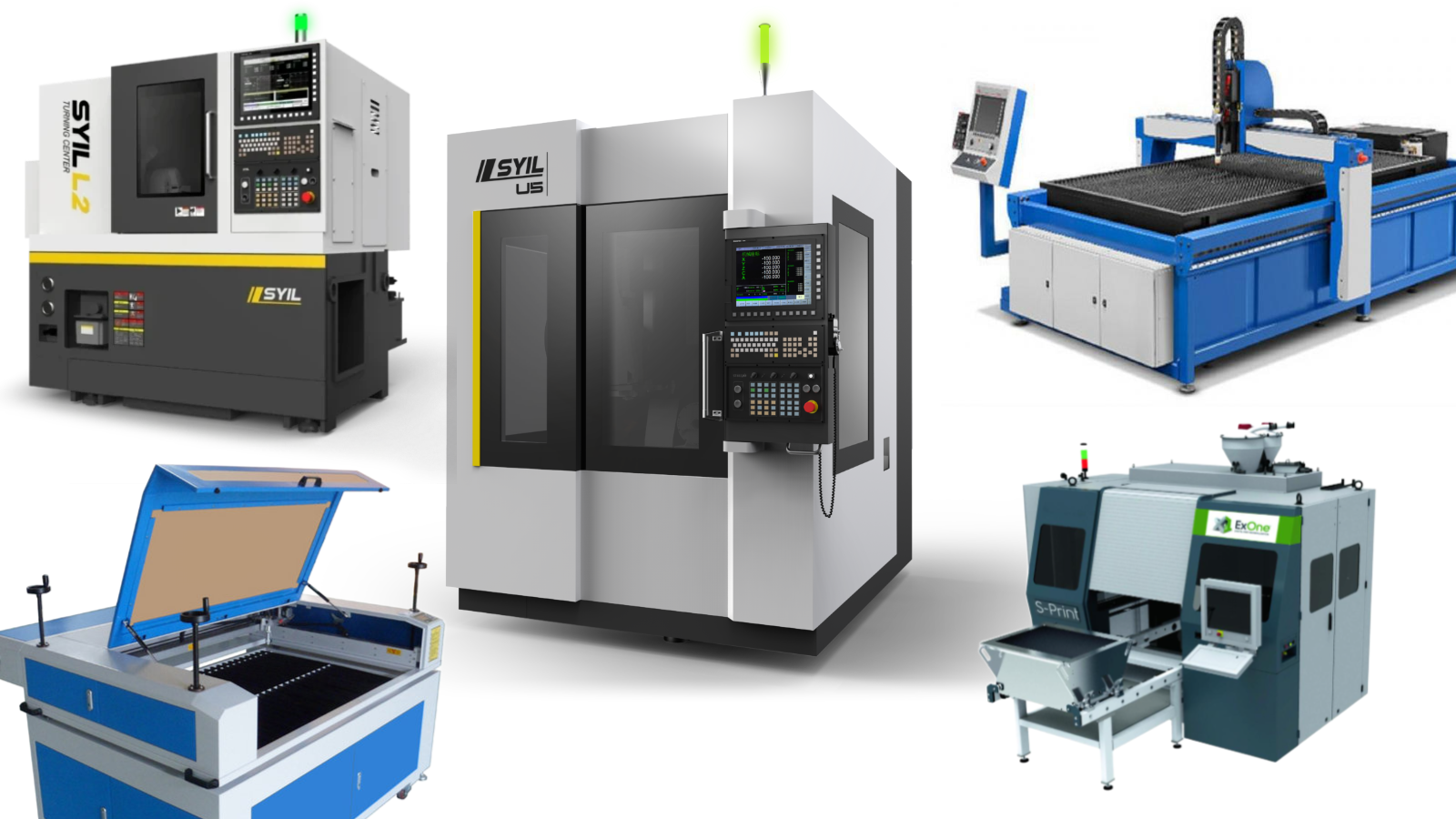
When embarking on a precision CNC milling project, understanding the associated costs is essential. The initial investment can vary significantly based on factors such as machine type, material selection, and complexity of the design. Budgeting for precision CNC projects involves not just the upfront costs but also ongoing operational expenses to ensure quality and accuracy throughout the machining process.
Budgeting for Precision CNC Projects
Budgeting for precision CNC projects requires a comprehensive approach that accounts for multiple variables. First, consider the cost of the precision CNC machine itself, which can range from affordable entry-level models to high-end machines with advanced features. Additionally, factor in expenses related to tooling, materials, labor, and maintenance; these elements play a crucial role in determining the overall budget while ensuring you achieve what is precision milling at its finest.
Moreover, it’s wise to allocate funds for unexpected costs that may arise during production. Delays or complications can lead to additional expenses that might derail your budget if not planned for ahead of time. By carefully calculating all potential costs associated with what is the CNC precision machining process, you’ll be better equipped to manage your finances and stay on track.
Cost vs. Quality: Finding the Balance
In any manufacturing endeavor, striking a balance between cost and quality is paramount—especially in precision CNC milling where accuracy is non-negotiable. While it might be tempting to opt for lower-cost solutions or machines that promise high efficiency at a bargain price, this could compromise quality and lead to increased rework or scrap rates down the line. Remember that investing in a reliable precision CNC machine often pays off by delivering superior results consistently over time.
Quality should never be sacrificed on the altar of cost-cutting; instead, consider how investing in higher-quality tools or machinery can enhance overall productivity and reduce long-term operational costs. What is most precise CNC technology? It’s typically found in machines built with robust components designed for longevity and consistent performance under demanding conditions. Ultimately, finding this balance will ensure you achieve optimal results without breaking your budget.
Long-term Savings with Precision Milling
While initial investments in precision CNC milling may seem steep compared to traditional machining methods, long-term savings often outweigh these upfront costs significantly. High-quality machines deliver superior accuracy which leads to reduced waste and lower material costs over time; thus enhancing profitability per project undertaken. Moreover, efficient processes minimize downtime due to fewer errors or repairs needed during production runs.
Another aspect of long-term savings comes from improved labor efficiency—precision machines often require less manual intervention once set up correctly—which allows skilled operators to focus their efforts elsewhere rather than troubleshooting issues caused by inferior equipment or processes lacking consistency in what is precision milling techniques used today.
In summary, strategic investments into high-quality tools will not only optimize your operations but also yield substantial returns over time through enhanced production capabilities and reduced operating expenses associated with low-quality alternatives.
Conclusion
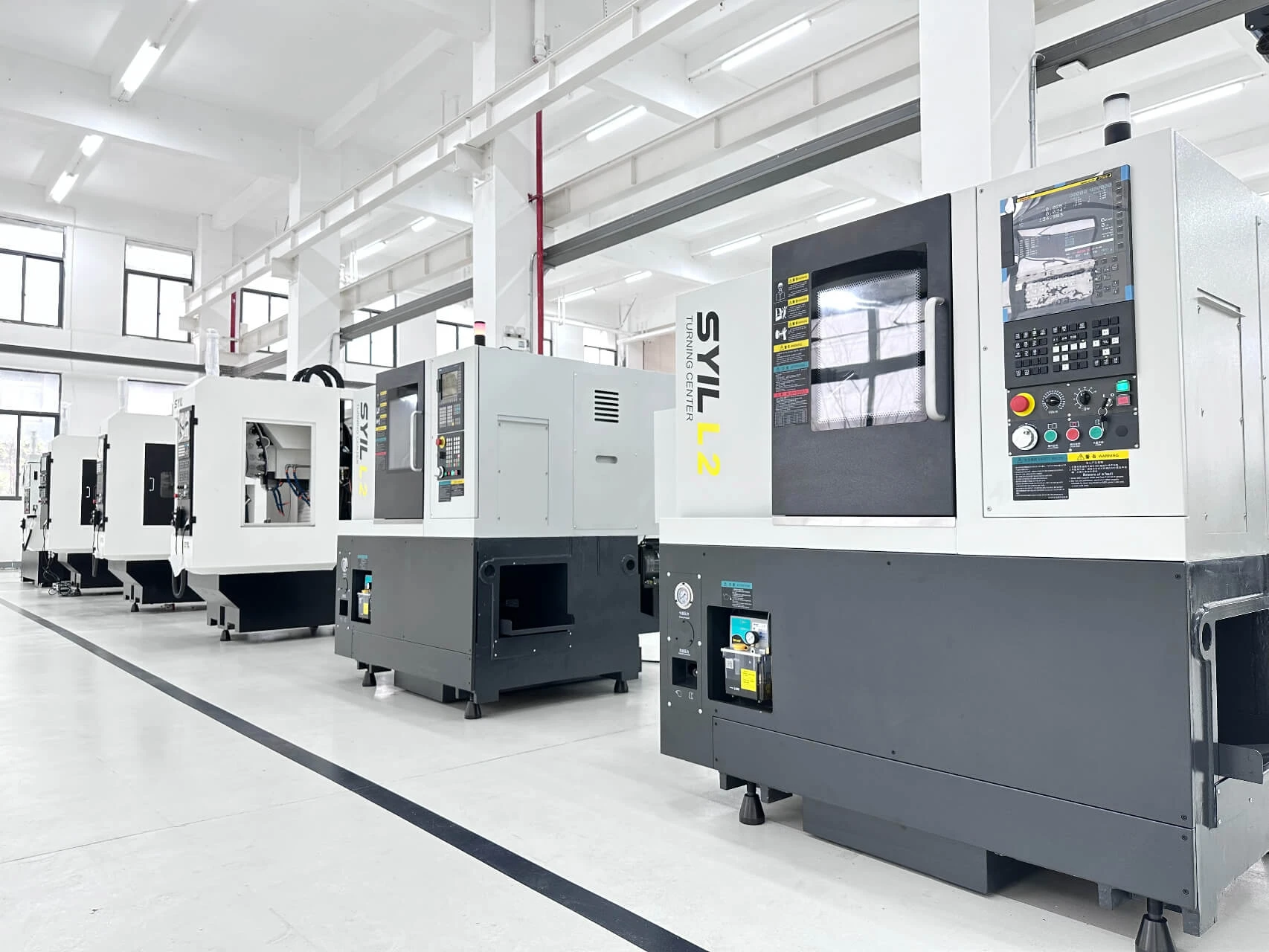
In the world of manufacturing, precision CNC milling stands as a cornerstone for achieving high-quality results. To maximize accuracy in CNC milling, it's essential to understand not only the machinery but also the processes involved and how they can be optimized. With advancements in technology and a keen focus on detail, manufacturers can ensure that every piece produced meets stringent specifications.
Maximizing Accuracy in CNC Milling
Maximizing accuracy in CNC milling involves a combination of precise machine settings, skilled operators, and quality materials. One key aspect is understanding what is the precision of a CNC mill; tolerances can often be as tight as ±0.001 inches depending on the application. Consistent calibration of machines and regular maintenance are vital to uphold these standards over time, ensuring that what is precision milling becomes second nature in your operations.
Future Trends in Precision CNC Technology
Looking ahead, future trends in precision CNC technology promise even greater enhancements in machining capabilities. Innovations such as AI-driven automation and advanced sensor technologies will likely redefine what is the CNC precision machining process by improving real-time monitoring and adjustments during production. As these technologies evolve, we can expect to see an increase in efficiency and reduction in waste—making precision CNC milling not just more accurate but also more sustainable.
Choosing the Right CNC Machine for You
What is the most precise CNC machine available may vary depending on your requirements—be it intricate designs or mass production runs—but knowing your operational goals helps narrow down options effectively. Ultimately, investing time into researching various models will pay off by ensuring you select a machine that aligns perfectly with your manufacturing aspirations.