Introduction
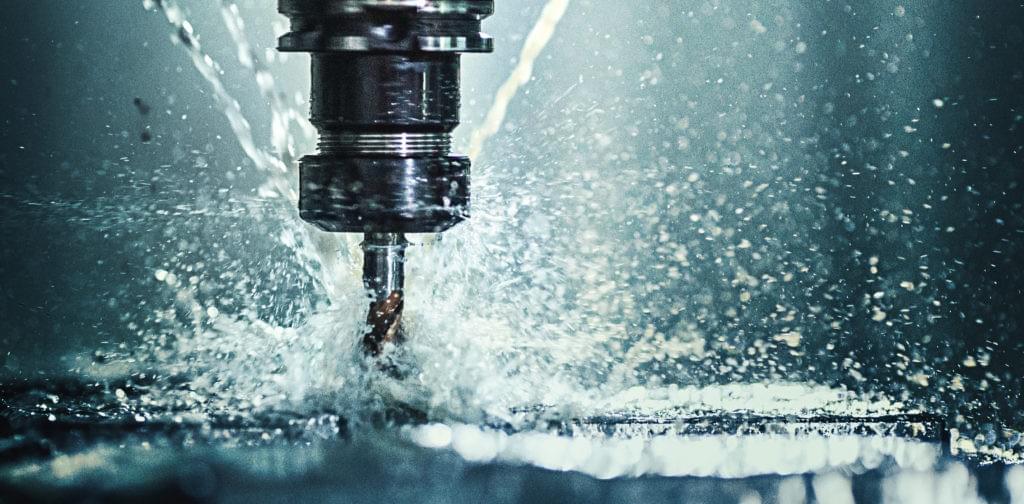
CNC lathe programming is a crucial skill in manufacturing, allowing operators to control and automate the movements of a lathe machine. By understanding how to program a CNC lathe, individuals can efficiently produce precise and complex parts with ease.
Learning CNC lathe programming is essential for anyone looking to excel in machining. It opens up opportunities for career advancement and enables individuals to take on more challenging projects. Whether you are a seasoned professional or just starting your journey in machining, mastering CNC lathe programming will undoubtedly give you a competitive edge.
In this article, we will explore the fundamentals of CNC lathe programming and delve into SYIL Machine Tools' expertise in developing precision CNC machines for milling and drilling. We will also discuss the benefits of using SYIL's state-of-the-art CNC machines, which have become synonymous with quality and reliability in the industry.
Understanding CNC Lathe Programming
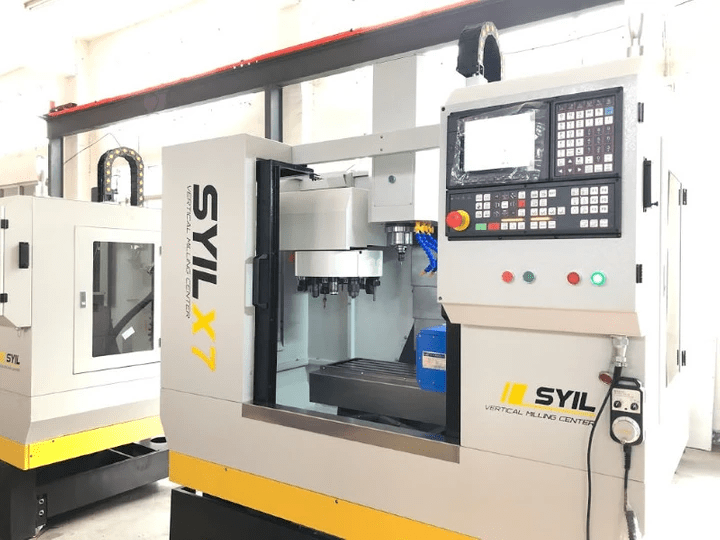
CNC lathe programming is a crucial skill for anyone working with precision machining. By mastering this skill, individuals can efficiently operate CNC lathe machines and easily create intricate designs. In this section, we will explore the basic principles of CNC lathe programming, introduce G-code and M-code, discuss SYIL's user-friendly CNC software for programming, and highlight key considerations for efficient programming.
Basic Principles of CNC Lathe Programming
To understand CNC lathe programming, it is essential to grasp the basic principles behind it. At its core, CNC lathe programming involves creating a set of instructions that guide the machine's movements and actions. These instructions are typically written in a language called G-code.
G-code consists of commands that tell the machine how to move its tools along the workpiece to shape it according to the desired design. It includes instructions for tool positioning, tool speed, feed rate, and other parameters necessary for accurate machining.
Introduction to G-code and M-code
G-code is the primary language used in CNC lathe programming. It consists of a series of alphanumeric codes representing specific commands or functions. For example, G01 represents linear interpolation for tool movement along a straight line.
M-codes, on the other hand, are used to control auxiliary functions such as coolant activation or spindle rotation direction. They provide additional control over various aspects of the machining process.
SYIL's user-friendly CNC software for programming
SYIL Machine Tools understands the importance of user-friendly software in simplifying CNC lathe programming. Their advanced software offers an intuitive interface enabling users to input their designs and generate corresponding G-code programs easily.
With SYIL's software, operators can visualize their designs in 3D before initiating the machining process. This feature allows them to identify potential issues or errors before wasting valuable resources on faulty programs.
Mastering CNC Lathe Programming Techniques
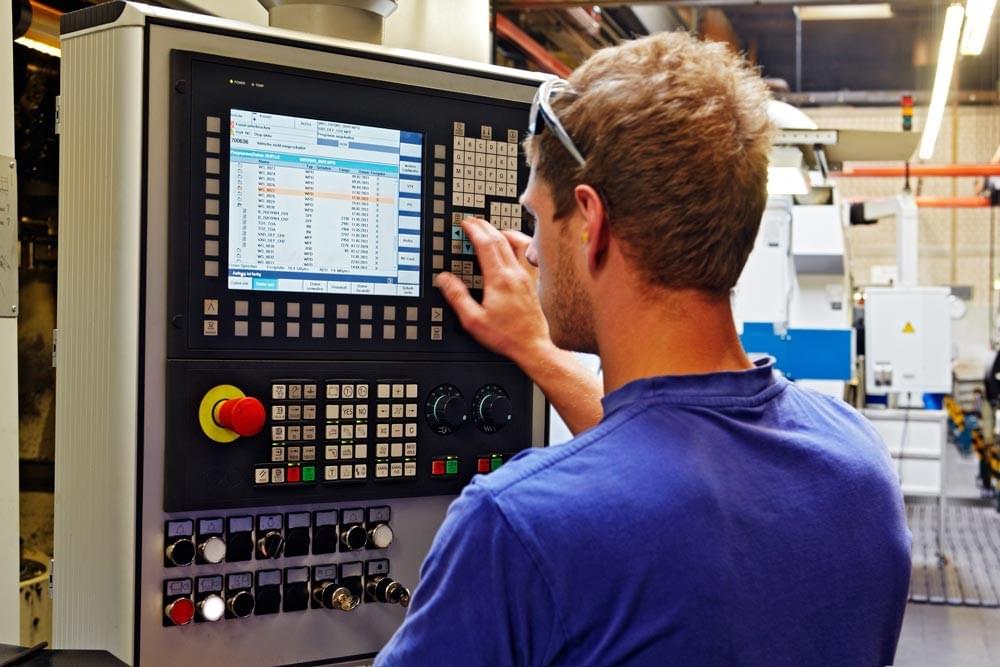
Step-by-Step Guide to Setting Up a CNC Lathe
Setting up a CNC lathe may seem daunting at first, but it can be a straightforward process with the right guidance. Here's a step-by-step guide to help you get started:
- Prepare the machine: Ensure the CNC lathe is powered and connected to the computer system. Check for any loose parts or debris that may hinder its performance.
- Install and secure workpiece: Carefully mount it onto the lathe's chuck or collet, ensuring it is firmly secured. This will prevent movement during machining.
- Select and install cutting tools: Choose appropriate ones based on your desired machining operations and materials. Insert them into the tool turret or holder, properly tightening them.
- Set work offsets: On the CNC control panel, set work offsets to determine the reference point for your machining operations. This will ensure the accurate positioning of your tools relative to the workpiece.
- Input program code: Use SYIL's user-friendly CNC software to input your program code, which consists of G-code and M-code instructions. This code will dictate the movements and actions of the CNC lathe during machining.
- Test run and adjust parameters: Before starting full-scale production, perform a test run to ensure everything functions correctly. Adjust cutting parameters such as feed rate, spindle speed, and depth of cut to optimize performance.
Proper setup is crucial for achieving accurate and efficient machining results with a CNC lathe.
Fundamentals of Tool Selection and Toolpath Planning
The right tools and planning toolpaths are essential for successful CNC lathe programming. Here are some fundamentals to keep in mind:
- Tool selection: Choose cutting tools based on the machined material, desired surface finish, and machining operations required. Consider tool geometry, coating, and durability factors to ensure optimal performance.
- Toolpath planning: Carefully plan the sequence of tool movements to achieve the workpiece's desired shape and dimensions. Determine the order of operations, such as roughing, finishing, and threading, to minimize tool changes and optimize efficiency.
- Consider machine limitations: Consider the capabilities and limitations of your CNC lathe when selecting tools and planning toolpaths. Ensure the machine can handle the chosen tools' size, reach, and cutting forces without compromising accuracy or stability.
- Optimize toolpath efficiency: Minimize unnecessary movements by optimizing toolpaths for efficient machining. Use techniques such as contouring, peck drilling, and adaptive roughing to reduce cycle times while maintaining quality.
Understanding these fundamentals of tool selection and toolpath planning can enhance productivity and achieve superior results with your CNC lathe programming.
Optimizing Cutting Parameters for Better Results
Optimizing cutting parameters is crucial to maximize efficiency and achieve high-quality results in CNC lathe programming. Here are some key considerations:
- Feed rate: The feed rate determines how fast the cutting tool moves along the workpiece during machining. Adjusting it appropriately based on material properties can prevent issues like excessive heat generation or poor surface finish.
- Spindle speed: The spindle speed determines how fast the workpiece rotates during machining operations. Finding an optimal speed based on material hardness and desired chip formation is essential for achieving accurate cuts.
- Depth of cut: The depth of cut refers to how deep each pass of the cutting tool is into the workpiece material. Balancing it with the tool's capabilities and the material's properties is crucial to avoid tool breakage or excessive wear.
- Coolant usage: Coolant helps dissipate heat, lubricate the cutting tool, and remove chips from the workpiece during machining. Adjusting the coolant flow and application method can improve tool life and surface finish.
By fine-tuning these cutting parameters based on material characteristics and machining requirements, you can optimize your CNC lathe programming for superior results.
Troubleshooting Common Programming Errors
Even with careful planning, programming errors can occur during CNC lathe operations. Here are some common issues to watch out for and how to troubleshoot them:
- Incorrect tool offsets: Check your tool offset values if your machined features are not aligning properly with the intended dimensions. Ensure that they accurately reflect the physical dimensions of your cutting tools.
- Improper feed rate or spindle speed: Inconsistent surface finish or excessive tool wear may indicate incorrect feed rate or spindle speed settings. Review your program code and adjust these parameters accordingly.
- Toolpath collisions: If you encounter collisions between the cutting tool, workpiece, or machine components, review your toolpath planning. Ensure that there is enough clearance for all movements and adjust as necessary.
- Syntax errors in program code: Mistyped commands or missing semicolons can cause syntax errors in your program code. Carefully review the code for inconsistencies or use SYIL's user-friendly CNC software for error detection.
Remember to thoroughly test and simulate your CNC lathe programs before running them on actual workpieces to minimize potential errors and maximize productivity.
Now that we have covered mastering CNC lathe programming techniques, let's move on to exploring advanced features and customization options in Section IV.
Advanced Features and Customization Options
Exploring Advanced Tooling Techniques and Strategies
When it comes to CNC lathe programming, exploring advanced tooling techniques and strategies can greatly enhance the precision and efficiency of the machining process. By utilizing specialized tools and implementing innovative strategies, operators can achieve superior results while optimizing production time.
One effective technique is using indexable carbide inserts, which allow for quick and easy tool changes without regrinding. These inserts offer excellent durability and cutting performance, making them ideal for high-speed machining operations.
Another strategy is the implementation of multi-axis machining, which enables simultaneous cutting on multiple axes. This technique allows complex geometries to be machined highly, reducing the need for multiple setups and increasing overall productivity.
By continuously exploring and adopting advanced tooling techniques and strategies, operators can stay at the forefront of CNC lathe programming and ensure optimal performance in their machining operations.
SYIL's Advanced CNC Lathe Features for Enhanced Precision
SYIL Machine Tools understands the importance of precision in CNC lathe programming. That's why they have developed advanced features that elevate the accuracy and quality of their machines.
One notable feature is SYIL's high-resolution linear scales, which provide precise feedback on machine positioning. This ensures that every movement is executed accurately, producing superior finished products.
Additionally, SYIL incorporates state-of-the-art spindle technology into its CNC lathes. With high-speed spindles capable of reaching impressive RPMs, operators can achieve faster cutting speeds while maintaining exceptional surface finishes.
Moreover, SYIL's machines have intelligent control systems with real-time monitoring and adjustment capabilities. This allows operators to make on-the-fly modifications, ensuring optimal performance and minimizing errors.
By harnessing these advanced features, operators can achieve enhanced precision in their CNC lathe programming, leading to higher-quality products and improved customer satisfaction.
Customizing CNC Lathe Programs for Specific Applications
One of the key advantages of CNC lathe programming is its versatility. Operators can customize programs to suit specific applications, making it possible to tackle a wide range of machining tasks with precision and efficiency.
To customize CNC lathe programs effectively, operators must first understand the specific application's requirements. This includes considering the type of material, desired surface finish, and dimensional tolerances.
Once the requirements are identified, operators can make adjustments to various parameters within the program. This may involve modifying cutting speeds, feed rates, tool selection, or toolpath strategies.
By tailoring the CNC lathe program to match the unique demands of each application, operators can optimize productivity and achieve optimal results. Whether it's producing intricate components or large-scale production runs, customization is crucial in maximizing efficiency and minimizing waste.
Improving Efficiency and Productivity
In CNC lathe programming, efficiency and productivity are key factors that can significantly affect the success of a manufacturing operation. By implementing time-saving strategies, utilizing automatic tool changers, implementing lean manufacturing principles, and synergizing CNC lathe programming with other processes, manufacturers can optimize their operations and achieve higher efficiency and productivity.
Time-Saving Strategies For CNC Lathe Programming
Time is money in the manufacturing industry, and finding ways to save time in CNC lathe programming can greatly impact overall productivity. One effective strategy is to use pre-programmed templates or macros that allow for quick and easy setup of common machining operations. These templates can be customized to fit specific needs and greatly reduce programming time.
Another time-saving strategy is to utilize simulation software that allows programmers to visualize the machining process before running the program on the CNC lathe. This allows for early detection of potential issues or errors, saving valuable time that would otherwise be spent on trial-and-error testing.
Utilizing SYIL's Automatic Tool Changers for Increased Productivity
SYIL Machine Tools offers a range of precision CNC machines with automatic tool changers. These tool changers allow seamless transitions between cutting tools without manual intervention, resulting in significant time savings during machining operations.
By utilizing SYIL's automatic tool changers, manufacturers can reduce downtime between tool changes and increase overall machine uptime. This improves productivity and ensures consistent quality throughout the machining process.
Implementing Lean Manufacturing Principles for Efficiency
Lean manufacturing principles focus on eliminating waste and maximizing value-added activities. When applied to CNC lathe programming, these principles can help manufacturers achieve higher levels of efficiency and productivity.
One key aspect of lean manufacturing is optimizing the layout of the machining area to minimize unnecessary movement and reduce setup time. By organizing tools, materials, and equipment in a logical and efficient manner, programmers can save valuable time during setup and changeover processes.
Industry Applications and Case Studies
Real-World Examples of CNC Lathe Programming Applications
CNC lathe programming has revolutionized various industries, enabling precise and efficient manufacturing processes. One notable application is the automotive industry, where CNC lathe machines produce complex engine components such as crankshafts and camshafts. The ability to program intricate toolpaths allows for consistent and accurate production, ensuring high-quality vehicle parts.
Another industry that benefits greatly from CNC lathe programming is aerospace. The precision required in aerospace manufacturing demands advanced machining techniques, which can be achieved through CNC lathe programming. From turbine blades to landing gear components, CNC lathe machines enable the production of intricate parts with tight tolerances, ensuring safety and reliability in aircraft.
Success Stories of Companies Using SYIL CNC Machines
SYIL Machine Tools has played a vital role in empowering companies across various industries with their precision CNC machines. One success story comes from a small automotive parts manufacturer that struggled with manual machining processes before adopting SYIL's CNC lathes. The company significantly improved productivity by implementing SYIL's user-friendly software and leveraging its advanced features while maintaining exceptional quality standards.
SYIL's Commitment to Sustainability in Manufacturing
SYIL Machine Tools prioritizes quality and precision and places great importance on sustainability in manufacturing. They actively seek ways to minimize waste and reduce environmental impact throughout their production processes. Manufacturers can optimize cutting parameters by utilizing CNC lathe programming, reducing material waste and energy consumption.
SYIL also promotes eco-friendly materials and implements recycling initiatives within its facilities. Their commitment to sustainability extends beyond their own operations as they encourage their customers to adopt sustainable practices through efficient CNC lathe programming techniques. By minimizing waste and maximizing resource utilization, SYIL aims to contribute to a greener future for the manufacturing industry.
Conclusion
CNC lathe programming is a crucial skill for individuals and industries alike. By learning how to program a CNC lathe, you can unlock a world of possibilities in precision machining. SYIL Machine Tools significantly empowers individuals and industries with their expertise in developing and manufacturing precision CNC machines.
It is essential to recognize the vast potential of CNC lathe programming. With the right knowledge and tools, you can create intricate designs and achieve remarkable precision in your machining projects. Whether you are a hobbyist or a professional, exploring the capabilities of CNC lathe programming can take your work to new heights.
The future of CNC machining and programming looks promising. As technology advances, we can expect even more innovative features and customization options in CNC machines. Staying updated with the latest trends and techniques can help you stay ahead of the competition in this dynamic industry.
Now is the time to embrace the power of CNC lathe programming and unlock your full potential as a machinist or manufacturer. Start your journey today with SYIL Machine Tools by your side.