Introduction
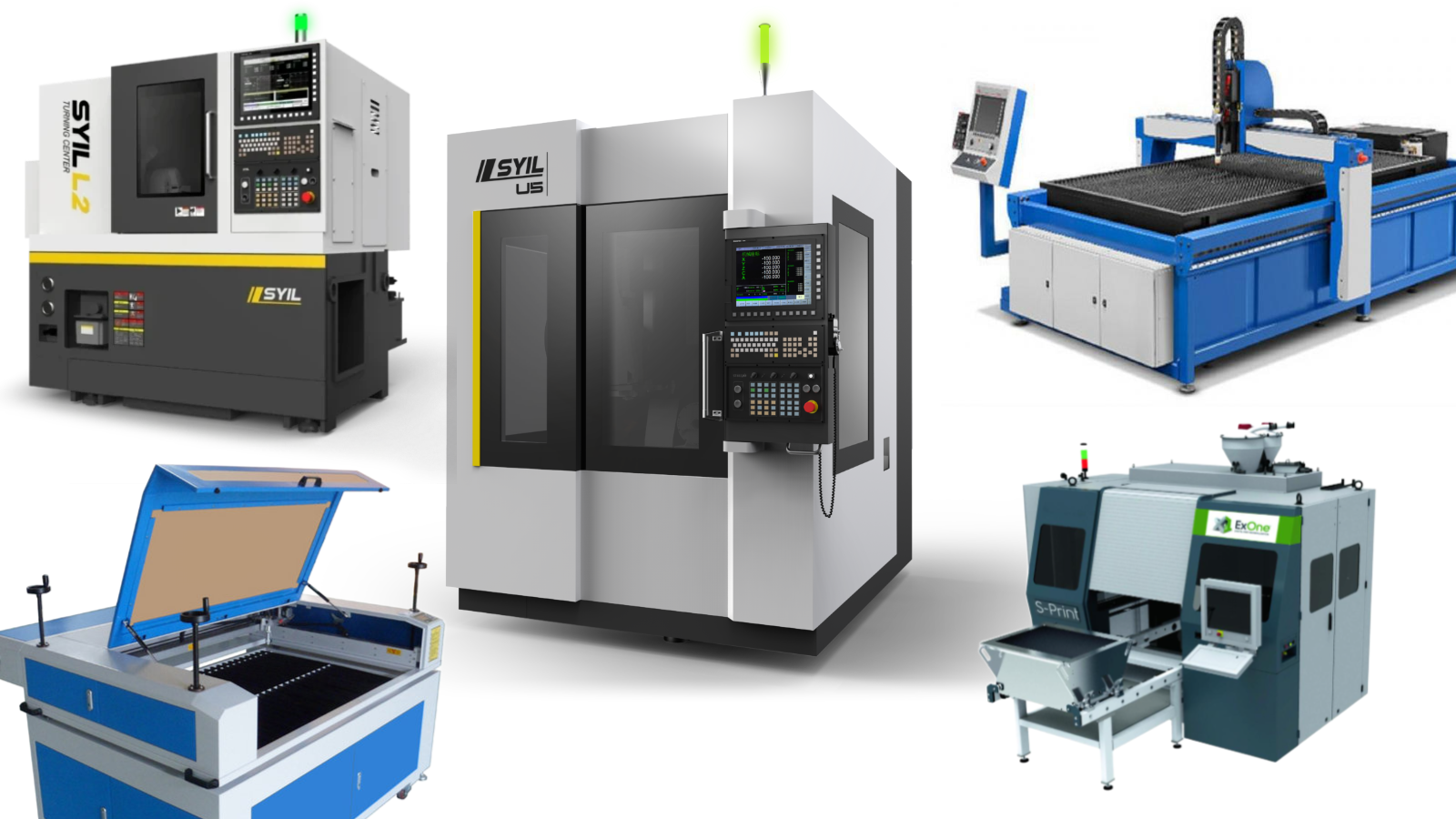
In the ever-evolving world of manufacturing, CNC turning has emerged as a game changer, especially in the realm of medical device machining. This innovative process enables the creation of precise and intricate medical machined components that are crucial for modern healthcare solutions. With its ability to produce high-quality parts efficiently, CNC turning is revolutionizing how we think about what are the examples of machined components in medical applications.
Understanding machined components is essential for grasping the full impact of CNC technology. These components range from simple fasteners to complex assemblies that play critical roles in the functionality and safety of medical devices. By delving into what are the components of a medical device, we can appreciate how each part contributes to overall patient care and operational efficiency.
Exploring medical device applications reveals a landscape rich with innovation and precision engineering. The demand for reliable and efficient healthcare solutions has spurred advancements in CNC medical parts, leading to enhanced performance and better patient outcomes. As we navigate through this topic, we'll uncover a comprehensive medical machined components list that highlights both common and specialized parts used within the industry.
What is CNC Turning?
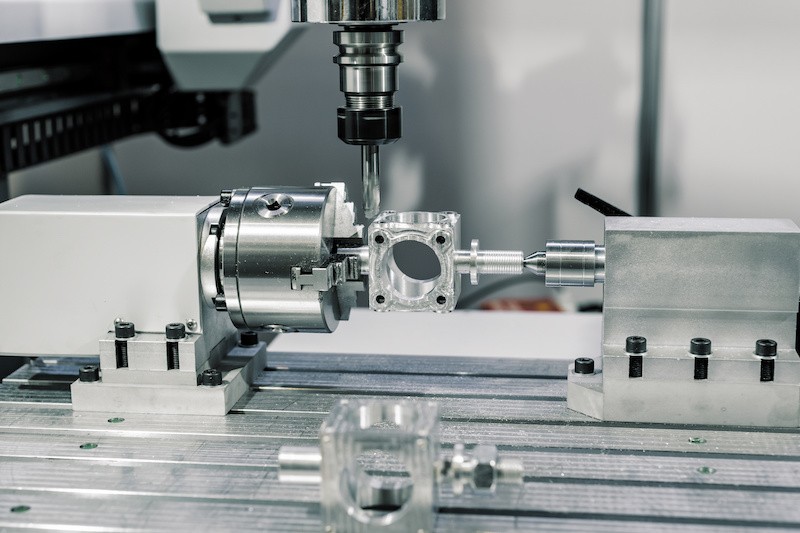
CNC turning is a revolutionary manufacturing process that has transformed how parts are produced, particularly in precision-driven industries like healthcare. By utilizing computer numerical control (CNC) technology, this method allows for the automated shaping of materials into specific geometries, ensuring high accuracy and repeatability. This makes CNC turning an essential technique for creating medical machined components that meet stringent regulatory standards.
Definition and Process Overview
At its core, CNC turning involves rotating a workpiece on a spindle while a cutting tool shapes it into the desired form. The process begins with a digital design file that guides the machine's movements, allowing for precise cuts and finishes. This level of automation not only speeds up production but also minimizes human error, making it ideal for producing critical components in medical device machining.
The versatility of CNC turning means it can create various machined components across different industries. From simple cylindrical shapes to intricate designs required in medical applications, the possibilities are nearly endless. Understanding what are the components of a medical device highlights how crucial CNC turning is in producing parts like connectors, housings, and surgical instruments.
Key Benefits of CNC Turning
One of the standout benefits of CNC turning is its ability to deliver exceptional precision consistently—vital when dealing with medical machined components where tolerances can be measured in microns. Additionally, this method significantly reduces production time compared to traditional machining processes due to its automated nature and efficiency. Cost-effectiveness also plays a role; once set up properly, CNC machines can produce large quantities of parts without sacrificing quality.
Moreover, flexibility is another advantage; manufacturers can quickly switch between different designs without needing extensive retooling or downtime. This adaptability makes it easier to respond to changing market demands or custom requests from clients seeking specific examples of machined components tailored for unique applications. In essence, these benefits position CNC turning as an indispensable tool across various sectors beyond just healthcare.
Applications Beyond Medical
While medical device machining showcases some of the most critical uses for CNC turning technology due to its demand for precision and reliability, this technique extends far beyond healthcare applications. Industries such as automotive rely heavily on CNC-turned parts for engine components like crankshafts and pistons that require durability under extreme conditions. Additionally, aerospace manufacturers utilize these machines to produce lightweight yet robust structures essential for flight safety.
Even consumer electronics benefit from CNC turning; think about those sleek smartphone casings or intricate internal mechanisms crafted with meticulous attention to detail using this method. The ability to create complex geometries efficiently means that almost any sector requiring high-quality machined parts can find value in adopting this technology into their production processes—making it an all-around game changer!
Examples of CNC Turned Parts
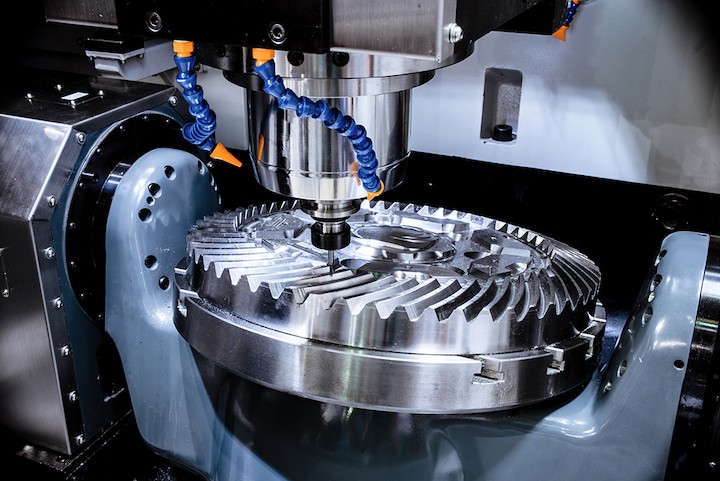
CNC turning has revolutionized the manufacturing landscape, producing parts that are essential across various industries. Among these, medical machined components stand out due to their critical role in healthcare. Let’s dive into some fascinating examples of machined components across different sectors.
Medical Machined Components Overview
In the realm of healthcare, medical machined components are vital for ensuring the safety and efficacy of devices used in patient care. These parts range from intricate surgical instruments to implantable devices like stents and prosthetics. The precision required in medical device machining means that each component must be manufactured with extreme accuracy, as even the slightest defect can have significant consequences for patient outcomes.
What are the examples of machined components in this field? Common items include syringes, dental tools, and orthopedic implants—all crafted using advanced CNC techniques to ensure reliability and performance. Additionally, a comprehensive medical machined components list would highlight features such as biocompatibility and sterilization capabilities that are crucial for these applications.
Automotive Component Cases
While medical applications showcase the high-stakes nature of CNC turning, automotive component cases reveal how versatile this technology is across industries. In automotive manufacturing, CNC turned parts play a pivotal role in producing everything from engine components to custom fittings that enhance vehicle performance.
Aerospace Industry Applications
The aerospace sector is yet another area where CNC turned parts shine brightly—literally! Components used in aircraft must withstand extreme conditions while maintaining lightweight characteristics; this is where precision machining comes into play. Aerospace manufacturers often rely on CNC technologies to produce turbine blades, landing gear mechanisms, and other critical elements with exacting standards.
What are the key features of aerospace-related machined components? They typically require materials resistant to high temperatures and corrosion while also being engineered for optimal aerodynamics. As with both medical machined components and automotive cases, attention to detail during production ensures safety and efficiency at every altitude.
Essential Components of Medical Devices
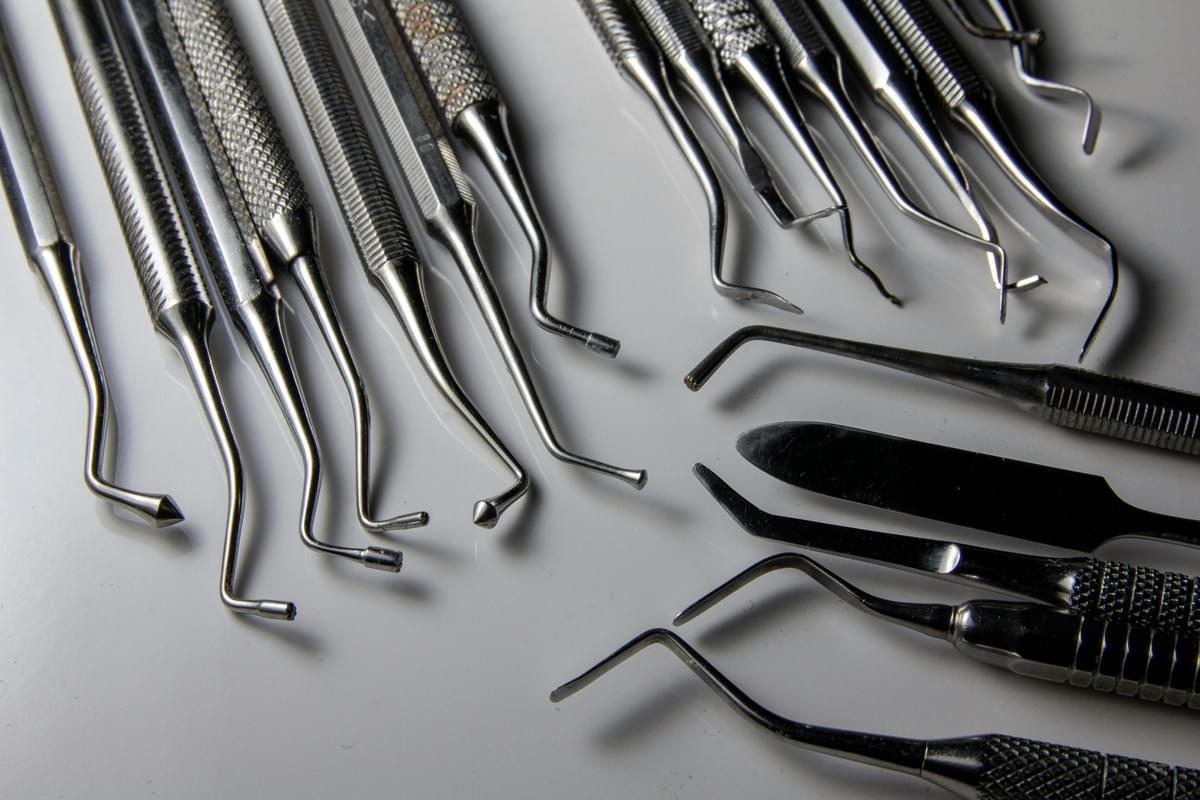
In the realm of healthcare, understanding the essential components of medical devices is crucial for effective design and manufacturing. Medical machined components play a pivotal role in ensuring that devices function properly and meet stringent industry standards. A thorough breakdown of these parts reveals their significance in enhancing patient care and safety.
Breakdown of Medical Device Parts
Medical devices are composed of various machined components, each serving a unique purpose. Commonly, these include housings, connectors, valves, and intricate surgical instruments. Understanding what are the components of a medical device helps manufacturers focus on quality and precision during the CNC medical parts production process.
These components often require customization to meet specific requirements dictated by their intended use. For instance, surgical tools may need to be tailored for ergonomic handling while maintaining high durability standards. The medical machined components list can vary widely depending on the device type but typically includes items like implantable devices, diagnostic equipment fittings, and patient monitoring systems.
Importance of Precision in Medical Machining
The importance of precision in medical machining cannot be overstated—devices must fit together seamlessly to ensure proper functionality and safety during use. This high level of accuracy is what sets CNC medical parts apart from more conventional manufacturing processes.
When dealing with life-saving equipment such as pacemakers or surgical implants, every dimension must adhere strictly to specifications outlined by regulatory bodies. Inaccuracies not only jeopardize patient safety but also increase costs due to rework or recalls—something no manufacturer wants on their record! Thus, investing in advanced CNC turning technology becomes essential for achieving the necessary precision in producing vital medical machined components.
Regulations Impacting Medical Components
The landscape of medical device manufacturing is heavily influenced by regulations aimed at ensuring safety and efficacy. Regulatory bodies like the FDA impose strict guidelines that govern everything from material selection to testing protocols for new devices entering the market. Understanding these regulations is critical for manufacturers involved in producing medical machined components.
Compliance with regulations not only affects how products are designed but also dictates how they are tested before reaching consumers—this involves rigorous quality checks throughout the production process. What are some examples of machined components that need regulatory approval? Think about everything from orthopedic implants to dental instruments; each requires thorough validation before being deemed safe for use.
Manufacturers must stay updated on evolving regulations as they can impact timelines and costs associated with bringing new products to market—a challenge that calls for agility in both design and production strategies! Ultimately, navigating this complex regulatory environment is vital for ensuring that all produced CNC medical parts meet required standards while fulfilling market needs efficiently.
Medical Machined Components List
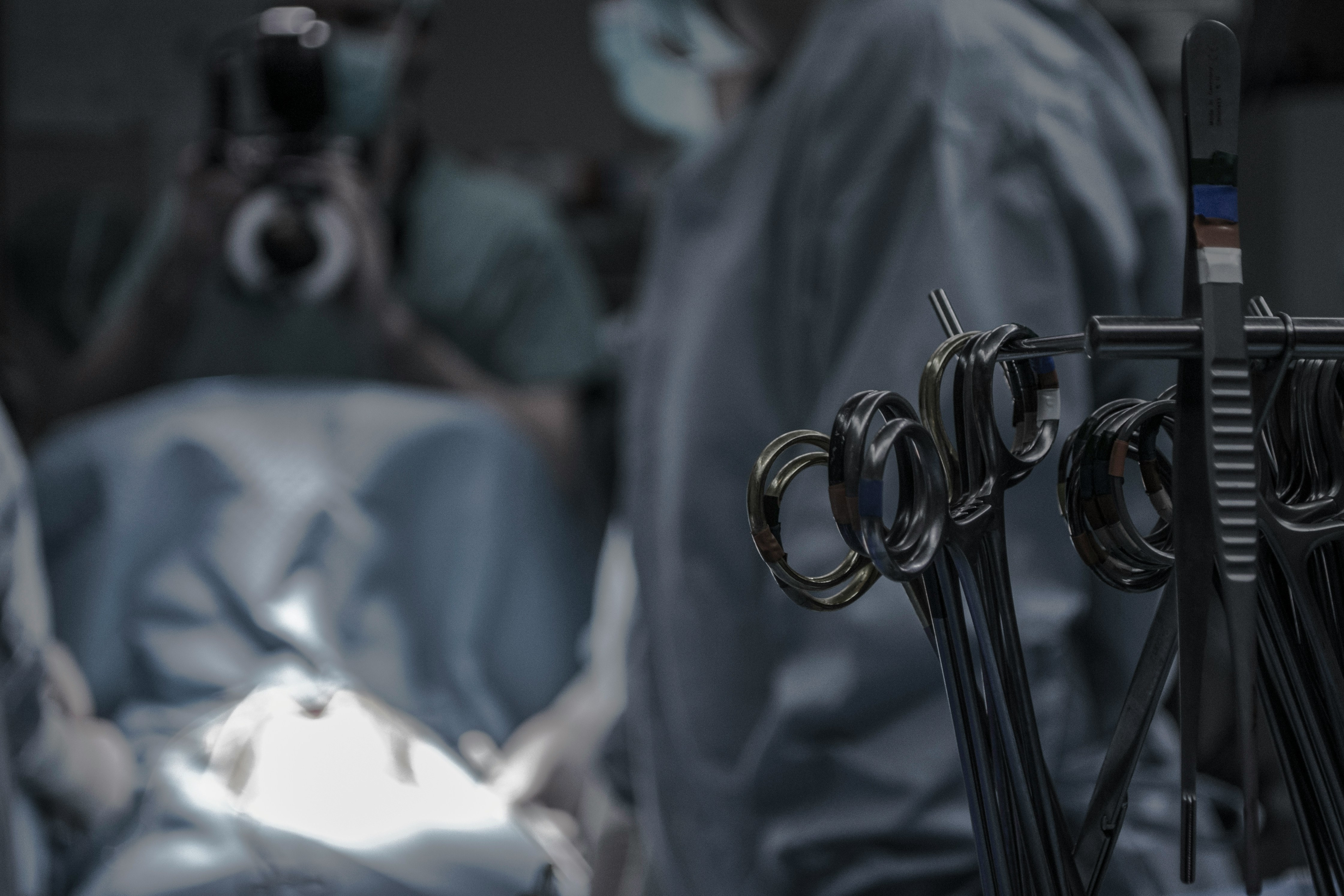
In the realm of healthcare, medical machined components play a pivotal role in ensuring the functionality and reliability of various devices. From surgical instruments to diagnostic machines, these components are designed with precision to meet stringent industry standards. Understanding what makes up a medical device can help in recognizing the importance of each part and its contribution to patient care.
Commonly Used Parts in Healthcare
When we talk about medical machined components, several parts come to mind that are commonly used across various healthcare applications. Examples include surgical tools such as scalpel handles, orthopedic implants, and housings for imaging equipment. Each component is crafted with precision machining techniques, ensuring they can withstand rigorous use while maintaining safety and efficacy.
What are the examples of machined components? Beyond surgical tools, other vital parts include valves for fluid management systems and connectors for electronic devices used in patient monitoring. These components must not only be durable but also biocompatible to ensure they do not adversely affect patients’ health during procedures or treatments.
In summary, the medical machined components list is extensive and diverse, reflecting the complexity of modern healthcare technologies. Each part plays a crucial role in enhancing treatment outcomes and improving patient safety in an increasingly demanding environment.
Customization in Medical Device Machining
Customization is key when it comes to medical device machining; no two devices are exactly alike due to varying patient needs and technological advancements. Manufacturers often tailor medical machined components based on specific requirements such as size, shape, or material properties that align with intended applications. This level of customization ensures that each component fits seamlessly into its respective system or device.
Moreover, customization allows for innovation within medical device design—think 3D-printed implants or specialized surgical instruments that cater to unique anatomical considerations. The ability to modify CNC medical parts means that manufacturers can address both standardization needs while also accommodating unique clinical scenarios effectively.
Ultimately, customization enhances the overall performance of healthcare devices by providing solutions tailored specifically for their intended use cases—bringing us closer to ideal outcomes in patient care through advanced engineering techniques.
Innovations in CNC Medical Parts
The field of CNC medical parts is constantly evolving thanks to innovations driven by technology and research advancements. New materials like bioresorbable polymers are being integrated into designs for temporary implants that dissolve over time—minimizing long-term complications for patients post-surgery. Such innovations contribute significantly towards improving recovery times while ensuring optimal functionality during critical periods.
Additionally, advancements in CNC machining processes have led to increased efficiency and precision when creating complex geometries required by modern medical devices. Technologies like multi-axis machining allow manufacturers greater flexibility when producing intricate designs necessary for high-performance equipment—ultimately enhancing capabilities across various specialties within healthcare.
As we look toward the future of medical machined components, it's clear that innovation will continue playing a central role—pushing boundaries on what’s possible within device design while keeping patient safety at the forefront of development efforts.
Choosing the Right CNC Machine
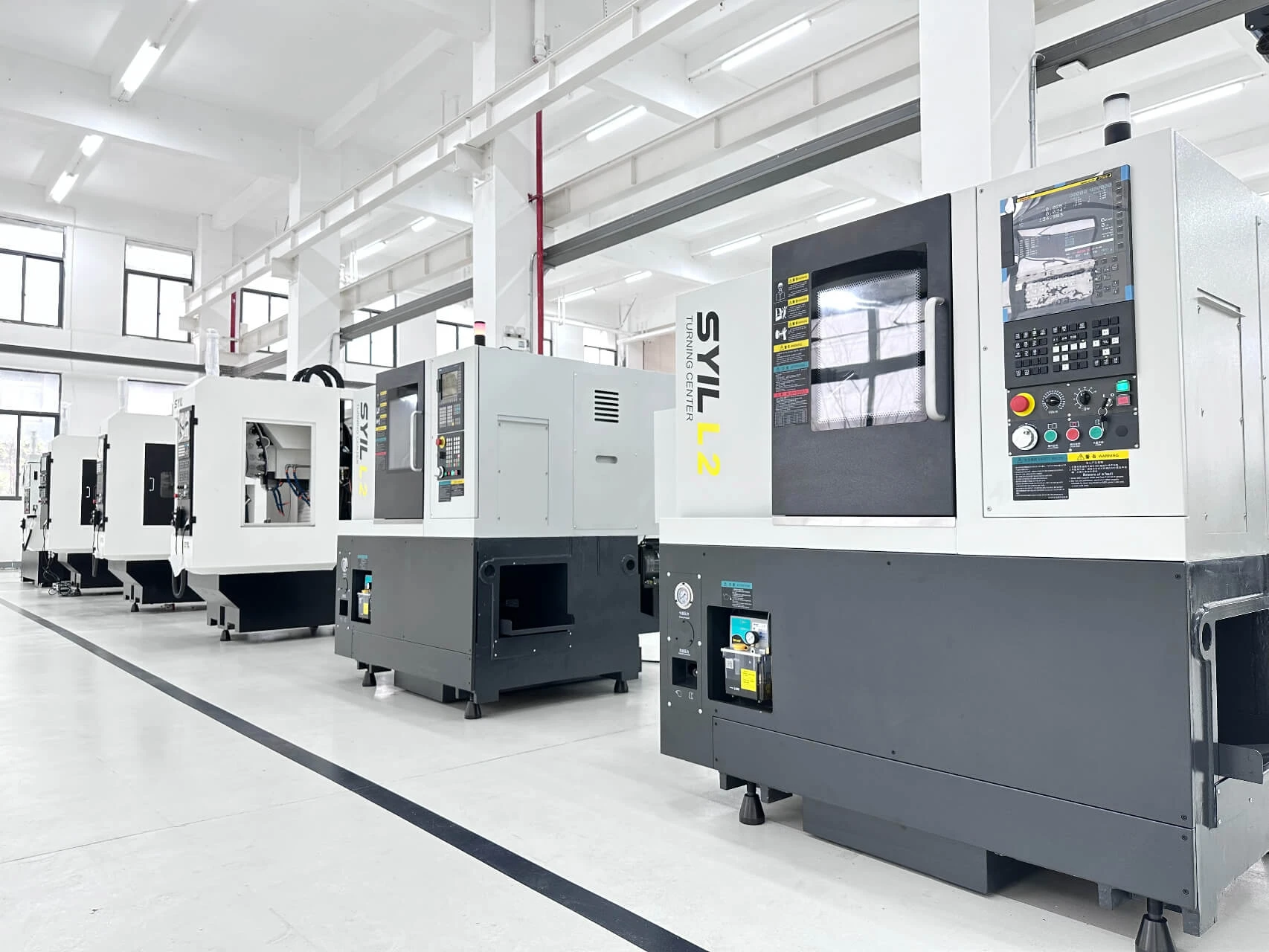
Selecting the right CNC machine is crucial for producing high-quality medical machined components. The choice can significantly affect the efficiency, precision, and overall success of your medical device machining operations. With numerous options available, understanding what sets different machines apart is essential for making an informed decision.
Why SYIL CNC Machines Stand Out
When it comes to medical device machining, SYIL CNC machines have carved a niche for themselves due to their exceptional performance and reliability. These machines are designed specifically to handle the intricate requirements of medical machined components, ensuring precision and quality in every part produced. Additionally, their user-friendly interface and robust construction make them a favorite among manufacturers looking to optimize production efficiency.
SYIL's commitment to innovation means that they continually update their technology, incorporating advanced features that enhance machining capabilities. This focus on cutting-edge development allows users to produce complex shapes and designs that are often required in modern medical devices. When considering options for CNC machines, SYIL stands out as a trusted choice for those serious about quality in medical device machining.
Comparing Options for Medical Device Machining
With various brands offering CNC machines tailored for different applications, it's important to compare features specific to medical device machining. Key factors include spindle speed, tooling options, and software compatibility—each of which can influence the production of precise medical machined components. For example, some machines may excel in speed but lack the necessary precision required for delicate parts; others may offer high accuracy but at a slower pace.
Additionally, consider how well each machine can handle different materials commonly used in healthcare applications such as titanium or polymers found in surgical instruments. Understanding what are examples of machined components needed will help narrow down choices based on specific manufacturing needs. Ultimately, selecting a machine that balances speed with accuracy will yield better results when producing complex parts used in life-saving devices.
Factors to Consider When Buying CNC Machines
When investing in a CNC machine for producing medical machined components, several factors must be evaluated beyond just price or brand reputation. First and foremost is the machine's capability to produce consistent quality over time; this is critical when dealing with components where precision can impact patient safety directly. Also essential are after-sales support services; having access to technical assistance can be invaluable when troubleshooting issues during production runs.
Another factor includes scalability—consider whether your chosen machine can grow with your business needs as demand increases or projects become more complex over time. Furthermore, understanding what are the components of a medical device will guide you toward selecting machinery capable of crafting those specific parts accurately and efficiently without compromising on quality or compliance with industry regulations.
In conclusion, making an educated choice about which CNC machine fits best will not only enhance your manufacturing capabilities but also ensure you deliver top-notch products within the competitive landscape of healthcare technology.
Conclusion
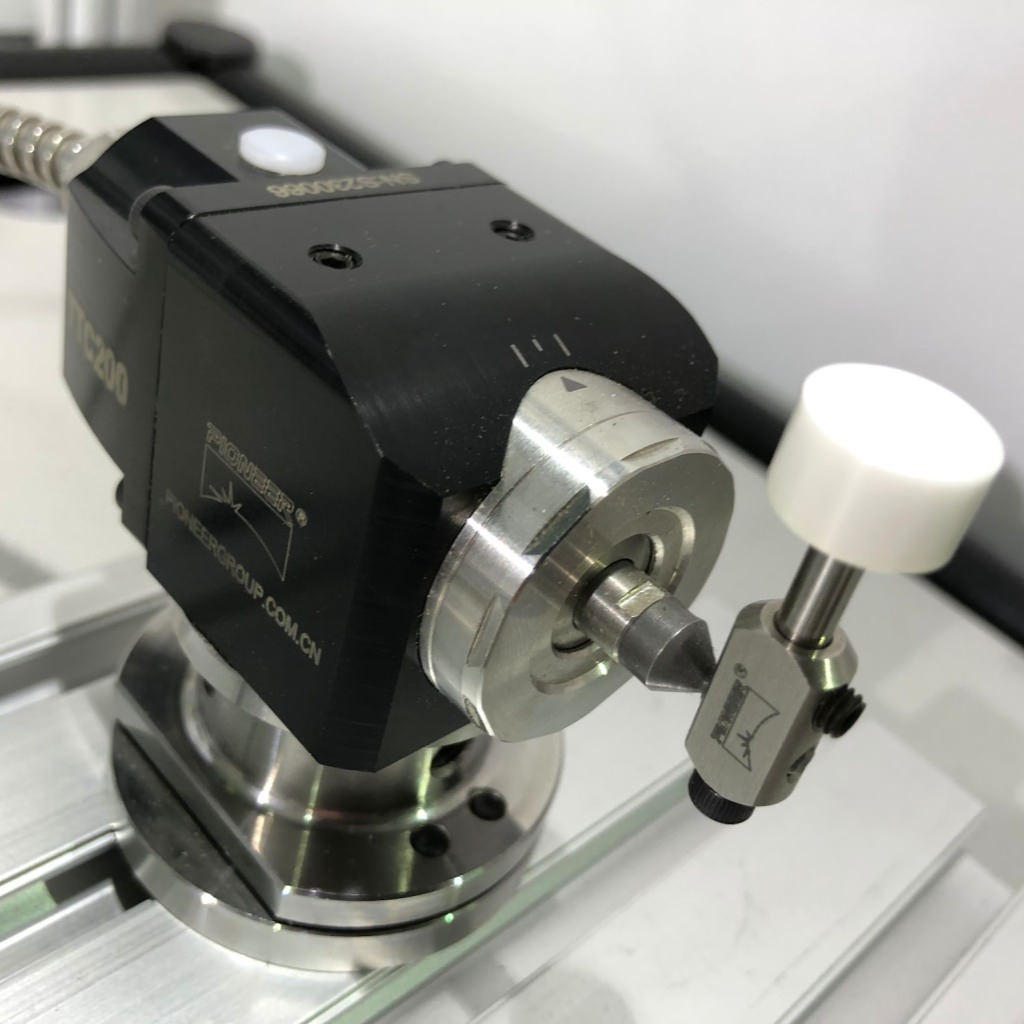
In wrapping up our exploration of CNC turning and its impact on the production of medical devices, it’s clear that this technology is not just a trend—it's a revolution. The precision and efficiency offered by CNC turning are reshaping the landscape of medical machined components, paving the way for innovations that enhance patient care and safety. As we look to the future, understanding what are the components of a medical device becomes crucial in leveraging CNC capabilities to their fullest potential.
The Future of CNC Turning
The future of CNC turning is bright, especially in the realm of medical device machining. With advancements in technology, we can expect even greater precision and efficiency in creating complex shapes and intricate designs required for modern healthcare applications. This evolution will likely lead to new examples of machined components that were previously unimaginable, further expanding the possibilities within the industry.
Enhancing Medical Device Efficiency
Enhancing medical device efficiency is at the forefront of healthcare innovation, with CNC medical parts playing a pivotal role in this process. By utilizing advanced machining techniques, manufacturers can produce high-quality components with reduced lead times and improved accuracy. This not only streamlines production but also ensures that medical machined components meet stringent regulatory standards essential for patient safety.
Key Takeaways on Machined Components
When considering a medical machined components list, remember that each part plays a vital role in overall device functionality and reliability. Understanding what are the examples of machined components helps manufacturers identify opportunities for improvement and customization tailored to specific needs within healthcare settings. Ultimately, embracing CNC technology is key to unlocking new levels of innovation in medical device machining.