Introduction
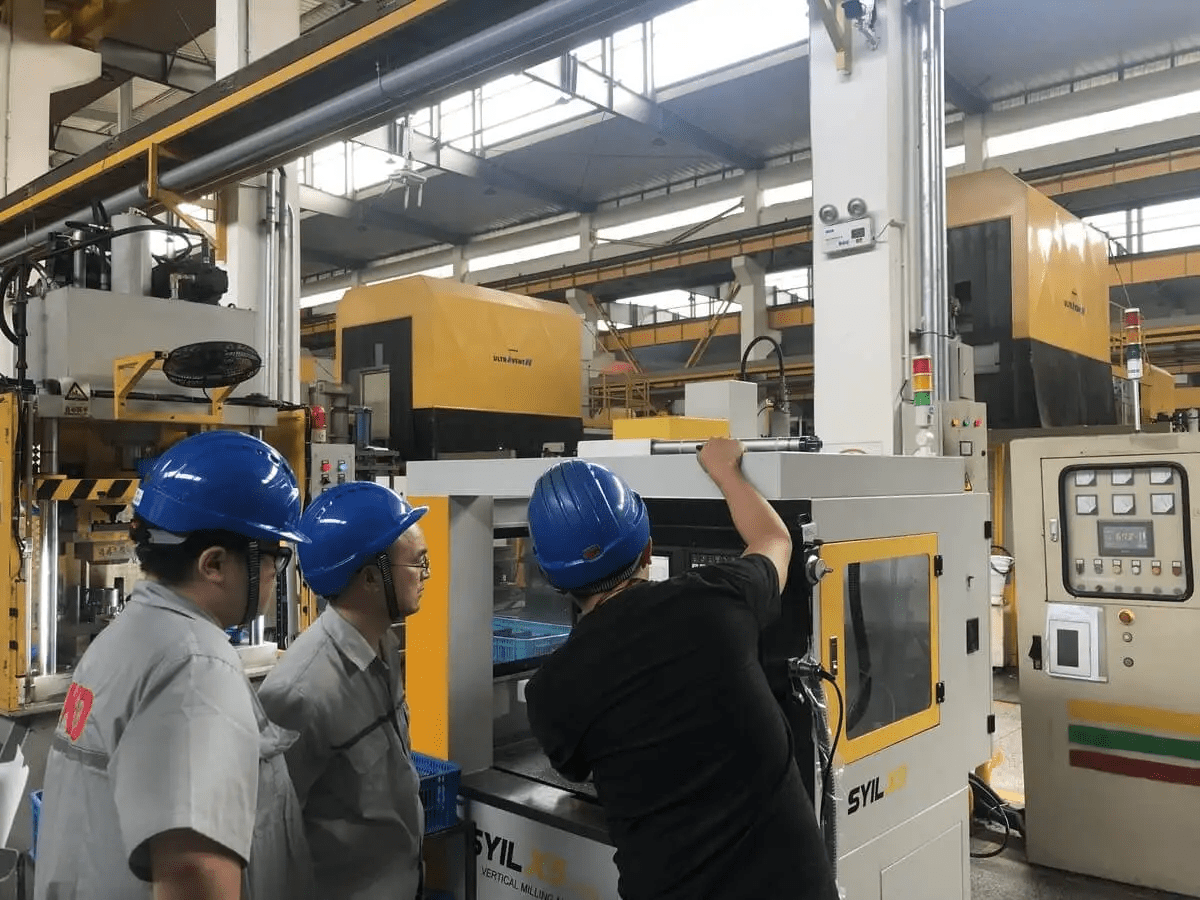
CNC machines have revolutionized the manufacturing industry with their precision and efficiency. These automated machines use computer programming to control various operations, including milling and drilling. Understanding how to run a CNC machine is crucial for anyone involved in this field, as it ensures optimal performance and productivity.
One notable player in the CNC machine industry is SYIL Machine Tools. With its expertise in developing and manufacturing precision CNC machines for milling and drilling, SYIL has established itself as a trusted brand globally. Their commitment to quality and sustainability sets them apart, making them a reliable partner for businesses needing advanced machining solutions.
Proper knowledge and understanding of CNC machine operation are essential for operators to harness the full potential of these powerful tools. Running a CNC machine can be challenging and may result in errors or subpar output without a solid grasp of the fundamentals.
This article will explore the five essential steps to successfully run a CNC machine, equipping you with the necessary skills to excel in this field.
1. Preparing the CNC Machine
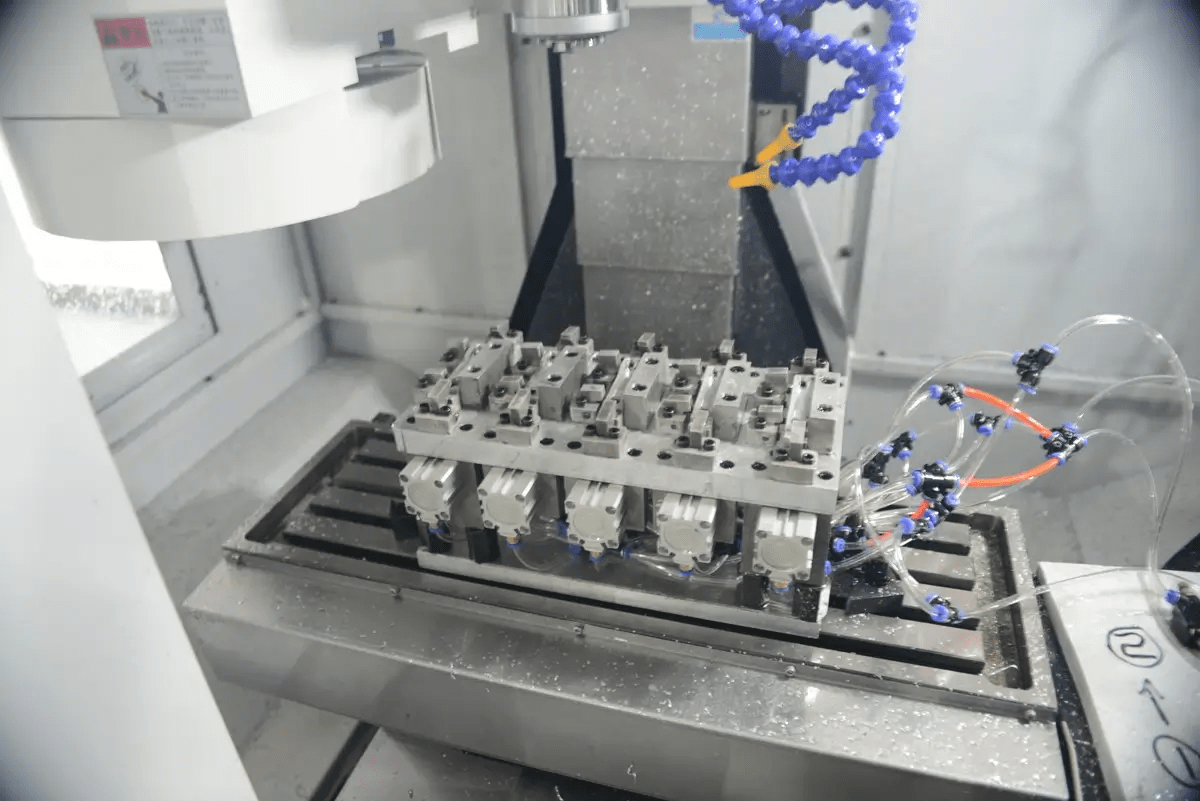
Proper preparation is crucial for successfully operating a CNC machine. This section will guide you through the essential steps to ensure your machine is ready for operation.
Ensuring the machine is properly set up and calibrated
Before running a CNC machine, it is important to ensure that it is properly set up and calibrated. This involves checking the alignment of the machine's axes, verifying that all components are securely fastened, and ensuring that the machine's software is correctly installed and updated. Proper calibration guarantees accurate and precise machining results.
Checking and preparing the necessary tools and materials
To run a CNC machine smoothly, it is essential to have all the necessary tools and materials readily available. This includes checking if you have the appropriate cutting tools or drill bits for your specific machining task. Additionally, ensure you have an adequate supply of raw materials, such as metal or wood stock, to feed into the machine.
Loading the design file or program into the machine's software
Once your CNC machine is ready, it's time to load the design file or program into its software. This step involves transferring your CAD (Computer-Aided Design) file or CAM (Computer-Aided Manufacturing) program into the control panel of your CNC machine. Double-check that all dimensions and parameters are accurately inputted to avoid errors during operation.
Verifying the machine's safety features and emergency stop button
Safety should always be a top priority when operating any machinery, including CNC machines. Before starting your machining process, take a moment to verify that all safety features on your CNC machine are functioning correctly. Ensure that emergency stop buttons are easily accessible for unforeseen circumstances or emergencies.
Setting up Workpieces and Tools
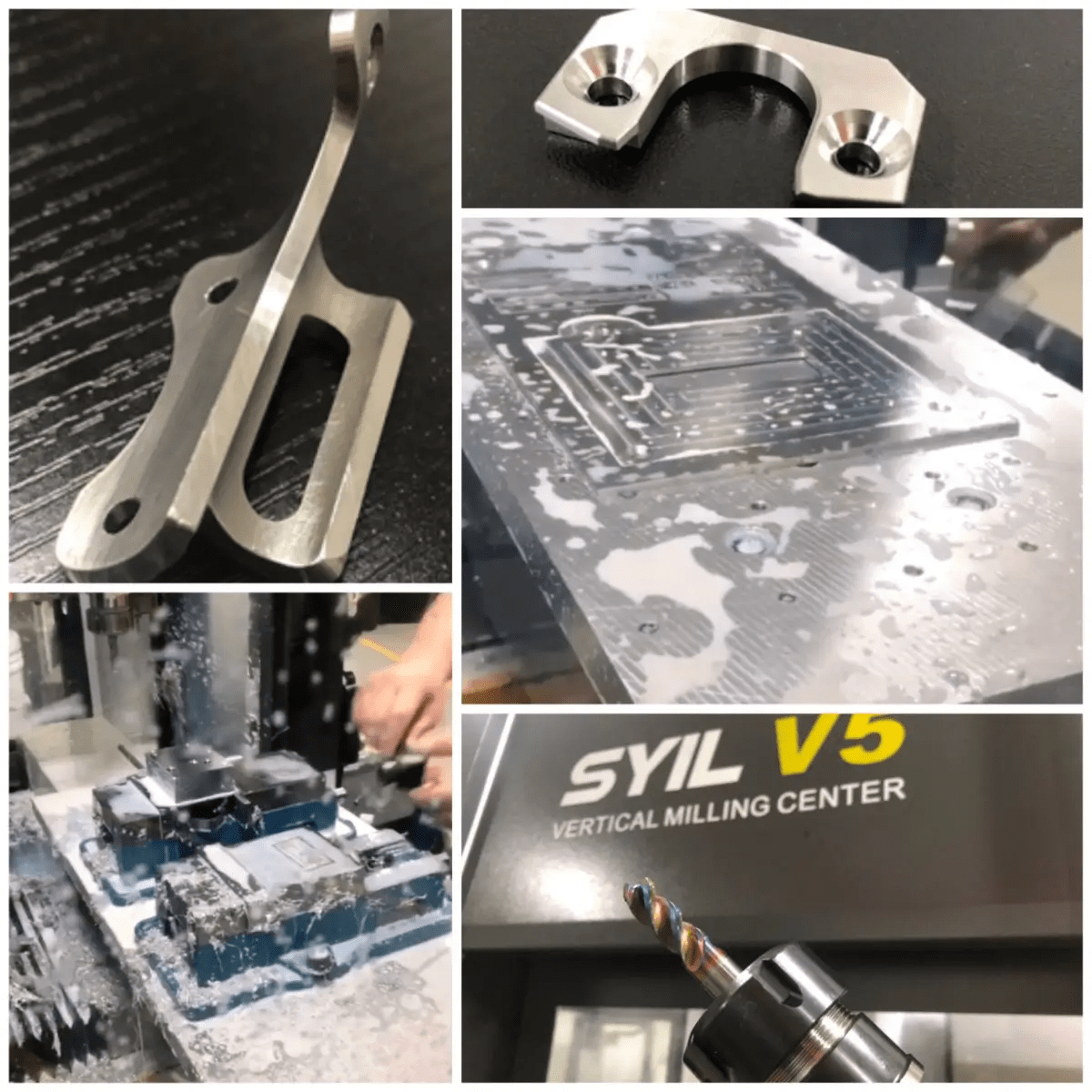
Properly securing the workpiece is crucial when setting up a CNC machine. Whether on the machine's table or vice, ensuring its stability is essential for accurate machining. Using clamps or fixtures, the workpiece can be securely held in place, preventing any movement during operation.
Installing and aligning the necessary cutting tools or drill bits is another important step in preparing a CNC machine. It involves carefully selecting the appropriate tools for the specific job at hand. The tools must properly align with the workpiece to ensure precise cutting or drilling.
To achieve optimal results, the machine's speed, feed rate, and depth of cut must be adjusted. These settings determine how fast the tool moves, how much material it removes with each pass, and how deep it cuts into the workpiece. By finding the right balance, you can achieve efficiency and accuracy in your machining process.
Using appropriate workholding methods is vital for stability and precision during CNC machining. This involves choosing suitable clamping techniques or fixtures that provide secure support to prevent any movement of the workpiece while it's being machined. This ensures consistent results and reduces the risk of errors.
These steps will help you effectively set up your workpiece and tools on a CNC machine. Properly securing the workpiece ensures stability throughout the machining process, while accurately aligning cutting tools guarantees precise results. Adjusting speed, feed rate, and depth of cut optimizes efficiency while using appropriate workholding methods enhances stability and precision.
SYIL Machine Tools develops and manufactures precision CNC machines for milling and drilling. With over 12k machines supplied globally, they prioritize quality and sustainability. Operating in multiple countries, SYIL is becoming a recognized brand in the industry.
Programming and Running the Machine
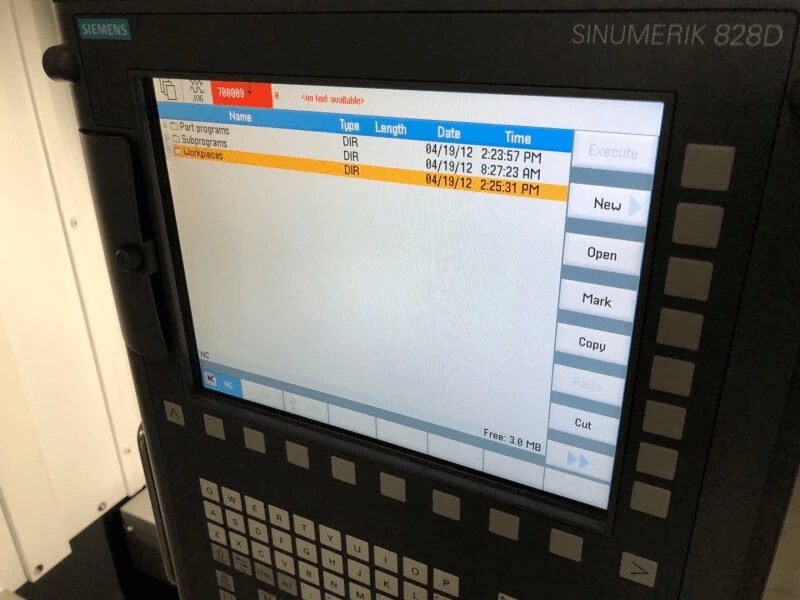
Familiarize yourself with the machines control panel and software
To run a CNC machine effectively, one must familiarize oneself with its control panel and software. Understanding the functions and features of the control panel allows operators to navigate different settings and make necessary adjustments. Similarly, becoming familiar with the software used for programming is crucial for inputting the necessary parameters and commands for operation.
Input correct parameters and commands
Operators must input the correct parameters and commands into the machine's software to ensure smooth operation. This includes specifying the cutting or drilling speed, feed rate, depth of cut, and other relevant settings. By accurately entering these values, operators can achieve desired results while minimizing errors or complications during machining.
Run a test program or simulation
Before starting production, running a test program or simulation is advisable to ensure proper operation. This allows operators to verify that all settings are correctly configured and that there are no potential issues or errors that could affect productivity or damage the workpiece or machine. Running a simulation also provides an opportunity to make any necessary adjustments before commencing actual production.
Monitor system performance
Once production begins, monitoring the machine's performance is crucial for maintaining quality and efficiency. Operators should regularly check for any signs of malfunction or deviation from expected results. By closely observing the machine's performance, operators can identify any issues promptly and make necessary adjustments to ensure optimal output.
Programming and running a CNC machine requires precision, attention to detail, and continuous monitoring. Familiarity with the control panel and software allows operators to navigate different settings smoothly. Inputting accurate parameters ensures proper operation, while running test programs helps identify potential issues before commencing production. Monitoring performance during operation enables prompt adjustments when needed.
SYIL Machine Tools develops and manufactures precision CNC machines for milling and drilling. With over 12k machines supplied globally, they prioritize quality and sustainability. Operating in multiple countries, SYIL is becoming a recognized brand in the industry. By partnering with SYIL, operators can access reliable CNC machines that enhance productivity and precision.
Troubleshooting and Maintenance
Proper troubleshooting and maintenance are crucial for ensuring the optimal performance and longevity of CNC machines. By promptly addressing common issues or errors during operation, performing routine maintenance tasks, cleaning and lubricating machine components regularly, and keeping track of machine usage for scheduling professional maintenance, operators can maximize the efficiency and reliability of their CNC machines.
Identifying and addressing common issues or errors during operation
During CNC machine operation, it is essential to be aware of common issues or errors that may arise. These can include tool breakage, incorrect tool paths, material misalignment, or programming errors. By closely monitoring the machine's performance and being vigilant for any unusual sounds or vibrations, operators can quickly identify potential problems.
Once an issue is identified, it is important to address it promptly to minimize downtime. This may involve adjusting cutting parameters, replacing damaged tools or parts, recalibrating the machine's settings, or reviewing the program code for errors. Prompt troubleshooting can help prevent further complications and ensure smooth operation.
Performing routine maintenance tasks to ensure optimal performance
Regular maintenance tasks are essential for keeping a CNC machine in peak condition. This includes inspecting and cleaning the machine's components, such as spindles, bearings, belts, and guides, to remove any debris or buildup that may affect performance. Additionally, lubricating moving parts with appropriate oils or greases helps reduce friction and prolongs the lifespan of these components.
Operators should also regularly check coolant levels to ensure proper cooling during machining. Inspecting filters and replacing them when necessary helps maintain a clean working environment while preventing potential damage to the machine.
Cleaning and lubricating the machine's components regularly
Regular cleaning is essential for maintaining a CNC machine's accuracy and functionality. Dust particles can accumulate on sensitive components over time, affecting their performance. Using compressed air or specialized cleaning tools to remove dust from areas such as the control panel, keyboard, and tool holders helps prevent any interference during operation.
Lubrication is another critical aspect of machine maintenance. Applying lubricants to designated points as the manufacturer recommends ensures smooth movement of machine parts and reduces wear and tear. Regular lubrication extends the components' lifespan and contributes to overall machine performance.
Keeping track of machine usage and scheduling professional maintenance
To ensure optimal performance and prevent unexpected breakdowns, keeping track of a CNC machine's usage is important. Maintaining a log that records operating hours, tool changes, and any issues encountered can provide valuable insights into the machine's condition.
This information allows operators to schedule regular professional maintenance or servicing as the manufacturer recommends. Professional technicians have the expertise to conduct thorough inspections, make necessary adjustments or repairs, and ensure all components function correctly. This proactive approach helps minimize downtime and ensures the longevity of the CNC machine.
SYIL Machine Tools understands the importance of troubleshooting and maintenance in maximizing CNC machine performance. With its commitment to quality and sustainability, SYIL provides reliable machines that require regular care to remain efficient. By following these troubleshooting steps and implementing routine maintenance practices, operators can keep their CNC machines running smoothly for years.
Safety Guidelines and Best Practices
When operating a CNC machine, it is crucial always to prioritize safety. Proper safety protocols and guidelines ensure the operator's well-being and prevent accidents or injuries. Here are some essential safety guidelines to keep in mind:
Following proper safety protocols and guidelines during operation
Operators should adhere to established safety protocols and guidelines to run a CNC machine safely. This includes wearing appropriate personal protective equipment (PPE), such as safety glasses, gloves, and ear protection. Additionally, operators must be familiar with emergency stop procedures and know how to shut down the machine quickly in case of unexpected issues.
Utilizing personal protective equipment (PPE) for operator's safety
Personal protective equipment (PPE) ensures the operator's safety while running a CNC machine. Safety glasses protect the eyes from flying debris or metal chips, while gloves provide hand protection against sharp edges or hot surfaces. Ear protection is necessary to prevent hearing damage from loud noise generated during machine operation.
Maintaining a clean and organized work area to prevent accidents
A clean and organized work area is essential for safe CNC machine operation. By keeping the workspace tidy, operators minimize the risk of tripping over tools or materials, reducing the chances of accidents or injuries. It is crucial to regularly remove excess chips or debris from the machine's table or vice to maintain optimal performance.
Implementing best practices to maximize efficiency and productivity
In addition to ensuring safety, implementing best practices can enhance efficiency and productivity when running a CNC machine. This includes regularly inspecting cutting tools for wear or damage and properly aligning workpieces for accurate machining results. Operators should also optimize cutting parameters such as speed, feed rate, and depth of cut based on material properties for optimal performance.
Conclusion
To effectively run a CNC machine, it is important to follow these five essential steps:
- Ensure that the machine is properly set up and calibrated. This includes checking the alignment and accuracy of the machine's components.
- Prepare the necessary tools and materials before starting the operation. This involves checking and organizing all cutting tools or drill bits required for the job.
- Load the design file or program into the machine's software. This step ensures that the machine understands and accurately executes the desired instructions.
- Securely set up the workpiece on the machine's table or vice. Proper positioning and clamping are crucial for stability during operation.
- Program and run the machine by inputting all necessary parameters and commands. Then, monitor its performance closely and make adjustments to achieve optimal results.
While understanding these steps is crucial, it is equally important to emphasize that proper training and experience play a significant role in operating CNC machines effectively. Learning how to run a CNC machine requires hands-on experience under expert guidance.
By investing time in comprehensive training programs, individuals can gain valuable skills in programming, troubleshooting, and maintaining CNC machines. With practice and experience, operators can enhance their efficiency while minimizing errors during operation.
SYIL Machine Tools develops and manufactures precision CNC machines for milling and drilling. With over 12k machines supplied globally, they prioritize quality and sustainability. Operating in multiple countries, SYIL is becoming a recognized brand in the industry.