Introduction
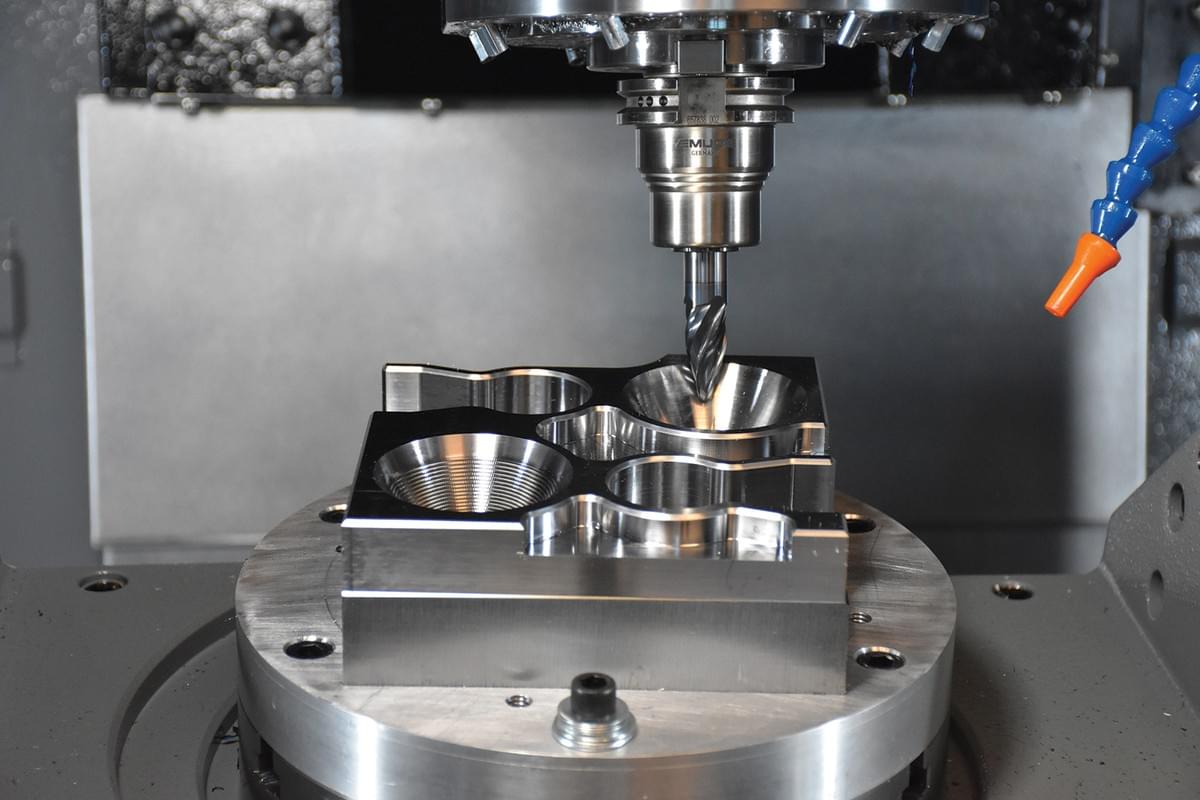
In today's competitive manufacturing landscape, understanding machining costs is essential for businesses to thrive. The ability to accurately calculate and control machining costs can significantly impact a company's profitability and success. This guide aims to provide manufacturers with valuable insights into finding affordable machining solutions, with a particular focus on how SYIL's CNC machines can help lower machining costs.
The Importance of Understanding Machining Costs
Machining costs play a crucial role in determining the overall cost of production for manufacturers. By having a comprehensive understanding of these costs, businesses can make informed decisions regarding pricing, budgeting, and resource allocation. From labor expenses to material costs and overheads, every factor contributes to the final machining cost per hour. By analyzing these factors, manufacturers can identify areas for improvement and implement strategies to optimize efficiency.
Finding Affordable Machining Solutions: A Guide for Manufacturers
For many manufacturers, finding affordable machining solutions is key to remaining competitive in the market. This guide aims to provide valuable insights into various strategies and techniques that can help reduce machining costs without compromising on quality or productivity. From streamlining operations to implementing advanced tooling techniques, manufacturers will discover practical tips they can apply in their own production processes.
How SYIL's CNC Machines Can Help Lower Machining Costs
SYIL Machine Tools develops and manufactures precision CNC machines for milling and drilling. With over 12k machines supplied globally, they prioritize quality and sustainability. SYIL's CNC machines offer an affordable solution for manufacturers looking to lower their machining costs without sacrificing precision or efficiency. By leveraging advanced technology and innovative design features, SYIL machines enable businesses to optimize productivity while reducing overall expenses.
With the introduction set up, we will now delve deeper into understanding machining costs and the factors that contribute to them. By exploring average machine shop rates and strategies for reducing machining costs, manufacturers can gain valuable insights to make informed decisions in their production processes.
Understanding Machining Costs
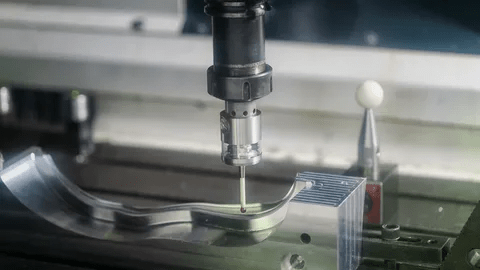
Machining costs are a crucial consideration for manufacturers looking to optimize their operations and reduce expenses. By understanding the factors that contribute to machining costs, calculating the machining cost per hour, and recognizing the role of labor, materials, and overhead expenses, manufacturers can make informed decisions to improve their bottom line.
What Factors Contribute to Machining Costs?
Several factors influence machining costs. First and foremost is the complexity of the part being machined. Intricate designs require more time and precision, increasing the overall cost. Additionally, the type of material being used plays a significant role in determining machining costs. Harder materials often require specialized tools and techniques, driving up expenses.
Furthermore, the quantity of parts being produced affects machining costs. Larger production runs typically benefit from economies of scale, resulting in lower per-unit costs. On the other hand, smaller production runs may incur higher setup costs.
Calculating Machining Cost per Hour: A Detailed Analysis
Calculating machining cost per hour involves considering various elements such as labor, machine depreciation, tooling expenses, energy consumption, and maintenance costs. By summing up these components and dividing by the number of hours a machine operates within a given period, manufacturers can determine their hourly machining cost.
Accurate calculation is crucial for effective budgeting and pricing strategies. It allows manufacturers to understand their true operational expenses and make informed decisions regarding pricing structures and profitability.
The Role of Labor, Materials, and Overhead Expenses in Machining Costs
Labor is one of the most significant contributors to machining costs. Skilled operators can demand higher wages due to their expertise in operating CNC machines effectively. Investing in training programs or hiring skilled personnel can help optimize labor efficiency while minimizing overall expenses.
Materials also play a vital role in determining machining costs. The price of raw materials fluctuates based on market conditions or availability. Manufacturers must carefully manage their material inventory to avoid waste and unnecessary expenses.
Overhead expenses, including rent, utilities, and administrative costs, are indirect but essential factors in machining costs. These expenses should be allocated proportionally to each machine's usage to accurately reflect the true cost of production.
In the next section, we will explore average machine shop rates and regional variations in machining costs on a global scale. Stay tuned for valuable insights on competitive pricing strategies for manufacturers.
Exploring Average Machine Shop Rates
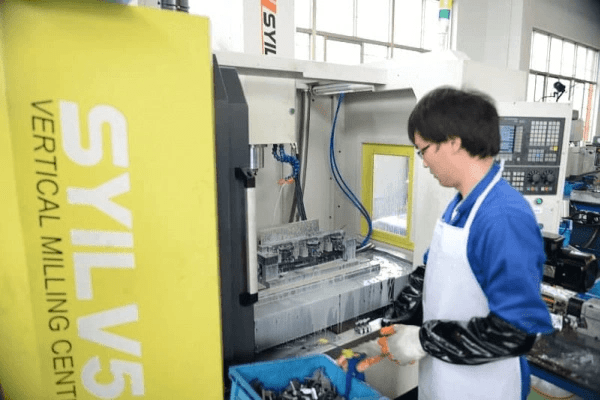
Comparing Machine Shop Hourly Rates: What to Expect
When it comes to machining costs, one crucial factor to consider is the machine shop hourly rate. This rate determines how much you will be charged for the time spent on your project. It's important to compare and understand these rates to ensure you are getting a fair price for your machining needs.
Different machine shops may have varying hourly rates based on factors such as location, expertise, and equipment capabilities. On average, machine shop hourly rates can range from $50 to $150 per hour. However, keep in mind that these rates can vary significantly depending on the complexity of the project and the level of precision required.
Regional Variations in Machining Costs: A Global Perspective
Machining costs can also vary significantly across different regions globally. Factors such as labor costs, overhead expenses, and market competition all play a role in determining regional variations in machining costs.
For example, countries with lower labor costs like China or India may offer more competitive pricing compared to countries with higher labor costs like the United States or Germany. However, it's important to consider other factors such as quality standards and communication barriers when outsourcing machining projects internationally.
Using Benchmarking Data to Determine Competitive Pricing
Benchmarking data is a valuable tool for manufacturers looking to determine competitive pricing for their machining projects. By comparing your machining costs to industry standards and competitors' rates, you can identify areas where you may be overspending or opportunities to reduce costs.
SYIL Machine Tools, a leading manufacturer of precision CNC machines, provides customers with access to benchmarking data through their cost calculation tools. These tools allow manufacturers to input their specific project details and receive accurate estimates of machining costs per hour.
By leveraging technology and utilizing SYIL's cost calculation tools, manufacturers can gain a competitive edge in the ever-changing manufacturing landscape. These tools not only simplify the process of calculating machining costs but also provide valuable insights for optimizing efficiency and reducing expenses.
Strategies for Reducing Machining Costs
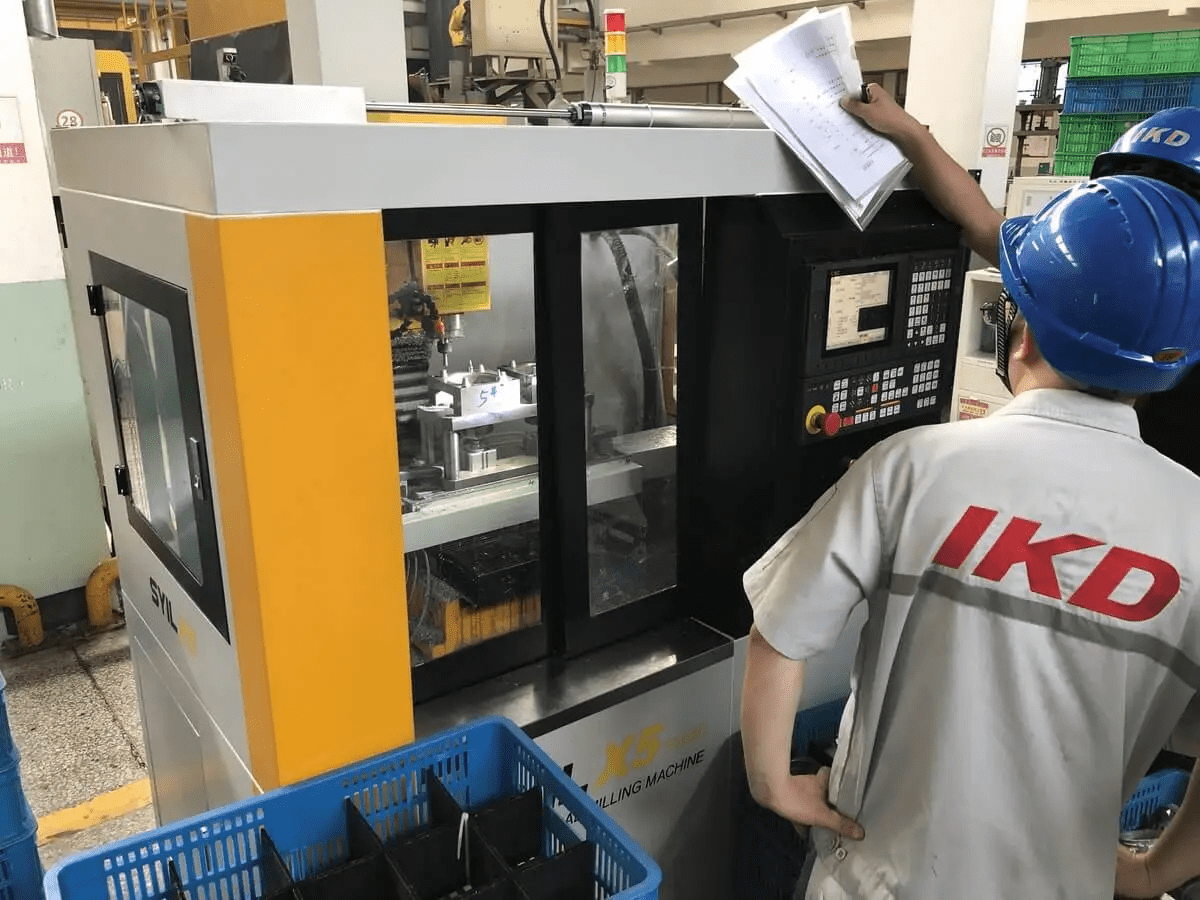
In order to lower machining costs, manufacturers can implement various strategies that focus on maximizing efficiency, optimizing productivity, and considering the benefits of outsourcing versus in-house machining.
Maximizing Efficiency: Tips for Streamlining Operations
One effective way to reduce machining costs is by maximizing operational efficiency. This involves carefully analyzing each step of the machining process and identifying areas where improvements can be made. For example, manufacturers can eliminate unnecessary steps or redundant tasks that consume time and resources. By streamlining operations, companies can significantly decrease production time and minimize waste, ultimately lowering overall machining costs.
Another way to maximize efficiency is by investing in advanced machinery and technology. Upgrading to state-of-the-art CNC machines like SYIL's precision tools can greatly improve productivity and accuracy. These machines are designed to perform complex tasks with minimal human intervention, resulting in faster turnaround times and reduced labor costs.
Implementing Advanced Tooling Techniques to Optimize Productivity
Implementing advanced tooling techniques is another effective strategy for reducing machining costs. By using high-quality cutting tools that are specifically designed for specific materials and applications, manufacturers can optimize productivity and achieve better results.
The Benefits of Outsourcing vs. In-House Machining
When it comes to reducing machining costs, businesses should also consider the benefits of outsourcing certain manufacturing processes instead of performing them in-house.
Outsourcing machining tasks to specialized external vendors can often result in cost savings due to economies of scale. These vendors typically have access to advanced machinery, specialized expertise, and established supply chains, which can lead to lower production costs. Additionally, outsourcing allows manufacturers to focus on their core competencies while leaving the machining processes to experts in the field.
However, it's important to weigh the pros and cons of outsourcing versus in-house machining based on factors such as quality control, intellectual property protection, and overall business objectives. SYIL's CNC machines provide an affordable solution for manufacturers looking to bring machining operations in-house without compromising on quality or cost-efficiency.
By implementing these strategies for reducing machining costs – maximizing efficiency through streamlined operations, implementing advanced tooling techniques to optimize productivity, and considering the benefits of outsourcing versus in-house machining – manufacturers can significantly improve their bottom line while maintaining high-quality standards.
SYIL's CNC Machines: An Affordable Solution
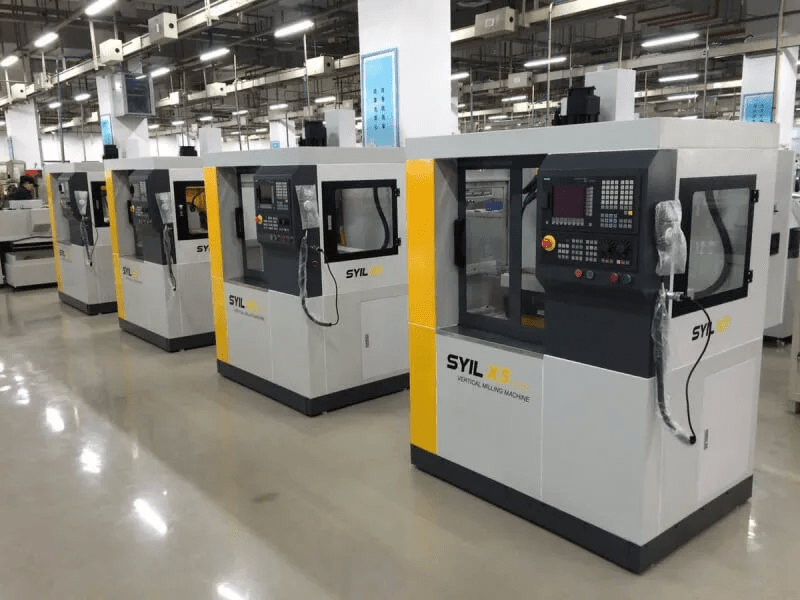
SYIL Machine Tools develops and manufactures precision CNC machines for milling and drilling. With over 12k machines supplied globally, they prioritize quality and sustainability.
Introducing SYIL Machine Tools: Precision CNC Machines for Every Budget
SYIL Machine Tools offers a wide range of precision CNC machines that cater to every budget. Whether you are a small-scale manufacturer or a large industrial operation, SYIL has the perfect solution for you. Their machines are designed to deliver exceptional performance and accuracy, ensuring that you can achieve high-quality results without breaking the bank.
The Advantages of SYIL's CNC Machines in Reducing Machining Costs
Investing in SYIL's CNC machines can significantly reduce your machining costs. These machines are equipped with advanced features that maximize efficiency and productivity. With faster cutting speeds and improved accuracy, you can complete machining tasks in less time, saving on labor costs. Additionally, the precision of SYIL's machines minimizes material waste, further reducing expenses.
Customer Success Stories: How SYIL Machines Have Lowered Production Expenses
SYIL has a long list of satisfied customers who have experienced substantial cost savings by using their CNC machines. One such success story is XYZ Manufacturing, a small-scale automotive parts manufacturer. By switching to SYIL's CNC machine, they were able to increase their production output by 30% while reducing machining costs by 20%. This allowed them to remain competitive in the market and expand their business.
SYIL's commitment to providing affordable precision machinery has made them a trusted partner for manufacturers worldwide. By investing in their CNC machines, you can optimize your operations and achieve significant cost savings. Don't miss out on the opportunity to enhance your productivity and profitability with SYIL Machine Tools.
Leveraging Technology: Machining Cost Calculation Excel
In today's fast-paced manufacturing landscape, leveraging technology is essential for optimizing efficiency and accuracy in machining cost calculations. By utilizing advanced tools such as Machining Cost Calculation Excel, manufacturers can simplify the process and ensure accurate estimations of their machining costs.
How Technology Can Simplify and Accurately Calculate Machining Costs
Technology plays a crucial role in simplifying and accurately calculating machining costs. With the help of software like Machining Cost Calculation Excel, manufacturers can input various factors such as labor costs, material expenses, machine depreciation, and overhead expenses to generate precise estimates of their overall machining costs.
By automating the calculation process, technology eliminates the need for manual calculations that are prone to errors. This not only saves time but also ensures accuracy in determining the true cost per hour for each machining operation.
Exploring Machining Cost Calculation Excel Templates
Machining Cost Calculation Excel offers a range of templates that cater to different manufacturing needs. These templates provide pre-defined formulas and fields where manufacturers can input relevant data to calculate their machining costs effectively.
Templates may include sections for labor costs, material prices, machine maintenance expenses, tooling costs, and other variables that contribute to overall machining costs. By using these templates as a starting point, manufacturers can easily customize them to fit their specific requirements and obtain accurate cost estimates.
Conclusion
Choosing the Right Machining Solution for Your Business
When it comes to selecting a machining solution for your business, it's crucial to consider factors such as cost, efficiency, and precision. SYIL Machine Tools offers a range of precision CNC machines that cater to every budget. With over 12k machines supplied globally, SYIL prioritizes quality and sustainability, ensuring that their machines deliver reliable performance while reducing machining costs.
SYIL's CNC Machines: Empowering Manufacturers with Affordable Precision
SYIL's CNC machines are designed to provide affordable precision without compromising on quality. By investing in SYIL's machines, manufacturers can benefit from advanced tooling techniques, streamlined operations, and optimized productivity. These features help lower machining costs by maximizing efficiency and reducing labor expenses.
Unlocking Cost Savings Opportunities in the Ever-Changing Manufacturing Landscape
In today's ever-changing manufacturing landscape, finding cost-saving opportunities is essential for businesses to stay competitive. SYIL's CNC machines offer a solution by providing affordable precision that helps reduce machining costs. By leveraging technology and utilizing tools like the machining cost calculation excel templates provided by SYIL, manufacturers can accurately calculate their machining costs and identify areas for improvement.
With the right machining solution in place, manufacturers can unlock significant cost savings opportunities. Whether it's through maximizing efficiency, implementing advanced tooling techniques, or outsourcing certain tasks, businesses can optimize their operations and reduce overall expenses.
By choosing SYIL Machine Tools' precision CNC machines, manufacturers can empower themselves with affordable solutions that deliver precise results while minimizing machining costs. With SYIL's commitment to quality and sustainability combined with their extensive experience in the industry, businesses can trust that they are investing in reliable and cost-effective machining solutions.